
Ермолаев Технологические процессы в машиностроении 2011
.pdf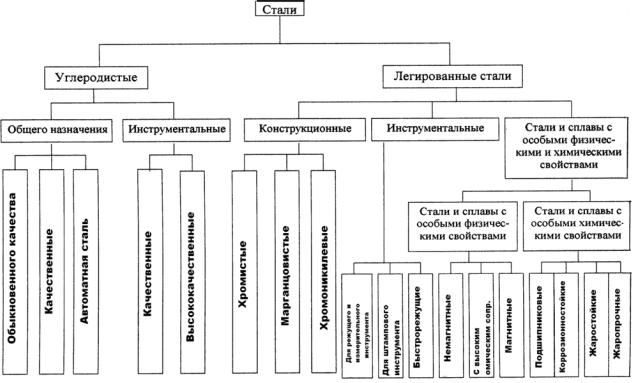
41
Рис. 2.5. Маркировка сталей
Понятие заготовки. Заготовка – определенное количество необходимой марки металла заключенного в определенную форму, обеспечивающую изготовление указанной в чертеже детали в результате механической обработки. Заготовка должна иметь несколько большие размеры, чем обработанная деталь, т.е. иметь припуск – слой металла, снимаемый при механической обработке. Припуск должен быть наименьшим (форма и размеры заготовки должны приближаться к форме и размерам готовой детали) и при этом обеспечивать получение годной детали.
Виды заготовок и характеристика основных методов их по-
лучения. Заготовки получают литьем, ковкой, штамповкой, прессованием, прокаткой, волочением, термической резкой, рубкой. В зависимости от этого различают виды заготовок: отливки, штамповки, поковки прокат из стали и цветных металлов (простых и сложных профилей) в виде прутков и труб, различных профилей.
Классификация способов производства заготовок приведена в табл. 2.1.
|
|
Таблица 2.1 |
|
|
|
|
|
Литейное |
Давлением |
Термическая резка |
|
|
|
|
|
В песчаные формы |
Ковка |
Газовая |
|
В оболочковые формы |
Штамповка |
Плазменная |
|
По выплавляемым моделям |
Прессование |
Лазерная |
|
В кокиль |
Прокатка |
|
|
Под давлением |
Волочение |
|
|
Центробежное литье |
|
|
|
Отливки получают путём заливки расплавленного металла в специальную форму, полость которой имеет конфигурацию заготовки (детали). При охлаждении залитый металл затвердевает и в твердом состоянии сохраняет конфигурацию той полости, в которую был залит.
Для изготовления отливок применяют множество способов литья:
9в песчаные формы;
9в оболочковые формы;
9по выплавляемым моделям;
42
9в кокиль;
9под давлением;
9центробежное литьё; и прочее.
Область применения того или иного способа литья определяется объёмом производства, требованиями к геометрической точности и шероховатости отливок, экономической целесообразностью и другими факторами.
Теория и практика технологии литейного производства на современном этапе позволяет получать изделия с высокими эксплуатационными свойствами. Свидетельством тому является надежная работа отливок в реактивных двигателях, атомных энергетических установок и других машинах ответственного назначения.
Литые заготовки используются в отраслях машиностроения, приборостроения, при изготовлении различных строительных конструкций доменных печей и других металлургических агрегатов, морских и речных судов, деталей бытового оборудования и сантехники, художественных и ювелирных изделий.
(Более подробно метод получения отливок см. в теме «Литейное производство».)
Получение заготовок обработкой металлов давлением. Этот способ включает в себя ковку, штамповку, прокатку, прессование и волочение.
Пластическое деформирование в обработке металлов давлением осуществляется при разных схемах напряженного деформированного состояний, при этом исходной заготовкой могут быть объёмное тело, пруток, лист. По назначению технологические процессы обработки металлов давлением группируют следующим образом:
-для получения изделий постоянного поперечного сечения по длине (прутков, проволоки, лент, листов), применяемых в строительных конструкциях или в качестве заготовок для последующего изготовления из них деталей обработкой резанием с использованием предварительного пластического формоизменения или без него; основными разновидностями таких процессов являются – прокатка, прессование, волочение;
-для получения деталей или заготовок (полуфабрикатов), имеющих приближенно формы и размеры готовых деталей и тре-
43
бующих обработки резанием лишь для придания им окончательных размеров и получения поверхности заданного качества; основными разновидностями таких процессов являются ковка и штамповка; Основными схемами деформирования объёмной заготовки можно считать сжатие между плоскостями инструмента, ротационное обжатие вращающимися валками, затекание металла в полость инструмента, выдавливание металла из полости инструмента и волочение, при котором в качестве заготовки может быть использо-
ван только пруток!
