
Учебное пособие 800606
.pdf
При этом в «юбке» конического колпачка возникает сжа- то–растянутое напряженное состояние, как при вытяжке, а у вершины колпачка – двухосное растяжение, как при формовке.
Критерием штампуемости является отношение диаметра краевой части конического колпачка в момент разрыва дна колпачка к диаметру заготовки mф D p Do : чем меньше
mф, тем металл штампуется лучше.
Данный вид испытаний чрезвычайно прост, не требует специального оборудования и измерительной аппаратуры. Он может применяться для испытания листового металла толщиной 0,6–1,6 мм. При испытании металла толщиной менее 0,6 мм вытяжка не происходит вследствие складкообразования краевой части заготовки. Диаметр заготовки и размеры пуансона и матрицы выбираются в зависимости от толщины испытуемого металла.
Испытание по методу Фукуи наиболее эффективно для оценки штампуемости металла, предназначаемого для штамповки деталей сложной формы (например, кузовных деталей автомобиля), в процессе формоизменения которых вытяжка сочетается с формовкой.
Испытания на силовые условия вытяжки Оценка штампуемости листового металла в зависимости
от силовых условий вытяжки была предложена В. Энгельгардтом (ГДР, 1960 г.), методика и нормативные данные испытания регламентированы стандартами Германии с 1963 года.
Испытание металла по методу Энгельтгардта заключается в вытяжке цилиндрического колпачка диаметром 30 мм с радиусом скругления дна, равным 4 мм, из заготовки диаметром 53 мм в штампе совмещенного действия для вырубки и вытяжки с прижимом заготовки (рис. 1.4).
Коэффициент вытяжки при испытании по методу Энгельгардта является величиной постоянной, равной 0,57. Испытание выполняется в два этапа: вначале происходит вырубка и вытяжка колпачка до момента возникновения максимального усилия вытяжки, затем фланец колпачка жестко защемля-
21
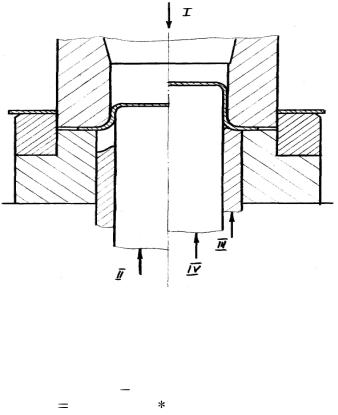
ется прижимным кольцом штампа, после чего продолжающий свое движение пуансон открывает дно колпачка. Последовательность движения инструмента показана на рис. 1.4 цифрами
I – IV.
Рис. 1.4. Схема испытаний на силовые условия вытяжки
Критерием оценки штампуемости листового металла по Энгельгардту служит относительная разность усилий вытяжки и отрыва дна
T |
Pmax |
Pz |
100 , |
(1.2) |
Pmax |
|
|||
|
|
|
|
где Pz – усилие, необходимое для отрыва дна колпачка;
Pmax - максимальное усилие, возникающее в процессе вытяжки.
Считается, что чем выше критерий Т, тем штампуемость металла выше. Для тонколистовой стали марки 08кп величина Т должна быть не менее 40 – 45 %. Испытание на вытяжку колпачка осуществляется на специальном приборе модели
22
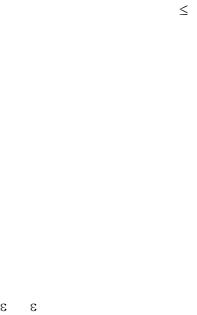
«TZP», выпускаемом в Германии заводом машин для испытания металлов.
Идея оценки штампуемости листового металла по Энгельгардту в функции силовых условий, возникающих при вытяжке цилиндрического колпачка, представляется нам весьма ценной, поскольку соотношение между усилием вытяжки и усилием отрыва дна колпачка зависит от комплекса факторов, в том числе от характеристик механических свойств металла и условий деформирования. Кроме того, данный вид испытания моделирует процесс вытяжки цилиндрических изделий, следовательно, внешние условия испытаний и реально существующие условия вытяжки сходны по схеме напряженного состояния очага деформации, конструкции штампа и условиям трения. Наряду с этим испытания по Энгельгардту имеют некоторые недостатки, например, радиусы скругления вытяжного пуансона и матрицы прибора модели ―TZP‖ регламентированы стандартами Германии и равны 4 мм. Испытания металлов, имеющих показатель интенсивности упрочнения n 0,22 на приборе модели ―TZP‖ показали, что при этих радиусах скругления инструмента не происходит полный охват заготовкой тороидальных поверхностей пуансона и матрицы, вследствие чего усилие вытяжки не достигает экстремальной величины. Указанное обстоятельство вызывает некоторую погрешность при определении критерия Т.
