
- •FRACTURE 1977
- •МЕХАНИКА
- •ОТ РЕДАКТОРА ПЕРЕВОДА
- •СПИСОК ЛИТЕРАТУРЫ
- •1. ВВЕДЕНИЕ
- •4.1. Оценка методами механики разрушения
- •4.2. Количественное описание «пластического» роста усталостных трещин (тип I)
- •5. ЗАКЛЮЧЕНИЕ
- •СПИСОК ЛИТЕРАТУРЫ
- •НЕКОТОРЫЕ ОСОБЕННОСТИ РОСТА УСТАЛОСТНЫХ ТРЕЩИН В МЕТАЛЛАХ И СПЛАВАХ
- •ВВЕДЕНИЕ
- •НИЗКИЕ СКОРОСТИ РОСТА УСТАЛОСТНЫХ ТРЕЩИН
- •ПОРОГИ
- •ВВЕДЕНИЕ
- •ТЕОРЕТИЧЕСКАЯ ОСНОВА АНАЛИЗА ДИНАМИЧЕСКОГО РОСТА И ОСТАНОВКИ ТРЕЩИНЫ
- •ПАРАМЕТРЫ МАТЕРИАЛА
- •ПЕРСПЕКТИВЫ ПРИМЕНЕНИЯ ТЕОРИИ
- •РАСПРОСТРАНЕНИЕ ТРЕЩИН В ТРУБОПРОВОДАХ
- •ПРОЕКТИРОВАНИЕ С УЧЕТОМ ТОРМОЖЕНИЯ ТРЕЩИН
- •СПИСОК ЛИТЕРАТУРЫ
- •Разрушение при сварке
- •Трещиностойкость в зоне термического влияния (ЗТВ)
- •СПИСОК ЛИТЕРАТУРЫ
- •ЛОКАЛИЗАЦИЯ ПЛАСТИЧЕСКОГО ТЕЧЕНИЯ И ТРЕЩИНОСТОЙКОСТЬ ВЫСОКОПРОЧНЫХ МАТЕРИАЛОВ
- •СПИСОК ЛИТЕРАТУРЫ
- •ВВЕДЕНИЕ
- •Теория
- •Сравнение теории с экспериментальными данными
- •НЕКОТОРЫЕ НЕДАВНИЕ ТЕОРЕТИЧЕСКИЕ И ЭКСПЕРИМЕНТАЛЬНЫЕ ИССЛЕДОВАНИЯ ПО МЕХАНИКЕ РАЗРУШЕНИЯ
- •/^-кривая
- •Критерий COD
- •Метод /-интеграла
- •Обсуждение результатов испытаний пластин с центральной трещиной
- •Результаты и обсуждение испытаний компактных образцов на растяжение
- •IV. РАЗРУШЕНИЕ ТИПА II
- •Анализ
- •Испытания и результаты
- •СПИСОК ЛИТЕРАТУРЫ
- •РАЗРУШЕНИЕ
- •8. ОБСУЖДЕНИЕ
- •СПИСОК ЛИТЕРАТУРЫ
- •СПИСОК ЛИТЕРАТУРЫ
- •СОДЕРЖАНИЕ:
Компонентами флюса, составляющими расплавленный |
шлак, |
являются такие окислы, как MnO, S i0 2, CaO, MgO, |
А120 3, |
ТЮ2, и фториды, подобные CaF2. Все перечисленные окислы, за исключением S i0 2 и МпО, устойчивы и имеют высокие стандартные свободные энергии образования [33]. Раскисле ние S i0 2 и МпО в расплавленном шлаке может производить ся железом, если фактические условия близки к равновесным и имеет место следующая реакция:
М.хОу + Fe хМ. + r/FeO.
Здесь под М понимаются Si, Мп. Раскисление S i0 2 является главным источником кислорода в металле сварного шва. Воз можность раскисления S i0 2 в шлаке зависит от его активно сти. Ключ к регулированию содержания кислорода в наплав ленном металле состоит в снижении активности S i0 2 в шла ке. Основные составляющие флюса, такие, как СаО, могут выполнить это снижение активности, реагируя с S i0 2 с обра зованием неактивного ортосиликата CaOSi02.
