
Ермолаев Технологические процессы в машиностроении 2011
.pdfмов происходит без подогрева на непрерывно-заготовочном или крупносортном стане. Затем заготовки сечением 140×140 – 60×60
ммрежут на мерные части. После осмотра их нагревают в методических печах и прокатывают на сортовых, проволочных и других станах.
Сляб – заготовка прямоугольного сечения, предназначенная для прокатки толстого листа. Для прокатки слябов используют плоские слитки прямоугольного сечения.
Прокатка листовой стали. После нагрева слябы прокатывают в листы в две стадии. В первой стадии после одного-двух проходов сляб кантуют в горизонтальной плоскости на 90 градусов относительно направления прокатки и прокатывают в поперечном направлении до получения требуемой ширины. Во второй стадии обжатый сляб вновь кантуют в той же плоскости на 90 градусов и прокатывают на длину листа. Прокатка в двух направлениях уменьшает разницу в структуре и механических свойствах вдоль и поперек листа.
Прокатку толстолистовой стали выполняют на одноклетьевых станах трио и кварто, двухклетьевых и полунепрерывных автоматизированных станах. Качество поверхности листов на двухклетьевых станах получается лучше, чем на одноклетьевых, так как в чистовую клеть двухклетьевого стана поступают листы, очищенные от окалины в черновой клети.
Тонколистовую сталь прокатывают в горячем и холодном состояниях. Горячую прокатку выполняют в полунепрерывных и непрерывных станах из слябов и получают листы шириной 600–2200
мми более при толщине свыше 1,25 мм. Для удаления окалины в таких станах перед чистовой группой клетей установлен окалиноломатель. Так как горячую прокатку тонколистовой стали заканчивают при температуре ниже температуры рекристаллизации, то листы после прокатки подвергают нормализации.
Горячекатаные листы, предназначенные для последующей холодной прокатки, травят для снятия окалины на травильных установках и сушат, а листы, предназначенные для холодной листовой штамповки, после отжига дополнительно обрабатывают на дрессировочных станах, правят на правильных машинах и режут на нож-
101

ницах. Дрессировка – холодная прокатка с обжатиями в пределах 0,5–3 %. Этот процесс приводит к наклепу металла. Обработанные после отжига и травления листы называют декапированными.
Холодную прокатку тонких листов производят на реверсивных станах кварто и на непрерывных трех-, четырех- и пятиклетьевых станах, снабженных разматывателями и наматывателями рулонов. В качестве исходной заготовки используют рулонную полосу толщиной 1,2–6 мм и шириной до 2000 мм.
Сортамент прокатных изделий. Форму поперечного сечения проката называют профилем, который может быть по длине изделия либо постоянным, либо переменным (периодическим). Совокупность различных профилей и их размеров называют сортаментом. Сортамент проката (рис. 4.7) делится на следующие основные группы: сортовой прокат, листовой прокат, трубы и профили специального назначения.
Рис. 4.7. Сортамент проката:
а– сортовой прокат простой: круг, квадрат, шестигранник, овал, треугольник;
б– сортовой прокат фасонный: уголок, тавровая балка, швеллер, двутавровая балка, рельс; в – лист; г – труба; д – специальные профили: колесо, шпунтовая свая, автообод, оконный профиль, периодический профиль
102
Сортовой прокат подразделяют на простой геометрической формы (круг, квадрат, шестиугольник, овал, треугольник) и фасонный (уголки, швеллеры, двутавровые балки, рельсы и т.д.). Листовой прокат толщиной свыше 4 мм называют толстолистовым и толщиной менее 4 мм – тонколистовым. Трубы бывают бесшовные и сварные. К специальным видам проката относятся кольца, зубчатые колеса, периодические профили и др.
4.4. Прессование металлов
Технологический процесс прессования. Процесс прессования металла состоит из следующих стадий:
1)подготовки слитка к прессованию (удаление наружных дефектов, разрезка на мерные длины и т.д.);
2)нагрева слитка до заданной температуры и подачи к контей-
неру;
3)собственно прессования;
4)отделки изделия (охлаждение, ломка заднего конца для полного удаления пресс утяжины, резка на мерные длины, правка, удаление дефектов).
