
Механическое оборудование предприятий по производству вяжущих строи
..pdfРис. 109. Гидроупор
на раме 5 с межцентровым расстоянием, обеспечивающим одинаковый зазор а между роликами и бандажом исполнения 2 в пределах 20—
60мм.
Работа контрольных роликов заключается в следующем. Корпус
печи при вращении постепенно смещается вниз, к разгрузочному концу до соприкосновения бандажа с роликом, что вызывает его вращение. Это является сигналом о достижении максимально до пустимого смещения корпуса печи и для принятия мер для возврата корпуса печи в нейтральное положение. Для контроля положения корпуса печи при его подъеме вверх служит верхний контрольный ролик, установленный с другой стороны бандажа.
Для восприятия усилия горизонтальной составляющей от массы печи, а также для обеспечения периодических осевых перемещений корпуса в целях создания равномерного изнашивания рабочих поверхностей роликов и бандажей по всей их ширине применяют гпдроупоры. На печи в зависимости от ее длины установлены три — пять гидроупоров с общей насосной станцией.
Гидроупор (рис. 109) включает в себя упорный ролик 3, напрессо ванный на ось 5, вращающуюся в подшипниках — двухрядных сферических 4 и 10 и упорных 9. Подшипники смонтированы в кор пусе 2. Корпус под давлением масла, подаваемого под поршень 6 в гильзе 7, перемещается по двум цилиндрическим направляющим /, закрепленным в стойках 11 станины 8.
Управление работой гидроупоров осуществляется автоматически или вручную с пульта машиниста. Использование гидроупоров позволяет не только контролировать положение корпуса печи, но и управлять скоростью его движения как вниз под действием усилия, так и вверх с помощью гидроцилиндров.
Для снижения изгибающих сил, действующих на вертикальный вал гндроупОра, его ролик выполняют конусным, работающим в кон такте со скошенным торцом бандажа исполнения 2. Система гидро
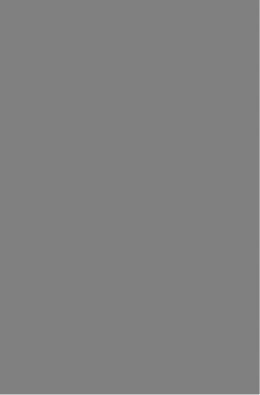
к опорными роликами, равная F = )Р, где / — коэффициент трения между бандажами и роликами (в сухом состоянии), / = 0,15-;-0,2.
Выразив силу Т и силу F |
через G (при р = 4 %, а = |
30°): |
Т = |
G sin р = 0.04G; |
(134) |
F = \Р |
= /Geos р = 0.17G. |
(135) |
можно увидеть, что сила F более чем в 4 раза больше силы Т Однако сползание печи не происходит только при ее остановке, при враще нии бандажи «перекатываются» по роликам и печь сползает вниз. При расчетах упорных роликов влияние силы F не учитывают, что повышает надежность работы гидроупоров.
IПосле определения нормального давления Рп проверяют кон тактную прочность рабочей поверхности упорного ролика (в МПа)
р, = 0,418 ] Л " £ ^ " + Ги), |
(136) |
где £ — модуль упругости. £ = 2,02-105 МПа; R„ — радиус нормальной |
поверх |
ности качения бандажа по ролику, м; г„ — радиус нормальной поверхности качения
ролика, м; Г — длина липни касания бандажа и ролика, м.
Значения /, R„, г„ находят из соотношений.
Пример 31. Проверить контактную прочность рабочей поверхности упорного
ролика. Вес |
вращающейся |
печи, приходящийся |
па опору |
(реакция |
опоры) Р — |
|||||||
= 8,09 МН; максимальное усилие гндроцнлнндра |
Ргц = |
1,12 МН; диаметра |
бан |
|||||||||
дажа D = 6,8 м; |
максимальный диаметр |
ролика г = 1,2 м; |
высота ролика |
Лр = |
||||||||
= 0,21 м; угол конусности |
упорного ролика у = 10°; |
материал ролика и бан |
||||||||||
дажа — сталь ЗОГСЛ; твердость рабочих |
поверхностей |
НВ > |
197, |
уклон |
печи |
|||||||
4 % (2° 10'). |
|
|
|
|
|
|
|
|
|
|
|
|
Решение. По формуле (134) определяем составляющую Т |
|
|
|
|
||||||||
|
|
|
Т .-= 8,09-0,04 = |
0,32 МН. |
|
|
|
|
|
|
||
Нормальную |
составляющую, действующую |
на ролик, |
находим по формуле |
|||||||||
|
|
|
Р„ = 0,32/0,985 = |
0,324 МН. |
|
|
|
|
|
|
||
Для определения максимального контактного давленн |
|
|
|
|
|
|||||||
определяем |
составляющие |
этой формулы; |
|
|
|
|
|
|
|
|
||
|
|
/ = |
/ip/cos у = 0,21/0,985 — |
|
|
|
|
|
|
|||
и = |
ЯСр. yn/sin У (гДе Pep. уп = Р |
|
(Лр/2) = |
|
|
|
|
|
|
|||
„ = 3,295/0,173= 19,04 м; |
|
|
|
|
|
|
|
|
|
|||
|
