
2533
.pdfn |
i |
n |
|
d1 |
n , |
(2.12) |
|
d2 |
|||||||
1 |
12 |
1 |
|
2 |
|
где n1 – частота вращения первого вала; i12 – передаточное число между Ι-м и ΙΙ-м валами; d1 и d2 – диаметры шкивов; n1 – частота вращения первого вала.
Определим частоту вращения третьего вала
n |
|
i |
|
n |
|
|
z1 |
n i |
i |
|
n |
|
d1 |
|
z1 |
n |
|
, |
(2.13) |
|
|
|
z2 |
|
d2 |
z2 |
|
||||||||||||
|
2 |
|
23 |
|
2 |
|
1 12 |
|
23 |
1 |
|
|
|
3 |
|
|
где i23 – передаточное число между ΙΙ-м и ΙΙΙ-м валами. Определим частоту вращения четвертого вала
n i |
n |
|
z3 |
n i |
i |
|
i |
n |
|
d1 |
|
z1 |
|
z3 |
n |
|
. |
(2.14) |
z4 |
|
d2 |
z2 |
z4 |
|
|||||||||||||
3 34 |
3 |
|
1 12 |
|
23 |
34 |
1 |
|
|
|
|
4 |
|
|
Четвертый вал, на котором установлен барабан 3 (см. рис. 2.2), называется тяговым валом, т.к. он непосредственно перемещает (тянет) ленту 4 транспортера. Скорость ленты равна окружной скорости барабана. За 1 оборот барабана лента переместится на длину окружности барабана, т.е. π·dБ , а за n оборотов – π·dБ ·n, следовательно:
π·dБ ·n4 = υ, |
(2.15) |
где n4 – частота вращения тягового вала (четвертого в нашем случае); υ – скорость ленты, м/мин; dБ – диаметр барабана, м.
Произведение π·dБ = tТВ называется шагом тягового вала. В ленточном транспортере шаг тягового вала равен длине окружности барабана.
Рассмотрим, как определяется шаг тягового вала tТВ в других машинах. На рис. 2.3, а изображен механизм подъемного крана или электротали. На тяговый вал 1 посажен барабан 2, на который намотан канат 3. Канат закреплен своим концом в стойке 4, а в петле каната подвешен подвижный блок 5. С блоком 5 шарнирно соединен крюк 6, за который подвешиваются поднимаемые грузы. Крюк является рабочим органом крана. Его скорость υ – заданная величина. Уравнение кинематического баланса для участка кинематической цепи от вала 1 до каната 3 имеет вид
π · dБ ·nТВ = υТ , |
(2.16) |
где nТВ – частота вращения тягового вала, об/мин; dБ –диаметр барабана, м; υТ – скорость ветви каната (троса), которая наматывается на барабан, м/мин.
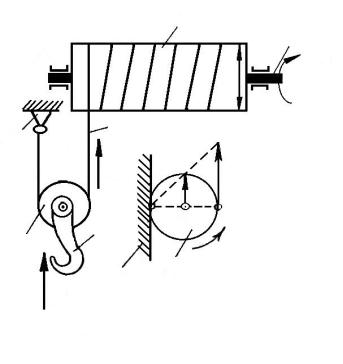
Сравним подвижный блок 5 с колесом 8, которое катится по стене 7. Действительно, ветвь каната, связанная со стойкой 4, представляет собой натянутую струну, по которой катится блок 5. Аналогия очевидна. Точка А колеса 8 и блока 5 касается неподвижной стены либо неподвижного каната и принадлежит одновременно колесу 8 и стене 7, блоку 5 и неподвижной ветви каната. Точка А является мгновенным центром вращения. Скорости точек О и В относительно неподвижной стены, а следовательно, и точки А
равны следующим величинам. |
|
|
υ = ω · r ; |
υТ = 2 r · ω. |
(2.17) |
Если взять их отношение, то получим |
|
|
υ / υТ = 1 / 2. |
(2.18) |
|
а) |
2 |
|
|
|
|
|
dБ |
4 |
3 |
б) |
|
||
|
vт |
vт |
|
|
υ |
|
А |
О В |
5 |
6 |
ω |
|
7 |
8 |
|
|
υ |
|
|
Рис. 2.3 |
Откуда
nтв
υТ = 2υ. |
(2.19) |
Подставляя (2.19) в (2.16),
получим
π · dБ ·nТВ · 1/2= υ. (2.20)
Это УКБ для изображенного участка кинематической цепи (рис. 2.3, а). Шаг тягового вала
tТВ= π · dБ · 1/2. (2.21)
На рис. 2.4 изображен шнековый (винтовой) транспортер. На тяговый вал 1 посажен цилиндр 2, на который приварена винтовая лента 3. Детали 1, 2 и 3 в совокупности называются шнеком, который вращается в подшипниках 7. Заодно с подшипниками изготовлен цилиндрический корпус 4, в котором размещен шнек. В корпусе имеются горловины: входная – 5, куда подается транспортируемая масса, и выходная – 6, откуда транспортируемая масса выходит наружу.