Процессы деформирования листовой заготовки – операции листовой штамповки – объединяются в две группы: разделительные (отрезка, вырубка, пробивка, надрезка) и формоизменяющие (гибка, вытяжка, формовка и др.)
Схема свободного течения металла при сжатии между плоскостями инструмента лежит в основе операций ковки: осадки, протяжки, раскатки и др., а также во многих других способах объёмной штамповки.
Ротационное обжатие вращающимися валками обуславливается силами трения между вращающимся инструментом и заготовкой, благодаря которым последняя перемещается в зазоре между валками, одновременно деформируясь. Эта схема лежит в основе прокатки. Кроме того, она может быть использована в ряде способов получения поковок: поперечно-клиновой прокатке, вальцовке, раскатке.
Получение заготовок термической резкой. По характеру и на-
правленности кислородной струи различают следующие способы резки.
Разделительная резка – режущая струя направлена нормально к поверхности металла и прорезает его на всю толщину. Разделительной резкой раскраивают листовую сталь, разрезают профильный материал, вырезают косынки, круги, фланцы и т.п.
Поверхностная резка – режущая струя направлена под очень малым углом к поверхности металла (почти параллельно ей) и обеспечивает грубую его строжку или обдирку. Ею удаляют поверхностные дефекты отливок.
Резка может быть ручной и механизированной.
44
Ручная резка вследствие неравномерности перемещения резака и вибрации режущей струи не обеспечивает высокого качества реза, поэтому поверхность реза обычно механически обрабатывают.
Для получения реза высокого качества применяют машинную резку, которая обеспечивает равномерное перемещение резака по длине реза, строгую перпендикулярность режущей струи к разрезаемой поверхности и постоянное расстояние мундштука от поверхности металла. Машинную резку выполняют специальными автоматами и полуавтоматами с одним или несколькими резаками, а при вырезке прямолинейных и криволинейных фасонных заготовок применяют металлические копиры.
Обычной кислородной резкой разрезают металлы толщиной 5– 300 мм. При резке металла толщиной более 300 мм применяют специальные резаки.
Резку плазменной струей, плазменной дугой и лазерную можно применять практически для всех материалов. Лазерная резка – очень высокопроизводительный процесс, позволяющий получать резы различной конфигурации, как при отрезке заготовок, так и при вырезке их по замкнутому контуру. Современные лазерные установки для резки снабжены системами перемещения заготовок с ЧПУ или управляемыми ЭВМ.
2.3. Производство цветных металлов
Медь и ее сплавы. Технически чистая медь (в земной коре меди около 0,01 %) имеет плотность 8940 кг/м3, температуру плавления 1083 °С, обладает высокой пластичностью, коррозионной стойкостью, малым удельным электросопротивлением (7 10-8 Ом м), высокой теплопроводностью [385 Bт/(м К)], поэтому её широко используют для изготовления электропроводов, деталей электрических машин и приборов, в химическом машиностроении.
Медь по чистоте подразделяют на марки М0 (99,97 % Сu), М1 (99,9 % Cu), М2 (99,7 % Cu), М3 (99,5 % Сu), М4 (99 % Cu).
Медные сплавы разделяют на бронзы и латуни. Бронзы (ГОСТ 493-79, 613-79) – это сплавы меди с оловом (4–33 % Sn), свинцом
(30 % Pb), алюминием (5–11 % Al), кремнием (4–5 % Si), сурьмой и
45
фосфором. Латуни – это сплавы меди с цинком (до 50% Zn) с небольшими добавками алюминия, кремния, никеля, марганца (ГОСТ 17711-80, 15527-70). Медные сплавы обозначают начальными буквами их названия (Л – латунь, Бр – бронза), после чего следуют первые буквы основных названий элементов, образующих сплав, и цифры, указывающие количество легирующего элемента в процентах. Например, ЛЦ40Мц1,5 – латунь, содержащая 40% Zn, 1,5% Mn, остальное Cu.
