
Механическое оборудование предприятий по производству вяжущих строи
..pdfКритическая скорость для пульпы с твердыми частицами породы размером менее 0,2 мм (в м/с)
Укр = п уЛ(рс — рв)gD/p„, |
(61) |
где п — коэффициент, учитывающий степень перемешивания пульпы, п = 0,7-г-1,2 (значения п берут больше для пород с трудноразмалываемыми включениями); g — ускорение свободного падения, g = 9,81 м/с2.
Благоприятному режиму транспортирования отвечает следующее условие
»п = (1.14-1,2) t»Kp, |
(62) |
где vn — рабочая скорость транспортирования пульпы, м/с.
Перемещение пульпы по трубопроводу (в м) характеризуется потерями напора, обусловленными подъемом пульпы на некоторую высоту, и потерями напора при движении пульпы на горизонтальном участке:
Hn = (h + KLi)pJpB, |
(63) |
где h — геодезическая высота подъема пульпы, м (при наличии на трассе спусков значение h принимают со знаком минус); К — коэффициент, учитывающий потери напора на местные сопротивления (краны, задвижки и др.), К = 1,1; i — потери напора при движении чистой воды, приходящиеся на 1 м длины трубопровода,
i = lv2J(Dg), |
(64) |
здесь X — коэффициент гидравлических сопротивлений, зависящий от диаметра трубопровода:
D, м |
0,15 |
0,2 |
0,25 |
0,3 |
0,35 |
0,4 |
0,45 |
0,5 |
X |
0,0185 |
0,018 |
0,0175 |
0,0165 |
0,016 |
0,0155 |
0,0155 |
0,015 |
Мощность |
электропривода |
насоса |
(в кВт) |
|
|
|||
|
|
|
N = К3ПпНиРп, |
|
|
(65) |
где /С3 — коэффициент запаса мощности, К3 = 1,1-г-1,2.
Пример 19. Рассчитать насосную станцию для перекачки пульпы от мельницы «Гидрофол» производительностью 400 т/ч по сухому сырьевому материалу. Состав сырья: 80 % глины плотностью рГл == 1,76 т/м3 и 20 % известняка плотностью ризв = = 2,5 т/м3. Содержание воды в пульпе — 60 % объема. Дальность транспортирова ния пульпы L — 2,5 км, общая высота подъема трассы пульпопровода h = 15 м.
Решение. Учитывая, что сырье двухкомпонентное различной плотности, плот ность транспортируемого «сухого» сырья определяем по формуле (58):
рс = 0,8ргл + 0,2рИзв = 1,408 + 0,5:= 1,9 т/м3.
Тогда плотность пульпы
рп = 0,6рв + 0,4рс = 0,6 + 0,76 = 1,36 т/м3,
где рв — плотность воды, рв = 1 т/м^.
Подача Насоса пульпы в соответствии с формулой (59):
Пп = 400/(3600-1,36) = 0,08 м3/с.
Диаметр пульпопровода определяем по формуле (60)
D = Y % ^ V 6708 = 0,28 м,
принимаем О = 0,3 м.
По формуле (57) находим объемную концентрацию пульпы:
5 = (рп — Рв)/(рс — Рв) = (It 36 1)/(1 *9 |
1) = 0,4. |
Критическая скорость пульпы в соответствии с формулой (61):
vttp = (0,7 + 1,2) l / 0 ’9 - 1 ^9,81' 0,3 = (0,7 + 1,2) 1,62 м/с.
Учитывая, что в пульпе содержатся неразмолотые частицы известняка, прини маем п = 1,2. Тогда укр = 1,2-1,62 = 1,94 м/с. Рабочую скорость транспортирова ния пульпы определяем по формуле (62):
цп = (1,1-*-1,2) 1,94= 2,13-2,32.
Принимаем vn = 2,3 м/с и %= 0,0165. По формуле (64) i = 0,0165-2,32/(0,3-9,81) = 0,029 м"1.
По формуле (63) определяем напор, необходимый для транспортирования пульпы: Яп = (15 -1- 1,1-2500-0,029) 1,36/1 = 142,5 м.
Необходимая подача насоса пульпы
Ян = 3600-0,08 =-- 288 м3/ч.
По данным табл. 25 выбираем грунтовой насос Гр400/40 с подачей Ян = 400 м3/ч и напором Ян = 40 м.
