
Pivovarennaya_inzheneria_ / Глава 9
.pdfВСПОМОГАТЕЛЬНОЕ ОБОРУДОВАНИЕ СОЛОДОВЕННОГО И ПИВОВАРЕННОГО ... |
915 |
|
|
|
|
избежание попадания смазки в перемещаемый продукт. С одной из сторон конвейера расположен электропривод 1, от которого вал приводится во вращение. Частоту вращения вала (20–200 мин–1) выбирают так, чтобы скорость перемещения продукта не превышала 1,3 м/с. При транспортировании зерна для его лучшего сохранения от механических повреждений рекомендуется устанавливать скорость перемещения 0,6–0,8 м/с. Для обеспечения нормальной работы винтового конвейера коэффициент заполнения желоба не должен превышать 20–30%.
К преимуществам винтовых конвейеров следует отнести: компактность; простоту конструктивного устройства; хорошее перемешивание транспортируемого зерна; дешевизну при изготовлении и обслуживании.
В то же время их работа сопряжена с существенными проблемами: возникновением механических повреждений и измельчения транспортируемого зерна из-за его сдавливания
иповышенного трения о стенки желоба и витки вала; плохим проветриванием зерна при транспортировании; высоким энергопотреблением (см. табл. 9.7); возможностью закупорки
иповреждения конструкции при неравномерной загрузке и переполнении желоба. Винтовые конвейеры целесообразно использовать при перемещении сыпучих продуктов
на короткие расстояния с малой или средней величиной подачи.
Винтовые конвейеры изготавливают с винтами следующих размеров (мм):
Диаметр… |
100 |
125 |
160 |
200 |
250 |
320 |
400 |
500 |
650 |
800 |
Шаг……… |
80 |
100 |
125 |
160 |
200 |
250 |
320 |
400 |
500 |
650 |
Производительность (кг/с) винтового конвейера |
|
|
|
|
|
П = 0,785(D2 — d2)Sρn K |
K |
K |
y |
, |
(9.29) |
в |
з |
|
|
|
где D — диаметр винта конвейера, м; d — диаметр вала шнека, м; S — шаг винта, м; п — частота вращения винта, с–1; Kв — коэффициент зависимости шага винта от его диаметра (для легкосыпучих грузов Kв = 0,5–0,6; для крупнокусковых и абразивных грузов Kу = 0,5–0,6);
Kз — коэффициент заполнения желоба: для легких и неабразивных грузов (мука) Kз |
= 0,40, |
||||
для легких и малоабразивных грузов (отруби, зерно, солод, сода и т. п.) Kз = 0,4–0,8; для |
|||||
тяжелых и абразивных грузов (соль, сахарный песок, и т. п.) Kз = 0,25; Kу — коэффициент, |
|||||
зависящий от угла наклона конвейера. |
|
|
|
|
|
Угол наклона, град…………………… |
0 |
5 |
10 |
15 |
20 |
К ………………………………………… |
1,0 |
0,9 |
0,8 |
0,7 |
0,6 |
у |
|
|
|
|
|
Мощность (кВт) электродвигателя привода горизонтального и наклонного винтового
конвейера |
|
Nэ = 3,6gП(L Kc + H)Kзм / (3670η), |
(9.30) |
где П — производительность конвейера, кг/с; L — длина конвейера, м; Kс — коэффициент сопротивления движения груза (для зернистых грузов Kс = 1,5–1,6; для мучнистых Kс = = 1,2–1,3; для кусковых и абразивных Kс = 1,8–2,0); Kзм — коэффициент запаса мощности (Kзм = 1,15–1,25); η — КПД привода (η = 0,8–0,85).
