
Операційна діяльність 2015
.pdf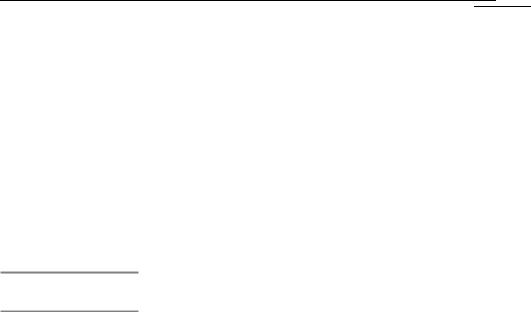
Тема 8. Організовування виробничих та сервісних процесів у часі |
241 |
|
Виробничий вузол — це найтриваліший ланцюжок взаємопов’язаних послідовних операцій робіт (тривалості виготовлення найтрудомісткішої деталі з урахуванням партіонності, складання найтрудомісткішого вузла).
На підставі схеми складання та циклового графіка виробничий цикл вузла можна записати формулою:
Тц |
к |
к |
|
(8.17) |
виробу Тці Тм.о.і max, |
||||
|
і 1 |
і 1 |
|
|
де к — кількість послідовно пов’язаних між собою процесів виготовлення деталей або складальних процесів; Тці — виробничі цикли виготовлення деталей або виконання складальних процесів; Тмоі — міжопераційні (міжциклові) перерви.
Цикловий графік дає можливість визначити термін запуску деталей у виробництво. При цьому запускаються деталі не всі водночас, а виходячи з термінів подавання їх на складання і тривалості виробничого циклу та термінів випередження запуску порівняно із випуском.
Особливість розрахунку виробничого циклу складних виробів полягає в тому, що вони запускаються на складання партіями. Партіонний метод забезпечує підвищення продуктивності праці та зниження собівартості виготовлення
продукції за рахунок: застосування найпродуктивнішого процесу; скорочення витрат ресурсів; зменшення підготовчо-завершального часу на одиницю продукції; швидкого опанування робітниками раціональних прийомів і методів складальних робіт; спрощення календарного планування виробництва.
Для забезпечення точності розрахунку виробничого циклу використовують календарно-планові нормативи: розмір партії; кількість партій, що запускаються; ритм. Використовуючи нормативні дані, послідовно визначають: час операційного циклу партій виробів за складальними одиницями; необхідну кількість робочих місць; цикловий графік складання виробів без урахування завантаження робочих місць; закріплення операцій за робочими місцями; стандарт-план складання виробу; уточнений цикловий графік з урахуванням завантаження робочих місць; тривалість виробничого циклу; випередження запуску-випуску за складальними одиницями.
В одиничному та серійному виробництвах важливо спочатку встановити економічно оптимальний розмір партії виробів, який є базовим для розрахунку інших нормативів. Відомо, що необмежене збільшення розміру партії порушує принцип безперервності, оскільки зростають, з одного боку, час пролежування кожної складальної одиниці і, відповідно, тривалість виготовлення партії, а з іншого — незавершене виробництво і додаткові площі для збереження цих складальних одиниць.
На практиці використовують спрощений метод розрахунку оптимального розміру партії. Для цього використовується відповідна таблиця.
Наприклад, на підприємстві місячна програма випуску виробу «А» становить Nвип = 700 шт. Кількість робочих днів у місяці Др = 21, режим роботи дільниці Кзм = 2 зміни. Втрати часу на планові ремонти Ар =2 % номінального фонду часу. У табл. 8.2 наведено норми часу на виконання операцій з виготовлення

242 |
|
Змістовий модуль 1 |
|
|
|
|
|
|
деталей і складання виробів, підготовчо-завершальний час, розмір подач складальних одиниць на операції. Графи 6—8 таблиці заповнюються після розрахунку показників.
