
Учебное пособие 800606
.pdf
Если учесть возможные отклонения условий вырубки – пробивки, толщины металла и его характеристик механических свойств коэффициентом К=1,2 1,3, то технологическое усилие вырубки – пробивки
Р = КРт . |
(2.21) |
Представляет интерес попытка Е.А. Попова теоретическим путем установить характер изменения усилия вырубки – пробивки по мере внедрения пуансона в заготовку. При выводе формулы для определения усилия вырубки – пробивки были сделаны допущения о равномерном распределении деформаций (а следовательно, и упрочнения) и постоянстве направления главных осей в процессе деформирования по толщине заготовки, а также о совпадении траекторий максимальных касательных напряжений с поверхностей скола.
Усилие вырубки – пробивки в любой момент деформирования до момента появления скалывающих трещин можно представить в следующем виде (рис. 2.10):
Рх = L(a – x) S(x) , |
(2.22) |
где х – глубина погружения пуансона в металл;
S = S/2 – наибольшее касательное напряжение.
Рис. 2.10. К определению усилия вырубки-пробивки
61
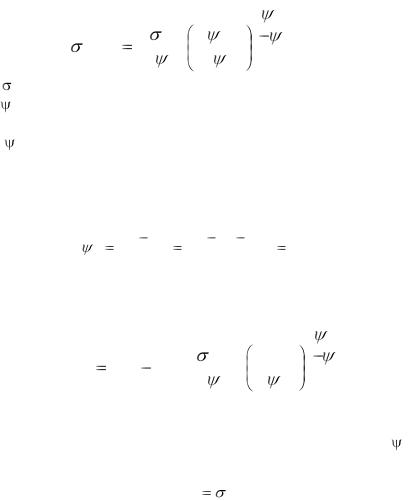
Поскольку рассматривается вырубка – пробивка в холодном состоянии заготовки, напряжение текучести по мере увеличения степени деформации увеличивается вследствие упрочнения.
Если считать, что изменение напряжения текучести в зависимости от степени деформации происходит по степенной зависимости предложенной С.И. Губкиным
|
|
|
|
|
|
|
ш |
|
|
|
в |
|
|
x |
1 |
ш , |
(2.23) |
||
|
|
|
|
|
|||||
S(x) 1- ш 1- |
ш |
|
|
||||||
|
|
|
|
|
где в – временное сопротивление материала заготовки; ш – относительное сужение при растяжении в момент по-
явления шейки;
х– степень деформации.
ичто в качестве эквивалентной степени деформации при вырубке – пробивке можно принять относительное изменение степени среза
|
F0 Fx |
|
aL (a x)L x |
, |
(2.24) |
||
x |
F0 |
|
aL |
|
a |
||
|
|
|
|
||||
|
|
|
|
|
то формула для определения усилия вырубки – пробивки примет следующий вид:
|
|
|
|
|
|
|
|
ш |
|
P L(a x) |
|
в |
|
|
x |
1 |
ш . |
||
|
|
|
|
|
|
||||
|
|
|
|
|
|
|
|||
x |
2(1- |
|
ш ) a ш |
|
|
|
|
||
|
|
|
|
|
|
Исследование полученной зависимости на экстремум позволяет установить существование максимума усилия при x = a ш. Тогда
Рmax |
|
La |
, |
(2.25) |
|
|
|
||||
в 2 |
|||||
|
62
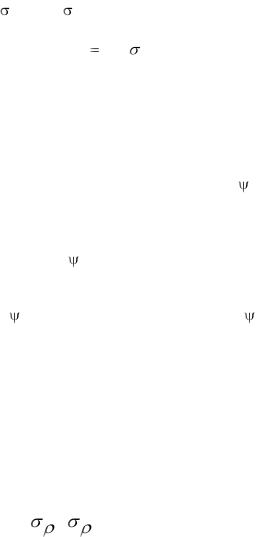
если принять, что ср = 0,71 в, то окончательно получим |
|
Pmax 0,71 cp La . |
(2.26) |
Формула Е.А. Попова является приближенной, так как она получена в результате применения ряда допущений. Однако ценность ее заключается в том, что она вскрывает физическую сущность процесса вырубки – пробивки, показывая, что максимальное усилие деформирования возникает при определенной глубине внедрения пуансона в металл x = a ш, а не в начале деформирования, когда толщина заготовки наибольшая.
