
ШПОРЫ ГОССЫ 2021
.pdf9. Оборудование, применяемое при гостехосмотре. Типы диагностических станций.
Диагностические станции, производящие гостехосмотр, должны иметь соответствующее оборудование для проверки ТС, которое подразделяется на обязательное и рекомендуемое.
Приведем перечень обязательных средств технического диагностирования. Средства распознавания: устройство автоматического распознавания ТС (видеокамера).
Средства для диагностирования тормозных систем: -роликовый тормозной стенд для проверки тормозных систем; -рулетка (для проверки мототранспортных средств); -секундомер;
-прибор (комплект манометров, датчик) для проверки пневматического тормозного привода; -прибор для проверки тормозных систем дорожным методом –деселерометр –применяется
для ТС, которые в силу своих размерных или конструктивных характеристик не могут пройти диагностирование на роликовом тормозном стенде.
Средства для диагностирования рулевого управления:
-прибор для проверки суммарного люфта в рулевом управлении (люфтомер); -Стенд для проверки зазоров рулевого механизма, привода и подвески (тестер люфтов).
Средства для диагностирования внешних световых приборов: -прибор проверки внешних световых приборов; -линейка; -секундомер.
Средства для диагностирования стекол — прибор для проверки светопропускания стекол.
Средства для диагностирования колес и шин: -шинный манометр;
-измеритель глубины протектора шин (прибор, калибр-шаблон, штангенциркуль). Средства для диагностирования двигателя и его систем:
-газоанализатор для измерения содержания СО и СН; -дымомер;
-прибор для проверки герметичности газовой системы питания ТС (течеискатель). К рекомендуемым средствам технического диагностирования относятся:
-стенд измерения бокового схождения колес; -стенд для проверки амортизаторов; -стенд для оценки точности показаний спидометра;
-прибор для контроля качества тормозной жидкости; -прибор для проверки подлинности маркировки; -прибор для проверки подлинности документов;
-набор манометров для проверки пневматического тормозного привода.
Обработка результатов контроля технического состояния ТС производится путем регистрации полученных значений измеряемых величин и заключений о соответствии установленным требованиям контролируемых показателей, а также обеспечения их хранения и передачи в установленном порядке.
Обработку результатов контроля технического состояния ТС проводят с использованием компьютерного оборудования и соответствующего программного
обеспечения. |
Компьютерное |
оборудование, |
обеспечивающее |
работу |
средств |
технического |
диагностирования, |
а также |
регистрацию результатов |
контроля |
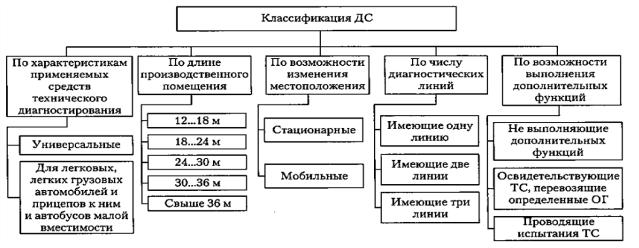
технического состояния ТС, должно соответствовать параметрам, указанным изготовителями средств технического диагностирования
Типы диагностических станций
Классификация диагностических станций, функционирующих в Республике Беларусь
Взависимости от технических характеристик диагностического оборудования, касающихся величины нагрузки, воспринимаемой от массы проверяемого ТС, диагностические станции подразделяются на универсальные(допустимая величина воспринимаемой нагрузки превышает 3 т на ось ТС) и так называемые легковые (допустимая величина воспринимаемой нагрузки не превышает 3 т на ось ТС), предназначенные для контроля технического состояния легковых (категория М1легких грузовых (N1) автомобилей и прицепов к ним (O1и О2), автобусов малой вместимости
(М2).
Взависимости от способности производственного помещения ДС обеспечить стендовую проверку тормозной системы с размещением внутри этого помещения одного ТС или автопоезда ДС подразделяются по длине При этом учитываются значения габаритной длины типовых ТС отдельных категорий, а также допустимые значения длины автопоезда, предусмотренные действующими Правилами дорожного движения.
