
2533
.pdf
Для уточнения межосевого расстояния вводится коэффициент обратного сдвига или уравнительного смещения
у = хС – с. |
(3.9) |
Формулы для определения основных размеров зацепления прямозубых передач с цилиндрическими колесами наружного зацепления с угловой коррекцией приведены ниже.
Делительное межосевое расстояние некорригированных зубчатых колес
а0 = 0,5 т ·zС. |
(3.10) |
Межосевое расстояние корригированных зубчатых колес |
|
а = 0,5 т · zС + с · т= 0,5 ·т ·zС + хС т - ут. |
(3.11) |
Высота зуба |
|
h = 2,25m – ym. |
(3.12) |
Делительные диаметры |
|
d01 = m z1 ; d02= m z2. |
(3.13) |
Начальные диаметры |
|
d1 = 2а / (и + 1); d2 = 2а – d1. |
(3.14) |
Диаметры вершин зубьев |
|
dа1 = m (z1 + 2 +2х1 – 2у); |
(3.15) |
dа2 = m (z2 + 2 + 2х2 – 2у). |
(3.16) |
Диаметры впадин зубьев |
|
df1 = m (z1 – 2,5 + 2х1 ); |
(3.17) |
df2 = m (z2 – 2,5 + 2х2). |
(3.18) |
Толщина зуба по делительной окружности |
|
s m 0,5 2x tg . |
(3.19) |
Угол зацепления при α 0= 20 0 |
|
cos α = а0 · cos α0 / а = m (z1 + z2) · cos α0 / 2а. |
(3.20) |
Коэффициент обратного сдвига у и суммарный коэффициент смещения хС определяются по табл. 3.1 по известным с и zС. Пример. Дано: z1 = 15, z2 = 45, zС = 60, m = 3 мм, а0 =90 мм, а = 92 мм. Нужно определить хС . По формуле (3.8) находим
са 0,5т zс 92 0,5 3 60 0,667.
т3
Величина 1000с / zС = 1000·0,667/60 = 11,11. Методом интерполяции находим по табл. 3.1 величину 1000у / zС = 0,88. Отсюда находим коэффициент у
у = 0,88· zС /1000 = 0,88·60 / 1000 =0,0528.
Таблица 3.1
Определение коэффициента обратного сдвига
1000с / zС |
1 |
2 |
3 |
4 |
5 |
6 |
7 |
8 |
9 |
10 |
1000у / zС |
0,003 |
0,019 |
0,063 |
0,125 |
0,19 |
0,265 |
0,35 |
0,45 |
0,57 |
0,7 |
|
|
|
|
|
|
|
|
|
|
|
1000с / zС |
11 |
12 |
13 |
14 |
15 |
16 |
17 |
18 |
19 |
20 |
1000у / zС |
0,85 |
1 |
1,17 |
1,35 |
1,55 |
1,75 |
1,97 |
2,2 |
2,43 |
2,675 |
|
|
|
|
|
|
|
|
|
|
|
1000с / zС |
21 |
22 |
23 |
24 |
25 |
26 |
27 |
28 |
29 |
30 |
1000у / zС |
2,93 |
3,2 |
3,48 |
3,77 |
4,08 |
4,4 |
4,72 |
5,05 |
5,37 |
5,72 |
|
|
|
|
|
|
|
|
|
|
|
1000с / zС |
31 |
32 |
33 |
34 |
35 |
36 |
37 |
38 |
39 |
40 |
1000у / zС |
6,07 |
6,44 |
6,82 |
7,22 |
7,62 |
8,01 |
8,4 |
8,83 |
9,26 |
9,68 |
Теперь по формуле (3.9) определяем суммарный коэффициент смещения
хС = с + у = 0,667 + 0,0528 = 0,7198 ≈0,72.
Коэффициент смещения шестерни определяется по формуле
х1 0,5 хС z2 |
z1 xС y / zС . |
(3.21) |
Если использовать данные из приведенного расчета, то получим
х1 0,5 0,72 42 15 0,72 0,0528 /60 0,1932 0,193.
