
книги из ГПНТБ / Шнейдер, Юрий Григорьевич. Холодная бесштамповая обработка точных деталей давлением
.pdfскоростей роликов вертикальная составляющая усилия обкатывания прижимает заготовку к опорному ножу, в результате чего пласти ческое деформирование металла сочетается с истирающим действием ножа. По такому принципу производится обработка цапф малого диаметра (фиг. 113, б) с помощью специального обкаточного приспо
собления, показанного на фиг. 114 |
[471. |
|
|
|
|
|
От электродвигателя через шкив 1 вращение передается на ось 9 |
||||||
с винтовой нарезкой (г = 17) на |
эавой части |
и с винтовым коле- |
||||
сом 4 (г = 30) — на левой. Далее, |
ерез винтовые колеса 5 (z = 17) |
|||||
|
и 8 (г = 30) |
получают враще |
||||
|
ние оси 13 и 3 с закрепленными |
|||||
|
на них роликами 14. |
|
|
|||
|
Ось правого ролика смонти |
|||||
|
рована в подвижной раме 6, |
|||||
|
перемещаемой винтом 12 в ра |
|||||
|
диальном |
направлении |
при |
|||
|
установке |
ролика на |
размер |
|||
|
обработанной заготовки. |
|
||||
|
На рамке |
6 закреплен упор |
||||
|
10, в который упирается нако |
|||||
|
нечник мерительного |
стержня |
||||
|
индикатора |
|
7, |
фиксирующего |
||
|
положение |
регулируемого |
ро |
|||
|
лика после установки его на |
|||||
|
размер. |
|
|
давление |
пра |
|
|
Равномерное |
|||||
|
вого ролика на заготовку осуще |
|||||
Фиг. 114. Приспособление для калибро |
ствляется |
тарированной |
спи |
|||
ральной пружиной 11. |
|
|
||||
вания цапф малого диаметра. |
Заготовка |
3 |
(фиг. |
ИЗ, а) |
||
|
устанавливается на оснащенный
твердым сплавом нож 1 между роликами 2. Зубчатая часть заготовки триба размещается в выемке опорного ножа. Соответствующие выемки
сделаны и в роликах, что позволяет производить калибрование
одновременно обеих цапф.
Производительность описанного способа обработки — 10 дета лей в минуту; точность — 3-й класс, чистота обработки — 10-й
класс.
Представляют интерес результаты проведенного за рубежом [59] сравнительного исследования процесса калибрования обкатыванием между гладкими цилиндрическими роликами и между роликами
с уступом, расположенным по винтовой линии (фиг. 115, а). Схема обкатывания дана на фиг. 99, а.
Особенностью процесса обкатывания во втором случае является наличие продольного смещения поверхностных слоев металла, что позволяет при одинаковых усилиях обкатывания достигать больших обжатий и уменьшения размеров калибруемых заготовок, чем при обработке гладкими цилиндрическими роликами. При этом несколько позднее наступает и явление отслаивания металла. Исследования
192
показали, что максимальная деформация при обкатывании и соот ветственно изменение формы и размеров заготовки имеют место под поверхностным слоем не только в зоне упругой, но и в зоне пласти ческой деформации, о чем свидетельствует деформация торцовых поверхностей, показанная на фиг. 115, б. Поскольку при этом плот ность металла остается неизменной, изменяется размер заготовки.
Полученные экспериментальным путем зависимости изменения размеров и формы обкатываемых между роликами заготовок от раз личных факторов показаны на графиках фиг. 115, в, г, д [59].
Анализ приведенных на графиках зависимостей и других резуль
татов исследований позволяет сделать следующие выводы:
1) при обкатывании роликами с уступом (фиг. 115, а) величина продольного смещения металла зависит от диаметра заготовки
иугла наклона винтовой линии кромки уступа;
2)скорость продольного смещения (в пределах 0,2 -ч- 10 мм/об) не оказывает влияния на микрогеометрию поверхности, а к умень
шению диаметрального размера приводит лишь при обработке
деталей малого диаметра из мягких легкообрабатываемых металлов;
3) |
окружная |
скорость обкатывания должна быть в пределах |
1,8 -ч- |
12 м/мин |
при калибровании изделий малого диаметра |
(1,5 -н 5 мм).