Интересно отметить, что на основании полученных данных, зная величину xmax = a ш = h (где h – высота блестящего пояска, глубина проникновения ножа в толщу металла в момент появления трещин скалывания), можно определить относительное сужение ш без испытаний на растяжение: ш = h/a.
Усилие проталкивания и съема Известно, что всякая пластическая деформация металла,
в том числе и деформация, возникающая в процессе вырубки – пробивки, сопровождается упругим формоизменением. При нормальном зазоре между пуансоном и матрицей это может привести к некоторому увеличению поперечных размеров вырубленной заготовки и уменьшению размеров отверстия, в результате чего заготовка (или деталь) остается в рабочем отверстии матрицы, а отход охватывает пуансон (рис. 2.11).
Рассмотренное явление вызывает возникновение нор- |
||
мальных напряжений |
ми |
n на поверхности контакта заго- |
товки и матрицы, отхода пуансона, а следовательно, и сил трения на этих поверхностях.
63
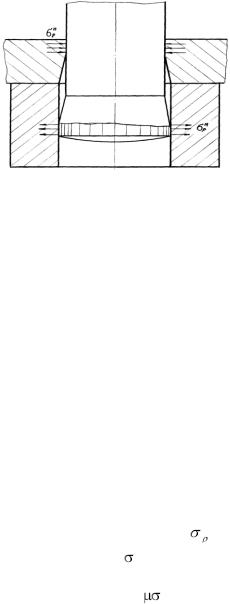
Рис. 2.11. Схема возникновения усилий проталкивания и съѐма
Таким образом, при ходе ползуна пресса вниз ему необходимо преодолеть сопротивление материала вырубки – пробивки, сопротивление сил трения проталкивания заготовки сквозь отверстие в матрице и сопротивление сил трения, приложенных на поверхности контакта пуансона и отхода, а при ходе вверх – сопротивление сил трения съему (снятию) отхода с пуансона.
Практическое значение возможности определения усилий проталкивания и съема заключается не только в уточнении силовых условий вырубки – пробивки и работы деформаций, но и в возможности получения исходных данных для расчета на прочность отдельных деталей вырубных штампов (съемники и их пружины, пуансонодержатели и детали их крепления и пр.).
Если считать, что отход металла соприкасается с пуансоном только в пределах блестящего пояска высотою h и макси-
мальная величина нормального напряжения |
n равна пределу |
текучести штампуемого материала S, то формула для опреде- |
|
ления усилий съема имеет вид |
|
Pcн = Lh S , |
(2.27) |
где L – длина контура штампуемой детали (или заготовки);
- коэффициент трения на поверхности контакта отхода металла и пуансона.
64

Ориентировочно, принимая h = 0,3a, = 0,2, S = cp, получаем:
Pcн = L*0,3a*0,2 cp = 0,06La cp = 0,06P.
Таким образом, для принятых условий усилие съема составляет 6 % от усилия пробивки Р.
По изложенной методике усилие проталкивания должно быть равно удвоенному усилию съема (Рпр = 2Рсн), поскольку при ходе пуансона вниз ему необходимо преодолеть силы трения, приложенные к поверхности контакта пуансона и отхода метала, и равные им силы трения, приложенные к поверхности контакта заготовки и матрицы.
Однако вследствие даже незначительного изгиба отделенной части металла нормальные напряжения М , прило-
женные к поверхности контакта заготовки и матрицы, существенно уменьшаются, поэтому усилие проталкивания оказывается немногим больше усилия съема.
Кроме рассмотренных факторов (длина контура штампуемой детали, условия трения, толщина материала и его механические характеристики), на величину усилий проталкивания и съема существенно влияют: ширина перемычки между соседними отделяемыми контурами (чем она больше, тем усилия проталкивания и съема больше), форма штампуемого контура, величина зазора между пуансоном и матрицей, возможность перекоса отхода металла относительно пуансона и пр.
