
ПРОМЫШЛЕННАЯ ЭКОЛОГИЯ Учебное пособие
.pdf371
работы, сушка), при производстве резиновых изделий (дозаторы, смесители, на шлифовальных операциях), в промышленности по изготовлению минеральных удобрений.
Тканевые фильтры (рис. 4.13) нашли широкое применение как высокоэффективное средство борьбы с загрязнением воздуха (эффективность очистки 99 % и выше). Они могут задерживать частицы различных размеров, включая даже менее 0,5 мкм, в том числе частицы размером всего 0,01 мкм. Запыленный поток газа проходит через рукава (трубчатой формы или плоские), в которых задерживаются частицы твердых веществ. Рукава подвешены в корпусе, называемом рукавным фильтром. Его размер зависит от числа рукавов (т. е. от таких факторов, как требуемая фильтрующая поверхность и размер рукава) и необходимых зазоров между ними (исключающих взаимное трение, обеспечивающих удобство очистки и доступ для технического обслуживания). Осевшую внутри рукава пыль периодически удаляют и собирают в пылеприемнике (бункере), расположенном у основания корпуса. Принцип улавливания частиц в матерчатых фильтрах – инерционные удары, зацепление, диффузия и, возможно, электростатическое осаждение. В таких фильтрах поддаются улавливанию частицы значительно меньшего размера, чем свободное пространство в ячейках материала. Основным механизмом улавливания частиц крупнее 1 мкм являются инерционные удары о волокна фильтра; этот эффект зависит от инерции, размера частицы и размера волокон. Для частиц размером меньше 1 мкм с малой инерцией основной механизм осаждения (до определенного размера) – прямое зацепление. Он осуществляется следующим образом: по мере приближения частицы к волокну матерчатого фильтра на расстояние в пределах, равных ее радиусу, она захватывается волокном. С уменьшением размера частиц от 0,05 до 0,01 мкм начинает действовать другой механизм – диффузия, – который играет главную роль при броуновском движении крайне малых частиц. Диффузионный эффект улавливания проявляется в больших матерчатых фильтрах при низкой скорости движения потока газа.
Важным фактором, характеризующим процесс фильтрации, является скорость или коэффициент фильтрации, который представляет собой отношение расхода очищаемого газа к площади фильтрующей поверхности. Если коэффициент фильтрации слишком велик, эффективность очистки может снизиться, возникает повышенная потеря давления, ускоряется износ ткани и ее «забивание». Под «забиванием» ткани подразумевают закупоривание пор до такой степени, что ее сопротивление потоку становится чрезмерно высоким; если этот процесс начался, его остановить нельзя.
В рукавных фильтрах используют два основных вида материала – тканое полотно и войлок. Ткань выступает в роли основы для образования пористого пылевого слоя, который сам способен улавливать частицы пыли и действует, таким образом, как дополнительный фильтрующий слой. По мере его роста эффективность очистки достигает своего максимума. После установки нового рукавного фильтра с ростом пылевого слоя эффективность очистки продолжает увеличиваться. Но одновременно и повышается сопротивление проходу воздушного потока, что приводит к увеличению перепада давления. Этот перепад может достичь такого значения, когда пропускная
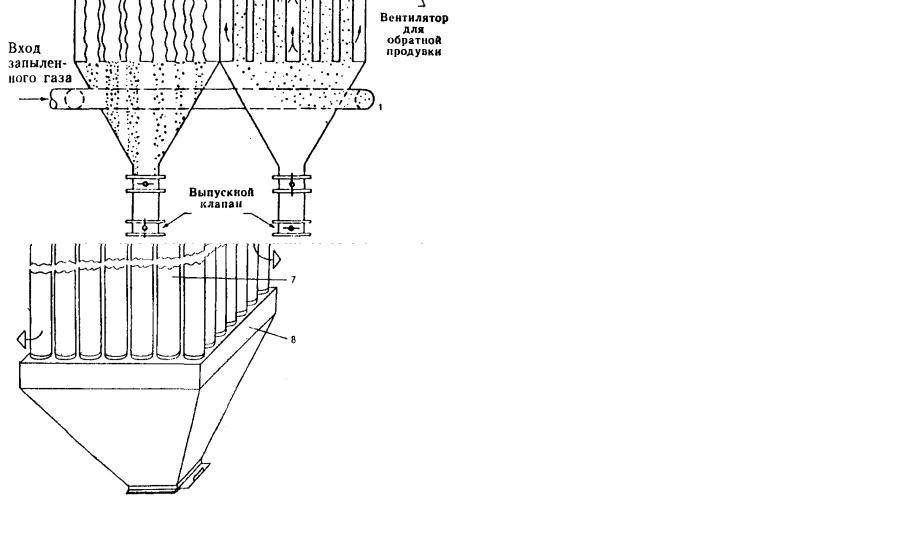
372
а |
б |
Рис. 4.13. Устройство фильтра тканевого:
