
Методичка по пропедевтике 3 семестр (стомат)
.pdfВыплавление восковой модели и прокаливание литейной формы.
Снимают подставку после ее предварительного подогревания во избежание повреждения восковой формы и облицовчного слоя, устанавливают кювету-опоку на поддон воронкой вниз для отекания воска и переносят в печь, нагретую до температуры 200 °С на 20-25 минут для окончательного удаления воска. Устанавливают опоку в прокалочную печь с температурой 400°С , доводят ее до 800 - 9001 в течение 1,5 ч., выдерживают при этой температуре 20-30 минут и переносят в печь для заливки металла.Хорошее прокаливание литейной формы обеспечивает хорошие литейные свойства металлу, уменьшает его усадку, исключает газовыделение при заливке металла.
Пользоваться прокалочными печами для выплавления воска нельзя, т. к. возникающая при этом копоть увеличивает содержание углерода в отливке, и засоряя электронагреватели, выводит печь из строя. При литье на огнеупорных моделях в.состав которых входит кристобаллит, незначительно расширяющийся в интервале температур 200 - 3001 подъем температур от 200 до 300 С надо проводить медленно ( 30-40 минут) для удаления кристаллизационной воды и газов. Ускорение подъема температур в этом интервале приводит к растрескиванию и разрыву литейной формы.
Плавильные и литьевые аппараты.
Сплавы, применяемый в ортопедической стоматологии, делятся на три группы, в зависимости от температуры плавления. К первой группе относятся сплавы с точкой плавления до 300'(легкоплавкий сплав на основе олова, олова с присадкой серебра и меди и т. д.); ко второй группе - сплавы с точкой плавления до 1100'{золотые сплавы); к третьей группе - сплавы с точкой плавления выше 1200° (нержавеющая сталь, хромокобальтовые сплавы и т.д.). Плавление сплавов первой группы осуществляется в металлической ложечке над пламенем спиртовой или газовой горелке. Для плавления сплавов второй и третьей группы требуется специальнаяаппаратура, позволяющая достичь высокой температуры.
Наиболее простым плавильным аппаратом, применяемым также для прогрева металлических деталей и паяния, является бензиновыйпаяльныйаппарат.
Аппарат состоит из автоматического компрессора, рассчитанного на непрерывную работу при определенном давлении.При увеличении давления в воздушном резервуаре компрессора нагнетатель. В состав паяльного аппарата входит бачек для бензина (карбюратор), горелка (пистолет), соединенных рези-овыми шлангами. Воздух из компрессора попадает в карбюратор, где, проходя через бензин в виде мелких пузырьков,насыщается его парами, и поступает в горелку. Горелка устроена таким образом,что струя насыщенного бензином воздуха проходит через регулировочный кран и
металлическую сетку.Это позволяет регулировать силу подачи воздуха и менять форму пламени горелки. Металлическая сетка предохраняет засасывание пламени по шлангу в карбюратор, и, следовательно, предотвращает взрыв бензина. Бензи н в бачек следует наливать только половину объема, так как при б )льшем его количестве из горелки будут выбрасываться капли бензина.
Пламя бензинового аппарата имеет температуру 1200°.
Более высокую температуру можно получить с помощью вольтовой дуги.
Аппарат для плавки вольтовой дугой состоит:
1.Из ручного щитка с приспособлением для удержания углей, снабженный регулирующим винтом для сближения и раздвиж-ёйия углей.
2.Угольные прожекторные электроды 12-16 мм в диаметре.
3.Трансформатор силовой 3-5 KV.
Собранные по схеме детали позволяют при сближении углей получить пламя с температурой до 3000°. Плавку следует вести пламенем, не касаясь металла углями, чтобы не науглеродить металл. Отливать рассплавленный металл необходимо немедленно, т. к. он может вскипеть или сгореть.
Недостатком плавления металлов открытой вольтовой дугой является науглероживание металла и трудность определения режима плавки.
Для устранения этих недостатков были предложены аппараты Д. Н. Цитриным и И. П. Корнеевым.
Основу этих двух аппаратов составляет электрическая печь с находящимися внутри огнеупорным цилиндром из керамики. Между керамическим цилиндром и металлическим каркасом печи прокладывают огнеупорную изоляцию из асбеста. Внутрь керамического цилиндра вводят угольные электроды, засыпают крептолом - мелкими кусочками графита - и вставляют огнеупорным тигель для помещения и расплавления в нем сплава.При включении тока между кусочками графита возникают вольтовы микродуги, выделяется много тепла, что ведет к нагреву тигля и расплавлению в нем сплава.
