
ПРОМЫШЛЕННАЯ ЭКОЛОГИЯ Учебное пособие
.pdf381
В восстановительных нейтрализаторах для глубокого восстановления оксидов азота необходимо, чтобы газ, поступающий в реактор, был слабо восстановленным или близким к нейтральному. В этом случае реакции восстановления оксидов азота в нейтрализаторе будут протекать достаточно полно:
2NO + 2CO N2 + 2CO2;
2NO + 2Н2 N2 + 2Н2О.
При большом содержании кислорода в обезвреживаемых газах оксид углерода и водород реагируют в основном с кислородом и эффекта очистки выхлопных газов по оксидам азота не достигается.
Принцип действия трехкомпонентных нейтрализаторов основан на одновременной и достаточно эффективной очистке (до 80 %) выхлопных газов бензиновых двигателей.
Процессы поглощения твердым телом (адсорбция) или жидкостью (абсорбция) проводят в адсорбционных и абсорбционных колоннах.
Абсорбционная колонна – это массотеплообменный аппарат для разделения газовых смесей путем избирательного поглощения их отдельных компонентов жидким абсорбентом. Применяют при осушке и очистке природных газов, в производстве серной кислоты, хлора, аммиака и пр. Абсорбция происходит на поверхности раздела сред, поэтому абсорбционные колонны имеют развитую поверхность массопередачи между жидкостью и газом, по способу образования которой их условно делят на 4 группы: поверхностные, пленочные, насадочные и барботажные.
В поверхностных абсорбционных колоннах газ проходит над поверхностью неподвижной или медленно движущейся жидкости; в более эффективных – пленочных абсорбционных колоннах контакт фаз происходит на поверхности текущей жидкости. В насадочных абсорбционных колоннах (разновидность пленочных) контакт фаз осуществляется на поверхности твердых тел различной формы, заполняющих рабочий объем аппарата, – так называемых насадках. Жидкость стекает по насадке в виде тонкой пленки, омываемой газом. Барботажные (тарельчатые) абсорбционные колонны имеют расположенные внутри колонны на определенном расстоянии друг от друга тарелки (рис. 4.16). Газ поднимается вверх и проходит сквозь слой жидкости на тарелках (через отверстия или особые устройства – клапаны). Жидкость по переливным трубам перетекает вниз с одной тарелки на другую. В распыливающих абсорбционных колоннах контакт между фазами достигается при распылении или разбрызгивании жидкости внутри колонны различными способами.
Адсорбционная колонна – это аппарат для поглощения одного или нескольких компонентов из смеси газов или раствора твердым веществом – адсорбентом. Применяют при извлечении из газов и жидкостей различных веществ, содержащихся в небольших концентрациях, летучих растворителей из их смесей с воздухом или каким-либо газом, в процессах осушения и очистки природных газов и т. п. В качестве адсорбента используют твердые пористые вещества с большой удельной поверхностью – активные угли, цеолиты, си-
382
ликагель, ионообменные смолы (иониты) и др. На поверхности или в порах адсорбента (рис. 4.17) происходит концентрирование извлекаемых компонентов. Различают адсорбционные колонны с неподвижным слоем адсорбента, в которых адсорбция осуществляется периодически (возобновляется после десорбции), и с движущимся либо «кипящим» слоем, в которых поглощение происходит непрерывно.
В адсорбционных колоннах периодического действия адсорбент располагается на горизонтальной решетке. После насыщения адсорбента, определяемого по началу проскока поглощаемого вещества (газа или жидкости), производится десорбция, а затем процесс возобновляется. Если в состав установок входят несколько адсорбционных колонн, то работа может быть организована по непрерывному циклу; при этом колонны работают поочередно.
В адсорбционных колоннах с движущимся слоем адсорбент непрерывно перемещается по колонне сверху вниз под действием силы тяжести, а навстречу ему поднимается газ или жидкость, при этом в верхней части происходит адсорбция, а в нижней – десорбция (под действием нагрева). Продукты десорбции выводятся из колонны. Для получения «кипящего» слоя адсорбента в адсорбционную колонну подается снизу газ. Проходя через решетку, на которой лежит слой мелкораздробленного адсорбента, газ приводит его в псевдосжиженное состояние. Адсорбент непрерывно поступает сверху, и после отработки удаляется для десорбции.