Коэффициент смещения колеса
х2 = хС – х1 . |
(3.22) |
Используя приведенный расчет, получим
х2 = 0,72 – 0,193 = 0,527.
Угол зацепления определим по формуле (3.20)
cos α = а0 · cos α0 / а = 90 · 0,9397 / 92 = 0,9193,
аугол α = arccos 0,9193 = 23,2 0 = 230 11′.
3.3.Определение модуля цилиндрических колес
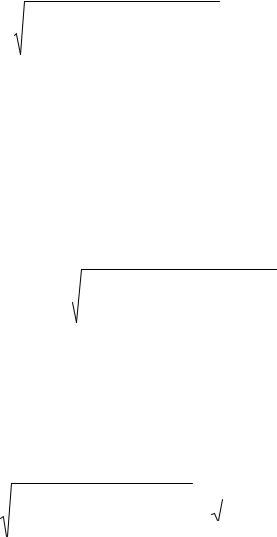
При расчете зубьев цилиндрических прямозубых передач с угловой коррекцией на контактную прочность по формуле (16.46) /1/ необходимо учитывать увеличение угла зацепления α, радиусов кривизны боковых поверхностей (профилей) зубьев, увеличение коэффициента перекрытия εα и длины контактной линии. Все это приводит к увеличению коэффициента контактного напряжения [CН], которое учитывается коэффициентом
кα = tgα / tgα0 .
Этот коэффициент вводят в формулу (16.46) см. /1/
т 3 |
|
2 М1 к |
|
u12 1 |
. |
(3.23) |
СН |
к z12 |
|
||||
|
|
u12 |
|
Проведем расчет цилиндрической зубчатой передачи z3 – z4 (см. рис. 2.2), используя приведенные выше формулы.
Модуль цилиндрической прямозубой передачи определяется по формуле (3.23).
Угол зацепления корригированных зубчатых колес определен в §. 3.4 и равен α = 220. Стандартный угол α0 = 20 0. Коэффициент
кα = tg22 0/ tg20 0=1,1.
В формуле (3.23) следует заменить индексы
т |
2 |
3 |
2 М3 к |
|
u34 1 |
, |
СН к z32 |
|
|||||
|
|
|
u34 |
где т2– модуль цилиндрической передачи, мм; М3 = 107·103 Н·мм – крутящий момент на ΙΙΙ – м валу; к = 1,3 – коэффициент нагрузки; и34 = z4 /z3 = =3,1 – передаточное отношение; [CН] =1,5 Н/мм2 – коэффициент контактной прочности для стали 45; ψ =10 – коэффициент ширины зуба; z3 =18 – число зубьев шестерни; кα = 1,11 – коэффициент угла зацепления.
Подставляя числовые значения в формулу (3.23), получим
т2 3 |
3,1 1 |
2 107 103 1,3 |
3 |
|
|
||
68,2 4,086 мм. |
|||||||
|
|
|
|||||
3,1 |
1,5 1,11 10 182 |
||||||
|
|
|
|
|
Стандартный ряд модулей: 1; 1,25; 1,5; 2; 2,5; 3; 4; 5; 6; 8; 10 мм.
Округлять полученный результат нужно до ближайшего большего стандартного, но т.к. (4,086 – 4) / 4 = 0,02, т.е. всего 2 %, модуль можно выбрать т2 = 4.
3.4. Определение размеров зубчатых колес
Расчет цилиндрической передачи следует начинать с определения межосевого расстояния, т.к. его нужно округлять до стандартного ряда Ra40 согласно ГОСТ 6636 – 69 (табл. 3.2).
