
ШПОРЫ ГОССЫ 2021
.pdf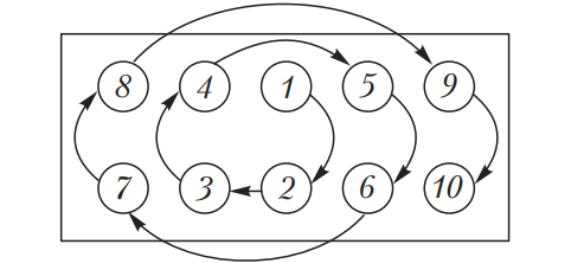
82 Регулировочные работы и ТО двигателя. Диагностирование газораспределительного механизма. Особенности выполнения ТО ГРМ.
В случае необходимости, а для старых моделей двигателей периодически, при ТО осуществляется проверка крепления головки блока цилиндров в определенной последовательности (рис. 1) моментом затяжки, индивидуальным для каждого двигателя.
Общий принцип затяжки: болты начинают затягивать от центра, удаляясь к периферии по спирали. Чугунную головку крепят в горячем состоянии, а головку из алюминиевого сплава — в холодном.
После пробега каждых 50…200 тыс. км (в зависимости от модели двигателя) меняется зубчатый ремень привода ГРМ. После установки зубчатого ремня следует проверить и при необходимости установить требуемое натяжение. Проверку производят с помощью специального прибора для измерения натяжения ремней, а при его отсутствии правильность натяжения проверяют поворотом ремня рукой: ремень должен поворачиваться на 90° вокруг своей оси. Натяжение ремня осуществляется натяжным роликом.
Рис. 1. Порядок затяжки болтов (1…10) головки цилиндров
Для определения натяжения ремня применяют приборы, в которых используется принцип струны — при разных натяжениях она издает звуки разных октав. Для определения звуковых волн создан специальный акустический прибор, который подносится к ветви ремня. Измерение натяжения ремня производится по вибрации ремня, получаемой при оттягивании ремня пальцем и его отпускании, а считывание подтверждается звуковым сигналом. На дисплей прибора выводится определенная частота колебаний (в герцах) соответствующей степени натяжения. Частоту настройки сравнивают со справочными данными.
При эксплуатации автомобиля в результате изнашивания и нагрева механических частей ГРМ изменяется зазор между рычагами (коромыслами) клапанов и кулачками распределительного вала (в двигателях других типов — между распределительным
валом и толкателями, между коромыслами и клапанами). Поэтому периодически (примерно через каждые 30 тыс. км пробега), а также при любых ремонтах механизма или снятии головки блока цилиндров следует проверить и в случае необходимости отрегулировать этот зазор в двигателях, имеющих механический привод клапанов.
Проверяют и регулируют тепловые зазоры клапанов при закрытых клапанах, т.е. при максимальном удалении вершины кулачка распределительного вала от коромысла (штанги толкателя, толкателя) клапана. Такое положение вала может быть достигнуто различными способами. Проверку зазоров производят с помощью щупа, представляющего набор пластин толщиной 0,02…0,50 мм
Наиболее распространен способ, при котором сначала регулируются зазоры в клапанах первого цилиндра; при этом его поршень находится в ВМТ на такте сжатия. Такт сжатия определяется по возрастанию давления воздуха в цилиндре при движении поршня в ВМТ: необходимо вывернуть свечу зажигания (форсунку), закрыть ее отверстие в блоке цилиндров специальным свистком (пробкой, пальцем) и проворачивать коленчатый вал до сигнала свистка (выталкивания пробки, резкого возрастания давления на палец).
После регулировки тепловых зазоров клапанов первого цилиндра зазоры остальных клапанов регулируют в порядке их работы, каждый раз проворачивая коленчатый вал на 180° (для 4-цилиндровых двигателей), 120° (для 6-цилиндровых) или 144° (для 5-цилиндровых).
83 Показатели и нормативы плавности хода автомобилей.
