
Механическое оборудование предприятий по производству вяжущих строи
..pdfРис. 87. Печной агрегат СМЦ-26 сухого способа с циклонным теплообменником и декарбонизатором:
|
1 — концевой дымосос; |
2 — электрофильтр; 3 — шибер; |
4 — подвод отработанных |
газов из агрегата для помола и сушки сырья; 5 — уста |
||||
|
новка для охлаждения и увлажнения отходящих печных |
газов; |
6 — отвод отходящих |
печных газов к агрегату для |
помола и сушки |
сырья; |
||
to |
7 — запечный дымосос; |
8 — двухветьевой четырехступенчатый |
циклонный теплообменник; 9 — патрубок для подвода сырьевой |
муки в |
||||
циклонный |
теплообменник; 10 — декарбонизатор; 11 — воздуховод из охладителя |
клинкера в декарбонизатор; |
12 — вращающаяся печь |
|||||
2 |
4 ,5 x 8 0 м; |
13 — колосниковый охладитель клинкера |
|
|
|
|
|
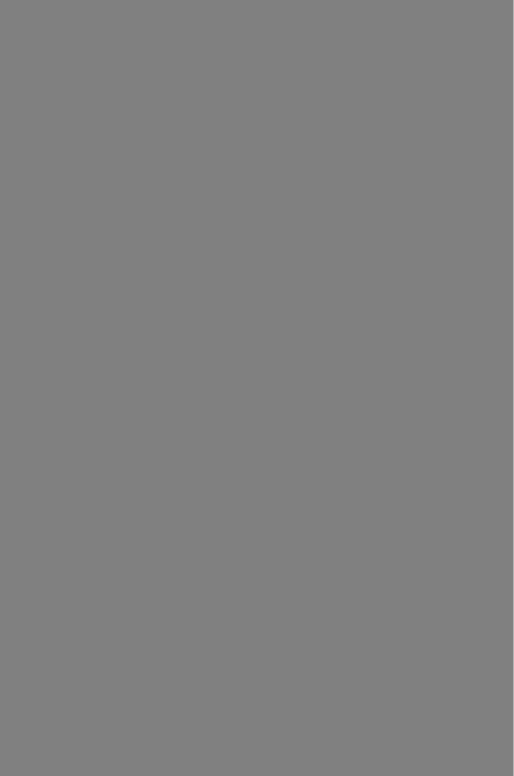
Запечный дымосос: |
|
|
|
|
|
1 |
количество |
м;,/ч |
|
|
|
|
|
производительность, |
|
|
|
|
550 000 |
|
напор, кПа |
|
|
|
|
|
10,5 |
мощность электродвигателя, кВт |
|
|
|
3 400 |
||
масса (без электродвигателя), |
т |
|
|
|
133 |
|
Концевой дымосос: |
|
|
|
|
|
|
тип |
. . |
|
|
|
|
ДРЦ-21Х2 |
количество |
|
|
|
|
2 |
|
производительность, |
м3/ч |
. |
|
|
|
328 000X2 |
напор, кПа |
|
|
|
|
1 ,9 7 |
|
мощность электродвигателя, кВт |
|
. . |
|
630X2 |
||
масса, т |
|
|
1 кг клинкера, |
|
20X2 |
|
Удельный-расход теплоты на обжиг |
кДж/кг |
3 470 |
||||
Технологическое топливо: |
|
|
|
|
Природ |
|
основное |
|
|
|
|
|
|
резервное |
|
|
. |
. |
. |
ный газ |
|
на |
Мазут |
||||
Удельный расход электроэнергии |
1 т клинкера, |
кВт-ч/т |
50 |
|||
Тепловая мощность, кВт |
|
|
. |
|
|
121 528 |
Масса основного технологического оборудования (без футеровки), т |
2 400 |
Кроме рассмотренных печных агрегатов сухого способа в отдель ных случаях находят применение агрегаты с шахтно-циклонными теплообменниками и конвейерными 'кальцинаторами — печи «Леполь».
