
Сборник 70 студ конференции БГТУ
.pdf561
Окись углерода является основным вредным газом, содержащемся в ваграночных выбросах. В настоящее время единственным промышленным способом очистки газов от CO является их дожигание. При ваграночной плавке этот процесс иногда происходит самопроизвольно в трубе вагранки и на уровне завалочного окна, где газы смешиваются с кислородом воздуха, попадающего через завалочное окно. Однако этот процесс не стабилен. Для стабилизации горения в зоне завалочного окна или выше устанавливаются горелки природного газа, являющиеся запальником смешанных ваграночных газов с воздухом, поступающим через окно. Но и этот метод не обеспечивает надёжного дожигания СО. Наиболее надёжным считается отсос ваграночных газов ниже завалочного окна и подача их в предварительно разогретую природным газом топку. Устойчивое горение поддерживается за счёт постоянно сжигаемого природного газа.
Выделяющееся при дожигании газов тепло может быть использовано для подогрева дутья.
Современные ваграночные установки включают комплекс оборудования, агрегатов и узлов, обеспечивающих очистку отходящих газов от пыли, СО и других вредных составляющих.
Работа выполнена под руководством проф.кафедры"Машиностроение и материаловедение" В.И.Хенкин
М.В. Малышева ВЛИЯНИЕ ВАНАДИЯ НА СВОЙСТВА КОНСТРУКЦИОННЫХ
НИЗКОУГЛЕРОДИСТЫХ СТАЛЕЙ
Объект исследования: ванадийсодержащая конструкционная сталь. Результаты, полученные лично автором: проведен объективный анализ
влияние ванадия на свойства конструкционных низкоуглеродистых сталей.
Ванадий относится к тугоплавким металлам (Тпл - 1735 °С) и применяется в основном для легирования высококачественных конструкционных сталей. Даже малое количество ванадия, добавленное при варке стали, значительно повышает коррозийную устойчивость и механические свойства сталей.
Одним из основных типов стали, при легировании которых применяется ванадий, является конструкционная сталь для изделий средних и крупных размеров, работающих со знакопеременными нагрузками.
Второй тип стали, содержащей ванадий — инструментальная сталь, к которой предъявляется требование сохранения твердости при повышенных температурах. К числу наиболее важных сталей этого типа относятся быстрорежущие стали, содержащие от 1 до2%V.
Ванадий как новый материал с особыми свойствами приобретает самостоятельное значение позднее других тугоплавких, химически активных металлов переходной группы. Это в значительной степени объясняется особенностями физических свойств ванадия, которые создают чрезвычайно большие технические трудности при получении ковкого металла.
Ванадий повышает прочность феррита примерно в такой же степени, как и вольфрам. Влияние же ванадия на твердость и предел прочности
562
отожженной и нормализованной стали незначительно. Вследствие связывания углерода и азота твердость и прочность стали с небольшим содержанием ванадия даже уменьшаются. Ванадий не удаляет кислорода; поэтому добавка ванадия в ковш позволяет получить кипящую мягкую сталь
схорошим качеством поверхности.
Вулучшаемых сталях, применяемых для работы при низких температурах, малые добавки ванадия могут оказывать благоприятное влияние, так как они способствуют измельчению зерна и повышению вязкости; в то же время ванадий при повышенном содержании может влиять неблагоприятно, так как выделение его карбидов при определенных условиях отпуска приводит к ухудшению вязкости. Однако карбид ванадия имеет особое значение для работы стали при высоких температурах.
Выводы о влиянии ванадия в углеродистой стали могут быть распространены и на сталь, легированную многими элементами. Влияние ванадия в значительной степени зависит от того, был ли растворен карбид ванадия при температуре закалки. Но при ее повышении вследствие выделения карбидов при отпуске сравнительно сильно снижается ударная вязкость. Легирование ванадием устойчивой против отпускной хрупкости хромомолибденовой стали также вызывает дальнейшее улучшение устойчивости против хрупкости в случае повышения температуры закалки.
Работа выполнена под руководством доц. каф. «Машиностроение и материаловедение» В. Г. Солдатова
А.А. Осипов СРАВНИТЕЛЬНЫЕ ХАРАКТЕРИСТИКИ ПРОЦЕССОВ С
ИСПОЛЬЗОВАНИЕМ ХОЛОДНОТВЕРДЕЮЩИХ СМОЛ
(«NO-BAKE»-ПРОЦЕССОВ)
Объект исследования: характеристики процессов с использованиемхолоднотвердеющих смол.
