
геодезия конспект лекций
.pdf

В схеме, не содержащей центрального пункта (см. рис. 49, б), по сторонам треугольников находят углы γ 3' ,γ 3" и γ 3 - образующие невязку w =γ 3' + γ 3" -γ 3 и
определяют поправки в измеренные стороны ( ci ) = − 12ci wρ ;( di ) = −22( ci ).
По исправленным длинам вычисляют окончательные значения центральных углов. Контролем правильности вычислений являются нулевые невязки в фигурах
1.4.4.9. Выверка плоскостности
Операция определения плоскостности конструкции является первичной, а все другие характеристики положения плоскости (горизонтальность, параллельность и т.п.) — производными от нее.
Для определения плоскостности малых деталей обычно используют специальные калибры — эталонные плиты (проверка под краску), контрольные линейки (проверка на просвет), карусельный плоскомер и т.п.
При контроле плоскостности крупногабаритных деталей прибегают к площадной съемке (нивелирование) поверхности. Для этого на исследуемой поверхности чаще всего строят сетку квадратов или прямоугольников, и положение точек поверхности определяют пространственными координатами. Следует, однако, различать три случая примерного положения конструкции при съемке поверхности: горизонтальное, вертикальное и наклонное. В первом случае
наибольшая точность измерений предъявляется к нивелированию вершин сетки квадратов, во втором — к измерению отклонений вершин сетки от вертикали, в третьем — к измерению всех трехмерных координат с учетом величины наклона плоскости конструкции к горизонту. Третий случай является общим и наиболее сложным, но редко встречающимся в производстве, а первый и второй — частными, но наиболее простыми в реализации и, следовательно, наиболее распространенными. Если плоский элемент расположен в горизонтальной плоскости, то выполняют геометрическое или гидростатическое нивелирование, а если в отвесной, то боковое нивелирование коллимационной плоскостью
теодолита. В нивелируемых .точках устанавливают вертикально (горизонтально) нивелирную рейку по- перпендикуляру к референтной плоскости прибора.
При затруднениях в установке рейки на точке конструкции (камера, бассейн) для измерения вертикальности можно эффективно использовать рейку-копир на трехколесной тележке с подвесной отсчетной шкалой (рис. 49). На раме 3 тележки смонтировано заднее рабочее колесо 7 и симметричные относительного него два передних опорных колеса 4. На оси вращения колеса 7 укреплена на шарнире 7 отсчетная линейка 2, снабженная на конце маркировочным индексом. С линейкой 2 жестко соединен стержень, несущий на конце дат чик вертикали (маятник) 8 с демпфером. Для обеспечения работы устройства при выверке вертикальности и горизонтальности выверяемой конструкции 6 датчик вертикали снабжен переключателем, обеспечивающим установку стрежня вдоль или перпендикулярно к оси линейки. В процессе измерений заднее колесо тележки устанавливают по индексу линейки в начальной точке трассы нивелирования и, протягивая тележку по характерным точкам профиля, что фиксируется по мерному тросику 5, нивелируют поверхность в заданных точках, доступ к которым затруднен или ограничен. При выверке плоскостности высокоточного оборудования применяют оптико-механические методы, в частности, автоколлиматор и оптический плоскомер. В Последние годы апробированы и интерференционные методы.
По результатам нивелирования определяют условные отметки точек поверхности объекта. Если референтная плоскость параллельна базовым точкам плоского элемента (обычно принимают 3—4 точки, расположенные по углам детали и не находящиеся на одной прямой), то разность hi = Нi — Hусл определяет неплоскостность текущей точки поверхности. Такая характеристика неплоскостности условная, но она широко распространена в практике, особенно
при контроле положения плоских элементов оборудования относительно осей технологических линий.

Рис. 49. Нивелирная рейка на тележке: а — геометрическое нивелирование; б —
боковое нивелирование При изготовлении или сборке из готовых блоков ответственных плоских
элементов оборудования (машиностроительных .столов, станов, для формовки материалов — стекла, листовой стали, проката и др.) с целью разработки наиболее
рациональной технологии обработки деталей необходимо использовать метод оптимальной плоскости, максимально приближающейся к семейству представительных точек объекта.
1.4.4.10. Выверка кривизны
Криволинейные элементы оборудования занимают особое место в монтажном производстве и подвергаются тщательному контролю при изготовлении и монтаже. Для характеристики кривизны окружности обычно пользуются радиусом. Если же контур конструкции описывается более сложной кривой (эллипсом, параболой или радоидальной спиралью) , то кривизна задается точками в прямоугольной или полярной системе координат.