4)высота уступа влияет на уменьшение диаметра и для обкаты
вания заготовок диаметром 1,5 -ч- 5 мм не должна превышать ~ 16 мк;
5)допустимое удельное давление (усилие обкатывания на 1 мм
ширины ролика) зависит от диаметра заготовки и может достигать 70 кг/мм при калибровании заготовок диаметром 5 мм, а с умень
шением диаметра должно соответственно уменьшаться;
6)микрогеометрия роликов заметно влияет на микрогеометрию обрабатываемых деталей; при Нср ролика, равном 1,5 мк (обкатыва
лись заготовки из стали 15 диаметром 3 |
мм при |
Нср = 3 -н 4 мк) |
|
НСр |
изделия равно 0,3 мк, а при Нср |
ролика, |
равном 0,15 мк, |
Нср |
изделия равно 0,15 мк; во избежание необходимости применения |
больших усилий обкатывания, вызывающих отслаивание металла,
Н£р заготовки не должно превышать 10 мк;
7)при обкатывании заготовок малого диаметра точность формы
иразмеров повышается; так, при обкатывании стальных заготовок из стали 60 (ag = 102 кг!мм2; 8=9%) диаметром 3 мм их размеры находились в пределах 3,005 -ч- 3,025 мм, после обкатывания в тече
ние 1,5 сек. размеры у 38 деталей оказались в пределах 2,989 -ч- -ч— 2,994 мм, а конусность на длине 7 мм уменьшилась с 13 до 2 мк;
8) твердость и временное сопротивление не могут служить кри терием обрабатываемости при калибровании обкатыванием между роликами; таким критерием в известной мере может служить удли нение материала при испытании на растяжение.
Основным достоинством метода калибрования обкатыванием между роликами является сочетание высоких технических и эконо мических показателей. Как уже указывалось, процесс обкатывания обычно длится не свыше 3 -ч- 5 сек. Результаты исследования [48]
сравнительной стоимости чистовой обработки поверхностей тонким
13 Ю. Г. Шнейдер 648 |
193 |
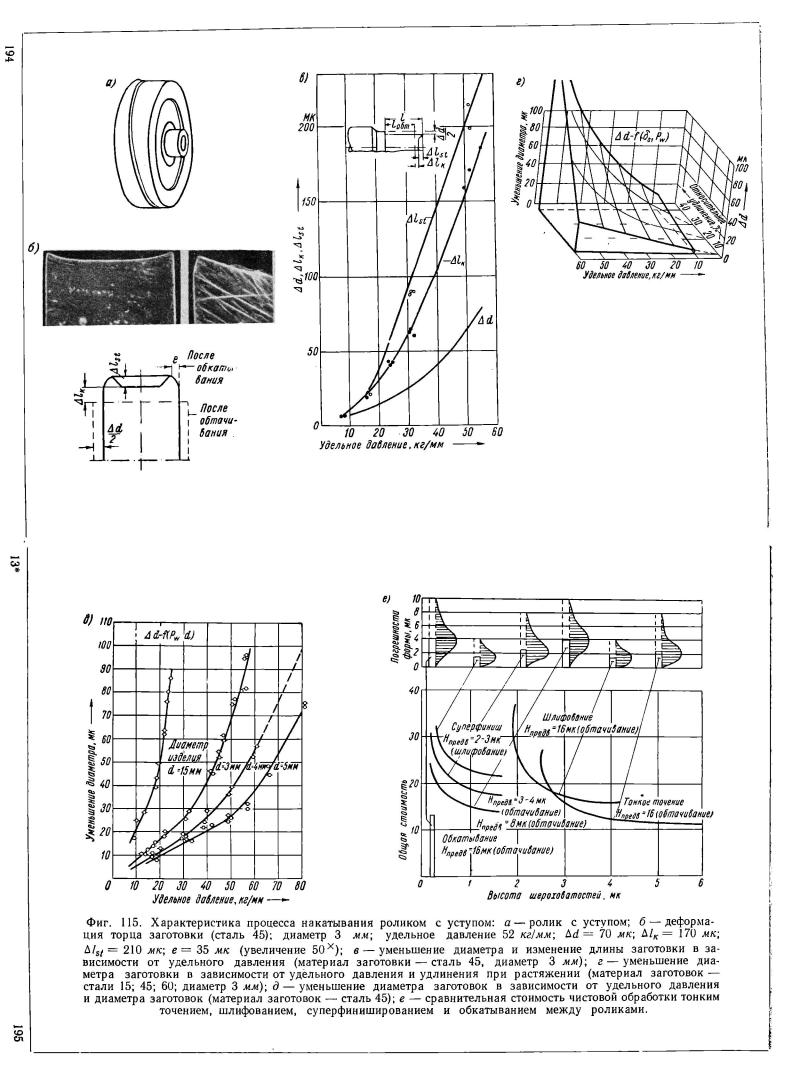
точением, шлифованием, суперфинишированием и обкатыванием между гладкими роликами, иллюстрируемые графиком на фиг. 115, е,
свидетельствуют о высокой экономичности процесса обкатывания.