Стационарная ДС должна иметь необходимое количество специальных
помещений и иных сооружений, обеспечивающих как проведение соответствующих контрольно-диагностических работ, так и высокий уровень приема и обслуживания заказчиков. Кроме того, такая ДС должна располагать полным комплектом средств технического диагностирования для проведения этих работ.
|
Мобильная ДС, т.е. станция, не имеющая постоянного места дислокации, может |
||||
на |
временной основе |
использовать |
для |
проведения |
гостехосмотра |
неспециализированные помещения и сооружения производственно-технической базы автотранспортных предприятий. При этом также допускается при наличии соответствующих внешних условий размещение мобильных ДС на открытых площадках.
Площадки открытого типа для размещения диагностического оборудования мобильной ДС должны быть оборудованы осмотровой канавой и навесом для защиты оборудования и персонала ДС от атмосферных осадков. Кроме того, на мобильных ДС допускается наличие отдельных технологических постов, размещенных в разных помещениях впределах территории одной организации.
По производительности ДС подразделяются в зависимости от числа имеющихся в распоряжении диагностических линий.
10 Методы оценки и измерения износов. Примеры изнашивания деталей автомобилей.
Методы оценки износа деталей разделяют на производственные и лабораторные. К производственным относятся метод микрометрирования детали и метод косвенной оценки по изменению эксплуатационных характеристик сопряжения; к лабораторным (исследовательским) методам — взвешивание деталей, определение количества железа в масле картера, применение радиоактивных изотопов, метод искусственных баз, профилографирование.
Метод микрометрирования основан на измерении линейных размеров деталей, бывших в эксплуатации, с использованием универсальных измерительных средств (микрометров, штангенциркулей, индикаторных приборов и др.).
Оценка износа по изменению эксплуатационных характеристик
сопряжения или узла широко используется в производстве. Например, износ деталей масляного насоса косвенно может быть определен по падению давления масла, износ деталей поршневой группы двигателя — по пропуску газов в картер двигателя, износ подвижного соединения — по изменению его температуры в процессе эксплуатации, например в подшипниках скольжения и т.д.
Метод взвешивания заключается в определении массы детали до эксплуатации и после нее. Этот метод применять нельзя, если превалирующим является износ от пластического деформирования деталей.
Определение количества железа и других продуктов износа в масле заключается в химическом анализе отработанного масла. Недостатком способа является невозможность определения износа каждой детали узла. Преимущество — отсутствие необходимости разборки агрегата.
Метод радиоактивных изотопов основан на использовании изотопов вольфрама, сурьмы или кобальта, вводимых в поверхностный слой рабочей поверхности детали. Интенсивность излучения масла, регистрируемого специальными приборами (счетчиками), является показателем интенсивности изнашивания детали.
Метод искусственных баз, предложенный М.М. Хрущевым и Е.С. Берковичем, заключается в нанесении на рабочую поверхность новой детали специального углубления (лунки) или выточки. По изменению размера углубления после определенного времени эксплуатации определяют расчетом линейный износ в пределах этой поверхности.
Метод профилографирования основан на определении с помощью профилографа весьма малых износов у таких деталей, как поршневые пальцы, плунжеры.
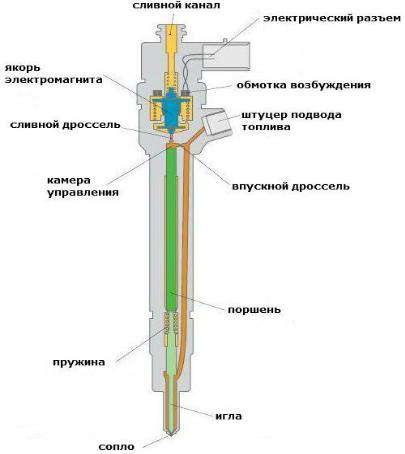
11. Электрогидравлическая форсунка сист. питан. Common Rail: назначение, схема, устройство, работа.
Работа
электрогидравлической форсунки осуществляется посредством изменения давления топлива в момент подачи его в камеру сгорания. Последовательность этапов работы инжектора:
- Игла изолирует камеру сгорания, т.к. на нее давит поршень, находящийся под давлением топлива в камере управления.
- На электрический разъем подается сигнал
- Срабатывает электромагнитный клапан.
- Сливной дроссель открывается, и горючее попадает в топливную линию.
-Игла поднимается, т.к. давление на поршень падает.
-Топливо впрыскивается в камеру сгорания.
