
Ермолаев Технологические процессы в машиностроении 2011
.pdfщие элементы (Ni, Со. Мо. Сu),сродство к кислороду у которых меньше, чем у железа, при плавке и разливке практически не окисляются, и поэтому их вводят в печь в любое время плавки (обычно вместе с остальной шихтой). Легирующие элементы, у которых сродство к кислороду больше, чем у железа (Si, Mn, Аl, Сг, V,Ti и др.), вводят в металл после раскисления или одновременно с ним в конце плавки, а иногда непосредственно в ковш.
Сталь, её свойства. Сталь – сплав железа с углеродом (FeC) до 2,14 %. Свойства стали подразделяются на:
9физические;
9химические;
9механические;
9технологические;
9эксплуатационные.
Эти свойства необходимо учитывать при выборе материала в зависимости от условий работы деталей и конструкций.
Кфизическим свойствам металлов и сплавов относят: цвет; температуру плавления; плотность; температурные коэффициенты линейного и объёмного расширения; электросопротивление и электропроводимость.
Физические свойства сплавов обусловлены их составом и структурой. Например: температура плавления вольфрама – 3380 оС; тантала – 2996 оС; железо – 1539 оС. Самую низкую температуру плавления имеет ртуть (–38,87 оС). К легкоплавким относят – олово, свинец, цинк.
Кхимическим свойствам относятся способность к химическому воздействию с агрессивными средами, а также антикоррозионные свойства.
Кмеханическим свойствам относят прочность, пластичность, ударную вязкость, усталостную прочность, ползучесть, твердость и износостойкость.
Внешняя нагрузка вызывает в твердом теле напряжение и деформацию. Напряжение – это сила, отнесенная к площади поперечного сечения, МПа: σ = P / F , где Р – сила, МН; F – площадь
поперечного сечения, м2.
31

Деформация – это изменение формы и размеров тела под влиянием воздействия внешних сил или в результате процессов, возникающих в самом теле (например: фазовых превращений, усадки и т.п.). Деформация может быть упругая (исчезающая после снятия нагрузки). При увеличении нагрузки упругая деформация переходит в пластическую; при дальнейшем повышении нагрузки происходит разрушение тела.
Прочность – это способность твердого тела сопротивляться деформации или разрушению под действием статических или динамических нагрузок. Прочность определяют с помощью специальных механических испытаний образцов, изготовленных из исследуемого материала.
Для определения прочности при статических нагрузках образцы испытывают на растяжение, сжатие, изгиб и кручение. Испытания на растяжение обязательны. Прочность при статических нагрузках оценивается временным сопротивлением σв и пределом текучести σт; σв – это условное напряжение, соответствующее наибольшей нагрузке, предшествующей разрушению образца; σт – напряжение, при котором начинается пластическое течение металла.
Прочность при динамических нагрузках определяют по данным испытаний: на ударную вязкость (разрушение ударом стандартного образца на копре), на усталостную прочность (определение способности материала выдерживать, не разрушаясь, большое число повторно-переменных нагрузок), на ползучесть (определение способности нагретого материала медленно и непрерывно деформироваться при постоянных нагрузках).
Пластичность – это способность материала получать остаточное изменение формы и размеров без разрушения. Пластичность характеризуется относительным удлинением δ при разрыве:
δ = (l −l l0 ) 100% ,
где l – длина образца после разрыва, мм; l0 – первоначальная длина образца, мм.
Твердость – это способность материала сопротивляться внедрению в него другого, более твердого тела, не получающего остаточ-
32
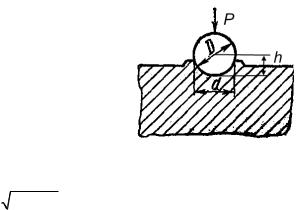
ных деформаций. Значение твердости и её размерность для одного и того же материала зависят от применяемого метода измерения. Значения твердости определенные раз-
личными методами, пересчитывают по |
|
|
таблицам и эмпирическим формулам. |
|
|
Например, |
твердость по Бринеллю |
|
(НВ, МПа) (рис. 2.2) определяют из |
|
|
отношения нагрузки Р, приложенной к |
|
|
шарику, к площади поверхности полу- |
|
|
ченного отпечатка шарика Fотп: |
|
|
|
НВ = Р/Fотп, |
Рис. 2.2. Схема измерения |
где F – площадь сферического отпе- |
твердости по Бринеллю: |
|
чатка |
|
D – диаметр шарика; |
|
πD(D − D2 −d 2 ) . |
d – диаметр отпечатка; |
F = |
h – глубина отпечатка |
|
|
2 |
|
К технологическим свойствам относится способность стали подвергаться различным методам горячей и холодной обработки: литейные свойства, деформируемость, свариваемость и обрабатываемость режущим инструментом. Эти свойства позволяют производить формоизменяющую обработку и получать заготовки и детали машин.