а – рукавный; 1 – вентилятор; 2 – эластичная вставка; 3 – регулирующий винт; 4 – виброизолятор; 5 – стержень; 6 – коллектор; 7 – фильтровальныйрукав; 8 – бункер; б – принцип работы рукавного фильтра с обратной продувкой, действующего в отличие от механического встряхивания мягко и обеспечивающего тщательную очистку рукавов воздухом
373
способность системы падает, и рукава могут лопнуть. Для того чтобы поддерживать систему в рабочем состоянии, из рукавов периодически удаляют пыль. После удаления пылевого слоя эффективность фильтрации снижается примерно до первоначальной величины нового фильтра. В процессе эксплуатации важно правильно установить периодичность очистки (очистные циклы), чтобы наиболее полно использовать периоды максимальной эффективности улавливания и в то же время не допускать излишнего падения давления. Иногда выгодно применять механические пылеуловители в качестве фильтров предварительной очистки, так как они снижают пылевую нагрузку и могут увеличить время между циклами очистки.
Для рукавных фильтров можно использовать различные виды тканей: хлопчатобумажные, шерстяные, из стекло- и синтетических волокон, такие, как нейлон и др.
Волокнистым фильтрам пылевой слой для повышения эффективности очистки не требуется, поскольку частицы пыли проникают в поры фильтра и осаждаются в них. Пыль не может пройти через фильтрующий слой, так как войлок представляет собой массу бессистемно ориентированных тонких волокон, через которые циркулирующий воздух движется, как по лабиринту. Чистый войлок – это самый эффективный пылеуловитель. Его изготавливают из шерсти и некоторых видов синтетических волокон. Они способны улавливать мельчайшие пылинки и даже частицы дыма, что затрудняет их регенерацию. По мере осаждения частиц сопротивление фильтра растет до тех пор, пока не достигнет максимально допустимого уровня; чтобы не перейти этот предел, фильтр необходимо регенерировать. При выборе фильтрующего материала учитывают его термическую, химическую и механическую стойкость, а также характеристики улавливаемой пыли. Что касается температурных показателей, то ткани не пригодны для очистки горячих выбросов. Наиболее термостойкими являются ткани из стекловолокна, которые выдерживают температуру выброса до 288 °С. Избыточная теплота может по-разному воздействовать на ткани (разлагать, сжигать, размягчать) и даже приводить к выделению токсичных газов; эту возможность также учитывают при выборе ткани. При выборе тканей также учитывают стойкость к воздействию химических веществ, которая у разных тканей различна. Например, хлопок не обладает стойкостью к кислотам, а шерсть – кислотостойка; шерсть слабо противостоит щелочам, а хлопок – очень хорошо; орлон успешно противодействует минеральным кислотам, полипропилен – едкому натру; стекловолокно обнаруживает стойкость к кислотам и щелочам, но разъедается фтором. Поэтому при выборе тканей необходимо знать химический состав выброса (как газов, так и твердых частиц), чтобы выбрать подходящую ткань для фильтра. Для очистки некоторых коррозионноактивных выбросов требуется химически стойкая ткань. Плотность и вязкость газового потока влияют на стойкость ткани и прочность пылевого слоя.
На выбор фильтрующего материала влияют его износостойкость и механическая прочность. Например, стекловолокно обладает хорошей стойкостью к температуре, кислотам и щелочам, но слабой износостойкостью и низкой механической прочностью, что создает серьезные трудности при регенерации.