Упомянутые аппараты являются одновременно и аппаратами для литься сплавов. Разница в том, что у аппарата Цитрина литье осуществляется с помощью вакуум-насоса у аппарата Корнеева -центробежной силой.
Металлический корпус печи Корнеева изготовлен из листовой стали толщиной 2,5 см, толщина дна и крышки 5 см. Внутри корпуса на асбестовой прокладке для термоизоляции помещается высокоогнеупорная магнитная футеровка, изготовленная из двух половинок. В цилиндрическое рабочее пространство печи, образуемое половинками футеровки, вводят два угольных электрода и огнеупорный тигель. Пространство между футеровкой и тиглем засыпают мелкими кусочками графита.
Сверху печь обмазывают той же огнеупорной магнезитовой массой и закрывают крыщкой, крепящейся на корпусе замками накидного типа.
Крышка имеет отверстие с уступом, куда вставляют металлическую опоку, в которой были заформованы восковые модели для отливки. Опоку крепят крышкой, перемещаемой винтом и укрепленные на подвижной рамке.
В нижней части орпуса находится вывод угольныхэлектр-дов, на которые насаживаются в процессе плавки провода, идущие от штепсельной колодки. Печь устанавливают на полуосях, опирающихся на шарикоподшипники, помещенные в двух литых чугунных стойках. На правую удлиненную полуось насажено на шпоньке малое зубчатое колесо, оно сцепляется с большим зубчатым колесом (передаточное соотношение 3:5),вращающееся с помощью рукоятки.
Вся печь монтируется на устойчивой поставке,внутри которой скрыт трансформатор. Снаружи справа располагается кожух переключателя ПК-2- 60/42, дающий возможность регулировать величины рабочего напряжения(30 V; 45 V; 70 V; 90 V) Электрощит с измерительными приборами крепится на стене.
Для изготовления тиглей из огнеупорной массы создается специальный металлический штамп, состоящий из двух половин. В отверстие дна штампа накладывают огнеупорную массу, утрамбовывают, затем вставляют срединный стержень и им формируют полость тигля. Затем форму разнимают,тигельпомеща-ют в муфельную печь для просушки на 2 часа при температуре 300 - 400 С, а затем обжигают тигель при температуре 1200-
1400°С 20 минут.
В состав огнеупорной тигенной массы входит 30% корунда N 325; 30% электрокорунда N 100; 40% шамотной глины. Эту массу замешивают на жидкости, состоящей из 90% воды и 10% отработанного машинного масла.
Разработана высокочастотная печь для плавки металла конструкции В. Ю. Курляндского.
Сущность метода индукционного нагрева токами высокой частоты заключается в том, что расплавляемый металл помещается в электромагнитное высокочастотное поле индуктора. При этом в слитке металла индруктируются переменные токи, называемые вихревыми токами высокой частоты, плотность которых неравномерна по сечению. В связи с большой плотностью индуктивных токов на поверхности слитка происходит быстрый нагрев и расплавление металла.
Чем меньше частота тока, тем глубже его проникновение внутрь слитка. К токам высокой частоты относятся переменные токи частотой от 500 до 10000000 гц(обыкновенный ток городской сети имеет частоту 50 гц). Токи высокой частоты получают от высокочастотных генераторов.
Литье может проводится как в специальных литьевых аппаратах, так и в аппаратах, осуществляющих плавку и литье.
Для того, чтобы металл заполнял полость формы, образующейся после выплавления воска, следует создать давление на металл. В зависимости от характера получаемого давления на металл различают следующие методы литья:
а) литье под давлением;
б) центробежное литье; в)вакуумное литье.
Литье под давлением и центробежное литье основаны на создании давления на металл извне, и это литье дает более плотные отливки, исключает пористость, недоливки, усадочные раковины.
Вакуумное литье основано на создании отрицательного давления внутри формы.Это способствует удалению пузырьков газа из полости формы, что предупреждает образование пор. Но при этом получают менее уплотненные отливки.