Число перекачивающих станций с насосами Гр400/40 для транспортирования
пульпы на требуемое расстояние |
|
|
г = |
Яп/Ян = 142,5/40 = |
3,56. |
Принимаем четыре последовательно расположенные перекачивающие станции |
||
с насосами Гр400/40. |
|
|
Запас пульпопровода по подаче и напору |
|
|
КН = 400 ~ 0288 100 - |
100 = 28%; Кп = |
100 - 100 = 12%. |
§ 36. Подвесные канатные дороги
Подвесными канатными дорогами называют транспортные устройства для перемещения материалов в вагонетках по канатам, подвешенным на опорах над землей. Их эффективно используют на цементных заводах средней мощности, расположенных в горной местности, а также в равнинных условиях при пересечении техноло гических путей от горных цехов железнодорожными путями, авто дорогами и др.
Подвесные канатные дороги по конструктивному признаку бывают одно- и двухканатные, по характеру движения вагонеток — коль цевые и маятниковые. У двухканатных подвесных дорог предусма тривают два каната: один — несущий, по нему катятся колеса вагонетки, другой— тяговый. У одноканатных дорог один канат служит одновременно несущим и тяговым органом. Одно- и двух канатные дороги выполняют с кольцевым и маятниковым движе ниями вагонеток. В первом случае тяговый канат замкнут в бесконеч ное кольцо, по одной линии дороги движутся груженые вагонетки, по другой — порожние. Во втором случае вагонетку жестко при крепляют к тяговому канату и она совершает реверсивное движение между конечными пунктами дорог. Для увеличения производитель-
92
ности маятниковые подвесные дороги выполняют двухпутевыми. На цементных заводах в большинстве случаев используют двух канатную кольцевую дорогу.
Двухканатная кольцевая дорога (рис. 29) имеет конечные (за грузочную и разгрузочную) и промежуточные станции, между которыми натянуты несущие канаты 4. На конечных станциях канаты заменены полукольцом из жесткого рельса 1, по которому вагонетки 6 движутся с помощью подвесных толкающих конвейеров или самокатом. На загрузочной станции материал в вагонетки посту пает из бункера 3. Автоматическую загрузку вагонеток ведут с при менением весовых или объемных дозирующих устройств. Автома тическая выгрузка материала на разгрузочной станции происходит при опрокидывании вагонеток. Для возвращения их в исходное положение загрузочная станция оборудована направляющей шиной (спиралью). Загрузочные вагонетки подключаются к тяговому ка нату 10 автоматически. Конструкция разгрузочных станций допу скает прохождение вагонеток без отцепки от тягового каната.
;Ширина колеи канатной дороги обычно равна 3 м. На концах
консоли верхней части опор 12 закреплены чугунные башмаки 5 |с канавками для несущих канатов, облегчающих прохождение ваго неток по опорам, а также роликоопоры 11 тягового каната. Для |создания натяжения каждый несущий канат с одной стороны за креплен на анкерах 13, а с другой — натянут с помощью груза 9. Тяговый канат натянут через натяжной шкив 7 с помощью груза 8. При движении тяговый канат огибает ведущий шкив 2 , получающий вращение от привода 14. В качестве несущих применяют канаты диа метром 30—50 мм, тяговых — канаты диаметром 26—32 мм.
Вагонетки (рис. 30, а, б) состоят из кузова /, подвески 2 и двухили четырехколесной ходовой тележки 3 со сцепным устройством. Подвеску к тележке крепят шарнирно, чтобы кузов на наклонных участках пути сохранял вертикальнее положение. По способу раз грузки различают два основных типа вагонеток: с опрокидываю щимся кузовом (рис. 30, в) и с откидным днищем (рис. 30, г). Для ва гонеток первого типа центр тяжести груженого кузова находится выше оси вращения, а порожнего — ниже. Это обеспечивает возврат Кузова в исходное положение после разгрузки. Объем кузова коль-
[ |
93 |
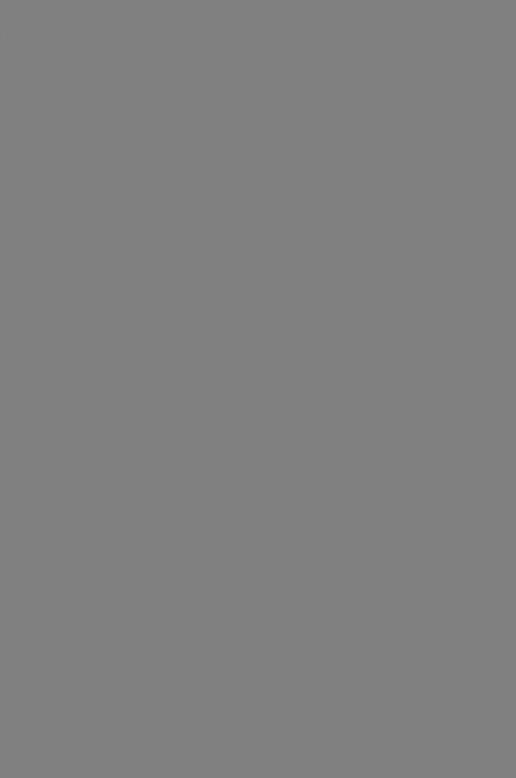
Достоинства подвесных дорог — независимость от рельефа мест ности, возможность полной автоматизации, малая трудоемкость обслуживания; недостатки — относительно небольшая производи тельность, неустойчивость вагонеток при сильных поперечных ветрах, большие капитальные затраты.
