
Ермолаев Технологические процессы в машиностроении 2011
.pdf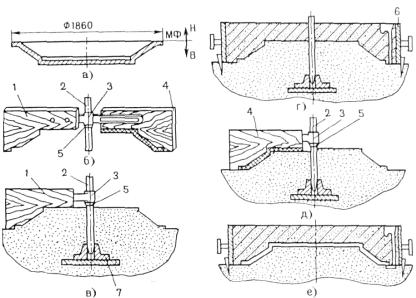
навливают стержень и накрывают нижнюю полуформу верхней. После заливки расплавленного металла и его затвердевания литейную форму разрушают и извлекают отливку.
Формовку шаблонами применяют в единичном производстве для получения отливок, имеющих конфигурацию тел вращения. Для примера рассмотрим технологический процесс изготовления форм для шлаковой чаши (рис. 3.3, а).
Рис. 3.3. Шаблонная формовка
Формовку осуществляют с помощью шаблонов 1, 4 (рис. 3.3, б); в яме устанавливают подпятник 7 со шпинделем 2 в вертикальном положении, засыпают формовочную смесь и уплотняют ее вокруг шпинделя; к серьге 3 прикрепляют шаблон 1, режущая кромка которой имеет очертания наружной поверхности отливки, и устанавливают его на шпиндель (рис. 3.3, в) до упора 5; вращением шаблона в ту и другую сторону срезают формовочную смесь в соответствии с профилем шаблона, удаляя излишки формовочной смеси; по полученному болвану изготавливают верхнюю полуформу 6 (рис. 3.3, г). Для этого серьгу с шаблоном снимают со шпинделя,
61

плоскость разъема формы покрывают разделительным слоем сухого кварцевого песка или бумагой, устанавливают модели литниковой системы, опоку, засыпают формовочную смесь и уплотняют ее, удаляют шпиндель и снимают верхнюю полуформу.
В подпятник 7 вновь устанавливают шпиндель, на который с помощью серьги устанавливают шаблон 4 (рис. 3.3, д), имеющий очертания внутренней поверхности отливки. С помощью этого шаблона с болвана удаляется слой формовочной смеси на толщину стенки отливки (рис. 3.3, д); после этого снимают шаблон и удаляют шпиндель, отделывают полученный болван и устанавливают верхнюю полуформу (рис. 3.3, е). Затем в литейную форму заливают расплавленный металл.
Формовку в кессонах применяют при изготовлении крупных отливок массой до 200 т. На рис. 3.4 показана форма станины, собранная в механизированном кессоне, который смонтирован на бетонном основании 7. Дно его выложено чугунными плитами 4.
Рис. 3.4. Формовка в кессонах
62

Две неподвижные стенки 1 и 8 также облицованы металлическими плитами. Противоположные чугунные стенки 3 и 6 передвигаются с помощью червячного редуктора 2, приводимого в действие электродвигателем, что позволяет изменять внутренние размеры кессона. Форму собирают из стержней-блоков 5, изготовленных из жидких самотвердеющих смесей. Литниковую систему изготовляют из керамических огнеупорных трубок. Верхнюю полуформу 10 устанавливают по центрирующим штырям 9 и прикрепляю к кессону болтами.
Формовку в стержнях применяют в массовом и крупносерийном производствах при изготовлении отливок сложной конфигурации. На рис. 3.5 приведен пример формовки в стержнях цилиндра двигателя с воздушным охлаждением. Форма для отливки цилиндра двигателя с воздушным охлаждением собрана из шести стержней.
Сборку формы производят в горизонтальном положении. В стержень 1 вкладывают стержень 2, затем стержни 3, 4, 5 и 6. Собранную форму скрепляют.
Формовку с использованием
жидкостекольных смесей при-
меняют при изготовлении отливок массой до 40 т в серийном и единичном производствах. При
формовке на модель слоем 50–70 |
Рис. 3.5. Формовка в стержнях |
|
мм наносят слой жидкостеколь- |
цилиндра двигателя |
|
с воздушным охлаждением |
||
ной формовочной смеси, осталь- |
||
|
ной объем опоки заполняют наполнительной формовочной смесью и уплотняют. После изготовления полуформы модели извлекают. Полуформы накрывают зонтом, под который под давлением 0,2– 0,3 МПа подводится углекислый газ, обеспечивающий быстрое равномерное отвердение формы.
