
Шейпак А.А. Гидравлика и гидропневмопривод (часть 2)
.pdf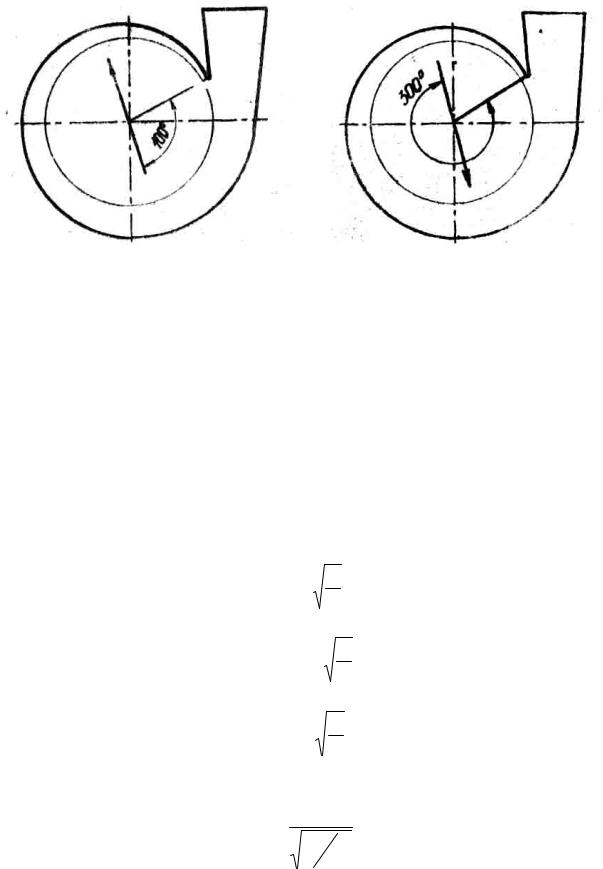
Направление действия силы при подачах, меньших расчетной, показано на рис.2.18 слева; направление действия силы при подачах, больших расчетной, показано на рис.2.18 справа.
Рис. 2.18. Радиальная сила, действующая на рабочее колесо центробежного насоса
2.2.10. Расчет центробежных насосов по нормативным данным
При выполнении геометрического, кинематического и динамического подобия для центробежных насосов очевидно следующее равенство:
|
V |
|
4Q |
60 |
|
|
K |
3Q |
|
|||||
|
0 |
= |
|
|
|
|
|
|
|
|
= |
|
|
, |
|
|
πD2 |
|
πDn |
nD3 |
|||||||||
U1 |
|
|
|
|
||||||||||
где K – постоянный коэффициент. |
|
|
|
|
|
|
|
|
|
|
||||
Отсюда можно сделать вывод: любой линейный размер насоса можно |
||||||||||||||
подсчитать как |
|
|
|
|
|
3 Q . |
|
|
||||||
|
|
|
|
L = K |
|
|
||||||||
|
|
|
|
i |
|
|
i |
|
|
|
n |
|
|
|
|
|
|
|
|
|
|
|
|
|
|
|
|
|
|
В частности, для наружного диаметра рабочего колеса |
||||||||||||||
|
|
|
|
D = K |
|
3 Q , |
|
|
||||||
|
|
|
2 |
|
|
|
|
2 |
|
n |
|
|
||
для ширины рабочего колеса на выходе |
|
|
|
|
|
|||||||||
|
|
|
b = |
K |
b |
3 Q . |
|
|
||||||
|
|
|
2 |
|
|
|
|
n |
|
|
|
|||
|
|
|
|
|
|
|
|
|
|
|
|
|
|
Результаты статистической обработки данных по выполненным центробежным насосам приводят к следующим эмпирическим формулам
[1]: |
К2 = |
9,35 |
, |
|
|
|
nS |
100 |
|
|
|
|
|
71

Kb = 0,8 |
n |
S |
|
|
|
|
Q |
56 |
|
|
|
|||
|
для nS ≤ 200 и Kb = 0,635 |
|
|
|
|
для nS |
≥ 200 . |
(2.50) |
||||||
|
|
|
|
|||||||||||
|
100 |
|
|
|
|
|
n |
|
|
( nS = |
|
|||
Для насосов низкой и средней быстроходности |
20…120) |
|||||||||||||
лучшие результаты дает формула, полученная нами: |
|
|
||||||||||||
|
|
|
K2 = |
|
|
8,9 |
|
|
|
|
|
|
|
(2.51) |
|
|
|
n |
s |
|
0,65 |
|
|
|
|||||
|
|
|
|
|
|
|
|
|
||||||
|
|
|
|
|
100 |
|
|
|
|
|
|
|
|
|
|
|
|
|
|
|
|
|
|
|
|
|
|
|
Коэффициент K0 для вычисления приведенного диаметра входа в рабочее колесо D0 меняется в очень широких пределах: от 3,3 для насосов
или ступеней насосов для получения высокого значения коэффициента полезного действия до 6,5 для обеспечения повышенных кавитационных качеств.