|
|
|
|
|
|
|
Таблиця 8.2 |
|
|
ТЕХНОЛОГІЧНИЙ ПРОЦЕС СКЛАДАННЯ ВИРОБУ «А» |
|
||||
|
|
|
|
|
|
|
|
Позначення |
|
Штучний |
Підготовчо- |
Подача |
Розмір пар- |
Тривалість |
Тривалість |
№ |
операційного |
||||||
складаль- |
час на |
завершаль- |
складальної |
тії |
операційного |
циклу |
|
них оди- |
операції |
операцію |
ний час |
одиниці до |
виробу |
циклу партії/ |
партії |
ниць |
|
(ti), хв |
(tп-зі), хв |
операції |
(nн), шт. |
виробів, год |
складальної |
|
|
|
|
|
|
|
одиниці, год |
1 |
2 |
3 |
4 |
5 |
6 |
7 |
8 |
|
|
|
|
|
|
|
|
АБ1 |
1 |
7,0 |
20 |
3 |
100 |
12 |
12 |
АВ2 |
2 |
16,5 |
30 |
3 |
100 |
28 |
18 |
АВ |
3 |
4,7 |
10 |
11 |
100 |
8 |
8 |
|
|
|
|
|
|
|
|
АБ |
4 |
15,9 |
30 |
5 |
100 |
27 |
|
|
|
|
|
|
|
|
|
|
5 |
12,4 |
20 |
6 |
100 |
21 |
56 |
|
|
|
|
|
|
|
|
|
6 |
4,7 |
10 |
10 |
100 |
8 |
|
|
|
|
|
|
|
|
|
АА |
7 |
7,0 |
20 |
8 |
100 |
12 |
40 |
|
|
|
|
|
|
|
|
|
8 |
16,6 |
20 |
9 |
100 |
28 |
|
|
|
||||||
|
|
|
|
|
|
|
|
А |
9 |
11,3 |
10 |
11 |
100 |
19 |
|
|
|
|
|
|
|
|
|
|
10 |
7,6 |
20 |
11 |
100 |
13 |
48 |
|
|
|
|
|
|
|
|
|
11 |
9,5 |
10 |
— |
100 |
16 |
|
|
|
|
|
|
|
|
|
Усього |
|
113,2 |
200 |
— |
— |
192 |
192 |
|
|
|
|
|
|
|
|
Послідовність розрахунку така:
1. Установлення межі нормального розміру партії (nн) виробів
nmin nн nmax.
Для цього визначається розмір мінімальної партії, виходячи з затрат часу на переналагодження і поточний ремонт робочих місць ( об). Для серійного виробництва об = 0,2–0,1 %, дрібносерійного і одиничного об = 2–10 %.
|
100 |
об |
m T |
|
|
|
пmin |
|
|
п-зі |
, |
(8.18) |
|
m |
і 1 |
|
||||
|
|
|
|
|
|
обi 1Tшті
де Tп-зi — сумарний час підготовчо-завершального часу на і-ті операції виготовлення партій складальних одиниць; Tштi — сумарний штучний час на і-ті операції.

Тема 8. Організовування виробничих та сервісних процесів у часі |
243 |
|
Використовуючи дані табл. 8.2, проведемо розрахунок мінімальної величини партії:
пmin (100 2) 200 86 шт. 2 113,2
Місячна програма випуску виробів (складальних одиниць) зазвичай вважається як максимальна величина партії (у нашому прикладі пmах = 700 шт.). Коригування граничного розміру партії виробів здійснюється, виходячи з мінімального його значення. Спершу встановлюється зручний для планування ритм (Rпл) періоду черговості партій виробів за таких умов: якщо в місяці 20 робочих днів, ритмами будуть 20, 10, 5, 4, 2, 1; якщо 21 день, ритмами будуть 21, 7, 2, 1; якщо 22 дня, то відповідно — 22, 11, 2, 1.
Період чергування партій виробів розраховується за формулою:
Rпл = Др × пmin / пmах , |
(8.19) |
де Др — кількість робочих днів у місяці.
Виходячи з наведеного прикладу, цей період дорівнюватиме:
Rпл = 21 × 86 / 700 = 2,58 дня.
У разі отримання нецілого числа вибирають із зручних для планування ритмів найближче ціле число, яке і буде прийнятим періодом чергування партій
(Rпр). У даному випадку Rпр = 3 дні (з ритмів 21, 7, 3, 1).
Потім відповідно до прийнятого періоду чергування, коригуючи параметри, визначаємо розмір нормальної (оптимальної) партії за формулою:
nн = Rпр × пmах / Др = 3 × 700 / 21 = 100 шт.
Отже, виконується умова 86 100 700. Нормальний розмір партії має бути кратним місячній програмі випуску (запуску) виробів.