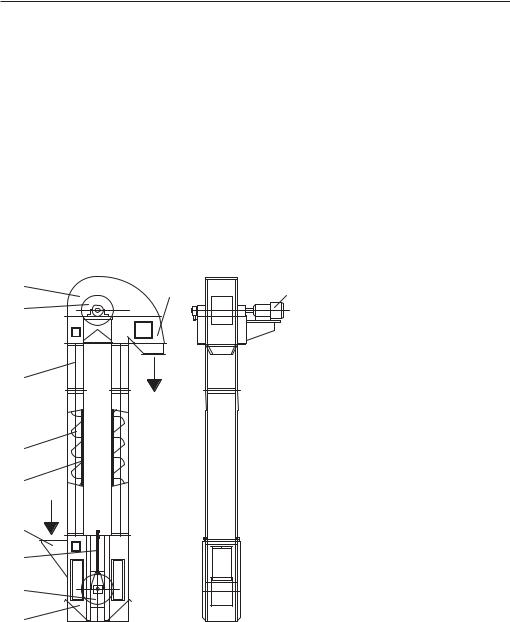
916 |
ПИВОВАРЕННАЯ ИНЖЕНЕРИЯ |
|||
|
9.7.2.4. Нории |
|
||
По конструктивному устройству различают ковшовые и люлечные нории (элеваторы). |
||||
Ковшовые нории предназначены для вертикального перемещения сыпучих материалов |
||||
(зерна, солода, сахара, муки) на высоту до 100 м подачей до 600 т/ч. Люлечные нории пред- |
||||
назначены для вертикального перемещения единичных грузов (ящиков, пакетов, бочек, |
||||
мешков, коробов, контейнеров и т. п.). |
|
|
||
Ковшовые и люлечные нории по направлению перемещения грузов разделяют на вер- |
||||
тикальные и наклонные, а по виду тягового органа — на ленточные, одно- и двухцепные. |
||||
Ленточные ковшовые нории из-за ограниченной прочности ленты имеют сравнительно |
||||
небольшую высоту подъема, не превышающую 25 м, скорость движения ковшей до 0,8 м/с, |
||||
а производительность до 80 т/ч. Производительность цепных норий может достигать до |
||||
300 т/ч при скорости движения ковшей от 2,5 до 4,0 м/с. |
||||
Ковшовая нория (рис. 9.14) представляет собой два вертикальных металлических |
||||
кожуха 7 прямоугольного сечения, опирающиеся на специальную конструкцию (баш- |
||||
мак) 1 с одним или несколькими загрузочными патрубками 4. К верхней части кожу- |
||||
|
|
|
хов прикреплена головка 9 нории |
|
9 |
10 |
11 |
с разгрузочным патрубком 10. |
|
Внутри кожухов нории по |
||||
|
||||
8 |
|
|
направляющим непрерывно дви- |
|
|
|
|
жется со скоростью 2 – 3 м/с |
|
|
|
|
замкнутая лента 5 из хлопчатобу- |
|
|
|
|
мажной или синтетической про- |
|
7 |
|
|
резиненной ткани, огибая шкивы, |
|
|
|
расположенные в башмаке и го- |
||
|
|
|
||
|
|
|
ловке. Вал шкива 8, расположен- |
|
|
|
|
ного в головке нории, соединен |
|
|
|
|
с электроприводом 11 (мотор- |
|
6 |
|
|
редуктором), установленным |
|
|
|
снаружи на специальной консоли, |
||
|
|
|
||
5 |
|
|
прикрепленной к головке. Вал |
|
|
|
шкива 2, располагаемого в баш- |
||
|
|
|
||
|
|
|
маке нории, соединен с натяжным |
|
4 |
|
|
устройством 3, предназначенным |
|
|
|
для регулирования величины на- |
||
3 |
|
|
тяжения ленты. |
|
|
|
На ленте равномерно, через |
||
|
|
|
||
2 |
|
|
300–400 мм, закреплены металли- |
|
|
|
ческие или пластмассовые ковши |
||
1 |
|
|
6, вместимость которых составля- |
|
|
|
ет обычно 2–15 дм3. Коэффициент |
||
|
Рис. 9.14. Ковшовая нория: |
|
заполнения ковшей ~60–75%. Во |
|
|
|
избежание повреждения ковшей |
||
|
1 — башмак; 2 — шкив натяжной; 3 — устройство |
|
||
|
|
в приемном устройстве башмака |
||
|
натяжное; 4 — патрубок загрузочный; 5 — лента; |
|
||
6 — ковш; 7 — кожух; 8 — шкив приводной; 9 — головка; |
10, лента должна быть всегда хо- |
|||
|
10 — патрубок разгрузочный; 11 — привод |
|
рошо натянута. |
ВСПОМОГАТЕЛЬНОЕ ОБОРУДОВАНИЕ СОЛОДОВЕННОГО И ПИВОВАРЕННОГО ... |
917 |
|
|
|
|
Зерно подают через загрузочный патрубок 4 в приемное устройство нории, в котором оно захватывается ковшами и поднимается вверх к разгрузочной головке. Разгрузка ковшей происходит при их опрокидывании в момент огибания лентой верхнего шкива 8. При опрокидывании ковша зерно отбрасывается от него в разгрузочный патрубок 10 под действием центробежной силы, возникающей вследствие высокой скорости движения ленты нории. По этой причине верхнее очертание головки в направлении разгрузочного патрубка выполняют в форме параболы (см. рис. 9.14).
