
Механическое оборудование предприятий по производству вяжущих строи
..pdf
Рис. 94. Затвор-мигалка однолепесткового типа:
1 |
— крышка |
люка; |
2, |
Н — за |
|
жимы; |
3 -- футеровка; |
/ — за |
|||
слонка; |
5 — корпус; |
в — ось; |
|||
7 — крышка; |
9 — противовес |
||||
газоходов |
и |
циклонов |
|||
вследствие их теплового |
|||||
расширения |
и |
удли |
|||
нения. |
транспортиро |
||||
|
Для |
||||
вания |
сырьевой |
муки |
|||
из циклонов в газоходы |
|||||
и |
вращающуюся |
печь |
|||
установлены футерован |
ные течки круглого сечения. На каждой течке предусмотрены специальные затворы-мигалки, линзовые компенсаторы и ремонт ные люки.
Мигалки однолепесткового типа обеспечивают герметизацию цик лонов, предохраняя от подсоса в них газов из расположенных ниже циклонов. Мигалка (рис. 94) состоит из сварного корпуса 5, за слонки 4 из жаропрочной стали, оси 6 на подшипниках скольжения, а также противовесов 9, закрепленных на оси. Мигалку настраивают так, чтобы заслонка открывалась только в те моменты, когда масса накопившегося на ней материала сможет преодолеть силу тяжести противовесов. Материал сбрасывается в течку и противовесы воз вращают заслонку в первоначальное положение.
§ 79. Декарбонизаторы
Декарбонизатор представляет собой аппарат, встраива емый в систему циклонных теплообменников и служащий для по вышения степени декарбонизации сырьевой муки путем дополнительного сжигания в нем значительного количества топлива.
Принцип действия декарбонизатора заключается в следующем. К декарбонизатору (рис. 95) подводят по воздуховоду 13 горячий воздух (600—700 °С) из охладителя клинкера. Перед декарбонизатором воздуховод разветвляется на три направления. По двум через тангенциальные окна воздух подводят к вихревому кальципатору 15, по третьему 12 — к вихревой камере сгорания 9.
Сырьевая мука температурой 750 °С из циклонов II ступени по течкам 8 выпадает в воздушные газоходы вихревого кальцинатора на специальные горизонтальные стержни — деспиргаторы, под хватывается потоками горячего воздуха и вносится в кальцинатор, где происходит эффективный теплообмен между горящим топливом и сырьевой мукой с достижением степени ее декарбонизации до 0,45. Этому способствуют, с одной стороны, создание вихревых потоков, обеспечивающих тесный контакт между горячим воздухом с относи тельно высоким содержанием кислорода и частицами материала, с другой — обеспечение высокотемпературной газовой среды в каль-
212
Рис. 95. Схсмз дскарбонизатора |
8 |
9 |
10 |
11 и |
|||||||
/ — загрузочная |
головка; |
2 — рс |
|
|
|
|
|||||
гулнрующая диафрагма; 3 |
смеси |
|
|
|
|
||||||
тельная |
камера; |
4 — течка |
сырье |
|
|
|
|
||||
ной |
муки |
и печь; |
5 — подъемный |
|
|
|
|
||||
газоход; 6 — циклоп I ступени; 7 — |
|
|
|
|
|||||||
газоход к циклону И ступени; 8 — |
|
|
|
|
|||||||
течка от циклона II ступени; 9 — |
|
|
|
|
|||||||
вихревая |
камера; |
10 — топливная |
|
|
|
|
|||||
форсунка |
вихревой |
камеры; 11 — |
|
|
|
|
|||||
шибер; |
12 |
— воздуховод к |
вихре |
|
|
|
|
||||
вой |
камере; |
13 — воздуховод горя |
|
|
|
|
|||||
чего воздуха от охладителя клин |
|
|
|
|
|||||||
кера |
к декарбонизатору; 14 — топ |
|
|
|
|
||||||
ливные |
|
форсунки |
кальцинатора; |
|
|
|
|
||||
15 — кальцинатор; |
16 — нисходя |
|
|
|
|
||||||
щий |
газоход; |
17 — вращающаяся |
|
|
|
|
|||||
печь |
(сплошные |
стрелки — движе |
|
|
|
|
ние материала, штриховые — пото ки газов)
Рис. |
|
96. |
Декарбонизатор |
|
СМЦ-29: |
|
|
||
1 — вращающаяся печь |
4,5x80 м; |
|||
2—уплотнение загрузочного конца |
||||
печи; |
3 —задвижка с приводом; 4 — |
|||
смесительная камера; |
5—газоход; |
|||
6 — кальцинатор; |
7—вихревая ка |
|||
мера; |
8 — воздуховод подачи горячего воздуха из охладителя; 9 — воздуховод к вихревой |
|||
камере; |
10 — подача сырьевой муки в декарбонизатор; 11 — подача сырьевой муки из цик |
|||
лонов |
I |
ступени |
во вращающуюся печь; 12 — загрузочная головка |
цинаторе в результате поступления продуктов сгорания из вихревой камеры 9 и сжигания топлива в самом кальцинаторе (в вихревой камере сжигается 2—5 % топлива, подаваемого в декарбонизатор).
