
Учебное пособие 800606
.pdf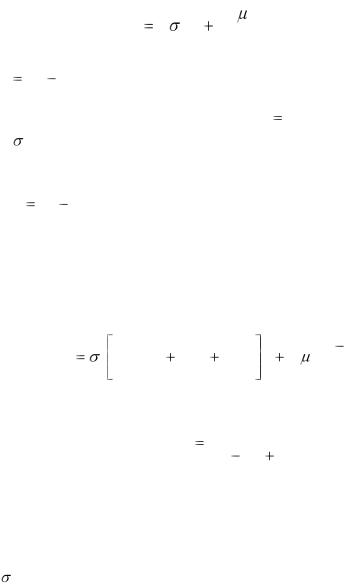
усилие обратного выдавливания
P k1 B (2 |
0,5 d |
)FП , |
|
||
|
S |
где k 1,2 1,5 - коэффициент, учитывающий влияние скорости деформации, упрочнение материала и наличие исходной
воронки в матрице (при малых скоростях k |
1,5 ); |
|
|||||||||||||
|
B - временное сопротивление; |
|
|
|
|
|
|
|
|||||||
F – площадь сечения заготовки; |
|
|
|
|
|
|
|
||||||||
f |
- площадь изделия; |
|
|
|
|
|
|
|
|
|
|
|
|||
k1 |
1,7 1,8 |
- коэффициент, |
учитывающий наличие фас- |
||||||||||||
ки на пуансонах и упрочнение; |
|
|
|
|
|
|
|
|
|
|
|||||
d - диаметр калибрующего пояска пуансона; |
|||||||||||||||
S - толщина стенки стакана; |
|
|
|
|
|
|
|
|
|
||||||
FП |
- площадь сечения по пояску. |
|
|
|
|
|
|
|
|||||||
Формула Овчинникова: |
|
|
|
|
|
|
|
|
|
|
|
||||
|
|
|
D2 |
H |
|
|
d |
|
2 |
|
D3 d 3 |
||||
|
P |
|
0 |
ln R |
|
(1 |
|
|
)R (1 |
|
|
|
|
|
, |
|
S |
|
|
|
|
|
|
|
|
||||||
|
max |
D |
D |
|
|
D |
|
3 |
|
D2 H |
|||||
|
|
|
|
|
|
|
|||||||||
где H - высота заготовки; |
|
|
|
|
|
|
|
|
|
|
|
||||
|
|
|
|
|
|
|
|
|
D2 |
|
|
|
|
|
|
R - степень деформации |
R |
|
|
|
0 |
|
|
|
; |
|
|
||||
|
D2 |
D2 |
d 2 |
|
|
||||||||||
|
|
|
|
|
|
|
0 |
|
|
|
|
|
|
|
|
D0 |
- наружный диаметр пустотелой части заготовки, по- |
лученный обратным выдавливанием;
D - внутренний диаметр пустотелой части заготовки, полученный обратным выдавливанием;
d - диаметр стержня;
S - напряжение текучести.
241
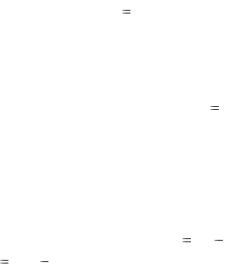
Принимая D0 D , можно получить формулу для прямо-
го выдавливания, а, принимая d = 0, можно получить формулу для обратного выдавливания.
Для технологических расчѐтов бывает достаточной фор-
мула
P qF .
Усилие выталкивания принимается 10 ÷ 15 % от усилия прессования.
Процесс холодного выдавливания применяется также для получения инструмента – прессформ, матриц для вытяжки, высадки и т.п. Мастер-пуансоны изготавливаются из стали
У10А, |
твѐрдость |
HRC 58 60 , удельное давление |
q 230 |
250кг/мм2 . В качестве смазки применяется омедне- |
|
ние. |
|
|
6. ШТАМПОВКА НЕМЕТАЛЛИЧЕСКИХ МАТЕРИАЛОВ
6.1. Неметаллические материалы, применяемые для штамповки
Наиболее часто применяются следующие группы неметаллических материалов:
1)пластические массы и резина: пластики сложной структуры, пластики однородной структуры, резина, эбонит;
2)материалы на основе бумаги: картон, фибра;
3)материалы минерального происхождения: слюда, ми-
каниты.
