
2533
.pdf– в сечении II–II
τа2 = Мк / 2 Wр2 = 47000/2·8418 = 2,8 Н/мм2.
14. Коэффициенты концентрации напряжений определяются по формулам (5.13) и (5.14), т.2.
– в сечении I–I:
kv = 1 – коэффициент влияния поверхностного уплотнения (без упрочнения), табл. 5.1, т.2;
kσd = 3,46 для диаметра dш2 = 36 мм и σВ = 800 Н/мм2 – коэффициент, учитывающий концентрацию напряжений и влияние абсолютных размеров поперечного сечения, табл. 5.2, т.2;
kF = 1 – коэффициент влияния шероховатости поверхности (табл. 5.3, т.2), которая соответствует шлифованию с отклонением профиля Rа = 0,1…0,4 мкм;
коэффициент концентрации нормальных напряжений kσ1 = (kσd + kF – 1) / kv = (3,46 + 1-1) / 1 = 3,46;
kτd = 2,48 для диаметра dш2 = 36 мм и σВ = 800 Н/мм2 – коэффициент, учитывающий концентрацию напряжений и влияние диаметра сечения,
табл. 5.2, т.2;
коэффициент концентрации касательных напряжений
kτ1 = (kτd + kF – 1) / kv = (2,48 + 1-1) / 1 = 2,48.
– в сечении II–II:
kv = 1 – поверхность без упрочнения, табл. 5.1, т.2; kσd = 3,43 для диаметра dп2 = 35 мм и σВ = 800 Н/мм2 ; kF = 1 –поверхность шлифованная, Rа = 0,1…0,4 мкм; коэффициент концентрации нормальных напряжений
kσ2 = (3,43 +1-1) /1 = 3,43;
kτd = 2,46 для диаметра dп2 = 35 мм и σВ = 800 Н/мм2; коэффициент концентрации касательных напряжений
kτ2 = (2,46 + 1-1) /1 = 2,46.
15. Коэффициенты запаса прочности вала по нормальным sn и
касательным sτ напряжениям, формулы (5.24) и (5.25), т.2.
– в сечении I–I
sσ1 = σ-1 / σа1·kσ1 = 260 / 18,2·3,46 = 4,1,
где σ-1 = 260 Н/мм2 , см. табл. 5.4, т.2;

sτ1 = τ-1 / τа1· kτ1 = 150 / 2,7·2,48 = 22,4,
где τ-1 = 150 Н/мм2, см. табл. 5.4, т.2;
– в сечении II–II
sσ2 = σ-1 / σа2·kσ2 = 260 / 20,8·3,43 = 3,6;
sτ2 = τ-1 / τа2· kτ2 = 150 / 2,8·2,46 = 21,8.
16. Проверяем условие прочности вала по расчетным коэффициентам запаса прочности согласно условию прочности (5.28), т.2:
– в сечении I–I
s1 s 1s 1 / s21 s21 4,1 22,4/
4,12 22,42 4 s 2,1;
– в сечении II–II
s2 s 2s 2 / s22 s22 3,6 21,8/
3,62 21,82 3,5 s 2,1.
17. Определим действительные запасы прочности вала и сравним результаты расчетов двух методов:
метод эквивалентного напряжения:
– в сечении I–I
n1 = [σ-1]1 / σэ1 = 55,5 / 21,7 = 2,56;
– в сечении II–II
n2 = [σ-1]2 / σэ2 = 74,5 / 23,57 = 3,17;
метод расчетного коэффициента запаса прочности:
– в сечении I–I
n1 = s1 / [s] = 4 / 2,1 = 1,9;
– в сечении II–II
n2 = s2 / [s] = 3,5 / 2,1 = 1,7.
Если взять среднее значение допускаемого коэффициента запаса прочности [s]ср = (1,3+2,1) / 2 = 1,7, то получим:
– в сечении I–I
n1 = s1 / [s]ср = 4 / 1,7 = 2,35;
– в сечении II–II
n2 = s2 / [s]ср = 3,5 / 1,7 = 2.