Электрогидравлическая форсунка используется на дизельных двигателях, в т.ч. оборудованных системой впрыска CommonRail. Конструкция электрогидравлической форсунки объединяет электромагнитный клапан, камеру управления, впускной и сливной дроссели.
Принцип работы электрогидравлической форсунки основан на использовании давления топлива, как при впрыске, так и при его прекращении. В исходном положении электромагнитный клапан обесточен и закрыт, игла форсунки прижата к седлу силой давления топлива на поршень в камере управления.
Впрыск топлива не происходит. При этом давление топлива на иглу ввиду разности площадей контакта меньше давления на поршень. По команде электронного блока управления срабатывает электромагнитный клапан, открывая сливной дроссель. Топливо из камеры управления вытекает через дроссель в сливную магистраль. При этом впускной дроссель препятствует быстрому выравниванию давлений в камере управления и впускной магистрали.
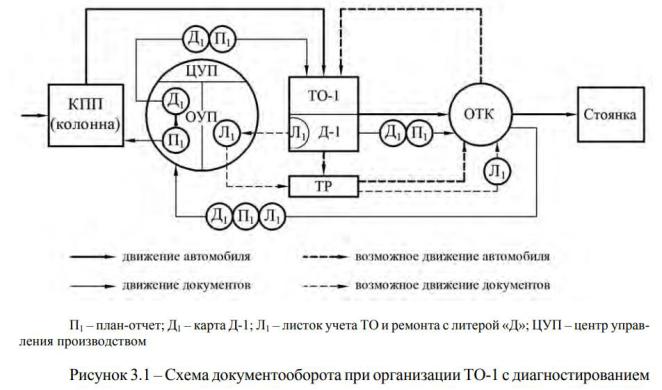
12. Схема документооборота для системы ТО и ТР автомобилей в ОАС.
Планирование постановки автомобилей в ТО-1 сД-1.
Планирование производится ОУП по фактическому пробегу, отражаемому в лицевой карточке автомобиля . Действующим ТКП 248-2010 допускаются отклонения планируемой периодичности ТО на ±10 % от нормативной. На основании данных лицевых карточек автомобилей, скорректированной нормативной периодичности и расчетной суточной программы ТО-1 ОУП составляется план-отчет ТО в трех экземплярах, которые передаются согласно
приведенной на рисунке 3.1 схеме: − первый экземпляр – механику КТП (колонны) не позднее, чем за сутки до постановки автомобилей в ТО-1 с Д-1; − второй экземпляр вместе с комплектом бланков диагностических карт Д-1 – бригадиру зоны ТО-1 перед началом смены; − третий экземпляр – в транспортный участок комплекса подготовки производства дежурному водителю-перегонщику.
Механик КТП (колонны) на основании полученного плана-отчета ТО предупреждает водителя перед выездом на линию о запланированном ТО-1 (эта информация дублируется обычно через службу эксплуатации, которая проставляет штамп «ТО-1» в путевом листе) и после возвращения автомобиля в парк контролирует подготовку его водителем к проведению ТО-1 с Д-1, что включает в себя: контроль качества уборочно-моечных работ; контроль постановки автомобиля на специальные места ожидания с удобным выездом;контроль отсутствия на автомобиле включенных противоугонных устройств и запоров.
С началом работы зоны ТО-1 с Д-1 перегонщик доставляет автомобиль на рабочие посты (линию) для выполнения работ в соответствии с принятой технологией. В процессе проведения регламентных работ ТО-1 с Д-1 бригадир заполняет диагностическую карту Д-1, по их окончании делает отметку вплане-отчете о техническом обслуживании и ставит подпись в диагностической карте.

Контролер ОТК проводит выборочный контроль полноты и качества выполнения работ (20–30 % суточной программы), подписывает диагностические карты Д-1 и план-отчет ТО. Если в процессе выполнения работ ТО-1 или, что чаще всего, работ Д-1 выявляются неисправности по тормозам, рулевому управлению, переднему мосту, ходовой части, устранение которых не предусмотрено технологией ТО-1 и утвержденным перечнем сопутствующих работ (для их выполнения требуется более 5–10 чел.-мин), то бригадиром выписывается ремонтный листок и передается в ОУП.
