
2328
.pdf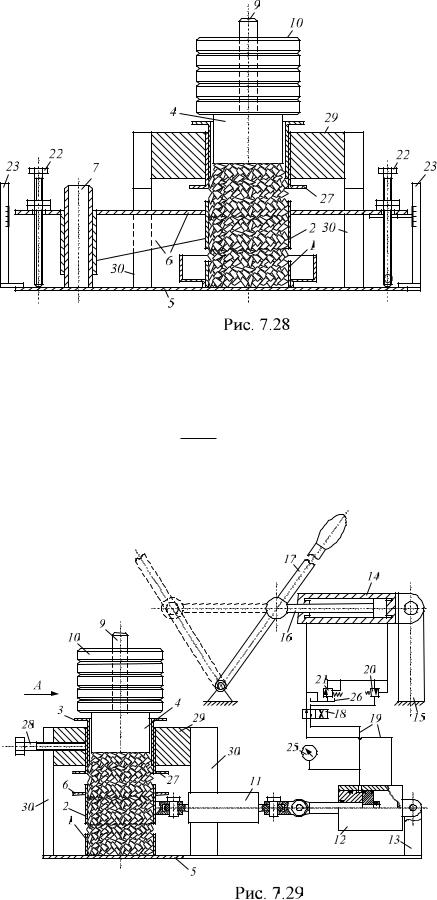
Касательные напряжения в плоскости среза столба материала определяются:
|
T |
, |
(7.18) |
|
D2 |
||||
|
|
|
4
где Т – сила среза; D – диаметр срезаемого столба материала, равный внутреннему диаметру подвижной обоймы.

На рис. 7.28 и 7.29 показана конструкция второго варианта способа испытания. Между неподвижными обоймами 1 и 27 находится подвижная обойма 2, закрепленная на кронштейне 6, который установлен на вертикальной штанге 7 с возможностью вертикального перемещения при регулировке зазоров подвижной обоймы 2 относительно неподвижных обойм 1 и 27. Зазор между неподвижной и подвижной обоймами принимается равным среднему диаметру dcp куска испытуемого материала. По рис. 7.28 зазоры
между обоймами регулируются винтами 22 с помощью измерительных шкал 23.
При сдвигании подвижной обоймы 2 относительно неподвижных обойм на рис. 7.29 с помощью гидроцилиндра 12 происходит срез столба испытуемого материала по двум сечениям.
Касательные напряжения при срезе определяются по формуле
T
2 D2 .
4
Благодаря осевому сжатию испытуемого материала и наличию сил трения между кусками сжатого материала его высыпания из рабочей камеры не происходит. Цилиндрический столб сыпучего мелкокускового материала в зазоре между подвижной и неподвижной обоймами представляет собой объемную структуру, способную воспринимать значительные сжимающие нагрузки и сдвиговые усилия. Выполняя постепенное увеличение силы сдвига, снимают по динамометру 11 значение силы Т, а по индикатору 24 (см. рис. 7.27) определяют соответствующую деформацию l и строят график функции f ( l). Для создания сдвигающей силы гидроцилиндром 12 устанавливают золотник распределителя 18 в позицию, показанную на рис. 7.27. Путем перемещения рукоятки 17 вправо (из пунктирного положения) обеспечивают подачу рабочей жидкости из поршневой полости гидронасоса 14 через клапан 20 и распределитель 18 в штоковую полость силового гидроцилиндра 12, шток которого при этом перемещается вправо, создавая сдвигающую силу Т на динамометре 11 и испытуемом образце. При перемещении рукоятки 17 влево рабочая жидкость засасывается в рабочую полость гидронасоса 14 из гидробака 26. В этот период штоковая полость силового гидроцилиндра 12 заперта и сила, созданная им, сохраняет свою величину. Для последующего увеличения силы сдвига Т
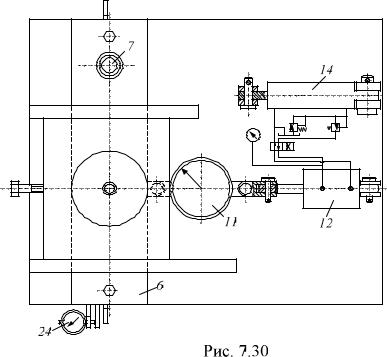
повторно перемещают рукоятку 17 ручного гидронасоса вправо, снова рабочую жидкость подают из поршневой полости гидронасоса 14 в штоковую полость силового гидроцилиндра 12.
