
ШПОРЫ ГОССЫ 2021
.pdf20. Дифференциалы и активные муфты (вискомуфта, Haldex): назначение, схемы, устройство, работа, характеристика.
Механизм трансмиссии, распределяющий крутящий момент между выходными валами и позволяющий им вращаться с разными угловыми скоростями, называется дифференциалом.
Дифференциал, При повороте автомобиля его внутреннее ведущее колесо проходит меньший путь, чем наружное, поэтому, чтобы качение внутреннего колеса происходило без скольжения, оно должно вращаться медленнее, чем наружное. Это необходимо для того, чтобы исключить при повороте пробуксовывание колес, которое вызывает повышенное изнашивание шин, затрудняет управление автомобилем и увеличивает расход топлива. Для обеспечения различной частоты вращения ведущих колес их крепят не на одном общем валу, а на двух полуосях, связанных между собой межколесным дифференциалом, подводящим к полуосям крутящий момент от главной передачи. Таким образом, дифференциал служит для распределения крутящего момента между ведущими колесами и позволяет правому и левому колесам при поворотах автомобиля и при его движении на криволинейных участках дороги вращаться с различной частотой. Межколесный дифференциал бывает симметричным или несимметричным, соответственно распределяющим крутящий момент между полуосями поровну или непоровну. На автомобилях получили применение межколесные конические симметричные дифференциалы, межосевые конические и кулачковые дифференциалы повышенного трения.
Межосевой конический дифференциал устанавливают на автомобилях повышенной проходимости с колесными формулами 6X4 и 6X6, ведущие мосты которых могут работать в различных условиях сцепления колес с дорогой.
Кулачковый дифференциал повышенного трения (рис. 14.32) за счет дополнительных сил трения (в результате самоблокировки) передает больший крутящий момент на то колесо автомобиля, которое вращается медленнее, что уменьшает возможность его пробуксовывания и повышает устойчивость автомобиля против бокового заноса.

Дифференциалы
По назначению |
|
По |
|
По внутреннему |
|
По распределению |
|
|
конструкции |
|
трению |
|
крутящего момента |
|
|
|
|
|
|
|
Межколесные |
|
Шестеренные |
|
Малого трения |
|
Симметричные |
Межосевые |
|
Кулачковые |
|
Повышенного |
|
Несимметричные |
|
|
Червячные |
|
трения |
|
|
|
|
|
|
|
|
|
|
|
|
|
|
|
|
Схемы устройства и работы шестеренного дифференциала показана на рисунке 20а.
Рисунок 20аКонический симметричный дифференциал: а — устройство; б — схема работы; 1, 7 — шестерни-сателлиты; 2, 8 — полуосевые конические колеса; 3, 9 — полуоси; 4 — крестовина; 5 — ведомое колесо главной передачи; 6 — ведущая шестерня главной передачи
Дифференциалы характеризуются передаточным числом. У симметричных дифференциалов оно равно 1. У них моменты и угловые скорости на правом и левом колесах определяются соответственно по выражениям
Мл +Мп =Мд (1) Мл =Мп =Мд/2 (2)
ωл+ ωп = 2ωд (3) ωп =2ωд, если ωл=0 (4)

Устройство шестеренных дифференциалов показано на рисунке 21.
а, б – симметричные; в, г – несимметричные; 1 – корпус; 2 – сателлит; 3,4 – полуосевые шестерни
Рисунок 21 – Схемы шестеренных дифференциалов Функции дифференциала может выполнять вязкостная муфта (рисунок 26), у
которой выходные валы могут проскальзывать при небольших скоростях и блокируются – при значительных. Работа ее основана на свойстве силиконовой (кремнийорганической) жидкости, находящейся внутри муфты, увеличивать вязкость при нагреве.
Рисунок 26 - Устройство вязкостной муфты (вискомуфты): 1 — корпус; 2 — вал корпуса; 3,6 — ведущий и ведомый валы; 4 — диски; 5 — уплотнения

C целью повышения управляемости и устойчивости автомобиля применяют активные дифференциалы типа активной гидравлической муфты Haldex (рисунок 28), управляемые электронным блоком.
Рисунок 28Схема активной гидравлической муфты Haldex: 1- ведомый вал с кулачковой шайбой; 2-рабочий поршень; 3-многодисковая муфта; 4-насосный поршень; 5- нагнетательный клапан; 6- впускной клапан; 7- регулятор управления давления муфтой; 8-ведущий вал
21. Крепежные работы. Назначение крепежных работ. Технология выполнения крепежных работ. Оборудование и инструмент для выполнения крепежных работ.