Наиболее простым аппаратом для литься является аппарат ЗольбригПлатшека. На подставке одновременно крепится кольцо для установки опоки и подвижная рукоятка с крышкой. В крышку закладывается влажный асбест.В момент расплавления металла(плавка ведется паяльным аппаратом или вольтовой дугой) опока плотно накрывается крышкой. Пар, образовавшийся при соприкосновении влажного асбеста с расплавленным металлом, создает повышенное давление, под действием которого металл по литниковым каналам загоняется в полости формы.
Широкое распространение получило центробежное литье.Существует много систем аппаратов для литья,построенных на действии центробежной силы. Наиболее простым является ручная центрифуга. В деревянной ручке укреплен неподвижно металлический стержень. На нем крепится подвижная петля, к которой прикрепляется стальная проволока 4-5 мм толщиной и 20 см длиной. К свободному концу проволоки подвижно прикрепляется проволочная дуга,спаянная концами с подставкой для опоки. Металл плавится в воронке оп-оки и центрифуга приводится во вращение. Необходимо произвести 15-20 оборотов, чтобы затвердение металла происходило под давлением. По этому принципу построена и ручная коромысловая центрифуга, печь-Корнеева.
Д. Н. Цитрин предложил аппарат, устроенный по принципувсасывания металла по литниковым системам в результате создаваемого в форме отрицательного давления. Крышка, укрепляющая опоку, сообщается посредством резиновой трубки с зажимом баллона из которого выкачивается воздух.Опока устанавливается над тиглем печи, когда металл расплавляется, открывают зажим на резиновом шланге. Вследствиесоздавшегося давления через поры формовочной массы металл всасывается в полость формы.
В НИИЭХАИ разработана автоматическая центрифуга для литья деталей зубных протезов. Центрифуга состоит из основания, механизма вращения с пусковым рычагом, защитного кожуха, подставки, сменных частей: коромысла, кювет, кюветодержателей и тиглей. Заливка расплавленного металла происходит под действием центробежной силы, возникающей при вращении двух спиральных пружин с ручным заводом. Минимальная скорость вращения коромысла от 350 до 600 об./мин. Пуск центрифуги происходит с помощью пускового рычага, поднимаемого кверху. Вращаясь, подвижное плечо коромысла с кюветой и с тигледержателем выпрямляется и создает дополнительное давление на расплавленный металл.
На втором плече коромысла имеется перемещающийся груз. |
Перемещение |
|
груза осуществляется по линейке с делениями, |
|
|
что позволяет сбалансировать коромысло с точностью |
и закрепить |
|
груз в необходимом положении. |
|
|
Плавка металла осуществляется ацетиленовой горелкой, вольтовой |
||
дугой или паяльным аппаратом. |
|
|
На Западе почти каждая фирма, выпускающая материалы (сплавы) для |
||
ортопедической стоматологии, выпускает и фирменные |
аппараты |
для |
расплавления и литья металлов и сплавов. |
|
|
Фирма «Degusa» (Германия) выпускает компактную высокочастотную линейную печь для расплавления и литья любых стоматологических сплавов. В комплект входят керамически тигли.
Фирма Hammacher предлагает следующие виды плавильных аппаратов: 1. Установка HFS 1,6 Export - установка для плавки и литья металлов и сплавов простого исполнения с ручным управлением с двумя режимами
нагрева (малая и полная мощность) Наиболее пригодна для |
работы в |
небольших производственных помещениях. Максимальные массы |
отливок: |
сплав кобальта - 40 г; золота - 80 г. |
|
2.Установка HFS 1,6 Muniterm - установка для высокочастотной плавки и центробежного литься для использования в небольших лабораториях. Применено микропроцессорное управление.Возможно литье в обычной воздушной атмосфере или в атмосфере инертного газа. Имеется инфракрасный спектральный пирометр Имеет 2 стержня нагрева. Максимальная масса отливок из сплава кобальта - 40 г; сплава золота - 80 г.
3.Установка HFS 3 Standard - предназначена для высокочастотной плавки
ицентробежного литья всех стоматологических сплавов универсального применения. Микропроцессорное управлениебесступенчатое регулирование момента вращения центробежного механизма, 2 ступени нагрева. Литье возможно в обычной воздушной атмосфере или в атмосфере инертного газа.Возможен дизайн по индивидуальному заказу. Максимальная масса отливок из сплава кобальта - 60 г; сплава золота -100г.
