
Ермолаев Технологические процессы в машиностроении 2011
.pdf
лей топливной аппаратуры двигателей внутреннего сгорания, сеток и сит, а также для упрочнения поверхностного слоя металлов деталей машин, пресс-форм, режущего инструмента.
Рис. 9.2. Схемы электроискровой обработки:
а– прошивание отверстия; б – обработка фасонной полости штампа;
в– прошивание отверстия по способу трепанации; г – прошивание отверстия
скриволинейной осью; д – вырезание заготовки из листа; е – шлифование внутренней поверхности фильеры
Упрочнение состоит в том, что на поверхность изделий наносят тонкий слой какого-либо металла, сплава или композиционного материала. Подобные покрытия повышают твердость, износостойкость, жаростойкость, эрозионную стойкость и другие характеристики изделий.
На ограниченных участках особо на груженной поверхности детали можно проводить сложнейшие микрометаллургические процессы.
221

Из электроэрозионных станков с системами ЧПУ наибольшее распространение в промышленности имеют координатнопрошивочные, копировально-вырезные и универсальные копиро- вально-прошивочные.
Координатно-прошивочные станки работают по позиционной системе ЧПУ, что позволяет автоматически по заданной программе устанавливать (позиционировать) заготовку относительно инструмента в необходимое положение. Обработку ведут профилированным инструментом. Во время обработки заготовка перемещений не имеет.
Рис. 9.3. Схема работы копировально-вырезного станка с ЧПУ:
1 – катушка с проволокой; 2 – электродвигатель привода натяжения проволоки; 3 – генератор импульсов; 4 – проволока-инструмент; 5 – электродвигатель привода подачи проволоки; 6 и 7 – электродвигатели привода винта продольной и поперечной подач; 8 – рабочий стол станка; 9 – электронная следящая система; 10 – блок управления работой станка
Копировально-вырезные станки работают по контурной системе ЧПУ. Обработку ведут непрофилированным инструментом – бесконечным электродом-проволокой (рис. 9.3). Применяют медную, латунную, вольфрамовую, молибденовую проволоку диаметром 0,02–0,3 мм. Программное устройство станков обеспечивает не только регулирование движений формообразования, но и регулирование технологического режима – напряжения на искровом промежутке. Особенность процесса вырезки состоит в наличии пере-
222

менной эквидистанты, зависящей от ширины прорезаемого паза. Следователь но, устройства ЧПУ станков должны обеспечивать коррекцию эквидистанты. В станках такого типа системы ЧПУ обеспечивают управление по четырем и более координатным осям.
В универсальных копировально-прошивочных электроэрозионных станках используют две системы ЧПУ: систему адаптивного управления с предварительным набором координат и режимов по программе и систему адаптивно-программного управления по трем координатным осям. В станках этого типа системы ЧПУ обеспечивают планетарное движение за готовки в следящем режиме, автоматическое позиционирование заготовки и автоматическую смену инструмента.
При электроимпульсной обработке используют электрические импульсы большой длительности (2·102–105 мкс) Большие мощности импульсов, получаемых от электронных генераторов, обеспечивают высокую производительность процесса обработки. Применение генераторов и графитовых электродов, а также обработка на обратной полярности позволили уменьшить разрушение электродов.
Электроимпульсную обработку (рис. 9.4) наиболее целесообразно применять при предварительной обработке штампов, турбинных лопаток, твердо сплавных деталей, фасонных отверстий в деталях из коррозионно-стойких сталей и жаропрочных сплавов.
Рис. 9.4. Схема электроимпульсной обработки:
1 – электродвигатель; 2 – импульсный генератор; 3 – инструмент-электрод; 4 – заготовка электрод; 5 – ванна.
В станках для электроимпульсной обработки широко используют различные системы программного управления. Высокоточная
223