§ 76. Печные агрегаты полусухого способа
При полусухом способе производства цемента в печные агрегаты подают частично обезвоженный шлам влажностью 17—
26%.
Для обезвоживания цементного шлама широко используют гори
зонтальные камерные пресс-фильтры. Фильтрование в пресс-филь трах представляет собой гидромеханический процесс разделения суспензий с помощью пористой перегородки, задерживающей твер дую фазу (осадок — кек) и пропускающей жидкую фазу (фильтрат).
Камерные пресс-фильтры (рис. 88) состоят из набора вертикально расположенных фильтровальных плит 4 одинаковой конструкции. Между плитами в два слоя уложена фильтровальная ткань 5, служа щая одновременно уплотнением камер, образующихся при сближении и зажиме плит. Для пресс-фильтров применяют в основном ткани из синтетических ма териалов, отличающиеся высокой проч ностью и хорошими фильтрационными свойствами. Шлам подают по каналу /.
Плиты имеют рифленую поверхность для сбора фильтрата, который отводят из фильтра по каналам 3 и 6. Жидкость для промывки и сжатый воздух для просушки
Рис. 88. Устройство камерного пресс-фильтра |
6 |
203
осадка подают по этим же каналам. После зажима плит нажимной плитой 2 операции выполняются в такой последовательности: фильтрование, промывка, просушка, разжим комплекта плит п выгрузка осадка.
Пресс-фильтры различают по способу подвода питания (с верх ним, нижним и центральным питанием) и по степени механизации зажима плит (с ручным или механизированным зажимом).
Фильтр LFA-1250 (ЧССР) (рис. 89) состоит из стоек 7 и 9, соеди ненных балкой 3 с механизмом 5 раздвижки плит 2, являющихся основным фильтрующим элементом, гидроцилиндров 5, осуществля ющих зажим плит, патрубков 1 для подачи шлама и 4 для подачи сжатого воздуха. Снизу установлен сливной желоб 8. Фильтр снаб жен фотоэлементами для предупреждения несчастных случаев при
перемещении |
плит. |
приведена |
|
Техническая характеристика фильтра LFA-1250 |
|||
ниже. |
|
|
|
Размер пластины, м |
|
1,25Х 1,25 |
|
Число камер |
|
м2 |
100 |
Площадь фильтрации, |
312 |
||
Общий объем камер, |
м3 |
5,8 |
|
Рабочее давление, МПа |
1,6 |
||
Максимальное давление в напорном гидроци.тиндре, МПа |
31 |
||
Толщина кека, |
мм |
|
40 |
Установленная |
мощность, кВт |
4,1 |
|
Масса пресса, т |
|
|
58 |
Внастоящее время используют две основные схемы обжига кека.
1.Кек подают на обжиг непосредственно в длинную враща ющуюся печь с внутрипечными теплообменниками. Удельный расход
теплоты на обжиг 1 кг клинкера не превышает 4620 кДж/кг.
2. Кек подают в сушилку-дробилку, куда поступают отходящие газы из укороченной печи или от специальной топки. После сушки порошок направляют в систему циклонного теплообменника печною
204
Рис. 90. Схема получения клинкера полусухим способом в печных агрегатах с длин ной вращающейся печыо
агрегата. Удельный расход теплоты на обжиг 1 кг клинкера в таких установках составляет около 3800 кДж/кг.
На рис. 90 приведена схема получения клинкера полусухим способом в печном агрегате с длинной вращающейся печью на одном из зарубежных заводов. Сырьевой шлам влажностью 43 % обез воживают до 18—19 % в пресс-фильтрах 2 с плитами круглой формы. Диаметр плит 2,3 м, а общая поверхность 1000 м2. После сближения плит (140 шт.) в пресс-фильтр центробежным насосом 1 закачивают шлам под давлением 0,2—0,4 МПа, а затем давление повышают до 1,6—1,8 МПа путем подачи в пресс-фильтр сжатого воздуха. Продолжительность полного рабочего цикла 40 мин, в том числе: закачка шлама — 10 мин, повышение давления до 1,6—1,8 МПа — 10 мин, выдержка под давлением — 10 мин; разгрузка — 10 мин. Через каждые 12 ч работы пресс-фильтр промывают водой.
