
Механическое оборудование предприятий по производству вяжущих строи
..pdfВ зависимости от компоновочной схемы установки первичного дробления колосниковые решетки над приемным бункером устанав ливают горизонтально или с наклоном (до 45°), что позволяет нега баритным кускам самопроизвольно скатываться с решетки. Наиболее часто используют горизонтальные решетки, опускаемые в бункер на некоторую глубину, что исключает просыпь при разгрузке транс портных средств. В этом случае предусмотрены механизированные средства для удаления с решетки негабаритных кусков породы.
Размеры горизонтальной колосниковой решетки, а следовательно,
и загрузочной части бункера принимают из расчета, что запас сырья
вбункере должен обеспечивать работу дробилки в течение не менее 2 ч с учетом возможности разгрузки принятых транспортных средств (автомобилей-самосвалов или вагонов-самосвалов). Глубина уста
новки решетки от верхней части бункера определяется объемом надрешеточного пространства (объем бункера от его верхней части до верхней части колосниковой решетки), который должен быть не менее одного объема разгружаемого транспорта.
Учитывая большие ударные нагрузки от разгружаемых кусков породы, колосники изготовляют, как правило, из сортного проката (двутавров, изношенных железнодорожных рельсов, кругов, ква дратов и др.). Чтобы исключить заклинивание кусков между колос никами, их устанавливают широким основанием вверх. Для пре дупреждения деформации длинных колосников и изменения зазора между ними приваривают поперек несколько рядов из проката. Увеличение срока службы колосниковой решетки достигают наплав кой ее рабочих поверхностей твердыми сплавами.
§ 40. Подвижные колосниковые грохоты
В отличие от колосниковых решеток в колосниковых грохотах сортирование породы по крупности происходит в результате дополнительного колебательного движения решетки. При встряхи вании сырьевого материала мелкие куски в результате большей насыпной плотности быстро переходят в нижние слои и провали ваются в подрешеточное пространство: более крупные куски, не про шедшие по размерам через щели колосниковой решетки, остаются на поверхности и транспортируются под уклон к ее разгрузочному концу.
Для отсева мелких кусков перед первичным дроблением породы используют инерционные наклонные колосниковые грохоты тяжелого типа (рис. 33). Грохот имеет мощный футерованный короб 1, внутри которого размещают одну или несколько наклонных решеток 2. Короб установлен на опорные кронштейны рамы 4 с помощью па кетов винтовых пружин 5. Конструкция опорных устройств позво ляет располагать колосниковую решетку под углом наклона к го ризонту до^ 30° Сменные колосники из износостойкой высокомар ганцовистой стали устанавливают с зазором до 250 мм и крепят их специальными клиньями 3. Расстояние между колосниками в на правлении от загрузки породы к выгрузке увеличивают, что пред
отвращает забивание решетки. Вал 8 вибратора приводится от элек тродвигателя 6 клиноременной передачей 7
Ниже приведена техническая характеристика инерционного ко лосникового грохота тяжелого типа.
Размер колосниковой решетки, мм |
1500X3000 |
||
Угол наклона |
решетки, ° |
. |
10—30 |
Частота вращенияэксцентрикового вала, об/мин |
800 |
||
Амплитуда колебаний, мм |
. |
3,5—4 |
|
Мощность электродвигателя, |
кВт |
17 |
|
Размеры, мм: |
|
|
3050 |
длина |
|
|
|
ширина |
|
|
2200 |
высота |
|
|
1500 |
Масса, т |
|
|
5,6 |
Грохот опирается на фундамент или его подвешивают с помощью |
|||
пружинных |
амортизаторов. |
|
|
Производительность |
колосниковых грохотов-питателей (в м3/ч) |
||
|
|
П = 3600В коК* |
(73) |
где В — ширина грохота, м; h — условная высота слоя крупнокусковой породы, принятая равной 0,24 м; v — средняя скорость перемещения крупнокусковой породы -по грохоту, м/с; К — коэффициент, учитывающий плоскую поверхность одноярус ной колосниковой решетки, К = 0,85.
Ниже приведены значения скорости перемещения кусков породы по колосниковой решетке.
