
2533
.pdf
по формуле (3
II |
dm1 |
Ft |
dm1 |
|
|
II |
|
||||
O2 |
П |
Fa2 |
M2 |
||
|
|||||
|
|
|
|||
M2 |
Fr2 |
|
|
|
|
|
|
П |
Fa2 |
||
|
dm2 |
|
|||
|
|
|
|||
III O |
O3 |
δ1 |
|
Fr2 |
|
|
|
|
|
M3 |
|
|
|
|
|
III |
Рис. 3.5
М2 = 36,8 Н·м = 36,8·103 Н·мм.
2a a
Ft =2·36,8·103 / 128,6 = 572 Н.
Рис. 3.6
Радиальная сила определится по формуле (3.38)
Fr2 = 572 · tg 20 0 · sin 18,43 0 = 65,8 Н.
dm2
Суммарную радиальную силу давления шестерни на вал ΙΙΙ вычислим по формуле (3.40)
F2 5722 65,82 576 Н.
Осевая сила определится по формуле (3.39)
Fa2 572 tg20 cos18,43 197,5 Н.
4. ЭСКИЗНЫЙ ПРОЕКТ РЕДУКТОРА
4.1. Основные сведения
Кинематический и силовой расчеты проводятся на базе теории механизмов и машин и служат основой для дальнейших расчетов на прочность, жесткость и долговечность. В результате этих расчетов (см. предыдущие 2 и 3 разделы) были определены:
1.Тип, мощность и частота вращения электродвигателя.
2.Передаточные отношения всех передач.
3.Скорости и частоты вращения всех валов.
4.Уточнена скорость рабочего органа.
5.Крутящие моменты на всех валах.
6.Проверена допускаемая нагрузка на рабочий орган.
7.Силы в зубчатом зацеплении редуктора.
8.Модуль зубчатой передачи редуктора.
9.Размеры зубчатых колес, межосевое расстояние и другие элементы
зубчатого зацепления.
Настоящая глава посвящается эскизному конструированию редуктора. Построение компоновочного чертежа основывается на знании технического черчения, курса механики и конкретных расчетов.
Ставится задача выполнить на миллиметровке формата А3 или А2 в масштабе 1:1 компоновочный чертеж одноступенчатого редуктора, т. е. эскизный проект, в три этапа:
1.Компоновочный чертеж зубчатых колес, валов и подшипников (вид в плане).
2.Построение корпуса редуктора и крышек для завершения предыдущего чертежа (вид в плане). Другими словами, «одевание» валов, колес и подшипников в корпус.
3.Построение главной проекции редуктора.
4.2. Устройство редуктора
Редуктор – это механизм, состоящий из зубчатых колес, валов и подшипников, помещенных в закрытый корпус, снабженный смазочным устройством и предназначенный для понижения частоты вращения и повышения крутящего момента ведомого вала по отношению к ведущему валу.
Редуктор – законченный механизм. Он изготавливается как самостоятельный отдельный узел. Зачастую ведущий вал соединяется через муфту с двигателем, а выходной (ведомый) вал через муфту или гибкую передачу – с остальной машиной.
Область применения редуктора широка: подъемные машины, дорожные машины, машины нефтедобывающей отрасли, транспортеры и конвейеры, машины для пищевой промышленности, средства механизации трудоемких работ и т.д.
По типу зубчатых передач редукторы различают: цилиндрические, конические, червячные, волновые и планетарные.
По количеству передач редукторы делятся на одноступенчатые, двухступенчатые и трехступенчатые.
Одноступенчатый редуктор (рис. 4.1) состоит из следующих основных частей: ведущего вала 1, ведомого вала 2, шестерни 3, зубчатого колеса 4, шариковых подшипников 5 и 6, составного корпуса, состоящего из собственно корпуса 7 и крышки корпуса 8. Плоскость разъема корпуса
совпадает с осями валов 1 и 2. Корпус и крышка имеют фланцы 9 и 10, с помощью которых они стягиваются болтами 11 и 12. В составном корпусе имеются отверстия 13 и 14, в которых устанавливаются валы 1 и 2 с напрессованными на них подшипниками 5 и 6. Снаружи отверстия закрываются крышками 15, 16, 17 и 18, а крышки привинчиваются к корпусу болтами 19 и 20. Между валом 1 и крышкой 15, валом 2 и крышкой 17 имеются уплотнения 21 и 22.