Плавность хода − это совокупность свойств автомобиля, которые ограничивают вибронагруженность механизмов рамы, водителя, пассажиров, перевозимого груза. Колебания автомобиля, возникающие при движении по неровной опорной поверхности, оказывают неудовлетворительное влияние на его эксплуатационные свойства. На дорогах, покрытия которых с большими неровностями, предельная скорость автомобиля по плавности хода составляет 35...45 км/ч. Расход топлива увеличивается на 50...70 %, производительность транспортных работ снижается на 35...40 %.
Плавность хода автомобиля в основном определяют характеристики подвески автомобиля. Подвеской называют совокупность узлов и деталей, соединяющих мосты с рамой автомобиля. Массы узлов, механизмов и деталей автомобиля разделяют на подрессоренные (масса элемента автомобиля воспринимается подвеской) и неподрессоренные (масса элемента не воспринимается подвеской). Массы элементов, соединяющих подрессоренные и неподрессоренные механизмы, частично относят к подрессоренной и неподрессоренной массам.
При движении по неровностям автомобиль совершает сложное колебательное движение, которое принято рассматривать как совокупность простых видов колебаний. Свяжем с автомобилем систему координат OXYZ. Начало координат О расположим в центре масс автомобиля, плоскость OXZ ‒ в его продольной плоскости симметрии, ось OX ‒ в направлении движения. Рама автомобиля может поступательно перемещаться вдоль осей и совершать угловые колебания вокруг них. Автомобиль имеет шесть степеней свободы. Различают следующие виды колебаний (рис. 5.1):
−поступательные продольные перемещения (ось OX) − подергивание;
−поступательные вертикальные перемещения (ось OZ) − подпрыгивание;
−поступательные поперечные перемещения (ось OY) − пошатывание;
−угловые продольные перемещения (ось OY) − галопирование;
−угловые поперечные перемещения (ось OX) − покачивание;
−угловые боковые перемещения (ось OZ) − рыскание.
Практика эксплуатации колесных машин показывает, что на физиологическое состояние человека и плавность хода автомобиля основное влияние оказывают поступательные вертикальные (подпрыгивание) и угловые продольные (галопирование) перемещения.
Следует различать собственные и вынужденные колебания. Собственные колебания автомобиля возникают от единичного возмущающего воздействия. Частота их имеет определенную величину и зависит от массогеометрических параметров автомобиля и характеристики подвески. Вынужденные колебания автомобиля появляются от непрерывных возмущающих воздействий. Их частота определяется параметрами автомобиля и внешними условиями: скоростью движения, неровностями дороги и др. При этом они могут быть затухающими и незатухающими.
84 .Классификация лакокрасочных материалов для покраски кузовов легковых автомобилей.
Лакокрасочные покрытия по внешнему виду подразделяются на четыре класса (Ровная гладкая однотонная, Ровная гладкая однотонная или с характерным рисунком, Гладкая однотонная или с характерным рисунком, Однотонная или с характерным рисунком), а по условиям эксплуатации — на восемь групп.
По условиям эксплуатации покрытия различают следующие их группы: стойкие, стойкие к воздействию окружающей среды, химически стойкие, водостойкие, термостойкие, маслостойкие, бензостойкие, электроизоляционные.
Наиболее высокие требования к лакокрасочным покрытиям предъявляются при окраске кузовов легковых автомобилей. Эти покрытия состоят из фосфатной пленки, грунтовки, шпатлевки (при ремонте автомобилей) и нескольких (2—5) слоев эмали.
Таким образом, лакокрасочное покрытие, как правило, состоит из фосфатной пленки, грунтовки, местной шпатлевки, общей шпатлевки и слоев эмали. Общая толщина ЛКП составляет 40—300 мкм (рис. 5.1).
Качество лакокрасочного покрытия и его долговечность возрастают, если перед грунтовкой поверхность подвергается химической обработке растворами солей фосфорной кислоты — фос-фатирование или бондеризация. В результате фосфатирования на поверхности металла образуется фосфатная пленка (серого цвета) толщиной 2—5 мкм из нерастворимых в воде фосфорнокислых соединений, которая защищает металл от коррозии, в том числе и в местах, где есть царапины Л КП, и проникает влага, а также улучшает сцепление Л КП с металлом. Фосфатирование выполняют окунанием с выдержкой, а на небольших поверхностях — кистью или тампоном, смоченным раствором или пастой.