Машинную формовку применяют для производства отливок в массовом и серийном производствах. При формовке на машинах формы изготовляют в парных опоках с использованием односторон-
63
них металлических модельных плит). Машинная формовка механизирует установку опок на машину, засыпку формовочной смеси в опоку, уплотнение смеси, удаление моделей из формы, транспортирование и сборку форм. Машинная формовка обеспечивает более высокую геометрическую точность полости формы, чем ручная формовка, повышает производительность труда, исключает трудоемкие ручные операции, сокращает цикл изготовления отливок. При машинной формовке формовочную смесь уплотняют прессованием, встряхиванием, пескометом, вакуумной формовкой и др.
Уплотнение формовочной смеси прессованием осуществляют при подаче сжатого воздуха при давлении 0,5 – 0,8 МПа в нижнюю часть цилиндра, в результате чего прессовый поршень, стол с прикрепленной к нему модельной плитой поднимаются. При этом колодка, закрепленная на траверсе, входит внутрь наполнительной рамки и уплотняет формовочную смесь в опоке. Плотность формовочной смеси уменьшается по мере удаления от прессовой колодки из-за трения формовочной смеси о стенки опоки. Неравномерность плотности формовочной смеси тем больше, чем выше опока и модели. Прессование используют для уплотнения формовочной смеси в опоках высотой 200–250 мм.
Для достижения равномерной плотности формовочной смеси в опоке используют многоплунжерные прессовые колодки. При прессовании стол машины движется в сторону многоплунжерной прессовой колодки. Вследствие различной степени сопротивления формовочной смеси в форме плунжеры под действием давления масла на поршень прессуют находящиеся под ним участки формы независимо от соседних.
Уплотнение формовочной смеси встряхиванием осуществляют при подаче сжатого воздуха при давлении 0,5–0,8 МПа в нижнюю часть цилиндра, в результате чего встряхивающий поршень 2 поднимается на высоту 25–80 мм. При этом впускное отверстие перекрывается боковой поверхностью поршня, а нижняя его кромка открывает выхлопные окна, воздух выходит в атмосферу. Давление под поршнем снижается, и стол с укрепленной на нем модельной плитой падает на торец цилиндра. Скорость стола, а следовательно, и скорость модельной плиты падают до нуля, в то время как формовочная смесь в опоке и наполнительной рамке, продолжая дви-
64
гаться вниз по инерции, уплотняется. В момент, когда канал встряхивающего поршня оказывается напротив отверстия встряхивающего цилиндра, сжатый воздух снова входит в полость встряхивающего цилиндра. Это влечет за собой новый подъем встряхивающего стола и новый удар его о торец и т. д.
Встряхивающий стол обычно совершает 120–200 ударов в минуту. В результате повторных ударов происходит уплотнение формовочной смеси в опоке. При этом слои формовочной смеси, лежащие у модельной плиты, будут иметь большую плотность, чем слои, лежащие в верхней части формы. Встряхиванием уплотняют формы высотой до 800 мм. Для уплотнения верхних слоев формы встряхивание совмещают с прессованием. Это обеспечивает высокую и равномерную плотность форм.
Уплотнение формовочной смеси пескометом осуществляют рабочим органом пескомета – метательной головкой, выбрасывающей пакеты смеси на рабочую поверхность модельной плиты. В стальном кожухе метательной головки вращается закрепленный на валу электродвигателя ротор с ковшом. Формовочная смесь подается в головку непрерывно ленточным конвейером через окно в задней стенке кожуха.
При вращении ковша (1000–1200 об/мин) формовочная смесь собирается в пакеты и центробежной силой выбрасывается через выходное отверстие в опоку. Попадая на модель и модельную плиту, смесь уплотняется за счет кинетической энергии равномерно по высоте опоки. Метательную головку равномерно перемещают над опокой. Пескомет является высокопроизводительной машиной, поэтому его применяют для уплотнения крупных литейных форм. Управление работой пескомета автоматизировано.
Автоматическую формовку используют в серийном и массовом производствах отливок, при этом литейная форма передается последовательно с одной позиции на другую. Этот переход осуществляется автоматически различными конвейерами, кантователями, толкателями и другими устройствами. Для автоматической формовки используются формовочные автоматы, формовочные машины для безопочной формовки и автоматические формовочные линии.