Одной из модификаций нории является конструкция с ковшами, не имеющими дна. Благодаря этому техническому решению зерно перемещается вертикально сплошным потоком, обеспечивая тем самым увеличение подачи нории.
Для обеспечения нормальной и безопасной работы норию оснащают защитным устройством, препятствующим противоположному направлению движения ленты; тахометром для контроля частоты вращения шкива нории; устройством для контроля сбегания ленты со шкивов в головке и башмаке; взрыворазрядителем и подключают к системе аспирации. Во избежание забивания и повреждения нории ее оснащают системой блокировки, которая при непредвиденной остановке ленты незамедлительно прекращает поступление транспортируемого продукта в приемный патрубок башмака.
Ковшовые нории просты по устройству и безотказны в работе. Однако их недостатком является неполное опорожнение ковшей в процессе разгрузки.
По способу разгрузки различают нории:
•с центробежной разгрузкой под действием центробежной силы, возникающей во время прохождения ковшей через барабан или звездочки; такую разгрузку применяют при расставленных ковшах (по 2–3 ковша на 1 пог. м) при скорости движения ковшей 1,0–3,5 м/с;
•с самотечной разгрузкой под действием сил тяжести при сомкнутых или несколько расставленных ковшах при скорости их движения 0,4–0,8 м/с.
Производительность (кг/с) ковшовой нории
П = VvρK3/l, |
(9.31) |
где V — вместимость ковша, м3; v — скорость перемещения груза, м/с (обычно v = 2–4 м/с); ρ — насыпная плотность груза, кг/м ; Kз — коэффициент заполнения ковшей (для мелкозернистых грузов Kз = 0,85–0,95, а для крупнозернистых и кусковых Kз = 0,5–0,8); l — шаг ковшей, м.
Потребная мощность (кВт) электродвигателя приводного барабана
Nэ = ПHg/(1000η), |
(9.32) |
где П — производительность нории, кг/с; Н — высота подъема груза, м; g — ускорение свободного падения, м/с2; η — КПД привода (η = 0,75–0,8).
Люлечная нория с жестким креплением захватов показана на рис. 9.15, а. Конструкция захватов зависит от формы перемещенного груза (бочки, ящики). Разгружаются такие нории со стороны размещения приводных звездочек.
На рис. 9.15, б показана цепная нория с шарнирным креплением люлек для перемещения штучных грузов (ящиков, контейнеров, бочек, мешков), которые находятся в пространстве
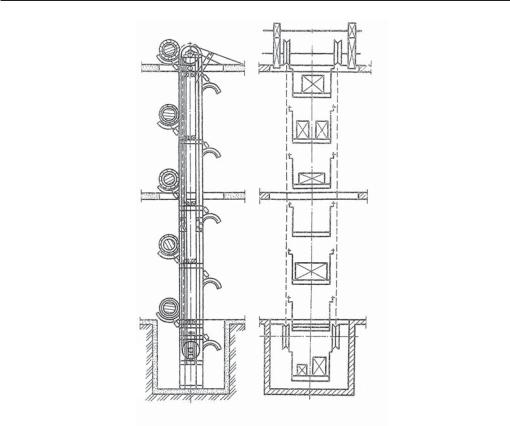
918 ПИВОВАРЕННАЯ ИНЖЕНЕРИЯ
а) б)
0
1
б) |
|
в) |
|
|
|
Рис. 9.15. Люлечная нория:
а— с жестким креплением захватов; б — с шарнирным креплением люлек
водном и том же положении вместе с люлькой. Этими нориями можно производить разгрузку в здании поэтажно по высоте подъема или спуска. Скорость перемещения люлек до 0,9 м/с при производительности до 300 мест груза в час.