374
Применение тканевых фильтров может быть ограничено и высокой влажностью выброса. Конденсация водяных паров «забивает» ткань и в конечном итоге выводит фильтр из строя. Поэтому в процессе эксплуатации необходимо поддерживать температуру очищаемого газа выше точки росы.
Присутствие в выбросе высокогигроскопичных («липких») частиц также сокращает область применения пылеуловителей данного типа, хотя гладкая ткань в какой-то мере может помочь решению этого вопроса.
Рукавные фильтры очищают вручную, механическими и пневматическими способами. Крайне редко применяют оборудование для акустической регенерации, поскольку при этом возникают нежелательный шум. Очистку рукавных фильтров производят вручную или автоматически, непрерывно или периодически. Обычно вручную очищают небольшие фильтры (с площадью фильтрации до 46,4 м2). Механическая очистка заключается во встряхивании; рукава встряхивают в горизонтальном или вертикальном положении, вручную или с помощью электропривода. При пневматической очистке используют, например, устройство для обратной продувки, в котором имеется полое кольцо, движущееся вертикально вдоль рукава с внешней его стороны. Через щель в кольце воздух направляется на рукав, который выгибается под напором кольцеобразной струи. Очистку производят в результате совместного действия струи воздуха, проникающей внутрь рукава, и деформации ткани. В основном этот способ применяют для тканевых фильтров. Его недостатком является то, что он способствует износу ткани при движении кольца, увеличивающему эксплуатационные расходы. Любая чистка ускоряет износ материала, и поэтому ее сводят к минимуму, за исключением случаев циклических производственных процессов, когда можно отключать для регенерации всю систему, необходимо располагать рукавные фильтры секциями, которые очищают поочередно. Тогда секция, подлежащая регенерации, отключается от системы аспирации.
Достоинствами тканевых фильтров являются:
высокая эффективность улавливания для очень широкого диапазона размеров частиц, включая самые мелкие (субмикронные), близкая к 100 %;
относительно низкое гидравлическое сопротивление; коррозионная стойкость (ткань при необходимости может выдерживать
действие химических веществ); возможность очистки выбросов с большими расходами (от 10 тыс. до
500 тыс. кубических футов в минуту, или от 283 до 14 160 м3/мин). К числу недостатков относятся:
высокая первоначальная стоимость; необходимость в тщательном уходе, включая регенерацию и строгое
техническое обслуживание; слабая стойкость к высоким температурам (самая высокая стойкость у
стекловолокна – 288 °С), что ограничивает их применение для некоторых горячих выбросов или требует предварительного охлаждения;
большая занимаемая площадь (больше всех из четырех указанных типов пылеотделителей);
375
чувствительность к влажности и поэтому ограниченное применение для выбросов с высоким содержанием влаги (если нет предварительной осушки);
закупоривание гигроскопическими и слипающимися частицами; опасность воспламенения некоторых видов пыли. Тканевые фильтры
используют в резиновой, пластмассовой и химической промышленности, на некоторых горнодобывающих и литейных предприятиях, на мукомольных предприятиях, при производстве пестицидов и минеральных удобрений. Можно применять их на печах для выплавки свинца и обжига цемента, но в этом случае необходимо предварительно охлаждать выброс и использовать термостойкую ткань из стекловолокна.
В электрофильтре (рис. 4.14) выброс, содержащий твердые примеси, проходит через электрическое поле, в котором частицы приобретают заряд и притягиваются к осадительному электроду, состоящему из трубы или пластины с противоположным зарядом. Электрическое напряжение подают на коронирующий электрод, у которого возникает коронный разряд; в результате этого генерируются отрицательные ионы, адсорбируемые попавшими в электрическое поле частицами. Заряженные частицы движутся в сторону осадительного электрода (с так называемой скоростью дрейфа), к которому прилипают (здесь их заряд нейтрализуется), и держатся на нем до момента встряхивания, после чего падают в бункер, расположенный под установкой. Удаление пыли с осадительных электродов упрощают путем смыва их водой.
К основным элементам электрофильтра относятся источник тока, разрядный (коронирующий) электрод, имеющий небольшое поперечное сечение (размером с проволоку), заземленный осадительный (пассивный) электрод с развитой поверхностью осаждения (в виде трубы или пластины), корпус и приемный бункер для уловленных частиц.