Угол а наклона колосниковой решетки, |
0 |
5 |
10 |
15 |
2о |
и, м/с |
0 |
0,15 |
0,32 |
0,55 |
0,8 |
102
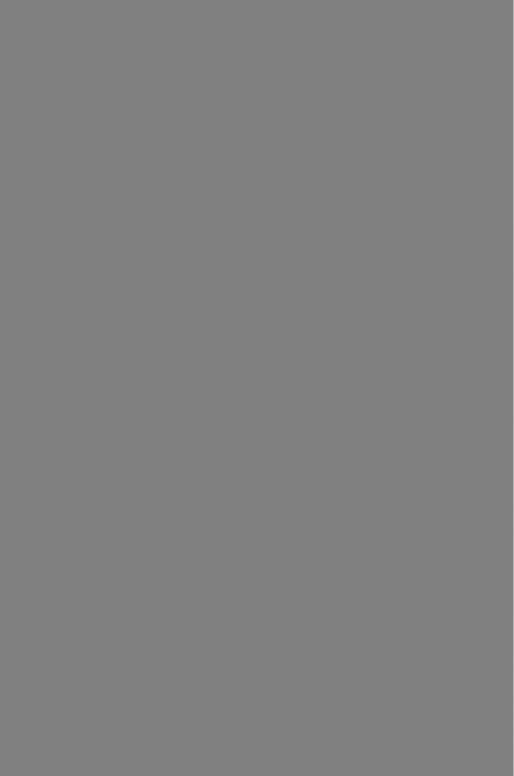
Рис. 34. Сепаратор шкивного типа:
а — общий вид; б — схема работы шкива электромагнитного сепаратора
притягиваются к магниту и выводятся из транспортируемого сырье вого материала.
Используемые на цементных заводах магнитные сепараторы по конструкции разделяют на шкивные и подвесные.
Сепаратор шкивного типа (рис. 34) представляет собой короткий ленточный конвейер. Ведущий разгрузочный барабан конвейера — набранная кольцами многополюсная электромагнитная система, которая насажена на вал 5 и вращается вместе с ним. Магнитная система представляет собой цилиндрический стальной якорь 4, в кольцевых пазах которого заложены катушки 3. Сверху пазы закрыты кольцами 1 из немагнитного материала (латуни, резины и др.). Концы проводов от катушек выводят наружу через пусто телый вал к контактной коробке 2 и через щетки и кольца соединяют с питающими проводами. Сепаратор работает на постоянном токе напряжением ПО или 220 В.
Т а б л и ц а 27. Техническая характеристика шкивов магнитных сепараторов
Показатель |
65-63 |
|
|
|
ШЭ- |
Ширина ленты, |
мм |
650 |
Диаметр шкива, |
мм |
630 |
Частота вращения, об/мин, не бо |
60 |
|
лее |
|
ПО |
Напряжение сети постоянного то |
||
ка, В |
|
2 |
Потребляемая мощность обмоток, |
||
кВт |
|
|
Ориентировочная толщина слоя |
170 |
|
материала на ленте, мм |
1 |
|
Масса, т |
|
о
00
о
ОС
СГ)
в
800
800
50
220
5
170
2,5
ШЭ-100-80 |
ШЭ-120-1 00 |
ШЭ-140-100 |
1000 |
1200 |
1400 |
800 |
1000 |
1000 |
50 |
50 |
50 |
220 |
220 |
220 |
5 |
6,5 |
9 |
170 |
320 |
350 |
2,7 |
4 |
4,2 |
Рис. 35. Подвесной электромагнит
Немагнитный сырьевой материал сво бодно сходит с ленты, огибающей бара бан. Магнитный же материал притяги вается к ленте в зоне магнитного поля, а по выходе из нее отделяется от холостой ветви ленты и направляется в емкость металлолома.
Шкивы магнитных сепараторов ис пользуют в ленточных питателях и кон вейерах в качестве разгрузочных шкивов.
Техническая характеристика шкивов электромагнитных сепара торов приведена в табл. 27.
