
Механическое оборудование предприятий по производству вяжущих строи
..pdf6 Лоскутов Ю. А. и др.
Показатель
СМЦ-15 |
3,5X27 м |
СМЦ-428.2 |
СМЦ-429.2 |
СМЦ-440.2 |
Размеры барабана, |
м: |
|
5,6 |
3~,5 |
2,8 |
2,8 |
2,2 |
||||
диаметр |
4 |
|
|
||||||||
длина! |
|
|
45 |
27 |
20 |
14 |
14 |
||||
Наклон барабана, % |
подсу |
5 |
4 |
1—4 |
1—4 |
1—4 |
|||||
Производительность |
по |
208 |
100 |
25—30 |
20—25 |
11 |
|||||
шенному материалу, |
т/ч |
|
|
|
|
|
|
|
|||
Влажность материала, |
%: |
17 |
18 |
22 |
20—22 |
22 |
|||||
на входе |
|
|
|
||||||||
на выходе |
барабана, |
8 |
8 |
3 |
1—8 |
3 |
|
||||
Частота |
вращения |
1,2—2,4 |
2; |
3; |
4,2 |
4,68 |
3,12; |
||||
об/мин |
|
кВт |
630 |
4; |
’6 |
75 |
55 |
3,6; |
9 |
||
Мощность привода, |
66; |
100; |
36; 40; |
||||||||
Масса, |
т |
|
|
|
1300 |
140; |
200 |
61,3 |
62,4 |
50; |
75 |
|
|
|
. 450 |
35,0 |
Например, внутренняя полость барабана разделена секторными пе регородками 16, на поверхности которых закреплены швеллеры 18 с приваренными к ним полосами 17 Испарение влаги из сырьевого материала происходит в результате соприкосновения материала с на гретыми металлическими элементами конструкции теплообменника и нагрева от газового потока при пересыпании кусков. Спиральные лопасти 15, установленные внутри барабана со стороны топки 5, служат для ускоренного транспортирования загружаемых сырьевых
материалов |
к |
теплообменнику и предотвращения их |
просыпи в |
шахту топки. |
|
а другой — |
|
Один конец барабана входит в топочную камеру 5, |
|||
в разгрузочную |
камеру 11. Оба конца имеют уплотнения, препят |
||
ствующие |
подсосу наружного холодного воздуха.' |
|
Предназначенный для сушки материал, предварительно дроб ленный до размеров 20—25 мм, с помощью питателя и наклонной течки 4 поступает в полость барабана. В результате наклона и вра щения барабана высушиваемый материал непрерывно перемещается
от места |
загрузки |
к разгрузочному концу. Одновременно с этим |
|
в барабан |
из топки |
поступают газы температурой до 700 °С. Перед |
|
подачей |
в |
сушильный барабан газы разбавляют наружным холод |
ным воздухом. Соприкасаясь с перемещающимся в барабане матери алом, газы нагревают и высушивают материал. Охлажденные д0 80—120 °С дымовые газы отсасываются из полости барабана через патрубок верхней части разгрузочной камеры 11 с помощью венти лятора.
Односторонний привод, которым оснащен сушильный барабан состоит из электродвигателя 10, редуктора 9, подвенцового зубча того колеса 7 и тормоза 8. На сушильных барабанах отдельных
162
|
|
|
К |
|
Вид теплообменника |
т |
при пря |
при про |
б |
|
|
мотоке |
тивотоке |
|
Лопастной или навеска цепей |
0,5 |
0,2—0,7 |
0,5—0,7 |
0,04—0,07 |
Ячейково-сепараторный |
1 |
0,7—1,2 |
1,2—2 |
0,01—0,02 |
типов кроме главного привода предусмотрен вспомогательный, пред назначенный для проведения ремонтных работ.
Для смазывания редуктора и подшипников качения подвенцового зубчатого колеса предусмотрена отдельная станция жидкого смазы вания. Смазочный материал для смазывания зацепления зубчатого венца и подвенцового зубчатого колеса — жидкий, от станции перио дической смены масла.
Техническая характеристика сушильных барабанов приведена в табл. 31.
Выбор параметров сушильных барабанов и режимов их работы зависит от физических свойств породы, главным образом от ее на чальной влажности и размеров кусков. Чем выше начальная влаж ность и мельче куски, тем интенсивнее протекает испарение влаги.