Для непосредственного измерения внутренних диаметров (лучше радиусов) малогабаритных деталей используют рулетку, нутромер с микрометрической головкой или с индикатором часового типа. В крупногабаритных деталях радиус (диаметр) измеряют либо непосредственно с помощью рулетки, либо получают косвенно из специальных измерений, используя способ "наездника" с помощью Струны и линейки. Струну известной длины хорошо натягивают, прижимают
концами к внутренним стенкам цилиндра и при помощи линейки с миллиметровыми делениями измеряют стрелу прогиба- расстояние от стенки до
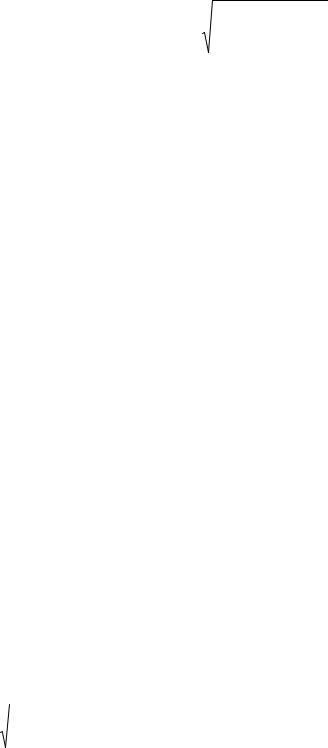
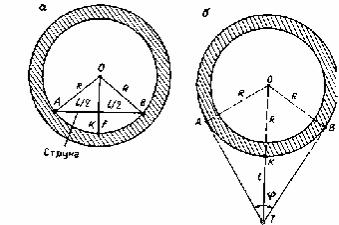
где ml и mϕ — погрешности измеряемых величин.
Рис. 50. Способы определения радиуса кривизны оболочки: а — внутреннего; б — наружного
Измерение внешнего диаметра осуществляется и способом обкатывания цилиндрической конструкции мерным роликом, например в процессе работы вращающейся печи, что отвечает рабочему состоянию деталей. Мерный ролик вводится в контакт с поверхностью детали (корпуса печи, опорного ролика) и вращается вместе с ней. При отсутствии скольжения мерного ролика по поверхности обмеряемой детали искомый диаметр вычисляют по формуле D = (п2/п1)·d, где d -диаметр мерного ролика; п2,п1— число оборотов детали и мерного ролика за время измерения.
1.4.4.11. Установка и выверка подкрановых балок и рельс
Установка
Для окончательной установки подкрановых балок по продольной оси проектную ось подкранового рельса, совпадающую с осью балки, выносят на специальные кронштейны, привариваемые над балками, или смещают ось на боковую поверхность колонны на уровне головки рельса.
При установке подкрановых путей допускается смещение оси рельса с оси балки в пределах 15 мм, а отклонение расстояния между осями подкрановых рельсов одного пролета ± 10 мм. Разбивку осей подкрановых балок (осей подкрановых рельсов) производят с обязательным соблюдением следующих условий:
а) независимо от длины подкранового пути выноска и закрепление осевых
точек должны быть произведены не менее чем в трех местах на равных расстояниях; б) при длинном подкрановом пути выноски оси производят через 100 м;
в) закрепленные осевые точки должны быть проконтролированы наблюдением их створности; от осевого створа закрепляют ось на кронштейнах или смещенную ось на колоннах не реже чем через 25 м; г) вынесенные и закрепленные оси проверяют непосредственным промером
подкранового пролета; отклонение расстояния между осями подкрановых рельсов одного пролета допускается ± 10 мм; д) после разбивки осей подкрановых рельсов второй исполнитель проверяет
правильность начальной и конечной выносок створа оси в подкрановой плоскости и выборочно - пролета между осями.
Для проверки установки балок по высоте на горизонт верха балок передают снизу через 50 - 60 м по направлению ряда колонн отметки. Рекомендуется для
лучшей увязки по высоте рельсов в пролете высоту выносить на уровень балки первого ряда, затем через 60 м - на второй ряд, через 60 м снова на первый и т. д.
Окончательную установку балок проверяют постановкой реек на верхней поверхности балок у стыков, на плече колонны и в промежутках через 5 - 7 м.