После кальцинатора пылегазовый поток температурой 950 °С попадает в смесительную камеру 3 по нисходящему газоходу 16. В смесительной камере пылегазовый поток интенсивно перемеши вается с потоком отходящих от вращающейся печи газов темпера турой 1000—1100 °С.
В результате этого степень декарбонизации после смесительной камеры достигает 0,85—0,95. Степень декарбонизации зависит во многом от доли сжигаемого в декарбонизаторе топлива. Так, при подаче в декарбонизатор 60, 65 и 70 % топлива, степень декарбони зации сырьевой муки составит соответственно 0,85; 0,86—0,88 и 0,9.
Из смесительной камеры пылегазовый поток выносится по подъем ному газоходу 5 в циклон I ступени 6, где происходит разделение газов и сырьевой муки. Сырьевая мука температурой 800—850 °С оседает и по течке 4, оснащенной мигалкой, поступает в печь 17 через загрузочную головку 1. Во вращающейся печи заканчивается процесс термической обработки материала.
Для уравновешивания двух аэродинамических систем враща ющаяся печь — декарбонизатор перед смесительной камерой уста навливают регулирующую диафрагму 2. Она состоит из двух шибе ров, перемещающихся в горизонтальной плоскости, и позволяет перекрывать до 70 % сечение газохода к декарбонизатору. Декар бонизатор изготовляют из листовой стали и облицовывают изнутри огнеупорными материалами. Общий вид декарбонизатора СМЦ-29
приведен на рис. |
96. |
|
Г ла ва |
18 |
|
ВРАЩАЮЩИЕСЯ |
ПЕЧИ |
|
§ 80. Общие сведения |
||
Вращающиеся |
печи входят в состав печных агрегатов |
сухого и мокрого способов и являются устройством, в котором завершается процесс клинкерообразования (агрегаты сухого способа) или происходит весь процесс термохимической обработки материала — сушка, подогрев, декарбонизация и др. (агрегаты мок рого способа).
Печи могут быть одинакового профиля (диаметра) по всей длине, а также иметь расширенные участки. Цель увеличения диаметра отдельных участков печи — увеличение времени пребывания в них сырьевого материала путем снижения скорости движения сырья и одновременно печных газов, что повышает эффективность тепло обмена в этой зоне. В зависимости от свойств сырьевых материалов диаметр печи увеличивают на различных участках по ее длине. Однако расширение участков печи имеет и отрицательные послед-
214

Р и с |
98. |
В р а щ а ю щ а я с я |
|
|
\ д л я М 1Д.1ЧИ |
|
И . 1я ф > р --у Н К |
|
М О П |
г v.- |
. ч и : ъ 'м .ч и к I1м м: |
Рис. 97. Вращающаяся печь СМЦ-9 размером 4,5X80 м печного агрегата сухого способа
печь С.ЧЦ-40‘2.16 размером 5X185 м печного arpeiaTa мокрого способа:
л г р \ д |
"i n ил) |
к о н ц а |
" i n ; 3 — корпус |
печи; 4 — бандаж; |
5 — разгрузочная |
головка; 6 — то- |
|
п о к |
>11 ц л |
п е ч и ; ' |
р о л и к о о п о р л ; Ч |
с т а н ц и я |
жидкого |
смазывания; 10 |
— установка тер |
\ с г p ’o i i c r u o д л я н о л н р л т л н ы л и н п е ч ь ; 1 3 |
г п д р о у п о р |
|
|
медленного Вращения (0,023 об/мин) включают в работу при автома тической сварке кольцевых швов корпуса печи во время проведения монтажных и ремонтных работ.
Загрузочная головка 1 служит для соединения вращающегося корпуса печи с неподвижными узлами печного агрегата — циклон ным теплообменником и декарбонизатором. Загрузочный конец корпуса изготовляют в виде конуса с фланцем, к которому при крепляют кольцевой элеватор с уплотнением.
