
Учебное пособие 800606
.pdf
Механизм деформирования заготовки в операциях вырубки и пробивки одинаков и соответствует ранее рассмотренному механизму резания без снятия стружки (сдвигом).
Поэтому в данном разделе будут изложены только некоторые технологические данные, которые нужно учитывать при проектировании технологических процессов.
Раскрой металла 1) Под «раскроем металла» будем понимать определе-
ние размеров вырубаемых заготовок (полуфабрикатов), обеспечивающих наиболее экономичное расходование металла, т.е. минимальные отходы, наилучшее качество получаемых деталей и наивысшую производительность труда.
Одним из наиболее существенных показателей рациональности раскроя является т.н. «коэффициент использования металла»
Ku |
f * n |
* 100 % , |
(2.12) |
|
LB |
||||
|
|
|
где f – площадь детали без отверстий;
n – количество деталей, получаемых из полосы; L – длина полосы или ленты;
B – ширина полосы или ленты.
Все многообразие применяемых в практике листовой штамповки раскроев можно разделить на две группы по признаку наличия перемычек, по характеру взаимного расположения контуров деталей и полосы. Прежде всего, рассмотрим типы раскроев с перемычками и без перемычек. Естественно, что раскрой без перемычек обеспечивает более экономное использование металла, т.к. за счет сближения контуров последовательно вырубаемых заготовок из полосы той же длины может быть получено большее количество деталей. Однако раскрой без перемычек имеет тот недостаток, что вырубка по существу переходит в отрезку, т.к. отделение заготовки идет не по замкнутому контуру. При последовательном перемещении полосы в зону вырубки и очередном выполнении операции в участках, где смежные контуры имеют общие точки или линии, резания
51
не происходит, т.к. эта часть контура уже подготовлена предыдущей вырубкой. То обстоятельство, что резание идет по замкнутому контуру приводит к ухудшению качества штампуемых деталей и к снижению стойкости инструмента. Объясняется это следующим:
1)Резание по незамкнутой линии приводит к тому, что изгибающие моменты, действующие вдоль резания, вызывают увеличенные прогибы заготовки (остаточные искажения) по сравнению с резанием по замкнутой линии, когда сопротивление прогибу значительно больше (изгиб свободной и защемленной по замкнутому контуру заготовки).
2)Кроме того, распирающие силы при незамкнутой линии резания взаимно не уравновешиваются, что приводит к изгибу пуансона под их действием и, как следствие, к изменению начального зазора между режущими кромками. Изменение же зазора относительно оптимального значения может ухудшить качество среза или привести к преждевременному образованию торцевого заусенца как вследствие более быстрого притупления режущих кромок, так и чрезмерного увеличения зазора.
3)Одним из факторов, вызывающих меньшую стойкость инструмента при вырубке без перемычек, является уменьшение зазора относительно оптимального при изгибе пуансона, благодаря чему растут удельные давления на кромке и притупление режущих кромок идет более интенсивно. Кроме того, стойкость уменьшается за счет увеличения распирающих усилий при уменьшенном зазоре и, наконец, при малых по диаметру пуансонах стойкость последних может быть значительно уменьшена за счет усталостного разрушения в результате периодического действия изгибающего усилия. Таким образом, наличие перемычек, обеспечивающих резание по замкнутому контуру: 1) повышает стойкость инструмента; 2) улучшает качество деталей. Для обеспечения постоянства удельного давления резания по всему периметру вырубаемой заготовки необходимо, чтобы ширина перемычки была не менее ширины зоны пластической деформации, возникающей около поверх-
52
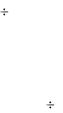
ности разделения. Ранее было указано, что ширина зоны пластической деформации равна (0,2 0,4)S. В случае же перемычек, жесткость которых значительно уменьшена, ширина зоны пластических деформаций может быть больше. Учитывая это можно считать, что равномерное распределение удельного давления резания по периметру будет обеспечиваться, если ширина перемычки будет не менее (0,8 1,0)S (перемычка не будет деформироваться полностью). Однако при назначении ширины перемычки при раскрое нужно учитывать влияние и таких факторов, как: 1) точность подачи; 2) конфигурация вырубаемой заготовки; 3) тип применяемой подачи полосы или ленты; 4) абсолютное значение толщины заготовки. Естественно, что номинальную ширину перемычки следует назначать такой, чтобы при данной точности подачи минимальное значение ширины перемычки не было меньше допустимого. Конфигурация заготовки оказывает влияние на номинальное значение ширины перемычки потому, что одна и та же неточность подачи может вызвать различное изменение ширины перемычки при круглой и прямоугольной вырубаемой детали. Так, например, одно и то же угловое перемещение полосы дает различное изменение ширины перемычки при круглой и прямоугольной форме вырубаемой детали. Естественно, что номинальное значение перемычки для прямоугольной детали (у которой больше изменение перемычки при повороте полосы) должно быть взято большим, чем для круглой, причем в тем большей степени, чем больше длина прямолинейного участка контура в направлении, перпендикулярном направлению подачи.