Крепежные работы включают: проверку и подтяжку стяжных хомутов крепления, гаек и штуцеров крепления трубопроводов с баллонами, газовой аппаратурой и приборами, а также проверку состояния газопроводов, герметичности вентилей и устранение причин, вызывающих утечку газа. Крепежные работы по аппаратуре и соединениям газопроводов следует выполнять при закрытых вентилях баллонов, только после этого, как двигателем израсходован весь оставшийся газ из системы. Крепежные работы при ТО-2 проводятся дополнительно к крепежным работам, выполняемым при ТО-1. При этом они включают контроль и крепление головки к блоку цилиндров подтягиванием гаек динамометрическим ключом. Момент и последовательность затяжки устанавливаются заводамиизготовителями. Чугунную головку цилиндров крепят в горячем состоянии, а головку цилиндров из алюминиевого сплава - в холодном, что объясняется неодинаковым коэффициентом линейного расширения материала болтов и шпилек (сталь) и головки (алюминиевый сплав). Затяжку выполняют от центра к краям по диагонали. Неисправности резьбовых соединений – это ослабление предварительной затяжки, повреждения и срыв резьбы. Ослабление резьбовых соединений и их самоотворачивание нарушают регулировку и приводят к ухудшению эксплуатационных свойств автомобиля, к потере герметичности уплотнений, к возрастанию динамических нагрузок на детали и к их поломкам. Самоотворачивание происходит в основном из-за вибраций, в результате чего снижается сила трения в самой резьбе и на контактном торце гайки или головки болта. Быстрому ослаблению крепления подвержены стартер, генератор, топливный насос, карданный вал. Вероятность самоотворачивания резко возрастет, если перед сборкой резьба была повреждена. Срыв резьбы при ремонтах является также распространенным дефектом. Основная причина этого - затяжка соединений с усилиями, значительно превышающими нормативные. Замятую резьбу можно восстановить специальным режущим инструментом (плашками, метчиками). Оборвавшуюся часть болта или шпильки из резьбового отверстия удаляют сверлом меньшего диаметра. Защита резьбы. Продолжительность простоя автомобилей в обслуживании или ремонте, трудоемкость работ очень часто увеличиваются из-за сложности разборки корродированного резьбового соединения. При этом могут возникнуть поломки. Для предотвращения этого перед каждой сборкой резьба должна быть очищена и смазана маслом. Наилучший эффект дает применение противокоррозионных средств на масляной основе. Для сокращения доли ручных работ применяют пневмоили электрогайковерты с различными видами насадок при работе с гайками (болтами) или винтами. Гайковерты обычно используются при работе с крепежными соединениями, имеющими большие моменты затяжки, например с гайками колес, рессор и стремянок. Гайковерты выполняются переносными или передвижными для удобства их транспортирования к автомобилю, имеют электрический привод. На ряде гайковертов предусмотрена возможность регулирования момента затяжки гаек.
22. Диагностирование автомобиля по показателям эффективности тормозов.
Диагностические параметры тормозов делятся на две группы:
обеспечивающие общее диагностирование;
обеспечивающие поэлементное диагностирование. Общее диагностирование:
тормозной путь и замедление;
тормозные силы и их разность по осям. Поэлементное диагностирование:
сила нажатия на педаль;
скорость нарастания и спада тормозных сил;
скорость срабатывания тормозных механизмов;
ход штоков тормозных камер;
свободный ход педалей;
производительность компрессора и др. Диагностические параметры измеряют:
путём ходовых испытаний на дороге;
встроенными средствами диагностирования (в процессе эксплуатации);
при помощи тормозных стендов (в стационарных условиях).
Ходовые испытания применяют главным образом как инспекторскую проверку для грубой оценки тормозных качеств автомобиля. Испытания могут проводиться визуально по тормозному пути к синхронности начала торможения при резком однократном нажатии на педаль (сцепление выключено), а также с использованием переносных приборов-деселерометров (или деселерографов).
Диагностирование по тормозному пути должно проводиться на ровном, сухом, горизонтальном участке дороги, свободном от движущегося транспорта.
Стационарное диагностирование тормозных показателей применяют для
получения более обширной информации о техническом состоянии тормозных механизмов. Кроме того, оно позволяет не только выявлять дефекты, но и контролировать качество их устранения.
Диагностирование тормозных показателей автомобиля проводят с помощью тормозных стендов. Они делятся на:
силовые тормозные стенды;
инерционные тормозные стенды.
