
ШПОРЫ ГОССЫ 2021
.pdfДля обнаружения утечки с помощью ультрафиолетовой лампы в рабочую жидкость кондиционера добавляют специальный краситель, с которым автомобиль должен проработать 1…2 дня. Некоторые автопроизводители добавляют индикатор в хладагент при производстве автомобиля при первой заправке системы. При проверке кондиционер включают, а все магистрали и элементы системы освещают ультрафиолетовой лампой — места утечки хладагента светятся зеленоватым светом.
Станция заправки автомобильных кондиционеров представляет собой блок измерительной аппаратуры которая предназначена для измерения низкого и высокого давления в системе.
Шланги измерительной аппаратуры всегда окрашены в разные цвета, чтобы исключить возможность их неправильного подключения. Корпус, вентиль и шланг манометра низкого давления 2 обычно красного цвета. Манометр подсоединяется к сервисному клапану 8. Это манометр двойного действия, так как он измеряет как абсолютное давление, так и разрежение. Корпус, вентиль и шланг манометра высокого давления 4 обычно синего цвета. Манометр высокого давления подсоединяется к сервисному клапану 6.
Проверку системы на работающем двигателе с помощью блока измерительной аппаратуры производят после подсоединения шлангов по сравнению величин низкого и высокого давления в системе при температуре испарителя, равной температуре окружающего воздуха.
Перед заправкой хладагента в систему необходимо проверить уровень компрессорного масла, наличие утечек хладагента, кроме того, система должна быть вакуумирована для удаления атмосферного воздуха и влаги. Влага может замерзнуть в магистрали системы, что затруднит циркуляцию хладагента. Кроме того, вода вступает в реакцию с хладагентом, образуя кислоты, чрезвычайно коррозионноопасные для элементов системы кондиционирования, а также может привести к возникновению в системе недопустимо высокого давления. Вакуумирование производится с помощью вакуумных насосов, заправка — через сервисные клапаны.
Существует два способа заправки системы хладагентом: заправка жидким хладагентом и заправка системы парами хладагента. Первый способ осуществляется со стороны высокого, второй — со стороны низкого давления.
При заправке используют электронные весы или заправочные колбы, которые определяют необходимое количество хладагента.
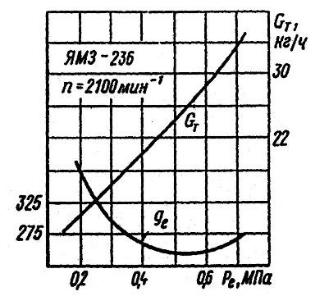
31. Нагрузочная характеристика двигателя внутреннего сгорания.
Нагрузочная характеристика двигателя определяется пропорциональностью главных параметров двигателя, а также показателем нагрузки при неизменных оборотах коленвала. Настоящее определение показывает деятельность мотора машины в движении в одинаковом скоростном режиме, на одной и той же передаче при различных сопротивлениях дорожного покрытия.
Типичный график нагрузочной характеристики мотора
Определяющими параметрами мотора по нагрузочной характеристике считаются GT и ge. Кроме этого, выделяют:
температуру высвобождаемого воздуха;
коэффициент заполнения; коэффициент повышенности газов; ускоренное впрыскивание; токсичность выхлопных газов; задымление (для дизельных
двигателей).
Холостой ход при определённых оборотах соответствует крайней точке характеристики слева. Точка справа — предельной нагрузке, которую двигатель
способен вынести на тех же оборотах.
В карбюраторном моторе снижение мощности при постоянном значении скорости происходит с помощью закрытия дросселя. Плотность снижается, а отсюда количество поступления топлива. Такой тип контроля именуется количественным. При закрытии дросселя экономия мотора изменяется. Её оценка, а также других параметров движка измеряется нагрузочной характеристикой.
Нагрузочная характеристика ДВС зависит от потребления горючего, удельной эффективности такого потребления, а также других параметров при равномерной скорости и режиме тепла.
Изменение часовой затраты горючего зависит от составляющих компонентов топлива, а также показателя заполнения. Одновременно с открытием дросселя сопротивление гидравлики впуска снижается, показатель заполнения поднимается, как и затраты горючего.
Вместе со всем этим процессом меняется качество впрыскиваемого топлива. Показатель избыточности воздуха меняется с требуемой мощностью и контролем экономии топлива.