Кроме создания удовлетворительных условий вырубки перемычка должна обеспечить и определенную жесткость высечки, т.е. отходы полосы после вырубки. Последнее требование оказывается особенно существенным когда, как например при крючковой подаче, перемещение полосы на шаг подачи осуществляется силой, приложенной к перемычке.
Одним из факторов, оказывающих существенное влияние на ширину перемычки, является абсолютное значение толщи-
53
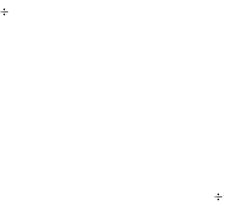
ны заготовки. Требование обеспечения должной жесткости перемычки привело к тому, что применяемые в практике штамповки значения относительной ширины перемычки K1/S, где К1 – ширина перемычки между деталями, а S – толщина полосы, при толщине не меньше 1 мм больше единицы, а при увеличении толщины уменьшается, принимая значение порядка
0,8 0,65.
Кроме указанных факторов на величину перемычки оказывает влияние также ряд механических свойств штампуемого материала. Общая закономерность такова, что чем меньше прочностные характеристики материала, тем больше приходится брать ширину перемычки с целью обеспечения необходимой ее прочности и жесткости.
Учитывая возможные (в пределах допуска) колебания в ширине полосы и непрямолинейность ее боковых кромок, перемычку между краем полосы и контуром вырубаемой детали (боковая перемычка) берут в 1,15 1,3 раза больше, чем между контурами деталей (продольная перемычка).
Из вышеуказанного видно, что штамповка с рационально выбранными размерами перемычек обеспечивает большую стойкость инструмента и лучшее качество штампуемых деталей. Однако в тех случаях, когда к детали не предъявляют высоких требований по точности, в практике штамповки используют штамповку без перемычки, несмотря на пониженную стойкость инструмента.
Объясняется это тем, что при листовой штамповке стоимость металла составляет примерно 40 – 65 % от полной стоимости детали, полученной штамповкой. Поэтому экономия металла, полученная за счет устранения перемычек при штамповке, дает снижение стоимости детали даже при условии некоторого увеличения расхода инструмента.
Стремление получить экономию металла заставляет внимательно подходить не только к назначению размеров перемычки, но и к выбору типа раскроя.
Так, например, в ряде случаев многорядная штамповка дает значительно лучший коэффициент использования метал-
54
ла, чем однородная, что может дать экономический эффект даже при удорожании штампа за счет его усложнения.
Многорядная штамповка осуществляется (для мелких деталей) в штампах, где за один ход получают несколько деталей (по числу рядов), обеспечивая высокую производительность. Этот способ штамповки используется обычно в крупносерийном и массовом производстве. При относительно малых сериях многорядная штамповка (чаще двухрядная) осуществляется за несколько проходов одной и той же полосы (чтобы усложнять штамп и не увеличивать усилие штамповки). Существуют и прессы с автоматической подачей, где лист или широкая полоса подаѐтся зигзагообразно, с поперечным движением, что позволяет вести штамповку в шахматном порядке (обычно используются при штамповке средних по размерам заготовок).
Целям экономии металла служит и комбинированный раскрой, при котором из одной и той же полосы штампуют две (или более) разные детали, причем контур одной детали располагается между смежными контурами другой детали или же между контуром детали и краем полосы (получается как бы штамповка другой детали в отходах от штамповки первой детали). При использовании комбинированного раскроя необходимо, чтобы штампуемые в полосе детали имели бы (по чертежу) одинаковую толщину и изготавливались из одинакового металла. Желательно, чтобы и серийность деталей была одинаковой. Штамповка с комбинированным раскроем может осуществляться как в одном штампе, так и в нескольких штампах, когда каждая деталь штампуется на своем штампе, а заготовкой для одной детали служит высечка другой.