Под пресс-фильтром установлен наклонный конвейер 4 (угол наклона 5°), на который выгружают из камер кек кусками массой до 250 кг и сливают остатки шлама и воды. Между пресс-фильтром и конвейером установлены неподвижные ножи 5, которые измель чают кек. Измельченный кек конвейером транспортируется в бункера 5 промежуточного складирования, выполненные в виде обратного конуса. Из бункера кек шнеком-разгрузчиком 6 направляют в весо вой дозатор 7 и с помощью конвейера 8 равномерно подают на обжиг во вращающуюся печь 9 размерами 3,6/3,3 X 105 м.
Использование пресс-фильтров для полусухого способа произ водства цемента является перспективным направлением реконструк ции действующих отечественных технологических линий мокрого способа, работающих на шламах с высокой влажностью (40 % и более).
§ 77. Определение основных параметров печных агрегатов
Печные агрегаты являются сложным уникальным обору дованием, работающим на различных видах сырьевых материалах и технологическом топливе, характеристики которых обычно строго индивидуальны для каждого завода. Поэтому основные режимные
205
и конструктивные параметры рассчитывают конкретно для каждого создаваемого агрегата с учетом индивидуальных особенностей его работы.
Основные параметры печных агрегатов (диаметр и длина печи, тепловая мощность, производительность агрегата) можно опре делять как на основе зональных е плотехнических расчетов, так и по эмпирическим зависимостям, полученным на основе анализа, обобщения и математической обработки статистических данных их эксплуатации.
Зональный теплотехнический расчет рассматривается в спе циальных курсах «Технология вяжущих веществ», «Технология' силикатов», и др., поэтому ограничимся лишь кратким описанием последовательности его выполнения.
Задаваясь производительностью агрегата, влажностью шлама и некоторыми другими исходными данными, расчет начинают с опре деления диаметра вращающейся печи в отдельных зонах по тепловой мощности печного агрегата, скорости газов и степени заполнения печи материалом. Далее определяют количество пыли, выносимой газами из печи, после чего рассчитывают материальный и тепловой балансы печи в целом, а затем балансы ее отдельных зон.
При составлении материального баланса все статьи прихода и расхода определяют в килограммах на 1 кг клинкера, теплового баланса — в килоджоулях на 1 кг клинкера. В расходной статье учитывают: теоретический расход теплоты на испарение влаги из сырьевой смеси; потери теплоты с газами, выходящими из печи; потери теплоты с клинкером, выходящим из охладителя клинкера; потери теплоты с воздухом, выбрасываемым в атмосферу; потери теплоты во внешнюю среду и др.
В приходной статье учитывают всю теплоту, которая вводится в печь: от сжигания топлива, вносимая с топливом, сырьем и возду хом, с учетом теплоты вторичного воздуха из охладителя, а также от экзотермических реакций.
Длину отдельных зон печи определяют из расчета теплообмена. Длину печи в целом определяют как сумму длин отдельных зон. Далее подсчитывают и остальные параметры.
Расчет параметров на основе эмпирических зависимостей, отли чаясь простотой, обеспечивает тем не менее достаточную для прак
тики |
точность. |
|
|
Длина вращающейся печи мокрого способа (в м) |
|
||
|
Дм = |
41 (Dn — 0,5) Кп> |
(114) |
где D n — внутренний диаметр корпуса печи, м; /Сп — поправочный |
коэффициент, |
||
/Сп = |
0,97-5- 1,03; в большинстве |
случаев принимают равным 1. |
|
Тепловая мощность печного агрегата мокрого способа (в кВт)
|
NT.M= 29DnL MK n- |
|
( 11^) |
|
Производительность |
печного агрегата |
мокрого |
способа (в т/м) |
|
|
= |
3,6А/Тв м/(пА7м> |
(116) |
|
где q M — удельный расход |
теплоты |
на обжиг 1 кг |
клинкера, |
кДж/кг. |
Удельный расход теплоты на 1 кг клинкера, в большей степени зависящий от влажности шлама (в кДж/кг),
<7„ = 17 10SKW< |
(117) |
где K w — коэффициент влажности шлама.