Кількість партій у місяці (Х) визначається таким чином:
Х = пmах / пн = 700 / 100 = 7 партій.
Результати розрахунку оптимального розміру партіїзаносимо в гр. 6 табл. 8.2. 2. Тривалість операційного циклу партій виробів за кожною операцією (tin)
розраховується за формулою:
tin = t × nн + Тп-зі / 60. |
(8.20) |
Для складальної одиниці АВ1
tin = 7 × 100 + 20 / 60 = 12 год.
Розрахунки записуються в гр. 7 табл. 7.2.
3. Тривалість операційного циклу партії виробів за складальними одиницями визначається за формулою:
|
m |
(8.21) |
Tоск.од |
tin , |
|
|
і 1 |
|
де m — кількість операцій, що входить у складальну одиницю.
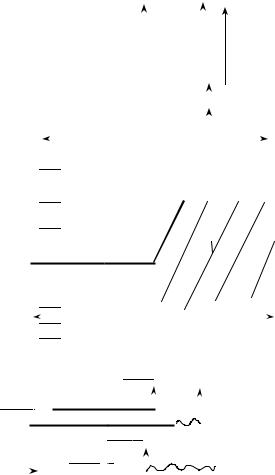

Тема 8. Організовування виробничих та сервісних процесів у часі |
245 |
|
Аналогічно здійснюються розрахунки і за іншими складальними одиницями, результати яких записуються в гр. 8 табл. 8.2.
4. Необхідну кількість робочихмісць для складаннявиробу розраховують так
РМпр = tі.шт / Тзм × S × Rпр. |
(8.22) |
У нашому прикладі РМпр = 192 / 8 × 2 × 3 = 4 робочих місця. |
|
5. Кількість робітників визначається за формулою: |
|
Чр.ск = РМпр × Кзм × Ксп, |
(8.23) |
де Кзм — коефіцієнт змінності; Ксп — коефіцієнт, що враховує спискову чисельність (можна прийняти Ксп = 1,1).
У даному прикладі: Чр.ск = 4 × 2 × 1,1 = 9 осіб.
Побудова циклового графіка складання виробу «А» (рис. 8.6) здійснюється на основі складальної схеми (рис. 8.4), тривалості циклів виготовлення та складання кожної складальної одиниці (гр. 7, 8 табл. 8.2) без урахування завантаження робочих місць.
Графік формується у зворотному порядку ходу технологічного процесу, враховуючи час завершення операцій, з яких здійснюється поставка оброблених деталей або складальних одиниць.
Наступним кроком є побудова стандарт-плану складання виробу «А», який має назву циклового графіка з урахуванням завантаження робочих місць. У стан- дарт-плані цикли окремих операцій проеціюються на відповідні робочі місця (рис. 8.6, б). Принцип пропорційності полягає у рівномірному завантаженні робочих місць і робітників. Для його дотримання здійснюється розподіл обсягу робіт по робочих місцях таким чином, щоб тривалість операційного циклу кожної з них не перевищувала їх пропускну спроможність протягом прийнятого періоду чергування партій (табл. 8.3).
|
|
РОЗРАХУНКОВІ ПАРАМЕТРИ ЦИКЛУ |
Таблиця 8.3 |
|||
|
|
|
||||
|
|
|
|
|
|
|
|
№ |
Умовне |
Сумарна |
Пропускна |
Коефіцієнт |
|
№ |
операції, |
|||||
позначення |
тривалість опе- |
спроможність |
завантаження |
|||
робочого |
що закріплена |
|||||
складальної |
раційного цик- |
робочого місця за |
робочого |
|||
місця |
за робочим |
|||||
одиниці |
лу, год |
Rпр = 48 год |
місця |
|||
|
місцем |
|||||
|
|
|
|
|
||
|
|
|
|
|
|
|
4 |
9, 10, 11 |
А |
48 |
48 |
1 |
|
|
|
|
|
|
|
|
3 |
6, 7, 8 |
АА, АБ |
48 |
48 |
1 |
|
|
|
|
|
|
|
|
2 |
4, 5 |
АБ |
48 |
48 |
1 |
|
|
|
|
|
|
|
|
1 |
1, 2, 3 |
АВ, АВ1, АВ2 |
48 |
48 |
1 |
Зміщення початку виконання робіт зазвичай пов’язане з завантаженістю робочих місць. Так, зсув початку здійснення операцій 4, 5, 6, 1 (рис. 8.6, б) збільшив тривалість виробничого циклу, спричинивши пролежування складальних одиниць. Завдання полягає в організації виробництва другої, третьої та наступної партій виробів за термінами таким чином, щоб повністю заповнити період чергування цих партій. Після цього графік називатиметься стандарт-планом.