Шнековый, или винтовой транспортер, – это транспортная машина,
предназначенная для перемещения сыпучих, кусковых и полужидких вязких тел. Он может работать в горизонтальном, вертикальном или наклонном положении. Транспортирует уголь, металлическую стружку,
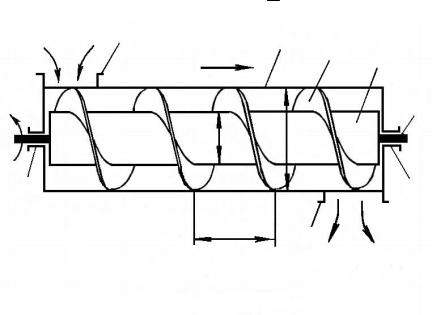
отходы линейного производства, мясо, сырую резину, горячую пластмассу, тесто и т.д.
При горизонтальном положении вязкие тела заполняют весь объем шнека (кольцо), а сыпучие – полкольца.
Производительность транспортера – это объем перемещаемого тела за 1 минуту.
Для вязких тел производительность определяется по формуле
Q S D2 d 2 ,
4
5 |
4 |
2 |
υ |
3 |
nтв
1
|
d |
D |
|
7 |
|
7 |
|
|
t |
6 |
|
|
|
|
|
|
Рис. 2.4 |
|
|
|
|
|
|
|
|
(2.22) |
где |
Q |
– |
производительност ь, м3/мин; D – наружный диаметр шнека, м; d – внутренний диаметр шнека, м; υ – скорость транспортирования
, м/мин;
S = (D2 – d2) π / 4 –
площадь кольца, м2.
Скорость транспортирования определяется по формуле
nТВ · t = υ. |
(2.23) |
Это уравнение кинематического баланса для шнекового транспортера, где nТВ – частота вращения тягового вала (шнека), об/мин; t – шаг винта (шнека), м.
Шаг тягового вала у шнекового транспортера равен шагу винта
|
|
tТВ = t. |
(2.24) |
||
Для сыпучих тел производительность будет вдвое меньше и |
|||||
определяется по формуле |
|
|
|
|
|
Q |
1 |
S |
|
D2 d2 . |
(2.25) |
|
|
||||
2 |
8 |
|
|
Пример. Дано: шаг винта t = 250 мм, диаметры шнека D = 300 мм, d = 150 мм, тело – уголь (полукольцо), nТВ = 120 об/мин.
Cкорость транспортирования
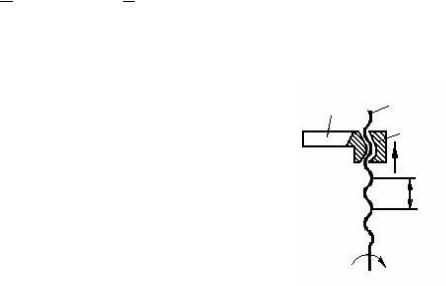
υ = nТВ · t = 120 · 0,25 = 30 м/мин.