Как правило, коронирующий электрод имеет отрицательный заряд, а осадительный – положительный с потенциалом земли. Разница в потенциале высоковольтных электрофильтров обычно колеблется в пределах от 60000 до
75000 В.
При проектировании или приобретении электрофильтра следует учитывать расход очищаемого выброса и его состав, характеристики твердых примесей (размер частиц, удельное сопротивление, концентрацию и т. д.) и необходимую эффективность очистки. Если расход выброса превышает проектную величину, расчетная эффективность электрофильтра падает. Эффективность возрастает с увеличением влажности и уменьшается с ростом вязкости выброса. Высокие концентрации пыли снижают эффективность электрофильтра, поэтому применяют пылеуловители предварительной очистки (например, циклоны). Важным фактором является удельное сопротивление улавливаемых частиц, от которого в значительной степени зависит эффективность очистки фильтра. До определенного предела удельное сопротивление возрастает вместе с увеличением температуры выброса (обычно от 120 до 200 °С), после чего оно начинает уменьшаться. Поэтому изменение температуры выброса отражается на эффективности электрофильтра. С увеличением влажности удельное сопротивление падает. Следовательно, водяной пар (наряду с другими увлажняющими веществами) можно использовать для по-
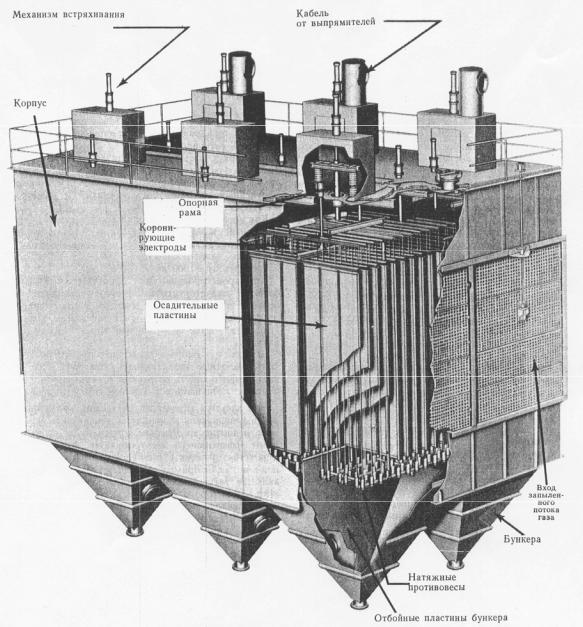
376
вышения эффективности улавливания частиц с высоким удельным сопротивлением.
Рис. 4.14. Основные элементы конструкции электрофильтра
Заряженные частицы пыли должны быстро потерять электрический заряд при контакте с осадительным электродом. Но если удельное сопротивление слишком мало, частица очень быстро теряет свой отрицательный заряд и, принимая положительный, отрывается от осадительного электрода, возвращается в ионизированный поток газа, где в присутствии отрицательных ионов снова становится отрицательно заряженной. Так, «переключая» заряды, частицы движутся через фильтр и выносятся из него. Если удельное сопротивление слишком велико, частица не отдает свой заряд осадительному электроду; на нем нарастает слой частиц, являющийся изолятором и отрицатель-
377
но влияющий на коронный разряд. При этом возникает состояние, известное под названием «обратная корона». Удельное сопротивление порядка 104 Ом
с/см или ниже, а также выше 1010 Ом с/см может снизить эффективность электрофильтра. К факторам, способствующим росту эффективности, относятся увеличение площади осадитель-ного электрода и более высокая скорость дрейфа.
Преимущества электрофильтров как средства борьбы с загрязнением атмосферы следующие:
высокая эффективность улавливания частиц любых размеров, даже микрочастиц;
улавливание как твердых, так и жидких частиц; возможность очистки больших объемов выброса; возможность очистки высокотемпературных выбросов.
Кроме того, гидравлическое сопротивление электрофильтров невелико; их можно изготавливать в случае необходимости модульными блоками с добавлением новых секций.
К недостаткам электрофильтров относятся: высокая первоначальная стоимость; большой занимаемый объем помещения; опасность, связанная с высоким напряжением;
трудности улавливания некоторых видов пыли с неблагоприятными характеристиками удельного сопротивления.