246 |
|
Змістовий модуль 1 |
|
|
|
|
|
|
У ньому показані стандартні повторювальні терміни проведення окремих операцій складання кожним робітником.
Побудова уточненого циклового графіка складання виробу (рис. 8.6, в) дає змогу визначити фактичну тривалість виробничого циклу, яка звичайно більша мінімальної, тому що виконання окремих операцій зсунуто на більш ранні терміни. Як показано на рис. 8.6, фактична тривалість виробничого циклу складання виробу збільшилася до 96 год. Хвильова лінія показує зміщення запуску відповідних складальних одиниць АБ та АВ1.
Для планування й організації виробництва важливим календарно-плановим нормативом є випередження запуску-випуску складальних одиниць виробів. У нашому випадку його розрахунок здійснюється безпосередньо на самих графіках (рис. 8.6, а, в). Зсув запуску складальних одиниць АБ та АВ1 на раніші терміни (рис. 8.6, в) змінив випередження їх запуску-випуску. При цьому тривалість виробничого циклу стала на 8 год більшою, ніж на початковому графіку.
Для визначення повного виробничого циклу виготовлення готового виробу до циклового графіка складання додають графіки заготівельних та обробних процесів виготовлення деталей (рис. 8.7).
Поставки сировини Ж |
Виготовлення |
|
|
|
|
деталей В |
Складання |
|
|
|
|
|
вузла А |
Завершальне |
Поставки |
|
|
|
складання виробу |
|
|
|
та контроль |
|
сировини З |
|
|
|
|
Поставки |
|
|
параметрів |
|
|
|
|
||
|
деталей Г |
|
Складання |
|
|
Поставки |
|
||
|
вузла Б |
|
||
|
деталей Д |
|
|
|
Поставки |
Виготовлення |
|
|
|
сировини І |
деталей Е |
|
|
|
|
Порядковий номер тижня |
|
Рис. 8.7. Циклограма виготовлення складного виробу
Виробничий цикл складного виробу дорівнює найтривалішому ланцюжку взаємопов’язаних робіт, що послідовно виконуються (тривалості виготовлення найбільш трудомісткої деталі з урахуванням партіонності, складання найтрудомісткішого вузла і тривалості загального складання виробу).
Іншими словами, виробничий цикл складного виробу визначається найбільшою сумою циклів послідовно пов’язаних простих процесів і міжциклових перерв:
m1 |
|
m1 |
|
|
Тмці , |
Тц.скл Tці |
||
i 1 |
|
i 1 |

Тема 8. Організовування виробничих та сервісних процесів у часі |
247 |
|
де m 1 — кількість послідовно пов’язаних між собою процесів виготовлення деталей і складальних процесів; Тці — тривалість циклу виготовлення деталей або
виконання складальних процесів; Тмці — тривалість міжциклових перерв.
При виготовленні складної продукції застосовуються сітьові методи планування, і тривалість виробничого циклу визначаєтьсядовжиною критичногошляху.
8.4. ЗАХОДИ СКОРОЧЕННЯ ВИРОБНИЧОГО ЦИКЛУ
Важливість скорочення виробничого циклу визначається економічними інтересами продуцентів. Чим менша тривалість виробничого циклу, тим більше продукції за одиницю часу за інших рівних умов можна випустити на під-
приємстві, в цеху чи на дільниці; тим вище використання основних фондів підприємства; тим менша потреба підприємства в обігових коштах за рахунок прискорення їх обігу; тим більше скорочується незавершене виробництво; тим вища фондовіддача тощо.
Скорочення тривалості виробничого циклу є найважливішим напрямом скорочення незавершеного виробництва на підприємстві, зниження потреби в обігових коштах, прискорення їхньої обіговості, підвищення рентабельності продукції й активівпідприємства.