Существуют значительные расхождения [34] относитель но оценки флюсов по их способности снижать активность S i0 2 и, таким образом, понижать количество кислорода в металле сварного шва. Классифицируется ли флюс по фор муле валентности [35] или по ионной теории [36], все же существует необходимость еще большего числа термодинами ческих исследований реакций, которые ответственны за кон центрацию кислорода и тем самым за содержание включе ний в металле сварного шва.
Трещиностойкость в зоне термического влияния (ЗТВ)
О факторах, влияющих на трещиностойкость в зоне тер мического влияния (ЗТВ) для сварных соединений углеро дисто-марганцовистых и микролегированных сталей, будет говориться главным образом в связи с вопросом о сопротив лении сколу. Меньшее внимание будет уделяться сопротивле нию пластическому разрушению, поскольку образование включений в ЗТВ не происходит столь интенсивно, как мо жет быть в зоне сварки.
а) Различные области ЗТВ. Температурные градиенты, характерные для ЗТВ в сварных соединениях, влекут за со бой образование микроструктурной зоны. В ЗТВ можно вы делить четыре подобласти, расположенные за зоной сварного шва: (1) область укрупненных зерен (максимальная темпе ратура Тр гораздо больше критической температуры нагрева стали Ас3)\ (2) область измельченных зерен (Тр лишь
немного превышает критическую температуру Ас3) ; (3) проме жуточная критическая область (Лс3 > Т0 > Ас{) ; (4) докритическая область (Тр<.Ас\). Вид микроструктуры, ко торая может образовываться в каждой из областей, зависит от таких факторов, как максимальная температура, химиче ский состав листа и скорость охлаждения. Скорость охлаж дения обычно оценивается по времени, необходимому для снижения температуры от 800 до 500 °С. Величина скорости охлаждения зависит от подводимого тепла, толщины и фор мы элемента конструкции и величины предварительного на грева.
При последующем обсуждении основной упор будет сде лан на область укрупненных зерен, которая, вероятно, яв ляется наиболее хрупкой подобластью ЗТВ.
б) |
Сопротивление сколу. Трещиностойкость крупнозерни |
|
стой |
области ЗТВ зависит от |
характера микроструктуры. |
В отношении трещиностойкости |
металла сварного шва такие |
микросоставляющие, как крупнозернистый бейнит и мартен сит, вредны, в то время как с мелкозернистой ферритной или мелкозернистой бейнитной структурой связана большая тре
щиностойкость. Исходный крупнозернистый аустенит |
ведет |
к снижению трещиностойкости ЗТВ. |
ЗТВ |
Для иллюстрации особенностей трещиностойкости |
в сварных соединениях из углеродисто-марганцовистой стали
|
|
Трещиностойкость |
Сварка |
Вид сварки (во всех случаях |
|
погруженной дугой) |
||
1 |
[37] |
Наплавка валика двумя |
2 |
[38] |
электродами |
Один электрод, много |
||
|
|
проходный стыковой |
3 |
[39] |
шов |
Один электрод |
||
4 |
[39] |
Один электрод |
б [37] |
Два электрода |
|
6 |
[38] |
Один электрод, много |
|
|
проходный стыковой |
|
|
шов |
|
|
|
Таблица 2 |
ЗТВ и основного листа |
|
|
|
Подводи |
Область свар |
Температура, при |
|
которой критиче |
|||
мое тепло. |
ного изделия |
ское COD равно |
|
кДж/мм |
|
0,1 мм |
|
7 |
Основной |
-120 °С |
|
|
лист, ЗТВ |
—100 °С |
|
|
|
11 |
о |
5,4 |
|
ии юо |
|
|
|
|
о |
1 |
|
-120 °С |
|
|
|
— 110 °с |
|
1 |
|
—170 °С |
|
|
|
- 6 0 °с |
|
5 |
|
-150 °С |
|
|
|
—80 °С |
|
2,1 |
» |
А 1 |
о |
О-V) оО |
|||
|
|
1 |
о•ь. П |