4.5. Выбор аппаратов очистки газа
При выборе типа аппаратов очистки газа учитывают следующие основные факторы:
а) характеристики выбросов, например химический состав, физикохимические свойства (коррозионную активность, плотность, гигроскопичность, температуру, воспламеняемость, электропроводимость, вязкость и т. д.), а для твердых частиц – дисперсный состав, плотность и т. д.;
б) характеристики технологического процесса, от которых зависит расход удаляемых газов, концентрации загрязняющих веществ (твердого вещества и газообразных компонентов), допустимая потеря давления в аппарате; в) эксплуатационные факторы, например наличие свободного пространства (площадь пола и высоту помещения), ограничения по материалам
оборудования (с учетом температуры, химических веществ и т. д.); г) требуемую эффективность очистки, которая обычно зависит от ха-
рактера загрязняющих веществ и местных стандартов по загрязнению воздушной среды, а также от экономической целесообразности утилизации некоторых ценных материалов (например, металлов, горючего и т. д.);
д) технико-экономические обоснования (например, потребность в электроэнергии, затраты на техническое обслуживание и ремонт и т. д.).
Следует учитывать, что при износе оборудования или его узлов эффективность очистки снижается. Поэтому важно правильно и своевременно проводить техническое обслуживание установок и аппаратов очистки газа. Как правило, расходы на эксплуатацию и техническое обслуживание в год составляют около 20 % стоимости самого очистного оборудования.

383
Рис. 4.16. Абсорбционная барботажная (тарель- |
Рис. 4.17. Адсорбционная колонна: |
чатая) колонна: |
1 – штуцер для входа газа; 2 – |
1 – дренаж; 2 – люк-лаз; 3 – глухая тарелка; 4 – |
распределитель газового потока; 3 – |
тарелки; 5 – отбойная сетка |
сетка; 4 – адсорбент; 5 – корпус; 6 – |
|
штуцер для отвода газа; 7 – люк для |
|
выгрузки адсорбента; 8 – люк для за- |
|
грузки адсорбента |
384
Пылеулавливающее оборудование, применяющееся в настоящее время для борьбы с атмосферным загрязнением, обычно разделяют на четыре основных категории по типовому признаку: инерционные пылеуловители, мокрые пылеуловители, матерчатые фильтры и электрофильтры.
Гравитационные отстойники, например пылеосадочные камеры, могут применяться для улавливания частиц относительно крупного размера, поэтому они малоэффективны при улавливании взвешенных твердых примесей и, следовательно, как средство борьбы с загрязнением воздуха могут применяться лишь в качестве первой из двух ступеней пылеулавливания.
Пылеосадочные камеры представляют собой оборудование для улавливания частиц под действием силы тяжести при резком падении скорости несущего потока газа внутри камеры. В качестве пылеуловителей первой ступени или предварительной очистки они отделяют из потока загрязненного воздуха грубые фракции пыли (> 50 мкм), например золу, шелуху от зерна, частицы тяжелых металлов и т. д.
Работа устройств механической очистки характеризуется эффективностью очистки Э, гидравлическим (аэродинамическим) сопротивлением и экономическими показателями.
Степень очистки (эффективность)
Э А1 А2 / А1 ,
где А1 и А2 – концентрация пыли в выбросах до и после очистки. Чаще всего эффективность очистки выражают в процентах.
Если очистка воздуха ведется не в одну, а в две ступени, то общая эффективность очистки
Э0 Э1 Э2 Э1 Э2 ,
где Э1 и Э2 – эффективность очистки на первый и второй ступенях. При сравнении эффективности двух аппаратов очистки, если один ап-
парат, например, задерживает в выбросах 85 % пыли, а другой 90 %, то он считается лучше первого не на 5 %, а в 1,5 раза, поскольку
100 85 1,5.
100 90
Гидравлическое сопротивление устройств механической очистки выражается в Па и есть не что иное как разность полных напоров загрязненного потока на входе в аппарат и очищенного потока на выходе.