Результаты, полученные лично автором:предложена методика экспертной суммарной оценки в баллах качественных характеристик процессов.
Процессы изготовления форм и стержней на основе синтетических холоднотвердеющих смол применяемых в мелкосерийном и серийном производстве отливок из всех видов литейных сплавов.
«NO-BAKE»-процессы получают всё большее распространение. Их основные преимущества по сравнению с изготовлением форм и стержней из песчано-глинистых смесей следующие: универсальные возможности при изготовлении любых отливок, простые методы регулирования технологических свойств, относительно низкие цены на смолы и катализаторы, возможности использования несложного технологического оборудования в механизированных линиях, хорошие антипригарные свойства, хорошая выбиваемость, высокий выход качественного регенерата при сухой механической регенерации.

564
Проанализировав современные процессы по перечисленным свойствам, можно сделать вывод, что наиболее предпочтительным является альфа-сет- процесс.
По этой методике могут быть оценены все другие характеристики и все существующие процессы, не рассмотренные в данной работе.
Работа выполнена под руководством проф. каф. «Машиностроение и материаловедение» Хенкина В.И.
И. С. Плюсова АНАЛИЗ ДЕФЕКТОВ ШВОВ СВАРНЫХ КОНСТРУКЦИЙ
Объект исследования: сварной шов.
Результаты, полученные лично автором: проведен анализ дефектов сварных соединений.
Дефектами сварных швов называются различные отклонения от требований чертежа и технических условий, ухудшающие качество сварного соединения: его механические свойства, сплошность, герметичность и пр. По месту расположения в шве дефекты могут быть внешними и внутренними.
Швы с внешним дефектом имеют плохой внешний вид; неравномерное распределение и усадка наплавленного металла шва могут вызвать деформации и напряжения. Выявляется дефект наружным осмотром и проверкой шва шаблоном; отклонения могут устраняться зачисткой с подваркой шва и срубанием излишка металла.
Наружные трещины могут быть в наплавленном и основном металле. Причинами образования трещин являются: напряжения, возникшие вследствие неравномерного нагрева и охлаждения, изменения структуры металла при сварке, повышенное содержание серы, фосфора, влияние водорода. Появлению трещин способствуют такие дефекты, как поры, непровары, включения шлака. Трещины появляются также при кристаллизации металла в процессе сварки. Возможность образования трещин тем больше, чем хуже сваривается данный металл. Участки швов с трещинами полностью вырубают или удаляют поверхностной кислородной (или воздушно-дуговой) резкой и заваривают вновь.
Подрезы — уменьшение толщины основного металла в месте перехода к наплавленному. Этот дефект возникает при сварке излишне большим током или горелкой большой мощности. Подрезы устраняют дополнительной зачисткой и заваркой.
Незаплавленные углубления (кратеры), остатки шлака и неровная поверхность шва являются следствием недостаточной квалификации сварщика или небрежного выполнения сварки. Дефектные участки следует вырубать или вырезать до основного металла и заваривать вновь.
Наплывы образуются при слишком быстром плавлении электрода и натекании жидкого металла на недостаточно нагретую поверхность основного металла. Наплывы необходимо срубать или вырезать и проверять, нет ли в этом месте непровара.
565
К внутренним дефектам сварных соединений относят поры, шлаковые включения, непровары, несплавления и трещины.
Поры образуются вследствие поглощения расплавленным металлом водорода, окиси углерода и др., которые не успевают выделиться при застывании металла и остаются в нем в виде газовых пузырьков. Пористые швы при газовой сварке уплотняют проковкой при соответствующей температуре нагрева. Если шов должен быть плотным, то пористые участки вырубают до основного металла и вновь заваривают.
Шлаковые включения и окислы ослабляют сечение шва. Они образуются при сварке длинной дугой и окислительным пламенем. Одиночные шлаковые включения и поры обычно не снижают механических свойств соединения. Цепочки и особенно скопления пор и шлаковых включений приводят к концентрации напряжений в данном месте и резкому снижению пластичности, вязкости и прочности наплавленного металла.
Непровар корня шва выражается в несплавлении наплавленного и основного металла в корне шва. Непровар резко снижает прочность шва, и соединение становится ненадежным. В местах непровара концентрируются напряжения, которые еще более понижают сопротивляемость шва внешним нагрузкам, особенно ударным. При динамических нагрузках, а также в изделиях ответственного назначения наличие непроваров недопустимо.