Завышенные затраты горючего при максимальных параметрах нагрузки можно объяснить насыщением топлива за счёт раскрытия створок экономайзера.
Механический КПД стремится к нулю при холостых оборотах, т. к. вся деятельность движка тратится, чтобы преодолеть механические потери. Также на холостых оборотах происходит обогащение топлива, потому что при открытии дросселя давление и температура снижаются, условия для зажжения искры становятся хуже.
Вместе с открытием дросселя в месте средней нагрузки обогащённое топливо уже не требуется, происходит
32. Основные неисправности ходовой части. Общая проверка ходовой части. Проверка амортизаторов. ТО ходовой части.
К ходовой части автомобиля относятся: кабина, платформа, рама, ступицы колес, подвеска, поворотные кулаки, шкворневые соединения, шины, колеса и др.
Основные неисправности ходовой части:
-изгиб, трещины и изломы продольных балок и поперечин рам;
-ослабление болтовых и заклепочных соединений;
-потеря упругости рессор, поломка их листов;
-утрата работоспособности амортизаторов;
-деформация передней балки;
-изнашивание шкворневых соединений;
-разработка подшипников и их гнезд в ступицах колес.
Общая проверка ходовой части
Для обнаружения дефектов крепления и зазоров в шарнирных соединениях, сайлентблоках, кронштейнах
амортизаторов ходовой части легковых и грузовых автомобилей, в подвеске двигателя, рулевом приводе, подшипниках ступиц колес и т.п., а также выявления мест возникновения различных посторонних стуков и скрипов предназначен детектор люфтов ходовой части и подвески.
Детектор люфтов (рис. 1) представляет собой одну (две) стационарно установленные платформы, состоящие из неподвижных плит с антифрикционными наладками и подвижных площадок, которые лежат на антифрикционных накладках и могут перемещаться под воздействием штоков гидроили пневмоцилиндров, расположенных во взаимно перпендикулярных направлениях.
Принцип работы детектора заключается в принудительном перемещении колеса передней подвески автомобиля знакопеременными силами и визуальном определении соответствующих люфтов. Колеса автомобиля устанавливают на две подвижные площадки, которые под действием привода попеременно, с частотой примерно 1 Гц, перемещаются в разные стороны, имитируя движение колес по неровностям дороги. Сочлененные узлы (шаровые опоры, шкворневые соединения, шарниры рулевых тяг, узел посадки сошки руля и др.) визуально проверяют на недопустимые перемещения, стуки, скрипы.
Контроль соединений осуществляют визуально с помощью подсветки, вмонтированной в переносной пульт управления, на которой размещена также кнопка управления площадками.
Внешними проявлениями неисправности амортизатора являются: продолжительное раскачивание кузова при движении по неровному дорожному покрытию; увеличивающееся колебание кузова при движении по неровному дорожному покрытию; неравномерное и неустойчивое движение колес (подпрыгивание) при движении в определенном диапазоне скоростей, в том числе и на поворотах; отклонение от заданной траектории движения автомобиля при торможении; неустойчивое прохождение поворотов и занос автомобиля; увеличенный износ шин, характеризующийся стиранием рисунка шин; появление щелчков и постороннего шума при движении автомобиля.
Существует несколько методов определения состояния амортизаторов:
-визуальный осмотр;
-раскачивание автомобиля;
-проверка степени нагрева амортизатора;
-оценка поведения автомобиля в движении;
-стендовая диагностика.
Визуальный осмотр предусматривает прежде всего выявление на поверхности корпуса амортизатора подтеков масла, что свидетельствует о потере герметичности и частичном или полном выходе амортизатора из строя.
Раскачивание автомобиля — оценка состояния амортизаторов по количеству колебательных движений кузова при раскачивании стоящего автомобиля до момента полной остановки кузова.
Проверка степени нагрева основана на учете принципа действия гидравлических амортизаторов, которые преобразуют энергию колебаний в тепловую энергию. Из этого следует, что чем теплее амортизатор, тем эффективнее он выполняет свою функцию.
Оценка поведения автомобиля в движении возможна потому, что при неисправных амортизаторах уже на скорости 80…90 км/ч начинает проявляться плохая управляемость автомобиля на дороге, особенно неровной, появляются продольная и поперечная раскачка, снижается курсовая устойчивость.