Литейные свойства определяются способностью расплавленного металла или сплава к заполнению литейной формы, степенью химической неоднородности по сечению полученной отливки, а также величиной усадки – сокращением размеров при кристаллизации и дальнейшем охлаждении.
Деформируемость – это способность принимать необходимую форму под влиянием нагрузки без разрушения и при наименьшем сопротивлении нагрузке.
Свариваемость – это способность металлов и сплавов образовывать неразъемные соединения требуемого качества.
Обрабатываемость – свойство металла поддаваться обработке резанием. Критериями обрабатываемости являются режимы резания и качество поверхностного слоя.
Технологические свойства часто определяют выбор материала для конструкции. Разрабатываемые материалы могут быть внедре-
33
ны в производство только в том случае, если их технологические свойства удовлетворяют необходимым требованиям.
К эксплуатационным свойствам в зависимости от условия работы машины или конструкции относят:
износостойкость – способность материала сопротивляться поверхностному разрушению под действием внешнего трения;
коррозионную стойкость – сопротивление сплава действию агрессивных кислотных и щелочных сред;
хладостойкость – способность сплава сохранять пластические свойства при температурах ниже 0 оС;
жаропрочность – способность сплава сохранять механические свойства при высоких температурах;
жаростойкость – способность сплава сопротивляться окислению в газовой среде при высоких температурах;
антифрикционность – способность сплава прирабатываться к другому сплаву.
Эти свойства определяются в зависимости от условия работы машин или конструкций специальными испытаниями.
При выборке материала для создания технологической конструкции необходимо комплексно учитывать его прочностные, технологические и эксплуатационные характеристики.
Диаграмма состояния железо-углерод. На диаграмме показа-
ны различные превращения, происходящие в сплавах (от чистого железа до цементита, содержащего 6,67 % углерода, от комнатной температуры до температуры плавления железа и цементита) (рис. 2.3). Цементит Fe3С – химическое соединение железа с углеродом, которое образуется при кристаллизации сплава, содержащего 93, 33 % Fe и 6,67 % С (максимальная растворимость углерода в железе). Диаграмма имеет применение при термической обработке и обработке металлов давлением.
На упрощенной диаграмме по оси ординат отложены температуры, а по оси абсцисс – процентное содержание углерода в сплаве железо – углерод. На ординатах имеются критические точки: А соответствует температуре 1539 °С, G – 911 °С (левая ордината соответствует 100 %-ному содержанию железа), D – 1600 °С, F – 1147 °С, K – 727 °С (правая ордината соответствует 100 %-ному содержа-
нию Fe3C).
34
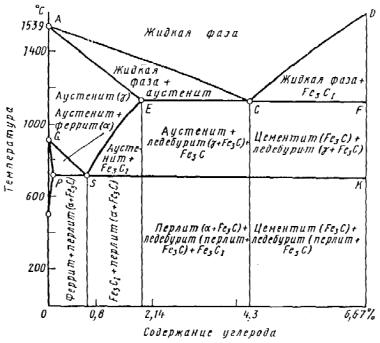
Рис. 2.3. Диаграмма состояния железо-углерод
Критические точки на диаграмме: Р отвечает температуре 727 °С
ссодержанием 0,025 % углерода , S – 727 °С с содержанием 0,8 % углерода; Е – 1147 °С с содержанием 2,14 % углерода; С – 1147 °С
ссодержанием 4,3 % углерода; К – 727 °С с содержанием 6,67 % углерода и F – 1147 °С с содержанием 6,67 % углерода. Область диаграммы влево от вертикальной линии, отвечающей содержанию углерода, равному 2,14 %, характеризует стали, вправо – чугуны.
Линия ACD соответствует температурам, выше которых сплавы
слюбым содержанием углерода (от 0 до 6,67 %) находятся в жидком состоянии. Эта же линия соответствует температурам начала затвердевания жидких сплавов. Линию ACD называют ликвидус, а линию AECF – солидус. Линии GSE и PSK диаграммы – области затвердевающего сплава – объясняют происходящие изменения структуры в системе сплава в твердом состоянии. При охлаждении
35
в сплавах происходят внутренние преобразования, при которых меняется структура сплава.
Структурные составляющие железоуглеродистых сплавов в металлографии имеют особые названия: феррит, цементит, аустенит, перлит и ледебурит.
Феррит обладает небольшой прочностью, невысокой твердостью (НВ 80–100), сравнительно небольшой вязкостью и до температуры 768 °С – магнитными свойствами.