Анализ графика позволяет сделать следующие выводы: |
мк) |
|
а) |
предварительно проточенные поверхности (Нпредв = 16 |
|
после тонкого точения имеют высоту шероховатостей 2,5 -4- 6 |
мк, |
|
после |
шлифования кругом зернистостью 60 — высоту 2 н- 4 |
мк, |
а после прокатывания между роликами — 0,2 -4- 0,3 мк; лишь супер финишированием (Ипредв = 2-4-3 мк) можно достичь такой же
чистоты поверхности, какая получается при обкатывании, но при этом стоимость общей обработки (предварительной и окончатель
ной) получается в 2-4-3 раза более высокой, чем при обкаты
вании;'
б) |
относительно |
грубые поверхности (Нср = 8-4-15 мк) эконо |
мически наиболее |
целесообразно обрабатывать точением; средние |
|
(Нср |
= Зн-4 мк) |
— шлифованием; особо чистые (Нср = 0,2 -4- |
4- 0,3 мк) — обкатыванием между роликами; в) наименьшие погрешности формы обрабатываемой поверхности
достигаются при шлифовании и при суперфинишировании предва рительно шлифованных заготовок (Нпредв = 2-4-3 мк);
г) наиболее экономичным способом чистовой обработки является
прокатывание между роликами, стоимость которого практически не зависит от исходной чистоты поверхности.
Столь высокие технико-экономические показатели позволяют считать способ калибрования обкатыванием между роликами весьма
перспективным и заслуживающим широкого внедрения на заводах различных отраслей промышленности.
16. Прошивание и протягивание отверстий выглаживающими прошивками и протяжками
Обработка точных отверстий продолжает оставаться сложной и трудоемкой операцией в производстве деталей машин и приборов. Особые трудности возникают при выполнении отверстий среднего
и малого диаметра, что обусловлено высокими требованиями, предъ
являемыми к точности и чистоте их поверхностей.
Поскольку отношение высоты микронеровностей к величине поля
2/Zrn |
резко |
возрастает с |
уменьшением диаметра |
о |
допуска —g-t- |
деталей, |
влияние микрогеометрии на прочность посадки в области малых размеров становится решающим. Это и определяет высокие требо
вания, предъявляемые к чистоте обработки сопрягаемых деталей. Эти требования в отношении отверстий 2-го и 1-го классов точности характеризуются 8—9-м, а в некоторых случаях и 10-м классом чистоты.
Сказанное не всегда учитывается конструкторами и техноло гами-приборостроителями; занижение требований к чистоте отделки
(особенно отверстий) приводит к ухудшению качества посадок
в сопряжениях и приборов в целом.
196
Обоснованность высоких требований к чистоте обработки сопря гаемых деталей посадок малого диаметра наглядно доказывается графиком, приведенным на фиг. 116.