Причинами непровара являются: недостаточный ток или малая мощность горелки; слишком быстрое перемещение электрода и горелки; попадание в шов пленки окислов или слоя шлака; неудовлетворительная зачистка кромок. Если по техническим условиям данное изделие не должно иметь непровар, то места швов, где имеется непровар, вырубают или удаляют поверхностной резкой, после чего шов в этом месте заваривают вновь.
Непровар кромки образуется: при сварке током недостаточной величины или пламенем малой мощности; при слишком быстром перемещении электрода или пламени вдоль свариваемого металла. Обнаружить непровар кромки можно просвечиванием шва рентгеновскими или гамма-лучами. Дефектный участок шва удаляют вырубкой или поверхностной резкой и повторной заваркой.
При перегреве металл имеет крупнозернистое строение. Чем крупнее зерна, тем меньше поверхность их сцепления и ниже прочность и пластичность металла. Этот дефект можно исправить соответствующей термической обработкой.
Пережог характеризуется наличием в структуре металла шва окисленных зерен, обладающих малым взаимным сцеплением. Пережженные участки шва полностью удаляют поверхностной резкой и заваривают вновь.
Дефектами микроструктуры сварного соединения являются: микропоры и микротрещины, нитридные, кислородные и другие неметаллические включения, крупнозернистость, участки перегрева и пережога.
На участке перегрева металл имеет крупнозернистое строение. Чем крупнее зерна, тем меньше поверхность их сцепления и выше хрупкость металла (перегретый металл плохо сопротивляется ударным нагрузкам).
566
Наиболее опасным дефектом является пережог, при котором в структуре металла шва много окисленных зерен с малым взаимным сцеплением. Такой металл хрупок и не поддается исправлению. Пережог возникает при высокой температуре сварки, плохой изоляции сварочной ванны от воздуха или избытке кислорода в пламени горелки.
Работа выполнена под руководством доц. каф. «Машиностроение и материаловедение» В. Г. Солдатова
А. А. Полторухо МЕТОДИКА ОПРЕДЕЛЕНИЯ И
ВЗАИМОСВЯЗЬЭКСПЛУАТАЦИОННЫХ СВОЙСТВ ДЕТАЛИ «БАЛКА НАДРЕССОРНАЯ» С МЕХАНИЧЕСКИМИ ХАРАКТЕРИСТИКАМИ МАТЕРИАЛА
Объект исследования: деталь «Балка надрессорная».
Результаты, полученные лично автором: проведен объективный анализ эксплуатационных свойств детали «Балканадрессорная».
«Балка надрессорная» - несущая деталь ответственного назначения тележки грузового вагона, к которой предъявляется целый ряд требований, регламентируемых нормативной документацией.Механические свойства материала «Балки надрессорной» – предел текучести, временное сопротивление, относительное удлинение и относительное сужение. Числовые значения этих свойств регламентированы ГОСТом. Методики определения стандартные – на образцах.
Эксплуатационные свойства– сопротивление усталости, хладостойкость и износостойкость.Хладостойкость определяется по испытаниям образцов на ударную вязкостьKCV-60при пониженной температуре (-60 °С), значение которой регламентировано ГОСТом.
Основным видом повреждения данных деталей при эксплуатации является развитие трещин усталости. Причиной появления трещин является относительно высокий уровень статических и динамических напряжений, несоответствие уровня и количества циклов номинальных рабочих напряжений, наличие литейных дефектов в наиболее опасных зонах детали.
Проблема: поиск основных характеристик сопротивления материала усталости в зависимости их от эксплуатационных, конструкционных, технологическихфакторов.
Если подвергнуть испытанию на выносливость серию специальных образцов, подобных какой-либо конкретной детали, т. е. отличающихся от нормальных образцов наличием концентратов напряжений, абсолютными размерами, качеством обработки поверхности (или только некоторыми из перечисленных факторов), то, как правило, при одном и том же материале нормальных и специльных образцов предел выносливости, определенный при испытании последних, ниже.
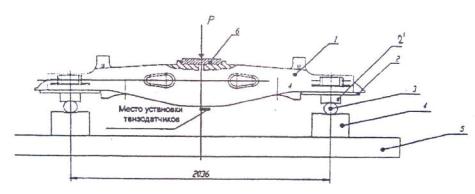
567
Таким образом, установлено, что пределы выносливости конкретной детали и материала, из которого она изготовлена, различны. Величины различных факторов, влияющих на пределы выносливости, определены при испытаниях в условиях симметричных циклов изменения напряжении.