Для уменьшения трения металла о стенки контейнера и достижения более равномерного истечения металла из матрицы применяют смазку – смесь машинного масла с графитом, жидкое стекло и др.
Температуру прессования выбирают, исходя из свойств обрабатываемого материала и ее влияния на качество получаемых изделий, стойкость прессового инструмента и усилие прессования. Температура прессования связана со скоростью прессования, т.е. скоростью движения пуансона в период рабочего хода (деформации металла). При высоких скоростях прессования температура металла заметно повышается. Это может привести к перегреву металла и получению изделия с трещинами и надрывами. На практике обычно придерживаются следующего правила: чем выше температура нагрева металла, тем меньше скорость прессования, и наоборот.
Скорость, с которой металл выходит из очка матрицы, называют скоростью истечения. Скорость истечения равна скорости прессования, умноженной на вытяжку. Эта зависимость указывает на
103
прямую связь скоростных условий процесса прессования со степенью деформации.
Выбор скорости истечения зависит от пластичности металла или сплава. Так, алюминий, углеродистая и легированная сталь, медь, латуни Л62, Л96 и ЛС59-1, никелевые сплавы, титан и его сплавы при прессовании прутков и труб небольших размеров с вытяжками более 30 допускают скорость истечения 100–500 см/с, в то время как бронзы, алюминиевые сплавы (Д1, Д16 и т. д.) и большинство магниевых сплавов имеют скорость истечения 5–10 см/с, (в ряде случаев ее можно увеличить до 20–25 см/с). Превышение указанных скоростей приводят к образованию поперечных трещин и разрывов. Следовательно, при выборе параметров процесса прессования установление рациональной скорости истечения металла имеет большое значение для получения качественных изделий и обеспечения высокой производительности пресса.
К недостаткам прессования следует отнести большие отходы металла: весь металл не может быть выдавлен из контейнера, и в нем остается так называемый пресс-остаток, который после окончания прессования отрезается от полученного профиля, масса пресс-остатка может достигать 40% массы исходной заготовки (при прессовании труб больших диаметров).
Схема прессования. Различают два основных метода прессования металла – прямой и обратный.
При прямом методе прессования (рис. 4.8, а) нагретую заготов-
ку 3 помещают в контейнер 4 пресса. Контейнер имеет набор втулок 5 с различным внутренним диаметром, что позволяет прессовать на одной и той же установке слитки различного диаметра. С одной стороны контейнера посредством матрицедержателя 2 закреплена матрица 1. С другой стороны контейнера установлен пуансон (шплинтон) 6 с пресс-шайбой 7 на конце, которая входит во втулку контейнера. При работе пресса пуансон получает необходимое давление р от плунжера и передает его через пресс-шайбу на заготовку, заставляя металл пластически деформироваться при прохождении через выходное отверстие матрицы. К концу процесса прессования в контейнере остается часть металла, называемая пресс-остатком слитка. Отходы металла составляют 18–20 % массы слитка.
104
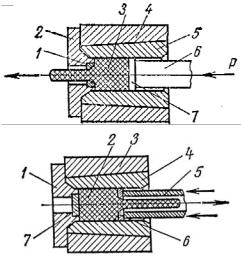
а
б
Рис. 4.8. Схемы прессования прямым (а) и обратным (б) методами
При обратном методе прессования металла (рис. 4.8, б) во втулку 4 контейнера 3 входит полый пуансон 5 с матрицей 6 на его конце; выходное отверстие в матрицедержателе 1 закрыто заглушкой 7. При движении пуансона матрица давит на слиток 2, в результате чего металл вытекает через отверстие матрицы в направлении, обратном перемещению пуансона.
При прессовании обратным методом по сравнению с прямым уменьшаются отходы металла (на 5–6 % массы слитка) и усилие прессования на 25–30 %.
