
Учебное пособие 800606
.pdf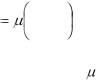
В требуемый момент включается коммутирующее устройство 4, которое замыкает батарею конденсаторов на индуктор 7.
При протекании тока через индуктор в каждой точке окружающего пространства возникает магнитное поле, напряженность которого зависит от взаимного расположения индуктора и заготовки 5, величины тока и его частоты. Образуемый при этом импульс магнитного потока индуктора наводит вихревые токи в заготовке, поля которых взаимодействуют с первоначальным полем, отталкиваются друг от друга и обжимают заготовку по оправке 6. Из электродинамики известно, что магнитное поле с напряженностью Н оказывает напряжение (давление):
|
H |
2 |
|
p |
, |
||
|
|||
5000 |
|||
|
|
где H - напряженность магнитного поля в эрстедах;
- магнитная проницаемость среды ( =1 при значительном Н).
Например, магнитное поле напряженностью 10 6 эрстед
создает напряжение 4103 МПа. Энергетика к.п.д. процесса
Энергия, накопленная в конденсаторной батарее, при разряде батареи превращается в полезную механическую работу деформирования заготовки и теряется на нагрев цепи и создание паразитного поля. Для увеличения КПД требуется уменьшить энергию на нагрев, паразитную индуктивность, уменьшить зазор и увеличить частоту разрядов.
По опытным данным на нагрев заготовки обычно расходуется (0,1 – 0,2)Е. Заготовка при этом нагревается до температуры равной 100 0 С.
Практически КПД составляет 10 – 40 %.
Операции, осуществляемые электромагнитной штампов-
кой.
231
1.Обжим трубчатых заготовок с помощью индуктора, охватывающего заготовку.
2.Раздача трубчатых заготовок с помощью индуктора, расположенного внутри заготовки.
3.Раздача трубчатых заготовок охватывающим индуктором импульсами разрядного тока, имеющего крутой спад, когда напряжѐнность поля должна нарастать медленно, чтобы перепад его не создал давления, превышающего предел текучести материала заготовки. После достижения определенного значения, оно должно быстро спадать до нуля.
Во всех перечисленных способах ток в заготовке индуцируется индуктором, но можно осуществлять штамповку путем непосредственного пропускания тока через заготовку.
С помощью импульсного магнитного поля можно осуществлять сборку неразъемных соединений, правку плоских и криволинейных плоскостей. Оригинальная операция – прессование резьбы внутри трубок и тонкостенных втулок по резьбовому болту или шпильке.
Оборудование Энергосистема установки с емкостным накопителем со-
стоит из пяти основных блоков: 1) зарядного устройства; 1) накопителя энергии; 2) разрядного устройства; 3) блока питания; 4) технического блока.
Зарядное устройство – высоковольтный выпрямитель с питанием от сети, напряжение повышается до величин номинального напряжения конденсаторного накопителя.
Накопителем энергии является батарея конденсаторов с низкой собственной индуктивностью и способностью выдерживать большое количество импульсных разрядов (ИМ5/150,
ИММ5/150).
Разрядное устройство должно пропускать большие токи, иметь малую индуктивность, значительную стабильность вре-
232
мени срабатывания, быть долговечным, прочным. Применяются высоковольтные дуговые разрядники.
Одной из важных проблем при конструировании установки является обеспечение малоиндуктивного соединения отдельных элементов разрядной цепи (плоские медные шины, разделенные диэлектриком и высоковольтные коаксиальные кабели).
Технический блок состоит из рабочего индуктора, матрицы или оправки. Индуктор должен быть прочным и обеспечивать высокую проводимость. Форма индуктора близка к форме заготовки.
Основная характеристика установок – величина накапливаемой энергии – от 12 до 400 кДж. Наибольшее распространение ещѐ в СССР получили установки МИУ20/1 с энергией 20 кДж. Целесообразно применение способа штамповки в мелкосерийном производстве.
4.2.Штамповка взрывом
ВСССР способ начал внедряться в производство в 1949 году проф. Р.В. Пихтовниковым (ХАИ). Сущность штамповки взрывом заключается в том, что на заготовку воздействуют либо непосредственно энергией взрыва волны, передающейся через воздух или жидкость, либо создаются машины – орудия,
вкоторых энергия взрыва преобразуется в кинетическую энергию подвижных частей этих машин, а следовательно, в кинетическую энергию инструмента – штампа.
Процесс деформирования протекает 1/30000 – 1/50000 с, скорость 100 м/с, давление подводного взрыва достигает 13000 МПа. Операции, осуществляемые взрывной штамповкой: вырубка, пробивка, формовка, вытяжка, калибровка, гибка, сварка и др.
Взрывчатые вещества, применяемые для штамповки: метательные (медленнодействующие) ВВ – порох, смеси горючих газов и др., бризантные (быстродействующие) ВВ – тротил, аммонит и др. Наиболее удобным является тротил.