Для определения основных параметров печных агрегатов сухого способа с циклонными теплообменниками используют следующие зависимости:
Lc = 17(Z>n — 0,5) /Сп; |
(118) |
NT. z = AbDlUK„\ |
(119) |
Пс = 3,6NT. cKn/qc- |
(120) |
Основные параметры печных агрегатов сухого способа с циклон ными теплообменниками и декарбонизаторами
Ьл = 20 (£>п — 0,5) Ки> |
(121) |
|
ЛГт. д = 3802пТдЛ:п; |
(122) |
|
/7Д = |
3,6N T_дЛ:п/9д. |
(123) |
Удельные расходы тепла |
qc и qK на обжиг |
определяют обычно |
в каждом конкретном случае тепловыми расчетами или на основе
данных эксплуатации: |
qc находится обычно в пределах 3300— |
3900 кДж/кг, а 9Д— в |
пределах 1600—1900 кДж/кг. |
Аэродинамический расчет печных агрегатов сводится к опре делению аэродинамических сопротивлений печи, запечных тепло обменных устройств, газоходов, электрофильтров и др., что позволяет определить параметры запечных и концевых дымососов (производи тельность, необходимый напор).
Пример 28. Определить длину печей, тепловую мощность и производительность печных агрегатов диаметром 4,5 м мокрого способа при влажности шлама 38% , сухого способа с циклонными теплообменниками при удельном расходе тепла qc = = 3600 кДж/на 1 кг клинкера, с циклонными теплообменниками и декарбонизатором при <7Д = 1630 кДж на 1 кг клинкера.
Решение. Удельный расход теплоты определяем по формуле (117) qM= 17* 103*0,38 = 6460 кДж на 1 кг клинкера.
Длину печей определяем по формулам (114), (118), (121):
LM= 41 (4,5 — 0,5) 1 = 164 м, принимаем LM— 170 м;
Lc — 17 (4,5 — 0,5) 1 — 68 м, принимаем Lc = 70 м;
■= 20 (4,5 — 0,5) 1 = 80 м.
Тепловую мощность печных агрегатов определяем по формулам (115), (119),
( 122) :
N T, м -= 29-4,52-170-1 = 99 832 кВт;
(VT. с |
45 • 4,52-70* 1 = 63 788 кВт; |
JVt . д == 38*4,52• 80• 1 = 61 560 кВт.
Производительность печных агрегатов определяем по формулам (116), (120), (123).
Ям = 3,6-99 832-1/6460 = 55,6 т/ч;
Пс |
3,6-63 788-1/3600 |
63.8 т/ч; |
Яд |
3,6-61 560-1/1630 |
135,9 т/ч. |
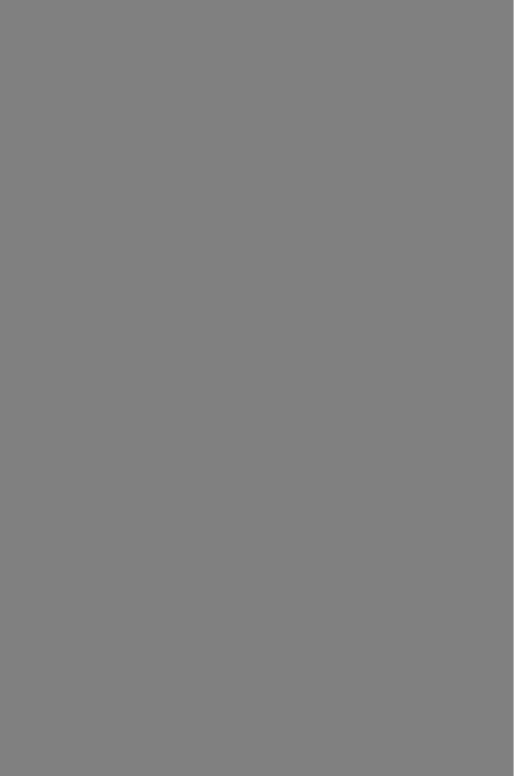
Рис. 91. Схема двухветьевого четырехсту пенчатого циклонного теплообменника
циклонов в газосборник 5. На III ступени теплообменника (циклоны 5, газоходы 3) процесс повторя ется вновь, но уже с участием более горячих газов. Материал, поступив в газоходы 5, подхваты вается газами и устремляется в циклоны 8, откуда после отде ления от газового потока выпа дает по течкам 9 в газоходы 2. Мука на III ступени нагревается до температуры 450—500 °С. На II ступени теплообмен происходит под воздействием еще более горя чих газов, где материал нагрева ется до 600—650 °С. После тер мической обработки на I ступени теплообменника (циклоны 12, га зоход 15) под воздействием наи более горячих (1050—1150 °С) отходящих печных газов сырье вая мука, нагретая до 700—800 °С
и частично декарбонизированная (до 0,2—0,3), поступает во враща ющуюся печь 1 для окончательного обжига. Для герметизации циклонов и предохранения от подсоса в них газов служат затворымигалки 13.
