
книги из ГПНТБ / Шнейдер, Юрий Григорьевич. Холодная бесштамповая обработка точных деталей давлением
.pdfо
—-------105----- -
Фиг. 57. Устройство к резьбонакатному станку для накатывания длинных резьб роликами
с кольцевой нарезкой.
определяется в основном точностью заготовок; фактическое рассеи вание размеров составило 0,09 мм;
2) фактическое рассеивание шага накатанной резьбы составило
45 мк.
По всем параметрам резьба, накатанная роликами с кольцевой нарезкой, соответствует 2-му классу точности на всей длине накаты
вания.
Накатывание резьбы на проход может производиться с помощью устройств типа, показанного на фиг. 57х.
Устройство состоит из двух одинаковых головок, одна из которых устанавливается на неподвижную, а другая — на подвижную бабку резьбонакатного станка. При помощи болтов и шпонок 9 и 13 головки закрепляются на имеющихся в корпусах бабок приливах для люне тов, поддерживающих шпиндели станков под углом т, соответствую щим углу подъема резьбы. Корпус каждой головки состоит из осно вания 4 с двумя стойками 11, из которых одна съемная, закрепляю щаяся на основании при помощи шпонки 10 и болтов 12. В стойках
корпуса, в игольчатых подшипниках 1, расположен валик-шестерня 3
с косыми зубьями. Ось валика вместе со всей головкой наклонена к оси шпинделя под углом, равным углу подъема накатываемой резьбы т.
Этому же углу равен и угол наклона зубьев шестерни валика. На валике шпонкой 6 и разъемной гайкой 8 закрепляется накатной ролик 7 с кольцевой нарезкой. Для фиксирования положения
накатного ролика в продольном направлении служит съемная втулка 5. Вращение накатному ролику передается от шпинделя резьбонакатного станка цилиндрической шестерней 2. Последняя закреплена на шпинделе станка с помощью шпонки и разжимной гайки и сцепляется с шестерней валика 3. Основными досто инствами описанного способа накатывания длинных резьб явля ются:
1)сравнительно малые усилия накатывания;
2)высокая производительность благодаря непрерывной подаче заготовок;
3)возможность автоматизации процесса накатывания;
4)универсальность роликов (одним комплектом роликов могут быть накатаны резьбы различного диаметра, одно- и многозаходные,
справой и левой резьбой заданного шага).
Внастоящее время разработана новая конструкция универсаль
ного резьбонакатного |
станка PH ЮК для накатывания резьбы |
как винтовыми, так и |
кольцевыми роликами. |
Новый способ накатывания длинных трапецеидальных и других специальных резьб с крупным шагом разработан в ЦНИИТМАШ.
Способ поперечно-винтовогонакаты вания осуще
ствляется по схеме, показанной на фиг. 51, г.
Оси роликов 1 и 2 наклонены относительно заготовки 4 и в про цессе накатывания остаются на постоянном межцентровом расстоянии
одна от другой.
1 Разработано Ленинградским филиалом ВПТИ к резьбонакатному станку РН-24.
112
Заготовка подается в осевом направлении, захватывается враща ющимися роликами и, поддерживаемая двумя проводками 3, полу чает вращательное и поступательное перемещение.
Ролики могут быть выполнены как с кольцевыми, так и с винто выми канавками.
Профиль канавок кольцевых и винтовых роликов соответствует профилю накатываемой резьбы; шаг канавок винтовых роликов должен быть равным шагу накатываемой резьбы.
При накатывании кольцевыми роликами оси последних должны быть наклонены на угол, равный углу подъема накатываемой резьбы
по среднему диаметру.
При накатывании длинных резьб роликами с винтовым профилем
угол подъема резьбы на роликах должен отличаться от угла подъема накатываемой резьбы на заготовке. Угол перекоса осей в этом случае
зависит от угла подъема и направления накатываемой резьбы
ирезьбы на роликах.
Восевом направлении витки роликов долж’ны быть установлены один против другого. Описанный способ накатывания используется не только для образования резьбы, но и для получения поперечно
винтовой прокаткой в винтовых калибрах (валках) таких деталей сплошного и полого сечения, как шары, ролики, втулки и т. п.
Расчет калибровки' роликов при поперечно-винтовой прокатке производят исходя из основных кинематических соотношений дан
ного процесса [24]. При установившемся процессе накатывания скорость осевой подачи заготовки определяется по формуле
и— v sin а мм/сек,
где v — окружная скорость накатных роликов в мм/сек; а — угол между осями роликов и заготовки в град.
