
Механика композитных материалов N3 2006
..pdfми, включая образование слоя диоксида кремния Si02 на арматуре SiC по средством предварительного искусственного окисления [8— И]. Послед ний подход привлек внимание многих исследователей и обусловил проведение работ [12— 16].
Причина интереса к методу предварительного окисления заключается в том, что благодаря разработке определенных реакций кремнезем поставля ет кремний, необходимый для предотвращения разложения SiC алюмини ем. По общему мнению эти реакции вырабатывают продукты более устой чивые, чем карбид алюминия AI4C3. Разное количество магния в системе может способствовать образованию AI2O3, MgO или MgA^CV Например, в [12] описано, что в системе А1— Mg— Si (А1— 1% Mg, А1— 5% Mg, А-356 и сплав 6061) с искусственно окисленными частицами SiC вырабатываются главным образом кристаллы M gA^O^ а относительно большое содержание Mg (выше 5%) способствует образованию MgO в добавление к MgA^CV
В настоящее время метод пассивного окисления становится общей прак тикой, однако ему присущи недостатки, которые следует учитывать при разработке недорогих и практичных технологий создания таких материа лов. Эти недостатки включают сложность управления однородностью и толщиной слоя SiC>2; применение высоких температур и продолжительного времени выдержки, повышающих стоимость производства, и выработку га зов СО2 и СО, вредных для окружающей среды, в процессе образования слоя Si02- Типичная процедура окисления заключается в нагревании по рошков SiC со скоростью 10 °С/мин и выдержке в течение 40 ч при заранее заданной температуре в диапазоне 1100— 1300 °С [13]. Установлено, что слой Si02 толщиной 100 нм на поверхности SiC можно образовать в режиме 1100 °С/2 ч, а 1000 нм — 1300 °С/40 ч [13, 14].
Основной недостаток метода пассивного окисления — сложность управ ления толщиной и однородностью образуемого слоя, в частности при окис лении подложки порошков в стандартной печи с естественной тягой. В [13] описано, что при образовании MgAl204 на поверхности раздела SiC/матри ца межповерхностная прочность зависит от толщины этой фазы. Кроме того, толщина слоя Si02 зависит от размера частиц порошков SiC. Термог равиметрический анализ (ТГА) показал, что при температуре окисления 1500 °С в порошках с частицами размером 18 мкм образуется слой толщи ной 50 нм, а с частицами размером 43 мкм — толщиной 160 нм [16]. После 8ч обработки при температуре 1200 °С была достигнута максимальная тол щина слоя 93 нм, а после 2 ч — 55 нм. Кроме того, при окислении расходует ся некоторое количество арматуры SiC и выделяются газы, вредные для окружающей среды [13]:
SiC(TB) + 0 2(Г) -> S i0 2(TB) +С (графит),
SiC(TB) +3/202(г)-> Si02(TB) +СО(г),
SiC(TB) + 2 0 2(г) -» S i0 2(TB) + С 0 2(Г).
Кроме того, реакция графита с жидким алюминием может выработать неже лательную фазу А14С3. В заключение можно констатировать, что намерен ное окисление SiC увеличивает количество производственных операций и удлиняет время изготовления и в итоге не снижает, а увеличивает стоимость изделия.
Интересно, что при получении карбида кремния с использованием про цесса Ачесона (Acheson process) обычно получают разные типы SiC с раз ным количеством примесей. Физически эти продукты различимы по цвету: от зеленого до желтого и черного. Зеленый карбид кремния, коммерчески называемый как тип GC, — это продукт с наименьшим количеством приме сей. Напротив, черный SiC (тип С) обычно содержит в качестве основной примеси природный или свободный диоксид кремния SiC>2 [17]. Влияние типа карбида кремния и содержания магния в сплаве на характеристики ин фильтрации композитов на основе Al/SiC, производимых методом бескон тактной инфильтрации, исследовали в [18]. Рассматривали образцы либо зе леного SiC либо черного SiC при инфильтрации двухслойных заготовок с меняющимся от слоя к слою размером частиц. Было установлено, что в сплаве с содержанием магния 3% по массе тип SiC значительно влиял на степень инфильтрации, тогда как при содержании Mg 6% степень инфиль трации была выше и влиянием типа карбида кремния можно было пренеб речь. Однако информация о влиянии типа SiC на механическое поведение композита отсутствует.