4.Установка HFS 3 Vacuterm - установка для высокочастотной плавки и центробежного литья. Применима для всех стоматологических сплавов. Плавка в атмосфере инертного газа или полном вакууме, что обеспечивает полное, отсутствие окисления металла. Микропроцессорное управление. Возможен монтаж с муфелем любого типа и размера. Максимальная масса отливок:из сплава кобальта - 60 г;из сплава золота - 100 г.
5.Vacutherm 3,3Titan - установка для высокочастотной плавки и центробежного литья универсального применения для всех стоматологических сплавов, драгоценных металлов, сплавов титана и чистого титана. Применяется метод выплавляемых восковых моделей с применением специальных тигельных систем и технологии формирования литейных оболочек,которые специально разработаны фирмой LinnMighTherm. Микропроцессорное управление. Муфельные вставки любого типа и размера, двухступенчатый роторный вакуумный насос позволяет достигнуть вакуума

10мбар. Плавка титана может осуществляться в высокоочищенном аргоне. В комплект входят специальные тигли фирмы LinnMighTherm из керамики,графита, кварца различных размеров. Максимальная масса отливок: из сплава кобальта - 80 г; титан - 40 г.
Фирма Kulzer предлагает индукционно-вакуумную печь GL-IG.
В печах других фирм, например США, Японии, используются те же принципы, что и в описанных выше. Они отличаются,.в основном, дизайном, размерами, комплектующими (наличием или отсутствием тиглей, муфельных
вставок), различными нюансами в электронных системах |
слежения за |
процессом плавки и литья. |
|
Обработка отлитых металлических деталей. |
|
После процесса литья опоку охлаждают, осторожно удаляют гипсовым ножом или из маленьких опок выдавливают формовочную массу и освобождают от нее отлитые детали. При литье деталей из нержавеющей стали приходится наблюдать достаточно плотное приткание облицовочного слоя к металлу. В таких случаях для очистки деталей используют раствор кислоты или щелочи или прибегают к механической очистке металлической щеткой, фиксированной на моторе.
Очистка деталей из золота от остатка формовочной массы проводится повторным нагревом детали на паяльном аппарате и охлаждением в растворе соляной кислоты.
При использовании химического метода очистки необходимо соблюдать технику безопасности: работать в очках и резиновых перчатках при хорошей вентиляции и совершенно сухими щипцами и отливке, т. к. вода, попадая в расплавленную щелочь, мгновенно испаряется, что может привести к выбросу жидкости из ковша.
Очистка литья может быть произведена и в корундоструйном аппарате с использованием корундового абразива с величиной зерен 1 мм. Присоединенные пылесос и компрессор создают необходимые условия для очитки литься от огнеупорной массы.
Затем удаляют литники. У стальных и хромо-кобальтовых деталей это производится на моторе карборундовым или вулканито-вым диском.
Удаление литников у золотых деталей ведут очень осторожно, над вощеной бумагой, собирая все опилки. Литники обрезают надфилем или борами, или же ведут и обработку металла. Применять карборундовые камни при обработке золотых деталей не рекомендуется из-за опасности засорения крупинками карборундо-золотых опилок.
После данной обработки, детали передают технику, занимающемуся изготовлением бюгельного протеза.
Дефекты отлитых металлических деталей

Вид |
Характерн |
Причины |
|
|
дефекта |
ые |
возникновения |
||
|
признаки |
дефекта, методы их |
||
Усадочны |
Пористая, |
1.Отсутствие; Недостаточ- |
||
е |
неровная |
ная по объему противо- |
||
раковины |
поверхность или |
усадочная« муфта»,а также |
||
в области |
углубление |
расположение ее от детали |
||
литника. |
неправиль ной |
более, чм на 2,0-2,5 мм. |
||
|
формы с ровными |
2.Тонкий |
|
|
|
краями. |
лнтникообразующий |
||
|
|
|
штифт. |
|
Усадочны |
Углубление |
Недостаточное |
||
е |
неправильной |
количество |
|
|
раковины |
формы с ровными, |
литейн.каналовприотливк |
||
на разных |
лладкими краями, |
еразнообъемной по |
||
участках |
но шероховатой |
протяженности детали. |
||
Газовые |
