
2533
.pdf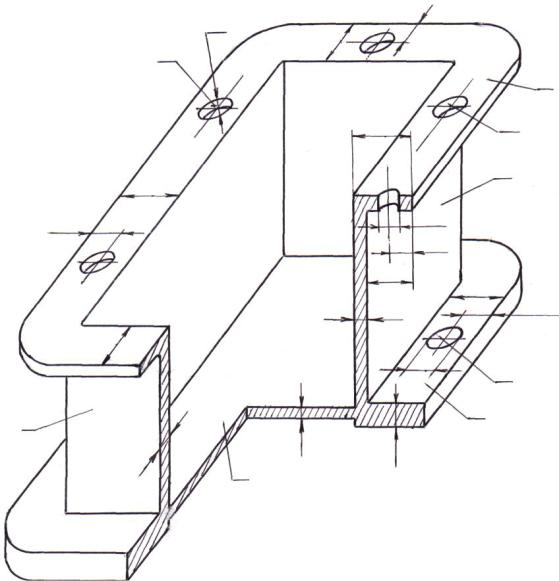
жим его компоновку согласно рис. 4.6. Фланец шириной
bр 2,5dc , |
(4.26) |
где dс – диаметр стяжных болтов, δ – толщина стенки корпуса, опоясывает корпус по периметру. В местах размещения подшипников фланец упирается в бобышки диаметрами Da3 и Da4 . Бобышки выступают за ширину фланца на 5 мм. Часть бобышки, расположенная под фланцем, обозначена штриховой линией, которая переходит в наружный контур стенки корпуса. Теперь вычерчиваем бобышки, диаметры которых были определены по формуле (4.18) и длина которых
lр bр 5 2,5dс δ 5, |
(4.27) |
где для проектируемого редуктора dс 12 мм; |
= 7 мм. После |
подстановки числовых значений в формулу (4.27) получим
lр 2,5 12 7 5 42 мм.
Внешние диаметры бобышек Da3 120 мм, Da4 130мм, внутренние их диаметры равны наружным диаметрам подшипников, т. е.
D |
|
|
с |
|
dc |
l |
|
|
|
||
|
|
5 |
р |
на |
|
b |
|
|
|
|
|
к |
|
|
bр |
|
|
bр |
|
|
lс |
|
dc |
|
|
lс 1,25dc |
|
|
|
|
|
|
|
|
2,5dc |
кр |
|
|
δ |
bр |
|
|
|
по |
|
dф |
|
tк |
|
|
|
|
|
|
|
мм |
1 |
|
|
|
|
|
|
|
|
δ |
ф |
|
δ |
d |
|
|
2 |
1,5 |
|
|
|
||
|
|
|
ки.
3
ширина
5
1
.28)
2,5dф
1,25dф
крышек
6
-
4
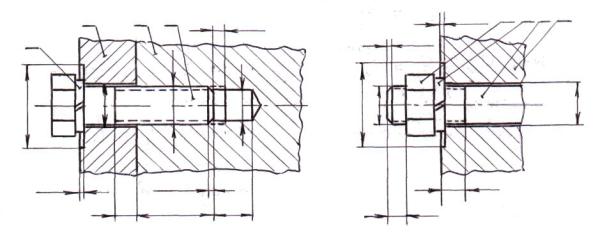
Вычерчиваем глухие крышки 13 и 14.
Сквозь крышки 9 и 12 проходят валы III и IV. Для герметизации внутренней полости редуктора от внешней среды в крышках устанавливают резиновые манжетные уплотнения 11 и 10. Размеры этих уплотнений приведены в табл. 4.2. Главным размером является внутренний диаметр уплотнения dУ , который соответствует диаметру шейки вала (см. рис. 4.5). В § 4.2 были выбраны манжеты:
для вала III dУ3 DУ3 BУ 38 58 10мм;
для вала IV dУ4 DУ4 BУ 48 70 10мм.