Г л а в а 8
ВСПОМОГАТЕЛЬНОЕ ТЕХНОЛОГИЧЕСКОЕ ОБОРУДОВАНИЕ
§ 37. Общие сведения. Назначение оборудования
На эксплуатацию основного технологического оборудова ния для предварительного измельчения породы и ее транспортиро вания значительно влияет предусматриваемое в технологических схемах горного цеха вспомогательное оборудование. К такому оборудованию относят питатели дробилок, устройства для сортиро вания кусков породы по крупности, для удаления из породы метал лических предметов и др.
На рис. 31 показана установка головной щековой дробилки в ком плексе с необходимым вспомогательным оборудованием. Куски породы выгружают в бункер У, перекрытый колосниковой решеткой 2, которая служит для выделения из породы негабаритных кусков. Непровалившиеся через решетку куски удаляют специальным за хватом подъемного устройства 3. Из бункера порода подается пла стинчатым питателем 4 на грохот 6, где происходит разделение кусков на фракции. Крупные куски породы с помощью загрузочного устройства 7 попадают в дробилку 8 и, пройдя стадию дробления, выгружаются на ленточный конвейер 10. Мелкая просыпь породы от пластинчатого питателя через систему бункеров 12, а также мелкие куски из-под грохота через систему бункеров 11 выгружаются на ленточный конвейер. При этом загрузка конвейера первоначально мелкими фракциями породы, а затем более крупными предохраняет ленту от преждевременного изнашивания. Выделяющуюся пыль при грохочении и загрузке породы в дробилку собирают в кожухе загрузочного устройства и отсасывают вентилятором для последу ющего улавливания в фильтрах. Для удаления из породы металли ческих предметов над лентой транспортера установлен мощный электромагнит 9, а для ремонта дробилки — мостовой кран 5.
Расчет и выбор вспомогательного оборудования дробильных Установок ведут с учетом заданной производительности дробилки, Размеров ее приемного отверстия и выходной щели. Например, при максимальном (200 мм) размере кусков породы, получаемых после Дробления, нерационально загружать дробилку кусками породы Размером менее 200 мм. Для этого перед дробилкой предусмотрена технологическая операция разделения с помощью грохочения кусков породЫ по заданной крупности.