можно обратиться к исследованиям [37—40]. Данные меха ники разрушения, приведенные в табл. 2, показывают, что, вообще говоря, не было большого различия в трещиностойкости ЗТВ и основного металла для сварных соединений пер вых трех указанных типов. В состав основного металла этих типов соединений входило номинально 0,14—0,16% С и 0,8— 1,2% Мп. Несмотря на отсутствие количественного металло графического анализа, было установлено, что в микрострук туре ЗТВ присутствовали эвтектоидный феррит и перлит вме
сте |
с |
крупнозернистым и |
мелкозернистым бейнитом. Одна |
ко |
в |
сварном соединении |
из углеродисто-марганцовистой |
стали могут быть гораздо большие различия в трещиностой-
кости ЗТВ |
и основного металла, если возрастает содержание |
||||
мартенсита |
в ЗТВ |
(сварное соединение типа 4). Факторами, |
|||
ускоряющими образование |
мартенсита |
в ЗТВ, |
являются |
||
обычно низкая |
величина |
подводимого |
тепла |
(меньше |
|
1 кДж/мм) |
и достаточная закаливаемость стали. |
|
Крупнозернистая ЗТВ в сварных соединениях из микролегированной стали может иметь гораздо более низкую трещиностойкость, чем основной материал. Для объяснения этого различия в трещиностойкости ЗТВ и основного материала рассмотрим сначала структурные изменения, которые про исходят в ЗТВ при сварке. В основном материале имеются мелкие зерна феррита (d = 0,01 мм), образовавшиеся при контролируемом прокате металла. Для контролируемого ро ста зерна важную роль играют частицы NbC и VC. Оконча тельная мелкозернистая структура имеет высокую прочность и сопротивляемость сколу. Когда эти структуры подвергают ся интенсивному тепловому прогреву в ЗТВ по соседству с зоной сварки, частицы второй фазы, регулирующие размер зерна, могут раствориться, и элементы Nb и V перейдут в раствор. По охлаждении ЗТВ могут образовываться различ ные продукты превращения, зависящие от скорости охлажде ния. При достаточно быстром охлаждении, когда такие леги рующие элементы, как Nb, V, остаются в растворе, они могут оказывать сильное влияние на тип получающихся продуктов превращения. Если охлаждение производится достаточно медленно, то может происходить выпадение карбонитридов
Nb и- V.
Обратимся к некоторым из исследований, выполненных с целью связать микроструктуру ЗТВ с трещиностойкостью микролегированных сталей. В работах [37, 38, 40] было ус тановлено, что Nb (в количестве приблизительно 0,046-^ 0,10%) способствует образованию крупнозернистого бейнита в крупнозернистой области ЗТВ. Для сварных изделий типа 5 ц 6 из табл. 2 имеется значительное различие в трещино*
стойкости ЗТВ и основного металла. Основной металл этих сварных изделий содержал номинально 0,16—0,18% С, 1,2% Мп, 0,2—0,3% Si и 0,04—0,06% Nb. В этих исследова ниях предполагалось, что наличие Nb в растворе способ ствует образованию бейнитной микроструктуры. Не было до казано, что вторая фаза из карбонйтридов Nb образовыва лась превращением аустенита.
Аналогично влиянию Nb при увеличении содержания V
может |
происходить |
ухудшение трещиностойкости |
ЗТВ |
(рис. |
12). В работе |
[41] предполагалось, что уменьшение |
Р и с . 12. Зависимость температуры |
перехода в испытаниях Шарли для |
ЗТВ (Т в градусах Цельсия) |
от концентрации ванадия V. |
трещиностойкости связано с выпадением в осадок нитридов ванадия. Это было доказано прежде всего для медленных скоростей охлаждения, Дt » 300 с при снижении темпера туры от 800 до 500 °С.
