
ЛС_конспект лекций
.pdf11.4.2.Технология работы
При выполнении погрузочно-разгрузочных операций мостовыми кранами-штабелёрами вначале выполняются манипуляции по перемещению грузозахвата в торце стеллажей – грузозахват «находит» проход стеллажах, в котором расположена ячейка с заданным адресом и ориентирует вилы в сторону заданной секции. Затем колонна входит в проход между стеллажами и грузозахват находит заданную ячейку стеллажа за счёт передвижения грузозахвата по колонне (поиск по координате «Z») и передвижения собственно моста (поиск по координате «Y»).
41
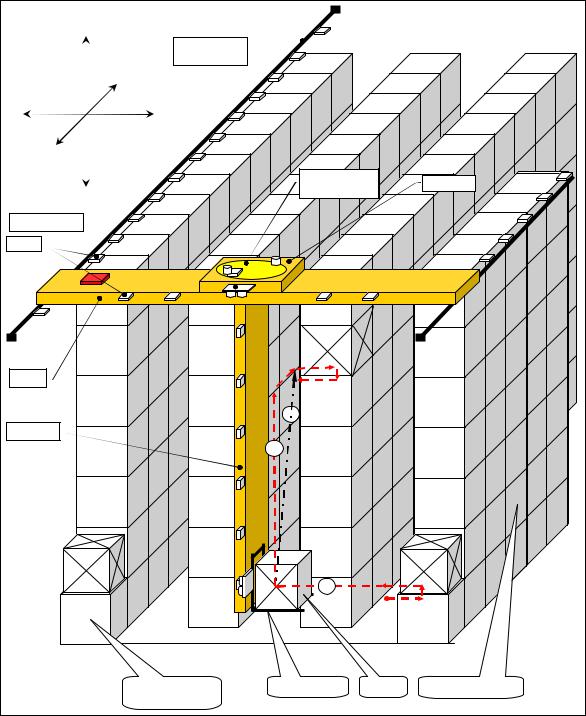
Z (Вверх) |
|
|
|
|
|
подкрановый |
|
|
|
|
рельс |
|
|
|
|
Y (Вперёд) |
|
|
|
X (Влево) |
X (Вправо) |
|
|
|
|
|
|
|
|
0 |
|
|
|
|
Y (Назад) |
|
|
|
|
|
|
поворотный |
тележка |
|
Z (Вниз) |
круг |
|
||
|
|
|||
|
|
|
||
блок датчиков |
|
|
|
|
шунт |
|
|
|
|
мост |
|
|
|
|
|
|
с |
|
|
колонна |
|
|
|
|
|
|
п |
|
|
|
|
п |
|
|
|
перегрузочное |
грузозахват |
груз |
ячейка стеллажа |
|
устройство |
|
|
|
Рис.11.5. Схема траектории движения грузозахвата при складировании груза |
||||
стеллажным роботом мостового типа в монооперациях |
||||
П – последовательный режим передвижения грузозахвата; С – совмещенный режим |
||||
|
|
42 |
|
|
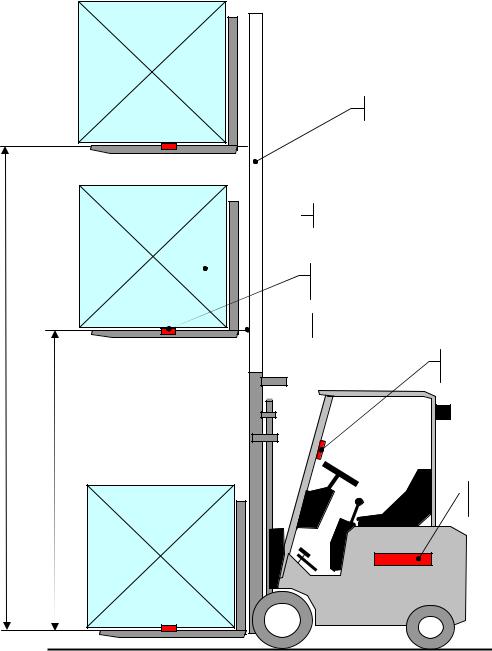
11.5.ОПТИМИЗАЦИЯ РЕЖИМОВ РАБОТЫ ПОГРУЗЧИКОВ
Этот тип подъёмно-транспортного механизма широко применяется на всех видах складов (рис. 11.6).