Наиболее распространенным методом определения сопротивления усталости – предела выносливости (ГОСТ 25.502-79) является испытание серий одинаковых образцов (не менее 10 шт.): на изгиб, кручение, растяжение-сжатие или в условиях комбинированного нагружения (последние два режима для имитации работы материала при асимметричных циклах нагружения или в условиях сложного нагружения).
Оценка сопротивления усталости целой детали.
Первый способ - это использование общего коэффициента снижения предела выносливостиKд, который учитывает влияние различных факторов. Таким образом, предел выносливости детали σ-1дзависит от предела выносливостиσ-1материала, из которого изготовлена деталь:
σ-1д = σ-1/Kд.
Второй способ. Реальные условия экплуатации не ограничиваются симметричными циклами нагружения. Они в большинстве своем ассиметричные, т. е. максимальные и минимальные напряжения цикла принимют различные значения. Всвязи с этим фактом ОАО «ВНИИЖТ» и ОАО «НИИ вагоностроения» разработали методики испытаний на усталость для деталей железнодорожного транспорта «Балки надрессорной» и «Рамы боковой» (рис. 1).
Рис. 1. Схема нагружения:
1 – балка надрессорная, 2 – фасонная плита, 2’ – опорный элемент, 3 – цилиндр, 4 – опорная тумба, 5 – стол стенда, 6 - вкладыш
Объектами испытаний служат именно литые стальные балки и боковые рамы. Испытания проводят на стендах с гидропульсаторными или электрогидравлическими силонагружающими установками. Каждую деталь испытывают при ассиметричном цикле нагружения до разрушения или достижения базового числа циклов. В экспериментальные результаты испытаний входят:
- для полных ускоренных испытаний – параметры кривой выносливости детали;
568
- для сокращенных ускоренных испытаний – число циклов до появления трещины и до разрушения или потери несущей способности детали при одном заданном режиме нагружения.
Общий результат – заключение о соответствии деталей установленным в нормативной документации на «Балкинадрессорные» и «Рамы боковые» требованиям к показателям сопротивления усталости.
Работа выполнена под руководством доц. каф. «Машиностроение материаловедение и» В. Г. Солдатова
В. С. Потапов АНАЛИЗ ВАРИАНТОВ ПОЛУЧЕНИЯ СТЕРЖНЕЙ НА
ОБОРУДОВАНИИ ФИРМЫ LAEMPE
Объект исследования: процессы получения стержней.
Результаты, полученные лично автором: проанализированы преимущества и недостатки различных процессов изготовления стержней на машинах фирмы Laempe.
В последнее десятилетие пескодувные (пескострельные) машины существенным образом изменились как конструктивно, так и по своему технологическому назначению. Жесткие требования по качеству поверхности и геометрической точности отливок, а следовательно, форм и стержней, привели к созданию новых технологий с использованием пескострельного процесса.
Примером пескострельных стержневых машин-автоматов, удовлетворяющим современным требованиям литейного производства, могут служить машины известной немецкой фирмы Laempe. Машины применяются на литейных заводам многих стран, в том числе и на заводе «Бежицкая сталь». Машины снабжены вихревым смесителем и газогенератором, и могут автоматически с помощью программного обеспечения реализовать следующие процессы изготовления стержней:
-Cold-box-amin-процесс (отверждение стержневых смесей с двухкомпонентным связующим из фенольной смолы и полиизоцианата при продувке амином);
-Beta-set-процесс (смесь с фенолформальдегидной смолой, отверждаемая парами метилформиата);
-SO2-процесс (смесь с фурановой или эпоксидной смолой, отверждаемой продувкой SO2);
-Resol-CO2-процесс (смесь с формальдегидной смолой, отверждаемой при продувке CO2);
-Hot-box-процесс (смесь на синтетических смолах, отверждаемая при нагреве);
При выборе процесса изготовления стержней для конкретных производственных условий следует проанализировать следующие факторы:
-технологические (прочность, текучесть, живучесть, выбиваемость, вероятность образования дефектов и др.);
569
-экономические (стоимость смесей и стержней, брак стержней, стоимость и стойкость оснастки и др.);
-экологические (объем газовыделений в «холодной» стадии процесса и при заливке, охлаждении и выбивке, возможность и стоимость захоронения отходов и т.д.).