Неметаллические материалы коренным образом отличаются от металлов по своей структуре, физическим и механическим свойствам. Они имеют меньший удельный вес, малую твердость и низкие механические показатели.
242
Рассматривая механические свойства, их можно разделить на две группы:
а) силовые, к которым относится гетинакс, текстолит и др., обладающие повышенными механическими свойствами, и равноценные, например, алюминию;
б) несиловые – органическое стекло, винипласт. Удельные характеристики у неметаллических материалов
– прочность, отнесенная к удельному весу, выше, чем у металлов, но они имеют преимущество (в коррозионной стойкости и др. свойствах) по сравнению со сталями. Поэтому применение их все более и более расширяется.
6.2. Операция резки
В зависимости от технологии резки все неметаллические материалы должны быть разделены на следующие группы:
1.Материалы, не требующие при штамповке специального термического режима.
2.Материалы, которые перед штамповкой необходимо подвергать термическому режиму.
3.Материалы повышенной хрупкости (слюда, миканит, органическое стекло, гетинакс, эбонит).
4.Материалы средней хрупкости (винипласт, тексто-
лит).
5.Легкоштампуемые материалы (картон, фибра, циллу-
лоид).
6.Волокнистые и упругие материалы, не допускающие резки в штампах обычного типа ( фетр, резина простая и губчатая).
Термический режим заключается, как правило, в подогреве штампуемого материала для обеспечения необходимой для вырубки штампуемости (пластичности). Осуществляется подогрев путем помещения полосы материала в специальные подогревательные устройства (печи или установки для обогрева инфракрасными лучами) или обогревом непосредственно в
243
штампе посредством встроенного в штампы обогревательного устройства того или иного типа.
Конструкция штампов различается в зависимости от свойств штампуемого материала. Штамповка (вырубка или пробивка) неметаллических материалов повышенной хрупкости в обычных штампах невозможна.
Явления, происходящие в хрупких неметаллических материалах, мало исследованы, при разделении их режущими кромками, по-видимому, возникающие при штамповке трещины захватывают довольно глубокий слой материала, что определяет их весьма непривлекательный внешний вид поверхности среза и приводит к выкрашиванию частиц уже после вырубки.
Для уменьшения толщины дефектного слоя материала и улучшения поверхности среза применяются сильный прижим и специальная форма режущих кромок штампа (имеются заостренные передние углы для облегчения резки материала). Острые режущие кромки концентрируют давление на небольшой площади и сводят к минимуму появление трещин.
Для улучшения поверхности среза применяется зачистка. Материалы средней хрупкости могут штамповаться и в штампах обычного типа, например, в штампах последовательного действия, но применение их нежелательно, т.к. фиксация на ловители, используемая в большинстве из них, приводит к повреждению деталей, а использование ножей приводит к излишнему расходу материала. Поэтому для этих материалов следует в основном применять совмещенные штампы, благодаря чему будет достигаться большая точность деталей и использование отходов, а также применение более рационально-
го раскроя.
Для волокнистых материалов достаточной плотности – картон, бумага и др. - наиболее целесообразно применять совмещенные штампы. Использование штампов последовательного действия и в этом случае нежелательно по отмеченным выше причинам.
244
Мягкие и упругие волокнистые материалы и резина штампуются с помощью просечек – специальных контурных ножей, имеющих конфигурацию детали и отверстий в ней. Ножи погружаются в материал до соприкосновения с подкладкой и производят полное разделение материала. Деталь удаляется специальными выталкивателями. В качестве подкладки используется дерево (торцевая поверхность), фибра и др.
Успешно на ряде заводов проводятся опыты по вырубке и пробивке листовой резины толщиной до 2,5 ÷ 3 мм на обычных штампах совмещенного действия (с жестким выталкивателем). При этом обеспечивается удовлетворительная поверхность среза.
Часто применяют просечки для разделки материалов типа картона, бумаги – однако это нерационально, т.к. изготовление просечек некруглой формы весьма трудоемко, стоимость низкая, заточка их затруднена.
6.3. Технология процесса вырубки - пробивки
Технология процесса вырубки и пробивки состоит из следующих трех этапов:
1.Подготовка материала к штамповке (резка на полосы, подогрев).
2.Процесс штамповки, выполняемый в один или несколько переходов.
3.Доделочные операции.
Операция резки неметаллических материалов не отличается от процесса резки металлов, но зачастую производится на специальном оборудовании.