Таблица 3.2
Ряд чисел для выбора нормальных линейных размеров
№ |
Ra40 |
20 |
21 |
22 |
24 |
25 |
26 |
28 |
30 |
32 |
34 |
36 |
38 |
Ra40 |
40 |
42 |
45 |
48 |
50 |
53 |
56 |
60 |
63 |
67 |
71 |
75 |
|
ряда |
Ra40 |
80 |
85 |
90 |
95 |
100 |
105 |
110 |
120 |
125 |
130 |
140 |
150 |
чисел |
Ra40 |
160 |
170 |
180 |
190 |
200 |
210 |
220 |
240 |
250 |
260 |
280 |
300 |
|
Ra40 |
320 |
340 |
360 |
380 |
400 |
420 |
450 |
480 |
500 |
530 |
560 |
600 |
Определяем расстояние между осями валов III и IV (см. рис. 2.2):
а034 = т2· (z4 + z3) / 2 = 4 (18+56) / 2 =148 мм,
где а034 – межосевое расстояние некорригированных колес.
Согласно ряду Ra40 выбираем значение ближайшего большего числа. Стандартное межосевое расстояние а34 = 150 мм. Это межосевое расстояние корригированных колес.
Чтобы увеличить межосевое расстояние, нужно произвести коррекцию зубчатого зацепления.
Определяем коэффициент отклонения межосевого расстояния
с = (а34– а034) / т2 = (150 –148) / 4 = 0,5.
Величина
1000с / zС= 1000·0,5 / 7=6,75,
где zС = z4 + z3 – суммарное число зубьев, zС= 74.
По табл. 3.1, применяя метод интерполирования, находим
6 |
7 |
∆ = 0,35 – 0,265. |
|
0,265 |
0,35 |
||
|
Если эту разность разделить на 7 – 6 и умножить на 6,75 – 6 = 0,75, то получим приращение к числу 0,265. Прибавив приращение к числу 0,265, получим искомую величину, которая соответствует числу 6,75. Итак, искомая величина
1000у / zС= (0,35 – 0,265)·0,75 + 0,265 = 0,329.
Отсюда находим коэффициент у
у = 0,329· zС/1000 = 0,329·74 /1000 =0,0243.
Теперь по формуле (3.9) определяем суммарный коэффициент смещения
хС = у + с = 0,0243 + 0,5 = 0,5243.
Коэффициент смещения шестерни находим по формуле (3.21)
х1 0,5 хС z2 z1 xС y /zС
0,5 0,5243 56 18 0,5243 0,0243 /74 0,1338.
Коэффициент смещения колеса находим по формуле (3.22)
х2 = хС – х1 = 0,5243 – 0,1338 =0,3905.
Угол зацепления корригированных колес найдем из формулы (3.20)
cos α = а034 · cos α0 / а34 = 148·0,9397 / 150 = 0,9272,
где α0 = 200 – стандартный угол зацепления. Угол зацепления корригированных колес
α = arccos 0,9272 = 220.
Делительные диаметры колес определим из формулы (3.13)
– диаметр шестерни
d03 = m2 z3 = 4 · 18 = 72 мм;
– диаметр колеса
d04 = m2 z4 = 4 · 56 = 224 мм.
Найдем начальные диаметры колес, используя формулы (3.14):
– диаметр шестерни
d3 = 2а34 / (и34 + 1) = 2·150 / (3,1 + 1) = 73,17 мм;
– диаметр колеса
d4 = 2а34 – d3 = 2 ·150 – 73,17 = 226,83 мм.
Диаметры вершин зубьев определим по формуле (3.16) и (3.17):
– диаметр шестерни
dа3 = m2 (z3 + 2 + 2х1 – 2у) = 4(18 + 2 +2 · 0,1338 – 2 · 0,0243) = 80,88 мм;
– диаметр колеса
dа4 = m2 (z4 + 2 + 2х2 – 2у) = 4(56 + 2 + 2 · 0,3905 - 2 · 0,0243) = 234,93 мм.
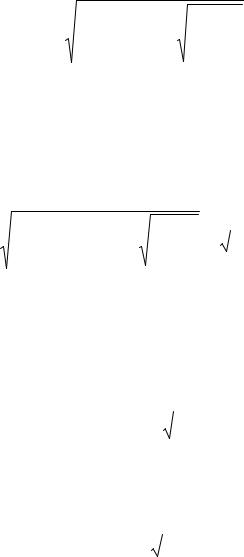
Ширину зубчатого колеса найдем по известной формуле
b4 = ψ · m2 = 10 · 4 = 40 мм.
