
Pivovarennaya_inzheneria_ / Глава 9
.pdf
ВСПОМОГАТЕЛЬНОЕ ОБОРУДОВАНИЕ СОЛОДОВЕННОГО И ПИВОВАРЕННОГО ... |
945 |
|
|
|
|
трубопровода, а при входе зубьев в зацепление — жидкость выдавливается из межзубного пространства и нагнетается в напорный трубопровод. Шестеренчатые насосы не требуют предварительной заливки перед пуском, так как способны откачивать воздух и создавать разрежение в корпусе.
Винтовые насосы. Принцип действия винтового насоса напоминает принцип действия шестеренчатого. Чаще всего винтовые насосы состоят из одного ведущего и двух ведомых винтов, находящихся в зацеплении с ведущим. При вращении винтов жидкость, находящаяся во впадинах нарезки, перемещается вдоль оси винта на расстояние равное шагу винта за один оборот. Давление, развиваемое винтовыми насосами, может достигать очень высоких значений (до 17,5 МПа), и зависит от числа шагов винтовой нарезки, а подача их не превышает 300 м3/ч. Винтовые насосы компактны, быстроходны, бесшумны и могут применяться для транспортирования очень вязких сред, но не содержащих твердых, особенно абразивных включений.
Разновидностью винтового насоса является одновинтовой или героторный насос, который может быть использован для транспортирования не только чистых, но и загрязненных взвесями жидкостей. Подача одновинтовых насосов не превышает 7 м3/ч, а развиваемое давление составляет 1,0–2,5 МПа.
Вихревые насосы конструктивно напоминают центробежные, однако принцип действия их существенно отличается. Роль центробежной силы в них минимальна, а основная часть создаваемого напора обеспечивается энергией вихрей, образующихся в жидкости при вращении рабочего колеса. Вихревые насосы предназначены для относительно невязких жидкостей, не содержащих твердые включения. Развиваемые ими напоры выше, чем у центробежных и достигают 250 м, а подача их обычно не превышает 40 м3/ч. В отличие от центробежных, вихревые насосы необходимо пускать при полностью открытой задвижке, так как при уменьшении подачи у них резко возрастают напор и потребляемая мощность.
* * *
Кроме рассматриваемых выше, промышленностью выпускаются и другие типы насосов, например, пластинчатые, лабиринтные и др., однако они практически не применяются
впивобезалкогольном производстве и поэтому в настоящей главе не описаны.
9.7.4.3.Трубопроводы
Для изготовления трубопроводов применяют трубы из различных материалов: металлов, полимеров, стекла, керамики, а также стальные трубы с различными внутренними покрытиями — гуммированные (покрытые резиной), футерованные полимерами (винипластом, полиэтиленом и др.) и эмалированные.
Впивобезалкогольной промышленности в зависимости от свойств транспортируемой среды и условий работы применяют в основном трубы из нержавеющих и углеродистых сталей, чугуна и стекла.
Впроцессе монтажа трубопроводов трубы соединяют между собой, с арматурой и с технологическим оборудованием различными способами, которые можно разделить на неразъемные и разъемные. К первым относят сварные, паянные и клеенные соединения, а ко вторым — фланцевые и резьбовые.