Стендовая диагностика — самый точный метод определения состояния амортизаторов. Существует два способа данной проверки: на автомобиле при установке его колеса на рабочие площадки вибрационного стенда; проверка величины демпфирующего усилия снятого амортизатора на специальном измерительном стенде. Второй способ дает более точные результаты, однако из-за неудобств и сложностей, вызванных необходимостью снимать амортизаторы, он не нашел широкого применения, тогда как первый способ распространен достаточно широко.
ТО ходовой части
ЕО. Проверить состояние дверей кабины, платформы, оперения, номерных знаков, механизмов дверей, запорного механизма опрокидывающейся кабины, запоров бортов платформы, капота, крышки багажника, заднего борта автомобиля-самосвала и механизма его запора, рамы, рессор, колес, шин, опорно-сцепного (буксирного) устройства, опорных катков (полуприцепа); убедиться в надежности сцепки прицепного состава.
ТО 1. Проверить:
люфт подшипников ступиц колес; осмотром состояние рамы, узлов и деталей подвески, буксирного и опорносцепного устройств;
состояние и действие механизма подъема опорных катков (полуприцепа); крепление стремянок и пальцев рессор, крепление колес; герметичность пневматической подвески;
состояние шин и давление воздуха в них (удалить посторонние предметы, застрявшие в протекторе и между спаренными колесами).
ТО 2. Проверить:
-состояние цапф поворотных кулаков и упорных подшипников, состояние подшипников ступиц передних колес и сальников ступиц, крепление клиньев шкворней;
-состояние и правильность установки балки передней оси. Проверить и при необходимости отрегулировать:
-углы установки передних колес; -при необходимости провести статическую и динамическую балансировку колес. Проверить также:
-правильность расположения (отсутствие перекосов) заднего (среднего) моста, состояние рамы, буксирного устройства, крюков, подвески, шкворня опорно-сцепного устройства;
-крепление хомутов, стремянок и пальцев рессор, амортизаторов, реактивных штанг и оси балансирной подвески;
-герметичность амортизаторов, состояние и крепление их втулок. Проверить:
-состояние и действие механизмов подъема опорных катков полуприцепа; при необходимости заменить втулки.
Отрегулировать подшипники ступиц колес. Проверить состояние:
-колесных дисков и крепление колес; -шин и давление воздуха в них;
-удалить посторонние предметы, застрявшие в протекторе; -проверить крепление запасного колеса.
33.Требования к заготовкам. Методы получения заготовок и технико-экономический анализ их выбора. Особенности получения и применения различных видов заготовок.
Материал заготовок обычно задается конструктором и обозначается на рабочем чертеже детали. Вид заготовки, форму и размеры определяют исходя из условий наибольшей простоты и экономичности обработки с учетом возможностей производства.
Правильный выбор заготовки осуществляется на основе технико-экономических расчетов путем сопоставления себестоимости изготовления того или иного вида заготовки.
При выборе метода получения заготовок учитывают множество факторов, среди которых:
1.Форма, размеры и масса детали
2.Материал;
3.Тип производства;
4.Точность изготовления.
Наиболее широко для получения заготовок в машиностроении применяют следующие методы: -литье; -обработка пластическим деформированием; -резание; -сварка;
-а также комбинация этих методов.
Литье – получение заготовок путем заливки расплавленного металла заданного химического состава в литейную форму, полость которой имеет конфигурацию заготовки.
Обработка пластическим деформированием – технологические процессы, которые основаны на пластическом формоизменении металла.
Сварка – технологический процесс получения неразъемных соединений из металлов и сплавов в результате образования атомно-молекулярных связей между частицами соединяемых заготовок.
Резание – получение заготовки из проката, полученного пластическим деформированием, отрезкой или вырезкой.
