
ШПОРЫ ГОССЫ 2021
.pdfдетонационного сгорания топлива. В этой связи для ДВС с высокой степенью сжатия необходимо использовать высокооктановый бензин.
5.Частота вращения коленчатого вала. Увеличение частоты вращения коленчатого вала приводит к росту турбулизации заряда, что влечет за собой увеличение скорости распространения пламени. В результате времени на развитие предпламенных процессов в последних частях заряда становится недостаточно, и детонация снижается. Кроме того, с увеличением частоты вращения коленчатого вала увеличивается содержание остаточных газов в рабочей смеси, что также снижает интенсивность предпламенных процессов и приводит к снижению детонации.
6.Нагрузка. Уменьшение нагрузки сопровождается прикрытием дроссельной заслонки карбюратора, вследствие чего давление и температура заряда в конце
процесса сжатия снижается, а коэффициент остаточных газов γг увеличивается. Кроме этого уменьшается количество вводимого рабочего тела, а значит и выделяемая теплота, вследствие чего снижается давление в цилиндре. Поэтому уменьшение нагрузки приводит к снижению детонации и наоборот.
7.Тепловое состояние двигателя. С ростом температуры деталей камеры сгорания увеличивается вероятность возникновения очагов самовоспламенения и детонации.
8.Температура и давление воздуха на впуске в цилиндр. Увеличение температуры и давления окружающей среды усиливает вероятность детонации. Поэтому применение наддува в двигателях с принудительным воспламенением затруднительно.
8.Форма и размеры камеры сгорания. Двигатели с формой камеры сгорания, обеспечивающей наибольшую турбулизацию смеси, более защищены от детонации.
Сэтой точки зрения наиболее рациональными являются камеры сгорания в поршне или клиновые и плоскоовальные камеры с вытеснителями.
Уменьшение пути пламени от свечи до периферийных зон камеры сгорания сокращает время его распространения и тем самым снижает вероятность возникновения детонации. Следовательно, детонацию ограничивает применение двух свечей зажигания вместо одной и уменьшение диаметра цилиндра.
9.Материал поршня и головки блока цилиндров.Материал этих деталей во многом определяет теплоотвод от рабочего тела. Применение алюминиевых сплавов, обладающих высокой теплопроводностью, позволяет снизить требования к октановому числу бензина на 5—7 единиц.
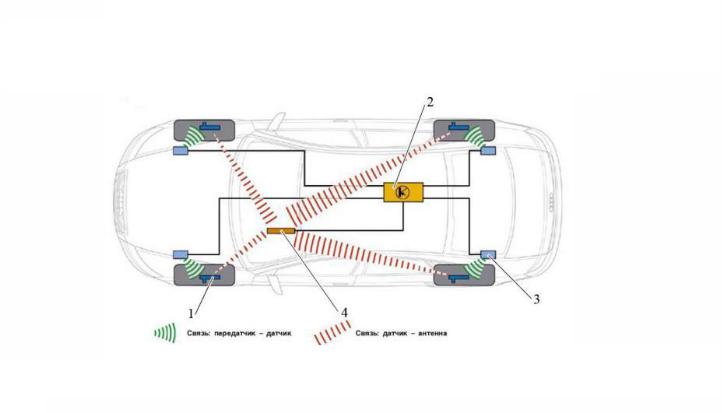
59. Система контроля давления воздуха в шинах: конструкция, назначение и принцип действия.
Система контроля давления воздуха в шинах с использованием радиосигнала состоит из датчиков давления воздуха навинченных на металлические корпуса вентилей, от которых передается радиосигнал на приемную систему, передатчиков, устанавливаемых обычно в арках колес, электронного блока управления. В крыше находится приемная антенна системы контроля давления. Некоторые производители вместо передатчиков устанавливают антенны в арках колес.
