
2533
.pdf36 211 |
46 211 |
55 |
100 |
21 |
2,5 |
58,4 |
34,2 |
50,3 |
31,5 |
36 212 |
46 212 |
60 |
110 |
22 |
2,5 |
61,5 |
34,3 |
60,8 |
38,8 |
- |
46 213 |
65 |
120 |
23 |
2,5 |
- |
- |
69,4 |
45,9 |
36 214 |
- |
70 |
125 |
24 |
2,5 |
80,2 |
34,8 |
- |
- |
- |
46 215 |
75 |
130 |
25 |
2,5 |
- |
- |
78,4 |
53,8 |
36 216 |
46 216 |
80 |
140 |
26 |
3 |
93,6 |
65 |
87,9 |
60 |
4.7. Компоновочный чертеж корпуса конического редуктора в плане
Задача дальнейшего эскизного конструирования, так же как и в цилиндрическом редукторе, заключается в том, чтобы поместить компоновку валов (см. рис. 4.15) в корпус и вычертить корпусные детали аналогично § 4.4 и рис. 4.6. Конструирование будем выполнять в том же порядке, что и
для цилиндрического редуктора.
Прежде чем приступать к компоновке конического редуктора, нужно внимательно познакомиться с § 4.4 и 4.5.
Корпус конического редуктора, как и цилиндрического, состоит из собственно корпуса и крышки корпуса (см. рис. 4.1), которые отливаются из чугуна или легкого сплава. Форма и соотношения размеров отдельных типичных элементов литого корпуса систематизировались и стали довольно определенными. Эти элементы были рассмотрены при конструировании корпуса в § 4.4. Корпус конического редуктора (см. рис. 4.19) составляется в основном из таких же или близких к ним по форме элементов.
Размеры корпусных деталей определяют по эмпирическим формулам, выведенным опытным путем.
|
Толщину |
стенки корпуса определяем по формуле (4.15), где |
а ак |
120 мм – |
условное межцентровое расстояние. После подстановки |
получим |
|
0,025а 3 0,025 120 3 6 мм.
Вычерчиваем вначале внутренний контур корпуса (см. рис. 4.15). Стенки корпуса 11, 12 и 13 проводим через торцы подшипников быстроходного и тихоходного, т.е. входного и выходного валов.
Внутренний контур нижней стенки 14 отстоит от зубчатого колеса на расстоянии 4 , которое определяется по формуле
4 |
4m. |
(4.74) |
Подставляя числовые значения, получим
4 4 3 12мм.
Бобышки и крышки диаметрами Da (см. рис. 4.19) вычерчиваем в соответствии с рис. 4.6 и 4.7 и описанием к ним.
Диаметры стяжных и фундаментных болтов dс и dф соответственно
определяем из табл. 4.4.
Относительно внутреннего контура на расстоянии толщины стенкикорпуса проводим пунктирной линией внешний контур, который с закруглениями переходит в бобышки (см. рис. 4.19), которые также обозначены пунктирной линией. Внешний контур с бобышками является невидимым, т.к. закрыт фланцем с отверстиями диаметром dс под стяжные болты, которых в данном фланце корпуса 12 штук.
Принципиальная конструкция корпуса без бобышек изображена на рис. 4.9 (см. описание этого рисунка). Конструкция бобышки, подшипника и крышки изображена на рис. 4.7 (см. описание к этому рисунку).
На рис. 4.11 представлен чертеж корпуса и крышки корпуса со всеми элементами, конструкцию которых следует применять для конического редуктора.
bр 2,5dс , |
(4.75) |
где dс – диаметр стяжных болтов, – толщина |
корпуса. Фланец |
опоясывает корпус (см. рис. 4.19) по периметру. Во фланце 12 отверстий диаметром dс . В местах размещения подшипников фланец упирается в бобышки диаметрами Da2 и Da3, которые определяются по формуле (4.19). Бобышки выступают за ширину фланца на 5 мм. Часть бобышки, расположенной под фланцем, обозначена пунктирной линией, которая переходит в пунктирную линию наружного контура стенки корпуса. Длина бобышек lр определяется по формуле (4.27).