Для штамповки деталей иногда используют и отходы от пробивки сравнительно больших отверстий. В некоторых случаях, как, например, при штамповке колец для конических роликоподшипников из полосы значительной толщины, отход подсаживают и затем из него штампуют деталь с меньшей заданной толщиной.
Единственным типом раскроя, при котором намеренно идут на увеличенный отход металла, является раскрой с вы-
55
резкой перемычки. При штамповке с перемычками этот раскрой применяется для изготовления малых по ширине деталей с целью упрощения изготовления инструмента и повышения его стойкости. Применяемые виды раскроя для простых деталей приведены у В.П. Романовского.
Выбор рационального типа раскроя Необходимость экономии металла предъявляет новые
требования к раскрою и методам его проведения. В большинстве случаев он проводится в настоящее время расчетным и опытно–графическим путем. Но для деталей сложной конфигурации очень трудно найти оптимальное расположение графическим путем. Вопрос этот решается с применением ЭВМ. При решении задач методом математического программирования при большой размерности или при невозможности учета всех производственных особенностей раскроя задача сводится
ксокращению времени на решение вопроса.
Взадачах раскроя листового проката на заготовки сложных геометрических конфигураций требуется задать сведения о детали. Для этого на контуре определяются опорные или узловые точки, т.е. точки, в которых происходит смена контура. Описание контура можно задать перечислением в определенном порядке координат опорных точек и видов линий между ними.
Существует система обработки чертежей детали, по которой по определенным правилам кодируется чертеж детали и, основываясь на этой информации, ЭВМ рассчитывает координаты опорных точек. Информация чертежа заносится в таблицу. Все точки нумеруются в определенном порядке. Для определения раскроя с помощью ЭВМ необходимо иметь данные о размерах и количестве материала и программы. Затем необходимо сформулировать математическую модель заготовки и ввести ее в ЭВМ. При неудовлетворительном коэффициенте раскроя решение можно повторить, уточнив вводную информацию.
56
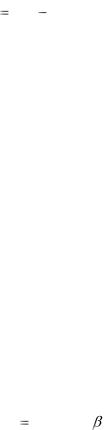
Зазоры при вырубке Основным фактором, влияющим на возможность полу-
чения детали или полуфабриката с чистой боковой поверхностью, является зазор между матрицей и пуансоном. Кроме того, величина зазора существенно влияет на стойкость вырубного инструмента и величину усилия деформирования.
При вырубке – пробивке двусторонний зазор Z между матрицей и пуансоном равен разности их соответственных поперечных размеров:
Z Dm Dп , |
(2.13) |
где Dm - диаметр матрицы; Dп – диаметр пуансона.
Как и при резке листового металла, в условиях вырубки – пробивки существует оптимальный зазор Zопт, при котором складывающиеся трещины, возникающие у острых кромок матрицы и пуансона, совпадают друг с другом в момент разрушения. В этом случае боковая поверхность отделенной части металла получается сплошной и относительно ровной, а стойкость инструмента – наибольшей.
Если зазор между матрицей и пуансоном больше или меньше оптимального, скалывающие трещины не совпадают по направлению, вследствие чего на боковой поверхности отделенной части металла образуется уступ в виде волнистого протянутого заусенца.
Величина двустороннего оптимального зазора при вырубке – пробивке, как и при резке, зависит от толщины и рода материала обрабатываемой заготовки. Оптимальный зазор определяется по табличным данным, составленным на основании обобщения экспериментальных и практических данных, или расчетным путем по формуле
Z опт 2(S - h)tg . |
(2.14) |
57
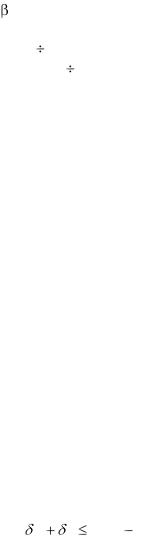
Величины h и зависят от рода материала, его характеристик и механических свойств.
При толщине от 0,3 10,0 мм величина оптимального зазора колеблется в пределах 4 16 % от толщины листа (меньшие значения относятся к меньшей толщине, а большие – к большей). Таблицы оптимальных зазоров при вырубке – пробивке приведены в справочной литературе.