До основних напрямів зменшення тривалості виробничого циклу належать скорочення:
тривалості технологічного циклу;
тривалості виконання контрольних операцій;
часу транспортних і складських операцій;
тривалості природних процесів;
часу перерв.
Тривалість технологічного циклу може бути скорочена за рахунок:
♦удосконалення конструкції продукції, що випускається, підвищення рівня
їїтехнологічності (конструкційні зміни деталей для технологічного спрощення поверхонь, підвищення рівня уніфікації деталей, вибір раціональної заготовки);
♦заміни конструкційних матеріалів для виготовлення продукції (наприклад
металу на пластмаси);
♦упровадження новітніх високоефективних технологічних процесів (заміна обробки методом металорізання на економічний метод пластичної деформації металів, наприклад прокатка, пресування та ін.);
♦використання комп’ютерної техніки, що дає змогу обирати оптимальні режими обробки деталей;
♦підвищення рівня механізації й автоматизації виробництва, застосування робототехніки;
♦застосування ефективного спеціального й універсального оснащення, використання досконалішого інструмента, пристроїв, приладів тощо;
248 |
|
Змістовий модуль 1 |
|
|
|
|
|
|
♦зменшення підготовчо-завершального часу на переналагодження устаткування, яке доцільно виконувати в неробочі зміни, в обідні та інші перерви. У сучасній практиці скорочення періоду такої роботи досягається завдяки груповій обробці деталей, типовим і універсальним налагодженням.
Час контрольних операцій можна зменшити шляхом:
♦удосконалення методів і прийомів контролю якості продукції (перехід від суцільного контролю до вибіркового, застосовуючи статистичні методи контролю якості продукції, що значно знижує обсяги контрольних операцій);
♦упровадження засобів механізації й автоматизації контрольних операцій,
які вмонтовуються в устаткування;
♦застосування активного контролю якості (суміщення контролю за часом з технологічним циклом як на роторних автоматичних лініях, а також із часом виконання транспортних і складських операцій) та ін.;
♦застосування сучасних методів контролю і діагностики на основі лазерних
ірадіаційних установок, високочутливих контактних датчиків, що вможливлює безперервнийконтроль за перебігом технологічногопроцесу та якістю продукції.
Скорочення часу транспортних і складських операцій забезпечується:
♦механізацією та автоматизацією транспортних операцій;
♦скороченням внутрішньовиробничих маршрутів транспортування предме-
тів праці за рахунок оптимізації планування підприємства;
♦застосуванням потокових методів організації виробничого процесу;
♦переплануванням устаткування за принципом прямоточності;
♦механізації та автоматизації підйому та переміщення продукції за допомогою різних засобів.
Скорочення часу проходження природних процесів досягається за рахунок:
♦удосконалення технологічних процесів виготовлення продукції;
♦штучної інтенсифікації природних процесів (пришвидшення охолодження деталей, упровадження примусової циркуляції повітря, заміни природного сушіння фарбованих деталей індукційним сушінням у полі струмів високої частоти, застосування штучного старіння відповідальних деталей у термічних печах, використання каталізаторів тощо).
Скорочення часу перерв досягається шляхом:
♦збільшення змінності роботи підприємства, раціоналізації відпочинку робітників, застосування ефективних систем оперативно-календарного планування;
♦переходу від послідовного до паралельно-послідовного і далі до паралельного руху предметів праці (цьому сприяє організація цехів і дільниць за принципом предметної спеціалізації, яка територіально наближує різні стадії виробни-
цтва, спрощує і скорочує внутрішньозаводські та внутрішньоцехові маршрути руху заготовок і виробів). Підвищення паралельності виконання робіт скорочує технологічну трудомісткість і час на транспортування;
♦удосконалення оперативно-календарного планування та диспетчерування виробництва;
♦усунення причин незадовільної організації виробництва (аварії устаткування, недостача матеріалів, оснащення та ін.).

Тема 8. Організовування виробничих та сервісних процесів у часі |
249 |
|
У практичній діяльності підприємств скорочення тривалості виробничого циклу здійснюється одночасно за трьома основними напрямами:
зменшення часу робочого періоду (трудових процесів);
скорочення часу природних процесів;
усунення та зведення до мінімуму різних перерв.
Це забезпечується двома шляхами: а) удосконалюванням техніки і технології; б) підвищенням рівня організації виробництва.