Глухие крышки вычерчиваются согласно рис. 4.7 и описанию к нему. Крышки, сквозь которые проходят валы, вычерчиваются согласно
рис. 4.5 и описанию к нему.
Крышки к бобышкам привинчиваются болтами, диаметр которых выбирают по табл. 4.3. В этой же таблице указаны число болтов и элементы крышки. Отверстия под болты в бобышках сверлятся равномерно по окружности, диаметр которой определяется по формуле (4.29). Глубина отверстий должна соответствовать рис. 4.10, табл. 4.5 и описанию к ним, а также рис. 4.7.
Отверстия под стяжные болты диаметром dс (см. рис. 4.19) сверлятся по периметру фланца на расстоянии lс от внешнего контура фланца. Размер lс определяется по формуле (4.30). Болты, стягивающие
подшипники, устанавливаются по краям бобышек на расстоянии ta2 и ta3, которое определяется по формуле (4.31). Расстояние между остальными стяжными болтами в 8…12 раз больше диаметра болтов. Во фланце корпуса редуктора сверлят отверстия под резьбу dс" согласно формуле (4.32) и нарезают резьбу, а во фланце крышки корпуса сверлят отверстия dс' согласно формуле (4.33).
4.8. Построение главного вида конического редуктора
Главный вид редуктора нужно соотносить с видом в плане, поэтому вначале вычерчивают вид в плане, а над ним строят главный вид. Примером такого построения могут служить рис. 4.1 и 4.11.
Построение главного вида цилиндрического редуктора подробно описано в § 4.5. Цилиндрический редуктор в двух проекциях изображен на рис. 4.1, а размеры элементов корпуса показаны на рис. 4.11.
В коническом редукторе все элементы корпуса и крышек, которые относятся к узлу вала зубчатого колеса, полностью соответствуют узлу колеса цилиндрического редуктора. Конструирование стакана и крышки конического вала-шестерни описано в § 4.6.
Чертеж вида в плане (см. рис. 4.19) поворачивают по часовой стрелке на 90°, чтобы ось вала-шестерни заняла горизонтальное положение, а вал с зубчатым колесом, чтобы смотрел своим выходным концом вниз так же, как у цилиндрического редуктора (см. рис. 4.1). Вид в плане в выбранном масштабе размещают внизу листа. На главном виде, который располагают над видом в плане, наносят горизонтальную ось валов и зубчатых колес и вертикальную ось колеса с выходным валом. Затем циркулем проводят окружности вершин зубьев колеса пунктирной линией и бобышки выходного вала диаметром Da3 (рис. 4.20).
На расстоянии ас 0,5Dа от центра колеса проводят симметрично слева и справа вертикальные оси стяжных болтов. Определяют элементы фланцев корпуса и крышки. Толщина полки разъема редуктора
t 1,5dc .
Толщина полки у бобышки (толщина утолщения)
tс 0,3Da.
Расстояние от центра болта до края утолщения
c 1,5dc .

Затем слева и справа от бобышки диаметром Da3 вычерчивают фланцы с утолщениями.
Следующий этап – вычерчивание коробочки корпуса и крышки.
Длина коробочки |
L переносится с вида в плане (см. рис. 4.19). |
||
Д |
. |
||
|
|
Da2 |
|
до |
|
|
ВУ |
|
|
|
|
|
Рис. 4.19 |
|
|
(4 |
|
|
|
|
|
|
|
ta2
2
a3 |
L |
D |
ta3
δ4 δ
bр
dc
lс
В
tк4
bр 5 lр
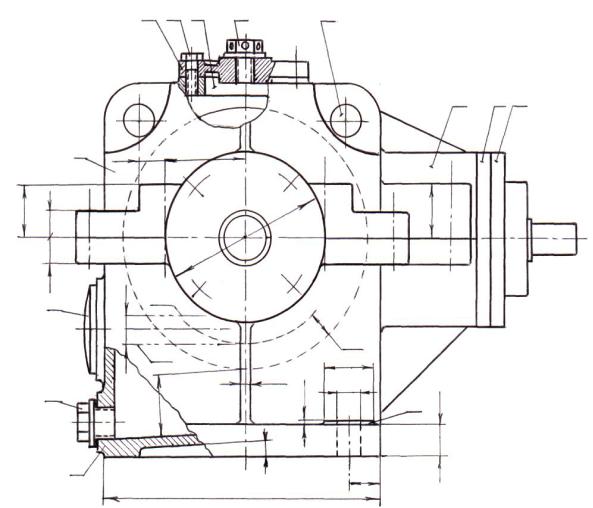
нижний уровень погружения приравнен ширине зуба hм min= b = 18мм, разность уровней hм 6m 6 3 18 мм.