Такие циклы увеличения сдвигающей силы повторяют до тех пор, когда столб материала разрушится этой силой или придет в предельное состояние. Через заданные интервалы увеличения сдвигающей силы снимают показания индикатора, фиксирующего деформацию сдвига, и строят графики. Конструкция прибора защищена патентом № 2311630 от 23.11.2007 г.
Разработку чертежей и изготовление прибора выполнила фирма «ИНТАстрой» г. Омск. Прибор имеет следующую техническую характеристику: максимальная сила сдвига Т=5000 Н; диаметр подвижной обоймы D=103 мм; масса грузов, обеспечивающих вертикальное сжатие испытуемого материала – 42 кг; максимальная величина зазора между подвижной и неподвижной обоймами равна максимальному среднему размеру куска материала dcp =15 мм.
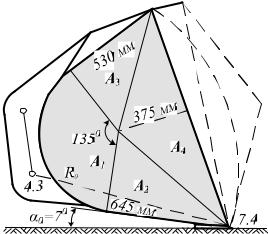
8. МЕХАНИКА СПОСОБОВ ЧЕРПАНИЯ МАТЕРИАЛОВ КОВШОМ ПОГРУЗЧИКА
8.1. Процесс раздельного черпания ковшом погрузчика сыпучего материала в штабеле
Рассмотрим процесс черпания сыпучего материала в штабеле на примере погрузчика ПК-3. Геометрический объем внутренней полости ковша и основные размеры определены по методике, разработанной в данной работе. Сечение внутренней полости ковша, определяющее его номинальную вместимость, представлено на рис. 8.1.
Ширина внутренней полости между боковыми стенками ковша Bo=2,49 м; радиус днища ковша ro=0,41 м. Номинальное сечение ковша, состоящее из кругового сектора A1, двух прямоугольных
41 0
М М
1 2 3 0
М М
треугольников A2, A3 и треугольника A4, имеет площадь
AC.H = =0,669 м2, номинальный
объем ковша VH = =1,667 м3 и
номинальная вместимость QH =3300 кг. Заполнение ков-
ша материалом до номинального объема соответствует коэффициенту наполнения ковша KH =1.
На рис. 8.1 пунктиром дополнительно показана шапка ковша, заполнение которой в легких условиях соответствует коэффициенту наполнения ковша KH =1,25. Внедрение ковша в штабель сыпучего материала начинают при минимальном угле установки днища ковша к опорной поверхности o 7o. Первой составляющей силы сопротивления при внедрении ковша в штабель является сила лобового сопротивления Wл , определяемая по формуле раздела 7
W |
л |
(sin |
o |
|
2 |
cos |
o |
) |
bзBo |
|
Г |
. |
(8.1) |
|
|||||||||||||
|
|
|
|
|
sin o |
|
|
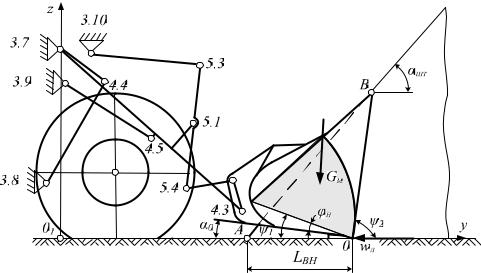
Величины в формуле имеют следующие значения: o |
24o ; |
||
2 =0,413; |
Г =0,23782 МПа; bз =0,005 |
м. Лобовая |
сила |
сопротивления для заданных условий по |
формуле (8.1) |
равна |
Wл 5707,4 Н.