Бронзы и латуни разделяют на деформированные и литейные. Литейные бронзы и латуни отличаются от деформируемых тем, что в их состав вводят добавки, улучшающие литейные свойства сплава – повышающие жидкотекучесть, уменьшающие усадку. Однако эти добавки снижают пластические свойства литейных бронз и латуней по сравнению с деформируемыми.
Производство меди. Медь получают главным образом пирометаллургическим способом (рис. 2.6), сущность которого состоит в производстве меди и медных руд, включающем её обогащение, обжиг, плавку на полупродукт – штейн, выплавку из штейна черновой меди и её очистку от примесей (рафинирование).
Для производства меди применяют медные руды, содержащие 1–6 % Cu, а также отходы меди и её сплавов. В рудах медь обычно находится в виде сернистых соединений (CuFeS2, Cu2S, CuS), оксидов (Cu2О, CuО) или гидрокарбонатов [CuCO3, Cu(OH)2, 2CuCO3*Cu(OH)2]. Перед плавкой медные трубы обогащают и получают концентрат. Для уменьшения содержания серы в концентрате его подвергают окислительному обжигу при температуре 750–800 оС. Полученный концентрат переплавляют в отражательных или электрических печах. При температуре 1250–1300 оС восстанавливаются оксид меди (CuO) и высшие оксиды железа. Образующийся оксид меди (Cu2O), реагируя с FeS, дает Cu2S. Сульфиды меди и железа сплавляются и образуют штейн, а расплавленные силикаты железа растворяют другие оксиды и образуют шлак. Затем расплавленный штейн заливают в конвертеры и продувают воздухом (конвертируют) для окисления сульфидов меди и железа и получения черновой меди. Черновая медь содержит 98,4–99,4 % Cu и небольшое количество примесей. Эту медь разливают в изложницы.
46
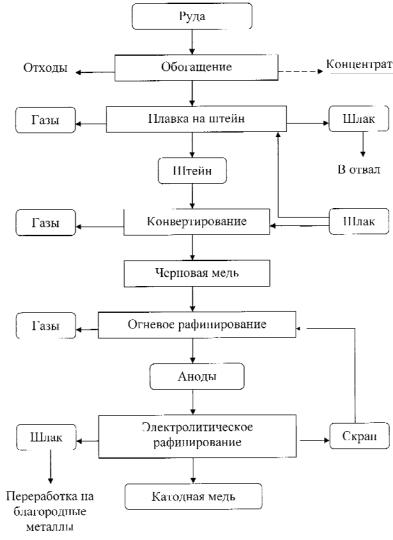
После огневого рафинирования получают медь 99–99,5 %. Из нее отливают чушки для выплавки сплавов меди (бронзы и латуни) или плиты для электролитического рафинирования.
Рис. 2.4. Получение меди пирометаллургическим методом
47
Электролитическое рафинирование проводят для получения чистой от примесей меди (99,5 % Cu). Электролиз ведут в ваннах, покрытых изнутри винипластом или свинцом. Аноды делают из меди огневого рафинирования, а катоды – из листов чистой меди. Электролитом служит водный раствор CuSO4 (10–16 %) и H2SO4 (10–16 %). При пропускании постоянного тока анод растворяется,
медь переходит в раствор, а на катодах разряжаются ионы меди: Cu2+ + 2e – →Cu
Примеси (мышьяк, сурьма, висмут и др.) осаждаются на дно ванны, их удаляют и перерабатывают для извлечения этих металлов. Катоды выгружают, промывают и переплавляют в электропечах.
Алюминий и его сплавы. Алюминий – легкий металл (плотность 2700 кг/м3), обладает высокими теплопроводностью [200 Вт/(м К)] и электропроводимостью (10–5 Ом), стоек к коррозии. Температура плавления алюминия 658 °С.
Алюминиевые сплавы разделяют на деформируемые и литейные. Те и другие могут быть упрочняемые и неупрочняемые термической обработкой.
Деформируемые алюминиевые сплавы (ГОСТ 4784-74) хорошо обрабатываются прокаткой, ковкой, штамповкой. К деформируемым алюминиевым сплавам, не упрочняемым термической обработкой, относятся сплавы системы Al – Mn (Амц), содержащие до 1,6 % Mn, и сплавы системы Al – Mg (Амг), содержащие до 5,8 % Mg. Эти сплавы обладают высокой пластичностью и невысокой прочностью.