9.7.2.5.Гравитационные и роликовые конвейеры
Гравитационные и роликовые конвейеры применяют для перемещения ящиков с порожней посудой и готовой продукцией по горизонтальной и пологонаклонной трассе. По конструкции роликовые конвейеры подразделяют на приводные и неприводные. На приводных конвейерах грузы перемещаются под действием силы трения, возникающей при вращении роликов от привода, который выполнен в виде системы зубчатых или цепных передач, на неприводных — под действием силы тяжести или приложенной извне силы. Неприводные конвейеры устанавливают с уклоном 1,0–1,5% при перемещении грузов с помощью прикладываемой извне силы, а при уклоне 1,5–3,0% грузы способны передвигаться под действием силы, тяжести.
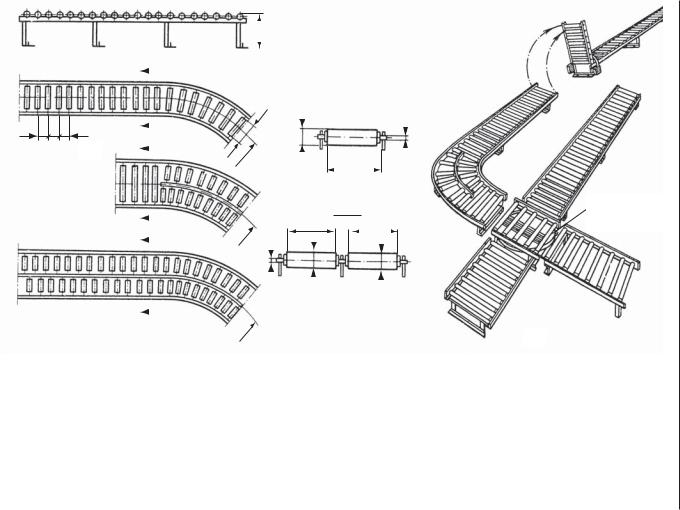
а)
t t t
a)
б)
в)
|
|
|
|
|
h |
|
|
|
|
|
|
|
|
|
|
|
|
|
г) |
|
|
|
|
|
|
|
|
|
|
|
|
|
|
|
|||||||
|
|
|
А |
|
|
|
|
|
|
|
|
|
|
АА |
||||||
|
|
|
|
|
|
|
|
|
|
|
|
|
||||||||
|
|
|
|
|
l |
|
|
|
|
|||||||||||
|
|
|
|
|
|
|
|
|
||||||||||||
|
|
|
|
|
|
|
|
|
|
|||||||||||
|
|
А |
|
|
|
|
|
|
|
|
|
d |
|
|||||||
|
|
|
|
|
|
|
|
|
p |
|
|
|
|
|
|
|
|
|||
|
|
|
|
|
|
|
|
|
|
|
|
|
||||||||
|
|
|
А |
|
|
|
|
|
d |
|
|
|
|
|
|
|
|
|||
|
|
|
|
R |
|
|
|
|
l |
|
|
|||||||||
|
|
|
|
|
|
|
|
|
||||||||||||
|
|
|
|
|
|
|
|
|
||||||||||||
|
|
|
А |
|
|
|
|
|
|
|
|
|
ББ |
|||||||
|
|
|
|
б) |
R |
|
l |
|
|
|
l |
|||||||||
|
|
|
|
|
|
|
|
|
|
|
|
|
|
|
|
|||||
|
|
Б |
|
|
|
|
|
|
|
|
|
|
|
|
|
|
|
|
|
|
|
|
|
|
|
|
|
|
|
|
|
|
|
|
|
|
|
|
|
|
|
|
|
|
|
|
|
d |
|
|
|
|
|
|
|
|
||||||
|
|
|
|
|
|
|
|
|
|
|
|
|
|
|
|
|
|
|||
|
|
|
|
|
|
|
|
|
|
|
|
|
|
|
|
|||||
|
|
|
|
|
|
|
|
|
|
p |
|
|
|
|
|
p |
|
|||
|
|
|
|
|
|
|
|
|
d |
|
|
|
|
|
||||||
|
|
|
|
|
|
|
|
|
|
|
|
d |
|
|||||||
|
|
|
Б |
|
R |
|
|
|||||||||||||
|
|
|
|
|
|
|
|
|
|
|
|
|||||||||
|
|
|
|
|
|
|
|
|
|
|
||||||||||
|
|
|
|
|
|
|
|
|
|
|
|
|||||||||
|
|
|
|
|
|
|
|
|
|
|
|
|||||||||
в) |
|
|
|
|
|
|
|
|
|
|
|
|||||||||
|
|
|
|
|
|
|
|
|
|
|
|
|
|
|
|
|
|
|
|
|
Рис. 9.16. Роликовые конвейеры:
а — неприводной; б — однорядный с многорядным поворотным участком; в — многорядный; г — неприводной с поворотным кругом
г)
Поворотный
Поворотны
круг
круг
... ПИВОВАРЕННОГО И СОЛОДОВЕННОГО ОБОРУДОВАНИЕ ВСПОМОГАТЕЛЬНОЕ
919
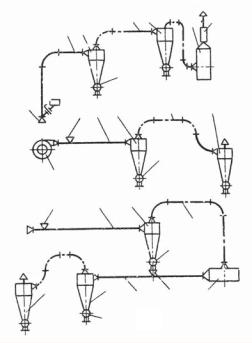
920 |
ПИВОВАРЕННАЯ ИНЖЕНЕРИЯ |
|
|
Роликовые конвейеры (рольганги) показаны на рис. 9.16. Они состоят из стальных секций, длина которых l = 2–3 м. Диаметр ролика dp принимают: с обработанной поверхностью — от 55 до 155 мм, с необработанной — от 57 до 159 мм, диаметр оси d — от 15 до 30 мм. Ролики изготовляют из труб, опорами которых служат подшипники скольжения или качения. В зависимости от величины диаметра ролики устанавливают с шагом t от 100 до 400 мм. Применяют цилиндрические и фигурные ролики. Высота конвейера h и радиус поворота R зависят от конкретных условий применения.