Силовые тормозные стенды предназначены для имитации движения автомобилей и измерения при этом параметров эффективности тормозов. Они состоят из:
опорно-приводного устройства;
измерительного устройства.
Инерционные тормозные стенды по принципу действия и назначению делятся на барабанные и платформенные.
При диагностировании на барабаном стенде эффективность тормозов определяют путём сопоставления их работы с кинетической энергией вращающихся

масс стенда, а при диагностировании на платформенном - с кинетической энергией поступательно и вращательно движущихся масс.
К недостаткам платформенного стенда относится большая площадь, занимаемая стендом (с учётом места необходимого для предварительного разгона автомобиля), зависимость результатов от точности заезда на платформы, нестабильность коэффициента сцепления и необходимость повторных контрольных заездов после устранения выявленных дефектов.
Тормозные инерционные стенды:
1.Роликового типа (лучшие функциональные свойства)
2.Площадочного типа
1 |
– Маховик |
|
2 |
– муфта |
|
3 |
– |
электродвигатель |
|
|
|
|
|
|
|
|
|
2 |
|
|
|
|
|
|
|
|
|
2 |
|
|
|
|
2 |
|
||||||||||||||||||||
|
|
|
= |
|
|
|
|
|
+ ПК |
|
|
ПК + ЗК |
|
ЗК |
|
||||||||||||||||||||||||||||||
|
|
|
|
|
|
|
2 |
|
|
|
|
|
|
|
|
|
|
|
|
|
2 |
|
|
|
|
|
|
|
|
|
|
|
2 |
|
|
|
|
|
|||||||
|
|
|
|
|
|
|
|
|
|
|
|
|
|
|
|
|
|
|
|
|
|
|
|
|
|
|
|
|
|
|
|
|
|
|
|
|
|
||||||||
|
|
|
|
|
|
|
|
|
|
|
2 |
|
|
|
|
|
|
|
|
2 |
+ |
2 |
|
||||||||||||||||||||||
|
|
|
= |
|
ПК |
|
|
ПК + р |
|
|
р |
|
|
м |
|
м |
|
||||||||||||||||||||||||||||
|
|
|
|
ст |
|
|
|
|
|
2 |
|
|
|
|
|
|
|
|
|
|
2 |
|
|
|
|
|
|
2 |
|
|
|
|
|
||||||||||||
|
|
|
|
|
|
|
|
|
|
|
|
|
|
|
|
|
|
|
|
|
|
|
|
|
|
|
|
|
|
|
|
|
|
||||||||||||
|
|
|
|
|
|
|
|
|
|
|
0,5 = ст |
|
|
|
|
|
|
|
|
|
|
|
|
||||||||||||||||||||||
|
2 |
|
|
2 |
|
|
|
|
|
|
|
2 |
|
|
|
|
|
|
|
|
|
|
|
|
|
|
|
|
|
|
|
|
|
|
|||||||||||
|
|
+ |
ПК |
ПК |
+ |
ЗК |
|
ЗК |
= |
|
|
|
2 |
+ 2 |
+ 2 |
||||||||||||||||||||||||||||||
|
|
|
|
|
|
|
|
|
|
|
|
|
|||||||||||||||||||||||||||||||||
2 |
2 |
|
|
|
|
|
|
|
|
|
|
2 |