конструкция станков с чувствительными сервосистемами позволяет изготовлять детали сложной геометрической формы с высокой точностью.
Приборы автоматического переключения на разные подачу и глубину резания, управляемые системой ЧПУ, обеспечивают оптимальное использование электроэрозионных станков, так как в зависимости от хода процесса обработки режим работы согласуется с технологическими требованиями к деталям. Применяемые адаптивные системы программного управления позволяют своевременно определять отклонения в ходе обработки и устранять их. Изменения параметров процесса обработки вносятся в устройства формирующие сигнал коррекции, что позволяет с помощью простых электродов изготовлять детали сложных геометрических форм, в частности полостей штампов.
Высокочастотную электроискровую обработку применяют для повышения точности и уменьшения шероховатости поверхностей заготовок из твердых сплавов, обработанных электроэрозионным методом, так как он исключает структурные изменения и образование микротрещин в поверхностном слое мате риала обрабатываемой заготовки.
Рис. 9.5. Схема высокочастотной электроискровой обработки: 1 – инструмент-электрод; 2 – заготовка-электрод; 3 – импульсный трансформатор; 4 – прерыватель тока; 5 – выпрямитель
Метод основан на использовании электрических импульсов малой мощности при частоте 100–150 кГц. При высокочастотной электроискровой обработке (рис. 9.5) конденсатор С разряжается при замыкании первичной цепи импульсного трансформатора прерывателем, вакуумной лампой или тиратроном. Инструмент-
224
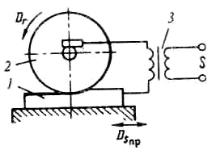
электрод и заготовка включены во вторичную цепь трансформатора, что исключает возникновение дугового разряда.
Производительность метода в 30–50 раз выше, чем при электроискровом методе, при значительном увеличении точности и уменьшении шероховатости поверхности. Износ инструмента незначителен.
Электроконтактная обработка основана на локальном нагреве заготовки в месте контакта с электродом-инструментом и удалении размягченного или даже расплавленного металла из зоны обработки механическим способом: относительным движением заготовки
иинструмента. Источником теплоты в зоне обработки служат импульсные дуговые разряды. Электроконтактную обработку оплавлением рекомендуют для обработки крупных де талей из углеродистых и легированных сталей, чугуна, цветных сплавов, тугоплавких
испециальных сплавов.
Метод применяют при зачистке отливок от заливов, отрезке литниковых систем и прибылей, зачистке проката из специальных сплавов, черновом круглом наружном, внутреннем и плоском шлифовании корпусных деталей машин из труднообрабатываемых сплавов (рисунок 23.6), шлифовании с одновременной поверхностной закалкой деталей из углеродистых сталей. Метод обработки не обеспечивает высокой точности
и качества поверхности, но дает высокую производительность съема металла вследствие использования больших электрических мощностей.
Электрохимические методы обработки деталей. Электрохи-
мические методы обработки основаны на законах анодного растворения металлов при электролизе. При прохождении электрического тока через электролит на поверхности заготовки, включенной в
225

электрическую цепь и являющейся анодом, происходят химические реакции, и поверхностный слой металла превращается в химическое соединение. Продукты электролиза переходят в раствор или удаляются механическим способом.
Производительность процессов зависит в основном от электрохимических свойств электролита, обрабатываемого токопроводящего материала и плотности тока.
Электрохимическое полирование (рис. 9.7) выполняют в ванне,
заполненной электролитом. В зависимости от обрабатываемого материала электролитом служат растворы кислот или щелочей. Обрабатываемую заготовку подключают к аноду; электродом-катодом служит металлическая пластинка из свинца, меди, стали. Для большей интенсивности процесса электролит подогревают до температуры 40–80 °С.
Рис. 9.7. Схема электрохимического полирования:
1 – ванна; 2 – обрабатываемая заготовка; 3 – пластина-электрод; 4 – электролит; 5 – микровыступ; 6 – продукт анодного растворения
При подаче напряжения на электроды начинается процесс растворения металла заготовки-анода. Растворение происходит главным образом на выступах микроне ровностей поверхности вследствие более высокой плотности тока на их вершинах. Кроме того, впадины между микровыступами заполняются продуктами растворения: оксидами или солями, имеющими пониженную электропроводимость. В результате избирательного растворения, т.е. большой скорости растворения выступов, микронеровности сглаживаются, и обрабатываемая поверхность приобретает металлический блеск.
226
Электрополирование улучшает электрофизические характеристики деталей, так как уменьшается глубина микротрещин, поверхностный слой обрабатываемых поверхностей не деформируется, исключаются упрочнение и термические изменения структуры, повышается коррозионная стойкость.
Электрополирование позволяет одно временно обрабатывать партию заготовок по всей их поверхности. Этим методом получают поверхности деталей под гальванические покрытия, доводят рабочие поверхности режущего инструмента, полируют тонкие ленты и фольгу, очищают и декоративно отделывают детали.
Электрохимическую размерную обработку выполняют в струе электролите, прокачиваемого под давлением через меж электродный промежуток, образуемый обрабатываемой заготовкой-анодом и инструментом-катодом.
Струя электролита, непрерывно поливаемого в межэлектродный промежуток растворяет образующиеся на заготовку аноде соли и удаляет их из зоны обработки. При этом способе одновременно обрабатывается вся поверхность заготовку находящаяся под активным воздействием катода, что обеспечивает высокую производительность процесса. Участки заготовки, не требующие обработки, изолируют, Инструменту придают форму, обратную форме обрабатываемой поверхности Формообразование поверхности происходит по методу копирования.
Импульсное рабочее напряжение способствует повышению точности обработанной поверхности заготовки. Точность обработки значительно повышается при уменьшении рабочего зазора между заготовкой и инструментом. Для контроля зазора используют высокочувствительные элементы, встраиваемые в следящую систему. Способ рекомендуют для обработки заготовок из высокопрочных сплавов, карбидных и труднообрабатываемых материалов. Отсутствие давления инструмента на заготовку позволяет обрабатывать нежесткие тонкостенные детали с высокой точностью и качеством обработанной поверхности. Для электрохимической размерной об работки используют нейтральные электролиты. Наиболее широко применяют растворы солей NaCl, NaNО3 и Na2SO4.
227