Производительность транспортера
Q D2 d2 0,32 0,152 30 0,8 м3/мин. 8 8
На рис. 2.5 изображен винтовой подъемник. Тяговый вал выполнен заодно с винтом. Тяговый вал может только вращаться, а в осевом
направлении двигаться не может. Гайка 2 выполнена заодно с платформой 3, которая двигается в вертикальных направляющих, а вращаться не может. Когда винт вращается, гайка ввинчивается (опускается вниз) или вывинчивается (поднимается вверх). Вместе с гайкой двигается вертикальная платформа.
Если винт вращается с частотой nТВ, |
то |
|
платформа движется со скоростью υ |
в |
|
соответствии с формулой |
|
|
nТВ · t = υ, |
(2.26) |
1
3
2
υ
t
nтв
Рис. 2.5
где nТВ – частота вращения тягового вала, об/мин; t |
– шаг винта, м; |
υ – скорость подъема или опускания платформы, м/мин. |
|
Шаг тягового вала у винтового подъемника равен шагу винта |
|
tТВ = t. |
(2.27) |
Теперь вернемся к кинематическому расчету ленточного транспортера
(см. рис. 2.2).
Подставляя в уравнение (2.15) равенство (2.14), получим
n |
|
d1 |
|
z1 |
|
z |
3 |
d |
Б |
. |
(2.28) |
d2 |
z2 |
z |
|
||||||||
1 |
|
|
|
4 |
|
|
|
Это уравнение кинематического баланса ленточного транспортера. В
этом уравнении известными величинами являются: n1= nЭ, d1 / d2 = 1 / u12, dБ и υ. Требуется определить z1 / z2 и z3 / z4.
Зададимся передаточным отношением u12 = z2 / z1 = 3, тогда в уравнении (2.28) останется одно неизвестное – передаточное число i34 = z3 / z4, передаточное число i23 = 1/ u23 = z1 / z 2= 1/3.
Решая уравнение (2.28) относительно z3 / z4, получим, учитывая, что
u12 = d2 / d1 и u23 = z2 / z1

z3 |
|
u12 |
u23 |
|
60 2 3 |
|
360 |
|
18 |
, |
z4 |
dБ |
n1 |
0,25 1435 |
|
|
|||||
|
|
1127 |
56 |
|
где z3= 18, z4 = 56, u34 = 56 /18 = 3,1, i34 =18 /56 = 0,32. Теперь подбираем числа зубьев конической передачи z1 / z2 = 1 /3 =20 / 60, где z1 =20, z2 = 60. Минимальное число зубьев шестерни zmin =17. Так как z1 =20 ≥ zmin и z3 =18 ≥ zmin , то расчет удовлетворительный.
Уточняем скорость ленты транспортера, используя УКБ (2.28):
1435 1 1 18 0,25 60,38 м/мин. 2 3 56
Погрешность скорости составляет
60,38 60 100 0,63%. 60
Результат показывает, что числа зубьев передачи подобраны удовлетворительно.
Определим скорости и частоты вращения валов:
n1 = nЭ = 1435 об/мин; ω1 = π · n1 / 30 = π · 1435 / 30 = 150,3 с- 1; n2 = n1· i12 = 1435 ·1/2 = 717,5 об/мин;
ω2 = π · n2 / 30 = π · 717,5 / 30 = 75,15 с- 1;
n3 = n1· i12· i32 = 1435 ·1/2 · 3 = 239,2 об/мин; ω3 = π · n3 / 30 = π · 239,2 / 30 = 25 с- 1;
n4 = n1· i12· i32· i34 = 1435 ·1/2 · 3 · 56 = 76,9 об/мин; ω4 = π · n4 / 30 = π · 76,9 / 30 = 8 с- 1.