В зависимости от содержания пыли в очищенных выбросах различают грубую, среднюю и тонкую очистку (табл. 4.32).

385
|
|
Таблица 4.32 |
|
|
|
Вид очистки |
Размер частиц пыли, мкм |
Конечная концентрация |
|
|
пыли в воздухе, мг/м3 |
Грубая |
Более 100 |
Более 50 |
Средняя |
От 10 до 100 |
От 2 до 50 |
Тонкая |
Менее 10 |
Менее 2 |
Если по санитарным нормам выбросы подвергаются средней или тонкой очистке и однократная очистка не дает требуемого результата, то выполняют двухступенчатую очистку: на первой степени применяют аппарат для грубой очистки, например батарейный циклон, а второй – для тонкой, например скруббер.
Если содержание загрязняющих веществ после второй степени очистки превышает допустимые среднесуточные концентрации, то дальнейшее снижение концентрации достигается методом рассеивания выбросов в атмосфере. Необходимая высота трубы для рассеивания равна, м,
H 0,235 G /V ПДКС.С ,
где Н – высота трубы, м; G – суммарный расход вредных веществ однонаправленного действия из трубы, кг/с; V – средняя скорость ветра, м/с; ПДКС.С. – предельно допустимая среднесуточная концентрация примеси в воздухе населенных мест, мг/м3.
Предварительно аппарат для механической очистки можно выбрать по данным, приведенным в табл. 4.33–4.34. Если требованиям к эффективности очистки удовлетворяют пылеуловители нескольких классов, то выбирается пылеуловитель низшего класса, так как чем выше класс пылеуловителя, тем выше его стоимость. Если требованиям к эффективности очистки удовлетворяют пылеуловители различных типов, выбирается пылеуловитель сухого типа. Пылеуловители сухого типа нельзя применять для очистки взрывопожароопасных пылей. Такие пыли улавливают аппаратами мокрого типа.
Выбор конкретного аппарата зависит от дисперсного состава пыли, фи- зико-химических свойств пыли, эффективности очистки, требуемой производительности, допустимого гидравлического (аэродинамического) сопротивления, температуры очищаемых выбросов. Предельно допустимая температура выбросов для пылеуловителей определяется материалом конструкции аппарата, обычно не должна превышать 400–500 °С. Предельно допустимая температура выбросов для фильтров определяется максимально допустимой температурой фильтроматериала, например: для асбестовой ткани – 90 °С, войлока – 130 °С, металлической сетки – 500 °С. Если температура очищаемых выбросов выше допустимой температуры, то загрязненный воздушный поток перед очисткой должен быть предварительно охлажден до допустимой температуры, например разбавлением за счет подсоса воздуха.
386
|
Исходные данные к выбору пылеуловителя |
|
Таблица 4.33 |
|||||||||||||
|
|
|
|
|||||||||||||
|
|
|
|
|
|
|
|
|
|
|
|
|
|
|
||
Класс |
|
Размер частиц |
|
Группа пыли |
|
Эффективность |
||||||||||
пылеуловителя |
|
|
пыли, мкм |
|
по дисперсности |
|
||||||||||
1 |
|
|
2 |
|
|
|
|
3 |
|
|
|
|
|
4 |
||