К деформируемым алюминиевым сплавам, упрочняемым термической обработкой, относятся сплавы системы Al-Cu-Mg (дуралюмины, ковочные сплавы), а также высокопрочные и жаропрочные сплавы сложного химического состава. Дуралюмины (Д16 –
Д18) содержат 3,8–4,8 % Cu, 0,4–1,8 % Mg, а также 0,4–0,9 % Mn,
который повышает коррозионную стойкость сплавов. После термической обработки эти сплавы приобретают высокие прочность и пластичность. Ковочные сплавы (АК6 – АК8) содержат 1,8–4,8 % Cu, 0,4–0,8 % Mg, 0,4–1 % Mn, 0,6–1,2 % Si, хорошо деформируют-
ся в нагретом состоянии, обладают высокой прочностью после термообработки.
48
Литейные алюминиевые сплавы ГОСТ 2685-75 применяют для изготовления деталей машин и приборов литьем. Наиболее широко используют сплавы алюминия с содержанием 10–13 % Si: АЛ2, АЛ4, АЛ9.
Сплавы алюминия с медью (до 5,3 % Cu) и марганцем (до 1 % Mn) обладают повышенной прочностью (сплавы АЛ7, АЛ19 и др.). Их применяют для литья деталей, работающих при достаточно высоких нагрузках (кронштейны, арматура и др.).
Сплавы алюминия с магнием (до 9,5–11,5 % Mn) обладают хорошей коррозионной стойкостью и применяются для отливок, работающих во влажной атмосфере (сплавы АЛ8, АЛ13). Часто отливки из алюминиевых литейных сплавов подвергают термической обработке для повышения прочности, пластичности, снижения остаточных напряжений.
Алюминий применяют для приготовления спеченных алюминиевых сплавов (САС) и спекаемых алюминиевых пудр (САП), из которых изготовляют детали методами порошковой металлургии, позволяющей получать детали с особыми свойствами – коррозионной стойкостью, прочностью, пористостью.
Производство алюминия. Сущность процесса производства алюминия заключается в получении безводного, свободного от примесей оксида алюминия (глинозема) с последующим получением металлического алюминия путем электролиза растворенного глинозема в расплавленном криолите (рис. 2.6).
Основное сырье для производства алюминия – алюминиевые руды: бокситы, нефелины, алуниты, каолины. Наибольшее значение имеют бокситы. Алюминий в них содержится в виде минералов – гидроксидов Al(OH)3, AlO(OH). Корунда Al2O3 и каолинита
Al2O3 2SiO2 2H2O .
Алюминий получают электролизом глинозема – оксида алюминия (Al2O3) в расплавленном криолите (Na3AlF6) с добавлением фтористых алюминия и натрия (AlF3, NaF). Производство алюминия включает получение безводного, свободного от примесей оксида алюминия (глинозема); получение криолита из плавикового шпата; электролиз глинозема в расплавленном виде.
Глинозем получают из бокситов путем их обработки щелочью:
49
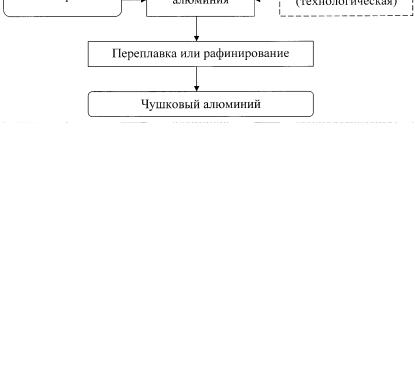
Al2O3 nH2O + 2NaOH = 2NaAlO2 + (n + 1)H2O.
Рис. 2.6. Получение алюминия
Полученный алюминат натрия NaAlO2 подвергают гидролизу: NaAlO2 + 2H2O = NaOH + Al(OH)3↓
В результате в осадок выпадают кристаллы гидроксида алюминия Al(OH)3. Гидроксид алюминия обезвоживают во вращающихся печах при температуре 1150–1200 °С и получают обезвоженный глинозем Al2O3.
Для производства криолита сначала из плавикового шпата получают фтористый водород, а затем плавиковую кислоту. В раствор плавиковой кислоты вводят Al(OH)3, в результате чего образуется фторалюминиевая кислота, которую нейтрализуют содой и получают криолит, выпадающий в осадок:
50