В настоящей работе исследовали влияние природного и/или непрореаги ровавшего диоксида кремния Si02 в коммерческом карбиде кремния типа С (черный SiC) на микроструктуру композита, особенно его влияние на обра зование карбида алюминия AI4C3. Кроме того, изучали влияние содержания магния в алюминиевом сплаве, размера частиц SiC и времени выдержки на микроструктуру и ударную прочность композита. Причина интереса к ис пользованию карбида кремния, содержащего кремнезем Si02, — меньшая стоимость по сравнению с таковым без содержания SiC>2.
Эксперимент
Заготовки карбида кремния в виде прямоугольных стержней размером 1 х 1 х 10 см с пористостью 50% изготовили одноосным прессованием смеси порошков с разным соотношением SiC двух типов: тип GC/тип С. Средние размеры частиц в порошках SiC были равны 20 и 75 мкм. Заранее опреде ленные количества этих порошков тщательно смешивали с 10% декстина по массе и примерно 1 мл воды. Затем заготовки сушили 1 ч при температуре 125 °С в сушилке с дутьевым охлаждением и более 12 ч отверждали при
температуре 225 °С. Заготовку вместе с алюминиевым сплавом (А1— 6 Mg—11 Si или А1— 9 Mg—11 Si) в форме пластинки массой от 60 до 80 г
|
|
|
|
|
|
|
|
|
Табл. 1 |
|
|
Характеристики SiC и время выдержки |
|
|
|||||
Испы |
Mg, % |
Время, |
Размер |
Отно |
Испы |
Mg, % |
Время, |
Размер |
Отно |
тание |
по мас |
мин |
частиц, |
шение |
тание |
по мас |
мин |
частиц, |
шение |
|
се |
|
мкм |
GC/C |
|
се |
|
мкм |
GC/C |
T1 |
6 |
45 |
20 |
25/75 |
T9 |
9 |
45 |
20 |
25/75 |
12 |
6 |
45 |
75 |
25/75 |
Т10 |
9 |
45 |
75 |
25/75 |
T3 |
6 |
60 |
20 |
25/75 |
Т11 |
9 |
60 |
20 |
25/75 |
T4 |
6 |
60 |
75 |
25/75 |
Т12 |
9 |
60 |
75 |
25/75 |
T5 |
6 |
45 |
20 |
75/25 |
Т13 |
9 |
45 |
20 |
75/25 |
T6 |
6 |
45 |
75 |
75/25 |
Т14 |
9 |
45 |
75 |
75/25 |
11 |
6 |
60 |
20 |
75/25 |
Т15 |
9 |
60 |
20 |
75/25 |
T8 |
6 |
60 |
75 |
75/25 |
Т16 |
9 |
60 |
75 |
75/25 |
очищали в ацетоне с помощью ультразвука и помещали в керамический контейнер, заранее покрытый нитридом бора. Характеристики карбида кремния и время выдержки, а также химический состав сплавов, специально разработанных и изготовленных для настоящего исследования, приведены в табл. 1 и 2 соответственно.
Эксперименты по инфильтрации выполнены в горизонтальной трубча той печи с алюминиевой трубой диаметром 6,5 см, закрытой по обоим кон цам заглушками для управления атмосферой процесса. Оба фитинга герме тизировали с помощью О-колец и система работала при очень малом избыточном давлении по сравнению с окружающим давлением. Для управ ления температурой образца в один конец трубы была вставлена термопара К-типа. Сборку прессованная заготовка— металл поместили в центре алю миниевой трубы и нагревали в атмосфере сверхчистого аргона со скоростью 15 °С/мин до температуры 1150 °С. Во время нагревания любое остаточное связующее улетучивалось и удалялось из системы в потоке аргона. Для улучшения смачивания частиц SiC сплавом А1—Mg— Si при достижении системой температуры 1150 °С атмосферу заменяли на высокочистый азот [И]. По достижении печью заданной температуры эксперимента систему
|
|
|
|
Табл. 2 |
|
Химический состав сплавов (% по массе) |
|
||
Сплав |
Mg |
Si |
Остальные |
А1 |
1 |
5,78 |
10,82 |
0,1192 |
Остаток |
2 |
9,23 |
10,98 |
0,1747 |
Остаток |
выдерживали изотермически в атмосфере азота в течение 45 или 60 мин. При последующем охлаждении образцы оставляли в азоте до температуры 450 °С. Затем подачу азота прекращали и образцы охлаждали в печи до ком натной температуры. Как видно из табл. 1, в соответствии с планом эксгТериментов испытания по инфильтрации выполнены при двух временах выдер жки для каждой совокупности рассматриваемых технологических параметров.