Рис. Система контроля давления воздуха в шинах:
1 — датчик давления воздуха в шине; 2 – электронный блок управления давления воздуха в шинах; 3 – передатчики системы контроля давления воздуха в шинах; 4 – приемная система контроля давления воздуха в шинах
Датчик давления измеряет текущее (абсолютное) давление в шине. Чувствительные элементы датчиков давления и температуры, а также электронные элементы измерения и управления объединены в общем корпусе.
Датчики давления могут быть многократно использованы при замене шин или дисков
колес.
Внутри колеса может устанавливаться чип, в память которого закладываются все данные о шине – ее тип, размерность, допустимая нагрузка, рекомендуемое давление, максимальная скорость, дата изготовления.
Принцип действия системы контроля давления воздуха в шинах
Контроль давления в шинах осуществляется постоянно как при движении автомобиля, так и при остановке. При открывании двери водителя или включении замка зажигания начинается процесс инициализации системы. При этом блок управления с небольшой разницей по времени присваивает каждому передатчику системы контроля давления в шинах и приемной антенне специальный адрес. По окончании инициализации каждый передатчик последовательно друг за другом получает сообщение от блока управления. Затем передатчик с присвоенным ему адресом однократно посылает радиосигнал частотой 125 кГц. Этот радиосигнал из-за его малого радиуса распространения может принять только соответствующий датчик системы контроля давления в шинах. Датчик по команде сигнала передает текущие измеренные значения давления и температуры. Антенна принимает этот сигнал и по LIN-шине передает его на блок управления. После этого связь прекращается до момента начала движения автомобиля. Температурный сигнал используется для введения поправки к величине давления, связанной с изменениями температуры воздуха в шине, а также в качестве диагностируемого параметра. Температурная поправка производится блоком управления системой контроля давления в шинах. При этом измеренные значения давления приводятся к температуре 20 °C.

60. Средства для диагностирования рулевого управления легковых автомобилей.
Контроль технического состояния ролевого управления состоит из диагностических операций, выполняемых на стендах или приборами, и из операций без измерения количественных величин – визуальные и на ощупь.
Контролируются: 1)Суммарный угловой люфт.
2)Усилие прокручивания рулевого колеса.
3)При наличии гидроусилителя: - герметичность. -развиваемое давление.
Гидроусилитель оценивается на герметичность, когда рулевое колесо находится в положении соответствующем прямолинейному движению, крайнем левом положении, крайнем правом положении. Двигатель при этом работает на средней частоте вращения.
Предельные значения люфта: Легковые-10º Автобусы-20º Грузовые-25º
При усилии на рулевом колесе 9,8Н.
Для измерения люфтов используется динамометр-люфтомер:
1-шток; 2-корпус; 3-пружина; 4-шкала; 5-крепление к рулевому колесу; 6- рулевое колесо.
Усилие прокручивания при вывешенных управляемых колесах 40…60Н. С гидроусилителем усилие прокручивания проверяется без вывешивания. Максимальное давления гидроусилителя при исправном насосе 6…7мПа.

61 Смесеобразование и формы камер сгорания в автомобильных дизельных двигателях.
Неразделенные камеры сгорания представляют собой камеру, образованную днищем поршня, когда он находится в ВМТ, и плоскостью головки цилиндров. Неразделенные камеры сгорания применяют в основном в дизелях тракторов и грузовых автомобилей. Они позволяют повысить экономичность двигателя и его пусковые качества (особенно холодного двигателя).
Разделенные камеры сгорания имеют основную и вспомогательную полости, соединенные каналом . Вспомогательная камера может быть не только сферической, но и цилиндрической.
В первом случае она называется вихревой (дизели Д-50, СМД-114), во втором – предкамерой или, как ее чаще называют - форкамерной (КДМ-100).
хревая камера работает следующим образом. В головке цилиндров имеется шаровая
– вихревая камера, соединенная каналом с основной камерой сгорания над поршнем. ижении поршня вверх во время сжатия воздух с большой скоростью входит в ю камеру по касательной к ее стенкам.