Манжеты располагаем на расстоянии 2 от внешнего торца крышек 9 и 12, как показано на рис. 4.6. Расстояние 2 3 5мм. Для облегчения установки манжет в отверстии крышки делается фаска шириной tУ и углом . Рекомендуют делать tУ 2 3мм и =15…30°. Внутренний торец крышки имеет кольцо шириной tц3 tц4 6мм.
Крышки к корпусу привинчиваются болтами 15, диаметр которых dБ и количество z выбираются по табл. 4.3. Диаметры подшипников D3 80мм и D4 90 мм попадают в один диапазон 63…95 мм, поэтому болты для III и IV вала имеют один диаметр dБ 8мм, а их количество
z 6штук. Отверстия под |
болты сверлятся в корпусе и крышке |
|
равномерно по окружности диаметром |
|
|
Dср 0,5 Da D |
(4.29) |
|
согласно рис. 4.7 и 4.10. Для крышки 9 (см. рис. 4.6) |
|
|
Dср3 0,5 Da3 |
D3 0,5120 80 100мм, |
|
для крышки 12 |
|
|
Dср4 0,5 Da4 |
D4 0,5130 90 110мм. |
|
Глубина сверления отверстий должна быть такой, чтобы болт мог
1 |
2 3 |
а2 |
а) |
1 |
5 4 3 2 б) |
4 |
|
|
|
с 45 |
|
d |
d' |
d |
d'' |
ц |
d |
d' |
d |
||||||
ц |
|
|
|
|
|
|
1 |
с 45 |
|
|
а1 |
|
|
|||
а1 |
a |
а3 |
Рис 4.10 |
а4 |
|
|
|
|
|
ввинчиваться на глубину a 1,5d , т. е. глубину, равную полутора диаметрам резьбы.
На рис. 4.10 изображены два варианта болтовых соединений а) и б). В варианте а) крышка 1 привинчивается к корпусу 2 болтом 3. При
|
|
Элементы болтовых соединений (рис. 4.10) |
Таблица 4.5 |
|||
|
|
|
||||
|
|
|
|
|
|
|
Пример |
|
Диаметр и шаг резьбы d t, мм |
|
|||
М6 1 |
М8 1,25 |
М10 1,5 |
М12 1,75 |
М16 2 |
||
a, мм |
10 |
12 |
16 |
20 |
25 |
|
a1 |
, мм |
3,5 |
4 |
4,5 |
5,5 |
6 |
a2 |
, мм |
2 |
2,5 |
3 |
3,5 |
4 |
a3, мм |
6 |
8 |
9 |
11 |
12 |
|
a4 |
, мм |
2 |
2,5 |
3 |
3,5 |
4 |
с, мм |
1 |
1,5 |
1,5 |
2 |
2 |
|
dц , мм |
13 |
16 |
20 |
25 |
32 |
этом в корпусе нарезана резьба и болт ввинчивается в чугунный корпус. Вариант этот прост и удобен, но имеет недостаток – резьба в хрупком чугуне непрочна, поэтому резьбовую часть а болта нужно выполнять длиной не менее 1,5d , и это соединение при частой разборке недолговечно. В варианте б) крышка 1 и корпус 2 (изображение б) повернуто на 180 ) сверлятся насквозь диаметром больше диаметра болта d . С противоположной стороны навинчивается гайка 5 и таким образом стягиваются крышка и корпус. Так как гайка стальная, то это соединение можно свинчивать и развинчивать много раз. Недостатками этого варианта является большая длина корпуса, а также необходимость иметь при свинчивании и развенчивании два ключа. В варианте а) свободная длина болта равна толщине крышки и болт завинчивается одним ключом.
На рис. 4.7 болты 5 и отверстия в крышке 1 и корпусе 2 вычерчены со всеми подробностями. На сборочных чертежах допускается изображение только болта без углубления отверстия на величину а3. Так изображено болтовое соединение на рис. 4.6 в левом нижнем углу.
На рис. 4.7 и 4.11 видно, что болты в крышках расположены диагонально, так как горизонтальная ось отверстия совпадает с плоскостью разъема. На сборочных чертежах допускается сечение а а (см. рис. 4.7) поворачивать в горизонтальную плоскость. Для этого на чертеже (см. рис. 4.6) сделан дополнительный вырыв в бобышке и крышке, в котором показано сечение а а.