После охлаждения до комнатной температуры композиты извлекали из печи, подготавливали к проведению химического и микроструктурного ана лизов, а также к испытанию на удар по Шарпи в соответствии со стандартом ASTM Е23-98 [19]. Образцы полировали, используя стандартные процеду ры, и исследовали посредством оптической микроскопии (ОМ), сканирую щей электронной микроскопии (СЭМ), энергетической дисперсии рентге новских лучей (ЭДР) и дифракции рентгеновских лучей (ДР, излучение СиКа ). Плотность композитов оценивали методом Архимеда, а остаточную пористость определяли по формуле
г\
Р = 1 - Р изм •100%,
V Ртеор j
где р изм — измеренная плотность; р теор — теоретическая плотность компо зитов, рассчитанная по правилу смеси.
Интенсивность
б
А
А |
M l |
|
|
3 L |
JukA |
□□ |
20, град |
|
|
|
|
||
20 |
40 |
60 |
80 |
100 |
120 |
Рис. 1. Рентгенограммы ДР порошков SiC: а — тип С (черный); б — тип GC (зеле ный). ▲ — Si02; Л — SiC-а 4Н; □ — SiC-a 6Н.
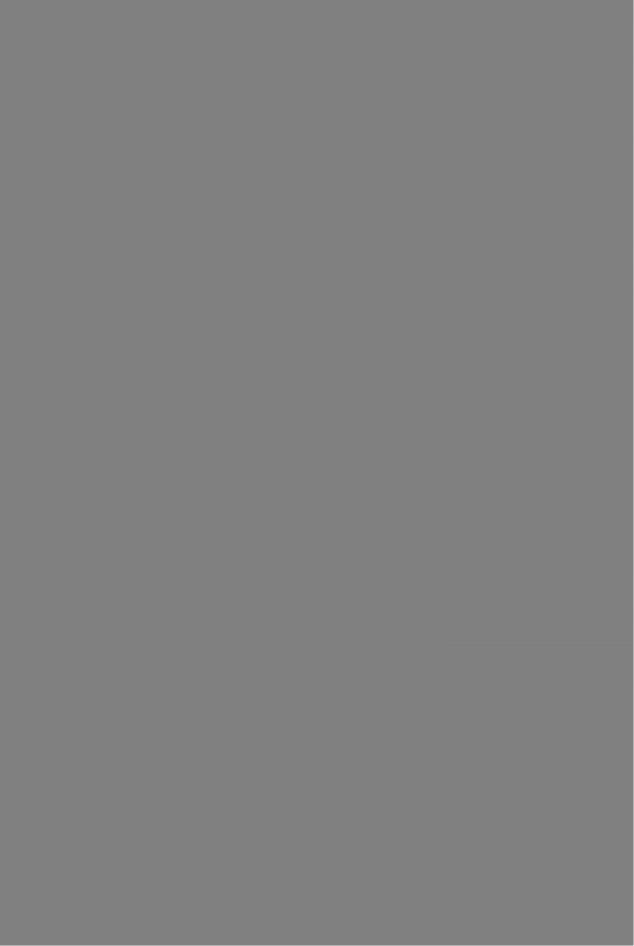
Рис. 4. Рентгенограммы ДР композитов, изготовленных из порошков SiC с разме ром частиц 20 мкм с соотношением типов 75/25 {а) и 25/75 (б) при содержании Mg в сплаве 6 % по массе и выдержке 60 мин.
Анализ фаз и микроструктура. Типичная микроструктура композита, изготовленного из SiC с соотношением типов 75/25 при выдержке 60 мин, видна на микрофотографии (рис. 2). На рис. 3— 9 представлены рентгено граммы дифракционных картин, иллюстрирующие влияние SiC с примесью Si02 на микроструктуру композитов. Согласно данным рис. 3 для компози тов, изготовленных из SiC с соотношением типов 75/25 и размером частиц 75 мкм, независимо от содержания магния в сплаве увеличение времени вы держки от 45 до 60 мин способствовало образованию нежелательной фазы AI4C3. Аналогично, как иллюстрируют данные рис. 4, при содержании Mg 6% по массе в алюминиевом сплаве и при большом времени выдержки боль шее количество SiC с Si02 в заготовке способствует образованию AI4C3. Эти результаты также выявили, что независимо от размера частиц типов SiC, используемых в заготовках, и начального содержания магния в алюми ниевом сплаве, даже при наибольшем времени выдержки карбид кремния с соотношением типов 25/75 ограничил образование карбида алюминия (рис. 5). Как иллюстрируют данные рис. 6 и 7, для композитов, изготовленных из SiC с частицами размером 20 мкм, независимо от содержания магния в алю-
Рис. 5. Рентгенограммы ДР композитов, изготовленных из порошков SiC с разме ром частиц 75 мкм с соотношением типов 25/75 при содержании Mg в сплаве 9 (а) и 6% по массе (б) и выдержке 60 мин.