Диаметр горловины, или горла рабочего колеса, определяется как
Dg = D02 + Dвт2 ,
где Dвт – диаметр втулки рабочего колеса.
Вычисленный по формуле (2.50) или по формуле (2.51) наружный диаметр затем уточняется в соответствии с материалами, приведенными в разделах 2.2-2.8.
Размеры отвода, соответствующие минимальным потерям, можно подсчитать исходя из размера стороны квадрата a , определяющего площадь минимального сечения спирального отвода.
Ka =1,18 + 0,0079nS .
Для оценки эффективности насоса можно до проведения детальных расчетов провести оценку КПД машин с закрытыми колесами в соответствии с принятой системой разделения потерь.
Для гидравлического КПД:
|
1 |
=1,15 + 0,66 |
10 |
−5 K0 nS43 . |
|||||||
|
|||||||||||
|
ηг |
|
|
|
|
|
|
|
|||
Для объемного КПД: |
|
|
|
|
|
|
|
||||
1 |
=1+ |
|
0,01 . |
||||||||
|
|
|
ηо |
2 |
|||||||
|
|
|
|
n |
3 |
3 Q |
|||||
Для механического КПД: |
|
|
S |
|
|
|
n |
||||
1 |
|
|
|
|
100 |
|
|||||
|
|
|
|
|
=1,08 + |
. |
|||||
|
|
|
|
|
|
|
|||||
|
|
|
|
ηм |
|
|
|
nS2 |
Эффективность насосов с открытыми и полуоткрытыми колесами целесообразно оценивать посредством другой номенклатуры частных КПД, предложенной А.С.Шапиро.
72

Составляющая КПД, зависящая от коэффициента быстроходности:
1 |
|
|
100 |
|
|
nS − |
3 |
||
|
|
|
|
||||||
|
= 0,14 |
|
|
|
|
+ 0,91+ 0,054 |
|
|
. |
ηn |
|
3 |
100 |
|
|||||
|
nS − |
|
|
|
|
||||
S |
|
|
|
|
|
|
|
|
|
Составляющая КПД, зависящая от размера насоса:
|
|
|
7 |
Q |
1 |
4 |
|
|
|
|
|
. |
|||||
ηQ |
=1−exp −1,2 10 |
|
|
|
|
|||
|
|
|
|
|||||
n |
|
|
|
n |
|
|
|
|
|
|
|
|
|
|
|
|
|
Составляющая КПД, зависящая от величины коэффициента приведенного диаметра входа при K0 > 4:
|
|
K |
0 |
− 4 |
|
|
n |
S |
|
|
η |
к0 |
=1− |
|
|
|
|
|
. |
||
|
|
|
|
|
||||||
|
|
25 |
|
100 |
|
|||||
|
|
Полный КПД насоса с открытым или полуоткрытым колесом:
η = ηn |
ηQ |
ηк |
0 |
. |
|
S |
n |
|
|
|
|
|
|
Во всех приведенных формулах размерность объемного расхода [м3/с], частоты вращения – [об/мин]. Погрешность расчета может быть до
10%.