С учетом всего вышесказанного вычерчиваем крышки 9 и 12 с успешными болтом 15 на своем компоновочном чертеже.
Отверстия под стяжные болты диаметром dc (рис. 4.6 и 4.9) сверлятся по периметру фланца на расстоянии lс от внешнего контура фланца.
Размер
lс 1,25dc . |
(4.30) |
Для рассматриваемого примера диаметр стяжного болта dc 12 мм. Подставляя это значение в формулу (4.30), получим
lс 1,25 12 15мм.
Разметку центров отверстий производят следующим образом. Болты, стягивающие подшипники, устанавливаются по краям бобышек на расстоянии (см. рис. 4.7)
ta 0,5 Da D |
(4.31) |
|
для вала III |
D3 0,5120 80 20мм; |
|
ta3 0,5 Da3 |
|
|
для вала IV |
|
|
ta4 0,5 Da4 |
D4 0,5130 90 20мм. |
|
Между бобышками, если перемычка имеет размер (см. рис. 4.6) tП 2dc ,
устанавливают в средней части перемычки один стяжной болт, если перемычка
tП 2 ta3 ta4 ,
устанавливают два стяжных болта по краям бобышек на расстояниях ta3 и
ta4 .
Вверху и внизу (см. рис. 4.6) отверстия во фланцах делают в средней части.
После разметки центров отверстий выбирают вариант а) или б) по рис. 4.11. Для варианта а) сверлят отверстия во фланце корпуса диаметром
(см. рис. 4.10)
dc'' dc t , |
(4.32) |
где d''– диаметр отверстия под резьбу, мм; dc – диаметр резьбы стяжного болта, мм; t – шаг резьбы, мм. Для резьбы М12 1,75
dc'' 12 1,75 10,25.
Затем нарезают резьбу. Во фланцах крышки корпуса (см. рис. 4.11) сверлят отверстия диаметром
dc' dc 1мм. |
(4.33) |
Для резьбы М12 1,75 dc' 12 1 13 мм.
Для варианта б) сверлят отверстия во фланцах крышки и корпуса диаметром d' .
4.5. Построение главного вида (окончание компоновки)
На рис. 4.11 в нижней части изображен корпус в плане, т.е. вид сверху в соответствии с рис. 4.6, но повернутый на 90° и уменьшенный в 1,3 раза. Верхняя часть вида в плане от оси симметрии закрыта крышкой корпуса, чтобы показать вид крышки сверху.
Главный вид изображен с крышкой 2, которая приподнята над корпусом 1 и представляет собой отдельный чертеж.
Вначале на компоновке изображается вид в плане корпуса без крышки, вычерченный по размерам рис. 4.6 в выбранном масштабе. Построение главного вида начинают с нанесения горизонтальной и вертикальной осей, проходящих через центры отверстий под подшипники D3и D4 . Затем циркулем проводят окружности этих отверстий. Далее циркулем проводят окружности бобышек диаметрами D3и D4 и получают контур, похожий на цифру 8. Затем на расстоянии ас от центров отверстий проводят вертикальные оси стяжных болтов. Расстояние ас определяется по формуле
ас 0,5Da . |
(4.34) |
Для оси III (вал шестерни)
ас3 0,5Da3 0,5 120 60мм,
для оси IV (вал колеса)
ас4 0,5Da4 0,5 130 65мм.
Определяют элементы фланцев корпуса и крышки:толщина полки разъема редуктора
t 1,5dc .
толщина полки у бобышки (толщина утолщения)
tc 0,3Da.
расстояние от центра болта до края утолщения
с 1,5dc .
После этого вычерчивают выступы под стяжные болты согласно размерам с3, tc3 , с4 , tc4 в корпусе и симметрично в крышке корпуса. Затем вычерчивают тонкую часть фланцев толщиной 1,5dc слева и справа по чертежу в корпусе и в крышке.