Обратный и прямой методы прессования осуществляются на одном и том же прессе. Имеются специальные прессы обратного прессования, у которых на неподвижный пуансон надвигается контейнер со слитком, получающие движение от главного плунжера.
Прессы обратного прессования имеют ограниченное применение вследствие сложности конструкции; в настоящее время их не строят.
При прессовании труб (рис. 4.9) нагретая сплошная заготовка 3, помещенная во втулку 5 контейнера 4, сначала 1 несколько обжимается, а затем прошивается стальной иглой 7. Иглу укрепляют на
105

конце пуансона или в проходящем через полый пуансон иглодержателе (как показано на рисунке).
При прошивке заготовки передний конец иглы выходит на некоторое расстояние из отверстия матрицы 7. Вследствие этого между стенками отверстия матрицы и наружной поверхностью стальной иглы образуется кольцевой зазор. При движении пуансона 6 вместе с пресс-
шайбой 8 в направлении матрицы металл выдавливается через кольцевой зазор и принимает форму трубы 9. Наружный диаметр трубы равен диаметру отверстия матрицы, а внутренний – диаметру стальной иглы.
Трубы прессуют также из полых заготовок. В этом случае игла проходит через заготовку и занимает рабочее положение в матрице, после чего начинается процесс прессования.
Различают прессование без «рубашки» (рассмотренное выше), при котором пресс-шайба плотно входит во втулку контейнера, и прессование с «рубашкой», при котором диаметр пресс-шайбы на 2–3 мм меньше диаметра втулки контейнера. В последнем случае пресс-шайба врезается в слиток и выдавливает внутренние слои слитка, а наружные остаются в контейнере в виде полого цилинд- ра-рубашки; при этом качество изделий повышается.
После рабочего цикла прессования рубашку удаляют из контейнера пуансоном с контрольной пресс-шайбой. Трубы прессуют без рубашки.
Обрабатываемые материалы. Исходным материалом для прессования являются круглые слитки диаметром 120–680 мм и длиной 200–1000 мм и заготовки. Прессованием обрабатывают специальные стали, которые ввиду низкой пластичности (особенно в литом состоянии) другими видами обработки деформировать невозможно или затруднительно.
Из углеродистых конструкционных качественных сталей: 20, 35, 45, 50, легированных: 30ХГСА, 40ХН, коррозийно-стойких –
106

12Х18Н10Т и других высоколегированных сталей прессуют трубы с внутренним диаметром 30–160 мм с толщиной стенки 2–10 мм.
Прессованные изделия из цветных металлов и сплавов (меди и ее сплавов, цинковых, титановых и других), а также из сталей и сплавов в основном являются заготовками для получения изделий волочением, холодной прокаткой и другими способами обработки. Прессованные профили из алюминия, магния и их сплавов, как правило, являются готовыми изделиями.
Сортамент изделий. Прессованием можно получать различные профили, сложных форм, которые не могут быть получены другими видами обработки металлов давлением (в частности, прокаткой) (рис. 4.10). Точность прессованных профилей выше, чем прокатных.
Получают прутки диаметром 3–300 мм, трубы с внутренним диаметром 20–400 мм и толщиной стенки 1,25–50 мм и другие профили.
Рис. 4.10. Виды изделий
Контроль качества прессованных изделий. При выполнении всех операций осуществляется контроль качества поверхности металла, нагрева, формы, размеров и т.д. готовые изделия подвергаются контролю качества с помощью ультразвуковых дефектоскопов, с применением которых выход годного металла с 70–80 % увеличился существенно.
107
4.5. Волочение металлов
Технологический процесс волочения. В технологический процесс волочения входят подготовка металла к волочению, установление режима волочения и отделка готовой продукции.
Волоки изготавливают из твердого сплава: ВК2, ВК3, ВК6, ВК8, ВК10, ВК15. Волочением обрабатывают углеродистые и легированные стали цветные металлы и их сплавы. Исходным материалом являются проволока (катанка), прутки и трубы, получаемые горячей прокаткой (сталь, цветные металлы и их сплавы), горячим прессованием (латуни, бронзы, алюминиевые сплавы), непрерывным литьем (алюминиевые сплавы) и методом порошковой металлургии (спеканием).