I |
|
|
0,3–0,5 |
|
|
|
|
V |
|
|
|
|
|
0,8 |
||
|
|
|
|
|
|
|
|
IV |
|
|
|
|
0,999–0,8 |
|||
II |
|
|
2 |
|
|
|
|
IV |
|
|
|
|
0,92–0,45 |
|||
|
|
|
|
|
|
|
|
III |
|
|
|
|
0,999–0,92 |
|||
III |
|
|
4 |
|
|
|
|
III |
|
|
|
|
0,999–0,8 |
|||
|
|
|
|
|
|
|
|
|
II |
|
|
|
|
|
0,99 |
|
IV |
|
|
8 |
|
|
|
|
|
II |
|
|
|
|
0,999–0,95 |
||
|
|
|
|
|
|
|
|
|
I |
|
|
|
|
|
0,999 |
|
V |
|
|
20 |
|
|
|
|
|
I |
|
|
|
|
|
0,99 |
|
Классы пылеуловителей и их характеристики |
|
Таблица 4.34 |
||||||||||||||
|
|
|
||||||||||||||
|
|
|
|
|
|
|
|
|
|
|
|
|
||||
Тип |
|
|
|
Класс пы- |
|
|
Группа пыли |
|
|
Сопротив- |
||||||
пылеуловителя |
|
леулови- |
по дисперсности |
|
ление, Па |
|||||||||||
|
|
|
|
теля |
I |
|
II |
III |
|
IV |
V |
|
|
|||
Пылеосадительные камеры |
|
V |
+ |
|
+ |
|
|
|
|
|
|
100–200 |
||||
Жалюзийные пылеуловители |
|
V |
+ |
|
+ |
|
|
|
|
|
|
250–500 |
||||
Циклоны большой пропуск- |
|
|
|
|
|
|
|
|
|
|
|
|
|
|||
ной способности: |
|
|
V |
+ |
|
+ |
|
|
|
|
|
|
400–600 |
|||
одиночные |
|
|
|
|
|
|
|
|
|
|
|
|||||
групповые |
|
|
|
|
IV |
|
|
+ |
+ |
|
|
|
|
|
50–700 |
|
Циклоны высокой эффектив- |
|
|
|
|
|
|
|
|
1200–2000 |
|||||||
ности |
|
|
|
|
II |
|
|
|
+ |
|
+ |
|
|
1200–2000 |
||
Рукавные тканевые фильтры |
|
|
|
|
|
|
|
|||||||||
Волокнистые фильтры |
|
|
II |
|
|
|
|
|
+ |
+ |
|
600–1000 |
||||
Электрофильтры |
|
|
|
|
II |
|
|
|
|
|
+ |
|
50–100 |
Для определения дисперсного состава используют различные приборы
– ротационные анализаторы, импакторы и др. В качестве примера на рис. 4.20 показан импактор НИИОГаз, в который запыленный воздух проходит через ряд последовательно установленных сопел уменьшающегося диаметра. Пылевые частицы оседают на расположенные под каждым соплом плоские поверхности (подложки), покрытые специальной смазкой. Сочетание сопла и подложки принято называть ступенью (каскадом) прибора. Связь между скоростью воздушного потока, проходящего через сопла, и размерами оседающих на подложках частиц позволяет судить о дисперсности исследуемой пыли. Для улавливания мелких частиц, не осевших на последнюю положку, служит фильтр. Анализируемая пыль оказывается разделенной на фракции, число которых равно числу ступеней импактора. Анализы дисперсного со-
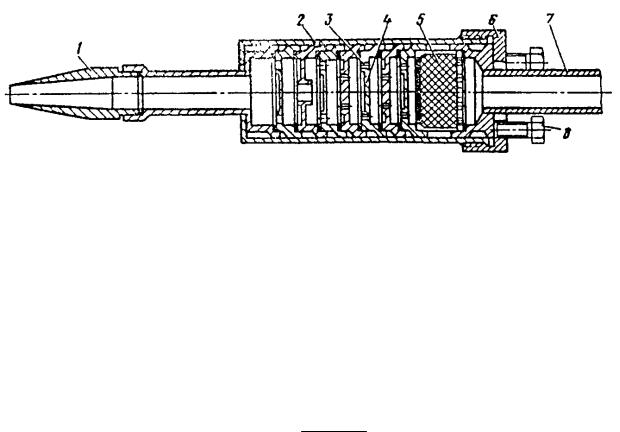
387
става пыли, выполняемые при помощи импактора, сводятся к нахождению доли частиц, осевших на каждой его ступени.
Основные виды расчетов при проектировании обеспыливающих установок:
вычисление общей степени очистки воздуха в пылеуловителе, исходя из заданных условий;
Рис. 4.20. Импактор НИИОГаз:
1 – наконечник; 2 – корпус; 3 – сопло; 4 – подложка; 5 – фильтр; 6 – крышка; 7 – отсосная трубка; 8 – поджимной болт
определение режима работы пылеуловителя (скорость воздуха, гидравлическое сопротивление), в зависимости от требуемой степени очистки воздуха от пыли.