Розроблення заходів зі скорочення виробничого циклу ґрунтується на принципах пропорційності, паралельності та безперервності.
Скорочення технологічного часу і часу перерв відбувається в результаті удо-
сконалення конструкцій продукції, що випускається, підвищення рівня її технологічності, упровадження найраціональніших високоефективних технологічних процесів.
Під удосконаленням технологічних процесів розуміють їх комплексну механіза-
цію та автоматизацію, упровадження швидкісних режимів різання, концентрацію операцій, яка передбачає багатоінструментальну й багатопредметну обробку або суміщення в одному робочому циклі кількох різнихтехнологічних операцій.
Підвищення технологічності конструкцій виробів полягає в максимальному наближенні їхніх параметрів до вимог технологічного процесу та технічних і організаційних можливостей підприємства. Наприклад, раціональне розчленування конструкції виробу на вузли та дрібні складові є важливою умовою для паралельногоскладання і, відповідно, скорочення тривалостівиробничого циклу.
З метою виявлення резервів скорочення тривалості виробничого циклу проводяться маршрутні фотографії. У результаті аналізу тривалості виробничого циклу можна виявити такі шляхи його скорочення, як зменшення розміру партії деталей, визначення порядку запуску деталей в обробку, розширення змінності роботи устаткування, оптимізація виробничого циклу під час обробки деталей кількох найменувань за рахунок визначення черговості їх запуску. Останнє завдання можна виконувати методами лінійного і динамічного програмування, послідовного конструювання за допомогою гілок і меж у вигляді дерева, матричними методами моделювання виробничого процесу.
Резюме
Вирішальне значення при розробленні виробничої програми та календарних планів виробництва продукції належить виробничому циклу, який характеризує період від запуску сировини матеріалів у виробництво до завершення виготовлення готової продукції. Скорочення його тривалості пришвидшує обіговість обігових коштів, впливає на ефективність виробничої діяльності підприємства.
Тривалість виробничого циклу складається з робочого періоду та часу перерв. Структура виробничого циклу включає технологічний цикл, тривалість допоміжних процесів (підготовчо-завершальних, контрольних і транспортно-складсь- ких операції), часу природних процесів, міжопераційних і міжцехових очіку-

250 |
|
Змістовий модуль 1 |
|
|
|
|
|
|
вань. У виробничому циклі найбільшу питому вагу має технологічний (операційний) цикл.
Розрахунок тривалості виробничого циклу визначає можливості його скорочення за рахунок зниження витрат праці на технологічні операції, паралельності (суміщення за часом) їх виконання, зменшення чи можливої ліквідації перерв. Графічна ілюстрація різних видів руху предметів праці унаочнює взаємозв’язок суміжних операцій технологічного процесу і варіантів його оптимізації. Таку можливість надають циклові графіки розрахунку тривалості виробничого циклу складного процесу.
Серед заходів скорочення тривалості циклу: зміна видів руху предметів праці за взаємозалежними операціями технологічного процесу; зниження витрат праці на технологічні операції, паралельності (суміщення за часом) їх виконання, зменшення чи можливої ліквідації перерв.
Терміни і поняття
– виробничий цикл |
– рух предметів праці за операціями |
– структура тривалості виробничо- |
(робочими місцями) |
го циклу |
– виробничийцикл простого процесу |
– операційний цикл |
– виробничий цикл складного про- |
– технологічний цикл |
цесу |
?Запитання для перевірки знань
1.Визначте сутність виробничого циклу, його призначення і сфери використання.
2.Схарактеризуйте структуру виробничого циклу й особливості впливу її елементів на тривалість циклу.
3.Від яких основних чинників залежить тривалість виробничого циклу? Поясніть їх взаємозв’язок.
4.У чому полягає економічне значення скорочення тривалості виробничого циклу?
5.Розкрийте методику розрахунку тривалості технологічного циклу при індивідуальному виготовленні продукції.
6.Охарактеризуйте особливості організації, розрахунку та доцільність застосування послідовного способу поєднання операцій.
7.Схарактеризуйте правила побудови графіка паралельно-послідовного руху предметів праці за операціями.
8.Якими способами здійснюють синхронізацію операцій і якими є її наслідки для виробничого циклу?