Корпус 7 привинчивается к станине или фундаменту болтами с помощью отверстий 23, которых, как правило, 4. Они сверлятся в нижнем фланце 24 корпуса 7. В верхней части крышки корпуса 8 имеется смотровой люк 25, привинченный болтами 26. В люке установлена отдушина 27. Она предназначена для выхода воздуха, который расширяется от выделения тепла в зубчатых зацеплениях и подшипниках и создает внутри корпуса давление. Если у воздуха нет легкого выхода, то он пробивается через стыки и уплотнения, а это способствует вытеканию смазки.
Крышка корпуса 8 снабжена проушинами 28 для подъема и транспортировки редуктора. В корпус заливается машинное масло 29. Его уровень должен быть такой, чтобы глубина погружения зубчатого колеса 4 составляла (0,5…5)m соответственно нижнему и верхнему уровням смазки, но не менее 10 мм. При окружных скоростях υ < 1 м/с допустимо и более глубокое погружение. Зубья конического колеса должны быть погружены по всей длине. Масло заливают через смотровой люк 25. Загрязненное масло, т. е. отработанное масло, сливается через резьбовое отверстие 30, закрываемое пробкой 31. Чтобы загрязненное масло сливалось полностью, дно корпуса 32 имеет уклон от правой стенки корпуса к левой, т. е. к сливному отверстию.
Контроль уровня масла в редукторе производится с помощью прозрачного маслоуказателя 33.
4.3. Компоновочный чертеж цилиндрических зубчатых колес, валов и подшипников
При эскизном конструировании определяют расположение деталей передач, ориентировочные диаметры ступеней валов, выбирают типы подшипников и схемы их установки, составляют эскизную компоновку деталей передач.
Диаметры различных участков валов одноступенчатого цилиндрического или конического редуктора определяют по формулам
(см. рис. 4.3 и 4.15).
Диаметры входной шейки быстроходного и выходной шейки тихоходного валов

12
8
11
10
9
7
31
dВi 3 |
Mi |
. |
(4.1) |
|
|||
|
0,2[ k ] |
|
28 |
26 |
25 |
27 |
12
23 33
30 |
2932 |
18 |
6 |
20 |
24 |
14 |
21 |
1 |
15 |
4
3
24 |
23 |
17 |
22 |
2 |
19 |
5 |
16 |
13 |
Рис 4.1
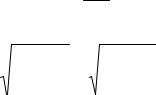
Диаметры валов рассчитывают на кручение по заниженным допускаемым напряжениям [ k ], исходя из формулы
d3
Mi Wр k i k .
16
Отсюда
di |
3 |
16 Mi |
|
Mi |
|
. |
|
k |
0,2 k |
||||||
|
|
|
|
Допускаемые напряжения для сталей 40, 45 рекомендуется выбирать:
–для быстроходных валов k = 50 Н/мм2 ,
–для тихоходных валов k = 63 Н/мм2.
Вформуле (4.1) диаметр dВi – в мм, а крутящий момент Mi – в Н·мм.
Следовательно, моменты, полученные в результате силового расчета в Н·м,
нужно умножать на 103 , чтобы получить размерность Н·мм. Диаметры шеек валов под уплотнения определяют по формуле
dУ dВ 2tЗ , |
(4.2) |
где dУ – диаметр шейки вала под уплотнение, мм; tЗ – высота заплечика между шейками dВ и dУ , мм, значения которого приведены в табл. 4.7. В этой таблице символом d обозначен диаметр шейки вала меньшей ступени, например, в формуле (4.2) – это dВ , а в формуле (4.6) – это dП и т.д. Диаметры шеек валов под подшипники больше шеек под уплотнение:
dП dУ 0 4.