Цементит (карбид железа) представляет собой химическое соединение железа с углеродом. Цементит обладает твердостью около НВ 800.
Аустенит представляет собой твердый раствор углерода в железе, образующийся при содержании углерода в сплаве от 0,8 до 2,14 %. В стали аустенит существует при температуре свыше 727 °С. При медленном охлаждении сплава аустенит распадается на феррит и цементит. При быстром охлаждении аустенит не успевает распасться. Частичный распад аустенита дает структуры сплава – мартенсит, троостит и сорбит. Эти структуры представляют наибольший интерес при рассмотрении термической обработки.
Перлит образуется при распадении аустенита, содержащего 0,8 % углерода. Структура перлита имеет вид перемешанных очень мелких светлых и темных частичек в виде пластинок или зерен; в соответствии с этим перлит называется пластичным или зернистым. Темные частички называются ферритом, а светлые – цементитом. Перлит обладает достаточно высокой вязкостью и твердостью НВ 200.
Ледебурит представляет собой механическую смесь аустенита и цементита при содержании углерода в сплаве 4,3%. Такую смесь называют эвтектикой. Ледебурит (белый чугун) обладает высокой твердость и хрупкостью.
Температура плавления сплава по мере увеличения содержания углерода понижается (линия АС на рис. 2.3), достигая наименьшего значения в точке С, соответствующей 1147 °С; для сплава с содержанием углерода 4,3 % при дальнейшем увеличении содержания углерода температура плавления повышается (линия CD), достигая 1600 °С при содержании углерода 6,67 %.
36
Линия AECF соответствует температурам конца затвердевания жидкого сплава. Если сплав содержит углерода меньше 4,3 %, затвердевание его происходит в интервале температур между линиями АС и AEC, при этом из сплава выделяются кристаллы твердого раствора аустенита. Если в сплаве содержание углерода больше 4,3 %, то он затвердевает между линиями CD и CF, при этом выделяются кристаллы цементита.
Ниже линии AECF сплавы находятся в твердом состоянии в виде стали или чугуна. При дальнейшем охлаждении стали аустенит начинает распадаться, выделяя феррит или цементит, в зависимости от содержания углерода. Начало распада аустенита происходит в зависимости от содержания углерода при температуре, соответствующей линии GSE и заканчивается при температуре 727 °С для всех сплавов независимо от содержания углерода (прямая РК). Линия PSK называется эвтектоидной, ниже ее превращения в сплавах не происходят. При содержании в стали 0,8 % в области между линиями GS и PS из аустенита будет выделяться феррит, пока концентрация углерода не достигнет 0,8 %, после чего оставшийся аустенит перейдет в перлит при температуре 727 °С.
Структура стали, содержащая углерода менее 0,8 %, состоит из механической смеси феррита с перлитом. Если содержание углерода в аустените больше 0,8 %, то в области между линиями SE и SK из аустенита будет выделяться цементит, в связи с чем процентное содержание углерода в аустените будет уменьшаться, и когда оно достигнет 0,8 %, аустенит при температуре 727 °С перейдет в перлит. Структура такой стали будет состоять из цементита и перлита. Сталь при достаточно медленном охлаждении может иметь одну из трех структур, зависящих от содержания в ней углерода: при содержании углерода до 0,8 % структура стали представляет собой механическую смесь феррита и перлита, при содержании углерода 0,8 % структура стали – перлит, при содержании углерода более 0,8 % структура стали представляет собой смесь цементита с перлитом.
Классификация сталей. Стали классифицируются по химическому составу, качеству и назначению (рис. 2.4). По химическому составу классифицируют главным образом конструкционные ста-
37

ли, предназначенные для изготовления деталей машин и металлических конструкций. Конструкционные стали делят на углеродистые и легированные.
Mn P
0,05%
СТАЛЬ = Fe + C → < 2,14 % 1,35%
S Si
ПО ХИМИЧЕСКОМУ СОСТАВУ:
по углероду
2. ПО НАЗНАЧЕНИЮ
1.Конструкционная сталь
2.Сталь инструментальная
3.Специальная – нержавеющая, жаростойкая
по легированию
3. ПО КАЧЕСТВУ
ОБЫКНОВЕННОГО КАЧЕСТВА
0,06/0,07
КАЧЕСТВЕННАЯ 0,04/0,04
В/КАЧЕСТВЕННАЯ 0,025/0,025
О/ВЫСОКОКАЧЕСТВЕННАЯ
0,015/0,025
ПО СТЕПЕНИ РАСКИСЛЕНИЯ (УДАЛЕНИЕ О2 ИЗ ЖИДКОГО МЕТАЛЛА)
Спокойная |
Полуспокойная |
|
Кипящая |
сп – ХОРОШО рас- |
пс – промежуточное |
|
кп – не полностью |
положение между |
|
||
кислена |
|
раскислена |
|
сп и кп |
|
||
|
|
|
|
|
Рис. 2.4. Классификации сталей |
|
38
Углеродистые |
стали могут |
быть низкоуглеродистые: |
C ≤0,09 ÷0,25 % ; среднеуглеродистые: C ≤0,25 ÷0,45 % и высо- |
||
коуглеродистые: |
C ≤0,45 ÷0,75 % . |
Легированные стали условно |
подразделяют на низколегированные с содержанием легирующих элементов 2,5–5 %; среднелегированные – до 10 % и высоколегированные – более 10 %.