Кривые графика выражают зависимость величины К = -2^ср 100%
от размера сопряжения ^^-^для различных классов чистоты
поверхности. Для каждого класса приняты средние значения Нср.
Величина К, выраженная в процентах от величины поля допуска,
в значительной степени характеризует прочность посадки.
Анализ |
графика |
показы |
|
|
|
|
|
||||||
вает |
следующее: |
К, |
соответ |
|
|
|
|
|
|||||
а) |
значения |
|
|
|
|
|
|||||||
ствующие |
7 ч- 8-му |
классам |
|
|
|
|
|
||||||
чистоты поверхности, |
весьма |
|
|
|
|
|
|||||||
велики и |
доходят |
до |
40 н- |
|
|
|
|
|
|||||
-г- 50%; |
|
|
|
|
|
|
|
|
|
|
|
||
б) значения К резко воз |
|
|
|
|
|
||||||||
растают с уменьшением диа |
|
|
|
|
|
||||||||
метра сопряжения; |
|
|
|
|
|
|
|
|
|||||
в) улучшение чистоты по |
|
|
|
|
|
||||||||
верхности |
деталей |
соедине |
|
|
|
|
|
||||||
ний |
малого |
диаметра |
до |
|
|
|
|
|
|||||
9 -4- 10-го |
классов |
приводит |
|
|
|
|
|
||||||
к резкому снижению значе |
|
|
|
|
|
||||||||
ния |
К, |
а |
следовательно, |
Фиг. |
116. Зависимость |
величины |
—g— |
||||||
к улучшению |
качества поса |
||||||||||||
от номинального |
размера |
сопрягаемых дета |
|||||||||||
док. |
|
|
|
|
|
|
|
||||||
|
|
|
|
|
|
|
лей |
для посадки С3: Нср — средняя |
высота |
||||
Естественно, что для поса |
|||||||||||||
шероховатостей; |
8 — поле допуска на диаметр |
||||||||||||
док 2-го класса |
точности |
за |
|
|
отверстия. |
|
счет уменьшения величины 8
отношение высоты микронеровностей к величине поля допуска еще более возрастает. Так, если при развертывании отверстия диамет ром 6 мм 3-го класса точности высота микронеровностей 8-го класса
составляет приблизительно 35% от поля допуска, то у отверстия
2-го класса точности та же величина НСр составит уже 75% от
поля допуска.
Если в первом случае первоначальный износ деталей пары при
ведет к значительному увеличению зазора, то во втором случае в результате лишь первоначального износа посадка будет иметь характер промежуточной между скользящей посадкой и посадкой движения, а в некоторых случаях полностью перейдет в посадку
движения.
Следовательно, для надежного обеспечения прочности посадок малого диаметра 3-го и 2-го классов точности требования к чистоте обработки поверхностей сопрягаемых деталей должны определяться не ниже, чем 9-ь 10-м классом по ГОСТ 2789 — 51.
Точность и чистота поверхности при обработке отверстий раз личными методами приведены в табл. 18.