При сборке на входной или выходной шейке вала установлены шпонки. Чтобы при сборке можно было насадить подшипники, не вынимая шпонку, нужно чтобы полуразность диаметров была больше выступающей части:
0,5 dП dВ tЗ 0,5h
шпонки, т.е. ее половины высоты 0,5h .
Входной конец быстроходного вала, если он является первым, соединяется муфтой с валом электродвигателя. В этом случае рекомендуется принимать
dВ1 0,8 1 dЭ ,
где dЭ – диаметр вала электродвигателя.
Цилиндрическая зубчатая передача расположена между III и IV валами (см. рис. 2.2) и состоит из шестерни z3 и колеса z4 .
4.3.1. Пример расчета и компоновки
Исходные данные: числа зубьев шестерни и колеса z3=18, z4 = 56; модуль прямозубой передачи m2= 4 мм; момент крутящий на III - м валу
M3 107Н·м 107 103 Н·мм; момент крутящий на IV - м валу M4 325
Н·м 325 103 Н·мм.
Нужно провести расчет и скомпоновать чертеж. Разберем этот вопрос на конкретном примере.
1.Определяем и выписываем размеры зубчатых колес (см. § 3.5):
диаметр начальной окружности шестерни
d3 73,17 мм,
диаметр окружности вершин шестерни
dа3 80,88 мм,
диаметр окружности впадин шестерни
d f 3 m2 z3 2,5 2x1 4 18 2,5 2 0,134 63мм,
диаметр начальной окружности колеса
d4 226,83мм,
диаметр окружности вершин колеса
dа4 234,93мм,
диаметр окружности впадин колеса
d f 4 m2 z4 2,5 2x2 4 56 2,5 2 0,39 217мм,
ширина зубчатых колес
b4 40 мм,
межосевое расстояние
a34 150 мм.
2. Определяем размер c от торца зубчатого колеса до середины подшипника (см. рис. 4.2) по эмпирической формуле
c 10m2 10 4 40 мм.
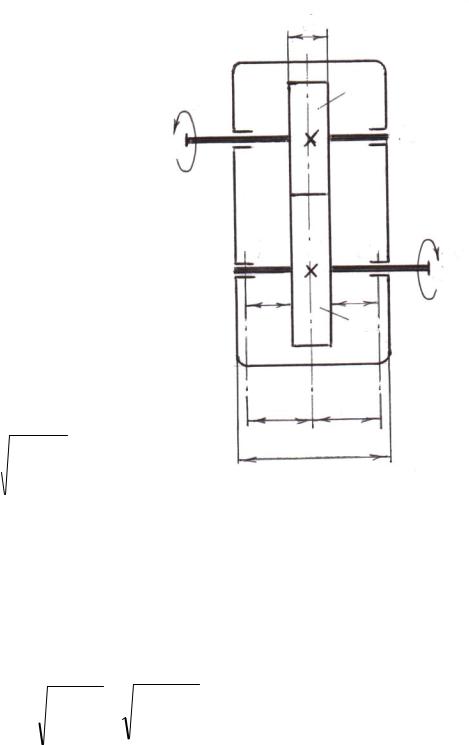
3.Определяем размер a0 (см. рис. 4.2) от середины колеса до
середины подшипника
a0 c b2 40 40
2 60мм.
4.Теперь на миллиметровке
вмасштабе 1:1 тонкими линиями вычерчиваем контуры зубчатых колес без ступиц (см. рис. 4.3) и проводим оси валов. При этом должно выдерживаться межцентровое расстояние a34.
Далее проводим перпендикулярно к осям валов оси симметрии, т.е. линии середин подшипников на расстоянии c от торцов зубчатых колес по обе стороны.
После этого переходим к построению ступенчатых валов.
5. Наименьшими диаметрами валов 3 и 4 являются (см. рис. 4.3) диаметры входной шейки dВ3 вала
3 и выходной шейки |
dВ4 |
вала 4. |
Они рассчитываются |
по |
формуле |
(4.1) |
|
|
d |
3 |
Mi |
|
, |
|
|
|||
|
Вi |
0,2[ k |
] |
|
|
|
|||
где dВi – |
диаметр |
входной и |
выходной шеек на i-м валу, мм; Mi – крутящий момент на i-м
b
М |
z1 |
3 |
III
A |
C |
М4 |
|
B |
|||
IV |
|
K |
|
c |
c |
||
|
|||
|
|
z2 |
а0 а0
B
Рис. 4.2
валу, Н·мм; k 50 63Н/мм2 –
допускаемое касательное напряжение.