Технико-экономический расчет изготовления заготовки производят в следующем порядке: -устанавливают метод получения заготовки согласно типу производства, конструкции детали, материалу и другим техническим требованиям на изготовление детали; -назначают припуски на обрабатываемые поверхности детали согласно выбранному методу получения
заготовки по нормативным таблицам или производят расчет аналитическим методом; -определяют расчетные размеры на каждую поверхность заготовки;
-назначают предельные отклонения на размеры заготовки по нормативным таблицам в зависимости от метода получения заготовки; -производят расчет массы заготовки на сопоставляемые варианты;
-определяют норму расхода материала с учетом неизбежных технологических потерь для каждого вида заготовки (некратность, на отрезание, угар, облой и т.д.); -определяют коэффициент использования материала по каждому из вариантов изготовления заготовок с технологическими потерями и без потерь;
-определяют себестоимость изготовления заготовки, выбранных вариантов для сопоставления и определения экономического эффекта получения заготовки; -определяют годовую экономию материала от сопоставляемых вариантов получения заготовки;
-определяют годовую экономию от выбранного варианта заготовки в денежном выражении.
Литьем получают заготовки фактически любых размеров простой и очень сложной конфигурации почти из всех металлов и сплавов, а также и из других материалов (пластмассы, керамики и т.д.).
Обработкой металлов давлением получают кованые и штампованные заготовки.
Сварные и комбинированные заготовки изготовляют из отдельных составных элементов, соединяемых между собой с помощью различных способов сварки.
34 Требование к технологическому оборудованию, используемому при ТР автомобилей.
Основным принципом разделения постового и контрольно – диагностического оборудования является его функциональное назначение, т.е. отнесение к определенному виду работ.
Группа 1. Уборочно-моечное оборудование. Группа 2. Смазочно-заправочное оборудование. Группа 3. Подъемно-транспортное оборудование.
Группа 4. Разборочно-сборочное и ремонтное оборудование (3 группы). А. оборудование для крепежных работ.
Б. Оборудование для прессовых работ. В. Оборудование для ремонта агрегатов.
Группа 5. Шиномонтажные и шиноремонтные оборудование. Группа 6. Оборудование для окрасочных и антикоррозионных работ.
Группа 8. Нестандартное оборудование - Подставки, козелки, подхваты. - Столы, верстаки, тумбочки, стеллажи. - Нестандартные грузовые тележки для снятия установки агрегатов и узлов автомобиля.
Основными из общих требований являются следующие: производственное оборудование должно быть безопасно при монтаже, эксплуатации и ремонте как отдельно, так и в составе комплексов и технологических схем, а также при транспортировании и хранении. Оно должно быть пожаровзрывобезопасным. Все это рассчитывается на обеспечение безопасности в течение всего срока службы оборудования.
Все виды производственного оборудования должны охранять окружающую среду (воздух, почву, водоемы) от загрязнения выбросами вредных веществ выше установленных норм.
Составные части оборудования должны исключать возможность их случайного повреждения, вызывающего опасность.
Конструкция производственного оборудования должна предусматривать защиту от поражения электрическим током, включая случаи ошибочных действий обслуживающего персонала, а также исключать возможность накопления зарядов статического электричества в опасных количествах.
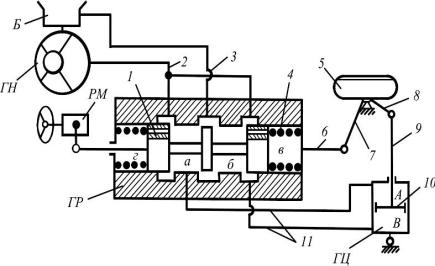
35. Усилитель рулевого управления автомобиля: назначение, схема, устройство, работа, следящее действие усилителя.
Усилители являются частью привода и позволяет уменьшить усилие на рулевом колесе со стороны водителя в 2-3 раза. В зависимости от используемой энергии для создания дополнительного усилия они подразделяются на пневматические, гидравлические, электрические и электрогидравлические.
Наибольшее применение нашли гидравлические усилители, в которых гидравлический насос подаёт масло под давлением в силовой цилиндр через распределительное устройство.
Схема гидроусилителя Б- бачок; ГНгидравлический насос; РМрулевой механизм; ГМгидрораспределитель; ГЦгидроцилиндр; 1 – золотник; 2, 3, 11 – маслопроводы;4 – центрирующая пружина; 5 – управляемое колесо;6, 9 – продольная и поперечная рулевые тяги; 7, 8 – рычаги; 10 – поршень гидроцилиндра
При неподвижном рулевом колесе золотник удерживается в среднем (нейтральном) положении центрирующими пружинами. Полости
распределителя соединены между собой так, что жидкость свободно перетекает из нагнетательной магистрали в сливную. Насос усилителя работает только на прокачку жидкости по системе, а не на поворот колес.