миниевом сплаве, большее количество карбида кремния, содержащего кремнезем (при соотношении типов 25/75) в заготовках, препятствовало об разованию карбида алюминия AI4C3даже при увеличении времени выдерж ки с 45 до 60 мин. При большом содержании магния в алюминиевом сплаве большее количество SiC с Si02 ограничивало образование карбида алюми ния при обоих временах выдержки (рис. 8 и 9).
Отсутствие карбида алюминия в образцах с большим содержанием SiC типа С можно приписать наличию природного и/или свободного диоксида кремния в порошках SiC. Обычно реакция Si02 с алюминием и/или магнием в сплаве вырабатывает фазы А120з, MgO и M gA^O^ термодинамически бо лее стабильные, чем карбид алюминия. Однако результаты испытаний ДР не выявили образования других фаз помимо A1N.
Реакция кремния с алюминием
3 S i 0 2(TB) + 4 А1(ж) —> 2 А120 3(ТВ) + 3 Si^B ЖИДКОм алюминии)’
Интенсивность *
б
• ♦
20 |
40 |
60 |
80 |
100 |
Рис. 6. Рентгенограммы ДР композитов, изготовленных из порошков SiC с разме ром частиц 20 мкм с соотношением типов 25/75 при содержании Mg в сплаве 6% по массе и выдержке 45 (а) и 60 мин (б).
AGI I 50°C = ” 420 кДж/моль
термодинамически возможна. Однако при наличии магния в алюминиевом сплаве наиболее вероятна реакция, вырабатывающая фазу алюмината маг ния (шпинель):
2Si0 2(TB) +2 А1(ж) |
—>M g A ^O ^g) + 2 Si^B ЖИДКом алюминии)» |
AGji5o°с = “ 383 кДж/моль.
Более того, кремний может реагировать с магнием в паровой фазе
S I0 2 ( TB) + 2 M g (rj —> M gO(TBj + S i(TB),
AGj i5o°c = —21 кДж/моль.
Благодаря наличию магния в сплаве реакция образования шпинели наи более вероятна. Однако возможно, что шпинель образовывалася в количест ве, недостаточном для обнаружения оборудованием ДР.
Фаза нитрида алюминия, обнаруженная в микроструктуре композитов, может образоваться в результате реакции расплавленного алюминия с газообразным азотом [20]:
А1(Ж) +[N ]-» A1N(TB), |
(1) |
AGn 0o°c =~325 кДж/моль.
В некоторых исследованиях наблюдали, что благодаря низкой темпера туре испарения по сравнению с таковой для алюминия при нормальном дав лении магний улетучивался из расплава при переработке. Фактически унос магния из системы Наблюдали при смачивании, а также инфильтрации [21, 22]. По этой причине A1N также может образоваться в результате взаимо действия магния в Паровой фазе с азотом в атмосфере процесса согласно следующим реакциям [20]:
Рис. 8. Рентгенограммы ДР композитов, изготовленных из порошков SiC с разме ром частиц 20 мкм с соотношением типов 75/25 (а) и 25/75 (б) при содержании Mg в сплаве 9% по массе и выдержке 45 мин.
ЗМ ё(г) + 2[N]-> M g3N 2(TB), |
(2) |
АСцоо°с = “ 175 кДж/моль, |
|
3N 2(тв) + 2 А1(ж) —>2 A1N(ТВ) +3 M g , |
(3) |
АСцоо°с =^"175 кДж/моль.
Реакции (1) и (2) — экзотермические, и хотя с термодинамической точки зрения азотирование как магния, так и алюминия весьма возможно, в [20] описано, что реакция образования Mg3^ является кинетически намного бо лее благоприятной, чем A1N в результате реакции (1).
Для использования преимущества магния в качестве поверхностно-ак тивного элемента и улучшения смачивания SiC при повторном применении в расплаве части испарившегося магния весьма желательно протекание реакций (2) и (3) [11].
Испытания на ударную прочность. В табл. 3 суммированы результаты измерений плотности, остаточной пористости и ударной прочности компо зитов. Видно, что с изменением содержания магния в алюминиевом сплаве