
Хлопковая целлюлоза
..pdfНесколько иной принцип работы имеют шаровые вращающиеся варочные котлы объемом 13,7 м3 (рис. 55), обеспечивающие равно мерный провар массы и легкую разгрузку. Такой котел имеет полые цапфы, через которые и подаются рабочий раствор и пар. Линт за гружают в котел при неподвижном его положении через люк диа метром 700 мм, закрываемый плотно прилегаемой крышкой на бол тах. Котел снабжен червячно-шестеренчатой передачей, с помощью которой от мотора мощностью 3,7 кВт/ч он вращается со скоростью 1—2 оборота в 5 мин. Бученую целлюлозу после спуска давления и снятия крышки выгружают постепенно при вращении котла за 5—6 оборотов в расположенную под котлом емкость или транспортер.
Шаровые варочные котлы применяют |
|
|
|||||
при варке тряпок, соломы, котонина, про |
|
|
|||||
верены они и для варки хлопковой целлю |
|
|
|||||
лозы в объеме 2—3 тыс. т в год. Недостат |
|
|
|||||
ком этих |
котлов является |
сравнительно |
|
|
|||
малая |
их загрузка (1200—1400 кг) при |
|
|
||||
больших |
габаритных размерах. В то же |
|
|
||||
время увеличение их объемов усложняло |
|
|
|||||
их конструкции и значительно удорожало |
|
|
|||||
стоимость оборудования. |
|
|
|
|
|||
С увеличением потребности в хлопко |
|
|
|||||
вой целлюлозе и, следовательно, расшире |
|
|
|||||
нием объемов ее производства и по этой |
|
|
|||||
причине |
строительством |
специализиро |
|
|
|||
ванных |
цехов на основе |
|
опыта работы |
|
|
||
целлюлозно-бумажной |
промышленности |
|
|
||||
были |
запроектированы, |
изготовлены и |
|
|
|||
проверены специальные вертикальные ва |
|
|
|||||
рочные котлы (рис. 56). |
|
|
|
|
|||
Эти котлы представляют собой метал |
|
|
|||||
лическую сварную емкость, состоящую из |
Рис |
56. Варочный котел |
|||||
цилиндрической и конической частей; ци |
|||||||
|
с выдувкой: |
||||||
линдрическая часть (верхняя) заканчива |
|
1 — барботер; |
|||||
ется |
горловиной с плотно |
закрываемой |
|
2 — ложное дно |
крышкой, через которую загружают линт; в нижней конической части котла имеется дырчатое ложное днище,
состоящее из 20 секций, из-под которого выбирают щелочь при цир куляции.
После окончания процесса варки массу выгружают методом вы дувки остаточным давлением 3,5—4 кгс/см2.
Первые варочные котлы с выдувкой были рассчитаны на загруз ку 1,5—2 т хлопкового линта, в последующем объем котлов был не сколько увеличен и загрузка котла доведена до 2,1—2,3 т.
Дальнейшее увеличение объемов варочных котлов при сущест вующих методах подачи и циркуляции щелочи ухудшало качество провара и, следовательно, приводило к колебаниям вязкости бученой массы.
По этой причине работы по увеличению размеров частных пар тий хлопковой целлюлозы должны быть направлены на создание не прерывного технологического процесса изготовления хлопковой цел люлозы, о чем будет сказано ниже.
В настоящее время применяется несколько типов варочных кот лов с выдувкой.
Модуль варки колеблется от 1:8 до 1:11.
Горловина варочного котла, приспособленная для выдувки сва ренной целлюлозы, показана на рис. 57, где 1— штуцер для закачки' варочной жидкости, 2 — штуцеры для пара. Выпуск массы происхо дит при открытии шибера 3, после чего содержимое котла направля ется по трубе 4 в сцежу или сдувочный циклон.