197
Таблица 18
Точность и чистота поверхности при обработке отверстий различными методами
|
|
|
|
Экономически достижимые |
||
|
Метод обработки |
|
показатели |
|||
|
|
Класс |
|
Класс |
||
|
|
|
|
|
||
|
|
|
|
точности |
чистоты |
|
Сверление и рассверливание |
....................................... |
|
5-4-4 |
■ |
V3-4-V4 |
|
Зенкерование .................................................................. |
|
|
4-4-За |
|
V4-HV5 |
|
Растачивание.................................................................. |
|
|
Зч-2а |
|
V5-4-V6 |
|
Тонкое растачивание .................................................. |
’ |
|
2^-1 |
|
V6-4-V8 |
|
Развертывание........................ |
|
3-4-2 |
|
V6-4-VS |
||
Протягивание и прошивание....................................... |
|
|
3-4-2 |
|
V6-4-V8 |
|
Хонингование.................................................................. |
|
|
2-4-1 |
|
V9-4-V11 |
|
Притирка .......................................................................... |
|
|
|
— |
|
V9-4-V11 |
Доводка.......................................................................... |
|
|
|
2-4-1 |
|
V9-4-V12 |
Прошивание шариками 1............................................... |
|
|
2 |
|
V10-4-VH |
|
Протягивание и прошивание |
цельными, выглажи |
|
V9-4-V10 |
|||
вающими протяжками и прошивками2................... |
2 |
|
||||
Протягивание и прошивание регулируемыми выгла |
|
|
||||
живающими |
протяжками............................................... |
|
|
2-4-1 |
|
V9-^V10 |
Раскатывание роликовыми раскатками .................... |
2-4-1 |
|
V94-V10 |
|||
Раскатывание шариковыми раскатками.................... |
2 |
|
V9-4-V10 |
|||
Упрочнение шариками .................................................. |
|
|
|
|
V9-4-V11 |
|
1 Этот процесс иногда называет «калиброванием», а обработку отверстий одно- |
||||||
и многокольцевыми прошивками — «дорнованием», |
«лорнированием» и т. п. В целях |
|||||
упорядочения терминологии в дальнейшем методы обработки отверстий с |
использо |
|||||
ванием инструментов, работающих на сжатие, |
будем называть «прошиванием», а |
|||||
инструментов, работающих на растяжение,—«протягиванием». |
|
калибров |
||||
Еь’глаживак щие щотяжки |
и прошивки иногда называют дорнами, |
|||||
ками ит. п. |
В целях единообразия и |
упорядочения терминологии |
инструменты, |
|||
применяемые |
для обработки отверстий |
и работающие по принципу |
выглаживания |
протягиванием и прошиванием, будем называть, по аналогии с режущими протяж ками и прошивками, выглаживающими протяжками и прошивками.
Анализ сравнительных данных, приведенных в табл. 18, пока зывает, что в результате обработки отверстий растачиванием, раз вертыванием и протягиванием может быть получена чистота не выше 7—8-го класса, причем лишь при тонкой обработке резанием, с при менением тщательно заточенных и доведенных режущих инструмен тов — резцов, разверток и протяжек.
Если учесть, что совместная притирка сопряженных деталей
является несовершенным процессом, не обеспечивающим взаимо
заменяемости деталей, а доводка отверстий |
малопроизводительна, |
то станет понятно и оправдано все более |
широкое применение |
198
в точном машино- и приборостроении методов обработки точных
отверстий без снятия стружки — пластическим деформированием. Данные табл. 18, характеризующие методы бесстружечной обра ботки в отношении обеспечиваемой точности и чистоты поверхности, свидетельствуют о их преимуществах перед методами обработки
резанием.
Методы обработки отверстий давлением могут применяться с целью как калибрования, так отделки и упрочнения.
Прошивание и протягивание сквозных отверстий
Прошивание точных сквозных отверстий шариками. Прошива ние точных сквозных отверстий может производиться не только прошивками, но и шариками.
Подобранные по размеру стандартные шарики на ручных или механических прессах продавливаются сквозь отверстия, меньшие, чем шарик.
Процесс прошивания шариками мало отличается от прошивания прошивками с уплотняющими кольцами. Однако условия сохранения положения оси отверстия при прошивании шариками значительно хуже, чем при прошивании прошивками без направляющей части
и тем более с направляющей. Поэтому прошивание шариками находит применение главным образом для обработки деталей из цветных металлов: бронзы, баббита и др., с относительно небольшой длиной отверстий.
Преимуществом прошивания шариками является возможность использования дешевых и в то же время хорошо изготовленных покупных шариков.
Вместе с тем необходимость применения пуансона для протал кивания шариков, а также установка под пуансон шариков (особенно малого размера) создают неудобства в работе и требуют значительно большей затраты ручного времени.
Приводимые ниже рекомендации по выбору размеров выглаживаю щих колец и числа переходов, с учетом изменения размеров отвер стия в результате упругого последействия металла при обработке уплотняющими прошивками, могут быть использованы и при про
шивании шариками.
Основной трудностью осуществления данного процесса (особенно при обработке отверстий высокой точности) является подбор шари ков требуемого размера.