Поскольку учет этих дополнительных факторов представляет непреодолимые трудности, усилие проталкивания и съема определяется на основании экспериментальных и практических данных в функции усилия вырубки – пробивки по следующим зависимостям:
Р |
|
К |
|
Р |
hм |
|
, |
(2.28) |
|
пр |
пр |
а |
|||||||
|
|
|
|
|
|||||
|
|
|
|
|
|
|
|||
|
РСН |
|
Ксн Р , |
|
(2.29) |
65

где Кпр и Ксн – коэффициенты проталкивания и съема; а - количество заготовок в отверстии матрицы;
hм – высота отверстия матрицы.
Величина коэффициентов проталкивания и съема Кпр и Ксн в зависимости от толщины и рода материала, формы штампуемых деталей, способа их расположения в полосе (или листе) и величины перемычки принимает значение в пределах:
Ксн = 0,05 0,08, Кпр = 0,01 0,09. Чем толще металл и чем больше величина перемычки, тем усилия проталкивания и съема больше.
Способы снижения усилия вырубки и пробивки В отдельных случаях, когда расчетное усилие, необходи-
мое для вырубки – пробивки, больше номинального усилия пресса, предназначенного для выполнения этой операции, применяют различные способы снижения усилия, а именно: вырубку контура по частям, вырубку – пробивку пуансонами со ступенчатым расположением рабочих кромок и вырубку – пробивку при помощи пуансонов и матриц с наклонными (скошенными) кромками.
При вырубке по частям контур заготовки (или детали) получают постепенно, путем вырубки в нескольких специальных штампах. Естественно, что при данном способе штамповки себестоимость детали выше, а точность ее размеров и производительность труда ниже, чем при одновременной вырубке всего контура в одном штампе.
Применение пуансона со ступенчатым расположением рабочих кромок возможно в том случае, когда требуется пробить несколько отверстий в одной детали. При таком расположении пуансонов пробивка отверстий происходит не одновременно, вследствие чего суммарное усилие пробивки снижается.
Ступенчатое расположение пуансонов следует выполнять за счет уменьшения длины пуансонов меньшего диаметра, так как при этом устойчивость их будет выше.
Поскольку максимум усилия вырубки – пробивки соответствует внедрению пуансона в металл примерно на глубину
66
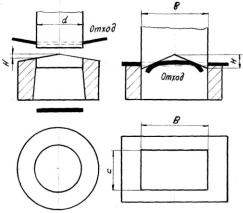
блестящего пояска. Достаточно, чтобы разность в длинах составляла 0,5 мм толщины металла.
Применение пуансонов и матриц с наклонными (скошенными) рабочими кромками дает возможность процесс вырубки
– пробивки осуществлять постепенно, как при резке на гильотинных ножницах, а не одновременно по всему контуру заготовки, как в том случае, когда рабочие плоскости инструмента параллельны друг другу. В результате усилие вырубки – пробивки может быть уменьшено на 30 – 40 %.
Для создания условий, при которых горизонтальные проекции усилий вырубки – пробивки, приложенные к наклонно расположенным рабочим кромкам инструмента, могли бы уравновешиваться, скосы делают симметричными относительно оси инструмента. Это дает возможность углы наклона рабочих кромок инструмента делать больше, чем при резке с односторонним наклоном режущей кромки ножа.
а) б)
Рис. 2.12. Вырубка-пробивка инструментом со скошенными кромками
В зависимости от характера операции (вырубки или пробивки), скосы выполняются на матрице или пуансоне (рис. 2.12). Применение скосов вызывает изгиб той части металла, которая соприкасается с инструментом, имеющим наклонные
67
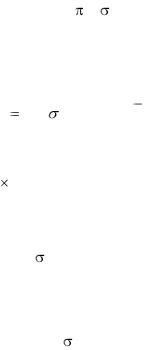
рабочие кромки. Поэтому при вырубке скосы делаются на матрице, а при пробивке – на пуансоне.