Передаточные отношения выбирают в пределах зубчатой передачи цилиндрической 1…4, конической 1…3, ременной 1..7, цепной 1…4.
3.СИЛОВОЙ РАСЧЕТ МЕХАНИЗМА
Врезультате этого расчета нужно получить крутящие моменты на валах, силы в зубчатом зацеплении конической и цилиндрической передач, которые являются внешними силами для расчета валов на прочность при поперечном изгибе и реакции опор валов, которые определяют выбор подшипников качения.
Для определения сил в зубчатом зацеплении необходимо знать модуль
иразмеры зубчатых колес, поэтому в эту главу включен расчет модуля и геометрических размеров зубчатых колес.
Расчет выполним на примере схемы, изображенной на рис. 2.2.
3.1. Расчет крутящих моментов на валах
Крутящий момент на первом валу, который непосредственно соединен с электродвигателем, определяется по формуле (2.4)
M1 = N1 / ω1 = NЭ / ω1 = 3000 / 150,3 =20 Н·м.
Крутящий момент на втором валу определяется по формуле (2.8)
M2 = M1 · u12 · η12 = 20 · 2 · 0,92 = 36,8 Н·м,
где η12 = 0,92 – КПД ременной передачи.
Крутящий момент на третьем валу определяется тоже по формуле (2.8), но все индексы увеличиваются на единицу.
M3 = M2 · u23 · η23 , |
(3.1) |
где η23 = 0,97 – КПД зубчатой конической передачи.
Если в формулу (3.1) подставить формулу (2.8), то получим
M3 = M2 · u12 · u23 · η12 · η23 . |
(3.2) |
Это второй вариант формулы (3.1).
Делая подстановку числовых значений в формулу (3.1), получим
M3 = 36,8 · 3 · 0,97 = 107 Н·м.
По аналогии крутящий момент на четвертом валу определяется по формуле
M4 = M3 · u34 · η34 = M2 · u12 · u23 · u34 · η12 · η23 · η34 , |
(3.3) |
где η34 = 0,98 – КПД зубчатой цилиндрической передачи. После подстановки числовых значений получим
M4 = 107 · 3,1 · 0,98 = 325 Н·м.
Делаем проверку допускаемой нагрузки на рабочий орган.
Нагрузкой на рабочий орган является тяговая сила ленты транспортера, определяемая по формуле, которая получается из условия равенства работ за 1 оборот тягового вала (см. рис. 2.2):
А = M4· 2π · ŋТР = Ft · π · dБ , |
(3.4) |
где А – работа за 1 оборот тягового вала IV; ŋТР – КПД транспортера, учитывающий потери между лентой и барабаном; Ft – окружная по отношению к барабану или тяговая по отношению к ленте сила; dБ – диаметр барабана; M4 – момент, вращающий тяговый вал с барабаном.
КПД ленточного транспортера ŋТР = 0,86.
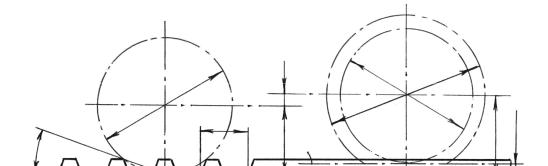
Решая формулу (3.4) относительно Ft, получим
Ft = 2 M4· ŋТР / dБ , |
(3.5) |
Подставляя значение M4 из формулы (3.3), получим
Ft = 2 M1 · u12 · u23 · u34 · η12 · η23 · η34· ŋТР / dБ . |
(3.6) |
Это второй вариант формулы (3.5).
Делая подстановку числовых значений в формулу, получим
Ft = 2 · 325 · 0,86 / 0,25 = 2236 Н ≈ 2,24 кН.
В задании Ft = 2 кН. Тяговая сила превышает заданную нагрузку на
0,24 кН. Погрешность силы составляет |
|
|
F |
2,24 2 |
100 12%. |
2 |
Это объясняется тем, что NЭ > N, т.е. мощность двигателя больше необходимой затрачиваемой мощности.