Для резки хрупких материалов часто служат кругопильные станки (как и для обработки дерева) с дисковыми пилами диаметром 300 ÷ 400 мм, толщина пилы 2 мм и разводом 0,3 ÷ 0,5 мм на сторону. Рекомендуемый шаг 4 мм, скорость резания
17 ÷ 20 м/с.
245
Картон, фибра и бумага могут быть нарезаны на обычных гильотинных ножницах с хорошо заточенными и отрегулированными ножами.
Резина и мягкие волокнистые материалы – фетр, войлок - режутся на гильотинных ножницах, при этом резину лучше резать в мокром виде.
Подогрев материала перед штамповкой представляет весьма ответственную операцию. Несоблюдение термического режима ведет к браку, недогрев ведет к появлению трещин, а перегрев – к появлению пузырей и других искажений формы.
Число штамповочных операций и их характер определяются в основном требованиями к чистоте поверхности среза и в меньшей мере к точности размеров детали.
Точность деталей неметаллических материалов ниже, чем у металлических. Это объясняется большими упругими и пластическими деформациями, которые возникают в материалах при штамповке, а также явление усадки при остывании. Предельная точность с применением зачистки: для наружного контура – 4 класс, для отверстий – 3 класс. Обычно точность размеров 4 и 5 классов может быть получена механической обработкой.
Расчеты операционных размеров сводятся к определению припусков на механическую зачистку. Величина размеров припусков определяется, в основном, толщиной дефектного слоя, образовавшегося при вырубке и равного в среднем: для текстолита, гетинакса и эбонита – 25 %, для фибры 20 % от толщины материала.
Величина припусков на зачистку дается равномерной для плавных контуров и уменьшенной на углах. Часто на углах применяется двойная зачистка. Припуски на механическую обработку (проточку, фрезерование, развертку отверстий и др.) по величине могут быть взяты несколько большими (на 30 – 50 %), чем при зачистке на штампах.
При конструировании штампов необходимо учитывать величину усадки изделий. Усадка для органического стекла, например, весьма значительна, в среднем 2,5 – 3 %, а при
246
штамповке текстолита и гетинакса искажением размеров по наружному контуру обычно пренебрегают.
6.4. Гибка
Операции гибки не подвергаются: гетинакс, коллекторный и прокладочный миканиты.
Текстолит подвергается гибке в тонких листах (2 ÷ 3 мм) при обязательном нагреве. При нагреве текстолит приобретает пластичность за счет размягчения смол. Текстолит следует нагревать
быстро в течение 1 – 2 минут при температуре 150 ÷ 170 0 С, т.к. при дальнейшем нагреве смола вновь становится твердой. Нагрев осуществляется в печи или инфракрасными лучами. Гибка осуществляется вручную или на специальных приспособлениях.
Гибка стеклотекстолита осуществляется аналогично текстолиту, но нагрев до 230 0 С.
Гибка органического стекла производится с нагревом до температуры 105 ÷ 150 0 С, время - в зависимости от температуры. Нагрев осуществляется осторожно, т.к. при перегреве образуются пузырьки, а поверхность становится мягкой и затем воспринимает все неровности приспособления.
Перед нагревом заготовки тщательно очищаются от пыли, бумаги и следов клея, промываются водой и мылом. Нагрев осуществляется в подвешенном состоянии. Приспособление для гибки органического стекла изготавливают из пластмасс, дерева и т.п. Применяется окончательная обработка при изготовлении приспособлений – шлифовка.
Гибка винипласта осуществляется при температуре не выше 150 0 С. При более высоких температурах материал расклеивается. Оптимальная температура нагрева 130 ÷ 150 0 С.
Для толщин не менее 8 мм температура нагрева 150 0 С. Нагрев винипласта производится довольно долго.
Гибка винипласта производится в приспособлениях из дерева. Наименьший радиус кривизны должен быть равен
247
приблизительно толщине листа. При гибке необходимо учитывать усадку. Величина усадки тем больше, чем больше температура перед гибкой.
Гибка целлулоида толщиной до 0,5 мм осуществляется при комнатной температуре. Нагрев целлулоида до температу-
ры 90 ÷ 100 0 С. При взрыве и нагреве целлулоид легко загорается.
Гибка эбонита осуществляется аналогично органическому стеклу. Нагрев производится до температуры 70 ÷ 80 0 С.