SHmax
Shc
мачта
груз
тензодатчик
перегрузки
позиция «А»
информационное
табло
бортовой
контроллер
Рис. 11.6. Погрузчик с грузом
43
При последовательном движении грузозахвата время, за-
трачиваемое на выполнение складского задания погрузчиком рассчитывается по формуле
t =Sy +SHmax− Shd +Shd +Sx +t |
||||||||
pп |
|
|
|
|
|
, |
||
|
|
|
|
|
|
|
вп |
|
V |
|
V |
|
V |
|
|||
|
|
|
V |
|||||
|
y |
|
z |
|
z |
|
x |
где Sx , Sy – расстояние, проходимое ГЗ погрузчика по «X», «Y»;
Vx , Vy , Vz – скорость движения ГЗ соответственно по координатам «X»; «Y»; «Z», соответственно;
SHmax – максимальное расстояние, которое ГЗ может проходить по вертикали (координате «Z»);
Shс – расстояние, которое грузозахвату допускается безопасно проходить с грузом по вертикали в совмещённом режиме.
Однако погрузчики имеют возможность совмещать движения ГЗ по двум координатам (X-Z или Y-Z), но при этом следует учитывать ограничения по совмещению движений в указанных координатах.
Суть ограничений связано с тем, что погрузчик может беспрепятственно совмещать движения ГЗ, если он не загружен, но если погрузчик везёт груз, то совмещение движений ГЗ разрешается только с расчётной точки (позиции) по координате «Z» (условно обозначена позиция «А»), ниже которой гарантируется устойчивое положение погрузчика. Поэтому при совмещении движений ГЗ погрузчика время, затрачиваемое на выполнение складского задания рассчитывается по формуле
|
|
|
S |
y |
|
S |
H max |
− S |
hd |
|
Shd |
|
Sx |
|
|||
t |
pс |
= |
|
+ |
|
|
+ |
+ |
+t . |
||||||||
|
|
|
V |
|
|
|
|
|
|||||||||
|
V |
y |
|
|
z |
|
|
|
V |
z |
V |
|
вп |
||||
|
|
|
|
|
|
|
|
|
|
|
|
|
x |
При использовании современных средств вычислительной техники использование бортовых контроллеров и средств тензоизмерительного контроля позволит автоматически оптимизировать процесс перемещения грузозахвата погрузчика за счёт деблокировки режима совмещения движения ГЗ по горизонтали (координаты «X» или «Y») и по вертикали (координата «Z»).
44
Расчёт оптимального времени перемещения ГЗ зависит от выполнения одного из условий:
1) если |
S y |
+ |
SH max − Shd |
³ |
Shd |
+ |
Sx |
, |
то |
|
|
|
||||||||||||||
|
|
|
|
|
|
|
|
|
|
|||||||||||||||||
|
Vy |
Vz |
|
|
|
|
|
|
|
|
|
|
Vz |
|
|
Vx |
|
|
|
|
||||||
|
|
|
t |
рс1 |
= |
|
S y |
+ |
SH max − Shd |
+t |
вп |
. |
||||||||||||||
|
|
|
|
|
|
|
|
|||||||||||||||||||
|
|
|
|
|
|
V |
y |
|
|
|
|
|
|
|
V |
z |
|
|
|
|||||||
|
|
|
|
|
|
|
|
|
|
|
|
|
|
|
|
|
|
|
|
|
|
|
||||
2) если |
S y |
+ |
SH max − Shd |
£ |
Shd |
+ |
Sx |
, |
то |
|
|
|
||||||||||||||
|
|
|
|
|
|
|
|
|||||||||||||||||||
|
Vy |
Vz |
|
|
|
|
|
|
|
|
|
|
Vz |
|
|
Vx |
|
|
|
|
||||||
|
|
|
|
|
t |
рс2 |
= |
Shd |
+ |
Sx |
+t |
вп |
. |
|
|
|||||||||||
|
|
|
|
|
|
|
|
|
||||||||||||||||||
|
|
|
|
|
|
|
|
|
|
Vz |
|
Vx |
|
|
|
|||||||||||
|
|
|
|
|
|
|
|
|
|
|
|
|
|
|
|
|
|
|
11.6. Методы расчёта оптимального времени поиска складской ячейки подъёмно-транспортными машинами
Ниже рассмотрены методы расчёта оптимального времени поиска складской ячейки подъёмно-транспортными машинами ПТМ, методология расчёта экономии складских затрат за счёт организации совмещения движений грузозахватов складских механизмов в современных складах логистических систем.