Простым сравнением можно прийти к выводу, что оба метода дают близкие по точности результаты и могут применяться для проверочных расчетов вала.
5.3. Проверочный расчет шпонок
Наибольшее распространение в соединении вал – деталь вращения
(зубчатое колесо, шкив, звездочка, муфта) получили призматические шпонки. Они имеют прямоугольное сечение и стандартизованы (ГОСТ 23360-78). При расчетах и конструировании ширину b и высоту h шпонки выбирают по таблицам. Их главное назначение передавать крутящий момент от детали вращения к валу и наоборот. Наряду с передачей крутящего момента шпонки выполняют роль слабого звена. Слабым звеном называют деталь, которая в случае перегрузки узла должна в первую очередь разрушиться, а остальные детали должны остаться невредимыми. По-другому это звено называют предохранительным. Одну из шпонок редуктора конструктор выбирает в качестве слабого звена и рассчитывает ее на допускаемое напряжение среза, меньшее в полтора-два раза, т.е. на предельное напряжение, соответствующее пределу текучести, обеспечивая этим срез именно этой шпонки в случае перегрузки.
Стандартные шпонки – широкие, их ширина b больше предельной ширины на срез, поэтому смятие боковых поверхностей наступает гораздо раньше, чем напряжения среза достигнут своего предела. Исходя из вышесказанного, основным расчетом шпонок является проверочный расчет на смятие. Длину шпонки l принимают на 5…10 мм меньше длины ступицы.
Боковая рабочая поверхность шпонки, которая передает напряжения смятия, ограничивается плоскостью, а закругления на смятие не работают (рис. 5.7). Поэтому рабочая длина шпонки на смятие
lp = l - b.
Размеры стандартных шпонок подобраны из условия прочности на смятие.
Рабочая ширина боковой поверхности шпонки (рис. 5.6)
k = 0,5h.
Площадь смятия
Sсм = k·lp = 0,5h(l-b).
Силу давления F на боковую поверхность шпонки можно определить через крутящий момент
F = 2M / d,
где d – диаметр вала.
Напряжения смятия можно определить по формуле
σсм = F / Sсм = F / 0,5h (l - b) = 2M / 0,5h·d (l - b). |
(5.24) |
Ступицы деталей вращения (колес, шкивов, звездочек) изготавливают из стали и чугуна, а шпонки из среднеуглеродистой стали σВ ≥ 500 Н/мм2
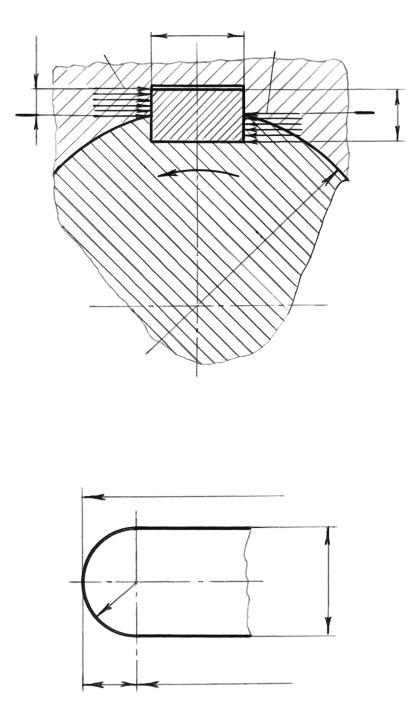
(марок 35…45). Допускаемые напряжения смятия при спокойной нагрузке
и стальной сту |
2 |
сталь 35, а |
|
k
а
b
σсм σсм
а
h
M
d
Рис. 5.6
0,5в lр
r
Рис. 5.7
b
большее – сталь 45), при чугунной ступице на смятие рассчитывается ступица, а допускаемые напряжения [σсм] = 70…100 Н/мм2, соответственно чугуны марок СЧ21-40…СЧ28-48, σВ = 200…280 Н/мм2 соответственно. Коэффициент динамичности: при спокойной нагрузке kд = 1, со слабыми толчками kд = 1,5, при ударной нагрузке kд = 3.