Углубление |
Выделение паров веществ |
||
раковины |
округлой формы с |
из формы во время литья |
||
на |
гладкой |
вслед ствии |
|
|
разных |
поверхностью. |
недостаточного удаления |
||
участках |
|
|
воска и влаги из формы |
|
Недолив - |
1 участках |
1.Мал диаметр |
||
неполное |
недолива |
литникового канала, |
||
заполнение |
акругленные углы [ |
малое количество |
||
формы |
грани с гладкой |
металла. 2.Неравномерное |
||
металлом. |
|
|
ние металла. 3.Низкая |
|
|
|
|
температура |
|
|
|
|
кюветы. 4.Засорение |
|
|
|
|
литникового |
|
|
|
|
канала. 5.Засорение формы |
|
|
|
|
при |
|
|
|
|
извлечении штифта |
|
|
|
|
крупинками формовочного |
|
Холодный |
На поверхности |
|
То же что,при недоливе |
|
спаи |
линия |
|
|
|
(стык). |
;вух потоков |
|
|
|
|
металлов С |
|
|
|
|
закругленными |
|
|
|
|
|
|
||
Прибыли. |
Зыступыокругл.фор |
1.Поры в облицовочном |
||
'. |
- |
|
|
|
|
мы или различной |
|
слое. |
|
|
толщине и |
|
2.Трещины |
в облицовоч- |
|
ности |
|
ном слое, |
образовав- |
|
.шероховатости. |
|
шиеся вследствие |
|
|
|
|
быстрого подъема |
|
|
|
|
|
|
Шлаковые |
Неправильной |
|
1 .Перегрев металла выше |
|
|
формы |
|
|
|
раковины. |
раковины с |
|
точки кипения с обра- |
|
|
краями. |
|
зованием различных |
|
|
|
|
окислов. 2. Попадание в |
|
|
|
|
форму буры. |
Физико-механические, химические и технологические свойства сплава определяются его составом, структурой и характером связи компонентов.
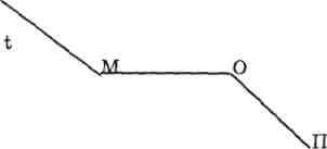
Четкая структура сплава формируется при кристаллизации из расплава. Расплавленный металл заполняет литейнуюформу и постепенно затвердевает с образованием кристаллической решетки. Этому способствует некоторое уменьшение объема отливки или усадки.
Затвердевание всегда начинается с поверхности.Кристаллы растут и располагаются перпендикулярно к охлаждаемой поверхности Скорость затвердевания в утолщенных местах отливки меньше, чем в тонких сечениях, где металл затвердевает раньше. Расплавленный металл оттягивается к участкам с более быстрой кристаллизацией и дает там более мелкокристаллическую структуру. В утолщенных местах образуется крупнозернистая структура. Вследствие недостатка металла в них могут образовываться усадочные раковины, возникающие обычно в верхней части отливки. Усадка металла может привести к внутренним напряжениям в отдельных частях отливки.
Усадочные раковины, внутренние напряжения, крупнозернистая структура сплава ухудшают механически показатели и антикоррозионные свойства.Борьба с этими нежелательными явлениями ведется в различных направлениях:
1)введение в состав сплава добавок, способствующих образованию мелкокристаллической структуры;
2)соблюдение температурного режима плавки и скорости охлаждения; 3)создание депо металла в- питательных муфтах за пределами отливки. Э. Я. Варес раскрывает следующие механизмы усадки.
Энергия взаимодействия атомов, составляющих кристаллы,является минимальной. Под действием тепла возрастает энергия взаимодействия атомов в кристаллической решетке и расстояние между ними увеличивается.
В связи с этим происходит объемное расширение металла, достигающее максимума в стадии расплавления. При охлаждении металла утрачивается поступившая дополнительная тепловая энергия и происходит обратный процесс, получивший название усадки.
Под литейной усадкой принято понимать уменьшение объема металла при охлаждении до температуры окружающей среды от температуры охлаждения. Основу усадки составляет сжатие, сопровождаемое фазовыми переходами. Различают три стадии понижения температуры и соответствующей им стадии фазового превращения. К
Рис.1 График трех стадий понижения температуры
расплавленного металла при охлаждении до температуры окружающей среды.
При понижении температуры от точки К до точки М (рис.1) происходит усадка металла в жидком состоянии. В этот момент внешние размеры отливаемой детали не уменьшаются, потому что по литнику свободно поступает металл, компенсирующий уменьшающийся объем отливки при построении первых кристаллов.