9.7.3. Пневмотранспортные системы перемещения сыпучих грузов
Пневматический транспорт представляет собой устройство перемещения по трубам сыпучих материалов в смеси с воздухом под давлением. В пивобезалкогольной промышленности пневмотранспорт применяют для подачи ячменя, солода, солодовых ростков со склада сырья в цех переработки. Установки имеют высокую производительность (до 400 т/ч) при расстоянии перемещения грузов до 100 м и при подъеме их на высоту до 100 м.
Пневмотранспортные системы по сравнению с механическими проще по конструкции, надежнее в эксплуатации и легче
|
|
|
|
|
|
|
|
|
|
в обслуживании. Они надежно герме- |
а) |
|
|
|
4 5 |
|
|
|
|
||
|
|
|
|
|
|
6 7 |
тизированы, имеют высокий уровень |
|||
2 |
3 |
|
|
|
|
|
||||
|
|
|
|
|
|
механизации и автоматизации. Однако |
||||
|
|
|
|
|
|
|
|
|
|
|
|
|
|
|
|
|
|
|
|
|
у пневмотранспортных систем большой |
|
|
|
|
8 |
|
|
|
|
|
расход электроэнергии — до 0,4 кВт на 1 т |
|
|
|
|
|
|
|
|
|
перемещаемого материала, вызванный |
|
1 |
|
|
а) |
|
|
|
5 |
тем, что вместе с грузом перемещается |
||
1 2 3 |
|
|
|
|
|
большой объем воздуха. |
||||
|
|
4 |
|
|||||||
|
|
|
|
|
|
|||||
|
|
|
|
|
|
|
|
|
|
Пневмотранспортные системы бы- |
б) |
|
|
|
|
|
|
|
|
||
|
|
|
|
|
|
|
|
вают всасывающие, нагнетательные |
||
|
|
|
|
|
|
|
|
|
|
|
|
|
|
|
|
|
|
|
|
|
|
|
|
|
|
|
|
8 |
|
|
и всасывающе-нагнетательные (рис. 9.17). |
|
6 |
|
|
|
|
|
|
|
Вовсасывающейустановке(рис.9.17, а) |
||
|
|
|
б) |
|
|
|||||
|
|
|
|
|
|
|
|
с помощью воздуходувной машины 6 от- |
||
1 |
2 |
3 |
|
|
|
|
сасывается воздух, в системе создается |
|||
|
|
|
|
|
|
|
|
|
4 |
разряжение, воздух движется в загру- |
|
|
|
|
|
|
|
|
|
зочное устройство 1 и, проходя сквозь |
|
|
|
|
|
|
|
|
|
|
|
|
|
|
|
|
|
|
8 |
|
слой сыпучего материала, подхватывает |
||
в) |
|
|
|
|
|
|
||||
|
|
|
|
|
|
|
|
его и перемещает по трубопроводу 2 |
||
|
|
|
|
|
|
|
|
|
|
|
|
|
|
|
|
|
|
|
|
|
|
|
|
|
|
2 |
|
|
|
6 |
в циклон-разделитель, в котором мате- |
|
5 |
3 |
1 |
риал отделяется, а запыленный воздух |
|||||||
|
|
|
8 |
|
в) |
|
движется далее через трубопровод 4 |
в циклон-очиститель 5 и далее, очищенный от пыли, выбрасывается воздуходувной машиной 6 через глушитель шума 7
Рис. 9.17. Пневматические транспортные системы: в атмосферу. Груз из циклона-разделителя
а — всасывающая; б — нагнетательная; |
при помощи шлюзового затвора 8 выво- |
в — всасывающе-нагнетательная |
дится на переработку или на склад для |
|
ВСПОМОГАТЕЛЬНОЕ ОБОРУДОВАНИЕ СОЛОДОВЕННОГО И ПИВОВАРЕННОГО ... |
921 |
|
|
|
|