Условие прочности шпоночного соединения на смятие имеет вид с учетом коэффициента динамичности
σсм = 2 kд M/0,5h·d (l-b). |
(5.25) |
Пример 6. Используем данные из примера 5: dВ2 = 22 мм, dШ2 = 36 мм, lВ2 = 36 мм, lC2 = 56 мм, М2 = 46,85 Н·м = 46850 Н·мм.
Решение
1. По таблице (см. прил. 30) выбираем сечения шпонок: для dШ2 = 36
мм, b1 = 10 мм, h1 = 8 мм, l1 = 50 мм; для dВ2 = 22 мм, b2 = 6 мм, h2 = 6 мм, l2 =
32мм.
2.Выбираем материал шпонки сталь 35, [σсм]1 = 120 Н/мм2 .
3.Проверяем условие прочности при спокойной нагрузке:
–ступица зубчатого колеса изготовлена из стали 45, поэтому рассчитываем на смятие шпонку
σсм1 = 2 kд M2 /0,5h1·dш2 (l1 - b1) ≤ [σсм]1
– после подстановки получим
σсм1 = 2·1·46850 / 0,5·8·36 (50-10) = 16,27<120 Н/мм2;
– ступица звездочки изготовлена из чугуна марки СЧ21-40, [σсм]2 = 70 Н/мм2 при скорости v ≤ 3 м/с. Проверяем скорость цепи
v = z3 n2 tц /60·1000 = 21·429,5·12,7 / 60·1000 = 1,9 м/с < 3 м/с;
где z3 = 21 – число зубьев звездочки; n2 = 429,5 об/мин – частота вращения; tц = 12,7 мм – шаг цепи. Рассчитываем на смятие ступицу звездочки
σсм2 = 2 kдM2 /0,5h2·dВ2 (l2 - b2) = 2·1·46850/0,5·6·22 (32 - 6) = 54,6 < 120 Н/мм2
Результаты расчета шпонок удовлетворительные.
5.4. Проверочный расчет подшипников
Теоретический материал по подшипникам качения изложен в [1, §18.4].
Расчет подшипников качения по усталостному выкрашиванию на долговечность является основным.
Долговечность подшипников L – это расчетный срок службы, базовая долговечность в миллионах оборотов. В течение этого срока не менее 90 % подшипников при одинаковых условиях должны отработать без появления признаков усталости материалов колец или тел качения.
Экспериментально выведена формула
L = а (С/Q)m млн.об, |
(5.26) |
где С – динамическая грузоподъемность подшипника, кН; Q – эквивалентная нагрузка, кН; m – показатель степени, для шарикоподшипников m = 3, для роликовых – m = 3,33; a – коэффициент качества материала и условий эксплуатации [5, с.33; 6 с.105], коэффициент а введен по рекомендации JSO в конце 80-х, а = 0,6…0,7 для роликовых конических, а = 0,7…0,8 для шарикоподшипников, кроме сферических, а = 0,5…0,6 для роликовых цилиндрических и шариковых сферических.
Приведенная (эквивалентная) нагрузка определяется по формуле |
|
Q = (X·R+Y·A)· kБ · kТ, |
(5.27) |
где R и А – радиальная и осевая нагрузки на подшипник (рис. 4.1 т.2), кН; X и Y – коэффициенты (табл. 5.7); kБ – коэффициент безопасности, kБ =
= 1,3…1,5 – редукторы всех конструкций, меньшее значение при умеренных толчках, большее – при значительных толчках; kТ – температурный коэффициент, kТ = 1 при tподш ≤ 100 ºC, kТ=1,05…1,25 при tподш =125…200ºC.
Коэффициенты X и Y выбирают по табл. 5.7.
