
2533
.pdf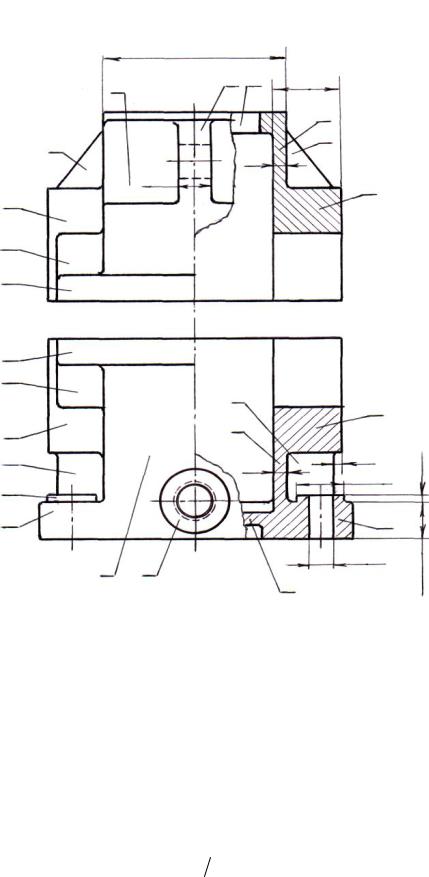
Вид А
|
Вкор |
|
2 |
11 10 |
lр |
4
7 |
7 |
|
|
||
|
2,5
6
13
12
12
13
|
7 |
|
6 |
4 |
|
7 |
|
|
14 |
||
|
||
5 |
|
|
1 |
8 |
9
Рис. 4.13
6
6 |
|
5 мм |
2…3 |
2dф |
|
5 |
|
' |
d |
dф |
|
|
ф |
|
1,5 |
разрезе согласно табл. 4.5. Под головки болтов поставить пружинные шайбы.
Подшипниковые гнезда закрываются накладными фланцевыми крышками 15, 16, 17, 18, которые крепятся к корпусным деталям болтами 19 и 20. Болты выбирают по табл. 4.3. Под головки болтов нужно поставить пружинные шайбы. Разметку отверстий под болты в крышках выполнять по табл. 4.3 и формуле
Dср Da D 2 D 2,5dБ , |
(4.41) |

где Dср– диаметр окружности центров болтов, мм; D – наружный диаметр подшипника, мм; dБ – диаметр болта, крепящего крышку (см. табл. 4.3) мм, центры болтов размечают равномерно по окружности в зависимости от их количества. В разъем между корпусом редуктора и его крышкой болты устанавливать нельзя!
Далее вычерчивают крышку 25, закрывающую люк в потолочной стенке крышки корпуса. Размеры длины крышки по отношению к длине корпуса
lкр Lкор 0,35...0,55, |
(4.42) |
где lкр – длина крышки, мм; Lкор– длина корпуса (см. рис. |
4.11) без |
фланца, мм. Ширину крышки можно выбрать равной ширине корпуса без фланца (см. рис. 4.13), т. е.
bкр Bкор , |
(4.43) |
где bкр – ширина крышки, мм; Bкор– ширина корпуса без фланца, мм.
На потолочной стенке крышки корпуса по контуру люка делают прилив, размеры которого соответствуют размерам крышки bкр lкр , и он
приподнят от верхней плоскости на 3…5 мм (см. рис. 4.11). Окно люка меньше крышки. При этом
bл bкр 5dк , |
(4.44) |
lл lкр 5dк , |
(4.45) |
где bл – ширина люка (окна), мм; lл– длина люка, мм; |
dк – диаметр болта |
(винта), крепящего крышку, мм. |
2,5dк делают по |
Разметку отверстий во фланце люка шириной |
средней части контура фланца, при этом ширина линии центров отверстий
|
bшк 0,5 bкр bл , |
(4.46) |
|
|
Болты для крышек люков |
Таблица 4.6 |
|
|
|
||
|
|
|
|
Длина крышки lкр , мм |
150 |
160…240 |
250 |
Диаметр болта dк , мм |
М6 |
М8 |
М10 |
а длина линии центров отверстий |
|
|
|
|
lшк 0,5 lкр lл . |
(4.47) |
Расстояние между болтами в крышке примерно в 10 раз больше диаметра болта.
Между крышкой люка и корпусом кладут тонкую прокладку. Отдушину 27 (см. рис. 4.1) устанавливают либо в крышке люка, как
на рисунке, либо в потолочной стенке корпуса. Для этого на стенке делают прилив высотой 3…5 мм и диаметром 2,5dотд (диаметра резьбы отдушины). Размеры отдушины приведены в приложениях 32 и 34.
