
Ермолаев Технологические процессы в машиностроении 2011
.pdfПроблема создания качественных и экономичных машин по праву считается центральной и наиболее сложной. Сложны не только создание конструкции и реализация самой идеи о новой машине. Сложно также обеспечение ее качества и экономичности при конструировании и изготовлении, так как любая машина создается для выполнения процесса, наделенного вероятностными свойствами, а изготовление сопровождается явлениями случайного характера.
Поскольку случайные события и явления неизбежны как при эксплуатации машины, так и в процессе ее изготовления, то решение задач обеспечения качества и экономичности создаваемой машины не может обойтись без привлечения теории вероятностей и математической статистики.
Изделие как объект производства. Машина (как и ее части)
является технической системой, которая создается для выполнения определенных функций, то есть имеет определенное служебное назначение. Функциональными компонентами машины называют сборочные единицы (узлы) различных уровней сложности, детали
ичасти деталей, включая неделимые элементы.
Впроцессе работы между элементами машины возникают и действуют размерные, кинематические, силовые, физикохимические и временные связи и отношения. Следует отметить, что все виды отношений и связей закладываются в процессе ее создания в виде размерных отношений (размеров, расстояний, относительных поворотов, формы и микрогеометрии поверхностей деталей) и в виде наборов свойств материалов, из которых изготовлены детали машин.
Функции машины и ее элементов отражены в технических требованиях (ТТ) – системе качественных показателей с установленными на них количественными значениям.
1.3. Обработка деталей
Этапы обработки материала от заготовки до готового изде-
лия Процесс изготовления изделий называется производственным процессом. Производственный процесс состоит из нескольких эта-
пов (рис. 1.2).
11

На машиностроительных заводах такими этапами являются: подготовка производства, получение материала, изготовление заготовок, обработка заготовок, изготовление деталей, сборка из деталей узлов и изделий, контроль качества деталей и испытание готовой продукции, окраска, упаковка и транспортировка. Производственный процесс является многогранным и очень сложным, он требует четкого планирования и организации, бесперебойного снабжения, правильной организации инструментального хозяйства, учета и т.п.
Методы обработки металлов.
Наиболее часто используемыми и актуальными видами обработки металлов на сегодняшний день являются механическая и термическая обработка (например, термообработка стали), литье, обработка давлением, сварка, электрофизические и электрохимические методы обработки.
Детали можно получить из заготовок, обрабатывая их резанием путем последовательного удаления металла. Причем на каждом переходе с заго-
товки удаляют определенный слой металла, а обрабатываемые поверхности постепенно приближаются по форме и размерам к детали.
Припуски на обработку деталей. Для определения разности размеров заготовки и детали введено понятие припуска.
Припуском называют избыточный (сверх чертежного размера детали) слой металла заготовки, удаляемый при обработке с целью получения окончательной формы, размеров и нужной шероховато-
12

сти поверхности детали при наименьших расходах материала. Припуск, удовлетворяющий указанным требованиям, с экономической точки зрения должен быть целесообразным и оптимальным.
Припуск указывают в виде слоя металла по толщине, подлежащего удалению обработкой (рис. 1.3). Припуск может быть с двусторонним и односторонним расположением. Для цилиндрических деталей припуск задают слоем избыточного металла на диаметр. Чем больше будет припуск на обработку, тем толще слой металла в процессе изготовления детали необходимо удалить, вследствие чего увеличивается трудоемкость изготовления детали. С целью экономии металла и обеспечения эффективности процесса необходимо назначить припуск исходя из условия получения требуемого качества детали при наименьшей трудоемкости обработки. Увеличенные припуски приводят к удалению наиболее износостойких слоев поверхности детали, вызывают излишние затраты на обработку, расход материала, энергии, рабочего инструмента. Заниженные припуски не гарантируют требуемого качества, так как затрудняют обработку.
Рис. 1.3. Расположение припусков и допусков на обработку
Классификация припусков. Припуск определяют в зависимости от способа изготовления деталей, материала заготовки, вида, размеров, величины дефектного слоя на обрабатываемой поверхности, формы детали, требуемой точности и шероховатости поверхностей, сложности обработки, погрешности установки и прочее.
13
Так, припуск зависит от толщины корки у отливок, обезуглероженного слоя у проката, глубины поверхностных неровностей, раковин, трещин.
Межоперационным припуском называют слой материала, сни-
маемый при резании. Численно межоперационный припуск равен разности размеров заготовки после двух смежных операций. Межоперационные припуски могут быть минимальными, номинальными и максимальными.
Минимальным припуском называют наименьший слой снимаемого металла за одну операцию, т.е. разность размеров минимального после предшествующей операции и максимального после данной операции.
Номинальным припуском называют разность размеров номинального предшествующего и номинального после данной операции. Он определяется как сумма минимального припуска и допуска, необходимого на выполнение предшествующей операции.
