
Учебное пособие 800606
.pdf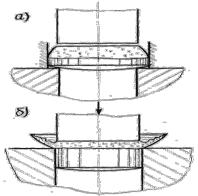
Пуансон зачистного штампа выполняет роль «толкача», назначение которого – перемещение заготовки относительно матрицы. Вследствие этого применяются зачистные пуансоны с поперечными размерами как меньше, так и больше соответствующих поперечных размеров рабочего отверстия матрицы.
Пуансон меньше матрицы стоит дороже, так как требуемая пригонка его к матрице с определенным зазором; изготовление пуансонов полнее матрицы дешевле, однако в этом случае настройка зачистного штампа и его эксплуатация несколько сложнее, так как пуансон не должен доходить до зеркала матрицы.
Рис. 2.18. Зачистка вырубленной заготовки
На матрицу зачистного штампа заготовка устанавливается блестящим пояском вниз (к матрице). По мере опускания пуансона припуск на зачистку срезается рабочей кромкой матрицы (рис 2.18). При этом образуется стружка в виде кольца, диаметр которого все время увеличивается. В определенный момент кольцевая стружка рвется и распадается на части. Зона пластической деформации носит локальный характер, она сосредоточена только у рабочей кромки матрицы.
81
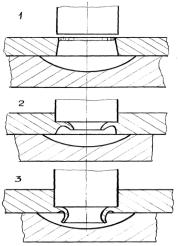
После полного удаления припуска боковая поверхность зачищенной заготовки становится блестящей, перпендикулярной плоскости детали.
Зачистка отверстий в плоских заготовках Зачистка боковой поверхности отверстий, полученных
обычной пробивкой, осуществляется в специальном зачистном штампе, рабочим органом которого является пуансон. Матрица такого зачистного штампа играет только роль опоры, она выполняется в виде плиты со сферическим углублением (лункой), служащим для размещения в нем отхода, отделенного после зачистки.
В том случае, когда возможна упругая деформация заготовки (прогиб при зачистке относительно толстых заготовок толщиною свыше диаметра зачищенного отверстия), применяют матрицы в виде кольца. При этом зазор между пуансоном и матрицей составляет 0,1 – 0,2 мм.
Заготовка с пробитым отверстием устанавливается на матрицу зачистного штампа блестящим пояском вверх (к пуансону). По мере опускания пуансона припуск на зачистку срезается его рабочей кромкой и отделяется от заготовки в виде кольцевой цилиндрической стружки (рис 2.19).
Рис. 2.19. Зачистка пробитого отверстия
82
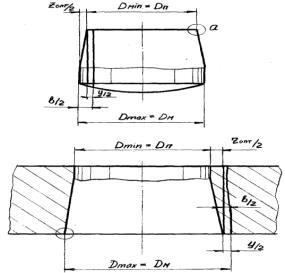
Зона пластической деформации сосредоточена только у рабочей кромки пуансона. После полного удаления припуска боковая поверхность отверстия становиться блестящей, перпендикулярной плоскости детали.
Припуски на зачистку Как уже было установлено, детали или заготовки, полу-
ченные обычным способом вырубки – пробивки (пуансоном меньше матрицы на величину оптимального зазора Zопт), имеют слегка конусную боковую поверхность. Поэтому соответствующие друг другу поперечные размеры внешнего контура заготовки неодинаковы. Наибольший поперечный размер заготовки (отверстия) равен размеру рабочего отверстия матрицы
(Dmax = Dм) наименьший – размеру пуансона (Dmin = Dп), а их разность равна величине двухстороннего оптимального зазора
Zопт между матрицей и пуансоном (рис. 2.20).
Dmax – Dmin= Zопт.
Рис. 2.20. Схема назначения припусков на зачистку
83
Для того чтобы соответствующие друг другу размеры внешнего контура заготовки были бы одинаковы во всех сечениях, параллельных плоскости листа, необходимо зачисткой удалить припуск шириной Z/2. Однако при такой величине припуска после зачистки не гарантируется возможность получения чистой блестящей поверхности среза по всей толщине и особенно у ее кромок (рис. 2.20, точка а).
Поэтому односторонний припуск на зачистку S/2 должен быть больше, чем Z/2, на некоторую величину y/2. Следовательно:
S = Z + y, |
(2.36) |
где S – полный двусторонний припуск на зачистку;
Z – двусто-ронний оптимальный зазор при обычной вырубке – пробивке;
у– дополнительный двусторонний припуск на зачистку. Величина дополнительного припуска на зачистку у зави-
сит от рода зачищенного материала, его толщины и формы контура детали. В соответствии с нормативными данными, составленными с учетом перечисленных параметров, величина дополнительного припуска на зачистку у составляет: для металлов 0,1 - 0,6 мм, для гетинакса и текстолита 0,2 – 0,5 толщины листа.
Как правило, зачистка срезанием припуска осуществляется в несколько переходов, число которых достигает пяти. Чем толще металл и выше его твердость, тем больше количество переходов зачистки. При многократной зачистке двусторонний припуск на зачистку равен
S = y(0,7n + 0,3)+Z, |
(2.37) |
где n – количество переходов зачистки.