Далее вычерчивают пробку и маслоуказатель. Ниже было подробно описано об этом.
4.6. Компоновочный чертеж конических зубчатых колес
Коническая зубчатая передача расположена между II и III валами и состоит из шестерни z1и колеса z2 (см. рис. 2.2).
Исходные данные: числа зубьев шестерни и колеса z1 20, z2 60, внешний окружной модуль конической передачи m1 3мм, момент крутящий на II – м валу М2 36,8 Н м, момент крутящий на III – м валу М3 107 Н м , коэффициент ширины зуба 6, модуль в среднем сечении зуба mm 2,7мм, внешний окружной модуль m 3 мм.
Нужно произвести геометрический расчет и скомпоновать чертеж. Разберем это на конкретном примере.
1. Определяем углы начальных (делительных) конусов шестерни и колеса:
угол делительного конуса шестерни, формула (3.12)
tg 1 z1z2 20
60 0,333,
1 arctg0,333 18,43 ,
угол делительного конуса колеса
2 90 1 90 18,43 71,57 .
Определяем размеры зубчатых колес:
внешний делительный диаметр шестерни
d1 m1 z1 3 20 60 мм,
внешний делительный диаметр колеса
d2 m2 z2 3 60 180мм,
средний диаметр шестерни
dm1 mm z1 2,7 20 54мм,
средний диаметр колеса
dm2 mm z2 2,7 60 162 мм,
диаметр окружности выступов (3.16) или внешний диаметр вершин зубьев шестерни
da1 m1 z1 2 cos 1 3 20 2 cos18,43 65,7мм,
диаметр окружности выступов или внешний диаметр вершин зубьев колеса (3.17)
da2 m1 z2 2 cos 2 3 60 2 cos71,57 181,9мм,
ширина зубчатых колес
b1 m1 6 3 18 мм,
условное межцентровое расстояние
aк 0,5 d1 d2 0,5 60 180 120 мм.
2. Строим схему конических зубчатых колес. Проводим вертикально ось шестерни ОО1 (рис. 4.14) и горизонтально ось колеса ОО2 . Параллельно оси ОО1 на расстоянии радиуса начальной окружности шестерни, равного 0,5d1 0,5 60 30мм, проводим вертикально линию BC, а параллельно оси ОО2 на расстоянии радиуса начальной окружности колеса, равного 0,5d2 0,5 180 90мм, проводим горизонтально линию AB. В пересечении этих линий получаем точку B. Симметрично точке B относительно осей ОО1 и ОО2 откладываем точки А и С. Соединяем точки А, B и С с центром О и получаем два начальных конуса АОВ (шестерня) и ВОС (колесо). При вращении зубчатых колес вокруг осей ОО1 и ОО2 начальные конусы катятся друг по другу без скольжения, постоянно касаясь друг друга по образующей ОВ.
Начальные конусы – это две конические поверхности АОВ и ВОС с общей вершиной О и образующей ОВ, перекатывающиеся одна по другой без скольжения.
Окружности оснований АВ и ВС конусов называются начальными окружностями конической передачи. Они расположены под углом 90 и при вращении катятся друг по другу без скольжения, как и в цилиндрической передаче. В отдельно взятом колесе начальная окружность называется делительной окружностью, а начальный конус –
делительным конусом.

Углы делительных конусов обозначают 1 и 2 . Межосевой угол 1 2 90 .
Профилирование зубьев, т.е. придание зубьям эвольвентной формы в поперечном сечении, конических колес выполняют на поверхностях
внешних дополнительных конусов АО1В и ВО2С с вершинами О1 и О2 ,
образующие которых перпендикулярны образующим делительных конусов.
Основные геометрические размеры прямозубой конической
A О1 B
D 2
1
90°
О2
E
R
С
0,5d1
0,5 d2
1 О2
Рис. 4.14
передачи определяют в зависимости от модуля и числа зубьев по формулам (3.8)…(3.17). Высота и толщина зубьев конических колес постепенно уменьшаются по мере удаления от внешнего дополнительного конуса А

(см. рис. 3.1) к вершине начальных конусов О.