результате этого поток воздуха закручивается со скоростью до 200 м/с. В этот нный (700…900 К) воздушный вихрь форсунка впрыскивает топливо, которое еняется и давление в камере резко возрастает.
зы с недогоревшим топливом по каналу выбрасываются в основную камеру, где дит догорание оставшегося топлива. Объем вихревой камеры составляет 40…60% объема камеры сгорания, т. е. примерно половину объема.
СПОСОБЫ СМЕСЕОБРАЗОВАНИЯ |
|
||
В дизельных |
двигателях с |
непосредственными |
впрысками камера |
сгорания образуется за счет пространства, заключенного между поверхностью днища поршня и головкой блока. Основная часть объема камеры сгорания создается за счет выемки в днище поршня, имеющей форму факела топлива, распыливаемого форсункой. Хорошее смесеобразование создается за счет большого количества и малого сечения выходных отверстий форсунки и высокого давления впрыска (от 150
до 1400 кгс/см ). |
Кроме того, в конце |
такта |
сжатия форма |
камеры |
|
сгорания способствует |
завихрению сжимаемого |
воздуха, |
что |
также |
улучшает |
смесеобразование. |
|
|
|
|
|
В дизельных двигателях смесеобразование полностью |
осуществляется в |
цилиндрах. На этот процесс отводится очень малое время — 0,003—0,005 сек., в течение которого должно быть достигнуто хорошее распыливание, испарение, перемешивание и равномерное распределение топлива по всему объему камеры сгорания.
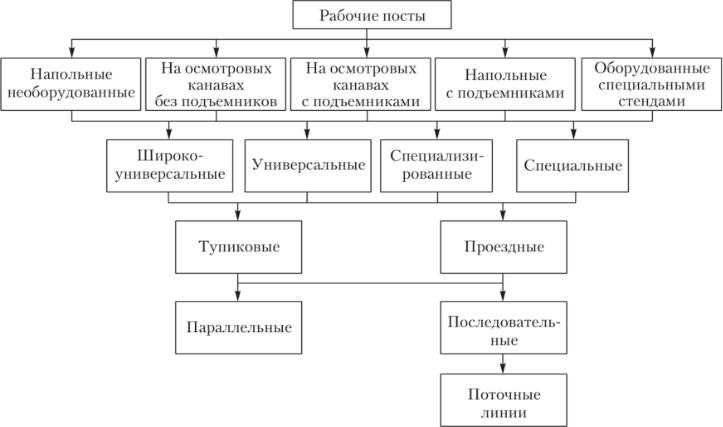
62. Формы и методы организации ТО и Р автомобилей
Формы и методы организации процессов технического обслуживания и ремонта транспортных средств в организациях автомобильного транспорта определяют характер осуществляемых при них трудовых процессов с учетом особенностей выполнения работ, их производственной программы, выбранного уровня универсализации и специализации производства и т.п.
Поскольку большинство технологических процессов ТО и ремонта выполняется непосредственно на автомобиле — свыше 50 % общей трудоемкости работ, их выполнение требует создания и использования разнообразных рабочих постов, которые классифицируют в зависимости от конструкции и технологической оснащенности, технологических возможностей, способа установки транспортных средств, взаимного расположения постов (рис. 2.3).