Результат показывает, что транспортер успешно справится с заданной нагрузкой.
3.2. Краткие сведения о геометрии зубчатого зацепления
Основы геометрии зубчатого зацепления изложены в учебном пособии [1]. При нарезании цилиндрических зубчатых колес используют метод обкатки нарезаемого колеса (шестерни) по производящей рейке.
На рис. 3.1 изображено зубчатое колесо, которое находится в зацеплении с архимедовым винтом, называемым цилиндрическим червяком. За 1 оборот винта колесо поворачивается на 1 шаг (на 1 зуб). Это закон зацепления. Если сделать сечение плоскостью, перпендикулярной оси вращения колеса и проходящей через ось винта, то получим трапецеидальный профиль резьбы червяка, который подобен профилю зубчатой рейки. Если на червяке сделать 6 …10 продольных канавок на глубину, превышающую высоту профиля винта h, то получим червячную фрезу. У червячной фрезы вдоль каждой канавки получается инструментальная рейка. Зубья инструментальных реек фрезы при вращении вынимают из впадин зубьев колеса послойно металл. Вращение фрезы согласуется с вращением колеса по закону зацепления.
a)
d0 |
xm |
|
|
O1 |
|
|
t |
|
0 |
|
r |
α0
б)
q1
d0 d
O2
r xm
q1
q
Рис. 3.1
Линия qq рейки, на которой толщина зуба равна ширине впадины,
называется средней линией, или модульной прямой. Прямая qq является образующей делительного цилиндра червяка.
При вращении червяка его витки «бегут» вдоль оси винта со скоростью υ = n1 · t / 60, где n1 – частота вращения червяка (червячной фрезы). Эта
скорость |
является одновременно окружной скоростью колеса |
υ = π d2 |
n2 /60. Поскольку в станке червячная фреза и обрабатываемое |
колесо связаны кинематически через зубчатые передачи, закон зацепления выполняется принудительно. Поэтому при повороте червячной фрезы на 1 оборот воображаемая зубчатая рейка перемещается вдоль оси фрезы (винта) на 1 шаг, а зубчатое колесо принудительно поворачивается тоже на 1 шаг за это же время. Таким образом, колесо обкатывается по профилю винта (инструментальной рейке), а зубья колеса получаются с эвольвентным профилем.
При проектировании зубчатых передач требуется межосевое расстояние a выбирать из ряда чисел Ra40, который соответствует ГОСТ 6636 – 69 (Прил. 4). Расчетное межосевое расстояние, как правило, не совпадает со стандартным. Для получения стандартного значения межосевого расстояния применяют коррекцию зубьев. Различают высотную и угловую коррекции. Высотная коррекция имеет специальное назначение, поэтому ее
опустим. Угловая |
коррекция |
используется для прямозубых |
цилиндрических и |
червячных |
передач. В косозубых цилиндрических |
передачах стандартное межосевое расстояние получают за счет угла наклона зуба β. Угловая коррекция прямозубых колес получается путем смещения инструментальной рейки. Если при нарезании колеса рейку, т.е. фрезу, расположить так, что модульная прямая qq будет касаться делительной окружности диаметра d0 колеса, то это колесо будет нарезано
без смещения (рис. 3.1, а). У такого колеса так же, как и у рейки, толщина зуба по делительной окружности равна ширине впадины (s0 = t / 2). Если отодвинуть нарезаемое колесо от рейки на величину xm, то получим колесо с положительным смещением (рис. 3.1, б). При этом толщина зуба колеса и ширина впадины по делительной окружности получаются неодинаковыми (s ≥ t / 2): толщина зуба рейки s1 = (t /2) – 2· хm·tg α, а сумма толщин зубьев по делительной окружности колеса d0 равна s1 + s = t. Толщина зуба рейки равна ширине впадины колеса, а толщина зуба колеса
|
|
t / 2 2 xm tg . |
||
s m |
|
2 x tg |
||
2 |
||||
|
|
|
Величина сдвига хт называется абсолютным сдвигом. Абсолютный сдвиг считается положительным, если колесо и рейка или два колеса (рис. 3.2, б) отодвигаются друг от друга, и отрицательным сдвигом, если происходит их сближение.