Точность формы обрабатываемого отверстия и чистота поверх ности при прошивании шариками в ряде случаев выше, чем при обработке прошивками (например, при обработке неглубоких отвер стий в мягких металлах, в деталях с достаточно толстыми и равно
мерными стенками).
Прошивание и протягивание сквозных отверстий однокольцевыми
выглаживающими прошивками и протяжками. В приборостроении
широкое применение при обработке точных сквозных и глухих отвер стий малого диаметра (до 10 мм) находит способ прошивания, осу-
199
ществляемый на прессах с помощью прошивок. Выглаживающие прошивки по длине обычно в 1,5-н 2 раза меньше протяжек, что делает их более прочными и облегчает изготовление, хотя произ водительность по сравнению с протягиванием значительно сни жается. Отсутствие на большинстве приборостроительных заводов малогабаритных протяжных станков также часто заставляет отка зываться от протягивания, более совершенного и производительного,
|
8) |
|
чем прошивание. |
||
|
|
По конструкции вы |
|||
|
|
|
глаживающие прошивки |
||
|
|
|
могут |
быть разбиты на |
|
|
|
|
четыре вида: |
|
|
|
|
|
1) |
однокольцевые |
|
|
|
|
(фиг. |
H7, a); |
|
|
|
|
2) |
комбинированные |
|
|
|
|
(фиг. |
117, б) |
— с режу- |
|
|
|
щими |
зубьями и выгла- |
|
|
|
|
живающими |
кольцами |
|
|
|
|
(в отличие от режущих |
||
|
|
|
зубьев, выглаживающие |
||
|
|
|
правильнее |
называть |
|
|
|
|
кольцами); |
|
|
|
|
|
3) |
многокольцевые |
|
Фиг. 117. |
Выглаживающие прошивки: |
а — одно- |
цельные (фиг. |
117, в); |
|
кольцевая; |
б — комбинированная, с |
режущими |
4) |
многокольцевые |
|
зубьями и выглаживающими кольцами; в — много- |
наборные (фиг. 117, а). |
||||
кольцевая цельная; г — многокольцевая наборная. |
Выглаживающие |
||||
|
|
|
кольца комбинирован-
ных и других прошивок предназначены для заглаживания шероховатостей, остающихся на поверхности отверстия после предва-
рительной обработки растачиванием, развертыванием и протягива
нием режущими протяжками, и для придания отверстию точного размера и формы.
После прошивания выглаживающими кольцами поверхность отверстия получается чистой (\7 9 -н \7 10), блестящей, со значи
тельно упроченным по сравнению с исходным поверхностным слоем.
Точность диаметрального размера отверстия может быть по
вышена на один-полтора класса.
Методы отделки отверстий давлением без снятия стружки, обес печивающие высокую точность и чистоту обработки, высокопроиз водительны. Как правило, они не требуют использования специаль ного оборудования и могут быть осуществлены на универсальных токарных, фрезерных и протяжных станках, а также на обычных прессах с ручным и механическим приводом.
Однако процесс обработки отверстий выглаживающим инстру ментом до сих пор мало исследован, что в производственных условиях часто приводит к необходимости экспериментально устанавливать припуски, конструкцию инструмента, режим обработки и т. д. Отсутствие надежных рекомендаций по выбору оптимальных условий
200
калибрования снижает эффективность методов бесстружечной
обработки отверстий и ограничивает их использование.
Ниже приводятся результаты ряда исследований, данные опыта по обработке точных отверстий давлением с применением различных инструментов и соответствующие рекомендации.
Прошивание сквозных и глухих отверстий однокольцевыми выглаживающими прошивками
Однокольцевые прошивки (фиг. 117, а) находят применение глав
ным образом для обработки точных отверстий (3 и 2-го классов) диаметром менее 10 мм, к которым предъ являются высокие требования и в отноше нии чистоты поверхности (8н-9-й классы и выше). Схема прошивания отверстия однокольцевой прошивкой показана на фиг. 118.
Такого рода прошивки особенно ши роко используются при отделке глухих отверстий, когда протягивание и другие методы обработки не могут быть приме
нимы. Преимуществами однокольцевых прошивок являются простота конструк ции и изготовления, а также большой срок службы.