233

Применяются детонаторы: гремучая ртуть, изид свинца. Для подрыва детонаторов применяется электрический ток, или удар. Заряды получают отливкой, прессованием или пластифицированием. Форма заряда должна быть подобна форме детали и подбирается экспериментально.
4.3. Электрогидроимпульсная штамповка
Сущность – в превращении энергии импульса электрической энергии в энергию механическую. Разряд в виде электрической дуги в жидкости вызывает появление волн и высоких давлений, которые деформируют заготовку. Процесс аналогичен взрывной штамповке. Принципиальная схема установки на ЭГШ приведена на (рис. 4.2).
1 – понижающий трансформатор, 2 – выпрямитель, 3 – конденсаторная батарея, 4 – воздушный разрядник, 5 – технологическая установка.
Рис. 4.2. Схема электрогидроимпульсной штамповки
234

Впервые советские ученые указали на возможность использования процесса в 1944 г. (Г.И. Покровский и Е.Н. Станкевич). В 1965 году Л.А. Юткин дал первые рекомендации.
Электрогидроимпульсным методом деформируются малопластичные металлы и сплавы с высокой точностью вследствие малых упругих деформаций. Преимущество по сравнению с взрывной штамповкой в том, что можно применять повторные импульсы без переналадки блока, возможна автоматизация процесса и применение его в линии.
Разряд в современных машинах осуществляется через зазор и через проволоку. Напряжение при разряде через жидкость 20 ÷ 30 кв, через проволоку – 4 ÷ 7 кв (проволока диаметром до 20 мм). Недостаток разряда через проволоку – необходимость еѐ замены.
ЭГШ позволяет сократить переходы, повысить точность. Осуществляется на ЭГШ – вытяжка, формовка, раздача, отбортовка, обжим, сборка и др.
Осуществлѐн серийный выпуск машин с энергией 10 –20 кДж типа Т1220 и Т1228, производительность до 80 деталей в
час, толщина заготовки 1,5 ÷ 4 мм. |
B |
50 25кг/мм2 |
размеры |
в плане 650 650 мм. Крупные машины с энергией 32, 60, 112, 150 кДж: ПЭГ – 25, ПЭГ – 60, ПЭГ – 100, ПЭГ – 150. Неболь-
шие прессы ―Удар – 12‖, с энергией 10 кДж и ―Удар – 20‖ с энергией 20 кДж.
5. ХОЛОДНАЯ ОБЪЕМНАЯ ШТАМПОВКА
5.1. Рельефная формовка
Рельефная формовка (чеканка, клеймение, разметка) – штамповочная операция, при которой происходит изменение формы изделия за счет перемещения металла по толщине заготовки.
235
Чеканкой получают монеты, медали и предметы широкого потребления. Достигаемая точность изделий, получаемых после чеканки, составляет 0,05 ÷ 0,1 мм.
Усилие чеканки определяется по формуле
P pF ,
где F – площадь проекции штампуемой детали; p – удельное давление.
Значение p зависит от материала и характера операции (приводится в справочной литературе.
Разметка, клеймение: осуществляется в штампах, применяется для нанесения лунок, центров. Находит широкое применение в часовой промышленности и приборостроении. Достигаемая точность 0,02 ÷ 0,03 мм.
5.2. Холодное выдавливание
Холодное выдавливание – процесс получения деталей методом истечения материала заготовки через калибрующее отверстие матрицы или в зазор между матрицей и пуансоном, а также тем и другим способом одновременно.
Процесс выдавливания по методу истечения разделяется на прямое, обратное и комбинированное (см. рисунок а, б, в), по виду деформации – холодное, горячее и полугорячее.
236
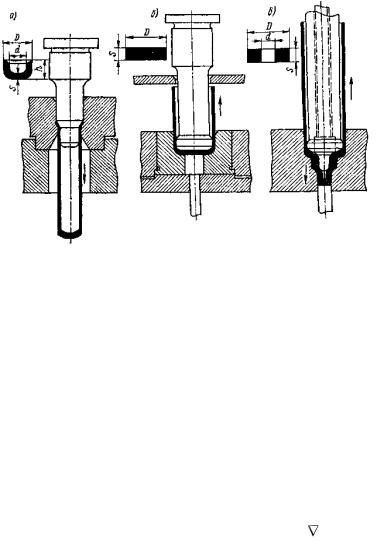
Способы выдавливания
В процессе прессования имеет место объемная схема всестороннего неравномерного сжатия.
Выдавливанием изготавливают осесимметричные детали, которые можно, в основном, подразделить на несколько конструктивных групп:
1.Стержни с головкой.
2.Трубные с фланцем.
3.Шлицевые валы, шестерни.
4.Односторонние и двухсторонние стаканы.
5.Сочетание конструктивных элементов. Преимущества процесса заключаются в следующем:
1)в экономии металла;
2)высокой точности и чистоте поверхности ( 10 );
3)более низкая трудоемкость по сравнению с резанием;
4)возможность механизации процесса.
Вопрос применения процесса для получения тех или иных деталей определяется исходя из его экономичности.