2.2.11. Стохастическая модель центробежного насоса
Кроме средних значений основных параметров гидравлических машин, в первую очередь напора и коэффициента полезного действия, важным критерием качества является величина их разброса. Во многих случаях нежелательным является как низкое значение параметра, так и чрезмерно высокое, так как возможно создание чрезмерно больших нагрузок в некоторых элементах общей системы. Поэтому целесообразно на этапе проектирования провести анализ задания допусков на основные размеры машины, определяющих поле разброса выходных параметров: КПД, напора, мощности.
Хорошие результаты во многих случаях дает имитационное моделирование методом Монте-Карло. Для реализации метода необходимо задать допуски на выполнение проточной части машины и закон их распределения. Обычно принимается нормальное распределение, если неизвестен характер влияния технологического процесса изготовления. Однако вид распределения не влияет существенным образом на процесс моделирования. Необходимо выбрать детерминированную модель и процесс случайного выбора размеров. Далее проводится серия расчетов, которая дает либо оценку основных статистик: дисперсии, размаха (разницы между максимальным и минимальным значениями параметра), асимметрии, эксцесса, либо, при достаточно большом числе экспериментов, распределение выходных параметров машины (гистограмму).
Содержание предыдущих разделов дает возможность создать стохастическую (вероятностную) модель центробежного насоса, учитывающую
73
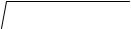
его следующие размеры: наружный диаметр рабочего колеса, диаметр начала лопаток, диаметр горла рабочего колеса, диаметр втулки, диаметр вала под подшипники, диаметры уплотнений, радиальные зазоры в уплотнении, ширина лопатки на входе в колесо, ширина лопатки на выходе из колеса, ширина колеса на наружном диаметре, число лопаток, угол установки лопатки на входе, угол установки лопатки на выходе.
Формула для определения гидравлических потерь в рабочем колесе была модернизована для получения оценки поля разброса.
ζк = 0,65 +0,36(h + 0,32)± ∆ζ, где ∆ζ = 0,09 1 + 31(h + 0,32)2 .
Кроме того, необходимо задать разброс коэффициента потерь в отводящем устройстве: ζо = 0,20 ± 0,02 .
В таблице 2.1 приведены результаты математического моделирования для насоса с коэффициентом быстроходности nS = 40.
|
|
|
Таблица 2.1 |
|
|
|
|
|
|
|
|
|
Критический |
|
Параметр |
КПД |
Напор |
кавитационный |
|
|
|
|
запас |
|
Среднее значение |
0,689 |
849 |
7,2 |
|
Среднее квадратичное |
0,005 |
38 |
0,1 |
|
отклонение |
|
|
|
|
Размах |
0,098 |
92 |
1,2 |
|
Эксцесс |
0,77 |
1,94 |
-0,85 |
|
Среднее квадратичное |
0,47 |
0,47 |
0,47 |
|
отклонение эксцесса |
|
|
|
|
Асимметрия |
0,89 |
1,01 |
0,76 |
|
Среднее квадратичное |
0,76 |
0,76 |
0,05 |
|
отклонение асимметрии |
|
|
|
|
Расчетная гистограмма распределения напоров одного из серийных насосов приведена на рис. 2.19,а. Соответствующая расчетная гистограмма распределения КПД приведена на рис. 2.19,б.
В численном эксперименте исследовалась партия из 200 насосов. Весь диапазон изменения параметров был разделен на 10 интервалов, границы которых обозначены цифрами на горизонтальной оси. Размер по вертикали пропорционален числу насосов, относящихся к определенному интервалу. Соответствующие числовые значения приведены на верхней стороне прямоугольников. Из рисунков видно, что распределение напоров и КПД соответствует нормальному закону.