Рис. 57. Горловина варочного котла для выдувки целлю
|
лозы: |
|
|
|
1 — штуцер для закачки варочной жидкости; 2 — шту- |
|
|||
церы для пара; |
3 — шиберы; |
4 — труба |
сдувочного |
|
|
циклона |
|
|
|
Техническая характеристика варочных котлов с выдувкой |
|
|||
|
|
|
Типы |
|
|
|
1-й |
2-й |
3»-й |
Диаметр цилиндрической части, |
мм |
2600 |
2600 |
2400 |
Высота цилиндрической части, мм |
3200 |
3900 |
2400 |
|
Высота конической части, мм |
|
1900 |
2100 |
2200 |
Полный объем, м3 |
|
22,7 |
24*7 |
[16,5 |
Рабочий объем, м3 |
|
20,6 |
22,5 |
15 |
Загрузка линта, т |
|
1,8—2,0 |
2,1-2,3 |
1,3 |
Общий объем заливаемой щелочи, м3 |
20,6 |
22,5 |
15 |
По методу подогрева раствора варочные котлы делят на две группы: котлы с подогревом раст вора в трубчатом аппарате-подо гревателе и котлы, работающие с подогревом массы острым паром.
Цех хлопковой целлюлозы по требляет большое количество па ра на операции варки, и поэтому вопрос о наиболее целесообраз ном использовании пара и мини мальном его расходе должен при ниматься в расчет при выборе той или иной системы котлов.
В котлах с подогревателем ра створ едкого натра нагревают в трубчатом аппарате (подогрева теле), находящемся отдельно от варочного котла.
Подогревательная колонка (рис. 58) представляет собой вер тикальный цилиндрический же лезный аппарат с двумя решетча тыми ложными днищами, соеди ненными набором трубок, по ко торым с помощью насоса непре рывно циркулирует раствор едко го натра. Пар подается сверху в межтрубное пространство, подо гревает раствор и отводится через конденсационный горшок, а подо гретый раствор подается в вароч ный котел и, пройдя через волок но, снова направляется в насос, затем в трубки, где вновь подогре вается, и т. д. Поверхность нагре ва в трубчатых подогревателях в зависимости от емкости варочного котла составляет от 26 до 40 м2. Применение подогревателей ис ключает разбавление раствора щелочи, что неизбежно при нагре вании котла острым паром.
Для уменьшения расхода пара при применении подогревателей последние конструируют макси мально узкими и высокими, что обеспечивает большую скорость
Рис. 58. Подогревательная колонка:
/— трубки; 2 — крышка подогре вателя; 3 — корпус подогревателя; 4 — дно подогревателя
1
Раствор
Рис. 59. Инжектор для подачи пара и цир куляции варочных щелоков в котле
пар
Рис. 60. Варочный котел с инжектором
движения пара и раствора щелочи, а следовательно, и более высо кий коэффициент передачи тепла между паром и жидкостью.
Применение острого пара сокращает время разогрева котла и варки и уменьшает расход пара примерно на 20—25% по сравне нию с расходом пара при использовании подогревателя.
В котлах с разогревом острым паром последний подается с по мощью специального инжектора (рис. 59), который производит цир куляцию варочных щелоков, одновременно подогревая их.
Более простой, но менее эффективный тип инжектора показан на рис. 60. Пар подводится по трубе к инжектору, установленному под ложным днищем котла. От инжектора до верхнего котла, вдоль его стенки проведена труба, оканчивающаяся против отражателя, укрепленного таким образом, чтобы увлекаемый паром раствор ще лочи равномерно разбрасывался по поверхности материала. В од ном котле следует устанавливать несколько инжекторов. При пло хой работе инжекторов циркуляцию жидкости производят насосом.
На вновь строящихся предприятиях подогрев рабочих растворов щелочи осуществляется только трубчатыми подогревателями.
Одним из наиболее серьезных и сложных вопросов при работе котлов с подогревателями и циркуляционными насосами является распределение щелочи в котле и постоянное пропитывание всех слоев волокнистого материала горячим рабочим раствором ще лочи.
Существует три вида схем циркуляции раствора щелочи: 1) вер тикальная (сверху вниз, снизу вверх) и смешанная (часть варки — снизу вверх, другая часть — сверху вниз); 2) радиальная (от пери ферии к центру, от центра к периферии) и смешанная (в обоих на правлениях); 3) вертикально-радиальная. Каждая из указанных схем циркуляции имеет ряд преимуществ и недостатков.