3.5. Определение модуля конических колес
Проведем расчет конической зубчатой передачи z1 – z2 (см. рис. 2.2). В
конической передаче полюс зацепления П расположен в середине зуба
(см. рис. 3.3.).
Сечение Ι – I , проходящее через полюс и перпендикулярное к оси зуба, называется средним сечением. Модуль в этом сечении определяется по формуле [1, с.176]
т |
|
3 |
2 М2 к |
|
и232 1 |
|
|||
т |
|
|
|
|
|
, |
(3.24) |
||
С |
|
z2 |
|
||||||
|
|
Н |
|
и2 |
|
||||
|
|
|
|
1 |
23 |
|
|
где тт – модуль в среднем сечении зуба, мм; М2 – крутящий момент на ΙΙ валу, Н·мм; ψ = 6…10 – коэффициент ширины зуба; и23 = z2 / z1 = 3 – передаточное отношение конической передачи; z1 = 20 – число зубьев конической шестерни; z2 = 60 – число зубьев конического колеса; остальные параметры соответствуют цилиндрической передаче.
После подстановки числовых значений в формулу (3.24) получим
|
|
2 36,8 103 |
1,3 |
3 |
2 1 |
|
|
||
|
|
|
|
||||||
тт |
3 |
|
|
|
|
|
3 |
25,06 2,93 мм. |
|
1,5 6 202 |
|
|
32 |
||||||
|
|
|
|
|
|
|
Принимать тт меньше 1,5 мм не рекомендуется [3, с.211]. Стандартный модуль конического зацепления выбирается на
поверхности дополнительного конуса А (см. рис. 3.3). Модуль на этой поверхности определяется по формуле
|
|
|
|
|
|
|
|
|
|
|
|
|
|
|
|
т т |
т |
|
1 |
|
|
|
|
|
|
|
, |
(3.25) |
|||
|
|
|
|
|
|
|
|
|
|||||||
1 |
|
|
|
z1 |
|
|
1 и232 |
|
|
|
|||||
|
|
|
|
|
|
|
|
|
|||||||
где т1 – модуль конической передачи, т.е. первой зубчатой передачи. |
|
||||||||||||||
После подстановки числовых значений в формулу (3.25) получим |
|
||||||||||||||
|
|
|
|
|
|
|
2 |
|
|
|
|
|
|
|
|
т 2,79 1 |
|
|
|
|
|
|
|
|
|
3,054 мм. |
|
||||
|
|
|
|
|
|
|
|
|
|||||||
1 |
|
|
|
20 |
|
1 3 |
2 |
|
|
|
|
|
|||
|
|
|
|
|
|
|
|
|
|
|
Поскольку 0,054 составляет всего лишь 1,8 % от 3, то значение модуля можно округлять в меньшую сторону. Выбираем стандартное значение модуля т1 = 3 мм. Уточняем значение модуля тm в среднем сечении зуба
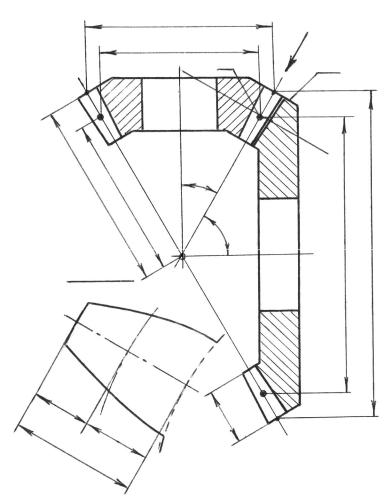
d1
dm1
I П
A B
δ1
R Rm
δ2
О
Вид В
ha в
hf С
h
Рис. 3.3
по формуле
тт = т1 – b·sin δ1 /z1 ,
где b = ψ · m2 = 6 · 3 = 18 мм – ширина зуба. Из рис. 3.3 находим отношение
B
A
I
m2 |
2 |
d |
d |
(3.26)
(d1 / 2) / (d2 / 2) = d1 / d2 = tg δ1. |
(3.27) |
Так как d1 = m z1 и d2 = m z2, угол конуса шестерни δ1 |
определяется по |
формуле |
|
tg δ1 = m1 z1 / m1 z2 = z1 / z2 = i23 = 1 / u23 . |
(3.28) |
После подстановки числовых значений получим
tg δ1 = 20 / 60= 0,333; δ1 =18,43 0; sin δ1 =0,316.