Для шариковых радиальных подшипников по таблицам находят статическую С0 и динамическую С грузоподъемности, а по табл. 5.7 определяют параметр е в зависимости от отношения А/С0. Дело в том, что шариковые радиальные подшипники нагружают не только радиальной R, но и осевой А нагрузками. Например, в цилиндрических косозубых редукторах применяют шариковые радиальные подшипники. Далее сравнивают отношение А/R: если А/R ≤ е, то X = 1, Y = 0, если
А/R > е, то X и Y назначаются по табл. 5.7.
Для роликовых радиальных подшипников всегда X = 1, Y = 0, т.к. осевую нагрузку они не передают А = 0.
Для радиально-упорных шариковых подшипников серии 36 000 с
углом контакта α=12º для заданного отношения А/С0 если А/R ≤ е, то X = = 1, Y = 0, если А/R > е, то X и Y назначают в зависимости от отношения
по табл. 5.7.
Для подшипников серий 46 000 и 66 000 с углом контакта α = 26º и α = = 36º если А/R ≤ е, то X = 1, Y = 0, если А/R > е, то согласно таблице для заданного значения А/С0.
Влияние осевой силы А на долговечность подшипника проявляется через коэффициент е=А/R, который определяет выбор коэффициентов X и Y. Для шариковых подшипников радиальных и радиально-упорных е соответствует минимальному значению силы А, когда она начинает сказываться на долговечности подшипника и величине коэффициентов X иY. Под действием силы А кольца подшипника смещаются и происходит
выборка радиального зазора до контакта, соответствующего отношению
А/R = е.
Определение коэффициентов X и Y
При этом более равномерно распределяется нагрузка по телам качения, поэтому при А/R ≤ е осевая сила А не оказывает влияния на величину эквивалентной нагрузки Q и Y = 0, а X = 1. Когда осевая сила превышает А/R > е, условия работы тел качения ухудшаются, суммарная реакция их увеличивается и это снижает долговечность подшипника. В этом случае Q определяют с учетом осевой силы А по табл. 5.7 для заданного значения
А/С0.
Для роликовых конических подшипников параметры С0, С, Y и е находят по таблицам, затем сравнивают: если А/R ≤ е, то X = 1, Y = 0, если А/R > е, то X = 0,4, а значение Y выбирают по таблицам.
Расчет на динамическую грузоподъемность. Эквивалентная нагрузка
Q определяется по формуле (5.27) с помощью табл. 5.7. Затем определяется долговечность подшипника L по формуле (5.26).
Условие долговечности проверяется по формуле
Lh = 106 L / 60n ≥ [Lh], |
(5.28) |
где n – частота вращения подшипника, об/мин; Lh – номинальная (действительная) долговечность; [Lh] – базовая или нормативная долговечность: для зубчатых редукторов [Lh] = 10 000 ч, для червячных редукторов [Lh] = 5000 ч.
Расчет на статическую грузоподъемность проводится для подшипников качения, работающих под большой нагрузкой в неподвижном состоянии или вращающихся с угловой скоростью n ≤ 1 об/мин. Они выходят из строя в результате остаточных пластических деформаций. Поэтому их работоспособность определяется статической грузоподъемностью. Условие выбора подшипника таково, чтобы его приведенная нагрузка, определяемая как большая из величин
Q = X0·R + Y0·A, |
(5.29) |
Q = R, |
(5.30) |
не превышала допускаемой статической грузоподъемности C0, т.е |
|
Q ≤ C0, |
(5.31) |
где X0 и Y0 – коэффициенты соответственно радиальной R и осевой А нагрузок, приводимые в таблицах подшипников.