24 25 23 26 27
20 21 22
16 |
c |
ac |
tc t t
17
tc
Dа3
ВУ
м |
|
|
|
h |
|
b |
|
НУ |
|
||
|
Dф |
||
18 |
dф |
||
|
|||
0 |
|
k |
|
|
|
||
h |
|
|
15 |
2 |
lф |
|
|
L |
19
tф
Рис. 4.20
Ось маслоуказателя 17 (см. рис. 4.20) делит разность уровней на две равные половинки 0,5 hм . Чертеж маслоуказателя и описание к нему см. § 4.5, рис. 4.12. Сливное отверстие в корпусе закрыто резьбовой пробой 18. Толщина подошвы tф 1,5dф , где dф – диаметр фундаментного болта,
выбираемого по табл. 4.4. Отверстие под болт располагают на расстоянии lф 1,5dф. Круглые приливы 19 (пятачки) делают диаметром Dф 2dф и
высотой k = 2…3 мм. Их фрезеруют, обеспечивая перпендикулярность торца прилива к оси отверстия фундаментного болта.
В бобышке 20 располагается стакан 21 с валом-шестерней (см. рис. 4.15, поз. 10). Стакан закрыт крышкой 22 (см. рис. 4.17).
Крышка корпуса 16 (см. рис. 4.20) по конструкции аналогична корпусу 15. В крышке корпуса предусматривают окно (люк) 23, размеры которого должны быть достаточны для осмотра передачи. Люк закрывают плоской крышкой 24 литой чугунной. Крышка крепится болтами 25 М6 или М8 в зависимости от размеров корпуса. В крышку можно вворачивать отдушину 26.
Для подъема и транспортировки редуктора делают проушины 27. Отверстия в проушинах de 0,02a 20 мм. Проушины оформляют согласно рис. 4.11 и описанию к нему.
После вычерчивания корпуса и крышки редуктора приступают к вычерчиванию остальных деталей. Вначале – стяжные болты. Два из них нужно показать в разрезе согласно табл. 4.5 и рис. 4.10.
Далее вычерчивают (рис. 4.20) крышку 24, закрывающую люк 23 в потолочной стенке крышки корпуса. Размеры длины крышки по отношению к длине корпуса
lкр L 0,35...0,55,
где lкр – длина крышки, мм; L – длина корпуса (рис. 4.19) без фланца, мм.
Ширину крышки можно выбирать из соотношения
bкр В 0,8...0,9,
где bкр – ширина крышки, мм; В – ширина корпуса, мм.
По контуру люка в потолочной стенке делают прилив толщиной
t 6 мм
Размеры прилива должны соответствовать ширине и длине крышки, т.е. bкр lкр . Окно люка меньше крышки
bл bкр 5dк ; lл lкр 5dк,
где bл – ширина окна люка, мм; lл – длина окна люка, мм; dк – диаметр болта, крепящего крышку, мм.