Диспетчер ЦУП вносит заявку в свой оперативный сменный план, дает указание водителю-перегонщику доставить автомобиль после окончания работ ТО-1 с Д-1 на рабочий пост зоны ТР и принимает меры к организации технологической подготовки указанных в ремонтном листке работ. Специализированной бригаде комплекса ТР дается задание на выполнение работ, как правило, в межсменное время с тем, чтобы утром автомобиль был готов к выходу на линию. В конце смены бригадир ТО-1 передает весь комплект заполненных и подписанных документов (план-отчет ТО, диагностические картыД-1) в ОУП для обработки и анализа.
Документооборот при организации производства ТР автомобилей.
Дежурный ЗОР осматривает автомобиль, проверяет качество мойки, комплектность (наличие зеркал, подфарников и т. д.) и ставит в листке учета ТО и ремонта автомобиля в специальной графе штамп ЗОР – «Автомобиль вымыт, комплектен, принят», свой шифр и подпись. После этого автомобиль считается принятым и за его сохранность несет ответственность инженернотехническая служба АТП, а перегон в зону ТР и с участка на участок осуществляют водители-перегонщики комплекса подготовки производства.
13. Внешний уход за автомобилем. УМР Оборудование и применяемые технологии
Классификация оборудования для уборочно-моечных работ. По способу выполнения: Ручная; Механизированная; Комбинированная. Ручная мойка производится струей воды, низкого и высокого давления с помощью моечного пистолета. Механизированная мойка - осуществляется с помощью специальных установок, которые классифицируются по следующим признакам: 1 Конструкция рабочего органа.2 Струйные, щеточные и струйнощеточные. 3 Относительному перемещению автомобиля и рабочих органов. 4 Проездные и подвижные установки. Условию применения. Стационарные и передвижные. Оборудование поста ручной мойки автомобилей. Для малых АТП ручная мойка, при всех её недостатках, экономически оправдана. На посту ручной мойки применяют: 1 Широкие канавы с колейным мостом; 2 Эстакады; 3 Подъемники; 4 Площадки и канавы. Пол водонепроницаемый с уклоном в 2-3% в сторону трапа для сточной воды. 4 Системы водопроводных труб; 5 Шланги с моечными пистолетами; 6 Насосные станции.
Аппараты высокого давления. Назначение, характеристика, отличительные особенности, причины выхода из строя. Для мойки автомобилей используются аппараты высокого давления, с рабочим давлением 10-15 МПа, расходом воды до 400 (600) литров в час. Используя дополнительные приспособления, аппараты высокого давления позволяют проводить пескоструйную и санитарную обработку. Струя воды с давлением более 15 МПа разрушительна для лакокрасочных покрытий, а с давлением более 20 МПа отчищает поверхность от ржавчины. Классификация аппаратов высокого давления: 1 Бытовые (детали из пластмассы, ресурс 120-150 часов, длительная работа запрещена); 2 Полупрофессиональные (металлические детали, ресурс в несколько раз больше); 3 Профессиональные (поршни из износостойких материалов, ресурс несколько тысяч часов); 3 Промышленные (для непрерывного обслуживания большого количества автомобилей, ресурс несколько десятков тысяч часов).
Основной неисправностью аппаратов высокого давления является падение производительности насоса и связанного с этим уменьшение рабочего давления, является вследствие утечек/потерь жидкости через изношенные сальники плунжеров насоса, износа перепускного клапана и плунжерного насоса.
Причинами выхода из строя является низкое качество жидкости, проявляющееся в большом содержании механических примесей и высокой жесткости жидкости.
Струйная установка для мойки автомобилей. Назначение, характеристика, достоинства и недостатки. В струйной моечной установке в качестве рабочего органа используются форсунки, установленные в подвижных или не подвижных коллекторах, на которые подается моечный раствор. Установка состоит из 4-ех механизмов, установленных попарно с обеих сторон моечного поста. При въезде на пост находится рамка предварительного смачивания, при выезде – рамка ополаскивания. Автомобиль перемещается своим ходом или на конвейере. Существуют также струйные моечные установки с подвижным порталом для мойки автомобиля снизу. Струйные моечные установки применяют для мойки автомобилей со сложной конфигурацией. Этот тип моечных установок отличается универсальностью, простотой конфигурации, малой металлоемкостью, компактностью. Преимуществами струйной моечной установки являются: 1 Отсутствие механического воздействия; 2 Струи воды очищают все наружные поверхности автомобиля. Недостатки: 1 Большой расход воды; 2 Низкое качество мойки; 3 Не обеспечивается мойка внутренних поверхностей кузова.