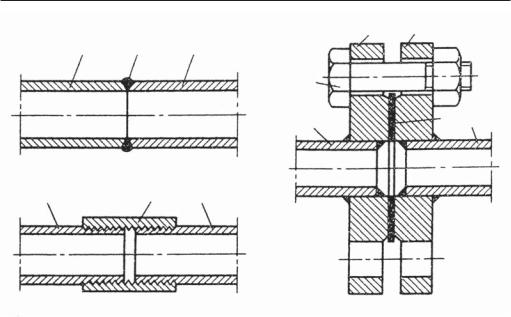
946 ПИВОВАРЕННАЯ ИНЖЕНЕРИЯ
|
|
|
|
|
|
|
|
|
|
|
|
|
|
|
|
|
|
|
|
|
|
|
|
|
|
|
|
|
|
|
|
|
|
|
|
|
3 |
4 |
|
|
|
|
|
а) |
|
|
|
|
|
|
|
|
в) |
|
|
|
||||||
|
|
|
|
|
|
|
|
|
|
|
|
|
|
|
|
|
|
|
||
|
|
|
|
|
|
1 |
2 |
3 |
|
|
|
|
|
|
|
|
|
|
|
|
|
|
|
|
|
|
|
|
|
||||||||||||
|
|
|
|
|
|
|
|
|
|
|
|
|
|
|
|
|||||
|
|
|
|
|
|
|
|
|
|
22 |
|
|
|
|
|
|
|
|||
|
|
|
|
|
|
|
|
|
|
|
|
|
|
|
|
|
|
|
|
|
|
|
|
|
|
|
|
|
|
|
11 |
|
|
|
5 |
6 |
|||||
|
|
|
|
|
|
|
|
|
|
|
|
|
|
|
|
|
|
|
|
|
|
|
|
|
|
|
|
à) |
|
|
|
|
|
|
|
|
|
|
|
|
|
|
б) |
|
|
|
|
|
|
|
|
|
|
|
|
|
|
|
|
|||
|
|
|
|
|
|
|
|
|
|
|
|
|
|
|
|
|
|
|
||
|
|
|
|
|
|
|
|
|
|
|
|
|
|
|
|
|
||||
|
|
|
|
1 |
|
22 |
3 |
|
|
|
|
|
|
|
|
|
|
|
||
|
|
|
|
|
|
|
|
|
|
|
|
á) |
|
â) |
|
|
|
|
|
|
Рис. 9.30. Основные виды соединений труб:
а — сварное: 1, 3 — соединяемая труба, 2 — сварной шов; б — резьбовое:
1, 3 — соединяемая труба; 2 — муфта; в — фланцевое: 1, 6 — соединяемая труба; 2 — болтовое соединение; 3, 4 — фланец; 5 — прокладка уплотнительная
Наиболее распространенные на практике соединения труб показаны на рис. 9.30. Соединение труб сваркой встык используют главным образом для стальных, титановых, алюминиевых труб, и реже — для труб из полимерных материалов. В отличие от сварных, резьбовые соединения, осуществляемые с помощью муфт, позволяют легко осуществлять монтаж и демонтаж трубопровода. На концах труб и в муфте нарезают мелкую резьбу, называемую «трубной».
При изготовлении технологических трубопроводов чаще всего используют фланцевые соединения — удобные при монтаже и позволяющие осуществлять разъемные соединения с арматурой, которая в большинстве случаев выпускается фланцевой.
Пример одного из типов фланцевого соединения показан на рис. 9.35, в. Фланцы 3 и 4 как правило, изготавливают круглой формы и приваривают к концам соединяемых труб 1, 6. При монтаже трубопровода фланцы стягивают попарно болтами 2, а герметичность соединения обеспечивают с помощью уплотнительной прокладки 5, материал которой выбирают в зависимости от условий эксплуатации трубопровода. Обычно для этой цели используют резину, паронит, фторопласт. Фланцы могут закрепляться на трубе не только сваркой, но и с помощью резьбы. При монтаже очень удобны фланцы, свободно располагающиеся на трубе и удерживаемые на ней с помощью отбортовки концов труб или бортиков, приваренных к концам труб. При использовании свободных (накидных) фланцев не возникает проблем при совмещении отверстий под крепежные болты. Соприкасаемые поверхности фланцев, между которыми располагается прокладка, выполняют не только
ВСПОМОГАТЕЛЬНОЕ ОБОРУДОВАНИЕ СОЛОДОВЕННОГО И ПИВОВАРЕННОГО ... |
947 |
|
|
|
|
гладкими, но и с выступами и впадинами, а также по типу «шип–паз», что позволяет повысить надежность герметизации соединения при работе трубопровода при высоких внутренних давлениях.