хранения. Достоинство всасывающих установок в том, что вследствие разрежения в системе исключено пылевыделение, и их можно использовать для перемещения пылеобразующих материалов (отрубей, зерна, сухого солода, муки, солодовых ростков, дробленого солода и несоложеных продуктов, крахмала и др.) к одной или нескольким технологическим точкам. К их недостатку можно отнести невозможность создания высокого перепада давления (до 50–60 кПа), что ограничивает расстояние перемещения груза и вызывает необходимость герметизации в местах вывода перемещаемого материала.
Нагнетательная пневмотранспортная установка (рис. 9.17, б) работает следующим образом. Воздуходувная машина 6 нагнетает воздух в систему установки, создавая в ней давление выше атмосферного (наибольшее — в месте загрузки, наименьшее — в месте выгрузки). Сжатый воздух, подаваемый по трубопроводу, по пути захватывает сыпучий материал, поступающий из загрузочного устройства, и направляет его в циклон-разделитель. Далее все операции проходят так же, как во всасывающей установке. В нагнетательных установках избыточное давление в трубопроводе достигает 400–600 кПа, чем обеспечивается перемещение сыпучих материалов на расстояние до 300 м и более в одну или несколько точек разгрузки.
Всасывающе-нагнетательная установка (рис. 9.17, в) сочетает преимущества как всасывающих, так и нагнетательных пневмоустановок. При транспортировании сыпучих материалов в этих установках скорость движения воздуха от 6 до 35 м/с, причем концентрация смеси (отношение величины массового расхода материала к массовому расходу воздуха) допускается до 25–30 кг/кг.
Расчет пневматических транспортных установок проводят следующим образом. При определении примерной производительности (кг/с) пневматического транспорта следует учитывать неравномерность работы установки в течение суток.
П = Gм Kн Kпр, |
(9.33) |
где Gм — масса перемещаемого груза, кг/с; Kн — коэффициент, учитывающий неравномерность подачи материала (Kн = 1,5); Kпр — коэффициент неравномерности, определяемый условиями технологического процесса (Kпp = 1,25).
Приведенная длина (м) трубопровода
Lпр = ΣLг + ΣLв + ΣLэк + ΣLэп, |
(9.34) |
где ΣLг — сумма длин горизонтальных участков труб, м; ΣLв — сумма длин вертикальных участков, м; ΣLэк — сумма длин, эквивалентных коленам, м; ΣLэп — сумма длин, эквивалентных переключателям трубопроводов, м (эквивалентная длина двухходового переключателя принимается 8 м, длина задвижки затвора — 10 м).
Длина трубопроводов Lэк,эквивалентных коленам, зависит от радиуса кривизны колена R и внутреннего диаметра трубы d (табл. 9.8).
Материал движется в трубопроводе потоком воздуха, скорость которого vв должна быть больше скорости vч витания частиц материала: vв > vч. Скорости витания частиц некоторых материалов приведены в табл. 9.6.