При накатывании роликами с винтовой нарезкой в случае, когда направление резьбы на роликах и заготовке разноименное и угол подъема накатываемой резьбы рз больше угла подъема резьбы на роли
ках рр, осевая скорость заготовки может быть выражена формулой
|
и = v sin а = |
- sin ( 3 — р), |
где |
Dcp — средний диаметр резьбы на роликах в мм; |
|
|
п ■— число оборотов роликов |
в минуту. |
|
Так как углы подъема резьбы малы, то принимается |
|
|
Sin ( 3—Рр) ^tg 3 —tg рр; |
|
|
tg p=^-, |
|
где |
k — число заходов резьбы на заготовке; |
|
|
т — число заходов резьбы на роликах; |
|
|
t — шаг резьбы в мм; |
заготовки в мм. |
dcp — средний диаметр резьбы |
8 Ю. Г. Шнейдер 648 |
ИЗ |
Таким образом,
Скорость осевой подачи при накатывании роликами с кольцевой нарезкой (т = 0) может быть определена по формуле
Размеры и параметры роликов с винтовой нарезкой определяются размерами и параметрами накатываемой резьбы и принятой схемой процесса накатывания.
При выборе диаметра роликов исходят из требуемого усилия при накатывании (с уменьшением диаметра роликов снижаются усилия накатывания и скорость скольжения) и стойкости роликов (с уве личением диаметра роликов стойкость их повышается).
Ролики для поперечно-винтового накатывания резьбы имеют заборный конус и цилиндрический калибрующий участок.
При коэффициенте трения 0,05 0,08 (холодное накатывание со смазкой без принудительной подачи заготовки) угол наклона образующей заборного конуса для надежного захвата заготовки
должен быть равен 3 |
5°. |
В случае принудительной подачи заготовки (например, с помощью
гидравлического или пневматического цилиндра) угол заборного конуса может быть увеличен по сравнению с углом трения.
После захвата заготовки одним или несколькими витками роликов
устойчивость процесса накатывания определяется величинами ради альных обжатий, производимых каждым витком профиля. Если радиальные обжатия превосходят определенную величину, заготовка начинает буксовать в роликах и процесс накатывания прекращается.
Радиальное обжатие при поперечно-винтовом накатывании резьбы определяют по формуле
z = stg ф мм,
где |
s — осевая подача заготовки за пол-оборота в мм; |
|
|
<р — угол заборного конуса роликов в |
град.; |
|
s = at, |
|
где |
и — скорость осевой подачи заготовки |
в мм/сек-, |
т — продолжительность полуоборота заготовки в сек.
_ 30 dCp
пDcp
s=4(4-^)-
Таким образом, радиальное обжатие
mdCp \ Dcp J
114
Для расчетов, связанных с предельными обжатиями, в первом приближении можно пользоваться таким соотношением, определяю щим условие захвата заготовки при обычном процессе поперечной
прокатки [241:
гРФ
d~'^'
1 |
л |
|
, |
мм; |
где z — обжатие за — |
оборота (7 — число валков |
в стане) в |
||
d — диаметр заготовки в |
мм; |
|
|
|
D — диаметр валка в мм; |
между заготовкой и |
валком; |
|
|
р, — коэффициент трения |
|
|||
ф — коэффициент |
уширения. |
|
|
При проектировании резьбонакатных роликов обжатия не должны превышать величин, вычисленных по данной формуле.
Остальные параметры роликов (ширина, угол заборного конуса, ширина калибрующего участка) рассчитывают исходя из того, что деформации металла одинаковы на различных участках по ширине роликов, а процесс накатывания протекает без буксования [24].
Для поперечно-винтового накатывания крупных резьб в ЦНИИТМАШ создан специальный стан, кинематическая схема которого показана на фиг. 58. Ролики приводятся во вращение от трехскоростного асинхронного электродвигателя через комбиниро
ванный редуктор и универсальные шпиндели.
Подача заготовок к роликам и сброс накатанных винтов осуще ствляются механизмами загрузки и выгрузки.
На этом стане могут накатываться различные резьбы диаметром от 15 до 100 мм, длиной до 1200 мм, с шагом до 8 мм. Наибольшая ширина накатных роликов 100 мм; диаметр роликов 160 -г- 230 мм. Скорость вращения накатных роликов 8 -н 30 мм/мин. Наибольшее давление при накатывании 25 т. Основной составляющей режима накатывания, определяющей качество и точность резьбы, а также стойкость роликов и производительность, является скорость накаты вания.
Превышение оптимальной скорости для данных условий накаты вания (профиль и величина шага резьбы, механические свойства металла) приводит к снижению стойкости накатных роликов и про водок, к сильному нагреву металла заготовки и налипанию его на инструмент.