Перед фосфатированием поверхности тщательно очищают, после фосфатирования промывают водой, подсушивают и подвергают грунтовке не позднее, чем через двое суток. Для получения фосфатирующего раствора выпускают фосфатирующий концентрат (цинковый фосфат) КФ-1, КФ-12 и пасты.
Грунтовка наносится сплошным ровным тонким слоем (толщиной 10—20 мкм) после фосфатирования или непосредственно на тщательно очищенную окрашиваемую поверхность.
Фосфатирующий грунт ВЛ-02 и аналогичные ему выгодно отличаются от других тем, что образуют на поверхности не только слой грунтовки, но и пленку фосфорнокислых соединений толщиной 8—12 мкм. Основной компонент этих грунтовок — суспензия пигментов в поливинилбутирольном лаке, который представляет собой кислотный разбавитель, а именно, водно-спиртовый раствор ортофосфорной кислоты. Перед применением они смешиваются, выдерживаются 30 мин и разбавляются растворителем. После фосфатирующей грунтовки наносится второй слой грунтовки, например, ФЛ-ОЗк, ГФ-021.
85 Механические потери и механический КПД автомобильного ДВС.
Механические потери двигателя Если мощность, снимаемую с коленчатого вала, сравнить по величине с
мощностью, развиваемую газами в цилиндре, то окажется, что первая меньше второй. Это уменьшение индикаторной мощности обусловлено механическими потерями.
Механические потери индикаторной мощности складываются из следующих потерь:
Потери мощности на трение (Nт) составляют большую часть всех механических потерь. Главным образом эти потери приходятся на следующие пары:
поршень и поршневые кольца — стенки цилиндра; шейки коленчатого и распределительного валов — подшипники скольжения;
поршневой палец — бобышки поршня и верхняя головка шатуна; стержень клапана — втулка.
Потери на трение увеличиваются с ростом нагрузки на двигатель, увеличением частоты вращения коленчатого вала, при грубой обработке поверхности сопряженных деталей, неоправданном увеличении их размеров, применении некачественных масел, нарушении нормальной работы смазочной системы и системы охлаждения, ухудшении технического состояния двигателя.
Потери мощности на совершение насосных ходов поршнем (Nнас) (или насосные потери). Для того чтобы всосать свежий заряд в цилиндр и вытолкнуть отработанные газы, необходимо затратить энергию. Поэтому для выполнения этой работы от полученной индикаторной мощности будет использована какая-то ее часть. Величина этих потерь определяется величиной сопротивления впускных и выпускных трубопроводов, которая растет с увеличением частоты вращения коленчатого вала, или степенью прикрытия дроссельной заслонки.На величину насосных потерь также влияют размеры и конструкция деталей, участвующих в газообмене, и их техническое состояние.
Потери мощности на привод вспомогательных механизмов (Nпр). К вспомогательным механизмам относятся жидкостной, масляный и топливный насосы, генератор, прерыватель-распределитель, вентилятор. Данный вид потерь зависит от конструкции этих агрегатов, их размеров и технического состояния. Потери мощности на механический привод нагнетателя (Nк). Имеется в виду механический привод компрессора в двигателях с наддувом, сюда не относятся двигатели с турбонаддувом, так как у них для привода компрессора используется кинетическая энергия отработавших газов, уже вне цилиндра. Так как механический привод нагнетателя воздуха или компрессора применяется довольно редко, а затраты мощности на него значительны, этот вид потерь выделен отдельно.
Гидравлические потери мощности (Nг) учитывают затрату мощности на преодоление сопротивления движению деталей кривошипно-шатунного механизма в картерном пространстве.
КПД двигателя внутреннего сгорания – это значение отношения двух величин,
мощности которая подается на коленчатый вал двигателя к мощности получаемой поршнем, за счет давления газов, которые образовались путем воспламенения топлива.КПД бензинового двигателя находится в пределах от 20 до 25 %. И на это много причин. Если взять поступающее топливо и пересчитать его на проценты, то мы
как бы получаем «100% энергии», которая передается двигателю, а дальше пошли потери:
1)Топливная эффективность. Не все топливо сгорает, небольшая его часть уходит с отработанными газами, на этом уровне мы уже теряем до 25% КПД. Конечно, сейчас топливные системы улучшаются, появился инжектор, но и он далек от идеала.