При подготовке металла к волочению удаляют окалину с поверхности заготовки и наносят на нее смазку.
Окалина может быть удалена с поверхности заготовки химическим, механическим или электрохимическим способами, а также при помощи ультразвука, вакуума и т. д. Чаще всего для удаления окалины применяют химическое травление в водных растворах кислот. После травления металл промывают, удаляя с его поверхности остатки кислоты и шлам.
Если заготовка предназначена для нескольких последовательных протяжек, то после травления и промывки на нее наносят подсмазочный слой дополнительной обработкой – желтением, омеднением, фосфатированием и последующим известкованием.
Завершающей операцией подготовки поверхности заготовки к волочению является сушка в специальных сушилах с усиленной циркуляцией воздуха при 300–350 °С. Во время сушки удаляются влага и некоторая часть растворенного в металле водорода, что способствует устранению хрупкости металла.
На сухую поверхность заготовки перед протяжкой наносят соответствующую смазку (масла минеральные, графит, мыло и некоторые эмульсии).
Схемы волочения. Области применения. Сущность процесса волочения состоит в следующем. У прутка 1 (рис. 4.11, а) с начальным сечением F1 заостряется передний конец, который пропускают
108

через очко волоки 2. К переднему концу прутка, выходящему из волоки, прикладывают внешнюю силу Р, называемую усилием волочения. Пруток, проходя через очко волоки, деформируется и принимает форму и размеры очка волоки. Конечное сечение F2 прутка меньше исходного F1 .
Рис. 4.11. Основные способы волочения изделий:
1 – изделие; 2 – волока; 3 – оправка; 4 – мундштук; 5 – волочильный болт; I – входная зона (распушка); II – смазочная; III – деформирующая;
IV – калибрующая; V – выходная
Сила давления N стенок очка волоки на металл вызывает со стороны последнего реактивные силы, равные по величине активным силам, но направленные в противоположную сторону. Движение металла в очке волоки вызывает скольжение на контактной поверхности, вследствие чего возникают внешние силы трения Т, направленные против движения прутка.
109
При волочении смазка металла и волочильного очка снижает силы трения и усилие волочения, а также температуру в очаге деформации, предотвращает прилипание металла к волоке и улучшает качество поверхности изделия. Кроме того, смазка позволяет увеличить обжатие за проход и скорость волочения.
Применяемые при волочении смазки разделяют на твердые (мыльные порошки, графит, парафин), консистентные или полужидкие (солидолы, тавоты, минеральные масла в смеси с мылом, петролатумом и др.) и жидкие (водные эмульсии минеральных масел и мыла и т. д.). Введение в смазку небольших количеств поверхностно активных веществ (серы, фосфора и др.) облегчает процесс деформирования металла. Эти вещества проникают в микротрещины на поверхности протягиваемой заготовки и создают в них дополнительные раздвигающие усилия, облегчающие процесс деформации под воздействием внешних сил.
При волочении металлическим изделиям придают точные размеры, заданную геометрическую форму, чистую и гладкую поверхность. Подвергая заготовку волочению несколько раз, можно получить изделие тончайшего сечения.
Технологические режимы процесса волочения. Режим воло-
чения металла регламентируется технологическими картами, в которых указывается:
1)маршрут волочения, т. е. последовательность изменения размеров сечения заготовки (обжатие или коэффициент вытяжки) по проходам,
2)температура и продолжительность промежуточного отжига для снятия наклепа,
3)режим травления с целью удаления окалины, полученной при отжиге, и дополнительной обработки металла перед последующим волочением.
Расчет маршрута волочения включает определение суммарной вытяжки или суммарного обжатия и числа проходов; выбор оборудования; определение частных вытяжек или обжатий; нахождение размеров протягиваемого изделия по проходам и определение скорости волочения.
Частные обжатия по проходам распределяют следующим обра-
зом: первое обжатие обычно небольшое, чтобы обеспечить лучшее
110