Гибка картона и фибры производится при влажности материала не менее 10 %. Иногда применяется местное увлажнение ( материал смачивается влажной тряпкой за 20 ÷ 30 мин. до гибки). Гибка производится на машинах и на трехвалковых станах.
Гибка слюды производится только в очень тонких листах (щипанка).
Гибка гибкого миканита осуществляется при нагреве. Со временем деталь теряет форму.
Гибка формовочного миканита производится с нагревом до температуры 80 - 120 0 С. Деталь снимается с приспособления после охлаждения до температуры 30 ÷ 40 0 С.
6.5. Формовка
Формовке подвергается текстолит, стеклотекстолит, органическое стекло, винипласт, целлулоид, картон, фибра и миканиты.
Текстолит, нагретый до 150 ÷ 170 0 С, приобретает пластичность и может формоваться. Формовка осуществляется в прессформах, представляющих собой закрытый вытяжной штамп, работающий до упора. Штампуются преимущественно детали типа тел вращения небольшой глубины (глубина изде-
лия 30 ÷ 40 мм).
248
Стеклотекстолит формуется с предварительным нагревом до 230 0 С.
Органическое стекло формуется при нагреве до 110 ÷ 120 0 С. Время нагрева определяется опытным путем. Формовка производится на болванке или в прессформе.
Винипласт формуется при температуре 130 0 С. Целлулоид не формуется, требуемая форма деталей по-
лучается вытяжной.
Картон, фибра формуются на болванке с предварительным увлажнением. Материал вымачивается водой из решета (1,5 ÷ 2 часа на 1 мм толщины материала).
Миканит формуется без нагрева. При штамповке обладает упругой деформацией.
Формовочный миканит нагревается до 150 ÷ 200 0 С в приспособлениях и штампах при удельном давлении 20 ÷ 50 МПа. Нагрев материала кратковременный.
6.6. Вытяжка
Вытяжке могут подвергаться следующие неметаллические материалы: текстолит, стеклотекстолит, органическое стекло, винипласт, целлулоид, картон, фибра. Кроме того, органическое стекло может подвергаться протяжке.
Вытяжка текстолита производится при нагреве 150 ÷ 170 0 С неглубоких деталей цилиндрической, конической и полусферической формы. Нагрев производится в течение 1 ÷ 2 минут. Вытяжка производится с прижимом заготовки. Радиусы вытяжного ребра не менее 6 ÷ 8 мм.
Вытяжка стеклотекстолита осуществляется при нагреве до 230 0 С. Штампуются детали неглубокой формы.
Органическое стекло. Вытяжка производится в вытяжных штампах или в штампах для выдавливания. Отштампованная деталь охлаждается вместе со штампом до 30 ÷ 40 0 С.
Вытяжка винипласта осуществляется в прессформах, ва- куум-формовочных установках или в штампах. Процесс со-
249
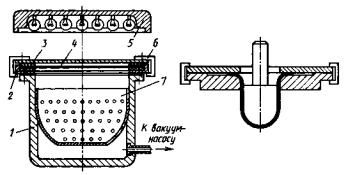
провождается нагревом до 130 0 С с последующим охлаждени-
ем до 30 ÷ 40 0 С в штампе (см. рисунок).
Вытяжка в прессформах производится способом выдувания (давление 1,5 ÷ 2 атм). Листы перед выдуванием смачивают в воде в течение 18 ÷ 96 часов при температуре 18 ÷
20 0 С, нагрев в течении 1 минуты паром при давлении 6 атм. Вытяжка целлулоида производится с нагревом материала
до 95 ÷ 110 0 С в течение 3 ÷ 4 минут. Штамп не подогревается. Глубина вытяжки составляет 70 мм.
а) |
б) |
Схемы вытяжки:
а) в вакуум-формовочных установках,б) в штампе Вытяжка фибры производится в увлажненном состоянии.
Выдержка 1,5 ÷ 2 часа на 1 мм толщины. После вымачивания материал посыпается графитом или тальком. Заготовку помещают в вытяжной штамп из дерева или силумина. Пуансон с деталью просушивают в течение 12 часов при температуре 65 ÷ 70 0 С.
Вытяжка картона производится аналогично вытяжке фибры.
Протягивание органического стекла (деталей с глубокой полостью) производится на универсальном основании, где устанавливаются специальные штампы, которые состоят из пуансона, матрицы, прижима и калибрующего кольца. В таких штампах можно получать изделия с соотношением размеров:
250