Щеточные моечные установки. Назначение, характеристика, конструктивное исполнение, достоинства и недостатки. Рабочим органом щеточной моечной установки являются цилиндрические вращающиеся щетки. Механическое воздействие на грязные поверхности повышает качество и производительность мойки, снижает расход воды и моющих средств. Применяют для легковых автомобилей, автобусов и автофургонов. Активная механическая часть этих установок состоит из вертикально (2-8) и горизонтально (1-2) расположенных цилиндрических щеток, снабженных индивидуальными приводами. Для смачивания и ополаскивания кузова устанавливают П и Г образные рамки с форсунками.
Вертикальные щетки бывают: 1 На жесткой подвеске (моют бока автомобиля); 2 Качающиеся боковые (нижняя часть кузова остается непромытой); 3 Шарнирные («обволакивают» поверхность автомобиля). Щеточные моечные установки делятся на:
1 Передвижные. Представляют собой П-образную арку, перемещающуюся по рельсовому пути, уложенному на моечном посту. Состоит из 2-ух вертикальных и 1-ой горизонтальной щеток и устройства для обдува воздухом. Время мойки 5-6 минут. Применяются на небольших СТО; Стационарные. Преимущества: 1 Значительная экономия воды по сравнению со струйной установкой; 2 Большая производительность. Недостатки 1 Недостаточное качество мойки;2 Ограничения по габаритам автомобилей.
Струйно-щеточные установки. Назначение, характеристика, достоинства и недостатки. Струйно-щеточные установки представляют собой комбинированные устройства из щеток и форсунок. Основная нагрузка по удалению загрязнения приходится на струйный аппарат, щетки являются дополнением. Используются для мойки легковых, грузовых автомобилей, автобусов, автофургонов. Механизация процесса значительно сокращает время, затрачиваемое на мойку. Рабочие органы совершают колебательные или круговые движения, а ротационные щетки делаются поворотными для более полного охвата обрабатываемой поверхности автомобиля. С этой же целью щетки выполняются спаренными распашными.
Портальные моечные установки. Назначение, составные элементы, характеристика. Автоматическую портальную мойку выгодно отличают небольшая занимаемая площадь и высокая производительность, около 12 машин в час. Действующими элементами автоматической мойки являются щетки и разнообразные арки. Арка высокого давления оснащена сдвоенным блоком подвижных сопел, обеспечивает очистку кузова автомобиля. Полной очистке способствуют аналогичные боковые блоки. Арка пенной мойки, путем глубокого воздействия очистителя в виде пены, повышает общую эффективность очистки. Несколько совместно действующих щеток очищают переднюю и заднюю части автомобиля. Необходимый уровень прижима щеток и согласование их движения с контурами автомобиля обеспечивается постоянным электронным контролем. Особая функция нагрева воска обеспечивает, так называемое, «горячее вощение». Арка ополаскивания может иметь несколько дополнительных элементов. Мойщик шасси позволяет эффективно удалять грязь из труднодоступных полостей автомобиля. При этом повышается антикоррозийная стойкость днища и увеличивается срок службы элементов подвески. Блок мойки колес бережно очищает колеса и колесные диски любого типа. Арка сушки состоит из двух вертикальных и горизонтального блока. Мощные вентиляторы, попеременно приближаясь и удаляясь, отслеживают контур кузова, создавая оптимальную аэродинамику воздушных потоков.
14. Выбор баз, принцип постоянства базы и совмещение баз. Погрешности установки.
Наибольшей точности обработки детали можно достигнуть в том случае, когда весь процесс обработки ведется от одной базы с одной установки, т.к. ввиду возможных смещений при каждой новой установке вносится ошибка во взаимное расположения осей поверхностей. Т.к. в большинстве случаев невозможно полностью обработать деталь на одном станке и приходится вести обработку на других станках, то в целях достижения наибольшей точности все дальнейшие установки детали на данном или другом станке производить по возможности на одной и той же базе.
Принцип постоянства базы – состоит в том, что для выполнения всех операций обработки детали используют одну и ту же базу.