5.ПРОВЕРОЧНЫЙ РАСЧЁТ РЕДУКТОРА
5.1.Проверочный расчет зубчатых колес на изгиб
иконтактную прочность
При работе зубчатой передачи крутящий момент передается за счет зубьев. Зуб шестеренки давит на зуб колеса (рис. 5.1), в результате

возникает сила нормального давления F . В зоне контакта двух зубьев возникают контактные напряжения σH, а в основании ножки зуба – напряжения изгиба σF. Эти напряжения изменяются во времени. За один оборот шестерни (или колеса) ее зуб подвергается нагружению в зоне зацепления один раз. Нагрузка эта изменяется во времени, имеет прерывистый характер. Она направлена в одну сторону и за цикл изменяется от нуля до σmax. Такой цикл называется отнулевым. При вращении зубчатых колес под нагрузкой отдельные их зубья периодически нагружаются и разгружаются, а напряжения σH σF изменяются во времени по прерывистому отнулевому циклу (рис. 5.2). Длительное действие переменных напряжений вызывает усталость боковых поверхностей и прикорневой части зубьев. На боковой поверхности одного отдельно взятого зуба периодическое действие силы F напоминает удары молотка по зубилу, отчего происходит поверхностное смятие материала с последующим уплотнением тонкого поверхностного слоя. Такой вид деформации называется наклепом. В поверхностном слое со временем возникают микротрещины от усталости. Твердый поверхностный слой начинает чешуйками отслаиваться от основного металла. На поверхности появляются мелкие раковинки, как от оспы.
М2
|
d02 |
ω2 |
|
|
|
|
|
|
d2 |
|
n2 |
|
|
|
|
|
|
П |
|
|
σf |
σн |
|
|
|
|
|
|
|
d1 |
|
n1 |
|
||
|
|
|
|
|
M1 |
d01 |
|
|
|||
|
ω1 |
|
|
|
|
Рис 5.1 |
|
|
|
|
|
Такой вид разрушения называется усталостным выкрашиванием [1,
рис . 16.5, б].

В прикорневой части зуба от периодической нагрузки разрушение начинается также с микротрещин, которые со временем разрастаются и
происходит излом зуба [1, рис. 16.5, в].
σОдин оборот
t
Рис. 5.2
5.1.1. Расчет цилиндрических зубчатых колес
а) проверка зубьев на изгиб
Теоретический материал и вывод формул можно прочитать в гл. 2 т.2 и
в пособии [1, с. 166…169].
Проверочный расчет зубьев шестерни проводят по формуле
|
и1 |
|
2M1kи |
|
|
и |
, |
(5.1) |
|
y z m3 |
|||||||||
|
|
|
|
|
|||||
|
|
1 1 |
n |
|
|
|
|
где M1 – крутящий момент на шестерне, Н·мм; y1 – коэффициент формы зуба; z1 – число зубьев шестерни; ψ=10…20 – коэффициент ширины зуба; mn – нормальный модуль; kи – поправочный коэффициент.
Для косозубых колес коэффициент формы зуба шестерни y1 определяется по табл. 2.1, т.2 для эквивалентного числа зубьев[10, с.258, ф. (9.26)]
zэ1 = z1 / cos3β. |
(5.2) |
Поправочный коэффициент находят по формуле
kи = kиα· kиβ· kиv |
(5.3) |
где kиα – коэффициент, учитывающий неравномерность распределения нагрузки между зубьями. Для прямозубых колес kиα =1,5; для косозубых

колес и шевронных зависит от окружной скорости и степени точности: при v ≤ 10 м/с и 6, 7, 8, 9 степени соответственно kиα = 1,1 , 1,2 , 1,35 , 1,5; kиβ
=1-β°/140 – коэффициент, учитывающий угол наклона зуба; kиv – коэффициент динамической нагрузки, учитывающий возникновение дополнительных нагрузок от v, точности и упругости. Для прямозубых колес при НВ ≤ 350, kиv=1,4, при НВ > 350 kиv = 1,2. Для косозубых колес при НВ ≤ 350 kиv = 1,2, при НВ > 350 kиv = 1,1.
Допускаемые напряжения для нормализованных сталей 45, 50, 40Х и др. с НВ ≤ 350 определяются в т.2 по формулам (2.28) и (2.29). Для других сталей с другой термообработкой можно допускаемые напряжения найти в
[3, с. 166; [6, с.14].