Подвесные электромагниты (рис. 35) применяют для извлечения железных предметов из перемещаемого ленточными конвейерами слоя породы высотой до 200 мм и более и движущейся со скоростью до 2 м/с в зависимости от мощности. Электромагнит имеет полюсную скобу, состоящую из соединительной планки 3 с сердечниками 7, на которые надеты электромагнитные катушки 2, заключенные в металлический кожух. Снизу к сердечникам прикреплены полюс ные наконечники. Катушки соединены последовательно, что позво ляет подключать их к сети постоянного тока напряжением 220 В. Электромагниты с помощью устройства 4 подвешивают вертикально или под углом, соответствующим углу наклона конвейера. Для повы шения эффективности сепарации электромагнит располагают над слоем транспортируемого сырья на минимальном расстоянии. По люсный наконечник периодически очищают от налипших на него ферромагнитных предметов.
Р А З Д Е Л Ш
ОБОРУДОВАНИЕ СЫРЬЕВЫХ ЦЕХОВ
Г л а в а |
9 |
СЫРЬЕВОЙ |
ЦЕХ |
§ 42. Общие сведения
Сырьевой цех цементного завода предназначен для бесперебой ного обеспечения вращающихся печей цеха обжига клинкера гото вым шламом или сырьевой мукой с заданными свойствами. В про цессе подготовки сырьевых смесей (шлама, сырьевой муки) к обжигу сырьевой передел является завершающим этапом. Качество смесей является одним из факторов, определяющих стабильность работы печного агрегата и свойства цемента.
Основной технологической операцией сырьевых цехов является помол в мельницах сырьевых компонентов в определенном соотно шении с целью получения для обжига в печи сырьевой смеси задан ного гранулометрического и химического составов.
Расчет производительности и выбор оборудования ведут с учетом круглосуточного режима работы сырьевого цеха. Рассчитывая не обходимое количество шлама или муки для питания вращающихся
печей, определяют годовую мощность сырьевого цеха |
(в м3) |
Q - 8760Кз?ЯКт.„, |
(75) |
где 8760 — годовое календарное время при круглосуточной работе печей, ч; /С3 — коэффициент запаса мощности, К 3 = 1,3; q — удельный расход шлама или муки на производство 1 т клинкера, м:1/т; П — суммарная производительность печей, т/ч; *Т . и — коэффициент технического использования печей.
Необходимое количество технологического оборудования сырье вого цеха рассчитывают, учитывая его производительность и коэф фициент технического использования.
§ 43. Технологические схемы приготовления шлама
Технологическую схему приготовления шлама выбирают с учетом наиболее эффективных способов стабилизации его химиче ского состава и методов помола.
На предприятиях цементной промышленности применяют в ос новном два метода корректирования шлама, обеспечивающих стабиль ность его химического состава: порционный и поточный методы. Корректирование шлама обоими методами осуществляется по титру (объемному содержанию углекислого кальция), коэффициенту на сыщения (КН) или по КН и одному из модулей.
Порционный метод корректирования заключается в следующем. После первой стадии измельчения отдозированные в определенном
106
Рис. 36. Схема поточного приготовления шлама
соотношении сырьевые компоненты (известняк, глиняный шлам) с доба влением необходимого количества воды подаются в мельницу для тонкого измельчения. Из приямка мельниц продукт помола подается насосом в один шламовый (вертикальный) бассейн. Затем приготовляется сырьевой шлам, отличающийся от ранее приготов ленного повышенным или пониженным коэффициентом КН (на 7—10 %), и за полняют им другой вертикальный бас сейн. Шламы в определенном количе
стве из |
обоих |
бассейнов подаются |
в третий |
вертикальный бассейн. Здесь |
|
полученная смесь |
перемешивается по |
даваемым сжатым воздухом, и после уточнения химического состава и не обходимого корректирования усреднен ный шлам сливается в горизонтальный бассейн, где перемешивается и хра нится. Из горизонтального, шламового бассейна шлам насосами подается в печ
ной агрегат. Этим методом корректируют, как правило, такие смеси, которые приготовляют из достаточно стабильных по составу сырьевых компонентов.
Поточным методом корректируют шлам с использованием двух промежуточных шламов с пониженным и повышенным титром или с приготовлением одного шлама при периодическом корректирова нии соотношения сырьевых материалов перед помолом и последу ющим усреднением шлама в горизонтальном шламовом бассейне.