Для третьего вала после подстановки числовых значений получим, если k = 50 Н/мм2
|
M |
|
107 10 |
3 |
|
|
||
d 3 |
3 |
|
3 |
|
29,8 |
мм 30 мм. |
||
0,2[ ] |
0,2 50 |
|||||||
В3 |
|
|
|
|||||
|
k |
|
|
|
|
|
Для четвертого вала, подставляя числовые значения, получим, если
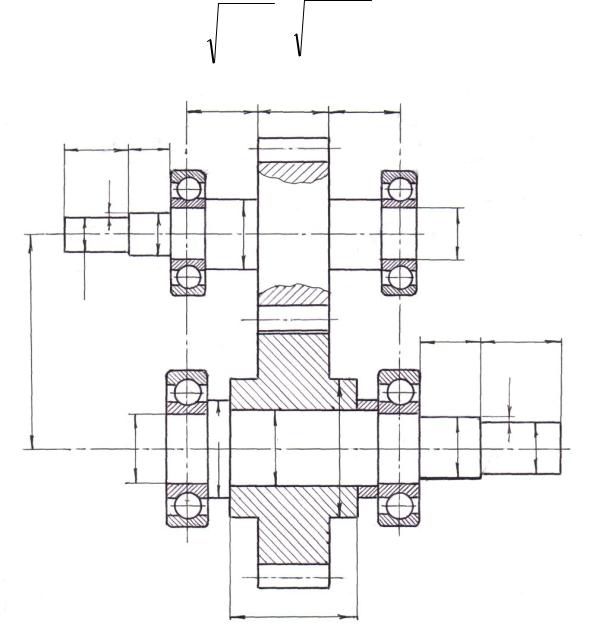
k 63 Н/мм2 .
|
|
|
M |
|
325 10 |
3 |
|
|
d |
3 |
|
4 |
3 |
|
40 мм. |
|
|
0,2[ ] |
0,2 63 |
|
||||||
В4 |
|
|
|
|
||||
|
|
|
k |
|
|
|
|
|
|
c |
|
b |
с |
|
|
||
lВ3 lУ3 |
|
|
|
|
|
|
|
|
З |
|
|
|
|
|
|
|
|
t |
|
|
|
|
|
|
|
|
У3 |
|
|
Б3 |
|
|
|
П3 |
|
|
|
d |
|
|
|
III |
||
d |
|
|
|
|
|
|
d |
|
|
|
|
|
|
|
|
||
В3 |
|
|
|
|
|
|
|
|
d |
|
|
|
|
|
|
|
|
|
|
|
|
|
|
|
lУ4 |
lВ4 |
34 |
|
|
|
|
|
|
|
|
а |
|
|
|
|
|
|
|
|
|
|
|
|
|
|
|
|
З |
|
|
|
|
|
|
|
|
t |
П4 |
Б4 |
Ш4 |
|
C |
|
У4 |
В4 |
|
d |
d |
d |
|
d |
|
d |
d |
lC
IV
6. Следующей ступенькой являются шейки валов под уплотнение диаметрами dУ3и dУ4 , расчет которых будет приведен ниже.
За ними следуют шейки валов под подшипники диаметрами dП3 и dП4, которые можно определить с помощью эмпирической формулы
dПi dУi 0 4 dВi 2t3 0.....4 |
(4.3) |
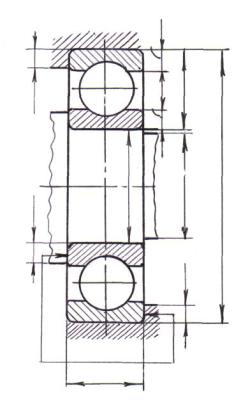
где tЗ – высота заплечика, табл. 4.7.