Оценка штампуемости листового металла по результатам анализа деформаций с помощью сеток
Данный способ оценки штампуемости листового металла был разработан в 60–х годах ХХ столетия американским исследователем С. Келером, а затем дополнен Г. Гудвиным (США). Сущность оценки заключается в определении главных деформаций, возникающих в опасной зоне штампуемой детали, а затем в сопоставлении этих деформаций с критическими для данной схемы деформированного состояния.
Главные деформации 1 и 2, возникающие в опасной зоне штампуемой детали, находятся по результатам измерения предварительно нанесенной на заготовку сетки в виде окруж-
23
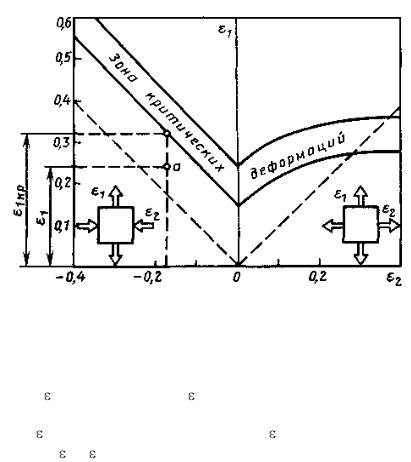
ностей, а оценка полученных данных – с помощью диаграммы предельной штампуемости Келера – Гудвина (рис. 1.5).
Рис. 1.5. Диаграмма предельной штампуемости
Диаграмма состоит из двух участков – правого, для условий двухосного растяжения (обе деформации положительны), построенного С. Келером, и левого, для сжато–растянутой схемы ( 1 – положительна, 2 - отрицательна), построенного Гудвиным. По оси ординат этой диаграммы отложена деформация 1, а по оси абсцисс деформация 2. Если точка с координатами 1 и 2 лежит ниже критической области, штамповка без разрушения возможна.
Исследования, выполненные А.Б. Хеберфельдом, показали, что диаграмма штампуемости Келера – Гудвина для листовых металлов с разной интенсивностью упрочнения (сталь
n = 0,25 и латунь n = 0,58) несущественно отличаются друг от друга. Исследование влияния плоскостной анизотропии на диаграмму штампуемости, проведенное на образцах из стали и сплава на основе Zn, показало, что диаграммы не дают количе-
24

ственной характеристики поведения металла при различной его ориентировке. В результате исследования влияния толщины металла, изменяющейся от 0,38 до 1,22 мм, было установлено, что для мягкой стали диаграмма предельной штампуемости лежит за пределами критической области диаграммы Келера – Гудвина (более тонкий лист ниже, а более толстый лист выше критической области). Влияние трения на вид диаграммы предельной штампуемости для стали практически не обнаружен, а для цинкового сплава влияние оказалось весьма значительным.
В результате выполненных исследований А.Б. Хаберфельд пришел к выводу, что применение диаграммы Келера – Гудвина для оценки штампуемости листового металла в известной степени ограничено.
Оценка штампуемости листового металла по соотношению накопленной и критической интенсивности деформаций
Согласно предложению руководителя лаборатории пластических деформаций ГНИИМаша А.Д. Томленова, критерием штампуемости листового металла служит коэффициент использования пластичности, который представляет собой отношение накопленной интенсивности деформации I к критической интенсивности деформаций к:
i |
. |
(1.3) |
|
||
k |
|
Чем ближе величина к единице, тем больше вероятность потери устойчивости или разрушения детали в процессе штамповки и, следовательно, штампуемость металла хуже. Интенсивность деформации I определяется зависимостью:
2
i 3
2 |
1 |
2 |
2 |
, |
(1.4) |
1 |
2 |
|
|
где 1 и 2 – алгебраически наибольшая и наименьшая логарифмические деформации, которые могут быть вычислены по
25

результатам измерения в опасных зонах ячеек деформированной сетки, предварительно нанесенной на заготовку.