Разгрузочная головка 9 предназначена для |
соединения корпуса |
с неподвижной шахтой охладителя клинкера. |
В месте соединения |
с вращающейся печью головка имеет расширенную часть с отверстием для входа разгрузочного конца печи. На торцовой стенке головки, противоположной стенке с отверстием для печи, расположена откат ная двухстворчатая дверь с отверстием для ввода форсунки 10, а также смотровыми и ремонтными люками. Размеры дверного про ема выбирают с таким расчетом, чтобы при ремонтных работах через него мог проходить в печь электропогрузчик для механизации футеровочных работ. Внутри головка и откатная дверь облицованы огнеупорными материалами. В местах примыкания к печи загрузоч ной и разгрузочной головок смонтированы уплотнения 2, 11. На разгрузочном конце корпуса устанавливают также устройство 12 воздушного охлаждения разгрузочного конца печи.
Вращающуюся печь оснащают устройством 8 воздушного охла ждения корпуса печи, индивидуальными станциями для подачи смазочного материала к роликоопорам 15, а также контрольно измерительными и регулирующими приборами.
Вращающиеся печи мокрого способа отличаются от печей сухого способа лишь конструкцией отдельных узлов и наличием некоторых
специфичных |
устройств. |
|
|
|
|
|
||
Т а б л и ц а |
47 |
Техническая характеристика вращающихся |
печей |
|
||||
|
|
|
Печн |
мокрого способа |
Печи сухого способа |
|||
Показатель |
|
4 X 150 м |
4 ,5х |
5Х 185 м |
5 x 7 5 м |
7/6,4Х |
4, 5Х 80 м |
|
|
|
|
||||||
|
|
|
|
X 170 м |
|
|
X 95 м |
|
Производительность, |
850 |
1200 |
1800 |
1600 |
3000 |
3000 |
||
т/сут |
|
|
(при |
1влажности |
шлама |
|
|
|
|
|
|
|
36%) |
4 |
3,5 |
3,5 |
4 |
Уклон печи, |
/о |
|
4 |
4 |
||||
Чистота вращения, |
0 ,5 5 - |
0.6— |
0,6— |
0,07— |
0,6—1,3 |
0,6— |
||
об/мин |
|
|
1.1 |
1,24 |
1,24 |
1,4 |
4 |
3,44 |
Число опор |
навески |
7 |
7 |
7 |
3 |
4 |
||
Длина зоны |
30—33 |
31—42 |
45—52 |
— |
— |
— |
||
цепей, м |
электро |
320 |
250X2 |
320X2 |
250 |
320X2 |
400 |
|
Мощность |
||||||||
двигателя, |
кВт |
|
1700 |
2200 |
2700 |
1010 |
1885 |
1030 |
Площадь внутренней |
поверхности по фу теровке, м2
Типовой конструкцией для печей мокрого способа можно считать конструкцию вращающейся печи 5 х 185 м агрегата мокрого способа производительностью 1800 т клинкера в сутки (рис. 98). Наиболее эффективные длинные печи мокрого способа используются с раз личными внутрипечными теплообменными устройствами. В данной конструкции применена цепная завеса 11. Цепную завесу монтируют внутри печи со стороны загрузочного конца. Она состоит из боль шого числа цепей, прикрепленных к корпусу печи одним или двумя концами. Завеса обеспечивает повышение теплообмена между газо вым потоком и сырьевым материалом. Кроме того, она служит свое образным мокрым фильтром, так как при прохождении запыленного газового потока частицы пыли осаждаются на цепях, влажных от налипшего шлама.
Печи мокрого способа обеспечиваются установками для возврата в печь пыли, уловленной в пылевой камере и электрофильтрах.
Техническая характеристика вращающихся печей приведена
втабл. 47.
§81. Корпус печи
Корпус печи представляет собой цельную трубу, сварен ную на месте монтажа из отдельных кольцевых цилиндрических обечаек, изготовленных из листовой стали. В случаях применения вращающихся печей с расширенными участками в местах перехода диаметров ввариваются кольцевые конические обечайки. Цилиндри ческие обечайки бывают двух типов: пролетные и подбандажные. Толщина пролетных обечаек 20—40 мм, подбандажных, обеспечива ющих необходимую жесткость корпуса в опорных узлах, — 40— 100 мм.
На корпус печи насаживают бандажи, закрепляемые с помощью специальных элементов (башмаков, прокладок, упоров и др.). В слу чае применения вварных бандажей их вваривают непосредственно в корпус между обечайками. На корпусе смонтирована также венцовая шестерня, посредством которой корпус печи получает враще ние от привода. Внутри корпуса печей мокрого способа со стороны загрузочного конца размещены различные теплообменные устрой ства (цепная завеса, пересыпающие теплообменники). В корпусе предусмотрены люки для проведения ремонтов футеровки и отбора проб материала.