Рекомендации по определению количества переходов зачистки приведены в работе.
84
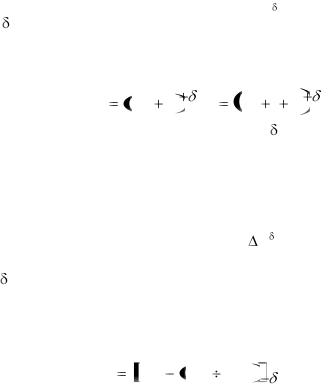
Рабочие (исполнительные) размеры инструмента Размеры инструмента для зачистки внешнего контура де-
тали
Зачистке подвергаются заготовки, полученные вырубкой. Следовательно, их наименьшие поперечные размеры после вырубки равны соответствующим размерам вырубного пуансона.
Если пуансон круглый, его диаметр Dпв должен быть равен сумме номинального диаметра зачищенной заготовки и дополнительного припуска на зачистку у
Dпв = (DH + y)- пв , |
(2.38) |
где пв – допуск на диаметр пуансона для вырубки.
Поскольку при обычной вырубке зазор назначается за
счет увеличения размеров матрицы, ее диаметр равен |
|
||||
D |
D |
Z |
мв D |
y Z мв , |
(2.39) |
мв |
пв |
|
H |
|
|
где Dмв – диаметр матрицы для вырубки; |
мв – допуск на диа- |
||||
метр этой матрицы. |
|
|
|
|
|
Так как размеры детали после зачистки соответствуют размерам зачистной матрицы, которая изнашивается «в тело», ее диаметр можно найти из следующего выражения:
Dмз = (DH - 0,8 )+ мз, |
(2.40) |
где Dмз – диаметр матрицы для зачистки;
мз – допуск на диаметр детали (после зачистки).
Диаметр пуансона для зачистки Dпз (если его размеры меньше зачистной матрицы) принимают на 0,03 – 0,08 мм меньше диаметра матрицы
Dпз Dмз 0,03 0,08 |
пз |
. |
(2.41) |
|
|
|
85
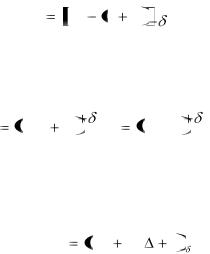
Размеры инструмента для зачистки отверстий Зачистке подвергаются отверстия, полученные пробив-
кой, следовательно, их наименьшие поперечные размеры после пробивки равны соответствующим размерам пробивного пуансона.
Если пуансон круглый, его диаметр должен быть меньше номинального диаметра отверстия Dн на величину полного припуска на зачистку
Dпл Dн Z y |
пл |
. |
(2.42) |
|
|
|
Поскольку при обычной пробивке зазор назначается за счет увеличения размеров матрицы, ее диаметр
D |
D Z мп |
Dн - y мп . |
(2.43) |
мп |
пп |
|
|
Так как диаметр отверстия после зачистки соответствует диаметру зачистного пуансона, который изнашивается «в тело», его диаметр Dпз находим из выражения
Dпз DH 0,8 i пз , |
(2.44) |
где i – так называемая «усадка отверстия», возникающая в результате упругой деформации материала детали.
Величина усадки i определяется согласно экспериментальным данным в зависимости от рода материала. Она колеблется в пределах 0,015 – 0,005 мм.
Для закрепления изложенного материала, относящегося к определению исполнительных размеров инструмента, рассмотрим следующий пример.
Требуется определить исполнительные размеры пуансона и матрицы для вырубки и последующей зачистки детали
Dн = 32-0,04,S = 2,5. Материал детали – латунь марки Л–59. Пользуясь нормативными данными определяем:
1) количество зачистных операций n = 1;
86
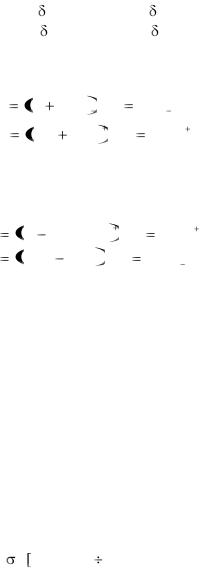
3) зазор между пуансоном и матрицей для вырубки
Z = 0,18 мм;
3)дополнительный припуск на зачистку у = 0,20 мм;
4)допуски на размеры инструмента:
а) для вырубки |
пв = 0,017 мм и |
мв = 0,027 мм; |
б) для зачистки |
пз = 0,008 мм и |
м з= 0,011 мм. |
Применяя расчетные формулы (2.38) и (2.39), находим исполнительные размеры инструмента для вырубки:
Dпв |
32 |
0,20 0.017 |
32,2 0,017 мм, |
D |
32,2 |
0,18 0,027 |
32,38 0,027 мм. |
мв |
|
|
|
Используя расчетные формулы (50) и (51). Определяем исполнительные размеры инструмента для зачистки:
D |
мз |
32 0,8 * 0,04 0,011 |
31,97 0,011 мм, |
|
|
|
|
Dпз |
31,97 0,01 0,008 |
31,96 0.008 мм. |
Технологическое усилие зачистки Технологическое усилие, необходимое для зачистки по-
верхности скола путем срезания припуска после обычной вырубки – пробивки, зависит от величины периметра зачищаемого контура, толщины материала, его прочностных характеристик и от величины припуска на зачистку. Если надо определить усилие зачистки внешнего контура детали, то следует принять во внимание усилие, необходимое для проталкивания зачищенной детали сквозь рабочее отверстие матрицы.