Изоляция трубопроводов. Специфической особенностью трубопроводов пивобезалкогольной промышленности является то, что по ним транспортируются среды, как правило, или ниже температуры окружающей среды, или выше. Поэтому значительную часть трубопроводов в указанных производствах покрывают тепловой изоляцией, которая позволяет сократить потери тепла (или холода). Кроме того, тепловая изоляция предохраняет водяной пар от конденсации в трубе, предохраняет производственные помещения от нагрева горячими трубопроводами, а также препятствует конденсации содержащихся в воздухе водяных паров на стенках трубопроводов с охлажденными средами.
Материал тепловой изоляции должен удовлетворять следующим требованиям:
•обладать малой теплопроводностью;
•обладать небольшой теплоемкостью;
•быть относительно доступным и дешевым;
•обладать малой массой и быть долговечным;
•быть прочным, недорогим и не оказывать разрушительное влияние на материал трубопровода;
•должен легко наноситься на трубопроводы.
Однако ни один из применяемых материалов не удовлетворяет всем указанным требованиям в полной мере. Например, чем более эффективен изоляционный материал, тем он обычно дороже.
В промышленности чаще всего используют следующие теплоизоляционные материалы: минеральную вату, асбозурит, асбестит, пробковую крошку, смешанную со смолой. В последние годы появились новые эффективные теплоизоляционные материалы на основе полиуретана.
Окраска трубопроводов. Продуктовые трубопроводы из нержавеющей стали не окрашивают. А все прочие трубопроводы для вспомогательных сред, за исключением стеклянных, керамических и фарфоровых, после их монтажа и испытания окрашивают стойкой краской, которая не только предохраняет их от коррозии и придает им опрятный вид, но и позволяет различать их по цвету и другим отличительным знакам нанесенных на них. Цвета окраски и отличительные знаки трубопроводов, по которым перекачиваются наиболее распространенные среды, регламентированы правилами техники безопасности. Некоторые из них, применяемые в пивобезалкогольной промышленности, приведены в табл. 9.10.
Различие в окраске трубопроводов облегчает их обслуживание, повышает безопасность их эксплуатации. Трубопроводы в теплоизоляции также окашивают. Толщина полос на трубопроводе должна составлять 50–100 мм, а расстояние между ними 1–2 м.
На арматуре, смонтированной, на трубопроводе, должны быть закреплены бирки с четкой надписью, поясняющей назначение трубопровода и арматуры.
Инженерные расчеты трубопроводов. От определения диаметра трубопровода в значительной степени зависит его экономичность. Это обусловлено тем, что при увеличении диаметра трубопровода возрастают затраты на его сооружение, ремонт, окраску и т. п. (так, общие затраты на сооружение трубопроводов могут достигать 30% от стоимости всего
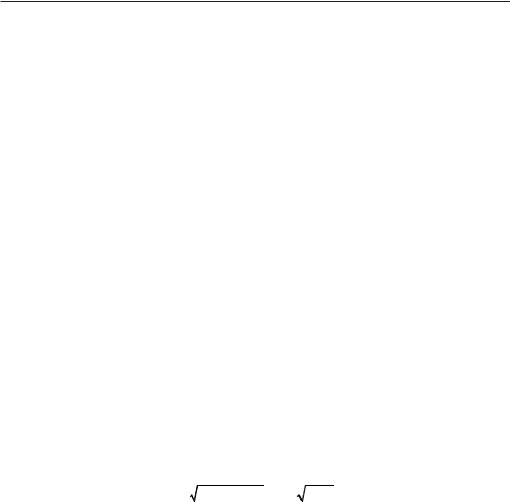
948 ПИВОВАРЕННАЯ ИНЖЕНЕРИЯ
|
Таблица 9.10 |
Цвета окраски трубопроводов различного назначения |
|
|
|
Транспортируемая среда или назначение |
Цвет окраски трубопровода и отличительные |
трубопровода |
знаки |
Вакуум |
Белый с желтыми полосками |
Вода горячая |
Зеленый с красными полосками |
Вода обратная (условно-чистая) |
Зеленый с коричневыми полосками |
Вода питьевая (хозяйственная) |
Зеленый |
Вода производственная |
Черный |
Воздух сжатый |
Синий |
Канализация |
Черный с желтыми полосками |
Конденсат водяного пара |
Зеленый с синими полосками |
Пар насыщенный |
Красный с желтыми полосками |
Пожарный водопровод |
Оранжевый |
Хладагент прямой |
Темнокоричневый с черными полосками |
Хладагент обратный |
Темнокрасный с желтыми полосками |
предприятия), а при уменьшении диаметра трубопровода возрастает его сопротивление и, соответственно, затраты на транспортирование.