Технико-экономические показатели данного процесса в значительной степени зависят от правильного выбора конструк
ции прошивок, |
припуска на обработку |
фиг. 118. Схема прошивания |
|
и режима прошивания. |
отверстия |
однокольцевой |
|
Применяемые |
для обработки точных |
прошивкой, |
отверстий малого диаметра однокольцевые прошивки выполняются либо бочкообразной формы с рабочим
профилем в виде плоской или сферической ленточки небольшой ширины с заборным и обратным конусами, либо шаровой формы, без направляющей или с направляющей частью.
Практика работы прошивками различной конструкции выявила целесообразность применения прошивок с плоской цилиндрической ленточкой, как менее трудоемких в изготовлении и обеспечивающих
точность положения оси отверстия при прошивании.
Большое влияние на усилие при прошивании и на качество обра батываемой поверхности оказывает геометрия рабочей части про шивки — угол заборного и обратного конусов а и ai и ширина ленточки b (фиг. 118). Установленные автором 1 опытно-эксперимен тальным путем значения а и ai равны соответственно 3 -н 5°
и 4-^-6°, а ширина ленточки—от 0,5 до 1,2 мм в зависимости от диаметра прошивки. Эти значения весьма близки к результатам,
1 Работа проводилась при участии инжII- II. Либензона.
201
полученным при исследовании обработки давлением отверстий диа метром 30 и 45 мм, длиной 30 мм по схеме, показанной на фиг. 119.
Экспериментальное исследование [49] показало, что при протя гивании стали 20; 30; 45 м 50Г и чугуна Сч 12-28 наиболее целесооб разно применять протяжки с конусообраз ной заборной и обратной частью профиля.
Надежным критерием наилучших условий
|
|
пластического |
деформирования |
металла |
||||||
|
|
при прошивании и протягивании является |
||||||||
|
|
величина толкающего или тягового уси |
||||||||
|
|
лия, |
резко |
возрастающая с |
увеличением |
|||||
|
|
сил |
трения |
и |
сдвигающих напряжений. |
|||||
|
|
Последние определяются качеством поверх |
||||||||
Фиг. 119. Схема протяги |
ностного слоя обрабатываемого металла. |
|||||||||
вания отверстия |
одноколь |
Из графика |
на фиг. |
120 |
[49] видно, |
|||||
цевой протяжкой . |
что оптимальные (в отношении тягового |
|||||||||
при протягивании стали |
усилия) значения угла заборного конуса а |
|||||||||
находятся в пределах от 4 до 5°, а при |
||||||||||
обработке чугуна — в пределах от |
3 |
до |
3°30'; |
для обоих металлов |
||||||
оптимальные |
значения |
а лежат |
в |
пределах |
от |
4 до |
5°. |
Эти же |
Фиг. 120. Зависимость тягового |
Фиг. 121. Зависимость чистоты |
||||||
усилия от величины угла забор |
поверхности |
отверстия от вели |
|||||
ного конуса. Обрабатываемый |
чины угла заборного конуса. |
||||||
материал: сталь 45 (кривая 1), |
Обрабатываемый |
материал — |
|||||
чугун (кривая 2). Диаметр от |
сталь |
45; |
aj = 5°; |
исходная |
|||
верстия 30 мм, длина |
30 мм. |
чистота |
поверхности |
НсР = |
|||
|
|
= 1,8 |
3,2 |
мк |
(кривая 1) |
и |
|
|
|
Нср =7-7-13 (кривая 2). |
|
||||
значения являются оптимальными |
и в отношении чистоты |
поверх |
|||||
ности обрабатываемого |
отверстия |
(фиг. |
121). |
|
|
|
При выборе ширины цилиндрической ленточки b рекомендуется пользоваться эмпирической формулой
& = ^cf + U,3,
1 о
где d — диаметр протяжки по цилиндрической ленточке в мм.
Во избежание налипания на рабочие поверхности инструмента металла заготонки, резко ухудшающего качество обработки,
202