2)Второе это тепловые потери. Двигатель прогревает себя и множество других элементов, такие как радиаторы, свой корпус, жидкость которая в нем циркулирует. Также часть тепла уходит с выхлопными газами. На все это еще до 35% потери КПД.
3)Третье это механические потери. НА всякого рода поршни, шатуны, кольца
–все места, где есть трение. Сюда можно отнести и потери от нагрузки генератора, например чем больше электричества вырабатывает генератор, тем сильнее он тормозит вращение коленвала. Конечно, смазки также шагнули вперед, но опять же полностью трение еще никому не удалось победить – потери еще 20 %
Таким образом, в сухом остатке, КПД равняется около 20%! Конечно из бензиновых вариантов есть выделяющиеся варианты, у которых этот показатель увеличен до 25%, но их не так много.
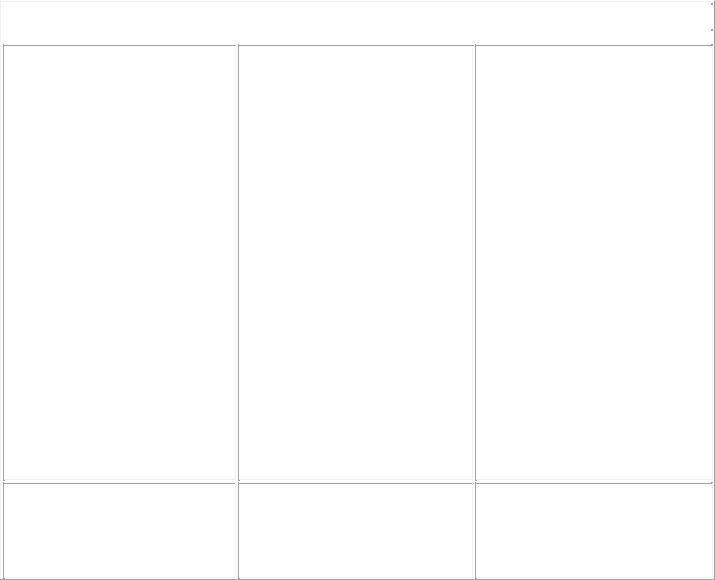
86. Текущий ремонт элементов системы питания автомобильных ДВС в зоне ТО и ТР и отделениях ОАС.
Системой питания называется совокупность приборов и устройств, обеспечивающих подачу топлива и воздуха к цилиндрам двигателя и отвод от цилиндров отработавших газов. Служит для приготовления горючей смеси, необходимой для работы двигателя.
Система питания:
-по месту приготовления горючей смеси:
+с приготовлением горючей смеси в карбюраторе
+с приготовлением горючей смеси во впускном трубопроводе
+с приготовлением горючей смеси в цилиндрах двигателя
-по способу приготовления горючей смеси:
+с пульверизационным приготовлением
+с впрыском топлива
+с непосредственным впрыском топлива.
Основные признаки и неисправности системы питания бензинового двигателя
Признак неисправности |
|
Неисправность |
|
Способ устранения |
|
|
|
|
|
|
|
|
|
|
1. Увеличение расхода топлива.
2. Увеличение токсичности отработавших газов.
Изменение пропускной способности жиклеров. Негерметичность клапана экономайзера. Загрязнение воздушного фильтра. Неправильная регулировка уровня топлива в поплавковой камере карбюратора. Негерметичность запорного клапана. Не открывается полностью воздушная заслонка.
Неправильная регулировка системы холостого хода. Изменение пропускной способности жиклеров (засорение каналов).
Проверить и при необходимости продуть или заменить жиклеры. Проверить герметичность и при необходимости притереть клапан. Очистить или заменить воздушный фильтр. Проверить и отрегулировать уровень топлива. Проверит
ь герметичность и при необходимости притереть или заменить игольчатый клапан. Отрегулировать привод воздушной заслонки.
Отрегулировать систему холостого хода по содержанию токсичных компонентов.