Если окружность диаметром d0 катится без скольжения (см. рис. 3.1, б) не по средней линии qq, а по параллельной ей делительной прямой q/q/, то в этом случае налицо коррекция колеса, а расстояние между линиями qq и q/q/ есть смещение исходного контура или сдвиг. Если обозначить расстояние от средней линии рейки до центра колеса буквой r, то (см. рис. 3.1)
r – r0 = хт. |
(3.7) |
Отношение величины абсолютного смещения исходного контура хт к
модулю m называется коэффициентом коррекции, или коэффициентом смещения, и обозначается буквой х.
С увеличением коэффициента х увеличивается толщина зуба у основания ножки, прочность зуба на изгиб увеличивается. При этом увеличиваются диаметры окружностей вершин da и впадин df. Профиль зуба переходит на участки эвольвенты, более удаленные от основной окружности, где радиус кривизны эвольвенты и, следовательно, профиля зуба увеличивается, что повышает поверхностную прочность зубьев.
На рис. 3.2 изображены две передачи: а) некорригированная, б) корригированная с тем же числом зубьев z1 и z2 и тем же модулем т.
Межосевое расстояние а у корригированных колес больше, чем делительное межосевое расстояние а0 у некорригированных, а также углы зацепления α >α0. Суммарный коэффициент смещения хС = х1+ х2 > 0.
Поскольку при коррекции изменяется угол зацепления α, она называется угловой коррекцией.
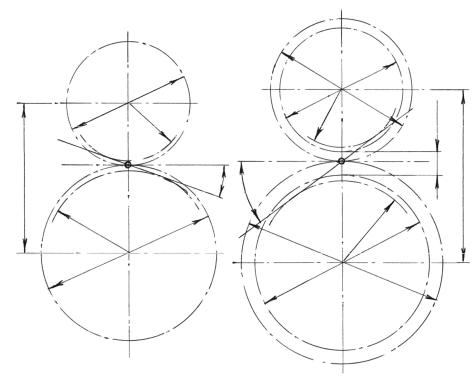
ao
а) |
|
б) |
|
|
d01 |
d1 |
d01 |
|
|
|
|
|
rосн1 |
rосн1 |
|
|
αo |
α |
rосн2 |
rосн2 |
do2 |
|
|
d2 |
do2 |
||
|
|
|
cm
а
Рис. 3.2
Отношение разности межосевых расстояний (а – а0) к модулю т называется коэффициентом отклонения межосевого расстояния и обозначается буквой с.
с |
а а0 |
|
а 0,5тzС |
, |
(3.8) |
|
|
тт
где zС = z1+ z2 – суммарное число зубьев передачи.
Если обозначить коэффициент коррекции шестерни х1, а колеса – х2, то суммарный коэффициент хС = х1+ х2,.
При угловой коррекции суммарное смещение хС > 0, кроме того, шестерня и колесо имеют положительное смещение х1 >0 и х2 >0. В этом случае на делительных окружностях d01 и d02 толщина зубьев колеса и шестерни больше t /2. По этой причине делительные окружности не могут соприкасаться, для чего зубчатые колеса необходимо раздвинуть. Качение колес без скольжения будет осуществляться по окружностям с диаметрами d1 и d2 (см. рис. 3.2), которые называются начальными. Если у некорригированных колес делительные и начальные окружности совпадают, то у корригированных колес они не совпадают, причем начальные окружности больше, чем делительные. Основные окружности и делительные у колес остаются прежними. Так как колеса отодвинуты друг от друга, общая касательная к основным окружностям радиусами rосн.1 и rосн.2проходит круче и угол α становится больше.