Теперь значение b и sin δ1 подставляем в формулу (3.26) и получаем уточненное значение тт:
тт = 3 – 18·0,316 / 20 = 2,844 мм.
Рассчитаем геометрические параметры конической передачи.
Диаметр начальной окружности шестерни |
|
d1 = m1 z1 = 3 · 20 = 60 мм. |
|
Диаметр начальной окружности колеса |
|
d2 = m1 z2 =3 · 60 = 180 мм. |
|
Угол начального конуса конического колеса |
|
δ2 = 90 0 – δ1 , |
(3.29) |
подставляя числовые значения, получим δ2 = 90 0 – 18,43 0 = 71,57 0. Средние диаметры зубчатых колес определяются по формулам:
– диаметр конической шестерни
dт1 = mт z1, |
(3.30) |
после подстановки числовых значений dт1 = 2,844 · 20 = 56,9 мм;
– диаметр конического колеса
dт2 = mт z2 , |
(3.31) |
подставляя, получим dт2 = 2,844 · 60 = 170,6 мм.
Внешние диаметры зубчатых колес (диаметры окружностей выступов) определяется по формулам:
– диаметр конической шестерни
dа1 = d1 + 2m1· cos δ1 = m1 (z1 + 2· cos δ1); |
(3.32) |
– диаметр конического колеса
dа2 = d2 + 2m1 · cos δ2 = m1 (z2 + 2· cos δ2). |
(3.33) |
После подстановки числовых значений в формулы (3.32) и (3.33) получим:
– внешний диаметр шестерни
dа1 = 3 (20 + 2· 0,949) = 65,7 мм;
– внешний диаметр колеса
dа2 = 3 (60 + 2· 0,316) = 181,9 мм.
3.6. Определение сил в зубчатых зацеплениях
Из пособия /1/ известно, что в цилиндрическом зацеплении зуб шестерни z3 (рис. 3.4) давит на зуб колеса z4 в полюсе зацепления П силой F под
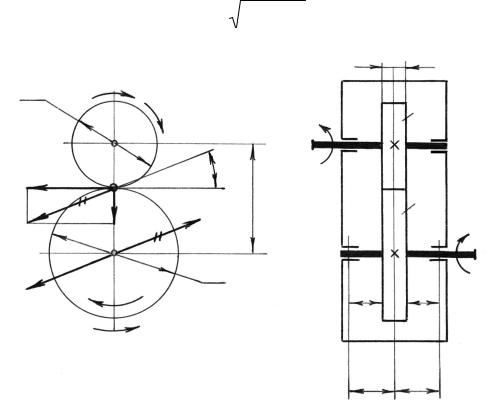
углом α. Силу F, приложенную в полюсе П, раскладывают на две составляющие: окружную силу Ft и радиальную Fr.
Окружная сила вычисляется по формуле
Ft = 2М3 / d3 , |
(3.34) |
где М3 – крутящий момент на шестерне; d3 – диаметр начальной окружности шестерни.