При поточном методе приготовления шлама из мягких сырьевых компонентов (глины и мела) полученный на первой стадии измель чения (дробления) в мельницах «Гидрофол» глиномеловой шлам по шламопроводу 1 (рис. 36) перекачивают в горизонтальные бассейныусреднители 2. Один бассейн заполняют шламом с пониженным ти тром или пониженным КН, а другой бассейн — шламом с повышен ным титром или повышенным КН. В бассейнах шламы усредняются по всей массе.
Шламы из бассейнов смешивают в пропорции, которая зависит от их химического состава, определяемого непрерывно путем ана лиза, проб, отбираемых автоматически пробоотборниками 4 и 11, рентгеновским квантометром 3. Протекание по трубопроводам необ ходимого количества шламов обеспечивается с помощью регулиру ющих клапанов 14 по команде ЭВМ 15. Количество протекающего по трубопроводам шлама измеряется электромагнитными расходоме рами 5. Оба шлама соединяются в общем трубопроводе и проходят
классификацию в гидроциклонах 6. При этом тонкая фракция шлама поступает в промежуточную емкость 10, а грубая фракция — в мель ницу 9 на доизмельчение, после чего также направляется в прия мок 10. В мельницу одновременно с грубой фракцией шлама весо вым дозатором 8 из бункера 7 подается железистый компонент (на пример, огарки). Из промежуточной емкости тонкодисперсный шлам центробежными насосами перекачивается в горизонтальный бассейн 12 вместимостью до 8 тыс. м3. В бассейне шлам перемешивается, в ре зультате чего он усредняется. Усредненный по составу шлам, отве чающий заданным модулям, центробежными насосами по шламопроводу 13 подается в печной агрегат.
При поточном методе приготовления шлама со сравнительно стабильным составом добываемого сырья производят предваритель ное его усреднение на складе с последующим дозированием сырьевых компонентов перед подачей в мельницу. В результате получают сырьевой шлам, требующий лишь незначительного корректирования. Корректирование производят в горизонтальных бассейнах путем подачи в них непосредственно из мельниц шлама определенного состава. Состав подаваемого шлама корректируется рентгеновским спектрометром на основе проб шлама из бассейна. В бассейне обеспе чивается интенсивное перемешивание и усреднение состава шлама.
Тонкий помол сырьевых компонентов при производстве цемента по мокрому способу осуществляется, как правило, в трубных мель ницах с шаровыми мелющими телами или комбинированной дробя щей загрузкой (шары с цильпебсами), работающих в открытом цикле. В последние годы все большее применение находят мельницы замк нутого цикла с гидроклассификаторами различных конструкций.
§ 44. Технологические схемы приготовления сырьевой муки
При сухом способе производства цемента высокая карьер ная влажность сырьевых материалов и требование низкой влажности сырьевой муки (до 1 %) приводят к необходимости их сушки перед помолом или совмещения процессов сушки и помола. К двум основ ным технологическим операциям производства шлама — помола сырьевых компонентов и корректирования их химического состава_ при приготовлении сырьевой муки добавляется третья — сушка.
Сырьевые компоненты сушат в специальных сушильных устрой ствах или в помольно-сушильных агрегатах с использованием теплоты отходящих из печных агрегатов газов температурой до 400 °С или 0т сжигания топлива в дополнительных топках.
Учитывая высокие энергетические и тепловые затраты при про изводстве шлама и сырьевой муки, а также свойство и состояцие измельчаемого сырья, используют различные технологические схе^ы и соответствующее оборудование. Основными типами помольных установок являются:
агрегаты с трубными тихоходными мельницами, в которых сырье измельчается загружаемыми на 25—30 % объема металлическиМц мелющими телами;
агрегаты с тихоходными мельницами самоизмельчения (типа «Аэрофол»), в которых сырье измельчается в основном крупными
кусками поступающего материала |
и |
небольшим количеством (2— |
3 % объема) загружаемых шаров |
с |
последующим доизмельчением |
в трубных мельницах (подобная установка показана в сырьевом переделе на схеме технологической линии завода производству це мента сухим способом — см. рис. 2);
среднеходовые валковые мельницы, в которых сырье, поступа ющее на горизонтальную или наклонную вращающуюся тарелку (диск), измельчается путем раздавливания роликами (валками) или крупными шарами.