|
|
|
|
|
|
|
|
|
|
|
|
ПК |
ПК |
|
|
р р |
м м |
|||||||||||||||
|
|
|
|
|
|
|
|
|
|
|
|
|
|
|
|
|
|
|
|
|
|
|
|
|
|
|
|
|
|
|
|
|
|
|
|
|
|
|
|||||||
|
|
|
|
|
|
|
|
|
|
2 |
|
|
|
|
|
|
2 |
|
|
|
2 |
|
|
|
|
|
|
|
|||||||||||||||||
|
|
|
|
|
|
|
|
|
|
|
|
|
|
|
|
− |
|
ПК |
|
ПК |
+ |
ЗК |
ЗК |
− 2 |
|
||||||||||||||||||||
|
|
|
|
|
|
|
|
|
|
|
|
|
|
|
|
|
|
|
|
|
|
|
|
|
|
||||||||||||||||||||
|
|
|
(ПК)= |
|
2 |
|
|
|
|
|
|
|
|
|
|
|
2 |
|
|
|
|
|
|
|
|
2 |
|
|
|
|
|
р |
р |
|
|||||||||||
|
|
|
|
|
|
|
|
|
|
|
|
|
|
|
|
|
|
2 |
|
|
|
|
|
|
|
|
|
|
|
|
|||||||||||||||
|
|
|
|
|
|
|
|
|
|
|
|
|
|
|
|
|
|
|
|
|
|
|
|
|
|
|
|
|
|
|
|
|
|
|
|
|
|
|
|||||||
|
|
|
|
|
|
|
|
|
|
|
|
|
|
|
|
|
|
|
|
|
|
|
|
|
|
|
|
|
М |
|
|
|
|
|
|
|
|
|
|
|
|
||||
|
|
|
|
|
|
= |
|
|
|
|
|
|
|
|
|
(4 |
− |
4) |
|
|
|
|
|
|
|
||||||||||||||||||||
|
|
|
|
|
|
|
2 |
|
|
|
|
|
|
|
|
||||||||||||||||||||||||||||||
|
|
|
|
|
|
|
|
|
|
|
|
|
|
|
|
|
п |
|
|
|
|
в |
|
|
|
|
|
|
|
||||||||||||||||
|
|
|
|
|
|
|
|
2 |
|
|
|
|
|
2 |
|
|
2 |
|
|
|
|
|
|
|
|||||||||||||||||||||
|
|
|
|
|
|
|
|
|
|
|
|
|
|
|
|
+ |
ПК |
|
ПК |
− |
ЗК |
|
ЗК |
− 2 |
|
||||||||||||||||||||
|
|
|
|
|
|
|
|
|
|
|
|
|
|
|
|
|
|
|
|
|
|
|
|
||||||||||||||||||||||
|
|
|
(ЗК)= |
|
|
|
2 |
|
|
|
|
|
|
|
|
|
|
|
2 |
|
|
|
|
|
|
|
|
2 |
|
|
|
|
|
р |
р |
|
|||||||||
|
|
|
|
|
|
|
|
|
|
|
|
|
|
|
|
|
|
|
2 |
|
|
|
|
|
|
|
|
|
|
|
|
||||||||||||||
|
|
|
|
|
|
|
|
|
|
|
|
|
|
|
|
|
|
|
|
|
|
|
|
|
|
|
|
|
|
|
|
|
|
|
|
|
|
|
|||||||
|
|
|
|
|
|
|
|
|
|
|
|
|
|
|
|
|
|
|
|
|
|
|
|
|
|
|
|
|
М |
|
|
|
|
|
|
|
|
|
|
|
|
||||
|
|
|
|
|
|
|
|
|
|
|
|
|
|
|
|
= |
|
|
|
2 |
|
|
|
|
|
|
|
|
|
|
|
|
|||||||||||||
|
|
|
|
|
|
|
|
|
|
|
|
|
|
|
|
|
|
|
|
|
|
|
|
|
|
|
|
|
|
||||||||||||||||
|
|
|
|
|
|
|
|
|
|
|
|
|
|
|
|
|
дв |
|
|
|
|
|
|
|
|
|
|
|
|
|
|
|
|
|
|
||||||||||
|
|
|
|
|
|
|
|
|
|
|
|
|
|
|
|
|
|
|
|
|
|
|
|
|
|
|
|
|
|
|
|
|
|
|
|
|
|
|

23.Организация, технология, оборудование и инструмент для выполнения смазочных работ.
Трудоемкость смазочных работ может составлять до 30% общей трудоемкости работ ТО-1 и ТО-2.