Максимальным припуском называют наибольший слой металла, снимаемый за одну операцию, т.е. разность наибольшего размера после предшествующего и наименьшего после данной операции. Межоперационный припуск определяют разностью размеров предшествующего и данного выполняемого. Например, для наруж-
ных поверхностей a1 – a2 = z1; a2 – a3 = z2; a3 – a4 = z3; для внутренних поверхностей a2 – a1 = z1; a3 – a2 = z2; a4 – a3 = z3, где z1, z2, z3 – межоперационные припуски, a1, a2, a3, a4 – межоперационные
размеры.
Величины припусков под механическую обработку. Для наружных поверхностей общий припуск z0 равен разности размеров заготовки и детали z0 = a4– a1, где a1 – размер заготовки; a4 – размер детали.
Общий припуск определяют как сумму операционных припус-
ков z0 = ∑n zi , где n – число переходов.
1
Величину симметричного припуска (на две стороны) определяют следующей зависимостью (рис. 1.4):
для обработки параллельных противоположных плоских поверхностей
14
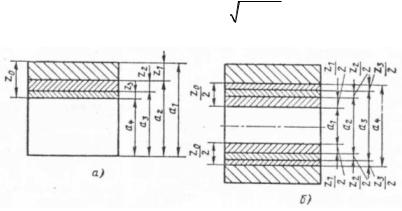
2zb = 2 (Ha +Ta )+(ρa +ξb ) ;
для обработки наружных и внутренних цилиндрических поверхностей
2zb = 2 |
(Ha +Ta )+ ρa2 |
+ξb2 . |
|
|
|
Рис. 1.4. Припуск на обработку наружных (а) и внутренних (б) поверхностей
Асимметричный припуск при последовательной обработке поверхностей определяют зависимостью zb =(Ha +Ta )+(ρa +ξb ), где
zb – минимальный припуск на обработку (на сторону), отнесенный к наименьшему размеру заготовки для наружных поверхностей и наибольшему размеру заготовки для внутренних поверхностей; На
– высота микронеровностей; Та – глубина дефектного поверхностного слоя; ρа – суммарное значение пространственных отклонений обрабатываемой поверхности; ξb – погрешность установки с выверкой заготовки для выполняемой операции.
Значение (Ha +Ta ) (рис. 1.5) для черновой обработки составля-
ет для проката 0,3 мм; для поковок, полученных свободной ковкой, 2–5 мм, в зависимости от поперечного размера поковки, начиная от
50до 2000 мм.
Расчеты для определения припусков сложны и трудоемки, по-
этому более удобно пользоваться табличными величинами. Ниже приведены припуски на чистовое обтачивание, причем меньший припуск берется при обработке вала длиной до 1000 мм, а больший
– при обработке вала длиной больше 1000 мм:
15

Диаметр вала, мм |
6-18 18-50 |
50-120 |
|
120-260 260-500 |
|
Припуск на диаметр, мм |
1-1,5 1,5-2 |
1,5-2 |
Рис. 1.5. Нормальная структура металла
с минимальным припуском
Количество материала (норма расхода), необходимого для изготовления детали, вычисляется по формуле Hq =G0 +Σq , где G0 –
масса готовой детали, Σq − суммарная масса отходов и потерь.
Критерием оценки степени прогрессивности нормы расхода ма-
териала является коэффициент использования материала
Kм = G0 , Hq
под которым понимают отношение массы детали к норме расхода материала. Чем больше коэффициент, тем больше экономия металла.
Факторы, влияющие на величину припусков. К таким факто-
рам относятся: материал; форма; габаритные размеры; точность (размеров и взаимного расположения поверхностей); шероховатость поверхностей; число деталей.
Технико-экономическое значение припусков. При выборе способов обработки поверхностей заготовки необходимо руководствоваться принципом наибольшей производительности и возможностью использования высокопроизводительных технологий, приспособлений и инструмента.
16
Вопросы для самоконтроля
1.Что такое технологический процесс?
2.Что такое изделие? Деталь?
3.Перечислите этапы производственного процесса.
4.Какие виды припусков Вы знаете?
5.От чего зависит величина припуска?
17
Тема 2. МАТЕРИАЛЫ, ПРИМЕНЯЕМЫЕ
ВМАШИНОСТРОЕНИИ
2.1.Производство чугуна
Материалы, применяемые в доменном производстве и их подготовка к плавке. Для выплавки чугуна в доменных печах используют железные руды, топливо, флюсы.
Железные руды содержат: железо в различных соединениях: в виде оксидов Fe3О4, Fe2О3; гидроксидов Fe2О3 * nH2О; карбонатов FeСО3 и др., а также пустую породу, состоящую в основном из
SiO2, Аl2О3, CaO, MgO и др.
К железным рудам относятся: магнитный железняк Fe3О4 (55–60 % Fe), красный железняк Fe2О3 (55–60 % Fe),
бурый железняк, содержащий гидраты оксидов железа
2Fe2О3*3H2О и Fe2О3* nH2О (37–55 % Fe);
шпатовые железняки, содержащие FeСО3 (30–40 % Fe). Марганцевые руды применяют для выплавки сплава железа с
марганцем – ферромарганца (10–82 % Mn), а также передельных чугунов, содержащих до 1 % Mn. Марганец в рудах содержится в виде оксидов и карбонатов: MnО2, Mn2О3, Mn3О4, MnСО3, и др.