Объемный расход (м3/ч) перекачиваемой среды Q прямо пропорционален площади поперечного сечения трубы F и средней скорости потока в трубе w, т. е.:
Q = 3600Fw, |
(9.67) |
где Q — объемный расход транспортируемой среды, м3/ч; w — средняя скорость потока в трубе, м/с; F — площадь поперечного сечения проточной части трубы, м2.
Преобразовав вышеуказанную формулу, с учетом F = πd2/4, можно получить выражение для определения внутреннего диаметра (м) трубы:
d = 4Q / 3600πw ≈0,02 Q / w. |
(9.68) |
Объемный расход перекачиваемой среды устанавливают исходя из требований технологического процесса, а средней скоростью потока задаются в соответствии с рекомендациями, выработанными практикой и учитывающими свойства транспортируемых сред. Ниже приведены рекомендуемые скорости (м/с) потока в трубопроводах для наиболее распространенных технологических сред:
Вода, маловязкие жидкости, малоконцентрированные суспензии .......... |
До 3,0 |
Затор ...................................................................................................... |
До 1,3 |
Сусло, пиво............................................................................................. |
До 1,5 |
Дрожжевая культура ............................................................................... |
До 1,2 |
Квас, безалкогольные газированные напитки, минеральные воды.......... |
До 1,2 |
Соки........................................................................................................ |
До 1,5 |

|
|
949 |
ВСПОМОГАТЕЛЬНОЕ ОБОРУДОВАНИЕ СОЛОДОВЕННОГО И ПИВОВАРЕННОГО ... |
|
|
Вязкие жидкости, сиропы ....................................................................... |
До 0,8 |
|
Пластические вещества .......................................................................... |
До 0,5 |
|
Пар ......................................................................................................... |
До 25,0 |
|
Сжатый воздух ........................................................................................ |
До 16,0 |
|
Газовые выбросы, СО2............................................................................. |
До 8,0 |
|
Растворы СИП......................................................................................... |
До 3 |
|
Растворы СИП при мойке труб ................................................................ |
Не менее 2,0 |
|
Раствор пропиленгликоля ....................................................................... |
До 2 |
|
Парогазовые смеси в вакуумпроводах .................................................... |
До 20,0 |
|
При расчете трубопроводов, по которым перекачиваются жидкие среды центробежными насосами, а также при значительной протяженности трубопроводов определяют потери давления на преодоление сопротивления трубопровода, которые складываются из потерь на преодоление трения о стенки трубы и потерь в так называемых местных сопротивлениях трубопровода — отводах, арматуре и т. п.
Потери давления (Па) на преодоление трения в прямом участке трубы определяют:
∆p =ρλ |
l |
|
w2 |
, |
(9.69) |
|
|
||||
ср |
d |
2 |
|
|
|
|
|
|
где ∆ рср — потери давления на преодоление трения в прямом участке трубы, Па; ρ — плотность среды, кг/м3; λ — коэффициент гидравлического сопротивления (определяют расчетным путем или находят по справочнику); l — длина участка трубопровода, м; d — диаметр трубопровода, м; w — скорость потока среды, м/с.
Потери давления (Па) от местных сопротивлений определяют по формуле:
∆p =ςρ |
w |
, |
(9.70) |
м |
2 |
|
где ζ — коэффициент местного сопротивления, установленный экспериментально для разных типов арматуры, соединительных частей и т. п. (его значение выбирают по справочнику).
Потери давления от местных сопротивлений часто выражают в метрах эквивалентной длины трубы (lэкв) того же диаметра, что и устройство, создающее сопротивление. Значение lэкв для различных типов арматуры или фитингов (соединительных деталей) выбирают из справочников.