Пример 7. Проверить на долговечность подшипники шариковые радиально-упорные серии 36207 согласно рис.5.5. Дано: n2 = 429,5 об/мин,
RA = 840 Н, RС = -1553 Н, А = 186 Н, подшипник 36207: d = 35 мм, С0 = 17,8
кН, |
|
|
|
|
|
|
|
|
|
C = |
|
Шарикоподшипники однорядные |
Шарикоподшипники радиально- |
||||||||||
|
|
||||||||||
|
|
радиальные |
|
|
упорные однорядные |
|
|
||||
|
А/С0 |
е |
X |
Y |
А/С0 |
е |
X |
|
Y |
|
|
|
0,014 |
0,19 |
|
2,30 |
|
Угол контакта α=12º |
|
|
|||
|
|
0,014 |
0,30 |
|
|
1,81 |
|
||||
|
0,028 |
0,22 |
|
1,99 |
0,029 |
0,34 |
|
|
1,62 |
|
|
|
0,056 |
0,26 |
|
1,71 |
0,057 |
0,37 |
|
|
1,46 |
|
|
|
0,084 |
0,28 |
|
1,55 |
0,086 |
0,41 |
|
|
1,34 |
|
|
|
0,11 |
0,30 |
0,56 |
1,45 |
0,11 |
0,45 |
0,45 |
|
1,22 |
|
|
|
0,17 |
0,34 |
|
1,31 |
0,17 |
0,48 |
|
|
1,13 |
|
|
|
0,28 |
0,38 |
|
1,15 |
0,29 |
0,52 |
|
|
1,04 |
|
|
|
0,42 |
0,42 |
|
1,04 |
0,43 |
0,54 |
|
|
1,01 |
|
|
|
0,56 |
0,44 |
|
1,00 |
0,57 |
0,54 |
|
|
1,00 |
|
|
|
|
|
|
|
|
|
|
|
|
|
|
|
|
|
|
|
|
Угол контакта α = 260 |
|
|
|||
|
|
|
|
|
− |
0,68 |
0,41 |
|
0,87 |
|
|
|
|
|
|
|
|
Угол контакта α = 360 |
|
|
|||
|
|
|
|
|
− |
0,95 |
0,37 |
|
0,66 |
|
30,8 кН, температура подшипника tº < 100 ºC, нормативная (базовая) долговечность [Lh] = 10 000 ч, условия работы подшипника обычные.
Решение
1. Определяем отношение
Таблица 5.7
А/С0 = 186/17800 = 0,0104,
согласно которому находим по табл. 5.7 методом интерполяции коэффициент е = 0,29.
2. Подшипник в опоре А нагружен только радиальной силой RA, а в опоре С радиальной силой RС и осевой – А. Так как RA < RС, то расчету
подлежит подшипник в опоре С, учитывая, что этот подшипник нагружен еще осевой силой. Для опоры С определяем отношение А/RC=186/1553 = 0,12 < е = 0,29. В этом случае X = 1, Y = 0.
3.Определяем эквивалентную нагрузку подшипника С по формуле
(5.27)
QС = RС·kБ·kТ = 1553·1,4·1 = 2174 Н = 2,17 кН.
4.Находим действительную (номинальную) долговечность более нагруженного подшипника С по формуле (5.26)
L= а (С/QС)m = 0,7(30,8/2,17)3 = 2000 ч.
5.Рассчитываем базовую долговечность по формуле (5.28)
Lh = 106 L / 60n = 106·2000/60·429,5 = 77 600 > [Lh] =10 000 ч,
что больше требуемой долговечности.
6. КОНТРОЛЬНЫЕ ЗАДАНИЯ И МЕТОДИЧЕСКИЕ УКАЗАНИЯ К КУРСОВОМУ ПРОЕКТУ (РАБОТЕ)
6.1. Задания к курсовому проекту
Каждое задание содержит кинематическую схему, номер которой соответствует последней цифре шифра студента (номера зачетной книжки или студенческого билета), вариант исходных данных, номер которого соответствует предпоследней цифре шифра студента, и дополнительные указания.
Каждая кинематическая схема изображена на отдельном листе, где в верхней части указан номер кинематической схемы и название механизма. Ниже приводится кинематическая схема, а внизу – таблица с вариантами исходных данных от 0 до 9. В нижней строке исходных данных указан тип редуктора: К – конический, Ц – цилиндрический, Ч – червячный. Редукторы – одноступенчатые.