Электрофильтры нашли широкое применение на электростанциях, работающих на твердом топливе, цементных заводах, в сталеплавильных цехах (доменные и мартеновские печи).
Установки пламенного или каталитического дожигания использу-
ют для очистки выбросов, содержащих горючие газы, пары или аэрозоли, которые утилизировать экономически нецелесообразно.
Основными узлами установок пламенного дожигания являются камера сгорания (из термостойкого материала, например огнеупорного кирпича), газовые горелки, органы управления и приборы для контроля температуры. Обезвреживаемые газы в установке дожигания необходимо тщательно смешивать с факелами пламени, а в камере сгорания – уничтожать. Продукты сгорания, в основном СО2 и воду, выбрасывают в атмосферу. Сгорание должно быть полным, иначе могут образоваться нежелательные химические соединения, которые будут по-прежнему загрязнять атмосферу.
Поскольку в большинстве случаев промышленные выбросы содержат горючие вещества с концентрацией и температурой ниже их предела воспламенения, их необходимо нагреть до температуры 649–815 °С. Это требует сжигания дополнительного топлива (газов), что влечет за собой увеличение энергозатрат; именно поэтому эксплуатационные расходы таких установок довольно высоки.
Если установка сконструирована правильно, хорошо обслуживается и работает в требуемом режиме, эффективность обезвреживания выбросов превышает 90 %.
Сгорание должно быть максимально полным, что зависит от подачи достаточного количества кислорода, поддержания необходимой температуры
378
в зоне горения (как правило, от 649 до 816 °С), времени пребывания дожигаемых веществ в камере сгорания (определяется по расходу обезвреживаемого выброса), полноты смешения этих веществ с топочным газом и факелами пламени. Эти установки применяют в случаях, когда состав загрязняющих веществ в выбросе и их концентрация обеспечивают эффективное сгорание.
К преимуществам установок дожигания как средства борьбы с загрязнением атмосферы относятся:
высокая эффективность (90 % и выше); относительная универсальность по отношению к составу загрязняю-
щих веществ (если они горючие); компактность; низкое гидравлическое сопротивление;
конструктивная простота; простота технического обслуживания.
Недостатками установок дожигания являются высокие эксплуатационные затраты, связанные с расходованием газообразного топлива для получения высоких температур, стоимость которого постоянно растет. Одним из способов снижения этих затрат является утилизация тепла с помощью теплообменников или путем использования обезвреженных горячих выбросов в технологических процессах, потребляющих тепло. Пламенное дожигание может оказаться неэффективным при колебаниях расхода обезвреживаемых газов. Установки пламенного дожигания применяют как средство борьбы с загрязнением атмосферы выбросами, сопровождающими такие технологические операции, как термообработка, варка лаков, сушка краски, прокаливание кофе, обработка канализационных отходов, копчение мяса, приготовление асфальта продувкой гудрона воздухом и т. д.
Принцип действия установок каталитического дожигания в основном тот же, что и пламенных. Разница заключается в том, что с целью интенсификации процесса горения применяют катализаторы, позволяющие снизить температуру в камере горения до 263–538 °С и сократить время пребывания выбросов в ней. Следовательно, сокращается расход дополнительного топлива и повышается экономичность обезвреживания, что является одним из главных преимуществ установок каталитического дожигания. Это особенно важно, когда обезвреживают выбросы с небольшими концентрациями горючих веществ, так как применение огневого дожигания потребует большого расхода топлива.
В каждом конкретном случае тщательно подбирают тип катализатора, поверхность которого должна быть максимально большой. Часто для обезвреживания газообразных веществ в качестве катализатора используют металлы и их соли на инертном носителе. Например, сплавы платины, хромит меди, оксиды меди, хром, никель, кобальт и другие металлы на пористом носителе с высоким коэффициентом адсорбции. В качестве носителя широко применяют керамические соты, преимущество которых заключается в низком сопротивлении, обеспечении хорошего распределения выброса по поверхности катализатора, возможности обезвреживания выбросов с большими расходами и термической нестабильностью.