В этом случае общие потери (Па) в трубопроводе определяют по вышеуказанной формуле для определения потерь давления на преодоление сил трения в прямом участке трубы, но к общей длине прямых участков прибавляют эквивалентную длину трубы, соответствующую местным сопротивлениям, т. е.:
|
w2 |
l +l |
экв |
|
|
|
∆р =ρ |
|
|
|
. |
(9.71) |
|
2 |
d |
|
||||
|
|
|
|
|
При разработке гидравлических или пневматических схем необходимо использовать условные изображения основных элементов, рекомендуемые ГОСТом, и показаные на рис. 9.31.
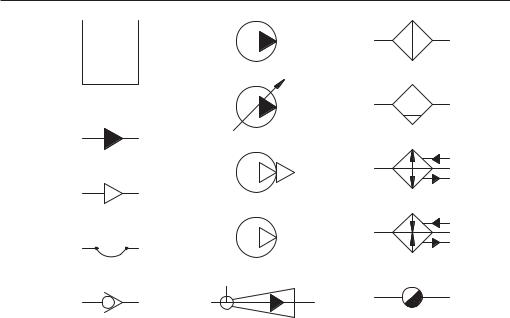
950 ПИВОВАРЕННАЯ ИНЖЕНЕРИЯ
1 |
6 |
11 |
|
|
|
|
7 |
12 |
2 |
|
|
|
8 |
13 |
|
|
|
3 |
|
|
|
9 |
14 |
4 |
|
|
|
|
|
5 |
10 |
15 |
|
Рис. 9.31. Условные изображения основных элементов гидравлических
ипневматических схем:
1 — емкость под атмосферным давлением; 2 — поток жидкости; 3 — поток газа; 4 — гибкий участок трубопровода; 5 — обратный клапан; 6 — насос; 7 — насос
срегулируемой подачей; 8 — вакуум-насос; 9 — компрессор; 10 — струйный насос; 11 — фильтр жидкостной или воздушный; 12 — влагоили маслоотделитель;
13 — теплообменник-охладитель; 14 — теплообменник-нагреватель;
15 — конденсатоотводчик
9.7.4.4. Трубопроводная арматура
Перекрытие трубопроводов осуществляют с помощью запорной арматуры. Ее можно использовать также для грубого регулирования величины потока транспортируемой жидкости, однако при необходимости точной регулировки для этой цели используют специальную регулирующую арматуру.
Запорную арматуру подразделяют на приводную и автоматическую.
Вприводной арматуре рабочий орган приводится в действие при закрытии или открытии трубопровода под действием внешней силы: мускульных усилий человека, электродвигателя, соленоида, гидроили пневмопривода. В автоматической арматуре действие рабочего органа осуществляется с помощью транспортируемой среды.
По конструктивному признаку приводную запорную арматуру разделяют на три основных типа: краны, вентили и заслонки. Принципиальные схемы их действия показаны на рис.9.32.
Вкране рабочим органом является затвор, выполненный в виде конической притертой пробки или шара, со сквозным отверстием. Затвор размешается в корпусе крана и может
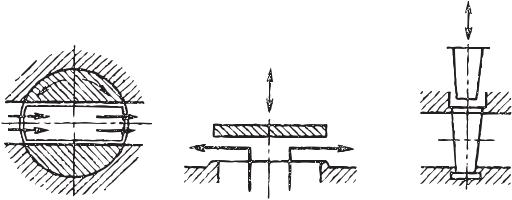
|
ВСПОМОГАТЕЛЬНОЕ ОБОРУДОВАНИЕ СОЛОДОВЕННОГО И ПИВОВАРЕННОГО ... |
951 |
|
|
|
||
|
|
|
|
а) |
б) |
в) |
|
Рис. 9.32. Принципиальные схемы действия основных видов трубопроводной арматуры:
а — кран; б — вентиль; в — заслонка
вращаться в нем вокруг своей оси. В открытом положении отверстие в затворе совмещается со входным и выходным штуцерами корпуса, а в закрытом положении (при повороте затвора вокруг своей оси на 90°) входное и выходное отверстие корпуса перекрываются затвором.