При температурном режима от точки М до точки О происходит усадка металла в процессе отверждения, а температура при этом фактически не снижается потому, что при формировании атомов в кристаллическую решетку происходит усиленная отдача тепла. На этой стадии происходит объемная усадка и могут образоваться полости внутри отливки. Объясняется это таким способом. Первые центры кристаллизации, т. е. отвердение, начинается с периферии в местах соприкосновения со стенками формы. В этих участках возникает твердая корковая зона, кристаллы которой притягивают к себе подвижные атомы. Внутри создается разрежение. Если в центральную часть отливки в этот момент поступают новые порции расплавленного металла, то возникающее разряжение компенсируется, иотливка может быть монолитной, если металл не поступает, то возникают значительные усадочные полости и раковины, суммарный объем которых равен объему усадки металла на этой стадии. На процесс образования усадочных раковин значительное воздействие оказывает первоначальные температура,формадиаметр литника, наличие депо металла, близость его расположения и скорость охлаждения отливки. Замедляя процесс охлаждения отливки, можно добиться (в интервале отвердевания) образования усадочных микропор по всей отливке (исключая корковую зону) без концентрации их в определенном участке.
Усадку металла на стадии отвердения можно компенсировать путем установки литников большого сечения и близким расположением «депо» металла при условии заливки расплавленного,но не перегретого металла в горячую форму. Заливку металла в холодные формы при изготовлении зубных протезов с технологических позиций следует считать недопустимой.
Различают зональную и рассеянную усадочную пористость. Зональная сосредотачивается восевых частях тепловых узлов, рассеянная распределяется по всему объему отливки. На возникновение пористости может влиять выделение газов, которые располагаются по всему объем отливки между кристаллами, и значительное давление. Поэтому пористость, в ряде случаев, имеет газовый характер. На возникновение пористости влияет скорость выхождения воздуха из формы через стенки формы-«рубашки».
Усадочные раковины в теле отливки образуются вследствие некомпенсированной объемной усадки при затвердении металла. Различают внутренние и наружные раковины. Внутренние образуются, как правило, в
тепловых узлах, наружные на поверхности или под тонкой коркой у поверхности металла.
При изменении температуры от точки О до точки П в третьей стадии происходит усадка в твердом состоянии.Объясняется это следующим образом. При первоначальном построении кристаллов атомы в кристаллической решетке хотя и занимают равновесное положение,но располагаются на значительном расстоянии друг от друга. При охлаждении они сближаются, поэтому объем каждого кристалла уменьшается. При этом, в отличии от первых двух стадий, происходит не объемная» а линейная усадка, которая приводит, как правило, к уменьшению длины промежуточной части мостовидных зубных протезов.
Таким образом, линейная усадка - это объективно существующая закономерность уменьшения объема металла при переходе из расплавленного состояния в твердое, и выражается она тремя явлениями: усадочными раковинами, усадочной порн-стостью и линейной усадкой.
Существенное правило технологии изготовления цельнолитых зубных протезов отлитая поверхность протеза должна быть настолько чистой, чтобы не было необходимости ее обрабатывать абразивными камнями и снимать корковый слой с тугоплавкими компонентами и мелкозернистой структурой.Моделирование и создание гладкой поверхности у первоначальной формы заготовки должно быть выполнено на высоком уровне. При этом недопустима традиционно сложившаяся у зубных техников привычка «прибавки на обработку».
Из вышесказанного видно, что устранить усадку, как объективное явление, невозможно, но можно использовать способы, обеспечивающие точность отливки формы.
Второе правило: использование форм, в которую производят отливку, непрямолинейного типа: г-образных, т-образных, кольцеподобных, т.е. затрудняющих усадку.
Третье правило:использование в качестве моделировочных материалов акриловые пластмассы. Проведенные исследования дают основание утверждать,что пластмассовые материалы превосходят восковые по требованиям, предъявляемым к моделировочным материалам, прочности, твердости, теплостойкости, имеют меньшую зонность и удовлетворительную стойкость к связующему раствору формовочных масс.
Акриловые пластмассы по своим физико-химическим требованиям наиболее полно отвечают требованиям, предъявляемым к моделировочным материалам для получения цельнолитых конструкций по выжигаемым моделям. Процесс выжигания акриловых заготовок должен проводится при медленном подъеме температуры в муфельной печи, чтобы не наступило разрыва огнеупорной «рубашки» вследствие быстрого расширения акриловой заготовки, возможно создание в пластмассовых заготовках «технологических окон», заполненных воском. Воск выплавляется раньше, и создает место для расширения акриловой пластмассы. Или пластмассовые заготовки покрывают