Схема классификации смазочно-заправочного оборудования Для раздачи моторных и трансмиссионных масел используется высокопроизводительное оборудование (до 10-15 л/мин), подающее масло под низким давлением – до 2 МПа. При раздаче пластичных смазок необходимо развивать среднее (5-10 МПа) или высокое (15-45 МПа) давление. Поэтому производительность этого оборудования низкая, не превышающая 250 г/мин. Подачу масла или смазки осуществляют нагнетающие устройства, приводимые в действие сжатым воздухом или электродвигателем. Некоторое оборудование имеет ручной привод. Смазочно-заправочное оборудование устанавливается на специализированном посту смазки, где и проводится весь комплекс смазочных работ по автомобилю согласно карте смазки. Маслозаправочные или маслораздаточные установки по принципу действия классифицируются следующим образом: Ручные маслораздаточные установки — насос подачи масла приводится в действие вручную; Компрессионные маслораздаточные установки — подача масла осуществляется за счет сжатого воздуха в резервуаре установки; Пневматические маслораздаточные установки — подача масла осуществляется дозированно пневматическим насосом двойного действия, подключенным к пневмолинии (предлагаются различные модели насосов и способы их установки на емкостях любого размера, включая стандартные бочки, возможно настенное закрепление, размещение на подкатных тележках с установленными на них емкостями); Маслораздаточные установки имеют передвижную платформу и электронный счетчик расхода масла. Маслораздаточное оборудование для заправки трансмиссионными маслами может быть передвижным и стационарным. При заправке картеров агрегатов автомобилей трансмиссионным маслом применяются передвижные маслозаправочные установки с ручным приводом. Установки состоят из двухколесной тележки-подхвата, специального бака, насоса, раздаточного шланга с наконечником. Стационарные заправочные установки предназначены для заправки трансмиссионным маслом агрегатов автомобилей непосредственно из масляного резервуара. Установки являются автоматическими, состоят из насосной установки и могут иметь до двух раздаточных рукавов с пистолетами. На специализированных постах по смазке и заправке (дозаправке) автомобилей используются многофункциональные смазочно-заправочные установки. Такие установки предназначены для централизованной механизированной дозированной выдачи моторного и трансмиссионного масел,
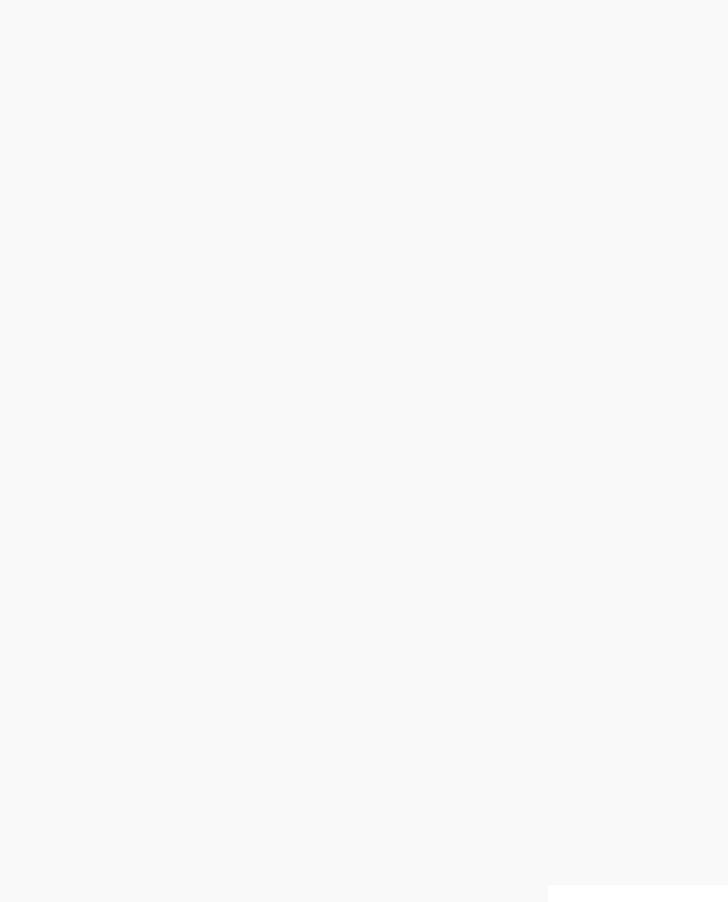
пластичной смазки, охлаждающей жидкости и воздуха с измерением давления в шинах. Для сбора отработавшего масла служат переносные и передвижные баки с воронками и стационарные сборникирезервуары, установленные под полом помещения с маслоприемными воронками. Передвижные установки для сбора отработавшего масла, сливаемого из агрегатов автомобилей на постах, не оборудованных стационарными сливными устройствами, состоят из специального приемного бака (баллона), оборудованного для его перемещения группой колес, приемной воронки со съемным поворотным лотком. Оборудование для смазки агрегатов и узлов автомобилей предназначено для подачи пластичной смазки через пресс-масленки в трущиеся узлы транспортных средств. К нему относятся различные нагнетатели смазки. Передвижные нагнетатели смазки с пневматическим приводом состоят из специального бака (баллона), размещенного на тележке, и насосной установки с насосами высокого и низкого давления. В комплект нагнетателя входит также рукав с раздаточным пистолетом. Стационарные нагнетатели смазки с электроприводом и перекачивающим насосом обеспечивают работу одновременно нескольких постов смазки с подачей ее непосредственно из стандартной тары к раздаточным пистолетам. Нагнетатели рекомендуется монтировать в отдельном помещении, а раздаточные пистолеты с рукавами