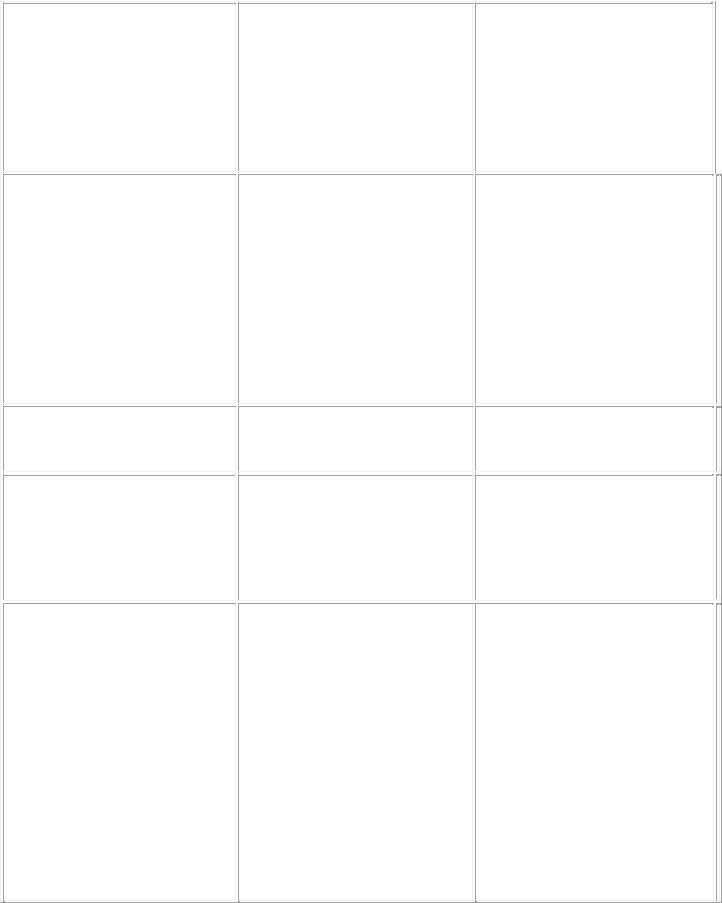
3. Двигатель не работает на холостом ходу.
4. Нестабильная частота вращения холостого хода.
5. Двигатель плохо увеличивает частоту вращения.
Неправильная регулировка системы холостого хода. Нарушение уровня топлива в карбюраторе.
Засорение жиклеров холостого хода.
Подсос воздуха во впускном трубопроводе.
Недостаточная подача топлива в поплавковую камеру. Неисправен клапан экономайзера. Неисправен ускорительный насос.
Промыть и продуть сжатым воздухом жиклеры и каналы. При необходимости проверить пропускную способность жиклеров и если нужно – заменить.
Отрегулировать частоту вращения холостого хода и минимальное содержание токсичных компонентов. Отрегулировать уровень топлива и проверить герметичность запорного клапана.
Промыть и продуть жиклеры сжатым воздухом.
Проверить состояние прокладки карбюратора, его крепление и герметичность впускного тракта.
Проверить бензонасос на развиваемое давление
ипроизводительность
и(или) отрегулировать уровень топлива в карбюраторе. Клапан экономайзера промыть и продуть сжатым воздухом. Проверить работоспособность и производительность ускорительного насоса.
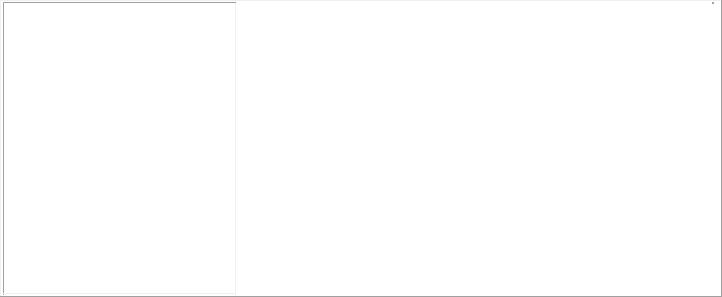
6. Отсутствует подача топлива
|
|
Проверить работу |
|
|
бензонасоса на |
|
|
стенде. Промыть и |
Неисправен бензонасос. |
|
очистить отстойник |
Засорен отстойник топлива. |
|
топлива. Снять и |
Засорен топливозаборник в |
|
очистить |
баке. Образование |
|
топливозаборник. |
паровоздушной пробки в |
|
Охладить бензонасос, |
системе питания. Наличие |
|
прокачать бензин |
воды в топливопроводах и ее |
|
рычагом ручной |
замерзание (в холодное время |
|
подкачки. Прогреть |
года). |
|
трубопроводы и |
|
|
прокачать бензин |
|
|
рычагом ручной |
|
|
подкачки. |
|
|
|
При ходовых испытаниях расход топлива определяется на мерном участке дороги (определяется приказом по автотранспортному предприятию) с помощью расходомера объемного типа.