Критическая деформация к определяется по формуле
|
2 1 |
m m2 |
|
|
к |
|
|
* n , |
(1.5) |
|
|
|||
2 |
m |
|
||
|
|
в которой m – показатель напряженного состояния детали, определяемый из уравнения связи между напряжениями и деформациями
m |
1 |
2 2 |
, |
(1.6) |
|
2 |
2 1 |
||||
|
|
|
а коэффициент интенсивности упрочнения n определяется по результатам испытания металла на растяжение.
Применяя методику ГНИИМаша, можно кроме коэффициента использования пластичности определить характеристики механических свойств листового металла ( р и р), обеспечивающие высокую штампуемость деталей сложной формы. Следует отметить, что рассмотренный метод оценки штампуемости листового металла, предложенный А.Д. Томле-новым, имеет наиболее строгое теоретическое обоснование на базе механики сплошных сред.
В заключении следует отметить, что критерий штампуемости, а следовательно, и способ испытания листового металлопроката на штампуемость необходимо выбирать в зависимости от характера напряженно–деформированного состояния зоны пластической деформации штампуемой детали, а также в зависимости от ее формы, размеров и относительной толщины.
26
2. РАЗДЕЛИТЕЛЬНЫЕ ОПЕРАЦИИ ЛИСТОВОЙ ШТАМПОВКИ
2.1.Механизм разделительных операций
Вразделительных операциях листовой штамповки отделение одной части заготовки от другой осуществляется путем смещения этих частей в направлении, перпендикулярном плоскости заготовки. Это смещение в начальных стадиях характеризуется пластическим деформированием, но обязательно завершающимся разрушением.
С тем, чтобы уменьшить искажения заготовки, вызываемые пластическими деформациями, при выполнении этих операций стремятся локализовать очаг пластической деформации, чему способствует уменьшение радиусов скругления рабочих кромок инструмента и уменьшения зазора между пуансоном и матрицей.
Наличие положительного зазора, отличного от нуля
(Z = Aм - Ап > 0), приводит к тому, что силы, приложенные к заготовке со стороны матрицы и пуансона не действуют по одной прямой, т.е. образуют момент, равный произведению равнодействующих элементарных сил, действующих от пуансона и матрицы на плечо, несколько большее, чем зазор Z. Наличие момента вызывает поворот отделяемых частей в пространстве (при отрезке) или изгиб заготовки (при вырубке и пробивке). Это в свою очередь приводит к резкой неравномерности распределения нормальных напряжений на контактных поверхностях. Нормальное напряжение увеличивается от нуля по мере приближения к режущим кромкам, достигая максимума вблизи последних. Неравномерность распределения напряжений на контактных поверхностях вызывает неравномерность распределения напряжений в слоях, параллельных плоскости листа и в толщине заготовки.
Согласно принципу Сен – Венана о локальности эффекта самоуравновешивающихся внешних нагрузок, по которому неравномерность распределения напряжений, вызванная дей-
27
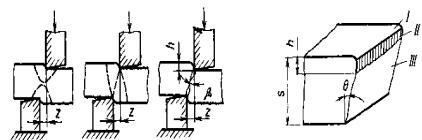
ствием сосредоточенных сил, быстро убывает по мере удаления от точки приложения этих сил, в разделительных операциях по мере удаления от режущих кромок в толщину заготовки неравномерность распределения напряжений уменьшается, а протяженность зоны пластических деформаций в направлениях, перпендикулярных направлению внешних сил резания – увеличивается. Отсюда следует, что очертания очага деформации в разделительных операциях, как это подтверждается и опытом, приближено имеют вид, показанный на (рис. 2.1).