— на постах смазки, оборудованных канавами или подъемниками Оборудование для заправки тормозной жидкостью предназначено для заливки тормозной жидкости в тормозную систему автомобилей с гидроприводом, приведения ее в рабочее состояние и выполнения, в зависимости от требований, отдельных контрольных операций. Оборудование для заправки тормозной жидкостью может быть переносным, передвижным и стационарным. Переносный бак для заправки тормозной жидкостью представляет собой закрытый стальной резервуар, давление в котором контролируется с помощью манометра. Заправка бака тормозной жидкостью осуществляется через горловину. Передвижные установки для заливки и прокачки гидравлических тормозов автомобилей предназначены для проведения комплекса работ по обслуживанию гидравлического привода тормозов. Современные авторемонтные хозяйства и специализированные станции для централизованного управления системой раздачи, сбора и утилизации всех видов масел, смазок и технических жидкостей применяют средства компьютерного контроля. Централизованная компьютерная система раздачи технических жидкостей позволяет одновременно отслеживать раздачу нескольких видов технических жидкостей на всех постах, контролировать наличие всех видов жидкостей и автоматически оповещать о необходимости дозаказа определенного вида жидкости. Эта система обеспечивает автоматическое запрещение выдачи жидкости, уровень которой в резервуаре сравнялся с минимально допустимым для безопасной работы насоса. Оборудование для смазки агрегатов и узлов автомобилей предназначено для подачи пластичной смазки через пресс-масленки в трущиеся узлы транспортных средств. К нему относятся различные нагнетатели смазки. Передвижные нагнетатели смазки с пневматическим приводом состоят из специального бака (баллона), размещенного на тележке, и насосной установки с насосами высокого и низкого давления. В комплект нагнетателя входит также рукав с раздаточным пистолетом. Стационарные нагнетатели смазки с электроприводом и перекачивающим насосом обеспечивают работу одновременно нескольких постов смазки с подачей ее непосредственно из стандартной тары к раздаточным пистолетам. Нагнетатели рекомендуется монтировать в отдельном помещении, а раздаточные пистолеты с рукавами — на постах смазки, оборудованных канавами или подъемниками По способу сбора отработанного масла различают: Самотечные маслосборники; Всасывающие маслосборники;Комбинированные установки для откачки/слива Чаще и удобнее всего использовать передвижные мобильные маслосборники различного объема. Маслосборники могут стоять как под подъемниками, так и в смотровых канавах. Всасывающие установки работают по следующему принципу: отработанное масло всасывается пневматическим вакуумным насосом без движения и износа каких-либо деталей с помощью заборного щупа или переходника, вставляемого в масляный щуп двигателя. Опорожнение установок обычно выполняется путем создания определенного давления с помощью насоса. Также современные установки комплектуются указателем уровня масла в баке, предохранительным клапаном, защищающим от сверхдавления, поддонами для инструментов, фильтров и т.д. Некоторые маслосборники комплектуются прозрачной колбой, которая позволяет выполнить осмотр отработанного масла.
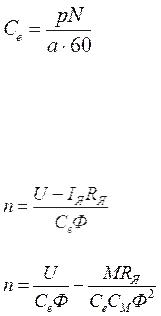
24.Электрические характеристики и основные параметры стартерных электродвигателей и привода.
В стартерах применяются электродвигатели постоянного тока. Для анализа особенностей их работы в системе пуска рассмотрим основные характеристики электродвигателей постоянного тока, которые подразделяются на двигатели последовательного, параллельного, смешанного и независимого возбуждения. Тип возбуждения определяется схемой включения обмоток возбуждения по отношению к якорной пени. Электромеханические параметры электродвигателя определяются выражениями:
(1)
(2)
(3)
где U—напряжение, подводимое к электродвигателю от источника питания; RЯ — активное сопротивление цепи якоря; Е— противо-ЭДС якоря; Ф — магнитный поток; п — частота вращения якоря; М— момент электродвигателя; Iя —ток якоря; Се. См —конструктивные постоянные;
; ;
р — число пар полюсов; а — число пар параллельных ветвей обмотки якоря; N — число проводников обмотки якоря.
Из выражений (1) - (3) можно получить формулы для определения частоты вращения:
(4)
(5)
В электродвигателях, с последовательным возбуждением обмотка возбуждения включается последовательно с обмоткой якоря, и поэтому Iя = IВ (рис. 2, а).