Радиальная сила вычисляется по формуле
Fr = Ft · tg α . |
(3.35) |
Полная сила F определяется по теореме Пифагора
|
|
F F |
2 |
F |
2 . |
(3.36) |
|
|
t |
r |
|
||
|
|
|
|
|
|
b |
d3 |
w3 |
|
|
|
|
|
|
M3 |
|
|
|
z3 |
|
|
O3 |
|
|
M3 |
||
|
|
|
III |
|
||
|
|
|
|
|
||
Ft |
П |
a |
|
|
|
|
|
|
|
|
z4 |
||
F |
|
a |
|
|
|
|
Fr |
F |
|
|
|
M4 |
|
|
|
|
A |
|||
|
|
|
|
|
B |
|
F |
O4 |
d4 |
|
|
IV |
|
|
|
|
|
|||
|
M4 |
|
|
|
c |
c |
|
|
w4 |
|
|
|
|
|
|
|
|
|
a |
a |
Рис. 3.4
Используя предыдущие расчеты согласно рис. 2.2, где крутящий момент на валу ΙΙΙ М3 =107 Н·м, а начальный диаметр шестерни d3 = 73,17 мм, определим окружную силу по формуле (3.34)
Ft =2М3 / d3 =2·107 / 0,073 = 2925 Н = 2,925 кН.
Радиальная сила определится по формуле (3.35)
Fr = Ft · tg α = 2925· tg220 = 1182 Н = 1,18 кН,
а полная сила
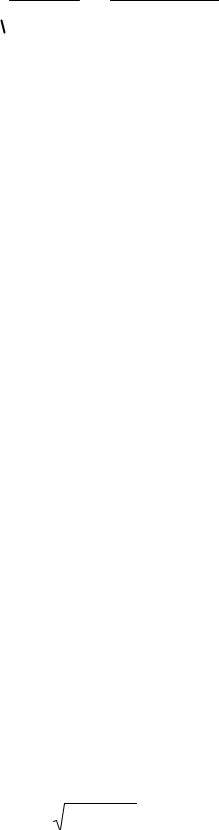
F Ft2 Fr2
2,9252 1,182 3,12 кН.
Сила F приложена в полюсе зацепления П (см. рис. 3.4). Чтобы узнать, как она действует на вал ΙV (О4), нужно перенести ее в точку О4. Для этого в точке О4 прикладывают две уравновешенные силы равные и параллельные силе F. Тогда силы, перечеркнутые двумя черточками, будут создавать крутящий момент М4 на зубчатом колесе, а сила F, не перечеркнутая и приложенная в точке О4, будет действовать на вал IV в центре зубчатого колеса z4 , вызывая реакции в опорах А и В и изгибая вал IV. Реакции в опорах являются радиальными силами давления на подшипники RА и RВ , которые будут определяться при уточненном (проверочном) расчете вала.
Сила F является внешней силой, приложенной к валу. Коническое зацепление отличается от цилиндрического тем, что сила давления F зуба шестерни на зуб колеса раскладывается на три составляющие (рис. 3.5). Окружная сила Ft направлена по касательной к начальным окружностям колеса и шестерни. Индексом 2 будем обозначать силы давления шестерни на колесо, приложенные к колесу: Fr2 – радиальная сила, направленная от точки касания (полюса) П к центру колеса О3, Fа2 – осевая сила, направленная вдоль оси колеса О3О. Силы Fr2 и Fа2 всегда направлены от шестерни (см. рис. 3.5 и 3.6).
Окружная сила Ft находится по формуле
Ft =2М2 / dт1, |
(3.37) |
где М2 – крутящий момент на конической шестерне, Н·мм, dт1 – средний начальный диаметр шестерни, мм.
Радиальная сила определяется по формуле
Fr2 = Ft · tg α ·sin δ1, |
(3.38) |
где α – угол зацепления (α = 20 0 ); δ1 – угол начального конуса шестерни. Осевая сила определяется по формуле
Fа2 = Ft · tg α · cos δ1. |
(3.39) |
Силы Ft и Fr2 направлены перпендикулярно к валу ΙΙΙ, поэтому их можно объединить как в цилиндрическом зацеплении, сложив их геометрически. Сложение векторов производят по формуле
F |
F2 |
F2 |
, |
(3.40) |
2 |
t |
r2 |
|
|
где F2 – суммарная радиальная сила давления шестерни на вал ΙΙΙ.
Продолжим силовые расчеты передач ленточного транспортера (см 2.2)