Проблема ограничения роста зерен в ЗТВ для сварных изделий из микролегированной стали была изучена в работе [42]. Когда мелкозернистые карбонитриды растворялись во время процессов сварки с большим тепловым подводом, в ЗТВ мог происходить интенсивный рост зерен, приводящий к плохой трещиностойкости. В испытаниях с моделированием сварки было найдено, что в стали, содержащей 0,14% С, 0,28% Si, 1,22% Мп, при добавлении частиц размера 0,1 мкм
с концентрацией TiN, равной 0,014%, структура аустенита с размером зерна 50 мкм сохранялась до максимальной темпе ратуры в 1400 °С (рис. 13). Частицы с TiN были настолько устойчивы, что ограничивали рост зерен при высоких темпе ратурах. Превращение, происходившее при охлаждении от максимальной температуры, приводило к образованию мел козернистой феррито-перлитной микроструктуры. Это проти воположно крупнозернистой бейнитной микроструктуре ЗТВ,
Р и с . 13. Связь между размером зерна аустенита (d |
в мкм) и макси |
мальной температурой в сталях (Т в градусах Цельсия), |
содержащих (/) |
и не содержащих (2) частицы с TiN [42]. |
|
образующейся в сталях при такой 'же термообработке, если добавка TiN отсутствует. ЗТВ в обычных сварных соедине ниях из подшипниковой стали с добавкой Ti, при сварке по груженной дугой и электрообработке в газовой атмосфере, стала значительно лучше, чем у обычной стали, что обнару живается ударным испытанием по Шарпи (найдено улучше ние на 25°С по температуре перехода).
Для контроля трещиностойкости ЗТВ необходимо иметь больше информации о микроструктурных особенностях ЗТВ. В этом отношении полезна количественная оптическая ме таллография, позволяющая определять тип и процентное со держание микрокомпонентоз. В частности, для сварных
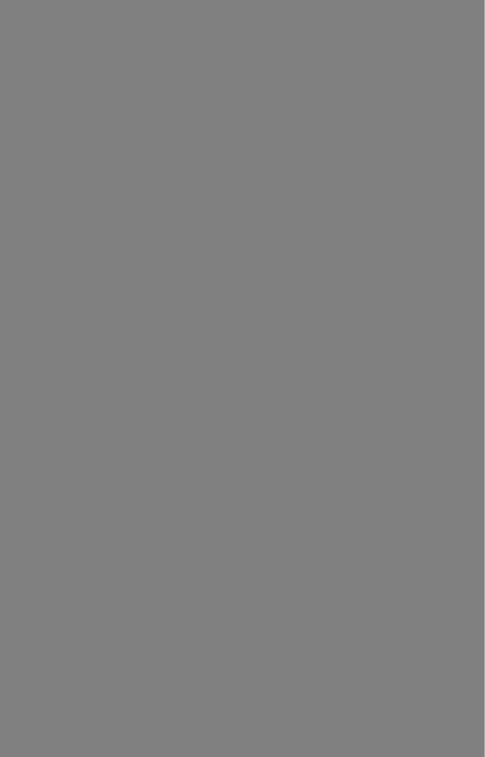
менялся образец типа Б с надрезом, сделанным двумя спо собами: (а) через наплавленный металл к ЗТВ и (б) через основной металл к ЗТВ. Более низкая трещиностойкость была получена для образца с вершиной надреза, примыкаю щей к наплавленному металлу. Размер пластической зоны в вершине надреза был достаточно велик, чтобы затронуть об ласть наплавленного металла. Поскольку наплавленный ме талл обладал низкой трещиностойкостью, этого было доста точно для снижения величины трещиностойкости ЗТВ.