Основные формы организации технологических процессов
икационный признак |
ые формы |
логические возможности поста |
окоупиверсальные |
|
версальные |
|
иализированные |
|
иальные |
чие технических средств, необходим |
олнение работ силами производственно |
лнения работ |
ления |
|
полнение работ в подразделении |
|
|
|
|
ением технических средств организации |
||
|
|
|
|
Выполнение |
работ |
внешн |
|
|
|
|
изированной организацией |
|
|
ещение |
автомобилей |
и средств |
ТО |
омобиль транспортируется к техническ |
||
|
|
|
|
м (зонам и участкам) ТО и ремонта |
||
|
|
|
|
Технические |
средства |
(мастерск |
|
|
|
|
тируются к автомобилю |
|
|
ие водителей при ТО и ремонте |
|
олнение водителем работ по ТО и ремон |
||||
|
|
|
|
тного средства |
|
|
|
|
|
|
олнение работ ремонтными рабочими |
||
|
|
|
|
ением водителей |
|
|
|
|
|
|
олнение работ по ТО и ремонту толь |
||
|
|
|
|
ыми рабочими |
|
|
выполнения работ |
|
|
жсменное время |
|
|
|
|
|
|
|
ходной день |
|
|
|
|
|
|
рабочий день с прекращением рабо |
||
|
|
|
|
тного средства |
|
|
ичество |
заездов |
автомобилей |
|
дин заезд |
|
|
ния технического воздействия |
|
есколько заездов |
|
|
Методы организации ТО и ремонта транспортных средств определяют структуру производственных подразделений и состав работающих в них трудовых коллективов. Их выбор в значительной мерс зависит от масштабов и сложности производства.
В настоящее время в ОАТ используются следующие методы организации производства ТО и ремонта автомобилей: специализированных бригад, комплексных бригад, агрегатно-участковый, операционно-постовой, агрегатно-зональный и др. Из них первые три получили наибольшее распространение.
Метод специализированных бригад предусматривает формирование производственных подразделений по признаку их технологической специализации по видам технических воздействий
Метод комплексных бригад характеризуется тем, что каждое из подразделений (например, автоколонна) крупной автотранспортной организации имеет свою комплексную бригаду, выполняющую ТО-1, ТО-2 и ТР закрепленных за ней автомобилей
Агрегатно-участковый метод организации производства состоит в том, что все работы по ТО и ремонту транспортных средств распределяются между производственными участками, рабочие которых полностью отвечают за качество и результаты своей работы
Другие методы выполнения ТО и ремонта являются производными от рассмотренных или их комбинациями и на практике встречаются достаточно редко.
63 Основные виды работ по окраске кузова автомобиля.
Покраска автомобиля — один из самых трудоемких и затратных процессов в автомобильном сервисе. Покраска производится в большинстве случаев после ДТП или капитального ремонта кузова или его отдельных элементов. Современные технологии способны помочь избежать полного цикла и предложить манипуляции по восстановлению лакокрасочного покрытия.
Основные стадии покрасочных работПолная мойка кузова автомобиля. Производится в несколько повторений,
после мойки с шампунем текущее лакокрасочное покрытие обрабатывается обезжиривающими жидкостями на основе технического спирта;
Демонтаж салона, кузовной обшивки и элементов, не задействованных в покраске. Рихтовка элементов, если требуется
Удаление старого лакокрасочного покрытия с помощью акриловых грунтовок и кислотных растворов
Обтяжка полиэтиленом секторов кузова, не задействованных в покраскеНанесение покрасочной базы для лучшего контакта с лакокрасочным
покрытием
|
Покраска авто лаковым слоем |
|
Сушка свежей краске в специальной камере |
|
Сборка кузова: установка салона, обшивки, демонтированных элементов. |
Контроль покрасочных работ Если покраска производится в специализированной организации, необходимо
принять к сведению перечень правил, которыми автолюбитель должен руководствоваться при контроле уровня выполненных покрасочных процедур.
1.После сдачи авто в мастерскую нужно учесть и задокументировать кузовные дефекты: вмятины, царапины и сколы. Делается это для того, чтобы исполнитель понес ответственность за повреждения, которые могут возникнуть в случае неквалифицированного вмешательства;
2.Помимо кузова нужно осмотреть прозрачные поверхности: стекла, люк, панорамную крышу. Осмотр проводится на предмет выявления загрязнений этих поверхностей краской и сопутствующими веществами процесса покраски
3.Проверить качество монтажа салона и обшивки (если что-то из этих составляющих демонтировалось);
4.Необходимо проверять количество нанесенной краски по всей площади обновленного элемента. Для этого используется толщиномер, который определит плотность лакокрасочного слоя. Автопроизводители держат этот параметр в диапазоне 100-200 мкм. Если верхнее значение превышено, то скорее всего, недобросовестный исполнитель работ нанес на элемент шпатлевку.