г„ = Яср. уп tg Y/cos у = 3,295-0,176/0,085 = |
0,59 |
м. |
|
|
|||||||
Определяем максимальное контактное давление от силы Р„, |
|
|
|
|||||||||
тельное время, по формуле (136): |
|
|
|
|
|
|
|
|
|
|||
|
. |
____ Т /0,324-2,02-10» (19,04 -f-0,59) |
|
|
|
иГ1_ |
|
|
||||
|
f>0 = |
°-4 l 8 |/ |
--------- 0,213-19,04-0,59------------ |
306 МПа. |
|
|
Для определения максимального контактного давления от кратковременного действия силы Р2, возникающей при максимальном усилии гидроцилиндра Ргп
1,12 МН, находим нормальную составляющую
|
|
л .= |
Рги |
1,12 |
1,14 МН. |
|
|
|
cos у |
~~ 0,985 |
|
||
Отсюда |
|
12-2,02-105 (19,04 + 0,59) = |
|
|||
|
Ро = |
0,418 |
569 МПа. |
|||
|
|
|
0,213-19,04-0759 |
|
||
Условие прочности для |
кратковременного |
действия |
усилия РГц — 1,12 МН |
|||
также |
выполняется. |
|
|
|
|
|
|
§ 85. Внутрипечные теплообменные устройства |
|||||
25 % |
При работе печных агрегатов мокрого способа в среднем |
|||||
теплоты, |
расходуемой |
на производство |
клинкера, уносится |
|||
с отходящими |
печными |
газами. |
|
|
При мокром способе имеется реальная возможность сокращения потерь тепла, снижения температуры отходящих газов до мини мально возможной, которая определяется устойчивостью работы пылеулавливающих устройств (при значительном снижении темпе ратуры печных газов может наступить точка росы в корпусе электро фильтра, т. е. возможна потеря его работоспособности) путем при менения следующих теплообменных устройств: цепных завес, тепло обменников.
Кроме основной задачи — снижения расхода теплоты — внутри печные теплообменные устройства позволяют решать ряд других задач (уменьшение толщины материала, усиливание перемешивания материала, снижение уноса пыли с отходящими газами), позволя ющих улучшать работу и повышать производительность печных агрегатов.
Цепные завесы обеспечивают наиболее эффективный теплообмен между газовым потоком и материалом во вращающихся печах. Длина цепной завесы определяется размерами печи и колеблется от 18 (для печей длиной 100 м) до 52 м (для печей длиной 185 м). Длину цепной завесы рассчитывают так, чтобы шлам выходил из цепной зоны в виде гранул влажностью не ниже 4—8 %. Конструк ция цепной завесы должна способствовать хорошей грануляции. Недостаточная поверхность цепей в цепной зоне приводит к пере увлажнению материала, выходящего из этой зоны, что вызывает перерасход теплоты на обжиг и снижает производительность печи. При излишней поверхности цепей в цепной зоне шлам пересуши вается, что приводит к разрушению гранул цепями и повышению уноса пыли и сырья с отходящими газами.
Цепи применяют с круглыми и овальными звеньями из Прутковой стали диаметром 20—25 мм. Общая длина цепей в современных длинных печах составляет 2000 м и более, а площадь поверхности — более 2000 м2.
Во вращающихся печах применяют различные схемы навески цепей. Свободповисящие цепи навешивают за один конец, навеску
234
гирляндами образуют при креплении цепи к корпусу за два конца по винтовой линии. При навеске свободновисящими концами по окружности подвешивают до 40 цепей, длина каждой цепи составляет 0,6—0,7 внутреннего диаметра печи по футеровке (в свету), шаг подвески — 250 мм. При навеске гирляндами цепи подвешивают с расстоянием между точками подвески цепи, равным 0,5—0,6 диаметра печи в свету. Точки подвески цепи смещены по окружности, в результате чего один конец цепи поднимается раньше, чем другой. Такое расположение цепей способствует продвижению материала. Длина каждой гирляндной цепи равна 1,2—1,3 диаметра печи.
Цепи крепят к корпусу печи с помощью кронштейна и кольцевых секторов. Элементы крепления должны обладать минимальным сопротивлением движению шлама и быть надежными, исключа ющими возможность обрыва цепей. Во время эксплуатации печей необходимо, чтобы температура газов перед цепями поднималась не выше допустимой, так как это может привести к разрушению цепной завесы. Сварные звенья для цепей изготовляются из стали СтЗ для навешивания в холодной зоне (до 500 °С) и из стали Х18Н10Т для навешивания в горячей зоне (до 1000 °С) цепной завесы.