В области исследований процесса вырубки – пробивки инструментом со скосами наиболее известны работы Б.П. Звороно и М.Е. Зубцова. В частности, Б.П. Звороно предложены расчетные формулы для определения усилия вырубки – пробивки при самых разнообразных формах рабочих кромок пуансонов и матриц. Так, например, при вырубке круглой в плане заготовки диаметром d в матрице с двусторонним скосом (см. рис. 2.12, а) формулы для определения усилия вырубки – пробивки имеют следующий вид:
а) при высоте скоса H, равной толщине металла:
Рт = ⅔ da cp , |
(2.30) |
б) при высоте скоса Н, находящийся в пределах 0,5 – 1,0 толщины металла:
Р |
2аd |
|
arccos |
H 0,5a |
(2.31) |
cp |
|
||||
Т |
|
|
H |
|
|
|
|
|
|
|
При пробивке прямоугольного отверстия (рис. 2.12, б) с размерами в плане в с пуансоном с двусторонними скосами формулы для определения усилия имеют следующий вид:
а) при высоте скоса Н, равной толщине металла:
Рт = 2а ср(в + 0,5с) , |
(2.32) |
б) при высоте скоса Н больше толщины металла:
Рт = 2а ср(в + с |
0,5а |
) |
. |
(2.33) |
|
||||
|
Н |
|
|
Одним из способов снижения усилия вырубки – пробивки является применение инструмента с так называемой фасон-
68
ной заточкой рабочих кромок пуансона и матрицы. Это придает кромкам волнообразный профиль.
Рекомендации о количестве «волн», их глубине и протяженности приведены в справочной литературе. Фасонная заточка инструмента применяется при вырубке заготовок (или деталей) диаметром свыше 200 ÷ 300 мм.
2.4.Чистовые разделительные операции
Врезультате рассмотрения механизма пластической деформации при резке, а затем при вырубке – пробивке было установлено, что даже при оптимальном зазоре между пуансоном и матрицей боковая поверхность отделенной части металла слегка конусная и шероховатая (исключая поверхность блестящего пояска, высота которого незначительна).
Чистота поверхности скалывания соответствует 3 - 5 классу, чистота поверхности блестящего пояска – 6 - 7 классу чистоты.
Вусловиях производства ряда отраслей машиностроения,
иособенно приборостроения (например, производство часовых механизмов), предъявляются повышенные требования к чистоте боковой поверхности и точности размеров плоских деталей. В частности, требуется, чтобы плоские детали имели точность размеров, соответствующих 3 - 4 классу точности, и чтобы боковая поверхность этих деталей была бы строго перпендикулярна ее плоскости, а чистота (по всей толщине делали) – соответствовала 7 - 9 классу точности.
При массовом и крупносерийном производстве наиболее эффективными способами получения плоских деталей (или полуфабрикатов), удовлетворяющими перечисленным требованиям, является чистовая вырубка – пробивка и зачистная штамповка. Их применение в ряде случаев дает возможность заменить механическую обработку штамповкой и этим существенно повысить производительность труда и снизить себестоимость выпускаемой продукции.
69

2.4.1 Чистовая вырубка и пробивка
Вырубка с обжимкой Особенность вырубки с обжимкой заключается в том, что
листовой материал, предназначенный для получения детали (или полуфабриката), обрабатывается инструментом, имеющим весьма малый зазор между пуансоном и матрицей (Z = 0,01 - 0,02 мм) и скругленную малым радиусом («заваленную») рабочую кромку матрицы. Радиус скругления рабочей кромки матрицы обычно принимается равным половине оптимального зазора, применяемого при обычной вырубке – пробивке (рис. 2.13).
Рис. 2.13. Схема вырубки с обжимкой
Механизм пластической деформации при выполнении чистовых способов вырубки – пробивки, в частности вырубки с обжимкой, использован недостаточно. Научно обоснованные рекомендации по ведению этих процессов отсутствуют, имеются лишь данные, полученные на основании обобщения экспериментов и производственного опыта.
При вырубке в матрице со скругленной рабочей кромкой трещина скалывания возникает у острой кромки пуансона. По мере опускания пуансона отделенная часть металла в виде
70