74

а)
б)
Рис. 2.19. Расчетные гистограммы распределения напора (а) и КПД (б) для серийных насосов
75
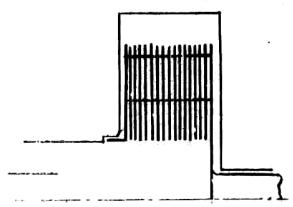
2.3.Насосы трения
2.3.1.Устройство и принцип действия дискового насоса
Дисковым насосом называется насос трения, в котором жидкая среда перемещается через рабочее колесо от центра к периферии. Конструктивная схема такого насоса изображена на рис. 2.20. Подводящее и отводящее устройства дискового насоса аналогичны рассмотренным ранее устройствам центробежного насоса. Рабочее колесо представляет собой совокупность тонких кольцевых дисков, расположенных в плоскостях, перпендикулярных оси вращения, на небольшом расстоянии друг от друга. Крепежные элементы размещены в периферийной части дисков, чтобы не загромождать входное сечение.
Рис 2.20. Дисковый насос трения
Жидкая среда по подводящему устройству поступает к рабочему колесу, в пространстве между дисками благодаря силам трения она получает приращение момента импульса. Как показывают расчеты и экспериментальные исследования, для повышения эффективности такого насоса необходимо иметь малые значения радиальных составляющих скоростей. Поэтому оптимальная конструкция рабочего колеса многодисковая. В выполненных конструкциях число дисков колеблется от 18 до 174, расстояние между дисками от 0,1 мм до 0,5 мм, толщина диска от 0,1 до 1,6 мм.
Напор дискового насоса при одинаковых окружных скоростях в 1,5…2 раза меньше, чем центробежного насоса, полученные значения КПД лежат в пределах от 0,2 до 0,6.
Однако, несмотря на невысокие энергетические показатели, дисковый насос, предложенный в 1911 году знаменитым югославским изобретателем Николой Тесла, имеет неоспоримое преимущество по кавитационным качествам. Формулу для критического кавитационного запаса дискового насоса можно получить из формулы (2.49), заменив относительную скорость радиальной Vr1
76
∆h |
= |
V 2 |
+ λ |
V 2 |
, |
н |
r1 |
||||
кр |
|
2g |
|
д 2g |
|
где коэффициент кавитации λд = 0,2Κ 0,6 .
Так как скорость Vr1 в отличие от относительной скорости не зависит
от частоты вращения, то дисковый насос является чемпионом по быстроходности: максимальная достигнутая частота вращения вала насоса равна 600000 об/мин при наружном диаметре D2 = 20 мм. КПД такого насоса остается постоянным при снижении размеров, он отличается малым уровнем шума, простотой изготовления, низкой стоимостью. Дисковый насос при сравнительно малом износе способен перекачивать суспензии металла и жидкости.
В автомобильной промышленности дисковый насос может использоваться как водяной, топливный, масляный. По такой же схеме выпускались и турбонагнетатели автомобильных двигателей.
2.3.2. Устройство и принцип действия вихревого насоса
Вихревые насосы были созданы в Германии в 30-х годах нашего столетия. В настоящее время они получили широкое применение при малых подачах и относительно высоких напорах, там, где центробежные насосы недостаточно эффективны из-за больших объемных и механических потерь.
Вихревой насос по современной классификации – это насос трения, в котором жидкая среда перемещается по периферии рабочего колеса в тангенциальном направлении.
Рабочими органами вихревого насоса (рис. 2.20) являются рабочее колесо 1 с лопатками, расположенными в его периферийной части, и рабочий канал, выполненный концентрично рабочему колесу в корпусе 2. Всасывающая и напорная полости разделены перемычкой 3. Колесо установлено в корпусе с небольшими торцевыми зазорами порядка 0,1 мм на сторону, такой же порядок имеет величина радиального зазора между колесом и перемычкой.
Рабочий процесс вихревого насоса основан на передаче энергии лопастями рабочего колеса потоку жидкости в канале в результате переноса импульса (количества движения) от жидкости, движущейся в ячейках рабочего колеса, к жидкости, движущейся в рабочем канале насоса. Перенос импульса осуществляется за счет увлекающего действия колеса и вследствие возникновения продольных и радиальных вихрей. Передача энергии сложной системой продольных и радиальных вихрей сопровождается большими потерями энергии, поэтому КПД вихревых насосов на оптимальных режимах работы ниже (0,20…0,60), чем у центробежных, несмотря на существенно большую (в 1,5…2 раза) напороспособность при одинаковых значениях окружных скоростей. Из принципа действия вихревых
77

насосов ясно, что они эффективны только для подачи чистых маловязких жидкостей. Они имеют более низкие кавитационные качества по сравнению с центробежными насосами.