Вычисление степеней очистки производят, исходя:
из фракционных степеней очистки, дисперсного состава и плотности частиц пыли на входе в аппарат, дисперсного состава и плотности частиц на входе в аппарат по формуле:
i n Rni фi ,
i1 100
где Rni – доля массы i-той фракции пыли, поступившей в пылеуловитель;фi – фракционная степень очистки i-той фракции пыли;
гидравлического сопротивления P, Па, дисперсного состава и плот-
ности частиц пыли на входе в аппарат.
Расчет степени очистки воздуха в пылеуловителе по P основан на экспериментально установленной зависимости диаметра частиц, улавливае-
мых на 50 % ( = 50) от P .
Гидравлическое сопротивление пылеуловителя P определяют как разность полных давлений на входе и выходеиз него.
Для определения режима работы пылеуловителя необходимы следующие данные:
о концентрации пыли в воздухе, поступающем в аппарат очистки Zн, и допускаемую концентрацию пыли в воздухе Zк, выбрасываемом в атмосферу;
параметры пыли 50, , Qт;

388
температуру t или вязкость поступающего в аппарат очистки воздуха. Требуемая степень очистки воздуха в пылеуловителе, %,
тр ZнZ Zk 100.
н
Определение режима работы пылеуловителя производят по номограммам в обратном по сравнению с расчетом общей степени очистки.
4.6. Требования к эксплуатации и обслуживанию установок очистки газа
Администрация предприятий, учреждений и организаций обязана:
а) назначить приказом (распоряжением) лицо, ответственное за эксплуатацию и обслуживание установок очистки газа по цехам (участкам);
б) разработать должностные инструкции для персонала, занятого эксплуатацией и обслуживанием установок очистки газа;
в) организовать техническую учебу и проверку знаний инженернотехнических работников и персонала, занятого эксплуатацией и обслуживанием установок очистки газа;
г) выделять своего компетентного специалиста для участия совместно с представителем Госсанэпиднадзора в обследовании установок, предоставлять необходимую техническую документацию и информацию о выполнении запланированных мероприятий по улучшению эксплуатации и обслуживания установок очистки газа;
д) обеспечивать инспектора Госсанэпиднадзора на период обследования соответствующей спецодеждой, служебным помещением, машинописными работами, транспортом и гостиницей, а на предприятии с особо вредными и тяжелыми условиями труда и спецпитанием;
е) обеспечить безопасность работы инспектора Госсанэпиднадзора на территории предприятия в соответствии с законодательством;
ж) представлять по требованию инспектора Госсанэпиднадзора анкетные данные должностных лиц, виновных в нарушении правил эксплуатации установок очистки газа для составления протокола.
Инструкция по эксплуатации и обслуживанию установок очистки газа – это документ, регламентирующий правила эксплуатации и обслуживанию установок очистки газа, и содержащий:
а) схему устройства и управления установки; б) технические характеристики аппаратов очистки газа, входящих в со-
став установки; в) сведения о предусмотренных проектом приборах контроля и автома-
тики;
г) оптимальные технико-экономические параметры работы установки, а также допустимые их отклонения, предусмотренные проектом или полученные в процессе пусконаладочных работ и согласованные с организациейразработчиком проекта;
389
д) режим работы технологического оборудования, обеспечивающий оптимальные параметры эксплуатации установки;
е) перечень учетно-отчетной документации по эксплуатации и обслуживанию установки с указанием периодичности ее заполнения;
ж) порядок пуска, остановки и обслуживания установки; з) перечень быстроизнашивающихся узлов и наиболее часто встре-
чающихся неисправностей с указанием способов их, устранения; и) порядок действия персонала в аварийных ситуациях (на технологи-
ческом оборудовании и на установках очистки газа; к) правила безопасности при эксплуатации и обслуживании установок
с перечнем вспомогательных устройств и инвентаря для эксплуатации и обслуживания установки (площадки, ограждения, приспособления, средства пожаротушения и индивидуальной защиты, предупреждающие и запрещающие плакаты, заземляющие устройства и т. д.);
л) схему размещения точек для измерения параметров работы установок очистки газа.