При внедрении ковша в легкий штабель сыпучего материала с размерами кусков материала dcp 0,005 0,015 м учитываем
незначительное сцепление С=2 КПа. В начальной стадии процесса внедрения происходит скольжение материала по плоскому днищу ковша. Сопротивление в конечной стадии внедрения резко увеличивается вследствие образования внутри ковша неподвижного объема материала и плоскости скольжения материала под углом 1, который увеличивается в процессе внедрения от начального значения1 o 7o до максимальной величины 1 15 20o (рис. 8.2).
Рис. 8.2
При внедрении ковша погрузчика ПК-3 на величину LВН 1,15 м сила горизонтального сопротивления WK становится максимальной и погрузчик останавливается вследствие исчерпания своих тяговых возможностей по сцеплению или другим техническим характеристикам. Максимальный угол 1 в момент прекращения внедрения ковша складывается из следующих величин:
1max o H ,
где o – угол начальной установки передней стенки ковша; H – угол неподвижной призмы материала, соответствующий величине внедрения ковша LВН .
Для ковша погрузчика ПК-3 при глубоком внедрении в легкий штабель LВН =1,15 м; 1max 19o. Сила сопротивления внедрению днища по аналитической формуле (7.14) имеет величину W1=52128 Н. Полная горизонтальная сила сопротивления при внедрении ковша равна сумме силы лобового сопротивления и сопротивления внедрению днища ковша погрузчика: WK =WЛ +W1=57835 Н.
В рассмотренной методике расчета горизонтальной силы сопротивления на ковше при внедрении в штабель не учитываются другие составляющие, например, силы трения материала о внутренние и внешние поверхности боковых стенок ковша и др., суммарное влияние которых составляет 5 10% от максимальной силы тяги по сцеплению. Определим коэффициент использования сцепного веса погрузчика, соответствующий суммарному значению силы сопротивления на ковше:
|
|
= |
WK |
|
57835 |
0,525. |
|
|
|
||||
|
СЦ |
|
m g |
11230 9,81 |
||
|
|
|
э |
|
|
Такое значение СЦ для колесной машины является нормальным.
Выполненные расчеты позволяют проанализировать процесс заполнения ковша материалом. Для угла штабеля ШТ 50o при глубоком внедрении в легкий штабель (LВН =1,15 м; 2 86,25o ) внутренняя полость ковша на 80% заполнена материалом (см. рис. 8.2).
Математическая модель позволяет вычислить массу разрыхляемого материала в призме сечением ОАВ, которая для погрузчика ПК-3 составляет mПР =3483 кг, т.е. превышает номинальную вместимость ковша.
Для завершения процесса черпания необходимо повернуть ковш при неподвижном погрузчике относительно стрелы. Рассмотренный способ черпания называют раздельным черпанием.
8.2.Расчет момента сопротивления при повороте ковша
вштабеле

При повороте ковша происходит срез материала штабеля по цилиндрической поверхности, радиус которой равен длине вырывного плеча RB , проведенного из шарнира 4.3 в точку 7.4 режущей кромки ковша. При повороте ковша максимальный момент возникает в начале поворота. На ковш при повороте действует сила тяжести ковша GK , сила тяжести сектора материала GM в ковше, ограниченная поверхностью цилиндра радиусом RB и плоскостями, совпадающими с положениями радиуса RB в начальном и конечном положениях (рис. 8.3).
В цилиндрической поверхности среза на элементарной дуге в точке М возникают нормальная элементарная сила давления dN со стороны материала штабеля, элементарная касательная сила трения dFТР и элементарная сила сцепления dFСЦ .
z CT
RВ
zCT. max
RВ
Рис. 8.3
Для определения максимального момента среза материала штабеля ковшом необходимо определить результирующую окружную касательную силу в цилиндрической поверхности среза, при этом нормальные силы dN и их равнодействующая не создают момент относительно вершины стрелы 4.3 при повороте ковша.