922 ПИВОВАРЕННАЯ ИНЖЕНЕРИЯ
|
|
|
|
|
Таблица 9.8 |
Длина трубопроводов, эквивалентных коленам, м |
|
||||
|
|
|
|
|
|
Характеристика материала |
|
|
R/d |
|
|
|
|
|
|
|
|
4 |
6 |
|
10 |
20 |
|
|
|
||||
|
|
|
|
|
|
Пылевидный |
4–8 |
5–10 |
|
6–12 |
8–10 |
|
|
|
|
|
|
Зерновой однородный |
— |
8–10 |
|
12–16 |
16–20 |
|
|
|
|
|
|
Скорость (м/с) воздуха при начале всасывания и нагнетания материала |
|
|||||
v |
в |
= a(ρ/1000)1/2 + K |
L |
2 |
, |
(9.35) |
|
м |
|
пр |
|
|
где а — коэффициент, учитывающий крупность частиц материала; ρ — плотность ма-
териала, кг/м3 (см. табл. 9.6); K |
м |
— коэффициент, учитывающий свойства материала |
|||||
[K |
|
= (2–5) · 10–5]. |
|
|
|
||
м |
|
|
|
|
|
||
|
Для всасывающих установок слагаемое Kм L2пр не учитывают. |
|
|||||
|
|
|
|||||
|
|
Значение коэффициента крупности а представлено в табл. 9.9. |
|
||||
|
|
|
|
|
|
|
Таблица 9.9 |
|
|
Коэффициент крупности для различных материалов |
|
||||
|
|
|
|
|
|
|
|
|
|
Материал |
|
|
Наибольшая крупность частиц, мм |
|
Коэффициент а |
Пылевидный и порошкообразный |
|
|
0,001–1,0 |
|
10–16 |
||
|
|
|
|
|
|
||
Зернистый однородный |
|
|
1–10 |
|
17–20 |
||
|
|
|
|
|
|
||
Мелкокусковой однородный |
|
|
10–20 |
|
17–22 |
||
|
|
|
|
|
|
||
Среднекусковой однородный |
|
|
20–80 |
|
22–25 |
||
|
|
|
|
|
|
|
|
Для устойчивой работы пневмоустановки рассчитанную скорость vв воздуха увеличивают на 10–20%.
Массовая доля материала в смеси с воздухом
µ = П / Gвм, |
(9.36) |
где П — производительность установки, кг/с; Gвм — массовый расход воздуха, кг/с. Массовую долю материала в смеси с воздухом определяют в зависимости от приведен-
ной длины трубопровода Lпр:
Для легкосыпучего сухого материала:
Lпр, м…………… |
0–200 |
200–400 |
400–600 |
600–800 |
800–1000 |
µ………………… |
70–40 |
40–25 |
25–20 |
20–15 |
15–12 |
Для зерна и подобного материала:
Lпр, м…………………………… |
0–25 |
25–50 |
50–75 |
75–100 |
µ………………………………… |
36–20 |
20–13 |
13–10 |
10–8,5 |
ВСПОМОГАТЕЛЬНОЕ ОБОРУДОВАНИЕ СОЛОДОВЕННОГО И ПИВОВАРЕННОГО ... |
923 |
|
|
|
|
Расход (м3/с) воздуха на транспортирование |
|
Gв = П/(ρвµ), |
(9.37) |
где ρв — плотность воздуха, кг/м3 (для приблизительных расчетов можно принимать ρв = 1,2 кг/м3).
Диаметр (м) трубопровода |
|
|
D = [4G |
/(πv)]1/2, |
(9.38) |
в |
|
|
где v — скорость перемещения продукта с воздухом, м/с. |
|
|
Мощность (кВт) электродвигателя воздуходувной машины |
|
|
Nэ = АмGм / (60 · 102η), |
(9.39) |
где Ам — работа, затрачиваемая на сжатие 1 м3 воздуха и зависящая от характера процесса сжатия в воздуходувной машине (изотермическое, адиабатическое или политропическое), Дж/м3; Gм — производительность воздуходувной машины, м3/мин (можно принять Gм = 60Gв или по паспортным данным машины); η — КПД воздуходувной машины (η = 0,55–0,75).