Весьма важной операцией, связанной с удалением из породы Металлических предметов, является так называемая магнитная

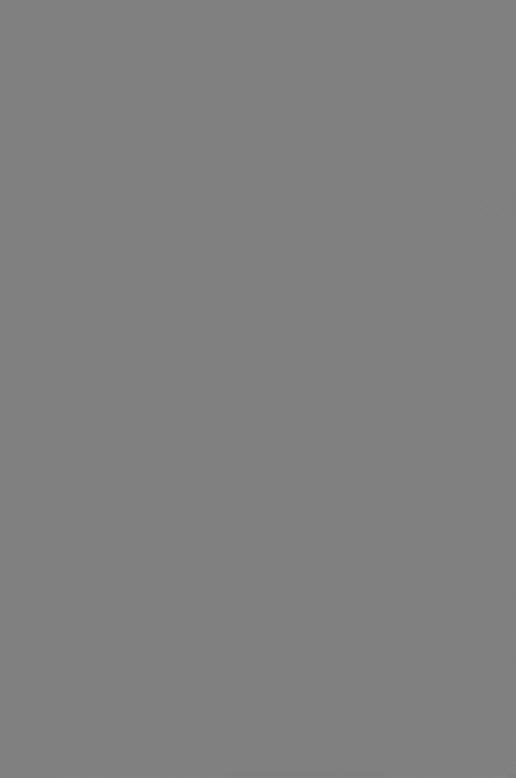
Типоразмеры
питателя
П-С-12-30 П-С-12-45 П-С-12-60 П-С-12-90 П-С-12-120
П-С-15-30 П-С-15-45 П-С-15-60 П-С-15-90 П-С-15-120
П-С-18-60 П-С-18-90 П-С-18-120 П-С-18-150 П-С-18-180
П-С-24-45 П-С-24-60 П-С-24-90 П-С-24-120 П-С-24-150 П-С-24-180
Скорость |
Ширина |
Расстояние |
|
|
между центра |
Масса, т |
|||
питателя, м/с |
полотна, мм |
ми звездочек, |
||
|
|
|
мм |
|
|
_ |
|
3 000 |
17 |
о |
о со |
1200 |
4 500 |
20,5 |
6 000 |
24,5 |
|||
|
Т |
|
9 000 |
32,5 |
|
|
|
||
|
. |
|
12 000 |
39,5 |
|
|
1 |
|
|
|
|
|
3 000 |
18,5 |
0,8-0,25 |
1500 |
4 500 |
22 |
|
6 000 |
30,5 |
|||
|
|
|
9 000 |
40 |
|
|
1 |
12 000 |
48 |
|
|
|
|
|
|
|
|
6 000 |
44,5 |
0,03—0,16 |
1800 |
9 000 |
55,5 |
|
12 000 |
65,5 |
|||
|
|
|
15 000 |
78 |
|
|
|
18 000 |
88 |
|
|
|
4 500 |
46 |
0,08-0,16 |
2400 |
6 000 |
50,5 |
|
9 000 |
67 |
|||
|
|
|
12 000 |
81 |
|
|
|
15 000 |
94 |
|
|
|
18 000 |
105,6 |
перемещающим звездочку 7, и поддерживается роликами 3 и 5. В отдельных конструкциях питателей ролики 12 груженой и хо лостой ветвей перемещаются по полкам рамы. Кроме этого, привод питателя также может осуществляться без промежуточной цепной передачи.
Основными параметрами, определяющими выбор питателей, яв ляются их производительность, ширина, высота бортов полотна
идлина настила.
Втабл. 26 приведена техническая характеристика наиболее
часто используемых в дробильных установках пластинчатых пита телей, выпускаемых заводом «Электростальтяжмаш».
Скорость движения питателя составляет 0,03—0,6 м/с. При более высоких скоростях резко возрастают динамические нагрузки, возникающие вследствие неравномерности движения цепей с круп ными шагом по звездочкам. Пластинчатые питатели позволяют транс портировать сырьевые материалы с наклоном до 30° К их недостат кам можно отнести сложность конструкции и обслуживания вслед ствие большого числа шарниров, высокую стоимость.
Производительность пластинчатых питателей (в т/ч)
П = 3600Fpy, |
(67) |
где F — площадь сечения слоя породы на полотне питателя, м2; р — насыпная плот ность породы, т/м3; v — скорость движения питателя, м/с.
Площадь сечения слоя насыпной породы для питателя с бор тами (в м2)
F = 0,25СБ2 tg (0,4ср) + Bh% |
(68) |
где С — коэффициент, учитывающий изменение площади поперечного сечения груза на наклонном питателе с бортами; В — ширина настила, м; ср — угол естественного
откоса крупнокусковатой породы при |
движении, |
(р = 30°; h — высота борта, м; |
||
ф — коэффициент наполнения настила |
по высоте |
бортов, |
ф = 0,65-г- 0,8. |
|
-Ниже приведены значения коэффициента С. |
|
|||
Угол наклона питателя, |
До |
10 |
10—20 |
Свыше 20 |
Коэффициент С |
|
1 |
0,95 |
0,9 |
При принятой скорости и заданной производительности из фор мулы (67) находят значение Г и, подставляя это значение в формулу (68), определяют ширину настила и высоту борта питателя. Рас считанные размеры в (м) округляют до ближайших стандартных значений: В = 0,4; 0,5; 0,65; 0,8; 1,0; 1,2; 1,4; 1,5; 1,6; 1,8; 2,0; 2,4; h = 0,1; 0,125; 0,165; 0,2; 0,25; 0,32.