Другие стали, например инструментальные, с особыми физикохимическими свойствами по химическому составу обычно не классифицируются.
По назначению стали подразделяют на конструкционные, инструментальные и стали и сплавы с особыми свойствами – жаропрочные, кислотостойкие, износостойкие, магнитные и др.
По качеству различают стали общего назначения, качественные, высококачественные и особовысококачественные, в последнем случае в маркировке указывается способ выплавки и последующей обработки стали.
Стали углеродистые общего назначения согласно ГОСТ 380-88 подразделяются на три группы: группа “A” – регламентированы механические свойства, группа “Б” – регламентирован химический состав, и группа “B” – регламентированы оба показателя. В соответствии с этим стали обозначают БСт1, ВСт2, –, БСт6, ВСт3 и т.д.;
всталях первой группы буквенный индекс, как правило, опускается: Ст3, Ст5 и т.д. Чем выше номер в обозначении, тем выше прочность стали и ниже её пластичность. Стали этой группы в зависимости от степени раскисления подразделяются на спокойные – “сп”, полуспокойные – “пс” и кипящие – “кп”: индекс “сп” обычно
вобозначении опускается, а другие ставятся в конце марки: БСт3пс, ВСт2кп.
Качественные углеродистые стали согласно ГОСТ 1050-74 маркируются цифрами, указывающими среднее содержание углерода в сотых долях процента: сталь 10, сталь 15, ..., сталь 80. Содержание серы и фосфора в этих сталях не должно превышать 0,035 %. стали этой группы, содержащие свыше 0,2 % С, выпускается только спокойными.
Углеродистые инструментальные стали (ГОСТ 1435-75 более 0,7% С) имеют в обозначении букву “У” и цифру, указывающую на содержание углерода в десятых долях процента: У9, У10 и т.д.
39
Легированные конструкционные стали (ГОСТ 4543-71) в зависимости от содержания серы и фосфора подразделяются на качественные (менее 0,035% каждого), высококачественные (менее 0,25% каждого) и особовысококачественные, содержащие S ≤0,015 % и P ≤0,025 % .
Все высоколегированные стали содержат минимальное количество вредных примесей и являются высококачественными. Для придания особых свойств их подвергают дополнительной обработке специальными методами, которые отражены в обозначении сталей в конце наименования марки. ВД – вакуумно-дуговой переплав, Ш – электрошлаковый переплав, ВИ – вакуумно-индукци- онная выплавка, СШ – обработка синтетическими шлаками.
Маркировка легированных сталей. В основу маркировки ле-
гированных сталей в России положено буквенно-цифровая система (ГОСТ 4543-71). Легирующие элементы обозначаются буквами русского алфавита: марганец – Г, кремний – С, хром – Х, никель – Н, вольфрам – В, ванадий – Ф, титан – Т, молибден – М, кобальт – К, алюминий – Ю, медь – Д, бор – Р, ниобий – Б, цирконий – Ц, азот – А.
Количество углерода, как и при обозначениях углеродистых сталей, указывается в сотых долях процента цифрой, стоящей в начале обозначения; количество легирующего элемента в процентах указывается цифрой, стоящей после соответствующего индекса. Отсутствие цифры после индекса элемента указывает на то, что его содержание менее 1,5 %. Высококачественные стали имеют в обозначении букву А, а особовысококачественные – букву Ш, проставляемую в конце. Например, сталь 12Х2Н4А содержит 0,12 % С, около 2 % Сr, около 4 % Ni и менее 0,025 % S и Р.
Влегированных инструментальных сталях цифра в начале указывает среднее содержание углерода в десятых долях процента, если его содержание менее 1 %; если равно 1 % или больше, то цифру не ставят, например: сталь 3Х2В8Ф содержит 0,3 % С, а сталь ХВГ – больше 1 % С.
Вмаркировке сталей иногда ставят буквы, указывающие на их применение: А – автоматные; Р – быстрорежущие; Ш – шарикоподшипниковые; Э – электротехнические.
40