Оптимальные скорости холодного накатывания крупных трапе цеидальных резьб на деталях из углеродистой стали находятся в пределах 10 н- 15 м/мин. Накатывание производится при обильной подаче в зону деформации металла сульфсфрезола, обладающего хорошей охлаждающей и смазывающей способностью, что способ ствует повышению качества резьбы и снижению усилий накатывания. Точность накатанной резьбы соответствует 2-му классу, чистота поверхности 7-н8-му классам. Отличительной особенностью резьбы,
накатанной в холодном |
состоянии, является |
сильно уплотненная |
и ориентированная по |
профилю волокнистая |
структура металла |
8* |
115 |
а>
(фиг. 59, б), твердость которого на значительной глубине от поверх ности повышается на 30 -н 40% по сравнению с исходной. Так, твер дость рабочей поверхности винтов с резьбой ТРАП 36 X 6 (фиг. 59, а) из стали 35 после холодного накатывания повысилась на 42 -н 46%, а их прочность при статических нагрузках — на 25 -н 50% по срав
нению с винтами с нарезанной резьбой.
Непрерывность процесса поперечно-винтового накатывания резьбы при установившемся режиме позволяет свести почти к нулю вспомогательное вре'мя, что делает этот метод обработки весьма про изводительным (по расчетам ЦНИИТМАШ, накатывание в Юн-30 раз производительнее скоростной токарной обработки и вихревого фрезерования).
Так, резьба винта домкрата автомобиля «Москвич» (диаметр 22 мм,
шаг 6 мм, длина резьбы 515 мм) накатывается за 25 сек. Экономия металла по сравнению с нарезкой — более 20% [25 ].
Способ поперечно-винтового накатывания крупных резьб весьма перспективен и как метод предварительной обработки точных и трудоемких деталей —■ ходовых винтов, червяков и т. п.
Однако технологические возможности накатывания в холодном состоянии ограничены максимально допустимой деформацией металла,
определяемой его механическими свойствами. Превышение допусти
мой деформации металла внешне проявляется как разрушение его поверхностных слоев, шелушение и отслаивание.
На основании данных исследований [24], в настоящее время методом холодного накатывания можно получать качественную тра
пецеидальную резьбу с шагом до 8 мм. Попытки накатывания более крупной резьбы приводили к образованию поверхностных дефектов и возрастанию величины давления на ролики. Крупные трапецеи дальные резьбы с шагом выше 8 мм, а также резьбы с меньшим шагом на деталях из малопластичных сталей можно накатывать
в горячем состоянии.
Особенно трудно поддаются накатыванию резьбы шлицы и рифли, требующие наличия на вершине профиля накатного инструмента плоской площадки, в результате чего резко уменьшается удельное давление накатывания; практикуемое в этих случаях округление вершины рабочего профиля инструмента (соответственно и впадин накатываемого профиля) дает хорошие результаты и расширяет возможности применения этого процесса. Примером 1 может служить накатывание трехзаходной трапецеидальной резьбы со скругленной впадиной на стальном шпинделе управления муфтой (фиг. 59, в).
Такая резьба диаметром 20 мм накатывается за 30 сек., а расположен
ные слева рифления — за 4 сек.
На полых деталях типа тонкостенного винтового колеса (фиг. 59, г)
во избежание деформации заготовки накатывание производится
при закреплении ее на оправке.
Другим способом, расширяющим технологические возможности на катывания и позволяющим значительно повысить производительность
'Seymour D. Н. Lomas F. М. Machinery (L), 93, 1958.
117
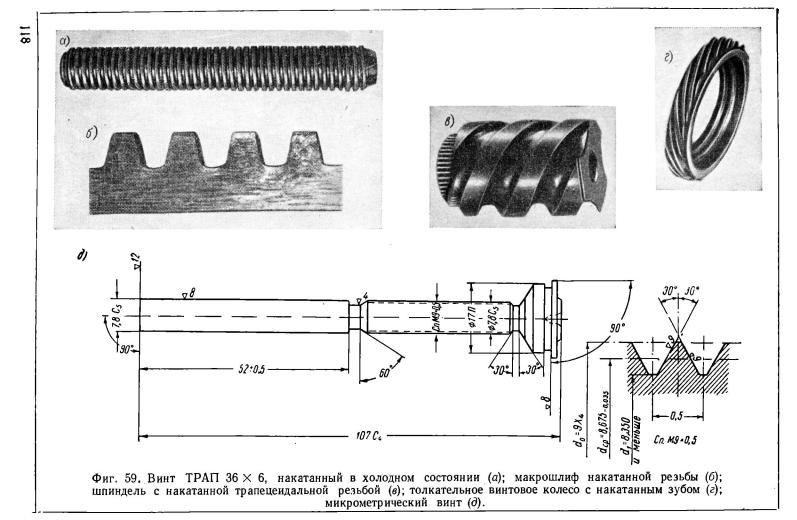
обработки резьбы роликами, является накатывание резьбы двумя роликами, вращающимися с раз личной скоростью, при тангенциальной подаче заготовок. Подача заготовок осуществляется непрерывно при постоянном меж центровом расстоянии (для данного размера резьбы) роликов.