При повороте руля золотник перемещается и перекрывает сливную магистраль. Масло под давлением поступает в одну из рабочих полостей цилиндра. Под действием жидкости поршень со штоком поворачивает колеса. Они, в свою очередь, перемещают корпус распределителя в сторону движения золотника. Как только рулевое колесо перестает вращаться, золотник останавливается и корпус его "догоняет". Восстанавливается нейтральное положение распределителя, при котором опять открывается сливная магистраль и прекращается поворот колес. Так реализуется кинематическое следящее действие усилителя - обеспечение поворота колес на угол, задаваемый водителем при вращении руля.
Такие усилители осуществляют следящее действие по усилию (обеспечивают пропорциональность между усилием на рулевом колесе и сопротивлением повороту управляемых колёс) и по углу поворота (обеспечивают пропорциональность углов поворота рулевого колеса и управляемых колёс).
Рабочее давление, создаваемое насосом, составляет 6-10 МПа, перемещение золотника распределителя- 1-2 мм.
36. Основные неисправности тормозной системы. Общее диагностирование тормозных систем. Стендовые испытания тормозных систем.
К наиболее частным неисправностям тормозной системы относят: 1.Наличие воды в тормозной жидкости
2.Недостаточная толщина фрикционных накладок тормозных колодок, менее 20-30% от нормы
3.Сильный износ тормозных дисков
4.Повреждение защитной манжеты тормозного поршня суппорта
5.Закисание направляющих в скобе суппорта 6.Повреждение резиновых и металлических трубопроводов, которое происходит в
результате механического воздействия или разъедания просочившейся тормозной жидкости. Общее диагностирование тормозных систем в АТО, организациях автосервиса (OA) или
контроль при прохождении государственного технического осмотра включает:
-измерительный контроль эффективности торможения транспортного средства (ТС) рабочей и стояночной тормозными системами, а также устойчивости ТС при торможении рабочей тормозной системой;
-органолептический и, при необходимости, измерительный контроль герметичности пневматического или пневматической части пневмогидравлического тормозного привода и элементов тормозных механизмов колес.
Эффективность торможения ТС измеряют с использованием роликового тормозного стенда для проверки тормозных систем или дорожным методом, если в силу своих размерных или конструктивных характеристик ТС не могут пройти контроль этих показателей на стенде.
Виды стендов и методы испытания тормозных систем Существует несколько видов стендов, использующих различные методы и способы
измерения тормозных качеств: статические силовые, инерционные платформенные и 12 роликовые, силовые роликовые, а также приборы для измерения замедления автомобиля при дорожных испытаниях.
Статические силовые стенды представляют собой роликовые или платформенные устройства, предназначенные для проворачивания «срыва» заторможенного колеса и измерения прикладываемой при этом силы.
Принцип действия инерционного платформенного стенда основан на измерении сил инерции (от поступательно и вращательно движущихся масс), возникающих при торможении автомобиля и приложенных в местах контакта колес с динамометрическими платформами.
Инерционные роликовые стенды состоят из роликов, которые имеют привод от электродвигателя или от двигателя автомобиля, когда ведущие колеса автомобиля приводят во вращение ролики стенда, а от них с помощью механической передачи - и передние (ведомые) колеса.
Силовые роликовые стенды, в которых используются силы сцепления колеса с роликом, позволяют измерять тормозные силы в процессе его вращения со скоростью 2...10 км/ч. Такая скорость выбрана потому, что при скорости 13 испытания больше 10 км/ч незначительно увеличивается объем информации о работоспособности тормозной системы.
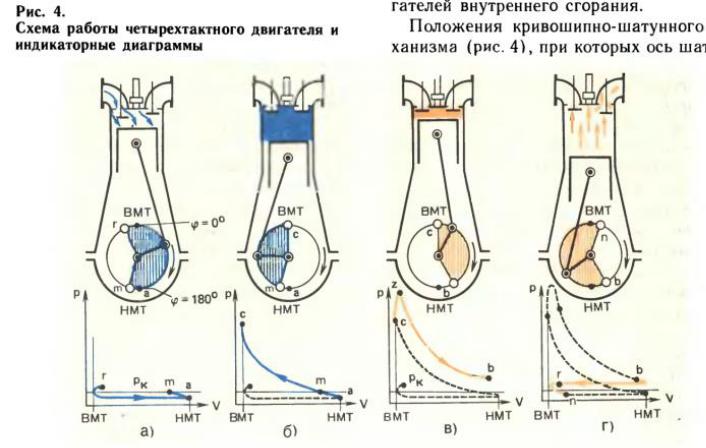
37. Основные процессы ДВС. Процесс впуска.