Поскольку процесс зачистки теоретически исследован недостаточно, суммарное усилие зачистки и проталкивания приближенно можно определить по формуле, полученной эмпирическим путем
P = L cp S + (0,15 0,20)na], |
(2.45) |
где L – периметр зачищаемого контура;
87

ср – сопротивление срезу материала заготовки; а – толщина зачищаемой заготовки;
n – количество деталей, находящихся одновременно в зачистной матрице.
При зачистке наружного контура пуансоном полнее матрицы усилие зачистки увеличивается на 30-50 % по сравнению с усилием зачистки пуансоном меньше матрицы. Соответственно технологическое усилие, необходимое для зачистки отверстий срезанием припуска равно
Pт = La cpS. |
(2.46) |
Технико-экономические показатели процесса Габаритные размеры деталей, подвергаемых зачистке, не
превышают 150 – 200 мм при толщине 3 - 4 мм. Зачистка более крупных деталей связана с трудностями, возникающими при изготовлении штампов. Зачистка деталей толщиною свыше 3 - 4 мм, как уже указывалось ранее, выполняется за несколько переходов. Чистота поверхности после зачистки достигает 7 - 8 класса чистоты при толщине материала до 3 мм. При этом практически достигаемая точность размеров соответствует 3 - 4 классу точности.
Трудоемкость зачистных операций близка к трудоемкости обычной вырубки – пробивки. Зачистка применяется в основном взамен механической обработки (фрезерования, развертывания, сверления, шлифования и др.), что существенно снижает трудоемкость. Например, замена фрезерования зубцов храповичка диаметром 26 мм и толщиною 2 мм зачисткой в штампе позволила снизить трудоемкость с 10,4 до 0,28 минуты на штуку при существенном улучшении качества обрабатываемой поверхности.
Следует отметить, что зачистные штампы требуют весьма точной сборки и пригонки рабочего инструмента, поэтому стоимость зачистных штампов в 1,5 – 2 раза выше стоимости аналогичных штампов для обычной вырубки – пробивки.
88
3. ФОРМОИЗМЕНЯЮЩИЕ ОПЕРАЦИИ ЛИСТОВОЙ ШТАМПОВКИ
3.1. Гибка листового и профильного металлопроката
Гибка представляет собой одну из формоизменяющих операций листовой штамповки, в результате которой происходит необратимое изменение кривизны срединной поверхности заготовки в плоскости изгиба.
Гибочные операции широко применяются для получения самых разнообразных деталей, в том числе деталей самолетов, автомобилей, тракторов, сельскохозяйственных машин, изделий широкого потребления и пр.
Так, например, на заводе ,,Ростсельмаш‖ до 70 % деталей зерноуборочного комбайна получают путем обработки металлов давлением, а 30 % из них при помощи гибки. С помощью гибки можно получить детали и полуфабрикаты самой разнообразной формы, применяя для этого различные виды кузнеч- но–прессового оборудования. Например, на гибочных вальцах при помощи изгиба с одновременным перемещением заготовки между валками, имеющими определенную настройку, изготовляют цилиндрические детали и заготовки различных диаметров и длин: заготовки для сварных труб больших диаметров, обечайки резервуаров, котлов и пр. (рис. 3.1, а).
На гидравлических и листогибочных кривошипных прессах при помощи универсального двухопорного приспособления можно получать детали и заготовки, изогнутые под определенным углом и по радиусу (рис. 3.1, б). При таком способе гибки формоизменение осуществляется поперечной силой путем так называемого ,,свободного изгиба‖, поскольку форма инструмента не сопряжена с формой изгибаемой заготовки.
89
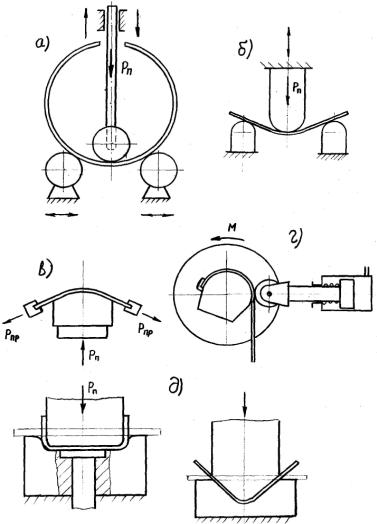
Рис. 3.1. Схемы гибки
На различного рода специализированных обтяжных станках (применяемых в основном на авиационных заводах) путем гибки поперечной силой с одновременным растяжением заготовки вокруг специального шаблона получают разнооб-
90