Что касается трещиностойкости наплавленного металла, то Доус [45] дал обзор способов отбора образцов в случае многопроходных, двупроходных и однопроходных стыковых швов с точки зрения механики разрушения. Поскольку мно гопроходные швы содержат как структуры с осадками, так и без них, вершина надреза должна затронуть обе области наплавленного металла. Что касается образца А рис. 14, то надрез должен располагаться в зоне сварного шва, причем линия надреза должна быть перпендикулярна поверхностям листов. Аналогично, в отношении двупроходных и однопро ходных стыковых швов рекомендуются образцы со сквозным надрезом через зону сварки.
С В Я З Ь С РАЗРУШЕНИЯМИ СВАРНЫ Х КОНСТРУКЦИЙ
Можно было бы привести много примеров, чтобы пока зать, что все дефекты, описанные в первой части статьи, вы зывают преждевременные и зачастую катастрофические разрушения. Их можно было бы избежать, если, исходя из представлений о механизмах образования дефектов, принять соответствующие меры предосторожности, особенно на ста дии изготовления.
Некоторые дефекты, а именно образующиеся в результате растрескивания при затвердевании и расслоения, требуют более пристального внимания к составу материала, глав ным образом в отношении снижения содержания примеси. Однако часто такие проблемы возникают в процессе свароч ной операции, и изготовитель не имеет возможности изме нить материал или средства, которые он использует. Тем не менее гораздо больше можно было бы сделать для решения этих проблем на стадии изготовления, обращая внимание на особенности технологии сварки. Например, растрескивание при затвердевании, зависящее от того, как протекает затвер девание в сварочной ванне, может быть преодолено с по мощью изменения тока при сварке и скорости процесса, мо дифицирующих структуру, образующуюся при затвердевании наплавленного металла.
Изменения конструкции сварного соединения также цен ны в борьбе со слоистым отрывом даже для очень чувстви тельных по отношению к нему сталей с высокой концентра цией включений, если обеспечить отсутствие усадочных на пряжений в направлении, поперечном к свариваемым листам. Можно бороться с водородным растрескиванием, используя электроды с низким водородным потенциалом и уделяя вни мание оптимальному высушиванию и хранению до употреб ления. Соответствующий предварительный нагрев соедине ния, содействующий диффузии водорода, и изменение скорости охлаждения для создания менее закаленной микро структуры являются также эффективными мерами.
При обсуждении разрушения элементов конструкций очень важна уверенность в том, что сделанные предположе ния не являются слишком оптимистичными. Для предсказа ния вероятных типов докритического роста трещины и их значения требуется весьма полное понимание конструкции устройства, рабочих приемов и свойств материала. На прак тике медленный рост трещины может происходить по одной из причин или комбинации усталости, ползучести и растрес кивания при усталостной ползучести, растрескивания моно тонным нагружением (пластический разрыв или микрохрупкое растрескивание).
Наименьшее количество данных имеется о поле напряже ний вокруг дефекта. Анализ напряжений в областях слож ной геометрии трудно проделать аналитически, и часто мож но с успехом пользоваться численным расчетом с помощью представления действительной конструкции по методу конеч ных элементов. Эти аспекты обсуждаются в родственной пленарной статье Соита [46].
В области сопротивления разрушению современные ис следования продвинулись вперед. В случае сопротивления сколу и пластическому разрушению достигнуто гораздо боль шее понимание влияния металлургической структуры и осо бенно включений на трещиностойкость. Управления метал лургической структурой металлов сварных швов и зоны тер мического влияния можно достичь путем изменения таких условий сварки, как величина подвода тепла и скорость ох лаждения, но на сегодняшний день по этому предмету нет исчерпывающих исследований. Контроль за включениями яв ляется общепринятым при обработке стали, особенно для улучшения трещиностойкости в высокопрочных микролегированных сталях. Необходимо проделать аналогичные вещи с контролем включений в металлах сварных швов.