Вертикальная циркуляция сверху вниз наиболее легко осущест вима, но в процессе варки наблюдается значительное уплотнение материала в котле, что приводит к неравномерности провара; цирку ляция снизу вверх дает более равномерный провар, но требует уста новки более производительных насосов; кроме того, при этом спосо бе легко забивается волокнистым материалом верхнее отверстие
трубы для отвода щелочи.
Более благоприятные условия создаются при радиальной и вер тикально-радиальной циркуляции. Для такой циркуляции необходи мы вертикальный стояк в центре котла, а внутри цилиндрической
части котла — дырчатый |
кожух. Рабочий раствор щелочи можно |
||
подавать как через кожух вверх и отсасывать через |
стояк, |
так |
|
и наоборот — подавать |
через стояк и отсасывать |
через |
верх |
котла.
На одном из предприятий исследовалось качество провара бученой массы при различных схемах орошения линта в стандартном ва рочном котле, имеющем в конической части ложное дно, из-под ко торого центробежным насосом производился отбор рабочего раство ра с последующей подачей его в подогревательную колонку.
Качество провара проверялось по результатам анализов на вяз кость и смачиваемость. Были испытаны три способа орошения ще лочным раствором:
1. Орошение через четыре ввода — по этой схеме щелочь подава лась в верхнюю часть котла через четыре трубы диаметром 50 мм каждая, укрепленных на равных расстояниях по периметру крышки котла и расположенных под углом около 20° к оси котла.
Отбор проб на равномерность провара производился из пяти сло ев, расположенных через каждые 1,2 м по высоте котла.
Результаты анализов сведены в табл. 67 и 68, при этом средний разброс всех показателей определяли как среднее арифметическое суммы разностей между средними и фактическими значениями по казателей, деленное на число определений.
|
|
|
|
|
|
|
Т а б л и ц а 67 |
|
|
Изменение вязкости бученой массы по объему котла |
|
||||||
|
|
|
(опыт № |
1) |
|
|
|
|
Точка |
отбора проб из |
Вязкость бученой массы, сП |
|
|||||
Точка отбора проб из слоя по диаметру котла |
||||||||
слоя |
по высоте |
котла |
2 |
3 |
|
|
5 |
средняя |
|
|
1 |
4 |
1 |
||||
|
I |
98 |
131 |
460 |
166 |
|
137 |
198 |
|
II |
92 |
1)00 |
97 |
112 |
|
87 |
98 |
|
III |
119 |
122 |
117 |
95 |
|
111 |
ИЗ |
|
'IV |
122 |
117 |
88 |
157 |
|
100 |
117 |
|
V |
1 U7 |
106 |
97 |
110 |
|
100 |
L06 |
|
Средняя |
109 |
115 |
172 |
128 |
|
107 |
127 |
Средняя вязкость — 127 сП
Средний разброс вязкости: по высоте котла — 36 сП по диаметру » — 30 сП
Из приведенных данных (табл. 68) следует, что худшее качество провара массы линта наблюдается в пробах, отобранных из верхне го слоя (I), особенно в центре верхнего слоя (III), где вязкость до стигает 460 сП при средней вязкости 127 сП, а смачиваемость — 102 г, при средней смачиваемости 123 г.
Плохое качество провара линта в верхней части варочного кот ла объясняется недостаточным орошением линта щелочью во время циркуляции.
2. Орошение через один центральный ввод —по этой схеме пода ча из подогревателя рабочего раствора щелочи в варочный котел осуществлялась в верхнюю часть котла через один ввод по трубе диаметром 100 мм.