Основные отметки должны быть переданы с нижнего горизонта с точностью ± 2 мм. После исправления положения балок по высоте (допуск ± 5 мм) производят контрольную нивелировку и балки, установленные по осям и высоте, закрепляют окончательно.
При тяжелых конструкциях балки укладывают не непосредственно на плечо колонны, а на специальные балансиры, которые нивелируют перед укладкой балок.
На выверенные балки по осям, вынесенным на кронштейны, или по смещенным осям, закрепленным на боковой поверхности колонн, укладывают рельсы. После укладки положение рельсовых путей окончательно проверяют в плане и по высоте.
Плановую выверку производят, устанавливая инструмент на подкрановой плоскости в створе осевых креплений. Ось уложенного подкранового рельса привязывают к этому створу, визируя с помощью теодолита на специальную рейку- шаблон (рис. 150, а). Эту рейку накладывают на головку рельса, ее нуль-пункт совмещают с осью рельса. Отсчеты по рейке производят вертикальной нитью сетки теодолита через 5 - 10 м длины пути, определяя смещение рельса от осевого створа.
По полученным данным составляют график смещений оси рельса (см. рис. 150, б). График составляют в горизонтальном масштабе 1: 500 и вертикальном 1: 1.
Одновременно измеряют рулеткой или светодальномером типа МСД-1 расстояние между осями подкрановых рельсов также через 5 - 10 м по длине пути.
Результаты контрольных измерений показывают на сводном графике положения путей (см. рис. 150, в). Головку рельсов нивелируют, устанавливая рейку в местах опорных поверхностей колонн и на середине балки между колоннами. Исполнительный профиль пути также составляют в горизонтальном масштабе 1: 500 и вертикальном 1: 1. Разность отметок головок подкрановых рельсов в одном разрезе пролета зданий на плечах колонн допускается 15 мм, а в пролете - 20 мм.
Разность отметок подкрановых рельсов на соседних колоннах при расстоянии между колоннами l допускается - l/1000, при l< 10 м - можно допустить 10 мм.
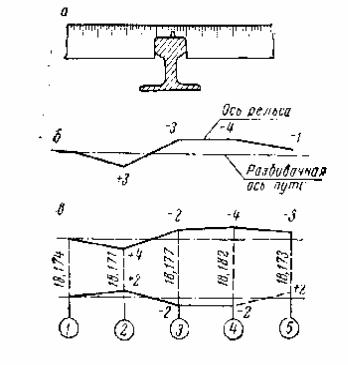
Геодезический контроль монтажа, съемка и рихтовка подкрановых путей
Контроль монтажа подкрановых путей состоит из следующих операций: нивелировка консолей колонн каркаса; перенесение осей подкрановых балок на консоли; контроль горизонтальности и прямолинейности подкрановых балок; контроль горизонтальности, прямолинейности и параллельности подкрановых рельсов.
Нивелирование консолей обычно ведется косвенным путем по высотным рискам колонн на уровне пола цеха. При этом используется геометрическое нивелирование. В связи с большим неравенством плеч в нивелирах должна быть проверена параллельность визирной оси и оси уровня.
Перенесение осей балок на консолях осуществляется от смещенных осей колонн при помощи теодолита, При отсутствии видимости на все консоли теодолит устанавливают в промежуточных точках смещенных осей. Совмещением осевых рисок торцов балок и консолей обеспечивается высокая точность монтажа.
При нивелировании подкрановых балок нивелир обычно устанавливают на самой балке, специальной консоли, прикрепляемой к колонне, на платформе крана и т. п. Нивелирование можно выполнять на каждой балке в отдельности или совместно. Однако во всех случаях для взаимной увязки отметок левой и правой балок устраивают перемычки между станциями в двух точках - на левой и правой балках. Это особенно важно для конечной стадии - монтажа подкрановых рельсов. Наверх отметка передается от рабочего репера в начале и в конце пути (на длинных путях контроль осуществляется по частям длиной 300 - 500 м). По максимальной отметке (минимальному отсчету) для обеих балок определяют толщины подкладок под рельсы, чтобы они были горизонтальны.
При контроле прямолинейности балок проверяют, чтобы элементы крепления рельсов располагались на оси балки. После крепления рельсов осуществляется окончательная выверка их горизонтальности, прямолинейности и параллельности. Горизонтальность проверяют путем нивелирования головок рельсов по схеме, аналогично балкам.
По результатам нивелирования составляют исполнительный профиль в горизонтальном масштабе 1: 100 (1: 200) и вертикальном - 1: 10. Чаще всего, для