Например, студент, имеющий шифр 03-153, должен выполнить курсовой проект (работу) механизма камнедробилки за номером 3, используя 5-й вариант исходных данных согласно табл. 3, для которого нужно в качестве первого звена применить конический редуктор и сконструировать его.
Задание: 1. Выходное звено механизма совершает вращательное, поступательное, возвратно-поступательное или возвратно-вращательное движение и нагружено на рабочем ходу постоянной силой Fc или моментом Мc полезного сопротивления. На холостом ходу, при обратном направлении движения выходного звена, полезное сопротивление отсутствует, но продолжают действовать вредные сопротивления. Учитывая трения в кинематических парах и зная КПД механизма ,
определить:
1) движущий момент Мд , постоянный по величине, который нужно приложить к входному звену 2 при установившемся движении с циклом, состоящим из рабочего и холостого ходов (в транспортирующих машинах холостой ход отсутствует, см. задание №№ 2,5 и 9);
2) работу сил полезного сопротивления на рабочем ходу, принимая силу полезного сопротивления Fc , или момент Мc величиной постоянной;
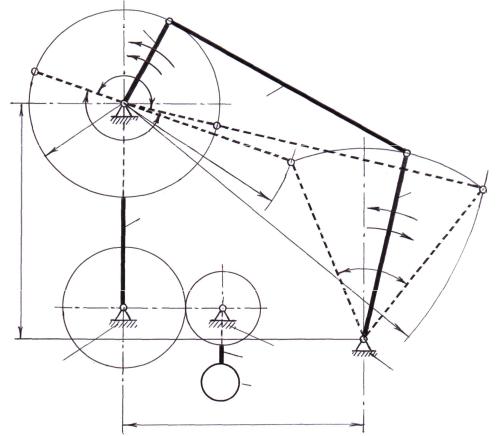
3)работы сил трения на рабочем и холостом ходах, считая, что вредное сопротивление постоянно на каждом из ходов, но на рабочем ходу оно в три раза больше, чем на холостом;
4)построить диаграмму сил сопротивления и определить мощность, приложенную к звену 2.
2. Выполнить кинематический расчет привода, включающего электродвигатель и звено 2.
3. Выполнить силовой расчет привода механизма.
4. Сделать эскизный проект редуктора.
5. Произвести проверочный расчет редуктора.
6. Представить пояснительную записку с полным расчетом привода и чертежи: 1) компоновки редуктора, 2) общего вида редуктора, 3) рабочих чертежей деталей.
6.2. Предварительный расчет рычажных механизмов (задания 1, 3, 4, 6, 7, 8, 10)
6.2.Предварительный расчёт рычажных механизмов (задания 1, 3,
4, 6, 7, 8, 10)
6.2.1. Построение крайних положений механизма
Целью предварительного расчета механизма является определение дополнительных исходных данных и выбор электродвигателя. Но для этого нужно графически определить ход поршня (ползуна) S4 , угол поворота кулисы 4 , угол поворота кривошипа на рабочем ходу р и на
хо |
|
|
|
B |
|
|
|
ло |
|
|
2 |
|
|
|
|
ст |
|
|
|
|
|
|
|
|
|
|
Mд |
|
|
|
|
ом |
В |
x |
|
|
|
|
|
хо |
|
|
2 |
|
|
|
|
|
A |
|
3 |
|
|
||
ду |
|
|
|
В |
|
|
|
х |
|
r2 |
|
|
|
|
|
|
|
|
|
C |
|
||
. |
|
р |
|
r |
C |
|
|
|
|
|
|
|
C |
||
|
|
|
|
|
4 |
||
|
|
|
|
|
|
||
|
a |
|
|
|
|
|
|
|
|
|
|
|
Mc |
|
|
|
|
|
I |
|
r |
4 |
|
|
|
|
|
|
|
O2 |
O1 |
|
|
|
|
D |
|
1 |
I |
1 |
|
1 |
|||
|
M 5 |
||
|
|
a