Точка отбора проб |
Смачиваемость бученой массы по объему котла, г |
||||||
Точка отбора проб из слоя по диаметру котла |
|||||||
из слоя по высоте |
|||||||
котла |
* |
2 |
3 |
4 |
5 |
средняя |
|
|
|||||||
I |
103 |
101 |
102 |
115 |
109 |
105 |
|
II |
131 |
136 |
140 |
134 |
129 |
134 |
|
III |
146 |
128 |
103 |
114 |
134 |
127 |
|
IV |
142 |
134 |
124 |
103 |
129 |
126 |
|
V |
119 |
108 |
124 |
123 |
120 |
125 |
|
Средняя |
128 |
121 |
119 |
122 |
124 |
123 |
Средняя смачиваемость— 123 г Средний разброс смачиваемости:
по высоте котла — 11 г по диаметру » — 7 г
Условия отбора проб были идентичны условиям отбора проб при орошении через четыре ввода. Результаты анализов по провару линта в котле сведены в табл. 69 и 70.
|
|
|
|
|
Т а б л и ц а 69 |
|
Изменение |
вязкости |
бученой |
массы |
по объему котла |
|
|
|
|
(опыт № 2) |
|
|
|
|
Точка отбора проб из |
|
Вязкость бученой массы, сП |
|
|||
Точка отбора проб из слоя по диаметру котла |
||||||
слоя по высоте котла |
1 |
2 |
3 |
4 |
б |
средняя |
|
||||||
I |
38 |
60 |
49 |
55 |
36 |
48 |
II |
20 |
19 |
19 |
21 |
23 |
20 |
III |
20 |
21 |
20 |
32 |
28 |
22 |
IV |
19 |
20 |
21 |
26 |
26 |
22 |
V |
21 |
19 |
20 |
22 |
21 |
21 |
Средняя |
24 |
28 |
26 |
29 |
27 |
27 |
Средняя вязкость — 27 сП Максимальная вязкость — 60 сП Минимальная вязкость— 19 сП Средний разброс вязкости — 8 сП
Точка отбора проб |
|
Смачиваемость бученого линта, г |
|
|
||||
Точка отбора проб из слоя по диаметру котла |
|
|||||||
из слоя по высоте |
|
|||||||
котла |
1 |
2 |
3 |
1 |
4 |
5 |
средняя |
|
I |
126 |
123 |
ПО |
|
119 |
|
|
119 |
II |
125 |
108 |
133 |
|
136 |
135 |
|
127 |
III |
107 |
106 |
113 |
|
134 |
131 |
|
118 |
IV |
121 |
— |
123 |
|
131 |
121 |
|
124 |
V |
98 |
121 |
114 |
|
122 |
132 |
1 |
117 |
Средняя |
115 |
114 |
'118 |
|
128 |
130 |
|
120 |
Средняя смачиваемость— 120 г Максимальная смачиваемость— 136 г Минимальная смачиваемость — 98 г Средний разброс смачиваемости — 5 г
Из приведенных данных табл. 69 следует, что вязкость целлюло зы в верхнем слое (I) была в 2 раза выше средней вязкости и нахо дилась в пределах от 36 до 60 сП, что объясняется неравномерным орошением в верхней части котла.
3. Орошение двумя кольцевыми оросителями — по этой схеме орошение щелочью производится через один ввод по трубопроводу диаметром 100 мм, от которого внутри котла отходят два кольцевых
оросителя: малый — диаметром |
50 мм и радиусом |
окружности |
700 мм и большой — диаметром |
100 мм и радиусом |
окружности |
950 мм. |
|
|
Оба оросителя охватывают по периметру 3/4 окружности котла, открыты на концах и, кроме того, каждый ороситель имеет по пять
отверстий диаметром от 4 до 30 мм для более равномерного ороше ния массы (рис. 61).
Условия отбора проб были идентичны условиям отбора проб по опытам № 1 и 2 (табл. 69 и 70).
Результаты анализов по провару массы линта в котле сведены в табл .71 и 72.
Из приведенных данных опыта № 3 (табл. 71 и 72) следует, что, несмотря на получаемый разброс по вязкости бученой массы в нижнеи части котла (линт частично применялся длинноволокнистый),
предложенная схема орошения щелочью обеспечивает наилучший провар массы.