Частоту вращения барабана п (в об/мин), время прохождения
через него породы т (в мин) в необходимую мощность |
привода N |
|||||
(в кВт) для вращения барабана определяют по формулам: |
||||||
|
mKL |
. |
(83) |
|
120Pp ((■)„ — <ом) . |
(84) |
|
TD tg а |
’ |
А [200 - (сос - шм)] ’ |
|||
|
|
|
||||
|
|
|
N = 0,0013D3Lprt6, |
(85) |
||
где т, |
К и б — коэффициенты, |
учитывающие |
условия теплообмена |
в барабане |
||
(табл. |
32); D, |
L — диаметр и длина барабана, |
м; а — угол наклона |
барабана, °; |
Р — коэффициент заполнения барабана в долях единицы, (3 = 0,1-ь0,25; р —сред няя насыпная плотность материала, кг/м3; А — паросъем, кг/(м3/ч); сос и сом — влаж ность сырья и высушенного материала, %.
Производительность сушильного барабана оценивают по выходу влаги Пт и по выходу высушенного материала Я:
В практике нормирующим показателем работы сушильных ба
рабанов |
является |
паросъем Л, |
для глины А = 50-f-60 кг/(м3-ч) |
и для |
известняка |
А = 45—65 |
кг/(м3-ч). |
При заданном значении паросъема может быть определен рабочий
объем сушильного барабана |
(в м3): |
|
V - |
3 m n w/A. |
(87) |
Нормируемые размеры и параметры сушильных барабанов при ведены в табл. 33.
Т а б л и ц а 33. Типоразмеры и частота вращения сушильных барабанов (по Д. Я. Мазурову)
Рабочий |
Размеры |
Частота |
Рабочий |
Размеры |
Частота |
|
объем |
барабана, м |
вращения |
объем |
барабана, м |
вращения |
|
бараба |
|
барабана, |
бараба |
|
|
барабана, |
на, м3 |
диаметр длина |
об/мин |
на, ма |
диаметр |
длина |
об/мин |
|
|
|
|
20 |
1,6 |
10 |
3,2—6,4 |
177 |
3,2 |
22 |
2— 6 |
38 |
2 |
12 |
3,2—6,4 |
259 |
3,5 |
27 |
2—6 |
53 |
2,2 |
14 |
3,2—6,4 |
352 |
4 |
28 |
2—6 |
88 |
2,5 |
18 |
2 - 6 |
556 |
4,5 |
35 |
2— 6 |
123 |
2,8 |
20 |
2— 6 |
686 |
5 |
35 |
2—6 |
141 |
3 |
20 |
2—6 |
|
|
|
|
Пример 24. Определить требуемые размеры сушильного барабана для сушки известняка в объеме Q = 240 т/ч по высушенной массе. Начальная влажность извест няка 15%, конечная 5% . Теплообменники прямоточного барабана лопастные.
Средняя насыпная плотность |
известняка р = |
1400 кг/м3. |
влажностью |
|||
Решение. Производительность |
барабана |
по |
выходу известняка с |
|||
5 % составит |
|
|
|
|
|
|
Q1000 |
“ |
240-1000 |
= 66,6 кг/с. |
|
||
/У~~ |
3600 |
3600 |
|
|
|
|
Производительность по |
выходу |
влаги |
определяем по формуле |
(86) |
п “ •« (тоо^тт - - Ш = г ) “ ■
Принимаем предварительно съем пара сушильного барабана А = 50 кг/(м3-ч). Тогда объем сушильного барабана по формуле (87) должен быть
V - 2 “ «£® _594 »..
о0
По данным табл. 33 выбираем барабан рабочим объемом 686 м3 с параметрами: D = 5 м, L = 35 м. Принимаем коэффициент заполнения барабана Р = 0,2. Тогда по формуле (84) время прохождения известняка через сушильный барабан
х = |
120-0,2-1400(15 — 5) |
= 37,3 мин. |
|
50 [200 — (15 — 5)] |
|
По данным табл. 32 |
принимаем значения |
коэффициентов: т = 0,5; К = 0,7; |
б = 0,04, а по данным табл. 33 п = |
2 об/мин. Тогда угол наклона барабана по фоп- |
муле (83) |
р |
О 5-0 7*35 |
|
tg а = —^ 3 7 ’з |- |
= 0,03234, отсюда а = 2°. |
Необходимая мощность привода сушильного барабана по формуле (85)
N= 0,0013-58-35-1400-2-0,04 = 637 кВт.