Если по характеру обработки это невозможно, то в качестве новой базы надо выбирать такую обработанную поверхность, которая определяется точными размерами по отношению к поверхностям, наиболее влияющим на работу детали в собранной машине; если при этом базовая поверхность не является измерительной, производят проверочный расчет допуска на выдерживаемый размер и в случае необходимости – пересчет допусков на размеры базовых поверхностей, т.е. прибегают к более жестким технологическим допускам на размеры этих поверхностей.
При обработке заготовок на станках и их установке в приспособлениях во многигих случаях нет необходимости в полной ориентировке заготовок с использованием всего комплекта из трех баз, контактирующих с шестью опорными точками приспособления или станка. Так, например, при обработке плоскости призматической заготовки ориентировка заготовки на станке в направлении горизонтальных осей координат для получения требуемого размера, не имеет значения, поэтому боковые поверхности заготовки теряют значение баз.
При обработке цилиндрических заготовок для их базирования во многих случаях тоже нет необходимости в использовании комплекта всех трех баз.
Например, при сквозном сверлении и растачивании заготовки, закрепленной в патроне, используется только одна двойная направляющая база, находящаяся в контакте с четырьмя опорными точками. При растачивании ступенчатого отверстия, когда выдерживается линейный размер а, необходимо использовать две базы: двойную направляющую и опорную.
При установке валиков в центрах они базируются по коротким крутым конусам центровых отверстий с помощью пяти опорных точек и лишаются пяти степеней свободы. При этом у валиков сохраняется шестая степень свободы - возможность вращения вокруг собственной оси, необходимая для обработки. При этом используемый в подобных случаях хомутик отнюдь не является шестой опорной точкой, так как он не участвует в базировании заготовки и не ориентирует ее положение, а служит только для передачи заготовке вращения.
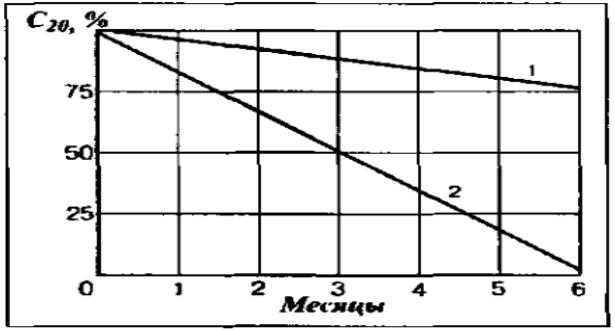
15. Эксплуатация стартерных аккумуляторных батарей для легковых автомобилей.
Снижение емкости С вследствие саморазряда при бездействии аккумуляторных батарей:
1 - необслуживаемых; 2 - традиционных Крепление батареи должно максимально предохранять ее от вибрации и
тряски при движении автомобиля. При вибрации и тряске батарея не должна перемещаться по опорной площадке. Посадочные места для батареи должны иметь амортизаторы и амортизационные прокладки.
Немаловажными в процессе использования аккумуляторной батареи являются условия, в которых она содержится. Рекомендуется раз в три месяца протирать батарею, особенно ее верхнюю часть, на которой могут быть следы электролита, влажной тряпкой, во избежание возникновения нежелательной электрической связи. Обязательно выкиньте тряпку сразу после протирки. Плюсовые и минусовые клеммы аккумулятора должны быть закрыты специальными коробами или смазаны густой нейтральной смазкой во избежание их окисления и последующей коррозии. Чтобы не разрядить аккумулятор, пуск двигателя автомобиля в условиях минусовых температур рекомендуется производить короткими (до 10 секунд) включениями стартера, с интервалом не менее полминуты. Допускается использование аккумуляторных батарей, если напряжение разомкнутой цепи батареи (без нагрузки) составляет не менее 12,6 Вольт, напряжение под нагрузкой должно быть не ниже 11 Вольт. Напряжение измеряется датчиками автомобиля или нагрузочной вилкой. Плотность электролита во всех аккумуляторах (ячейках АКБ) должна быть не ниже 1,26г/см3. В случае, если произошел глубокий разряд батареи, необходимо как можно скорее произвести ее заряд. В условиях низких температур снижение плотности электролита может привести к замерзанию АКБ, что влечет за собой разрушение пластин и корпуса. Заряд АКБ может производиться двумя способами - при