К основным геометрическим параметрам относят: mm – модуль в среднем сечении зуба, т.е. в точке П ;
m – внешний окружной модуль, т.е. максимальный модуль зубьев, измеряемый на поверхности внешнего дополнительного конуса А, который также называют внешним торцом конического колеса. Модуль m выбирают по стандарту;
R – внешнее конусное расстояние (см. рис. 4.14), т.е. длина образующей начальных конусов ОА, ОВ или ОС, которое определяется по формуле, получаемой из треугольников BDO или BEO с применением теоремы Пифагора или тригонометрических функций
d1 AB, d2 BC
R 0,5 d12 |
d22 |
0,5m |
z21 z22 , |
(4.48) |
R 0,5d1 |
sin 1 |
0,5d2 |
cos 1 . |
(4.49) |
Rm – среднее конусное расстояние (см. рис.3.1)
Rm R 0,5b, |
(4.50) |
где b – ширина зубчатого венца, определяемая по формуле
b m 0,28R; |
(4.51) |
dm1 и dm2 – средние делительные диаметры, определяемые по формулам
(3.14) и (3.15);
d1 и d2 – внешние делительные диаметры, определяемые по формулам
d1 m z1, |
d2 m z2 ; |
(4.52) |
ha – высота головки зуба на внешнем торце А (вид B), определяемая по формуле
ha m; |
(4.53) |
hf – высота ножки зуба на внешнем торце А, определяемая по формуле
hf 1,25m; |
(4.54) |
h – высота зуба на внешнем торце А, определяемая по формуле
h 2,25m; |
(4.55) |
da1 и da2 – внешние диаметры вершин зубьев, определяемые по формулам

|
da1 d1 2m cos 1, |
da2 d2 |
2m cos 2 ; |
(4.56) |
1 |
и 2 – углы делительных конусов, определяемые по формулам |
|
||
|
1 arctg z1 z2 , |
|
(4.57) |
|
|
2 90 1. |
|
(4.58) |
3. После определения геометрических параметров зубчатых колес приступим к выполнению компоновочного чертежа зубчатых колес, валов и подшипников.
Таблица 4.7
Высота заплечиков валов t3 и tБ (мм) по отношению к диаметру шейки d
предыдущей (меньшей) ступени
d |
10 - |
12 - |
17 - |
24 - |
32 - |
40 - |
45 - |
52 - |
60 - |
67 – |
80 - |
90 - |
100- |
|
12 |
17 |
22 |
30 |
38 |
44 |
50 |
58 |
65 |
75 |
85 |
95 |
110 |
t3 |
3 |
3,5 |
4 |
4,5 |
4,5 |
5 |
5 |
5,5 |
6 |
6,5 |
7,5 |
7,5 |
8 |
tБ |
3,5 |
4 |
4 |
5 |
5 |
6 |
6 |
6 |
7 |
8 |
9 |
9 |
10 |
h |
4 |
5 |
6 |
7 |
8 |
8 |
9 |
10 |
11 |
12 |
14 |
14 |
16 |
b |
4 |
5 |
6 |
8 |
10 |
12 |
14 |
16 |
18 |
20 |
22 |
25 |
28 |
Примечание. В табл. 4.7 b и h – ширина и высота шпонки.
Этот первый этап конструирования называется эскизным проектом, при котором определяют расположение деталей передачи, ориентировочные диаметры ступеней валов, выбирают типы подшипников и схему их установки, т.е. составляют эскизную компоновку деталей передачи (редуктора).
Начинают компоновку с вычерчивания зубчатых колес. В первую очередь тонкими осевыми линиями проводят в выбранном масштабе оси
шестерни ОО1 и колеса ОО2 |
(см. рис. 4.14). Затем намечают точки А, B и |
C. После этого осевыми (штрихпунктирными) линиями проводят |
|
начальные конусы AOB и BOC. |
|
Дальше от точки B (см. рис.3.1) откладывают высоту головки зуба |
|
ha m 3 мм и высоту |
ножки hf 1,25m 4мм, ширину зуба |
b m 6 3 18мм. Перпендикулярно к OA, OB и OC проводят линии образующих дополнительных конусов, которые очерчивают ширину зубчатого венца b у шестерни и у колеса. В точках А и С также откладывают высоту головки и ножки зуба. Затем соединяют полученные точки на внешних дополнительных конусах с вершиной О начальных конусов.
Получают полные контуры зубьев и зубчатого венца.
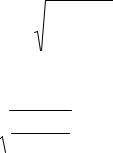
4. Приступаем к вычерчиванию вала-шестерни. Для этого необходимо сделать предварительные расчеты. Вал-шестерню будем называть быстроходным валом. Индексы, относящиеся к шестерне, будем обозначать
цифрой 1 согласно кинематической схеме z1 , а индексы, относящиеся к валу – цифрой 2, т.к. на кинематической схеме (см. рис.2.2) – это вал II.