Процесс накатывания может быть осуществлен по двум схемам:
1)ролики 1 и 3 (фиг. 51, е) разного диаметра вращаются с одина
ковой скоростью;
2)ролики 1 и 3 (фиг. 51, ж) одного диаметра вращаются с различ ной скоростью.
Вобоих случаях заготовка 2 вручную или автоматически подается
врабочее пространство между роликами, захватывается ими и, вращаясь вокруг оси, перемещается вниз или вверх. Захват и про филирование происходят в результате активного действия сил тре ния. Усилие проталкивания заготовки между роликами создается разностью окружных скоростей роликов. Расстояние между центрами роликов различного диаметра (фиг. 51, е) определяется по формуле
L = D'cp ±-Dicp + dcp - 23 мм,
где Dlcp — средний диаметр ведущего ролика; П2<,р — средний диаметр ведомого ролика;
dcp — средний диаметр накатываемой резьбы;
23 — допуск на средний диаметр резьбы по ГОСТ.
При Dj >Z)2 ролик 1, вращающийся с большей окружной ско
ростью, чем ролик 2, будет стремиться захватить и увлечь заготовку
в рабочее пространство между роликами.
Для обеспечения надежного захвата и накатывания резьбы пол- hqto профиля необходимо соблюдение определенного соотношения диаметров роликов и диаметра заготовки, при котором коэффициент трения между роликом и заготовкой f был бы больше угла захвата заготовки роликом а.
Эти соотношения принимаются равными [26]
-^^0,8 -ч-0,92;
Щср
Diep ~ ' dcP’ d^2cp = ^2 ’ dcp,
где kx и k2 — коэффициенты пропорциональности, определяющие равенство углов подъема винтовых линий роликов и накатываемой
резьбы.
Допустимое соотношение ~^1ср определяется из условий захвата
&ср
заготовки роликами в зависимости от коэффициента трения f и необ
ходимого для полного профилирования резьбы числа оборотов заго товки.
119
При f =0,1 (коэффициент трения при захвате заготовки изме няется в пределах от 0,05 до 0,15) имеет место отношение
-21£ ^32.
“ср
Максимальный диаметр заготовки, захватываемой роликом мак
симального диаметра на существующих резьбонакатных станках, определяется по формуле
.4 |
_ Diep «пят _ |
170 —. гг ос |
и3аг max |
32 |
32 |
что соответствует диаметру резьбы Мб X 1.
Максимальный диаметр ролика соответствует максимальному диаметру накатываемой резьбы Ml X 0,25, т. е.
Dlcomin = 32-0,838^ 27 мм.
С учетом минимального числа оборотов заготовки, необходимого для образования полного профиля резьбы (nmin = 3 оборота), мини мальный диаметр ролика принимается
&1ср min 45 ММ.
Таким образом, используя существующие резьбонакатные станки, можно описанным способом накатывать роликами разного диаметра
(DlCp = 45 -г- 170 |
мм) резьбы в пределах от Ml |
до Мб |
с шагом |
||||||
s < 1 |
мм. |
Производительность А |
получается |
весьма |
высокой; |
||||
она зависит |
от числа оборотов п роликов и разности числа заходов |
||||||||
роликов (&! |
— k2) |
А = n(k± — k2) |
шт/мин. |
|
|
||||
|
|
|
|
|
|
||||
Практически |
на |
заводах |
[27] |
внедрено накатывание резьб: |
|||||
М3 |
X 0,5 при ky |
= 56; |
k2 |
— 48; п = 60 об/мин.; А — 480 шт/мин..; |
|||||
М4 |
X 0,7 при |
|
= 44; |
k2 |
= 37; п |
= 60 об/мин.; А =360 шт/мин. |
|||
Резьба, |
накатанная роликами разного диаметра, по всем пара |
метрам соответствует 2-му классу точности; чистота поверхности профиля несколько ниже, чем при обычной схеме накатывания двумя роликами с радиальной подачей одного из них, и соответствует
6 -г- 7-му классам. Это может быть объяснено сравнительно малой про должительностью прокатывания заготовки между роликами. Осуще ствление принудительной подачи заготовок при накатывании резьбы по схеме, показанной на фиг. 51, ж, позволяет расширить возмож ности данного способа обработки резьб диаметром свыше 6 мм.
Такая схема может быть воспроизведена путем модернизации суще ствующих резьбонакатных станков. В этом случае толкатель 4 с пло
ской или вращающейся опорой должен делать 60 -ъ- 80 ходов
в минуту, проталкивая заготовку 2 в рабочее пространство между роликами 1 и 3, вращающимися с различной скоростью. В настоящее
время уже производятся станки, у которых ролики одного диаметра вращаются с различной скоростью. В частности, такой станок для накатывания резьб диаметром до 19,05 мм и длиной до 50,8 мм выпу скается английской фирмой Cheffield.
120