Проверочный расчет зубьев колеса проводят по формуле
σи2 = σи1·y1/y2 ≤ [σи] , |
(5.4) |
где y1 и y2 – соответственно коэффициенты формы зуба шестерни и колеса. Формула (5.4) объясняется тем, что σи = F/y·bm, где F, b и m не зависят от числа зубьев, поэтому σи1·y1 = σи2·y2 = F/bm.
Пример 1. Используем данные, приведенные в §2.3, т.2: z1=18; z2=81; β=8,07°; ψ=10; m=2 мм; материал – сталь 45, термообработка – нормализация НВ=250; n1= 1425 об/мин, степень точности 8.
Решение
1. Проводим проверку прочности на изгиб зубьев шестерни по формуле (5.1)
и1 y2zM1kmи 3 и
1 1 n
2. Определяем коэффициент формы зуба для эквивалентного числа зубьев
zэ1 = z1 / cos3β = 18 / cos3 8,07° =18,18.
По табл. 2.1, т.2 для zэ1 = 18,18 находим y1 = 0,356.
3. Находим поправочный коэффициент. Определяем окружную
скорость |
|
|
|
|
|
|
|
|
|
|
|
|
|
|
n |
|
d |
|
n m z |
|
1425 2 18 |
|
мм |
|
м |
|
|
v |
1 |
|
1 |
|
1 1 |
|
|
2686 |
|
2,686 |
|
. |
|
30 |
2 |
60 |
60 |
с |
с |
||||||||
|
|
|
|
|
|
|
Для 8 степени точности и v ≤ 10 м/с, kиα = 1,35. Коэффициент
kиβ = 1- β°/140 = 1- 8,07°/140 = 0,942.
Коэффициент kиv = 1,2, т.к. НВ < 350.
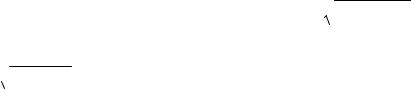
Поправочный коэффициент
kи= kиα· kиβ· kиv = 1,35 · 0,942 ·1,2 = 1,526.
4. Для нормализованных конструкционных углеродистых сталей при НВ ≤ 350 допускаемое напряжение на изгиб с учетом цикличности нагрузки определяется по формуле (2.28), т.2
и (1,8НВ /1,75)64 106 / N1 ,
где НВ = 250; N1 = 60·n1·h = 60·1425·40000 = 3.42·109 > 4·106, поэтому
6N0 / N1 1. Подставляя полученные значения, найдем
и (1,8 250/1,75) 1 257 Н/мм2.
5. Делаем проверку прочности зубьев шестерни
и1 |
|
2 14,3 103 1,526 |
85 Н/мм2 |
и 257 Н/мм2. |
|
0,356 18 10 23 |
|||||
|
|
|
|
Запас прочности составляет
[σu] / σu1 = 257/85 = 3 раза.
6.Определяем коэффициент формы зуба колеса:
–эквивалентное число зубьев (5.2)
zэ2 = z2 /cos3β = 81/сos3 8,07° = 83,45.
–по табл. 2.1, т.2 для zэ2 = 83,45 находим y2 = 0,478.
7.По формуле (5.4) определяем
σи2 = σи1·y1 / y2 = 85·0,356 /0,478 = 63,3 Н/мм2.
Запас прочности [σи] /σи2 = 257/63,3 = 4 раза.
б) проверка зубьев колес по контактным напряжениям
Теоретический материал и вывод формул можно прочесть в гл. 2, в
пособии [1, с. 169…172], учебнике [10, с. 260…264].
Проверочный расчет проводят по формуле:
– для прямозубых цилиндрических колес
С |
|
k |
|
Ft |
|
u12 1 |
k |
|
2M1 |
|
|
u12 1 |
C |
|
, |
(5.5) |
||
|
н b d |
|
|
|
|
|
||||||||||||
|
н |
|
|
u |
н |
2 |
m |
3 |
|
u |
н |
|
|
|||||
|
|
|
1 |
12 |
|
|
z |
|
|
12 |
|
|
|
|
||||
|
|
|
|
|
|
|
|
1 |
|
|
|
|
|
|
|
|
где Cн = 0,92 σн2/Е – коэффициент контактных напряжений, Н/мм2;