На эти шейки одеваются подшипники своим отверстием диаметра dП (рис. 4.4).
Внутренние диаметры подшипников качения, начиная с d 20 мм, оканчиваются на 0 и на 5, так построен стандартный ряд: 20 – 25 – 30 – 35 – 40 – 45 – 50 - … - 100 мм.
Внутренний диаметр является главным размером подшипников, поэтому последние подбираются по диаметру отверстия dП . Индекс П в таблицах справочников отсутствует. Диаметр отверстия подшипника обозначается d . В расчетах, приводимых в пособии, будет обозначаться диаметр шейки под подшипник и отверстие подшипника – dП .
|
0,3H |
|
|
h |
0,3H |
H |
|
П |
|
|
|
d |
|
У |
D |
|
|
d |
|
h |
|
|
|
|
|
h |
|
Полученный по формуле (4.3) |
T |
|
результат нужно |
округлить до |
B |
стандартного ряда. |
|
|
Определяем |
внутренний |
Рис. 4.4 |
|
|
диаметр подшипника на III - м валу
dП3 dВ3 2tЗ 0 4 30 2 4,5 2 40
мм.
Внутренний диаметр подшипника на IV-м валу
dП4 dВ4 2tЗ 0 4 40 2 5 2 50мм.
7. По табл. 4.1 или таблицам, приведенным в пособиях |5| или |6|, выбираем шариковые радиальные однорядные подшипники легкой серии №208 с d = 40 мм для вала III и №210 c d = 50 мм для вала IV.
Теперь делаем проверку пригодности выбранных подшипников для наших условий.
Проверку сделаем по динамической грузоподъемности C, применяя эмпирическую формулу (7.2) и пересчитывая числовой коэффициент, получим
C 0,04R kБ kТ kk nh 0,33, |
(4.4) |
где R F2 – радиальная нагрузка на подшипник, т.е. реакция опоры A или B; F – сила в зубчатом зацеплении; kБ = 1,2 – коэффициент нагрузки на подшипник при спокойном характере с легкими толчками; kТ = 1 – коэффициент, учитывающий температуру подшипника (t°≤100° C); kk = 1 – коэффициент, соответствующий вращению внутреннего кольца подшипника; h – срок службы, обычно принимают h = 10 000 ч., что соответствует двухгодичному сроку службы при двухсменной работе; n – частота вращения подшипника. С учетом сказанного выше формулу (4.4) можно переписать в виде (числовое значение h и коэффициентов обращается в единицу)
C R n0,33 . |
(4.5) |
Для третьего вала n3 = 239,2 об/мин; F3= 3,16 кН; |
R3 F3 / 2= 1,58 |
кН, динамическая грузоподъемность |
|
C3 R3 n30,33 1,58 239,20,33 9,63 кН.
Сравниваем расчетные данные с данными табл. 4.1.
Cрасч 9,63 кН < Cтабл |
32 кН. |
|
|
Следовательно, расчет удовлетворительный. |
|
|
|
Для четвертого вала n4 76,9об/мин; |
F4 3,16 кН; |
R4 F4 / 2= |
|
=1,58 кН, динамическая грузоподъемность |
|
|
|
C4 R4 n40,33 1,58 76,90,33 6,6кН.
Сравниваем расчетные данные с табличными:
Cрасч 6,6 кН < Cтабл 35,1 кН.
Следовательно, расчет удовлетворительный.
Теперь выбираем из табл. 4.1 размеры подшипников:
подшипник № 208; d = 40 мм; D = 80 мм; B = 18 мм; h = 4…5 мм; nmax= 10 000 об/мин;
подшипник № 210; d = 50 мм; D = 90 мм; B = 20 мм; h = 5…6 мм; nmax= 8 000 об/мин.
8.После расчетов на компоновочном чертеже (см. рис. 4.3) проводим
осевыми линиями, параллельными торцам зубчатых колес, на расстоянии c от них по обе стороны колес оси симметрии подшипников. Вычерчиваем подшипники по размерам, взятым из табл. 4.1, согласно рис. 4.4. Диаметр шарика определяется по формуле