Большая площадь поверхности сырьевой муки, находящейся в газовом потоке во взвешенном состоянии, снижает время ее термо обработки в циклонном теплообменнике до 20—30 с вместо 2—3 ч на аналогичных участках подготовки сырья в печах мокрого способа. Отходящие из теплообменника газы температурой 330—350 °С ис пользуют для сушки материалов в сырьевых помольных агрегатах.
Т а б л и ц а 46. |
Техническая характеристика циклонных теплообменников |
||||||
|
|
|
|
Показатель |
СМЦ-446 |
СМЦ-75 |
|
|
|
|
|
для печи |
для печи |
||
|
|
|
|
|
|
5x75 м |
7/6,4X95 м |
Производительность |
по клинкеру, т/сут |
1600 |
3000 |
||||
Число ветвей |
циклонов, шт. |
2 |
2 |
||||
Число ступеней |
4 |
4 |
|||||
Размеры |
циклонов |
в |
свету (диаметр X высота), |
м: |
6,5Х 10,8 |
||
I ступени |
|
|
|
4,3X7,8 |
|||
II |
ступени |
|
|
|
4,3X7,8 |
5,9Х 10,5 |
|
III |
ступени |
|
|
|
4,3X7,8 |
5,6Х 10,1 |
|
IV ступени |
|
|
т |
2,8Х 12,2 |
2 , 8 \ 12 |
||
Масса без |
футеровки, |
175 |
521 |
т В-Б
Рис. 92. Циклон I ступени:
1 — корпус циклона; 2 — входной патрубок; 3 , 4 — балки; 5 — выходной патрубок; 6 — накладки; 7 — компенсатор; 8 — газоход; 9 — несущая балка; 10, 11 — футеровка
Техническая характеристика отечественных циклонных тепло обменников приведена в табл. 46.
Основными узлами циклонных теплообменников являются цик лоны, газоходы и течки.
Циклон (рис. 92) представляет собой аппарат для тепловой обработки и отделения сырьевого материала от газового потока. Он состоит из конусно-цилиндрического корпуса, крышки, входного и выходного патрубков и опорных лап, служащих для установки циклона на «этажерке». Входной патрубок имеет сечение прямо угольной формы и тангенциально примыкает к цилиндрической части корпуса. Выходной патрубок верхним фланцем соединен с газо ходом. Для придания жесткости конструкции к внутренней поверх
ности корпуса |
приваривают |
кольца, |
которые одновременно слу |
жат опорными |
полками для |
футеровки. |
Для крепления футеровки |
к внутренней поверхности корпуса циклонов и крышки также при варивают анкера. Для придания жесткости крышкам циклонов их усиливают двутавровыми балками 6 и 9.
На корпусе циклона предусмотрены ремонтные, а в нижнеи части конуса — продувочные люки. Продувку осуществляют спе циальными устройствами (рис. 93). На крышке циклонов, входном патрубке и в конической части расположены шуровочные люк"
210