Следующим этапом будет вычерчивание коробочки корпуса и крышки. Для этого проводим штриховой линией окружность выступов зубчатого колеса. Дно корпуса определяет объем масла или емкость масляной ванны редуктора. В одноступенчатом редукторе на каждый киловатт передаваемой мощности должно приходиться 0,5…0,7 л масла. Площадь масляной ванны определили как произведение bк R3 a R4 согласно рис. 4.6, где bк b 2c B; bк – ширина внутренней части коробки корпуса редуктора; b = ψm – ширина зубчатого колеса; с 10m – расстояние от торца колеса до середины подшипника; B – ширина подшипника тихоходного вала. Таким образом, площадь дна масляной ванны где R3 и R4 определяются по формуле (4.17); a – межцентровое
расстояние. |
|
|
|
Sк b 2c B R3 |
a R4 , |
(4.35) |
|
Глубина масляной ванны |
|
|
|
hк ho |
hм, |
(4.36) |
где ho – расстояние от окружности выступов зубчатого колеса до дна корпуса (см. рис. 4.11); hм – глубина погружения зубчатого колеса в масляную ванну.
Объем масляной ванны
Vм hк Sк ho hм Sк Vo Nэ, |
(4.37) |
где V0 = (500….700)·103 мм3/кВт – удельный объем масла; Nэ – мощность электродвигателя, кВт.
Глубина погружения зубчатого колеса составляет
hм 2m 8m, |
(4.38) |
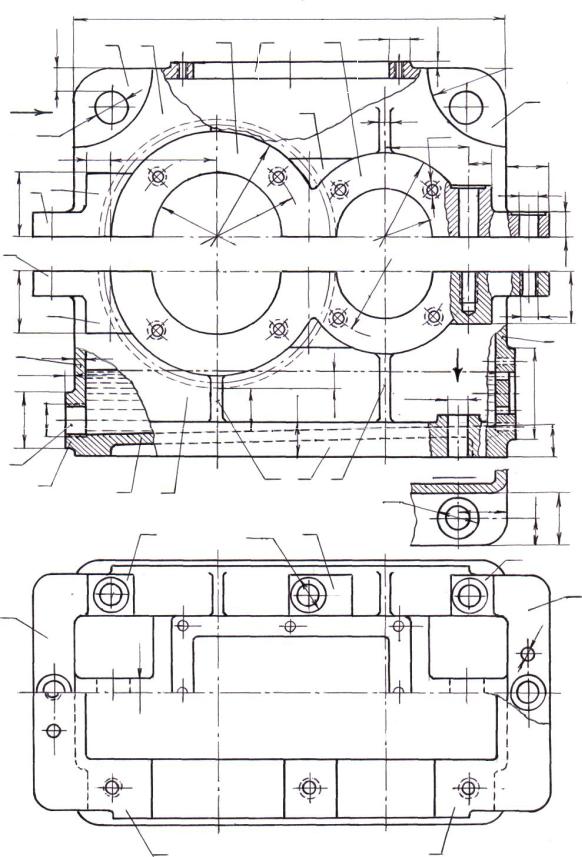
но не менее 10 мм, где m – модуль, мм. Из сказанного следует, что hм min =
10 мм, поэтому при значениях модуля m 5 мм формула (4.38) |
может |
быть записана в виде |
|
hм 10 8m. |
(4.39) |
Решая уравнение (4.37) относительно ho , получим |
|
0,7de
А
de
12 13
tc4
12
c4 |
13 |
t
4 3…5
пр |
пр |
D |
d |
3 |
8 |
|
12
|
|
|
|
Lкор |
|
|
|
11 |
2 |
6 |
|
|
|
2,5dк |
|
10 |
6 |
3…5 |
|||||
|
|
|
|
Рис. 4.11 |
|
||
|
|
|
|
|
|
||
|
|
|
|
|
|
|
Re |
|
|
|
|
|
|
|
|
|
|
|
|
|
13 |
δ |
|
|
|
|
|
|
|
dБ |
|
с4 |
|
ас4 |
|
|
|
ас3 |
|
|
|
|
|
с3 |
|||
|
|
|
|
|
|||
|
|
|
|
|
|
Da3 |
|
|
|
Da4 |
|
|
|||
|
|
|
Dср4 |
|
|
|
D4 |
D3 |
|
|
|
Dср3 |
|
|
|
|
|
|
|
А |
|
|
|
|
ф |
|
|
' |
|
|
|
|
|
|
dф |
|
|
|
|
0 |
d |
|
|
|
|
|
|
h |
1,5 |
м |
|
|
|
|
|
h |
|
|
||
9 |
1 |
IV |
7 |
5 |
7 |
III |
Вид А |
|
|
|
Dф |
|
|||
|
|
|
|
|
|
bф |
|
|
13 |
|
Dc |
13 |
|
|
|
|
|
|
|
|
2,5δ
40)
11
2,5dc dc'
d1,5 c
c3 t dc
4
dm
2
ф |
|
d |
ф |
1,25 |
b |
13 |
|
12
dШ
6 |
6 |

Определим глубину ho из условия минимального объема масла, соответствующего V0 min = 500 мм3/кВт и hм min.