РОСТ ТРЕЩИНЫ ИЗ ДЕФЕКТОВ В УСЛОВИЯХ ПОЛЗУЧЕСТИ
Чтобы гарантировать целостность сварных компонентов при высоких температурах, необходимо уметь предсказывать скорости распространения трещин из существующих дефек тов, когда растрескивание вызывается ползучестью. Различ ные подходы применялись при анализе данных о росте тре щины в условиях ползучести, включая механику разрушения или более общий подход. Одно из ограничений использова ния подхода механики разрушения состоит в том, что многие материалы при испытании в условиях больших деформаций ползучести оказываются «нечувствительными к надрезам». Эта ситуация изучена во многих случаях с помощью стан дартного анализа, пригодного для конструкций в условиях ползучести. Главные проблемы заключаются в установлении типа деформации и масштаба напряжений, соответствующих конкретному виду эксплуатации и условий испытания. Эти проблемы разрешены совсем недавно с помощью представле ний об отсчетном напряжении [47] или о напряжении в ха рактерной точке [48].
Однако в гораздо более ранней работе со сталями, содер жащими Сг, Mo, V [49], обнаружена хорошая корреляция между скоростью роста трещины при ползучести и коэффи циентом интенсивности напряжения К, а именно
чг=скTS tl .
Здесь da/dt — скорость роста трещины, С, п — материальные (зависящие от температуры) коэффициенты. Для К имеем формулу
K = Yo Vo".
в которой величина Y— функция геометрии, f(a,W), W— ширина образца, а — длина трещины, а — напряжение в се чении без учета трещины.
Аналогичное соотношение найдено для аустенитной стали [50] и для более обычных ферритных материалов в условиях
ползучести [51].
Хотя этот метод дает хорошее описание поведения таких материалов, не следует ожидать, что он вообще будет спра ведливым, поскольку по определению ползучести она являет ся процессом деформации, зависящим от времени, и теория упругости не должна по существу быть полностью примени мой. Однако при этом подходе можно описать совокупность опубликованных данных с точностью менее двух порядков величины для скорости роста трещины, что является типич ным разбросом данных по ползучести.
Чтобы решить эти задачи в рамках линейной упругости, были предложены два других подхода. В первом из альтер нативных подходов использовали критерий COD, согласно которому рост трещины контролируется локальными смеще ниями в вершине трещины [52]..Это весьма привлекательно в принципе, поскольку деформация и разрушение в вершине трещины при растяжении малого образца легко наблюдаемы [53], и для процессов ползучести накопление деформации является общепринятым физическим представлением. Однако на практике трудно применять этот подход из-за неизбежных проблем определения критической величины COD, большого рассеяния экспериментальных данных при повышенной тем пературе и необходимости подробного математического ана лиза для вывода общего соотношения для смещений вблизи любого реального конструкционного дефекта.
Во втором альтернативном подходе в качестве управляю щего параметра используются имеющиеся данные о разры вах при ползучести и напряжение в истинном сечении [54]. При изучении данных о росте трещины для нормализованных и отпущенных сталей, содержащих Сг, Mo, V, при 565 °С [49] было показано, что несколько лучшая корреляция по лучалась для напряжения в истинном сечении, чем для коэф фициента интенсивности напряжений.
Трудно добиться согласия всех различных моделей роста трещины с механизмами ползучести, поскольку материалы, подверженные ползучести, проявляют внутренние различия в пластических свойствах. Эти различия механизмов означают различия в распределении и накоплении повреждений при ползучести в различных материалах. Следовательно, любой анализ роста трещины, предложенный для общего примене ния, должен позволять учесть истинное межкристаллитное разрушение в условиях зависящей от времени деформации и давать механизм роста трещины при большей пластичности.
ПРЕДОТВРАЩЕНИЕ РАЗРУШЕНИЙ
Из предшествующего обсуждения можно видеть, что до стигнуто важное понимание механизмов, которые вызывают образование дефектов сварки, и факторов, которые влияют на разрушение конструкций в области сварки. Многих про блем производства сварных соединений и разрушения при эксплуатации можно было бы избежать, если бы эта инфор мация была передана изготовителям, конструкторам и ин- женерам-сварщикам и использовалась ими. Как отмечено Итоном в недавней статье [55], имеются многочисленные ме таллургические исследования, предпринятые в связи с про