65
Формовочные автоматы для изготовления литейных форм выполняют все технологические операции без участия человека и используются, как правило, в составе автоматических линий.
Автоматическую безопочную формовку используют при изготовлении форм для мелких отливок из серого, ковкого и высокопрочного чугунов и стали в серийном и массовом производствах. Изготовление литейных форм осуществляется на высокопроизводительных пескодувно-прессовых автоматических линиях.
Модельная плита закрепляется на прессовой машине, плита – на плите противодавления. Модельные плиты, боковые стенки и головка образуют формовочную камеру, которая заполняется формовочной смесью с помощью сжатого воздуха под давлением 0,5–1 МПа. После этого формовочная смесь прессуется плунжером под давлением до 2 МПа. Модельная плита отходит влево и поворачивается в горизонтальное положение, а уплотненный ком формовочной смеси плунжером проталкивается до соприкосновения с предыдущим комом, образуя полость. В результате получается непрерывный ряд форм, которые заливают расплавленным металлом из ковша. После затвердевания и охлаждения отливок формы подаются на выбивную решетку, где отливки освобождаются от формовочной смеси. Смесь поступает на переработку и повторное использование, а отливки – в обрубное отделение.
Автоматическая формовочная линия – пример полного автоматизированного производственного процесса формовки.
Нижняя полуформа, изготовленная на формовочном автомате, кантователем переворачивается на 180° и на позиции устанавливается на предварительно очищенную специальными щетками тележку литейного конвейера и подается к механизму спаривания полуформ. Верхняя полуформа, изготовленная на автомате, по роликовому конвейеру перемещается к позиции, где спаривается с нижней полуформой. Собранная литейная форма по конвейеру транспортируется на участок заливки. Установка стержней в литейную форму осуществляется во время продвижения ее по конвейеру позиции к позиции. Для увеличения продолжительности охлаждения отливок в залитых формах конвейер выполнен с дополнительной петлей на двух уровнях.
66
3.3. Получение отливок
Расплавленный металл из печи поступает в разливочный ковш. Ковш изготовляют из железа и футеруют огнеупорными материалами. Ковши бывают различных конструкций, форм и емкостей. Металл поступает в хорошо просушенный и подогретый (в зависимости от температуры расплавленного металла) ковш. Это помогает избежать выброса металла при заливке и его быстрого охлаждения. С помощью крана, тали или других устройств ковш перемещают к месту разливки и устанавливают над формой. Затем открывают стопор или шибер (в стопорных и шиберных ковшах) или поворачивают ковш (барабанный и чайниковые) и металл подается непрерывной струёй в литниковую чашу и через литниковую систему заполняет форму.
Остывшая до определенной температуры (от 100 до 800 °С в зависимости от сплава) форма поступает на выбивку. Выбивку отливок производят с помощью пневматических или гидравлических устройств. При выбивке отливка освобождается от опоки, формовочной смеси, стержней и поступает на обрубку и очистку.
Очистку отливок производят различными способами. Способ очистки выбирается в зависимости от металла отливки, ее размера и конфигурации. Отливки простой формы очищают в галтовочных барабанах. Барабаны с отливками и чугунными «звездочками» вращаются, и за счет их соударения происходит очистка отливки. В массовом производстве применяют дробеметную очистку. В этом случае отливки помещаются в специальный барабан и перемещаются в нем с помощью замкнутого вращающегося конвейера. Дробеметная турбина выбрасывает на поверхность отливок дробь (из чугуна или стали), за счет чего происходит очистка. Применяют также ультразвуковую, электрохимическую и другие способы очистки литья.
Очищенные отливки поступают на обрубку и зачистку. Эти операции выполняют с помощью зубил, шлифовальных кругов, дуговой резкой. Очищенные отливки поступают на термообработку (при необходимости) и контроль.
Охлаждение отливок в литейных формах после заливки продолжается до температуры выбивки. Небольшие тонкостенные от-
67
ливки охлаждаются в форме несколько минут, а толстостенные массой 50–60 т – в течение нескольких суток и даже недель. Для сокращения продолжительности охлаждения отливок, особенно массивных, используют различные методы принудительного охлаждения: формы обдувают воздухом; в формы при формовке укладывают змеевики или трубы, по которым пропускают воздух или воду. При этом качество отливок не ухудшается.