Должностное лицо, ответственное за эксплуатацию и обслуживание установок очистки газа обязано обеспечить:
а) соблюдение правил эксплуатации установок очистки газа и инструкций по эксплуатации и обслуживанию установок;
б) своевременное проведение текущих и капитальных ремонтов и реконструкции установок;
в) содержание в исправном состоянии пробоотборных устройств; г) ведение учетно-отчетной документации по эксплуатации и обслужи-
ванию установок; д) своевременное выполнение инспектора Госсанэпиднадзора.
Установки очистки газа должны работать надежно, бесперебойно и с показателями, соответствующими проектным или тем, которые получены в результате наладочных работ, и согласованными с организацией – разработчиком проекта. При эксплуатации установок очистки газа ведут документацию, содержащую основные показатели, характеризующие режим работы установки (отклонения от оптимального режима, обнаруженные неисправности, случаи отклонения отдельных агрегатов или выход из строя всей установки и т. д.). Все установки очистки газа регистрируют в органах Госсанэпиднадзора. Для регистрации установки очистки газа представляют:
паспорт установки очистки газа; акт приемки оборудования.
При регистрации установок, находящихся в эксплуатации, представляют акт, характеризующий их состояние и график работ по устранению имеющихся недостатков. Акт подписывают члены комиссии, созданной приказом руководителя предприятия, учреждения и организации. Регистрацию оформляют соответствующей записью в паспорте установки и документе регистрации органа Госсанэпиднадзора. Регистрационный номер наносят на корпус установки очистки газа с размером надписи 200х150 мм. Допускается нанесение регистрационного номера на табличке. Снятие с регистрации установки очистки газа производят в случае ликвидации технологического оборудования, за которым находилась данная установка на основании акта о
390
ликвидации основных средств по форме ОС-4. Регистрацию установок после реконструкция (модернизации) осуществляют в установленном правилами порядке с сохранением регистрационного номера.
Установки очистки газа должны подвергаться осмотру для оценки их технического состояния не реже одного раза в полугодие комиссией, назначенной руководством предприятия. По результатам осмотра составляют акт и при необходимости разрабатывают мероприятия по устранению обнаруженных недостатков. Акт прилагают к паспорту установки.
Установки очистки газа подвергают проверке на соответствие фактических параметров работы установок проектным не реже одного раза в год (установки с высоким содержанием токсичных примесей – не реже 2-х раз в год), а также в следующих случаях:
при работе технологического оборудования на измененном режиме более 3-х мес. или при переводе его на новый постоянный режим работы;
после строительства, капитального ремонта или реконструкции установки.
Результаты проверки оформляют актом и заносят в паспорт установки. В случае несоответствия работы установки проектным параметрам, принимают необходимые меры для наладки установки, ее реконструкции или замены.
Эксплуатация технологического оборудования при отключенных установках очистки газа запрещается. При каждом случае отключения установок очистки газа при работающем технологическом оборудовании, руководство предприятия, учреждения и организации обязано оповещать органы Госсанэпиднадзора, получить согласованное разрешение на выброс, представив технические решения по сокращению выбросов загрязняющих веществ в атмосферу. Увеличение производительности технологических агрегатов без соответствующего наращивания мощности существующих установок очистки газа запрещается. При эксплуатации установок, предназначенных для очистки газа с высоким содержанием горючих (взрывоопасных) компонентов, следует особо тщательно обеспечивать поддержание установленных параметров давления газа и герметичности сооружений, а также правильную; продувку коммуникаций и аппаратов во избежание взрыва и пожара. Одновременно предусматривают ограждение источников открытого огня и соблюдение требований специальных инструкций и правил. При эксплуатации установок, предназначенных для очистки газа с высоким содержанием токсичных примесей, особо тщательно обеспечивают герметичность сооружения, а также применение в необходимых случаях газозащитных средств и соблюдение требований специальных инструкций и правил. При эксплуатации установок, предназначенных для очистки газа от химически агрессивных или абразивных компонентов, следят за целостностью защитных покрытий и отсутствием разрушений металлоконструкций и оборудования, предупреждая тем самым преждевременный выход из строя установок очистки газа.
Ремонт установок очистки газа производят при остановленном технологическом агрегате.