§61. Вихревые сушилки
Вихревые сушилки (рис. 70) в отличие от сушильных бара банов представляют собой неподвижный воздухонепроницаемый цилиндр с круговым или эллиптическим сечением. В нижней части
164
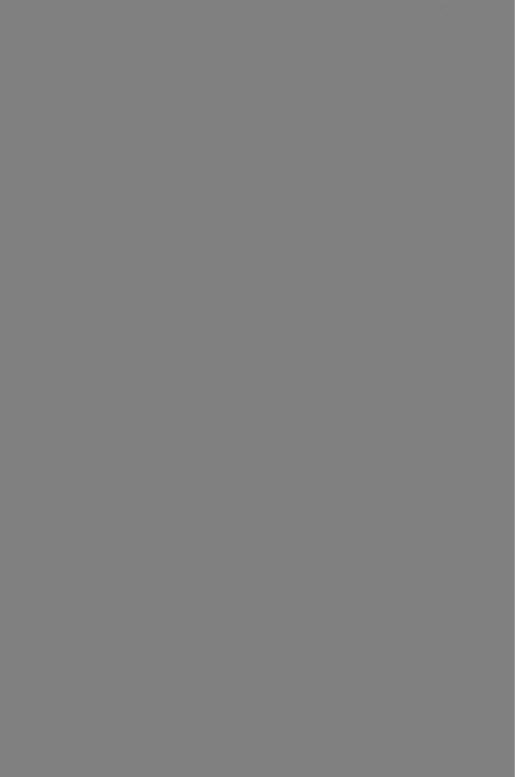
Г л а в а 14
ВСПОМОГАТЕЛЬНОЕ ТЕХНОЛОГИЧЕСКОЕ ОБОРУДОВАНИЕ
§62. Общие сведения
Всырьевых цехах действуют следующие виды вспомо гательного технологического оборудования: сушильное; для усред нения и хранения сырьевых смесей; для питания и дозирования по мольных агрегатов; аспирационное и обеспыливающее; тягодутье вое (вентиляторы, дымососы, воздуходувки); транспортирующее и др.
Для транспортирования сухих сыпучих материалов (цемента, сырьевой муки, добавок при помоле клинкера) применяют различные виды механического и пневматического транспорта. К механическим видам транспорта относят шнековые конвейеры и элеваторы, к пне
вматическим — пневмокамерные и пневмовинтовые насосы, пневмо подъемники , аэрожелоба.
Вид транспортирующего оборудования выбирают отдельно в ка ждом конкретном случае с учетом дальности и высоты подачи ма териала, компоновки оборудования в цехе, требований к надежности и экономичности.
Пневмовинтовые насосы обычно применяют при дальности подачи до 430 м, пневмокамерные — до 1000 м, аэрожелоба — до 100 м, шнековые конвейеры — до 40 м. Высота подачи пневмоподъемниками обычно не превышает 90 м, элеваторами — 80 м.
§ 63. Шнековые конвейеры
Шнековые конвейеры широко используют в сырьевых цехах, а также в других технологических переделах при горизон тальном и наклонном транспортировании сыпучих сырьевых Мате риалов.
Шнековый конвейер (рис. 71) представляет собой желоб 1 с Полуцилиндрическим днищем, внутри которого в подшипниках распо ложен вращающийся шнек (винт) 5. Вращение винта осуществдяют от электродвигателя 8 через редуктор 10, концы валов которых сое динены муфтами 9 и 11. Движение материала вдоль желоба проис ходит вследствие проталкивания его витками шнека.
Желоб по всей длине закрыт крышкой. Загрузку конвейера осуществляют через люк 3, для разгрузки предусмотрен один ИЛ1, несколько закрывающихся люков 6 и 7 Для их чистки на крыШКе желоба расположены лючки 12. Шнек состоит из трубы с приварен ными с определенным шагом перьями винта из листовой стали. Шнек вращается в подшипниковых узлах 4, расположенных сиа. ружи желоба.