Рабочим органом вентиля является золотник, который перемещается перпендикулярно продольной оси потока прокачиваемой жидкости, перекрывая при этом отверстие, расположенное в перемычке корпуса, разделяющей его на входную и выходную часть. В диафрагмовых вентилях роль золотника играет гибкая диафрагма, выполненная из эластичного материала, например, резины или пластика.
У заслонки рабочим органом является затвор, выполненный в виде диска, при этом различают заслонки поворотные и шиберные (задвижки). У поворотной заслонки затвор укреплен на оси и может поворачиваться вокруг ее в корпусе. У задвижки затвор клинообразного сечения перемещается в корпусе перпендикулярно продольной оси потока перемещаемой жидкости.
Традиционно в пивобезалкогольной промышленности наиболее широкое применение получили краны как наиболее простые и удобные в эксплуатации.
К достоинствам кранов следует отнести:
•малое гидравлическое сопротивление потоку жидкости;
•быстроту действия при открывании или закрывании;
•конструктивную простоту;
•способность пропускать суспензии и прочие загрязненные жидкости. А недостатками кранов являются:
•возможность возникновения гидравлического удара вследствие быстрого открытия или закрытия;
•малопригодность для регулирования величины потока;
•необходимость приложения определенных усилий при открытии и закрытии из-за большой площади поверхности контакта притертых деталей (поэтому в стандартных кранах диаметры условного прохода dу не превышают 80 мм);
952 |
ПИВОВАРЕННАЯ ИНЖЕНЕРИЯ |
|
|
•непригодность при температуре рабочих сред свыше 120 °С;
•трудоемкость восстановления (притирка) изношенного крана.
Вентили характеризуются следующими положительными особенностями:
•они надежны в работе, легко обеспечивают герметичность;
•хорошо регулируют величину подачи;
•при протоке через них капельной жидкости в них невозможно возникновение гидравлического удара при открытии или закрытии (однако это не характерно при проходе
через вентиль пара).
К недостаткам вентилей относят:
•высокое гидравлическое сопротивление потоку, которое у некоторых типов вентилей в 5–10 раз превышает сопротивление кранов;
•относительная дороговизна изготовления по сравнению с кранами;
•медленное действие при открытии или закрытии;
•непригодность при использовании в трубопроводах, предназначенных для перекачки загрязненных жидкостей (это обстоятельство не распространяется на диафрагмовые
вентили).
Задвижки изготавливаются для трубопроводов с диаметрами от 50 до 1500 мм. В зависимости от модификации они могут использоваться при давлениях до 10 МПа.
Для задвижек характерны:
•малое гидравлическое сопротивление;
•удобство регулирования расходов;
•исключение гидравлического удара при закрытии или открытии. Однако задвижки:
•более дороги (дороже вентилей);
•трудно поддаются ремонту уплотняющих поверхностей;
•более громоздки за счет большой длинны шпинделя, на котором закреплен диск задвижки;
•они не пригодны при работе с жидкостями, содержащими взвеси.
Вследствие перечисленных недостатков задвижки значительно реже используются
впивобезалкогольной промышленности, чем краны, вентили и поворотные заслонки.
Всовременных автоматизированных технологических системах пивоваренных производств с жесткой трубной обвязкой находят применение специальные двухседельные клапаны, устанавливаемые в точке пересечения потоков двух различных сред. Конструктивное устройство этих клапанов предотвращает смешивание этих потоков. Существуют различные типы двухседельных клапанов — один из них показан на рис. 9.33.
Верхний 9 и нижний 10 корпуса двухседельного клапана оснащены седлами, к которым плотно прилегают соответственно верхняя 3 и нижняя 2 тарелки. Прижим тарелок к соответствующим седлам осуществляют сверху с помощью штока 8, перемещаемого с помощью пневматического исполнительного механизма 5. Нижняя тарелка 10 жестко соединена со штоком 8 и перемещается вместе с ним, в то время как верхняя тарелка 9 со штоком жестко не связана и при его перемещении благодаря пружине 7, передвигается на меньшее расстояние по сравнению с нижней тарелкой. Герметичность соединений тарелок между собой и с седлами обеспечивают с помощью резиновых уплотнений.