Примем гипотезу о том, что давление в точках поверхности среза является функцией высоты столба материала над точками цилиндрической поверхности.
На рис. 8.3 показаны точки 1, 2, 3,…,7, которым соответствуют значения угла K поворота ковша и значения высоты столба zCТ материала (табл. 8.1). Аппроксимация этой зависимости выполнена выражением
|
zCТ |
0,0001 2K 0,0152 K |
1,4754. |
(8.2) |
||||||||
В выражении (8.2) угол K |
используется в градусах. |
|
|
|||||||||
|
Зависимость столба материала zCТ |
|
Таблица 8.1 |
|||||||||
|
от угла K |
|
|
|||||||||
|
|
|
|
|
|
|
|
|
|
|
|
|
Номер точки |
1 |
|
2 |
|
3 |
|
4 |
|
5 |
6 |
7 |
|
K , град |
0 |
|
16 |
|
26 |
|
35,5 |
|
46 |
56 |
63,5 |
|
zCТ , м |
1,49 |
|
1,13 |
|
0,95 |
|
0,75 |
|
0,48 |
0,22 |
0 |
|
Столб материала над точками 1, 2, 3, … ,7 (см. рис. 8.3) |
||||||||||||
изменяется от максимального значения zmax |
для точки 1, |
|||||||||||
находящейся |
в подошве штабеля, |
до нулевого значения |
z=0 для |
точки 7, которая находится на свободной поверхности штабеля. Функция связывает угол K с высотой столба zCТ . Элементарный момент от сил среза в произвольной точке цилиндрической поверхности штабеля при повороте представляет собой сумму двух составляющих: первая является крутящим моментом от сил кулоновского трения и вторая – моментом от сил сцепления материала в цилиндрической поверхности среза (см. рис. 8.3).
dM |
СР |
dM |
TP |
dM |
CЦ |
B |
R2 |
|
K |
d |
K |
B |
R2Cd |
K |
, |
(8.3) |
|
|
|
o |
B n |
|
|
o |
B |
|
|
где K – коэффициент трения скольжения в поверхности среза; n – нормальное давление на поверхности среза, зависящее от высоты столба zCТ в каждой точке; С – сцепление материала штабеля.
Запишем выражение для нормальных давлений с учетом выполненной аппроксимации (8.2):
n M gzCT M g( 0,0001 2K 0,0152 K 1,4754).
Первое слагаемое формулы (8.3) можно проинтегрировать численным методом, а второе превращается в простую формулу. Запишем момент от сил трения и момент от сил сцепления в виде отдельных формул:
dM |
|
B R2 |
|
g |
|
n |
|
|
|
d |
|
; |
(8.4) |
||
ТР |
M |
K |
z |
CT.CPi |
K i |
||||||||||
|
o |
|
B |
|
i 1 |
|
|
|
|
||||||
|
|
|
|
|
|
|
|
|
|
|
|
|
|
|
|
|
|
M |
СЦ |
B R2C |
K max |
, |
|
|
|
(8.5) |
|||||
|
|
|
|
|
o |
B |
|
|
|
|
|
|
где K max – полный угол дуги среза материала.
Численное интегрирование выражения можно выполнить путем использования численных значений углов K и высоты столба zCТ (см. табл. 8.1). При помощи выражения (8.3) можно задать любое число точек расчета.
