
Tipovye_raschyoty_pri_sooruzhenii_i_remonte
.pdf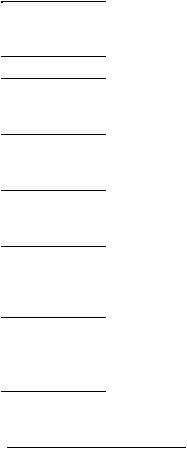
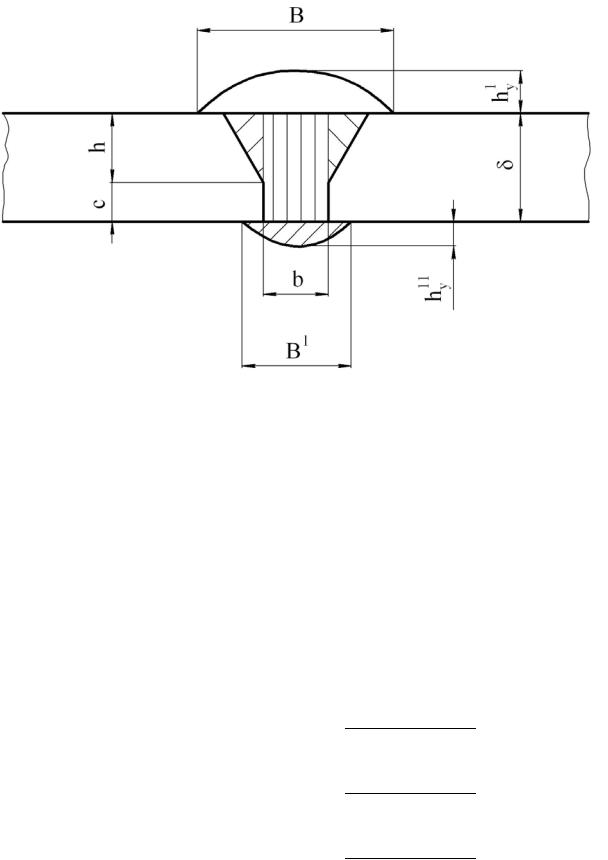
Рис.3.23. Форма поперечного сечения наплавленного металла стыкового шва с V-образной разделкой кромок
3.Определяем силу сварочного тока по формуле:
|
|
|
Iсв |
= |
πdэ2 |
j |
, |
|
(3.64) |
|
|
|
|
|
4 |
|
|||||
где dэ – диаметр электродного стержня, мм; j– допустимая плотность тока, |
||||||||||
А/мм2 (табл. 3.22). |
|
|
|
|
|
|
|
|
|
|
|
|
|
|
|
|
|
|
|
|
Таблица 3.22 |
Допустимая плотность тока при ручной электродуговой сварке, А/мм2 |
||||||||||
|
|
|
|
|
|
|
|
dэ, мм |
|
|
Вид покрытия |
|
|
|
|
|
|
|
|||
электрода |
|
3 |
|
|
4 |
|
|
5 |
6 |
|
Фтористо- |
|
|
|
|
|
|
|
|
|
|
кальцевое |
|
13–18,5 |
|
10–14,5 |
|
9–12,5 |
8,5–12 |
|||
(основное) |
|
|
|
|
|
|
|
|
|
|
Целлюлозное |
|
11,3–15,5 |
|
11,1–14,3 |
|
9,1–12,7 |
7–7,7 |
|||
|
|
|
|
|
|
|
|
|
|
|
4.Устанавливаем напряжение сварочной дуги.
При зажигании дуги напряжение между электродом и свариваемым изделием Uxx = 60–80 В. При замыкании сварочной цепи напряжение падает
213

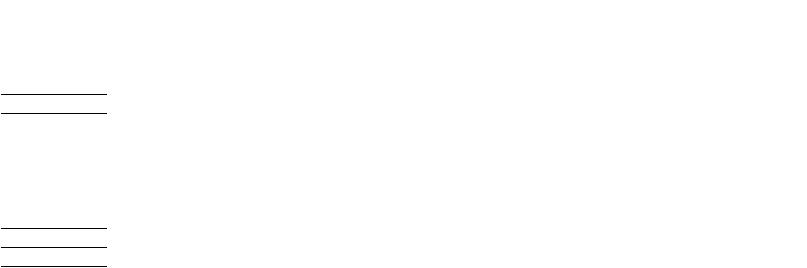