Система отвода утечек представляет собой полость между обеими тарелками клапана, которая сообщается с атмосферой через дренажный патрубок 1, расположенный в нижнем штоке клапана.
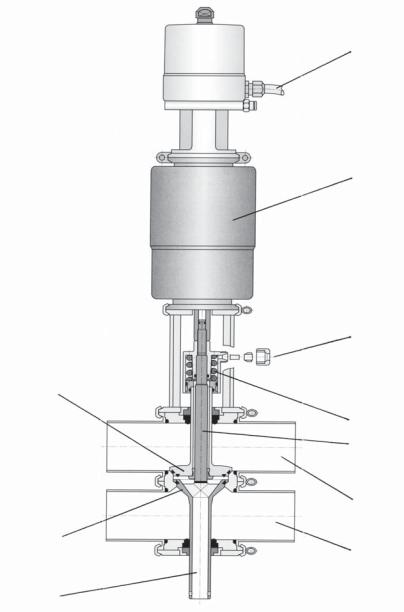
ВСПОМОГАТЕЛЬНОЕ ОБОРУДОВАНИЕ СОЛОДОВЕННОГО И ПИВОВАРЕННОГО ... |
953 |
|
|
|
|
4
5
6
3
7
8
9
2
10
1
Рис. 9.33. Двухседельный клапан:
1 — патрубок дренажный; 2 — тарелка клапана нижняя; 3 — тарелка клапана верхняя; 4 — подвод сжатого воздуха; 5 — исполнительный механизм;
6 — подвод моющих растворов; 7 — пружина; 8 — шток привода клапана; 9 — корпус клапана верхний; 10 — корпус клапана нижний
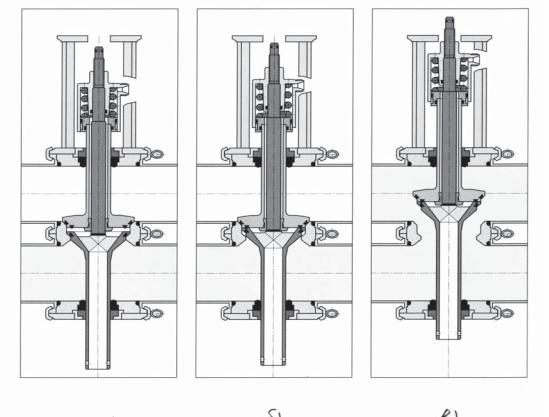
954 |
ПИВОВАРЕННАЯ ИНЖЕНЕРИЯ |
|
|
Верхний и нижний корпуса клапана, соединенные с соответствующими трубопроводами, промывают и дезинфицируют одновременно с этими трубопроводами, а полость между тарелками промывают индивидуально моющими и дезинфицирующими растворами, поступающими в нее через штуцер 6. В полости между тарелками моющий раствор разбрызгивается кольцевым соплом и свободно выводится наружу через дренажный патрубок.
Дистанционное управление клапаном осуществляют с помощью сжатого воздуха, подводимого к клапану через патрубок 4.
Основные положения при функционировании двухседельного клапана показаны на рис. 9.34.
Взакрытом положении (рис. 9.34, а) верхние и нижние тарелки плотно примыкают
ксоответствующим седлам верхнего и нижнего корпусов, образуя между собой полость дренажной системы, соединенную через дренажный патрубок с атмосферой.
Перед открытием клапана шток начинает перемещаться вверх, нижняя тарелка приподнимается и плотно прижимается к верхней тарелке, отключая при этом дренажную систему
а) |
|
б) |
|
в) |
|
|
|
|
|
à) |
á) |
â) |
|
|
|
Рис. 9.34. Принцип функционирования двухседельного клапана:
а — закрытое положение; б — отключение дренажной системы; в — открытое положение