Современные вращающиеся печи работают, как правило, па от крытом воздухе, поэтому материал их корпусов подвергается в зим нее время воздействию отрицательных температур (до —40 С и ниже). В связи с этим корпуса печей, работающих в климатических зонах с низкими температурами, изготовляют из сталей с высокой ударной вязкостью при хорошей свариваемости. Этим требованиям для обечаек любой толщины лучше всего удовлетворяет низколеги рованная сталь 09Г2С (ГОСТ 19282—73). Для работы в более мягких климатических условиях корпуса можно изготовлять из сталей других марок: ВСтЗспб (ГОСТ 380—71) — для обечаек толщиной до
218
25 мм включительно, 16Д (ГОСТ 6713—75) — для обечаек толщиной свыше 25 мм, ВСтЗГспб (ГОСТ 380—71)— для обечаек толщиной до 30 мм включительно.
На корпуса вращающихся печей действуют значительные знако переменные механические и тепловые нагрузки, что в условиях повышенных требований к их надежности позволяет отнести корпуса к ответственным конструкциям. Действительно, многие проявля ющиеся при эксплуатации неисправности корпуса (такие, как про жог, трещинообразование, значительные деформации и др.) приводят к остановке всего печного агрегата.
На корпус, представляющий собой тонкостенную цилиндриче скую оболочку переменной толщины, лежащую на нескольких опо рах, действуют следующие нагрузки: нагрузка Рк от собственной массы корпуса, включая массу зубчатого венца; нагрузка Рф от массы футеровки; нагрузка Рм от массы обжигаемого материала; нагрузка Робм от массы обмазки — наслоения материала на футе ровке горячего конца печи, являющегося следствием его технологи ческих свойств и служащего своеобразным предохранительным слоем, защищающим футеровку от излишнего температурного воз действия и изнашивания; нагрузка Рт. у от массы теплообменных устройств (для печей мокрого способа).
Например, эти нагрузки для печи 5,6/5 X 185 м мокрого способа составляют: Рк = 8919 кН; Р* = 14 259 кН; Рм = 2548 кН; Робм = = 3293 кН; РТв у = 1098 кН. Отсюда видно, что наибольшие на грузки возникают от воздействия собственной массы корпуса — 29,6 % и массы футеровки — 47,3 %.
Кроме того, на корпус действует крутящий момент от открытой зубчатой передачи привода. При работе вращающихся печей воз никают также дополнительные напряжения в месте посадки бандажей на корпус от их температурного расширения. Следует отметить, что, несмотря на принимаемые меры по теплоизоляции, температура корпуса печи в зоне спекания печей достигает 270—350 °С.
Расчет корпуса вращающейся печи представляет собой довольно трудную инженерную задачу, поэтому здесь он не приводится,
арассматривается лишь порядок его выполнения.
Вначале расчета составляют расчетную схему корпуса печи,
представляющей собой многопролетную неразрезную балку пере менной жесткости на опорах. Далее определяют усилия, действу ющие на корпус печи. К равномерно распределенным нагрузкам относят нагрузки от массы корпуса, футеровки, цепной завесы, теплообменника, обжигаемого материала, обмазки; к сосредоточен ным — нагрузки от массы венцовой шестерни, бандажей, подбандажных утолщений корпуса. После этого строят эпюры расчетных нагрузок. Затем определяют опорные реакции. В табл. 48 при ведены нагрузки на опоры некоторых вращающихся печей.
После определения опорных реакций строят эпюры поперечных сил и изгибающих моментов. Используя теорию расчета тонкостен ных оболочек, определяют приведенные напряжения в пролетах печи и сравнивают с допускаемым напряжением. За допускаемое напря-
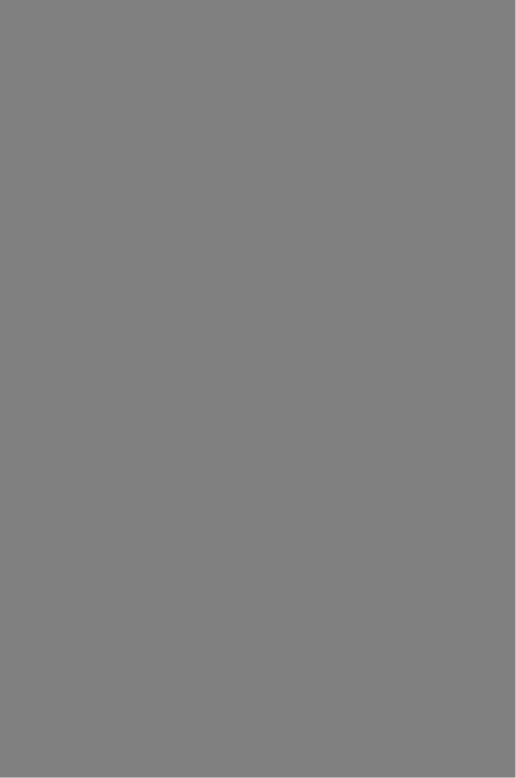