В логистике складирования для прогнозирования точного
времени выполнения складских технологических процессов (на-
пример, операций приёма-выдачи на складе), необходимо иметь достоверные данные по времени выполнения отдельных операций складскими механизмами.
Кроме того, при выполнении складских заданий следует на-
ходить оптимальный маршрут движения грузонесущего органа
(грузозахвата) складского механизма.
Для решения вышеназванных задач разработан базовый ал-
горитм расчёта оптимального времени выполнения складских технологических операций в совмещённом режиме (раздел 2).
Для предварительного апробирования эффективности предлагаемых автором методик, следует воспользоваться со-
45
временными методами имитационного моделирования или экс-
периментальными методами.
Стратегической задачей, которая должна решаться в логистике складирования - задача оптимизации маршрута, то есть определения кратчайшего пути достижения заданного адреса ячейки грузозахватом складского механизма в совокупности с достижением стабильности выполнения складских операций в долгосрочном временном интервале.
Радикальным решением поставленной задачи является эф-
фективное совмещение движений грузозахвата складского подъ-
ёмно-транспортного механизма в процессе поиска заданного адреса ячейки в плоскости или в пространстве, а как следствие, высокая и предсказуемая производительность складской переработки грузов.
Следует подчеркнуть, что до настоящего времени в учебной и научной литературе не уделено серьёзного внимания решению рассмотренным в статье задачам. Однако очевидна их важность особенно в связи с общей тенденцией использования автоматизированных систем управления ПТМ в логистике складирования.
Рассмотренная в данном разделе методология расчёта времени выполнения оптимизируемых операций при перемещении штучных грузов на складе позволяет определить экономический эффект от внедрения технологии совмещения движений грузозахватов складских ПТМ.
Предлагаемая методика расчётов позволяет принимать оптимальные решения в следующих случаях:
∙сравнительная оценка эффективности работы (ОЭР) складских ПТМ на базе показателей коэффициентов совмещения движений грузозахвата ПТМ в плоскости и в пространстве;
∙качественный выбор наилучшего ПТМ по техническим характеристикам и производительности из предлагаемых на рынке.
∙определение минимальных затрат от применения методики оптимизации маршрута движения грузозахвата ПТМ в процессе поиска заданной ячейки склада при выполнении отдельного складского задания по приёму или выдаче груза;
46
∙ оценка экономии финансовых затрат за счёт мониторинга функционирования склада и последующего анализа получаемых результатов.
Приведённый в статье алгоритм может быть использован как универсальный при применении рассмотренной методологии.
Экономия времени на погрузочно-разгрузочные операции за счёт совмещения движений грузозахвата позволяет сократить финансовые затраты на складские операции до 50%, что значительно влияет на снижение стоимости складской переработки грузов.
Рассмотренные методы расчёта, в конечном счёте, помогут оценить эффективность технологии совмещения движений ГЗ при выполнении операций поиска заданного адреса ячейки складирования не только для кранов-штабелёров, но и для других складских механизмов: погрузчиков и роботов.
Очевидно, что рассмотренная методология должна базироваться на использовании современных IT-технологиях и средствах вычислительной техники.
11.7. Методы оптимальной компоновки штучных грузов на грузоносителях и их экономическая эффективность
11.7.1. Общие сведения
Рассмотрены методы оптимальной компоновки штучных грузов на грузоносителях (поддонах и контейнерах) и в грузовых отсеках транспортных средств с использованием оригинальных математических моделей. Даны алгоритмы расчёта эффективности компоновочных решений и факторы экономии складских логистических затрат от применения этих методов. Приведены эскизы компоновки грузовых пакетов.
Приведён ряд специфических терминов логистики складирования, используемых в описании этой методики.
Актуальность темы в том, что существующие методы и программы расчёта компоновки грузов на грузоносителях формализованы и не позволяют просто адаптировать их к конкретным прикладным задачам.
47

Здесь же приведены методы простых для понимания расчётов компоновки грузов на грузоносителях при решении широкого спектра задач по загрузке грузоносителей и грузовых отсеков транспортных средств.
Влогистике складирования значительное время занимают погрузочно-разгрузочные операции. Статистика утверждает, что это время зачастую занимает до 60-70 % времени перевозки «из пункта А в пункт В».
Вкачестве методов сокращения этого времени можно на-
звать:
∙увеличение интенсивности (производительности) функционирования рабочих механизмов;
∙высокая организация погрузочно-разгрузочных операций с минимизацией пресловутого «человеческого фактора»;
∙эффективная компоновка грузов на грузоносителях (ГН), используя максимальное заполнение (загрузку) их по объёму и/или по грузоподъёмности.