5.Тщательно должны проверятся края обработанных новой краской элементов, а также крепежные части элементов (петли и.т.п.)
Самое сложное в контроле качества покраски автомобиля — проверка соответствия нанесенного цвета с тем, который требовался заказчику. Когда вам предлагают, образцы краски, требуйте предъявления образцов на металлической поверхности. Идентичные краски по-разному воспринимаются визуально на различных видах поверхности — металле, пластике, бумаге. Свежая краска тускнеет примерно за неделю — только тогда можно увидеть то, как машина будет выглядеть в естественных условиях эксплуатации. Ко всему прочему, в покрасочных мастерских используют хитрости в выставлением света. Световое оборудование выставляется так, чтобы новое покрытие выглядело более насыщенным и глубоким. Осматривайте машину в естественных условиях — на улице, в светлое время.
Дефекты покраски авто Основная доля дефектов приходится на неровное распределение краски по окрашиваемой поверхности. Часто образуется «апельсиновая кожура» — бугорки на поверхности, появляющиеся оттого, что краска высохла до контакта с поверхностью кузова. Такой дефект допустим и считается нормальным, поскольку не заметен визуально и не влияет на протекторные свойства лакокрасочного покрытия. К серьезным недостаткам можно отнести попадание пыли на поверхность покраски. При попадании пыли на кузове начинают возникать очаги коррозии. Попадание пыли особенно часто происходит, когда владелец красить автомобиль своими силами на открытом воздухе или в грязном помещении.
Инструмент для самостоятельной покраска кузова Цены на покраску авто в нынешней рыночной ситуации отнюдь не демократичные. Поэтому многие автовладельцы пытаются осуществить покрасочные работы своими силами в кустарных условиях. Особенно часто к этому прибегают владельцы старых авто. Во избежание большого числа дефектов автовладелец должен располагать определенным перечнем оборудования:
Шлифмашинка: нужна на подготовительном этапе работ. Удаляет старое покрытие, готовит поверхность кузова под нанесение грунтового слоя;
Насадки на дрель из винила: хорошо подходят для удаления коррозийных «воспалений» с рабочей поверхности;
Компрессор: обеспечивает автоматическое распыление краски на рабочую
Окрасочный пистолет. Он же краскопульт: отвечает за выход красящего вещества и за режим нанесения краски. Удобен в поэлементном окрашивании, так и в работе с кузовом в целом. Окрасочный пистолет способен наносить не только краску, но и грунт, и лак;
Прожектор: прожектором нужно подсвечивать рабочую поверхность, чтобы определить целостность нового лакокрасочного слоя и равномерность его нанесения.
64. Возможные повреждения кузова автомобиля при ДТП. Основные виды кузовных работ.
Повреждения автомобиля при авариях
Наибольшее количество соударений автомобилей приходится на переднюю часть, несколько меньше – на заднюю и наименьшее – на боковые.
Повреждения кузовов, полученные в результате соударения, делят на три категории. К первой относят очень сильные повреждения, в результате которых необходима замена кузова. Ко второй категории относятся повреждения средней тяжести, при которых большая часть деталей требует замены или сложного ремонта. К третьей относятся менее значительные повреждения – пробоины, разрывы на лицевых панелях, вмятины и царапины, полученные при ударе во время движения с малой скоростью. Эти повреждения не представляют опасности для пассажиров и водителя при эксплуатации автомобиля, хотя его внешний вид не отвечает эстетическим требованиям.