379
Установка каталитического дожигания состоит из камеры дожигания, в которой имеется зона предварительного нагрева и зона катализатора. Толщина слоя катализатора зависит от расхода обезвреживаемого выброса. Обезвреживаемые газы из технологического оборудования или вентиляционных систем подаются в установку вентилятором, который в данном случае способствует перемешиванию газов и их равномерному распределению по площади катализатора. Если вентилятор расположен внутри установки дожигания, его изготавливают из жаропрочного металла. Обезвреживаемые выбросы, перед тем как пропустить их через слой катализатора, предварительно нагревают до требуемой температуры.
К факторам, влияющим на процесс каталитического дожигания, относятся: состав выбросов, рабочая температура, количество подаваемого кислорода, соприкосновение с поверхностью катализатора (поскольку каталитическая реакция зависит от интенсивности диффузии молекул продуктов горения в пористой поверхности катализатора). Вещества с малой молекулярной массой реагируют быстрее благодаря более высокой скорости диффузии. Чем выше температура воспламенения вещества, тем более высокая температура необходима для полного окисления. Некоторые химические вещества отрицательно влияют на каталитическое окисление (например, Ag, As, Zn, Pb, отдельные галогензамещенные углеводороды); другие – образуют твердые оксиды.
Выбросы иногда содержат вещества, «отравляющие» катализатор. «Отравление» может происходить механическим путем или осуществляться химическими веществами, участвующими в каталитической реакции (например, фосфор и мышьяк действуют как «яд» на платиновый катализатор).
Путем периодической очистки катализатора можно уменьшить эффект «отравления»; с этой же целью используют фильтры предварительной очистки. Тем не менее, прежде чем остановить выбор на аппаратах этого типа, необходимо убедиться, что в выбросе отсутствуют вещества, которые могут вывести оборудование из строя или усложнить его эксплуатацию и техническое обслуживание.
Основное преимущество установок каталитического дожигания перед пламенными заключается в существенной экономии эксплуатационных затрат (требуется меньший расход топлива). Но затраты на техническое обслуживание довольно велики, поскольку катализатор постепенно теряет свою активность и нуждается в периодической регенерации или замене.
Недостатки: невысокая производительность, чувствительность к «ядам» (присутствие «ядов» в выбросе может служить препятствием для применения таких аппаратов) и сложность технического обслуживания. Эксплуатационные характеристики установок пламенного дожигания лучше, так как их эксплуатация не связана с проблемой катализаторов.
В качестве примера реактора каталитической очистки газа рассмотрим устройство и принцип действия автомобильного нейтрализатора выхлопных газов. Назначение нейтрализатора заключается в глубоком [не менее 90 % (об.)] окислении СО и углеводородов в широком интервале температур (250– 800 °С) в присутствии влаги, соединений серы и свинца. В нейтрализаторах обычно применяют платиновый катализатор, что обусловлено способностью

380
платины ускорять самые различные реакции. Катализаторы этого типа характеризуются низкими температурами начала эффективной работы, высокой температуростойкостью, долговечностью и способностью устойчиво работать при высоких скоростях газового потока. Основным недостатком катализаторов этого типа является их высокая стоимость.
Каталитические нейтрализаторы конструктивно состоят (рис. 4.15) из входного и выходного устройств, служащих для подвода и вывода нейтрализуемого газа, корпуса и заключенного в него реактора, представляющего собой активную зону, где и протекают каталитические реакции. Реактор- нейтрали-затор работает в условиях больших температурных перепадов, вибрационных нагрузок, агрессивной среды. Обеспечивая эффективную очистку отработанных газов, нейтрализатор по надежности не должен уступать основным узлам и агрегатам двигателя. По характеру осуществляемой в нейтрализаторах реакции они подразделяются на окислительные (называемые также дожигателями), восстановительные и трехкомпонентные или бифункциональные.
Рис. 4.15. Конструкция двухкамерного каталитического нейтрализатора:
1 – направляющие лопасти; 2 – отверстия для заполнения носителем; 3 – камера восстановления NО; 4 – подача воздуха; 5 – камера окисления CnHm и CO
В окислительных нейтрализаторах происходит окисление продуктов неполного сгорания – оксида углерода и углеводородов:
2СО + О2 2СО2;
СnНm + (n + m/4) О2 nСО2 + (m/2) Н2О.