h |
|
500 103 3 |
h |
|
S |
||||
o |
|
м min |
к
Для решаемого примера Nэ 3 кВт, m = 4 мм, hм min=10 мм,
Sk = (40 + 2 · 40 – 20)(85 + 148 + 90)=32300 мм2.
После подстановки получим
ho 500 103 3 10 36мм. 32300
Согласно формуле (4.38) для решаемого нами примера hм min = 10 мм; hмmax
= 8m = 8 · 4 = 32 мм, а разность уровней ∆hм =hм max – hм min =32–10=22 мм.
Дно корпуса делают с уклоном 2°, чтобы отработанное масло можно было слить через резьбовое отверстие 3, в которое при сборке ввинчивается пробка 31 (см. рис.4.1).
Стенки корпуса и крышки совпадают и представляют единую коробочку после их сборки. Вычерчивают вертикальные стенки слева и справа на главном виде, перенося положение стенок с вида в плане. После вычерчивания дна и стенок корпуса получается прямоугольная коробочка, нижняя часть которой используется в качестве масляной ванны. В левой части делают сливное отверстие 30 (см. рис. 4.1), а справа, где дно корпуса приподнято, устанавливают смотровое стекло 33, т. е. маслоуказатель, через который виден уровень масла. Пример такого маслоуказателя показан на рис. 4.12. Центральная ось маслоуказателя должна располагаться в средине разностей уровней масла 3: нижнего 1 и верхнего 2. Нижний уровень масла. определяют по формуле (4.36) и по рис. 4.11.
hk min = h0 + hм min = 36 + 10 = 46 (мм)
Верхний уровень масла
hk max = h0 = hм max = 36 + 32 = 38 мм.
Разность уровней
∆h=hk max – hk min = 68 – 46 = 22 мм.
В нижней части стенки корпуса справа проводят центральную ось маслоуказателя (см. рис. 4.11) и относительно нее делают круглый выступ диаметром
dm 60 5 65мм,
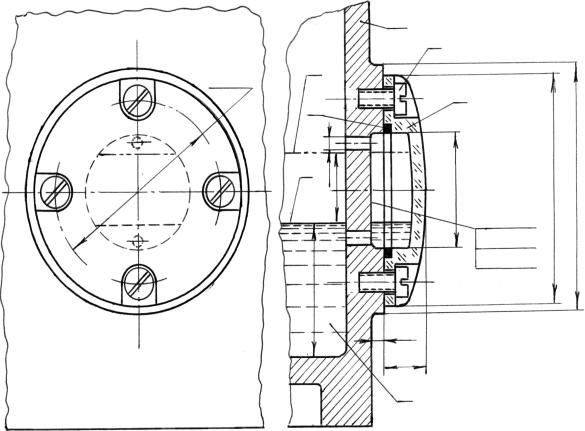
7
2
Ø48
6 5
1 |
4 |
30 |
60 65 |
|
Ø |
||
|
h |
Ø |
Ø Ø |
|
м |
|
|
|
|
|
Красит |
|
|
|
ь белой |
|
|
|
эмалью |
k |
|
|
|
h |
|
|
|
|
|
3… |
|
|
|
12 |
|
|
|
3 |
|
Рис. 4.12
который выступает от стенки 7 на величину 3…5 мм (см. рис. 4.12). В центре выступа делают круглое углубление диаметром 30 мм и глубиной 3…5 мм. Углубление красят белой эмалью, чтобы был хорошо виден уровень масла. Углубление соединяется с внутренней полостью корпуса двумя отверстиями диаметром 4 мм. К плоской поверхности круглого выступа четырьмя винтами 4 диаметром 5 мм (М5) крепится прозрачная крышка 5 маслоуказателя. Между крышкой и корпусом устанавливается резиновое уплотняющее кольцо 6.