Наиболее разрушительные повреждения кузова наблюдаются при фронтальных столкновениях – соударениях, нанесенных автомобилю непосредственно в переднюю часть кузова или под углом не более 40–45° в районе передних стоек. Такие столкновения происходят, как правило, между двумя движущимися навстречу транспортными средствами, скорости которых складываются, что и создает высокие ударные нагрузки. Количество энергии, которое должно поглотиться при таких соударениях, огромно: около 80 100 кДж для автомобиля массой около одной тонны. Эта энергия поглощается при деформации автомобиля за время менее 0,1 с. Кузов автомобиля разрушается, особенно его передняя часть, а действующие при этом большие нагрузки в продольном, поперечном и вертикальном направлениях передаются всем смежным деталям каркаса кузова и особенно его силовым элементам.
Основные виды кузовных работ.
Все кузовные работы делятся на несколько видов: Восстановление геометрии – возврат кузовных параметров, указанных в техническом паспорте производителем. Нарушенная геометрия влечет за собой повышение расхода топлива, ухудшение ходовых качеств и возникновение множества иных проблем. Покраска. Производится после выполнения восстановительных работ и обработки кузова. Локальная покраска. Если имеют место несущественные повреждения, вмятины и царапины устраняются, а затем в прошлом поврежденный элемент кузова подвергается окраске. Абразивная полировка – одна из разновидностей восстановительной полировки. Проводится, если глубина повреждений не достигла уровня грунтовки, что исключает покраску. Локальное удаление ржавчины и коррозии. Производится зачистка поврежденного места (сколов, царапин) до металла. Зачастую применяется преобразователь ржавчины. Удаление вмятин без покраски. Работы производятся без повреждения лакокрасочного покрытия кузова. Ремонт бампера и порогов. Часто выполняется из-за образованных сколов и ржавчины. Сварочные работы. Жестяные работы. Стапельные работы. Рихтовка. Представляет собой, по сути, удаление вмятин, но в больших масштабах .
65 Методы и средства диагностирования подвески легковых автомобилей.
Стенд для проверки амортизаторов представляет собой две площадки, на которые устанавливаются авто последовательно передним и задним колесам. Колебание площадок происходит с помощью эксцентрика приводимым в движение электродвигателем.
Диагностика подвески автомобиля на вибростенде представляет собой имитацию езды по плохим дорогам во время которой проверяется, как механизмы реагируют на изменения внешних условий. При этом компьютер сравнивает полученные показатели с нормальными и показывает отклонения. У каждой модели авто свои нормативы, поэтому важно, чтобы мастер выставил правильную марку в компьютере.
Автомобиль заезжает на вибростенд, после этого он начинает вибрировать. Вибрация возрастает, а компьютер замеряет все показатели. Передняя и задняя подвеска тестируется отдельно.
При этом проводится проверка всех элементов подвески:
|
Амортизаторов; |
|
Сайлентблоков; |
|
Пружин; |
|
Рычагов; |
|
Шаровых опор. |
Во время диагностики амортизаторы осматривают на предмет повреждений. Если имеется протечка жидкости из амортизатора, это говорит о его пробоине. Такой амортизатор не подлежит ремонту, его нужно менять. ШРУС – шарнир равных угловых скоростей. Обеспечивает передачу крутящего момента при поворотах. Он обеспечивает автомобилю лучшую проходимость и управляемость.
ШРУС долго служит, так как защищен пыльником. Нужно проверять его состояние, так как механические повреждения могут привести к поломке детали. При попадании пыли механизм заедает и выходит из строя.
Сайлентблоки – это шарниры, которые соединяют все детали подвески между собой. Они гасят колебания, которые возникают в рычагах, за счет резиновых или полиуретановых вставок. Они присутствуют как в передней подвеске, так и в задней части.Их состояние проверяют визуально: на резине не должно быть трещин и дыр, не должно быть механических повреждений. Об их неисправности может говорить неправильный сход-развал. тупичные подшипники крепят колеса к поворотному кулаку. Они достаточно быстро изнашиваются, так как принимают на себя большие нагрузки.
Диагностику ступичного подшипника проводят вручную. Для этого домкратят авто и пытаются раскачать колесо. Одной рукой берутся за верхнюю часть, а другой за нижнюю. Если имеется люфт при движении вверх-вниз, это говорит об износе ступичного подшипника.