Рис. 2.21. Вихревой насос
Однако компактность и малая металлоемкость вихревых насосов, способность к самовсасыванию и крутопадающая напорная характеристика делают их незаменимыми для подачи легколетучих жидкостей и жидкостей, насыщенных газами, особенно при подаче малых количеств жидкостей при больших напорах.
2.3.3. Устройство и принцип работы черпакового насоса
Для уменьшения механических и объемных потерь и улучшения кавитационных качеств динамических насосов в последние годы ряд фирм ФРГ и США применяют насосы с вращающимся корпусом (рис. 2.21). Это черпаковые насосы – насосы трения, в которых жидкая среда перемещается через отвод от периферии к центру.
Черпаковый насос состоит из отвода – черпака 1, представляющего собой обтекаемое тело с заборным отверстием на периферии и вращающегося корпуса 2 с радиальными лопатками.
Жидкость, поступающая в корпус через кольцевое входное сечение, закручивается лопатками и направляется к его периферии. Здесь она попадает в заборное отверстии отводного устройства, выполненного в виде черпака и по осевой трубе направляется в напорный патрубок.
78

Рис. 2.22. Черпаковый насос
В некоторых случаях черпаковые насосы могут быть конкурентно способными с вихревыми и объемными. Так, при одинаковых напорах и подачах они имеют несколько более высокий КПД и заметно лучшие кавитационные качества, чем вихревые. Черпаковые насосы могут перекачивать загрязненные жидкости, кристаллизующиеся растворы, жидкие металлы. Особенно эффективны черпаковые насосы при наличии высокооборотного привода (n > 5000 об/мин). Однако черпаковые насосы по сравнению с вихревыми насосами имеют большую металлоемкость и не обладают свойством самовсасывания.
2.3.4. Лабиринтные насосы
Лабиринтные насосы могут быть радиального и осевого типа.
Схема лабиринтного насоса осевого типа приведена на рис. 2.23. Он состоит из двух основных элементов: ротора 2 и статора 1, на поверхностях которых, обращенных друг к другу, выполнены лопатки противоположного направления.
Наиболее интересной конструкцией является случай выполнения решеток лопаток на цилиндрических поверхностях. В этом случае лопатки выполняются в виде многозаходной нарезки на винте и втулке, охватывающей винт, с противоположным направлением нарезок. Например, на винте выполняется правая резьба, а на втулке – левая. При вращении вала в кольцевом зазоре, образованном гладким валом и втулкой, возникают кольцевые вихри (вихри Тейлора). При вращении втулки таких вихрей не наблюдалось. Передача энергии от винта к окружающей жидкости происходит в результате непрерывного возникновения, развития и отрыва ука-
79

занных вихрей. Механизм передачи энергии от винта к жидкости сходен с механизмом турбулентного трения в жидкости.
Рис. 2.23. Схема осевого лабиринтного насоса
Значения КПД лабиринтного насоса примерно такие же, как и у вихревых насосов. Однако лабиринтные насосы требуют для своего изготовления меньше материалов. Большой практический интерес представляет использование лабиринтных насосов в качестве уплотнений валов различных машин.
2.3.5. Струйные насосы
Струйные насосы не имеют подвижных частей, энергосообщителем является поток жидкости (рис. 2.24).
Насос состоит из входного устройства, к которому подводится жидкость под большим давлением. В сопле происходит преобразование потенциальной энергии активного потока жидкости Qакт в кинетическую энер-
гию. В камере смешения происходит передача энергии основному или пассивному потоку жидкости Q , затем в диффузоре кинетическая энергия
суммарного потока жидкости преобразуется в потенциальную энергию.
80