Для каждой пары последовательных точек (см. табл. 8.1)
вычисляются интервалы углов |
|
i K(i 1) |
K.i |
и средние высоты |
|||||||||||||
столба zCT.i для двух точек: zCT.CP |
|
zCT.i zCT(i 1) |
. |
|
|
||||||||||||
|
|
|
2 |
|
|
|
|
|
|
||||||||
|
|
|
|
|
|
|
|
|
|
|
|
|
|
|
|
|
|
При помощи этих данных вычисляем момент сил трения для |
|||||||||||||||||
всей дуги среза материала: |
|
|
|
|
|
|
n |
|
|
|
|
|
|
|
|||
|
M |
|
B R2 |
|
g |
|
|
|
|
|
|
, |
(8.6) |
||||
|
ТР max |
M |
K |
z |
CT |
.CPi |
|||||||||||
|
|
o |
B |
|
|
i 1 |
|
|
i |
|
|
||||||
|
|
|
|
|
|
|
|
|
|
|
|
|
|
|
|
|
|
где i – индекс члена суммы произведений двух величин; i |
– угол в |
||||||||||||||||
радианах. |
|
|
|
|
|
|
|
|
|
|
|
|
|
|
|
|
|
Для определения полного момента при повороте ковша |
|||||||||||||||||
необходимо учесть момент от веса |
|
|
ковша GK |
и момент |
от веса |
||||||||||||
сектора материала GM , находящегося внутри вырезаемого грунтового |
|||||||||||||||||
цилиндра: |
|
|
|
|
|
|
|
|
|
|
|
|
|
|
|
|
|
MK max MTP max MСЦ max (GK |
GM )(y7.2 y4.3), |
|
|||||||||||||||
где y4.3; y7.2 |
– координаты конца стрелы и центра тяжести ковша. |
||||||||||||||||
Момент сил трения при повороте ковша погрузчика ПК-3 равен |
|||||||||||||||||
MТР =31632 Нм; момент от сил сцепления MСЦ =3906,4 Нм. Момент |
|||||||||||||||||
среза MСР |
материала при повороте |
|
ковша равен сумме |
момента |
|||||||||||||
трения MTP |
и момента |
сцепления |
|
MСЦ . |
Из |
полученных |
формул |
видно, что момент поворота при черпании ковша состоит из момента от сил трения, момента от сил сцепления, а также моментов от сил тяжести ковша и материала в ковше. Работу, совершаемую ковшом при повороте, целесообразно вычислять последовательно отдельно для каждого момента. Если принять гипотезу о линейном изменении моментов MTP и MСЦ при повороте ковша от максимального
значения до нуля, то работа этих моментов может быть вычислена по формуле

A (M |
TP max |
M |
СЦ max |
) |
K max |
. |
|
||||||
CP |
|
2 |
|
|||
|
|
|
|
|
|
При угле K max 40o =0,698 рад работа равна AСР =12402,9 Дж. Работа сил тяжести ковша и материала зависит только от
вертикального перемещения их центров тяжести:
где hK – |
A(GK ,GM ) (mK |
mM )ghK , |
(8.7) |
||
вертикальное |
перемещение |
центра тяжести |
ковша при |
||
повороте, |
hK =0,27 м; mK |
– |
масса ковша, mK =675 кг; |
mM – масса |
|
материала в ковше, mM =2640 |
кг. |
|
|
A(GK ,GM ) (675 2640)9,81 0,27 8780,5 Дж.
Работа среза материала оказалась значительно больше работы, совершаемой силами тяжести ковша и материала в ковше. При повороте ковша в результате выполнения операции среза дополнительный материал в ковш не поступает. Материал, находящийся в ковше, при его повороте осыпается внутрь ковша, осуществляя заполнение ковша с коэффициентом наполнения KН =1.
На рис. 8.4 точками 1, 2, …, 5 показано сечение материала в ковше, которое условно сохранило свою начальную форму при повороте.
Рис. 8.5
Рис. 8.4
Сравнение схем на рис. 8.4 и 8.5 позволяет наглядно продемонстрировать реальный факт осыпания материала внутрь ковша.
Рассмотрен раздельный способ черпания, заключающийся во внедрении ковша в штабель поступательным движением с последующей остановкой погрузчика и повороте ковша, который