Большинство указанных агрегатов работает в замкнутом цикле с сепараторами различных конструкций и типов.
Мировой цементной промышленностью накоплен большой опыт разработки схем стабилизации химического состава сырьевой муки, обеспечивающих высокое качество подготовки сырья и базирующихся на применении высокопроизводительного, экономичного усреднительного оборудования, быстродействующих анализаторов химиче ского состава, систем управления на основе микропроцессорной техники, автоматизированных систем управления и др.
В технологических линиях заводов по производству цемента су хим способом широко применяют стабилизацию химического состава сырьевых компонентов на всех технологических этапах: добычи в карьере; усреднения на складах; измельчения в помольных агре гатах, корректирования в гомогенизационных силосах.
Так же как и при подготовке шлама, при производстве сырьевой муки применяются порционный и непрерывный методы корректиро вания химического состава. При порционном методе требуются ми нимум два смесительных силоса. Один из них заполняется свежей сырьевой мукой, в то время как гомогенизированная мука из второго (расходного) силоса подается в печной агрегат. Возможно также размещение смесительного силоса над расходным. Это позволяет сокращать время разгрузки смесительного силоса.
При непрерывном |
методе гомогенизация |
может осуществляться |
с помощью одного |
смесительного силоса |
большой вместимости. |
Этот метод основан на протекании части гомогенизированной сырье вой муки через выпускной клапан смесительного силоса, причем через клапан перетекает столько гомогенизированной муки, сколько может вытеснить свежая сырьевая мука, поступающая в силос.
Оба метода корректирования имеют достоинства и недостатки. При порционном методе границы отклонения химического состава подаваемых на перемешивание сырьевых материалов от заданных значений могут быть сравнительно велики. При непрерывном ме тоде, наоборот, отклонения могут колебаться в узких пределах.
Непрерывный метод по сравнению с порционным методом значи тельно уменьшает нагрузку на электрооборудование, переключа ющие и распределительные устройства. В то же время наличие только одного смесительного силоса может создать большие затруд нения при авариях и поломках, когда выход его из строя приводит
©
Рис. 37. Схема обеспечения стабилизации химического состава сырьевых материалов
к остановке печного агрегата. Поэтому при проектировании сырьевых переделов новых цементных заводов сравнивают капитальные вло жения на строительство и производственные затраты, чтобы уста новить более дешевый метод.
На рис. 37 приведена схема обеспечения стабилизации химиче ского состава сырьевых материалов, примененная на Ново-Спасском цементном заводе. Технологическая цепь приготовления сырьевой муки на этом заводе упрощенно представляет собой следующее: добыча известняка в карьере — дробление в щековой дробилке производительностью до 600 т/ч до кусков размером 300 мм — усред нение на складе в двух штабелях — хранение дробленого извест няка в бункере диаметром 18 м и вместимостью 3700 т — совместное с глиной измельчение и сушка в мельнице «Аэрофол» производитель ностью до 260 т/ч с получением крупки — хранение в бункерах крупки высокого В и низкого Н коэффициентов насыщения — сов местное измельчение крупки и огарков в мельнице домола 4x13,5 м производительностью до 190 т/ч — гомогенизация сырьевой муки в двухъярусных силосах диаметром 18 м (вместимость верхнего сме сительного — 2000 т, нижнего расходного — 6000 т) — подача муки в печной агрегат.
Стабилизация химического состава сырьевых материалов осу ществляется в пять этапов (этапы обозначены на схеме цифрами).
Первый этап (на карьере) — проведение шихтовки известняков различных химических составов на основе данных геологической разведки.
Второй этап (на усреднительном складе) — штабелирование из вестняка и разборка штабеля экскаватором.
Третий этап — приготовление крупки заданного состава в мель нице «Аэрофол» — осуществляется следующим образом: автомати ческий пробоотборник отсекает ежеминутные пробы крупки из аэрожелоба перед бункерами крупки В и Н и собирает средние пробы за каждые 12 минут. Химический анализ проб производится анализатором БАРС-5, установленным на бункерах. В случае выхода из строя анализатора анализы выполняются в лаборатории квантометром КРФ-1Б. Доставка проб в лабораторию осуществляется пневмопочтой. По данным анализа пробы количество глины, пода
но