На рис. 9.8 показаны схемы обработки заготовок в струе проточного электролита: турбинной лопатки (а), штампа (б) и схема прошивания сквозного цилиндрического отверстия (в).
Рис. 9.8. Схема электрохимической размерной обработки: 1 – инструмент-электрод; 2 – заготовка; 3 – изолятор
Многие модели станков управляются системами ЧПУ. В процессе обработки система ЧПУ задает и контролирует вели чины напряжения и тока, постоянство рабочего зазора, скорость подачи электрода-инструмента, скорость потока и концентрацию электролита. Соблюдение этих параметров режима обеспечивает высокие точность и производительность обработки заготовок.
На модернизированных электрохимических или электроэрозионных станках осуществляют комбинированную обработку заготовок электроэрозионно-химическим способом. Этот процесс обработки, основанный на сочетании анодного растворения и эрозионного разрушения металла, более производителен, чем электрохимический, но уступает по точности и шероховатости обработанной поверхности. Скорость обработки до 50 мм/мин; точность 0,2 – 0,4 мм; шероховатость Ra 10–20 мкм.
При электроабразивной и электроалмазной обработке инст-
рументом-электродом служит шлифовальный круг из абразивного материала на электропроводящей связке (бакелитовая связка с графитовым наполнителем). Между анодом-заготовкой и катодомшлифовальным кругом имеется межэлектродный зазор, образованный зернами, выступающими из связки. В зазор подается электролит. Продукты анодного растворения материала заготовки удаля-
228

ются абразивными зерна ми; шлифовальный круг имеет вращательное движение, а заготовка – движения по дачи, т.е. движения, соответствующие процессу механического шлифования.
Введение в зону резания ультразвуковых колебаний повышает производительность электроабразивного и электроалмазного шлифования в 2–2,5 раза при значительном улучшении качества обработанной поверхности. Электроабразивные и электроалмазные методы применяют для отделочной обработки заготовок из труднообрабатываемых материалов, а так же нежестких заготовок, так как силы резания здесь незначительны. При этих методах обработки прижоги обрабатываемой поверхности практически исключены.
При электроабразивной обработке (рис. 9.9) 85–90 % припуска удаляется за счет анодного растворения и 15–10 % – за счет механического воздействия. При электроалмазной обработке ~75 % припуска удаляется за счет анодного растворения и ~25 % – за счет механического воздействия алмазных зерен.
Рис. 9.9. Схема электроабразивного шлифования:
1 – заготовка; 2 – абразивные зерна; 3 – связка шлифовального круга
Отделочную обработку поверхностей заготовок можно проводить электрохимическим хонингованием (рис. 9.10). Кинематика процесса соответствует хонингованию абразивными головками. Отличие состоит в том, что заготовку устанавливают в ванне, заполненной электролитом, и подключают к аноду. Хонинговальную головку подключают к катоду. Вместо абразивных брусков в головке установлены деревянные или пластмассовые. Продукты анодного растворения удаляются с обрабатываемой поверхности
229

брусками при вращательном и возвратно-поступательном движениях хонинговальной головки. Чтобы продукты анодного растворения удалялись более активно, электролит добавляют абразивные материалы. После того как удаление припуска с обрабатываемой поверхности закончена, осуществляют процесс «выхаживания» поверхности при выключенном электрическом токе для полного удаления анодной пленки с обработанной поверхности Электрохимическое хонингование обеспечивает более низкую шероховатость поверхности, чем хонингование абразивными брусками. Поверхность получает зеркальный блеск. Производительность электрохимического хонингования в 4 – 5 раз выше производительности механическою хонингования.
Рис. 9.10. Схема электрохимического хонингования цилиндра: 1 – хонинговальная головка; 2 – заготовка цилиндра;
3 – изолятор; 4 – ванна;
5 – стол хонинговального станка
Анодно-механическая обработка деталей. Анодно-механи-
ческая обработка основана на сочетании электротермических и электромеханических процессов и занимает промежуточное место между электроэрозионными и электрохимическими методами. Обрабатываемую заготовку подключают к аноду, а инструмент – к катоду В зависимости от характера обработки и вида обрабатываемой поверхности в качестве инструмента используют металлические диски, цилиндры, ленты, проволоку Обработку ведут в среде электролита, которым чаще всего служит водный раствор жидкого натриевого стекла. Заготовке и инструменту задают такие же дви-
230