Анализ имеющихся сведений показал, что по технологическим факторам Cold-box-amin-процесс обеспечивает высокую текучесть при заполнении оснастки, получение высокоточных стержней с высокой манипуляторной прочностью сразу после извлечения из оснастки, однако при этом процессе предъявляются высокие требования к качеству применяемых песков по влажности, стержни имеют плохую водостойкость при нанесении водных противопригарных покрытий, худшую выбиваемость по сравнению с другими процессами.
SO2-процесс превосходит аминный процесс по живучести смеси, прочности и влагостойкости стержней, выбиваемости.
Beta-set-процесс уступает процессам с продувкой аминном и SO2 по прочности стержней, но обеспечивает легкую выбиваемость.
Resol-CO2-процесс уступает другим по прочности стержней. Hot-box-процесс обеспечивает относительно высокую живучесть в
закрытом состоянии, хорошую выбиваемость стержней, особенно для отливок из цветных сплавов, высокую точность стержней. Однако точность стержней может уменьшаться при нагреве ящика в результате коробления.
По экономическим факторам производство стержней по Cold-box-amin- процессу приблизительно на 20% дешевле, чем Beta-set и SO2 процессам, Hot-box-процесс уступает холодным процессам из-за необходимости высоких энергетических затрат на нагрев ящика, из-за более высокой стоимости оснастки и необходимости её замены в связи с короблением при нагреве.
По экологическим факторам наименьшую токсичность обеспечивает Beta-set-процесс. Метод SO2 создает не самые лучшие условия труда на заливочных и выбивных участках из-за выделения в воздух сероводорода. Hot-box-процесс также создает неблагоприятные условия труда из-за выделения токсичных газов при отверждении стержней.
Из экспертных оценок современного уровня технологии производства стержней в индустриально развитых странах можно сделать вывод, что в общем объеме машинного изготовления стержней примерно 80% приходится на долю процессов холодного отверждения (Cold-box-процессов). В отечественном литейном производстве ещё велика доля изготовления стержней с тепловой сушкой в специальных сушилах и отверждение стержней в нагреваемой оснастке, но она постоянно уменьшается.
Если принять за 100% производство стержней в холодной оснастке, то доли разных процессов в индустриально развитых странах примерно распределяются так: с продувкой сернистым газом (SO2 процесс) 4…5%, метилформиатом (Beta-set-процесс) 3%, с продувкой CO2 (Resol-CO2) 10…12%, с продувкой амином (Cold-box-amin-процесс) 75…80%.
570
Таким образом, сравнение показателей рассматриваемых процессов по технологическим, экономическим и экологическим факторам позволяет сделать вывод о предпочтительности применения на машинах фирмы Laempe Cold-box-amin-процесса.
Целесообразность применения в отдельных случаях таких процессов, как Beta-set, Resol-CO2, SO2-процесс зависит от конкретных условий и решение принимается главным металлургом предприятия.
Работа выполнена под руководством проф. кафедры «Машиностроение и материаловедение» В. И. Хенкина
А. А. Преснякова ОСНОВНЫЕ ХАРАКТЕРИСТИКИ ЦИКЛИЧЕСКОГО НАГРУЖЕНИЯ
Объект исследования: характеристики циклического нагружения. Результаты, полученные лично автором: выявлены факторы, влияющие
на усталостные процессы.
Усталостью называют процесс постепенного накопления повреждений материала под действием повторных или повторно-переменных напряжений, приводящий к образованию трещин и разрушению. Важнейшей особенностью этого процесса является то обстоятельство, что он развивается при напряжениях, значительно меньших (в два и более раз), чем временное сопротивление, которое является мерой прочности при статическом нагружении. Другими словами, способность материала выдерживать повторно-переменные нагрузки, называемая выносливостью, существенно ниже статической прочности. Важно также, что разрушение в результате усталости во многих случаях не сопровождается заметной макродеформацией образца или детали, поэтому такое разрушение чрезвычайно трудно предупредить.
Основной характеристикой сопротивления материала усталостному разрушению является предел выносливости. Для определения его величины проводят испытание партии одинаковых образцов — не менее 10 штук. Существуют два способа испытания: либо его проводят при постоянном коэффициенте асимметрии цикла R, меняя от образца к образцу наибольшее по абсолютной величине напряжение цикла, либо поддерживают неизменным среднее напряжение цикла, изменяя амплитуду. В любом случае получают зависимость числа циклов N до разрушения образца от напряжения σ (максимального или амплитудного). Эту зависимость называют кривой Вёллера или диаграммой усталости. На диаграмме значения напряжений откладывают на оси ординат, а на оси абсцисс — логарифм числа циклов
LgN (рис. 1).