На рис. 4.13 показан вид А, т. е. профильная проекция корпуса, изображенного на рис. 4.11. На этих двух рисунках хорошо видны основные элементы корпуса: стенки 4, опорная подошва 5 и гнезда (бобышки) 6 для подшипников. Эти гнезда (бобышки) подкрепляют ребрами 7, которые создают дополнительные соединения между гнездами, стенкой корпуса и его подошвой, повышают общую жесткость конструкции и укрепляют переход от стенки к подошве, т. к. в районе
этого перехода нередко образуются трещины. Особенно важны ребра у бобышек подшипников тихоходного вала, которые нагружены сильнее. В нижней части корпуса имеется бобышка 8 с резьбовым отверстием для маслоспускной пробки. Чтобы загрязненное масло сливалось полностью, дно 9 корпуса делают с уклоном 2°.
Крышка корпуса 2 по конструкции аналогична корпусу 1, поэтому основные элементы ее обозначены теми же номерами. В крышке корпуса обычно предусматривают люк 10, размеры которого должны быть достаточны для осмотра передачи. Люк закрывают плоской крышкой 25 (см. рис. 4.1) литой чугунной или из стального листа. Крышка крепится болтами 26. В крышку могут вворачивать отдушину 27. Если корпус большой, то отдушину можно вворачивать непосредственно в потолочную стенку крышки корпуса.
Для подъема и транспортировки корпусных деталей и редуктора в сборе в крышке корпуса делают проушины 11 (см. рис. 4.11 и 4.13). Отверстия в проушинах de 0,02a 20мм. Радиус Re 2,2de 2 4мм.
К основным элементам относятся также фланцы 12, с помощью которых стяжными болтами прижимаются крышка 2 и корпус 1. Во фланце крышки полезно предусмотреть резьбовое отверстие, чтобы при разборке ввинтить болт и отжать крышку от корпуса.
Для болтов, расположенных по краям подшипниковых гнезд, делают приливы 13. Во фланцах крышки 2 под стяжные болты сверлят гладкие отверстия диаметром dc dc 1мм, а сверху делают цековки диаметром Dc 2dc и глубиной 1 мм, чтобы обеспечить перпендикулярность поверхности под головку болта. Во фланце корпуса делают резьбовые отверстия, в которые заворачивают, пропуская сквозь отверстия в крышке, болты и стягивают крышку и корпус.
В подошве 5 сверлят обычно четыре отверстия диаметром dф,
сквозь которые пропускают фундаментные болты диаметром dф для
крепления редуктора к фундаменту или станине. Диаметр отверстий dф dф 1мм.
Поскольку подошва сверху закрыта фланцем, цековку отверстий сделать невозможно. Поэтому на подошве делают приливы 14 диаметром Dф 2dф , которые фрезеруют до высоты 2…3 мм, обеспечивая
перпендикулярность торца прилива к оси отверстия.
Когда на главном виде тонкими линиями изображен корпус и крышка редуктора (см. рис. 4.1), приступают к вычерчиванию остальных деталей.
Вначале вычерчивают стяжные болты. Два болта нужно показать в