Для предотвращения прогиба шнека на определенном расстоЯии11 его вал закрепляют на подвесных опорах 2 со сферическими самоуста. навливающимися подшипниками качения. Эти опоры должны ..Иметь небольшие размеры, так как в месте их установки витки шнека Црер-
&аны и, кроме того, они создают препят ствие транспортируемому материалу. Под шипниковые узлы подвесных опор тщательно загерметизированы от попадания пыли, и подшипники систематически смазываются густым смазочным материалом от колпачко вой масленки через трубку. Для восприятия осевых усилий винта шнека в одной из крайних его опор предусмотрена установка упорного подшипника.
Кнедостаткам шнековых конвейеров
относятся повышенный износ винта шнека и нижней части желоба, склонность к за торам материала у подвесных опор шнека. В связи с этим шнековые конвейеры приме няют при подаче не более 100 м3/ч и рас стоянии транспортирования не более 40 м. Расстояние между подшипниковыми узлами шнека должно быть не более 3,5 м. По ГОСТам
наружный диаметр |
винта равен |
|
100, 125, |
||||||
160, |
200, |
250, |
320, |
400, |
500, |
650, |
800 |
мм. |
|
Диаметр |
винта должен |
быть |
не |
менее чем |
|||||
в 12 раз больше размера |
транспортируемых |
||||||||
кусков при |
сортированном |
материале |
и |
||||||
в 4 |
раза |
больше |
наибольшего |
куска |
при |
рядовом материале. Шаг винта S (в м) устанавливают в зависимости от свойств
транспортируемого материала: |
|
|
|
||||||||
|
для |
зерновых |
и сыпучих материалов |
||||||||
|
|
|
S - |
(0,7-М) |
D, |
|
|
|
(88) |
||
|
для |
крупнокусковых |
абразивных |
мате |
|||||||
риалов |
|
|
|
|
|
|
|
|
|
|
|
|
|
|
S = |
(0,5-г-0,7) D, |
|
|
(89) |
||||
где D — диаметр шнека, |
м. |
|
|
|
|
|
|
||||
и |
.Между наружной кромкой витков шнека |
||||||||||
желобом |
должен |
быть |
зазор |
не |
менее |
||||||
5 |
мм |
при сыпучем |
или мелком материале и |
||||||||
до 10 мм — при крупных кусках. |
|
|
|||||||||
|
Производительность |
шнека |
(в кг/ч) |
||||||||
|
|
|
Я = 60 |
|
Sn#C , |
|
(90) |
||||
где п — частота вращения |
шнека, |
об/мин; |
ф — ко |
||||||||
эффициент наполнения желоба |
(табл. 34); |
р — насып |
|||||||||
ная плотность |
материала, |
кг/м:*; |
|
С — поправочный |
|||||||
коэффициент, |
зависящий от угла |
наклона |
конвейера. |
Рис. 71. Шнековый конвейер
Материал |
4> |
об/мин |
Легкий, мелкий, неабразивный (например, сырьевая мука) |
0,4 |
80-140 |
Неабразивный или полуабразивный (сырьевая крупка, |
0,3 |
65-100 |
цемент) |
0,125 |
40 -70 |
Силыюабразивиый (клинкер) |
Ниже приведены значения коэффициента С.
Угол наклона конвейера вверх Р, ° |
|
О |
Скорость транспортирования |
(в м/с) |
|
и = |
Sn/60, |
(91) |
Мощность (в кВт), необходимая для вращения шнека при транс портировании материала
<9 2 >
где Н — высота транспортирования материала, м; L — расстояние между осями загрузочного н разгрузочного люков, в расчетах L можно принимать равной длине
шнека; ш0 — коэффициент сопротивления транспортированию материала.
Ниже приведены значения со0.
Транспортируемый материал; легкий неабраэивный легкий малоабразивный тяжелый малоабразивный . тяжелый абразивный
Мощность (в кВт) электродвигателя привода шнекового кон вейера
|
(93) |
где ц — КПД редуктора, ч = 0,8. |
|
Крутящий момент на валу шнека (в Н-м) |
|
Мнр = 9550 N/n, |
(94) |
а осевое усилие на валу шнека (в Н) |
|
Р = 2MHP/[KD tg (o + ф)1, |
(95) |
где К — коэффициент нагрузки, К = 0,7-т-0,8; а — угол подъема винтовой линии шнека (на радиусе г = KD/2), °; <р — угол трения материала о поверхность виткои
шнека, °
Угол подъема винтовой линии шнека
tg а = Szl(KnD), |
(96) |
где г — число заходов винта шнека, z = 3.