Большой точностью и удобством обладает диагностирование на стендах тяговых качеств. На них определяется не только расход, но и мощность двигателя. При отклонениях топливной экономичности, токсичности или мощности, целесообразно проводить поэлементное диагностирование бензонасоса и карбюратора на комбинированных стендах типа МВКV-II «Карбютест-стандарт». Они имеют две гидравлические системы: одна заполняется дизельным топливом и предназначена для проверки бензонасоса и карбюратора , другая – водой и предназначена для проверки клапана экономайзера и пропускной способности жиклеров.
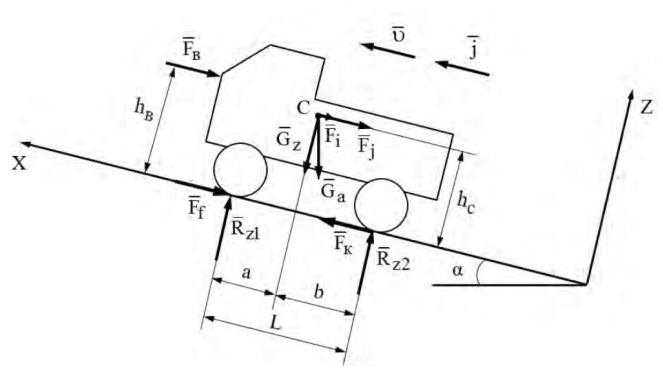
87. Уравнение тягового баланса автомобиля.
Уравнение тягового баланса:
F |
F |
f |
K |
|
Fi
FB
Fj
(силы проецируются на ось
Х) где
FK
– окружная сила на ведущих колесах (возникает от крутящих моментов,
подведенных к ведущим колесам).
F |
f |
– сила сопротивления качению колес. |
|
|
|
||||||
|
|
|
|
|
|
|
|
|
|
|
|
Fi |
|
– продольная составляющая веса автомобиля при движении на подъем. |
|||||||||
F |
|
– сила сопротивления воздуха. |
|
|
|
||||||
B |
|
|
|
||||||||
Fj |
– сила сопротивления, препятствующая ускоренному движению автомобиля |
||||||||||
F |
f |
f |
G |
cos |
|
|
|
|
|||
|
|
|
|
a |
|
|
|
|
|
|
|
где |
f – |
средний коэфф. сопротивления качению; |
Ga – вес автомобиля; |
– угол |
|||||||
уклона опорной поверхности |
|
|
|
|
|||||||
F G |
|
sin |
|
|
|
|
|||||
i |
a |
|
|
|
|
|
|
|
|||
|
|
|
|
|
|
v2 |
|
|
|
|
|
F c |
|
A |
H |
cos |
|
|
|
|
|||
x |
|
|
|
|
|
||||||
B |
|
|
|
2 |
|
|
|
|
|
||
|
|
|
|
|
|
|
|
|
|
|
|
где |
cx |
– |
коэфф. аэродинамич. сопротивления; |
A – |
площадь фронтальной проекции |
||||||
авто; |
|
– |
плотность воздуха; |
vH – скорость |
натекания воздушного |
потока на |
|||||
автомобиль. (зависит от скорости авто, направления и скорости ветра). |
|
||||||||||
F |
j |
m |
j |
|
|
|
|
|
|
||
|
|
|
a |
|
|
|
|
|
|
|
где ma – масса автомобиля; j – ускорение (замедление) автомобиля