3.4. Методы литья и области их применения
Технологический процесс изготовления отливок состоит из ряда основных и вспомогательных операций, выполняемых в определенной последовательности. Для изготовления литейных форм используются модельный комплект, формовочные и стержневые смеси и другие материалы и оборудование.
Сущность литья в песчаные формы. В настоящее время литье в песчаные формы является универсальным и самым распространенным способом изготовления отливок. Этим способом изготовляют разнообразные по сложности отливки любой массы и размеров из сталей, чугунов и сплавов цветных металлов.
Сущность литья в песчаные формы заключается в изготовлении отливок свободной заливкой расплавленного металла в разовую разъемную и толстостенную литейную форму, изготовленную из формовочной смеси по многократно используемым молельным комплектам (деревянным или металлическим), с последующим затвердеванием залитого металла, охлаждением отливки в форме, извлечением ее из формы с последующей отделкой
Отличительными особенностями способа являются малые теплопроводность, теплоемкость и плотность песчаной формы, что позволяет получать отливки с малой толщиной стенки (2,5–5 мм): невысокая интенсивность охлаждения расплава
В форме приводит к снижению скорости затвердевания отливки, укрупнению структуры и к появлению в массивных узлах усадочных раковин и пористости; сравнительно низкая огнеупорность материала способствует развитию на поверхности контакта форма - отливка физико-химических процессов, которые могут приводить к появлению пригара в поверхностном слое отливки.
68

Для изготовления отливок используют сырые, сухие и подсушенные песчаные формы; химически твердеющие формы, изготовленные из специальных сам отвердевающих смесей: формы, изготовленные по газифицируемым моделям; формы, изготовленные из песчано-смоляных смесей по металлической нагреваемой оснастке и др.
Технологический процесс изготовления отливок состоит из ряда основных и вспомогательных операций, выполняемых в определенной последовательности (рис. 3.6). Для изготовления литейных форм используются модельный комплект, формовочные и стержневые смеси и другие материалы и оборудование.
Рис. 3.6. Схема технологического процесса получения отливок в песчаных формах
Точность геометрических размеров, шероховатость поверхности отливок, полученных в песчаных формах, во многих случаях не удовлетворяют требованиям современной техники. Поэтому быстрыми темпами развиваются специальные способы литья: в оболочковые формы, по выплавляемым моделям, кокильное, под давлением, центробежное и другие, позволяющие получать отливки повышенной точности, с малой шероховатостью поверхности, минимальными припусками на механическую обработку, а иногда полностью исключающие ее, что обеспечивает высокую производительность труда и т. д.
69

Молельный комплект – это совокупность технологической оснастки и приспособлений, необходимых для образования в форме полости, соответствующей контурам отливки. В молельный комплект включают модели, модельные плиты, стержневые ящики и другие приспособления.
Литейная модель (рис. 3.7, а) – приспособление, с помощью которого в литейной форме получают полость с формой и размерами, близкими к конфигурации получаемой отливки. Модели бывают неразъемные, с отъемными частями и др.
Модельная плита (рис 3.7, б) – металлическая плита с закрепленными на ней моделями и элементами литниковой системы. Ее применяют, как правило, при машинной формовке.
Рис. 3.7. Литейная модель (а), модельная плита (б) и стержневой ящик (в) для корпуса вентиля:
1 – центрующие шипы; 2 – стержневые знаки; 3 – центрирующие штыри; 4 – металлическая плита; 5 – модели отливок; 6 – модели элементов литниковой системы
Стержневой ящик (рис. 3.7, в) – приспособление, служащее для изготовления стержней. Стержневые ящики бывают цельные, разъемные, вытряхные и др.
Исходным документом для разработки чертежа модельнолитейных указаний является чертеж детали (см. рис. 3.8, а) на котором указаны: разъем модели и формы, положение отливки в форме при разливке, припуски на механическою обработку, формовочные уклоны, число стержней, размеры стержневых знаков, границы стержней и т.п. Оформление чертежей элементов литейной формы и отливки осуществляется по ГОСТ 3.1125-88.
70