168
Угол (р трения находят из равенства tg ф = ц, где р. — коэф фициент трения материала о поверхность винта.
Транспортируем |
й материал |
Сухая |
Каменный |
Цемент |
р |
|
зола |
уголь |
0,65 |
|
0,84 |
' 1 |
||
Пример 25. |
Рассчитать шнековый конвейер для горизонтального транспортиро |
вания сырьевой абразивной крупки от сепаратора в течке сырьевой мельницы. Подача конвейера 50 т/ч, расстояние между загрузочным и разгрузочным люками
конвейера 15 м. Насыпная |
плотность крупки р = 1300 кг/м3. |
0,3 и п = |
80 об/мин; |
|||
Решение. Поданным табл. 34 принимаем предварительно^ = |
||||||
С = 1. С учетом формулы |
(88) |
принимаем S = 0.8D. |
|
|
||
При заданной |
производительности по формуле (90) определим требуемый диа |
|||||
метр шнека |
|
|
|
яD'i |
|
|
|
50 000 = |
60 |
|
|
||
|
— 0.8D •80 ■0,3 ■1 ■1300, |
|
|
|||
откуда D3 = 0,042 |
или D = |
|
|
Принимаем стандартный |
размер |
D = |
Тогда шаг шнека |
|
|
|
|
|
|
|
S = |
0,8D = 0,8 0,4 = 0,32 м. |
|
|
||
С учетом выбранных параметров шнека по формуле (90) уточняем частоту |
||||||
его вращения: |
|
|
|
|
|
|
|
50000 = |
|
60 |
3,1* ° '4а0,32л-0,3-1 ■1300. |
|
|
Отсюда п = 52,1 об/мин. |
сопротивления транспортированию |
|
||||
Принимаем коэффициент |
|
Необходимая мощность для вращения шнека по формуле (92) 3,27 кВт.
Принимая КПД привода т) = 0,8, по формуле (93) находим и ность электродвигателя привода:
N = 3,27/0,8 = 4,1 кВт.
По каталогу выбираем ближайший серийный электродвигатель в пылезащитном исполнении мощностью, равной или превышающей расчетную. С учетом частоты вращения вала выбранного электродвигателя и необходимой частоты вращения шнекового конвейера по передаточному числу подбираем серийный редуктор. При этом крутящий момент на выходном валу редуктора должен быть нс ниже, чем тре буемый для транспортирования материала на валу шпека, который определяем по формуле (94)
/И„р = 955-4,1/52,1 = 751.1Н-М.
Для определения осевого усилия на валу шнека по формуле (95) п выбора соответствующего упорного подшипника зададимся значениями /( = 0,7, г = 1, 11 = 0,65. Тогда tgтф= 0,65 н q> = 33°. По формуле (96) определяем
« л - * * ■
2-751,5
4045,1
~ 0,7 0,4 tg 53°
Основным технологическим транспортом цементных за водов при вертикальном перемещении сыпучих материалов на высоту до 30 м н более являются ковшовые элеваторы. Широкое использо
вание |
они нашли в схемах двухстадийного помола сырья и цемен |
та при |
подаче грубомолотых сырьевых материалов на сепарацию в |
специальные устройства, смонтированные, как правило, над по мольным оборудованием.
Ковшовые элеваторы (рис. 72) состоят из замкнутого тягового органа. I с жестко укрепленными на нем грузонесущими элемен тами — ковшами 2. Тяговый орган огибает приводной II и натяж ной 10 барабаны (или звездочки) и размещается в ограждающем составном металлическом кожухе 6 с направляющими. На нижней части кожуха — загрузочном башмаке 5 — смонтировано натяжное устройство 4. Привод приводного барабана состоит из электродви гателя 9 и редуктора 8. Материал загружается в ковши через те чку 3 и разгружается через течку 7 после опрокидывания ковшей при их огибании приводного барабана или звездочек.