Возможность применения процесса ограничивается:
237
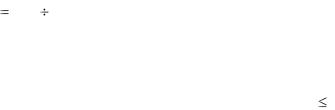
1) |
величиной |
удельных |
давлений |
qПРЕД . |
200 250кг/мм2 ; |
|
|
2) конструктивными ограничениями, которые связаны с предельной величиной удельных давлений:
а) детали с односторонним выступом, канавками;
б) детали с большим перепадом сечений |
F |
5 ; |
|
f |
|||
|
|
в) детали с высотой дна h < S (S – толщина стенки); г) детали, которые имеют острые углы, и т.п.; д) детали с отверстием малого диаметра.
Для холодного выдавливания применяются следующие материалы:
1.Цветные металлы и их сплавы.
2.Стали малоуглеродистые, среднеуглеродистые, малоле-
гированные: 08, 10, 15, 20, 25, 30, 35, 40, 45, 15Г, 20Г, 30Г, 40Г, 15Х, 20Х, 30Х, 35Х, 38ХА, 45Х, 18ХГТ, 12ХН2, 12ХН3, 15ХФ, 20ХФ, 20ХГ, 18ХГН, 20ХН, 40ХН.
Исходным материалом являются горячекатанные и холоднокатанные стали.
Проектирование техпроцесса выдавливания состоит из следующих этапов:
1)анализ конструкции заданной детали с точки зрения возможности ее изготовления выдавливанием;
2)определение формы, размеров заготовки и методов ее получения;
3)разработка маршрутной технологии с включением вспомогательных операций;
4)расчет технологических операций и переходов
(включая вспомогательные операции);
5)проектирование инструмента;
6)подбор оборудования и механизирующих устройств. При решении вопроса технологичности рассматривается
возможность получения данной детали из заданного металла требуемой точности и чистоты поверхности.
238
К заготовкам для холодного выдавливания предъявляются следующие требования:
1.Точность заготовок по объему.
2.Чистота поверхности не ниже 6 класса особенно при больших степенях деформации.
3.Перпендикулярность торцов осям симметрии.
4.Возможность ориентировки в автоматических загрузочных устройствах.
Исходя из этих требований при прессовании используются следующие формы и методы получения заготовок:
1)цилиндрические или многогранные сплошные;
2)цилиндрические или многогранные трубчатые;
3)фасонные сплошные или полые.
Диаметры заготовок должны обеспечивать их свободную загрузку в матрицу. Разница диаметров должна быть не более 0,5 мм на диаметр 10 ÷ 100 мм для прямого выдавливания и на 0,1 ÷ 0,2 мм для обратного выдавливания.
Заготовки для выдавливания получают следующим обра-
зом:
1.Токарной обработкой.
2.Отрезкой на специальных станках или пилах.
3.Рубкой прутка или вырубкой из листа.
4.Высадкой на холодновысадочных автоматах. Трубчатые заготовки получают обратным выдавливани-
ем с последующим удалением дна. Для повышения точности применяется протягивание.
Выбор формы заготовки и метода получения зависят от характера производства, конкретных условий и определяются экономическими расчетами.
Маршрутная технология состоит из следующих этапов: 1.Получение заготовки.
2.Подготовка заготовки под выдавливание.
3.Процесс выдавливания.
Подготовка заготовок под выдавливание включает целый ряд вспомогательных операций:
1) отжиг для снятия упрочнения, полученного при обра-
239
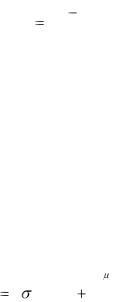
ботке заготовок; 2) выравнивание структуры заготовок ( для стали темпе-
ратура 680 – 720 0 С в течение 5 часов при медленном охлаждении);
3)очистка от окалины галтовкой или травлением;
4)обезжиривание при 70 - 80 0 С в течение 5 – 15 мин.;
5)промывка в холодной и горячей воде.
6)фосфатирование с целью получения пленки, разделяющей металл и инструмент, а также служащей для удержания смазки в процессе прессования;
7)смазка заготовок. Для смазки применяется жидкий
раствор мыла 60 – 72 % при температуре 70 0 С, графит или сушка горячим воздухом после омыливания.
Определение количества переходов при холодном выдавливании производится исходя из предельно-допустимой степени деформации, определяемой стойкостью инструмента.
Степень деформации определяется
q |
F3 Fn |
. |
|
||
|
F3 |
Если при определенной степени деформации удельные давления для данного материала не превышают прочности инструмента, то получить данную деталь можно за 1 переход. Если же удельные давления превышают прочность инструмента, процесс в таком случае разбивается на несколько переходов с промежуточными отжигами и полной подготовкой полуфабриката к следующему переходу выдавливания.
Усилия при выдавливании определяются по формулам С.И. Губкина, скорректированным Фаворским:
усилие прямого выдавливания
|
|
|
F |
|
2 h |
|
|
|
|
|
|
||
P k |
B |
(ln |
e d |
|||
f |
||||||
|
|
|
|
|||
|
|
|
|
|
)F ;
240