Для уменьшения потерь тепла и тем самым снижения расхода пара варочные котлы покрывают термоизоляцией следующим обра зом: поверхность котла тщательно очищают от ржавчины, промыва-
216
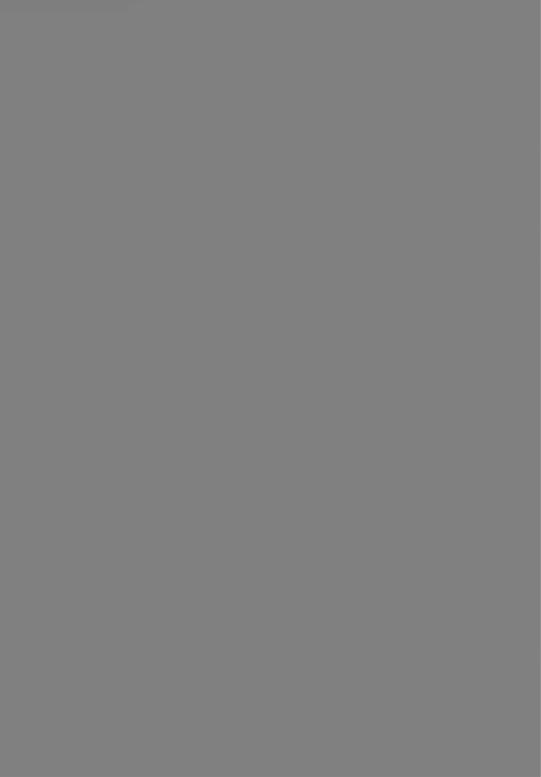
|
|
|
Смачиваемость бученой массы, г |
|
|||
Точка |
отбора проб из |
Точка отбо )а проб из слоя по диаметру котла |
|||||
слоя |
по высоте |
котла |
|
|
|
|
|
|
|
1 |
2 |
3 |
4 |
5 |
средняя |
|
I |
U6 |
135 |
130 |
129 |
131 |
128 |
|
II |
117 |
,120 |
128 |
124 |
117 |
121 |
|
III |
139 |
124 |
130 |
132 |
124 |
130 |
|
IV |
;н4 |
121 |
129 |
128 |
136 |
127 |
|
V |
121 |
128 |
118 |
121 |
128 |
123 |
|
Средняя |
123 |
126 |
127 |
127 |
131 |
126 |
Средняя смачиваемость— 126 г Максимальная смачиваемость— 139 г Минимальная смачиваемость — 115 г Средний разброс смачиваемости — 5 г
Существует другой, хотя и дорогой, но более надежный метод изоляции, по которому на тщательно очищенные железные стенки котла укладывают слой асбеста, предварительно сильно размочен ный в воде, толщиной около 20 мм. После нанесения слоя в котел пускают пар для просушки асбеста. После просушки, которая про должается около 2 суток, на асбестовый слой наносят слой из из мельченных старых джутовых мешков в виде полумассы, проклеен ной клейстером (100 л крахмального клейстера на 1800 л полумас сы). Полумассу перед нанесением на стенки котла отжимают рука ми от избытка воды и накладывают слой толщиной около 90 мм, который плотно обертывают парусиновыми лентами по всей поверх ности котла и сушат в течение 6—7 дней при 60—70° С.
Работа варочных котлов. Для удобства обслуживания варочных котлов (подачи к ним волокна, пара, воды и рабочих растворов ед кого натра) их обычно устанавливают в одну или две линии. При этом горловины варочных котлов должны быть на уровне полов следующего этажа. При такой установке котлов рабочему удобнее наблюдать за загрузкой, крепить или снимать крышку.
Загрузку рыхленого материала в котел можно производить раз личными способами в зависимости от конструкции горловины кот ла и технической оснащенности предприятия.
На предприятиях, где установлены варочные котлы с горлови ной, имеющей большой диаметр, применяют бункер (рис. 62), рас полагаемый ниже уровня пола рыхлительного отделения, в который поступает разрыхленный материал. Заполненный бункер с помощью мостового крана поднимают вверх, подводят к отверстию котла, дни-