Ширину настила дополнительно проверяют на гарантированное
размещение на нем кусков |
породы |
(в м) |
|
В = |
DmaxK + |
0,2, |
(69) |
где Р шах — наибольший размер куска породы, м; К — поправочный коэффициент,
для кусковатой |
несортированной породы К = 1,7. |
|
||
Мощность |
привода питателя (в |
кВт) |
|
|
|
АГ FJL (со cos а ± sin а) |
, |
А АО т |
(70) |
|
N = ----*— 267"^----- |
+ |
0>02соLv cos а, |
где П — производительность питателя, т/ч; L — длина питателя, м; (о — коэффи циент сопротивления движению, со = 0,1; а — угол наклона питателя, °; v — ско рость движения ленты, м/с (знак плюс соответствует подъему транспортируемой породы, знак минус — опусканию породы).
Необходимая мощность электродвигателя (в кВт)
ЛГдв |
= N/л , |
(71) |
где Я — КПД привода, ч = 0.92. |
|
|
Для преодоления инерции |
груженого питателя |
при трогании |
его с места мощность электродвигателя дополнительно увеличивают до 25 % сверх расчетной.
Пример 20. Рассчитать пластинчатый питатель производительностью 450 т/ч Для головной щековой дробилки. Крупность кусков известняка — до 800 мм, насып ная плотность породы 1,4 т/м3. Угол подачи породы вверх 20°, расстояние между
звезДочками 9 м.
решение. Принимаем скорость питателя v = 0,2 м/с. Преобразуя формулу (67),
полупим |
|
|
|
F = |
П |
450 |
= 0,44 м2. |
ЗбООру ~ |
3600-1,4-0,2 |
|
По формуле (68) определяем: |
|
|||
|
F = 0,25 СВ2 tg (0,4ф) -f 5Лф = 0,25-0,95-В2 tg 12° + |
||||
где |
С = 0,95. |
+ |
5/z-0,7 = 0,05Л2 + 0,75Л, |
|
|
0,2В и |
подставляем в полученное уравнение. Получаем |
||||
|
Принимаем h = |
||||
|
0,44 = |
0,0552 + |
0,75-0,25 = 0,1952, откуда |
5 = 1,52 м, |
|
|
|
h =10,25 = 0,2-1,52 = 0,3 м. |
|
||
|
Проверяем ширину полотна питателя на гарантированное размещение на нем |
||||
несортированных кусков породы по формуле (69): |
|
||||
|
|
5 |
= 1,7-0,8+ 0,2 = 1,56 м. |
|
|
|
Это значение немного больше расчетного. |
|
|||
5 = |
Принимаем окончательно ближайшие стандартные размеры полотна питателя: |
||||
1,6 м, Л = 0,32 м. |
|
|
|||
|
По формуле (68) уточняем площадь сечения породы на полотне питателя с учетом |
||||
принятой его ширины и высоты бортов: |
|
||||
|
F = |
0,25-0,95-1,62 tg 12°+ 1,6-0,32-0,7 = |
0,48 м2. |
С учетом уточненной площади сечения слоя породы по формуле (67) определяем рабочую скорость полотна питателя:
П450
V' = ЗбОО Р'р = 3600-0,48-1,4 = 0,186 м/с-
Мощность привода определяем по формуле (70)
N = |
450-9(0,1 cos 20° + sin 20°) |
0,02-0,1-9-0,186 cos 20° = 4,81 кВт. |
|
367 |
|
В скобке принят знак плюс, так как порода транспортируется вверх. Мощность электродвигателя рассчитываем по формуле (71)
/Удв = 4,82/0,92 = 5,23 кВт.
С учетом пуска груженого породой питателя выбираем стандартный электро двигатель мощностью не менее 1,25-5,23 = 6,5 кВт.
§ 39. Неподвижные колосниковые грохоты
Для сортирования загружаемых кусков породы по раз мерам перед загрузкой в головные щековые дробилки служат не подвижные колосниковые грохоты. Они представляют собой раму прямоугольной формы, состоящую из параллельно расположенных и скрепленных между собой с одинаковым зазором колосников (стержней).
Основным параметром решетки является зазор между колосни ками, обеспечивающий задержание на ее поверхности негабаритных кусков породы. Поэтому зазор (в мм) выбирают с учетом типа го ловной дробилки
|
Ь с |
0,85В, |
(72) |
где b — зазор |
между колосниками; |
5 — ширина |
приемного отверстия дрсби^ки> |
мм (см. табл. |
17). |
|
|
Для исключения случаев забивания приемного отверстия дро билок, а также повышения срока службы пластинчатого питателя на практике зазор между колосниками принимают в 2 раза меньше расчетного.