Особое место в организации погрузочно-разгрузочных опе-
раций следует уделять комплектации грузов на грузоносителях – поддонах и контейнерах. Предлагаемые математические модели компоновки8 грузов позволят без особых проблем решить задачи оптимального заполнения грузоносителей, чтобы, как говорят транспортники, «не возить воздух».
Кроме того, для прогнозирования точного времени выполне-
ния складских технологических операций приёма-выдачи на скла-
де, необходимо иметь достоверные данные по времени выполнения отдельных операций по компоновке грузов.
Приведённая информация поможет читателю изучить терминологию, используемую в сфере компоновочных операций в логистике складирования (ЛСК), приобрести опыт выполнения расчётов по формированию складских и транспортных грузовых пакетов из отдельных упаковок при подготовке грузов к перевоз-
8 компоновка – [< componere ] – составлять из отдельных частей одно целое. Здесь, компоновать, то есть – составлять (размещать) на грузоносителях из отдельных штучных грузов компактные грузовые пакеты, эффективно используя объём и грузоподъёмность грузовых контейнеров.
48
ке и расчётов по загрузке жёстких грузовых контейнеров, вагонов, грузовых отсеков и других транспортных средств (ТС).
На практике расчётные операции, предшествуют технологическим операциям по формированию грузовых пакетов и рациональной загрузке крупнотоннажных и авиационных грузовых контейнеров.
11.7.2.Компоновочные решения
Особенности логистического подхода к компоновке
В логистике складирования рассматриваются методологии, позволяющие:
∙получить наилучшие решения по компоновке грузов на грузоносителях;
∙применять технологические схемы складирования в ТС с целью минимизации времени погрузочно-разгрузочных операций и трудозатрат.
Эффективное применение рассматриваемых в данной работе методологий базируется на точном расчёте компоновочных решений по предложенным алгоритмам и компьютерным программам. От профессионального применения предлагаемых методик зависит сохранность груза, суммарное время перевозки, эффективное использование транспортных средств. Апробирование этих методик на практике является предпосылкой эффективного складирования и транспортного процесса в логистике складирования (ЛСК) в целом и, в конечном итоге, - реального осуществления базовых концепции логистики.
Впредлагаемой работе даны рекомендации по практической реализации компоновочных решений (подробнее изложено в [6]).
11.8.Технологический процесс компоновки
Вобщем виде - это процесс последовательного выполнения операций по формированию складской грузовой единицы или процесс загрузки грузов в контейнер или ТС. Этот процесс базируется на поиске оптимального варианта компоновки упаковок на
49
грузоносителях (поддонах) или грузовых пакетов в контейнерах, кузовах и грузовых отсеках транспортных средств, используя приведённые ниже математические модели (МТМ), с целью последующей его реализации.
На основании предлагаемых МТМ разработаны: базовый вариант компоновочного алгоритма; технологические схемы компоновки для ручной - на грузоносителях и для автоматизированной - в пакетоформировочных машинах.
11.9.Математические модели расчёта компоновок
Для эффективного формирования грузовых пакетов (ГП) или укладки ГП в контейнеры, на платформы ж.д. вагонов, в автомобили, в грузовые отсеки воздушных, морских и речных судов предлагаются разработанные автором математические модели. Эти модели можно применять для грузов, которые нельзя кантовать, то есть грузы, которые нельзя укладывать на бок или на торец. Они могут широко применяться для выбора наиболее эффективного варианта компоновки грузов на грузоносителе (поддон, контейнер) или в грузовых ёмкостях вышеперечисленных транспортных средств, используемых для грузовых перевозок.
Для каждой математической модели предлагается использо-
вать компактную символьную запись компоновки.
Например, математическая модель типа МР-1 обозначается символьной записью: «l-L & b-B» . По этой модели рассчитывается компоновка упаковок на грузоносителе, при этом изделия (упаковки, грузы) укладывается на рабочую плоскость (дно) грузоносителя длинной стороной упаковки (l) по длинной стороне грузоносителя (L) и короткой стороной упаковки (b) по короткой стороне грузоносителя (B).
Врассматриваемых математических моделях (МТМ) предлагаются гибкие варианты решения, позволяющие в результате их применения выбрать наиболее рациональный, а фактически, оптимальный вариант компоновки.
ВМТМ, для не кантуемых грузов, выделены две группы:
50