а) б) в) г) Рис. 2.1. Стадии процесса отрезки (а, б, в)
и поверхность разделения (г)
Неравномерности распределения напряжений в очаге деформаций соответствует неравномерность распределения величин деформаций. Максимальная величина деформаций будет вблизи режущих кромок, а по мере удаления от них как в толщину заготовки, так и в направлениях, перпендикулярных линии действия внешних сил, величина деформаций – уменьшается. Можно полагать, что в слоях заготовки, первоначально параллельных плоскости листа, наибольшая величина меридиональной деформации будет находиться в элементах, расположенных вблизи поверхности, соединяющей режущие кромки рабочего инструмента, также увеличиваясь по мере приближения рассматриваемых слоев к режущим кромкам.
Такому характеру распределения деформаций будет способствовать также и то обстоятельство, что очаг пластической деформации будет зарождаться вблизи режущих кромок, про-
28
никая на большую глубину по мере внедрения режущих кромок в заготовку вплоть до смыкания.
Таким образом, в слоях первоначально параллельных плоскости листа, неравномерность распределения деформации максимальна вблизи режущих кромок и несколько выравнивается в слоях более удаленных от режущих кромок (как вследствие большей протяженности очага деформаций, так и вследствие более позднего возникновения пластических деформаций, что обусловлено характером распределения напряжений в очаге деформаций).
Каждый металл способен воспринять без разрушения пластическую деформацию определенной величины, зависящую от свойств металла и схемы напряженного состояния. В соответствии с этим и в разделительных операциях без снятия стружки при достижении определенной величины пластической деформации может начаться разрушение. Так как максимальная деформация имеет место вблизи режущих кромок, то и разрушение может начаться в первую очередь в элементах, расположенных вблизи режущих кромок инструмента. Однако при этом следует учитывать, что величина предельной без разрушения пластической деформации зависит от схемы напряженного состояния и величины действующих напряжений, увеличиваясь с увеличением шарового тензора сжатия. Именно поэтому разрушение должно начаться не в элементах, расположенных под (или над) торцом рабочего инструмента, а в элементах, противостоящих свободным поверхностям (при положительном зазоре), где величина сжимающих напряжений будет меньше. Этим же объясняется появление торцевого заусенца, особенно в случае притупления режущих кромок. И, наконец, этим обстоятельством до некоторой степени объясняется и то, что развивающаяся от режущих кромок трещина наклонена к линии действия усилия (к оси инструмента) под некоторым углом и направлена во внешнюю (от торца инструмента) сторону. В связи с последним необходимо отметить, что как показали исследования распределения напряжений поляризованным светом на оптически активных материалах,
29

трещина совпадает с геометрическим местом точек, соединяющих вершины кривых максимальных касательных напряжений. В то же время анализ распределения деформации показал, что трещины развиваются по точкам, в которых сдвиговые деформации имеют наибольшую величину.
Приведенные соображения и данные позволяют воссоздать картину процесса деформирования в разделительных операциях без снятия стружки по мере внедрения режущих кромок. В начальных стадиях пластическая деформация сосредоточивается у кромок, которые внедряются в металл на некоторую глубину. Очаги деформации от режущих кромок увеличиваются, продвигаясь в толщину заготовки, до смыкания. Дальнейшее внедрение режущих кромок вызывает пластическую деформацию по всей толщине заготовки, дающую смещение одной части заготовки относительно другой. В другой стадии деформирования имеет место или только пластическая деформация (по Г.А. Смирнову - Аляеву) или уже начинается разрушение слоев заготовки, но только тех, которые приходят в непосредственное соприкосновение с режущей кромкой. Благодаря наличию упругих деформаций и повороту заготовки вследствие действия момента, на этой стадии внедрение режущих кромок дает образование гладкого блестящего пояска на поверхности среза за счет сглаживания трением заготовки о боковую поверхность режущего инструмента. Как только будет достигнута предельная величина деформации в слоях заготовки, не имеющих соприкосновения с режущими кромками, от последних образуются трещины, быстро развивающиеся в толщину заготовки. Встречей этих трещин завершается процесс отделения одной части заготовки от другой в разделительных операциях без снятия стружки.
Однако встреча трещин может произойти не при всех условиях деформирования. Если принять, следуя методике В.П. Романовского, что трещины имеют прямолинейную образующую, наклоненную под углом к оси инструмента, а в глубину внедрения режущей кромки до появления трещины обозначать через h, то величина зазора между режущими инструмен-
30