Как при внешнем, так и при внутреннем смесеобразований рабочий цикл поршневого двигателя состоит из следующих процессов: впуска, сжатия, сгорания и расширения (рабочий ход) и выпуска. Полезная работа совершается лишь в процессе сгорания и расширения.
Первый такт - впуск. В начале первого такта поршень находится в положении, близком к ВМТ (верхняя мертвая точка). Камера сгорания заполнена продуктами сгорания от предыдущего процесса, давление которых несколько больше атмосферного. На индикаторной диаграмме начальному положению поршня соответствует точка r (рис. 4а). При вращении коленчатого вала (в направлении стрелки) шатун перемещает поршень к НМТ (нижняя мертвая точка), а распределительный механизм открывает впускной клапан и сообщает надпоршневое пространство цилиндра двигателя с впускным трубопроводом. В результате движения порщня к НМТ цилиндр заполняется свежим зарядом (воздухом или горючей смесью). При этом вследствие сопротивления впускной системы и впускных клапанов давление в цилиндре становится на 0.01…0.03 МПа меньше давления Pk перед впускными органами. На индикаторной диаграмме такту впуска соответствует линия ra.
Давление перед впусными органами может быть близким к атмосферному в двигателях без наддува или превышать его в зависимости от степени наддува (Pk=0.13…0.45 МПа) в двигателях с наддувом. При наддуве с увеличением заряда в цилиндре увеличиваются работа за цикл и мощность давление и температуры цикла.
38 Система впрыска бензина в автомобильном ДВС: преимущества, классификация, схемы, устройство и работа систем.
Системы питания с впрыскиванием бензина классифицируют по следующим признакам:
по месту подвода топлива — центральный (одноточечный) впрыск, распределенный (форсунки у каждого впускного клапана), непосредственный (форсунки в головке цилиндров);
способу подачи топлива —с непрерывным впрыскиванием (в системах Джетроник типов К и КЕ) и прерывистым впрыскиванием (в системе Л-Джетроник), которое бывает фазированным (подача бензина только на впуске) и нефазированным (подача на каждом обороте коленчатого вала);
способу регулирования количества топлива — пневматические, механические, электронные;
способу определения расхода воздуха — по разрежению во впускном коллекторе, углу поворота дроссельной или специальной (типа «парус») заслонки, показаниям термоанемометрического датчика.
Системы впрыска в зависимости от места подачи топлива делятся на четыре основные группы:
1)с центральным впрыском (в дроссельный узел);
2)с распределенным впрыском топлива в зону впускных клапанов;
3)с впрыском непосредственно в цилиндры двигателя;
4)с впрыском в дополнительные камеры сгорания (форкамеры, вихревые
камеры).
Впрыск топлива может производиться непрерывно или циклами. Непрерывное впрыскивание осуществляется во впускную систему обычно
одновременно во все цилиндры (центральный впрыск). При этом количество подаваемого топлива может регулироваться изменением давления впрыскиваемого топлива или хода иглы форсунки.
В последнее время преимущественно используется цикловое впрыскивание во впускную систему, которое может производиться одновременно во все цилиндры — групповой впрыск, одновременно в два цилиндра пли по очереди в каждый из цилиндров — фазированный. Фазированный впрыск может производиться во впускной клапан, непосредственно в цилиндр, в дополнительную камеру. Регулирование количества подаваемого топлива осуществляется изменением времени открытия клапана электромагнитной форсунки.
Широкое распространение получили системы впрыска с микропроцессорным управлением вследствие необходимости обеспечения высокого быстродействия для выполнения жестких норм на выброс токсичных веществ с отработавшими газами (Евро-2, Евро-3 И Евро-4), что потребовало применения трехкомпонентных каталитических нейтрализаторов.
Система центрального впрыска топлива
Система центрального впрыска бензина обеспечивает более высокую точность дозировании топлива по сравнению с карбюраторном системой при небольшом