Работа (Дж/м3), затрачиваемая на сжатие воздуха воздуходувной машиной
Ам = 230 300р0 lg(pм / р0), |
(9.40) |
где р0 — атмосферное давление, кПа (р0 = 100 кПа); pм — давление воздуха, создаваемое воздуходувной машиной, кПа
рм = αрн + рв , |
(9.41) |
где α — коэффициент, учитывающий падение давления в питателе (α = 1,15–1,25); рн — давление в начале трубопровода питателя установки или конечной всасывающей части трубопровода (у сопла), кПа; рв — падение давления в воздухопроводе от воздуходувной машины до питателя, кПа (рв = 20–30 кПа).
р |
н |
= 102(1±µv2L |
пр |
β /d)1/2 |
± Hρ |
µ /102, |
(9.42) |
|
|
|
в |
|
|
где β — поправочный коэффициент; Н — высота подъема взвеси, м (при движении материала в магистральных установках вверх — со знаком «плюс», вниз — со знаком «минус»; во всасывающих — наоборот); ρв — плотность воздуха в трубопроводе, кг/м3 (в нагнетательных установках ρв = 1,6–2,0; во всасывающих ρв = 0,8–1,0).
Поправочный коэффициент β в магистральных установках зависит от величины
S = µ v2 Lпp/d:
S · 106………………………………… |
1 |
20 |
40 |
60 |
80 |
100 |
β · 10–7………………………………… |
15,0 |
4,0 |
2,5 |
2,0 |
1,8 |
1,5 |
Во всасывающих установках принимают поправочный коэффициент β = 1,5·10–7.
924 |
ПИВОВАРЕННАЯ ИНЖЕНЕРИЯ |
|
|
9.7.4. Системы гидротранспорта
Одной из особенностей пивоваренных и безалкогольных производств является обилие жидких сред (исходная вода, промежуточные и готовые продукты), которые необходимо транспортировать как внутри цехов, так и за их пределы.
Это может осуществляться самотеком, сифонированием, передавливанием с помощью вытесняющей среды (воздуха, диоксида углерода и др.) и вакуумированием. Однако наибольшее распространение в промышленности получил способ перемещения жидкостей насосами — устройствами для напорного перемещения жидких сред, в результате сообщения им внешней энергии. (Устройства для безнапорного перемещения жидкостей не относят к насосам, а называют водоподъемными машинами.) Поэтому в оборудовании пивоваренных предприятий существенное место занимают насосы и трубопроводы, от правильной эксплуатации и исправного состояния которых зависит бесперебойная работа производства, условия труда и качество продукции.
9.7.4.1. Системы гидротранспортирования твердых продуктов
Помимо перекачивания жидких сред — сусла, пива, воды, безалкогольных напитков, минеральных вод, сиропов, моющих средств и т. п. — на пивоваренных и безалкогольных предприятиях применяют гидравлическое транспортирование твердых продуктов, например, в солодовенных производствах при перемещении ячменя на замачивание и проращивание. При этом исключается пылеобразование, зерно подвергается предварительной мойке, замачиванию и меньшему механическому повреждению. Благодаря конструктивным особенностям системы гидротранспорта проще промывать и дезинфицировать, обеспечивая требования производственной санитарии.
Однако при использовании систем гидротранспорта ячменя необходимо руководствоваться тем, чтобы высота перекачивания не превышала 8 м. Это объясняется тем, что при перекачивании на большую высоту, после воздействия резкого перепада давления зерно испытывает шок, приводящий к так называемому «наркотизированному» состоянию, в результате чего его проращивание происходит труднее и продолжительнее. Например, при высоте перекачивания 10 м продолжительность проращивания возрастает на 0,5 суток. При этом следует учитывать, что замоченный ячмень более чувствителен к резкому перепаду давлений по сравнению с сухим зерном.
Транспортные устройства для замоченного ячменя должны регулярно очищаться
идезинфицироваться. При перекачивании ячменя уклон труб в системе гидротранспорта принимают 0,05.
Гидравлический транспорт твердых продуктов основан на способности потока воды перемещать различные материалы во взвешенном состоянии. Гидросмесь движется в трубе с определенной скоростью благодаря разности давлений в начале и конце трубопровода. Напор в системе создается либо с помощью насосов, либо естественно за счет разности высотных отметок начальной и конечной точек перемещения смеси.
Гидротранспортные установки по своему назначению могут быть стационарными
ипередвижными. Дальность транспортирования может быть от нескольких метров до сотен километров. Объемы перемещений подобными установками велики, особенно в спиртовой
ипивобезалкогольной промышленности, и достигают 250 т/ч сырья.