Хромовые руды используют для производства феррохрома, металлического хрома и огнеупорных материалов хромомагнезитов. Хромовые руды содержат хромит (FeО*Cr2О3), магнохромит
(Mg, Fe).
Комплексные руды используют для выплавки природнолегированных чугунов. Это железомарганцевые руды (до 20 % Mn), хромоникелевые руды (37–47 % Fe, до 2 % Сг, до 1 % Ni), железованадиевые руды (до 0,17–0,35 % V).
Топливом для доменной плавки служит кокс, позволяющий получать необходимую температуру и создавать, условия для восстановления железа из руды. В целях экономии часть кокса заменяют природным газом, мазутом, пылевидным топливом.
Флюсом при выплавке чугуна в доменных печах является известняк СаCO или доломитизированный известняк, содержащий
18
СаС03 и MgCO3, так как в шлаки должно входить определенное количество основных оксидов (СаО, МnО). Это необходимо для удаления серы из металла, в который она переходит из кокса и железной руды при плавке. В известняке суммарное содержание оксидов SiO2 и Аl2О3 не должно превышать 1 %, содержание серы и фосфора – минимальным. Для нормальной работы доменной печи необходим достаточно жидкотекучий шлак при температуре 1450 °С. В таком шлаке отношение кислотных оксидов к основным должно быть около единицы:
( SiO2+ Аl2О3) : (CaO+MgO) ≈ 1.
Подготовка руд к доменной плавке осуществляется для повышения производительности доменной печи, снижения расхода кокса и улучшения качества чугуна. Цель этой подготовки – увеличение содержания железа в шихте и уменьшение в ней вредных примесей серы, фосфора, повышение ее однородности по кусковатости и химическому составу. Метод подготовки добываемой руды зависит oт ее качества.
Дробление и сортировка руд по крупности служат для получения кусков оптимальной для плавки величины. Дробление руды осуществляется на щековых или конусных дробилках, а также в шаровых мельницах и других агрегатах. Размельченную руду сортируют по крупности грохочением, подобным просеиванию, на различных по конструкции классификаторах и гидроциклонах.
Обогащение руды основано на различии физических свойств минералов входящих в ее состав: плотностей составляющих, магнитных, физико-химических свойств минералов. Промывка руды водой позволяет отделить плотные составляющие руды от пустой породы (песка, глины).
Гравитация (отсадка) – это отделение руды от пустой породы при пропускании струи воды через дно вибрирующего сита, на котором лежит руда: пустая порода вытесняется в верхний слой и уносится водой, а рудные минералы опускаются вниз.
Магнитная сепарация основана на различии магнитных свойств железосодержащих минералов и частиц пустой породы. Измельченную руду подвергают действию магнита, притягивающего железосодержащие минералы, отделяя их от пустой породы.
19
Окускование производят для переработки концентратов, полученных после обогащения, в кусковые материалы необходимых размеров. Применяют два способа окускования: агломерацию и окатывание.
При агломерации шихту, состоящую на 40–50 % из железной руды, а также известняка (15–20 %), возврата мелкого агломерата (20–30 %), коксовой мелочи (4–6 %), влаги (6–9 %), спекают на агломерационных машинах при температуре 1300–1500 °С. При спекании из руды удаляются вредные примеси (сера, мышьяк), разлагаются карбонаты и получается кусковой пористый офлюсованный материал – агломерат.
При окатывании шихту из измельченных концентратов, флюса, топлива увлажняют, и при обработке во вращающихся барабанах, тарельчатых чашах (грануляторах) она приобретает форму шари- ков-окатышей диаметром до 30 мм. Окатыши высушивают и обжигают при температуре 1200–1350 °С на обжиговых машинах, после чего они становятся прочными и пористыми. Использование агломерата и окатышей исключает отдельную подачу флюсаизвестняка в доменную печь при плавке, так как флюс в необходимом количестве входит в их состав.
Выплавка чугуна. Чугун выплавляют в печах шахтного типа – доменных печах. Сущность процесса получения чугуна в доменных печах заключается в восстановлении оксидов железа, входящих в состав руды, оксидом углерода, водородом, выделяющимся при сгорании топлива в печи, и твердым углеродом.
Устройство доменной печи и ее работа. Доменная печь (рис. 2.1) имеет стальной кожух, выложенный внутри огнеупорным шамотным кирпичом. Рабочее пространство печи включает колошник 6, шахту 5, распар 4, заплечики 3, горн 1, лещадь 15. В верхней части колошника находится засыпной аппарат 8, через который в печь загружают шихту (офлюсованный агломерат и окатыши). Шихту взвешивают, подают в вагонетки 9 подъемника, которые передвигаются по мосту 12 к засыпному аппарату 8 и, опрокидываясь, высыпают шихту в приемную воронку 7 распределителя шихты. При опускании малого конуса 10 засыпного аппарата шихта попадает в чашу 11, а при опускании большого конуса 13 в домен-
20