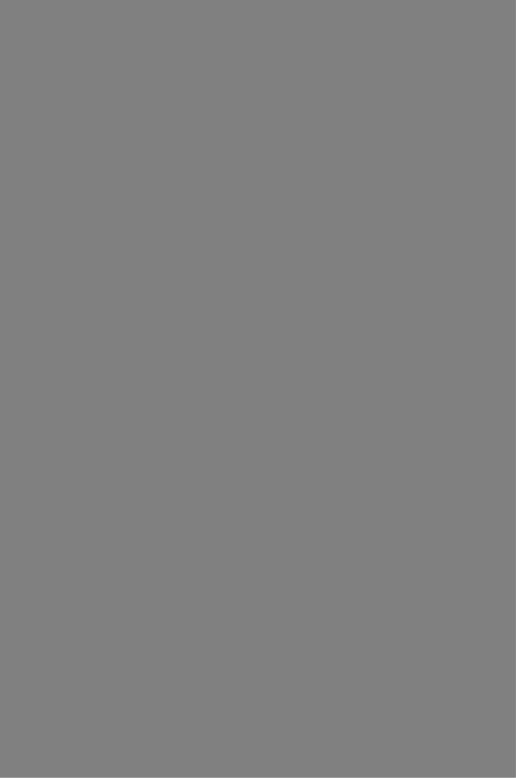
Рис. 113. Крепления зубчатых венцов:
а — шарнирное; б — тангенциальное
элементом привода, так как они обеспечивают компенсацию раз личного рода погрешностей изготовления, сборки и монтажа. Кроме указанного соединения с шарнирно-рычажными муфтами, которыми оснащаются приводы новых печей, в приводах вращаю щихся печей применяют также соединения с зубчатыми муфтами, шпиндельные соединения и др.
Открытая зубчатая передача, состоящая из подвенцовой ше стерни 11 и зубчатого венца, передает вращение корпусу печи. К креплению зубчатого венца на корпусе печи предъявляются особые требования: высокая точность установки, допускающая лишь не значительные радиальные и торцовые биения; надежность крепления и способность компенсировать деформации обечаек, возникающие во время работы. На современных вращающихся печах нашли широ кое распространение два типа крепления: шарнирное и танген циальное.
Шарнирное крепление зубчатого венца (рис. ИЗ, а) заключается в следующем. К корпусу 3 вращающейся печи приваривают пла стины 2У к которым при монтаже, в свою очередь, приваривают кронштейны 1. К ним с помощью болтов 5 крепят щеки 8. Другим концом щеки закрепляют с помощью пальцев на зубчатом венце 4. Окончательное регулирование зубчатого венца осуществляют с помощью клиновых втулок 6Узатягивающихся после регулирова ния. К недостаткам данной конструкции относят громоздкость кон струкции, сложность и необходимость частого регулирования в про цессе работы.

Тангенциальное крепление (рис. 113,6) значительно проще по конструкции, менее металлоемко, но при таком креплении отсут ствует возможность регулирования венца после монтажа. Крепление состоит из тангенциальных пластин 2 с приваренными щеками 5. Пластины приваривают к обечайке корпуса печи, а щеки закрепляют на венце 1 с помощью пальцев 4.
Вспомогательный привод содержит асинхронный двигатель 9 (см. рис. 112), двухступенчатый цилиндрический редуктор 5, коло дочный тормоз 10 с управлением от электрогидравлического толка теля. Тихоходный вал вспомогательного редуктора с главным со единяется через храповую предохранительную муфту 4 свободного хода, которая позволяет осуществить медленную остановку и пуск печи со вспомогательного привода, а также автоматическое управле ние приводом с пульта управления машиниста.
Микропривод состоит из |
электродвигателя 8 постоянного тока |
и клиноременной передачи 7 |
При эксплуатации печи микропривод |
отсоединяется от вспомогательного привода.
Для редуктора привода применяют циркуляционное смазывание жидким смазочным материалом от индивидуальных смазочных стан ций; для передачи зубчатый венец — подвенцовая шестерня — периодическое смазывание жидким смазочным материалом от инди видуальной станции.
В том случае, если привод проектируемых вращающихся печей получается слишком громоздким, применяют двусторонний привод,
представляющий собой |
два одинаковых |
односторонних при |
вода (рис. 114). |
|
|
Зубчатые венцы изготовляют литыми из стали 35ХМЛ, а под- |
||
венцовые шестерни — из |
поковок из стали |
34ХН1МА. |
Характеристика приводов вращающихся печей некоторых типо
размеров приведена в табл. 52.
Мощность привода (в кВт), необходимая для вращения печи,
N = NTP+ N M; |
(137) |
NrV = Np+ Ne, |
(138) |
где /VTp — мощность, затрачиваемая на преодоление сил трения; |
— мощность, |
затрачиваемая на преодоление сил трения в радиальных подшипниках опорных ро ликов; — мощность, затрачиваемая на преодоление сил трения качения бандажей по опорным роликам; N M — мощность, затрачиваемая на перемешивание материала.
Мощность, затрачиваемая на преодоление сил трения в радиаль
ных подшипниках опорных роликов (в кВт) |
|
|
|
N p = 1,19/Яц/г V |
G-jj*-, |
(139) |
|
Л** |
|
Р |
|
=1 |
|
|
|
где / — коэффициент трения для конических подшипников, f — 0,008; /?ц |
радиус |
Цапф опорных роликов, м; п — частота вращения печи, об/мин; G — вес печи с уче
том веса обжигаемого материала, кИ; k — число бандажей; i номер бандажей,
/' -I, .,Д\