Наименьший диаметр dВ2 входной шейки вала (см. рис. 4.15) рассчитывают на кручение по пониженным допускаемым напряжениям по формуле (4.1)
dВ2 3 |
М2 |
|
, |
|
0,2 к |
||||
|
|
где для быстроходного вала допускаемое напряжение к 50 Нмм2 . После подстановки получим
dВ2 336,8 103 15,4мм. 0,2 50
Округляем полученное значение до ближайшего согласно ряду Ra20, равному 16 мм.
длина этой шейки определяется по формуле (4.14)
lВ2 1,8dВ2 1,8 16 28мм.
Следующая ступенька вала – это шейка под уплотнение, которое устанавливается в крышке и уплотняет вал. Диаметр этой шейки определяется по формуле (4.59), которая применяется для конических редукторов,
dУi dВi |
2tЗ , |
(4.59) |
где tЗ – высота заплечика между шейками вала dВi и dУi , мм, которая определяется по табл. 4.7. После подстановки числовых значений получим dy2 = dB2 2t3 = 16 + 2 · 4 = 24 мм.
Согласно табл. 4.2 выбираем dy2 = 24 мм.
Длину этой шейки предварительно принимаем по формуле (4.13)
ly2 = dy2 = 24 мм.
В конических редукторах широкое применение находит консольное закрепление вала-шестерни (см. рис. 4.15). При этом подшипники 2, т.е. опоры вала, расположены по одну сторону от шестерни 9, а шестерня относительно опор расположена консольно. Подшипники,
поддерживающие вал шестерни, заключают в стакан 10. Конструкция узла получается простой, компактной и удобной для сборки и регулировки. Вся конструкция закрепляется одной гайкой 4. Наружные кольца подшипников 2 в осевом направлении упираются во внутренние заплечики стакана 10, внутренние кольца подшипников упираются с одной стороны в шестерню, а с другой – в гайку 4.
Для регулировки осевого зазора подшипников применяется стопорная многолапчатая шайба 3 (см. рис. 4.15 и 4.16), которая позволяет фиксировать гайку через каждые 15° ее поворота, чем обеспечивается
дискретность |
положения гайки при шаге |
резьбы t 1,5мм, равная |
s 0,06 мм. |
Таким образом, гарантируется |
минимальный осевой зазор |
0,06мм в радиально-упорных подшипниках 2.
Существуют другие варианты конструкции стакана, они приведены в пособиях /5,6 и 7/, но данная на рис. 4.15 конструкция предпочтительнее, потому что обеспечивает увеличение базы l2 – расстояния между радиальными реакциями подшипников, уменьшение расчетного вылета а0 консольной конической шестерни и повышение жесткости конструкции. Если развернуть подшипники на 180°, то точки приложения радиальных опор А иB перевернутся внутрь, расстояние между ними l2 значительно уменьшится, а консоль а0 увеличится.
Недостатком варианта по рис. 4.15 является то, что усложняется обработка посадочных диаметров под подшипники и обеспечение их соосности.
Диаметр резьбы dмi под гайку 4 определяется по формуле |
|
dмi dУi 2 4 . |
(4.60) |
Для проектируемого вала-шестерни
dm2 = dy2 + (2…4) = 24 + (2…4) = 26…28 ≈ 27…30 мм.
Диаметр шейки вала под подшипник должен быть dПi dмi .
Другое условие накладывает стопорная многолапчатая шайба 3 (см. рис. 4.16), для стопорения которой на валу фрезеруют шпоночный паз шириной а1. В пазу размещается язычок шайбы. Его ширина b а1 0,2 мм. Шайба 3 одевается на вал 1 так, как показано на рисунке. При этом диаметр шейки вала d1 l 0,5мм, где l– расстояние от язычка до противоположной стороны отверстия в шайбе. Шайбу двигают влево вдоль
осивала до резьбовой шейки. В этом месте шпоночный паз врезан в шейку ва-
ла диаметром d1 на расстоянии а2 от резьбовой шейки, равном длине отогнутой части язычка. Далее шайбу язычком опускают в паз, и она становится соосно с валом и резьбой. Теперь ее беспрепятственно можно двигать до упора в подшипник 2, а затем навинтить гайку. Итак, второе условие с учетом, что d1 dУi , т.е. резьбовой шейке предшествует шейка вала