При штамповке особо тонкого металла, менее 0,3 мм, применяют инструмент без специально предусмотренного зазора. В данном случае контур сырого (незакаленного) пуансона получают путем протяжки через термически обработанную матрицу, изготовленную по специальному шаблону.
В условиях высокоскоростной вырубки – пробивки (при числе двойных ходов пресса более 120 в минуту) из–за нагрева зазор увеличивается в 1,2 – 2 раза.
Исполнительные размеры пуансона и матриц при вырубке и пробивке
Расчет исполнительных размеров пуансона и матриц проводится с учетом следующего:
1.Размеры отверстий при пробивке определяются пуансоном, при вырубке размеры детали определяются матрицей.
2.Происходит в процессе работы износ инструмента «в тело», изменение его размеров.
3.Зазор изменяется от Zmin до Zmax.
4.Сумма допусков на изготовление пуансонов и матриц,
обеспечивающих взаимосвязь их не должна превышать разность между зазорами
м |
п Z max Z min . |
Диаметр изделия, получаемого вырубкой, соответствует диаметру рабочего отверстия матриц. Износ матрицы «в тело» приводит к увеличению ее размеров. Поэтому исполнительный диаметр рабочего отверстия вырубной матрицы должен быть наименьшим предельным.
58

Если допуски на штампуемое изделие назначены в системе отверстия, то исполнительный диаметр рабочего отверстия матрицы определяется как разность между номинальным диаметром изделия и допуском на этом диаметре
Dм = (DH - )+ м , |
(2.15) |
где DH – номинальный диаметр штампуемого изделия; |
|
- допуск на диаметр изделия. |
|
При вырубке зазор назначается за счет уменьшения раз- |
|
мера пуансона, поэтому его исполнительный диаметр |
|
Dп = (Dм - Z)- п = (DH - - Z)- п |
(2.16) |
Диаметр отверстия, получаемого пробивкой, соответствует диметру пуансона. Износ пуансона «в тело» приводит к уменьшению его диаметра. Поэтому исполнительный диаметр пуансона должен быть наибольшим предельным.
Если допуски на штампуемое изделие назначены в системе отверстия, то исполнительный диаметр пуансона определяется как сумма номинального диаметра отверстия и допуска на этот диаметр
Dп = (DH + )- п . |
(2.17) |
При пробивке зазор назначается за счет увеличения рабочего отверстия матрицы, поэтому исполнительный ее диаметр
Dм = (Dп + Z)+ п = (DH + + Z)+ м . (2.18)
Методика определения исполнительных размеров матриц и пуансонов для вырубки – пробивки некруглых изделий и отверстий в основном та же. Практика показала, что экономически целесообразно при изготовлении такого инструмента принимать допуск на его изготовление равным ¼ допуска на деталь.
59

При проектировании вырубного инструмента исполнительные размеры с соответствующими допусками ставить на чертеже матрицы при вырубке и на пуансоне – при пробивке, а соответственно, на чертеже пуансона и матрицы давать указание о пригоне с соответствующим зазором.
Стоимость инструмента в числе других факторов зависит от ширины поля допуска на износ. При жестких допусках увеличивается стойкость инструмента.
Допустимая величина зазора при износе может ограничиваться появлением торцевого заусенца недопустимой величины. Однако следует отметить, что вероятность образования торцевого заусенца еще в большей степени зависит от притупления режущих кромок и при вырубке торцевой заусенец появляется в случае притупления режущей кромки пуансона. Причины образования торцевого заусенца рассмотрены ранее.
В заключение отметим, что на качество деталей и стойкость инструмента существенное влияние оказывает равномерность зазора по периметру и точность направления пуансона относительно матрицы.
Усилие при вырубке и пробивке Технологическое усилие вырубки – пробивки зависит в
основном от сопротивления срезу штампуемого металла, его толщины, длины отделяемого контура, формы и состояния рабочих кромок пуансона и матрицы и величины зазора между ними.
Если величина зазора между пуансоном и матрицей находится в пределах нормы, то технологическое усилие вырубки – пробивки приблизительно можно определить по следующей формуле
Рт = Ls cp, |
(2.19) |
где L – длина отделяемого контура. |
|
При условии, что отделяемый контур имеет форму ок- |
|
ружности, формула (2.19) принимает вид |
|
Рт = Ds cp . |
(2.20) |
60