
книги из ГПНТБ / Шнейдер, Юрий Григорьевич. Холодная бесштамповая обработка точных деталей давлением
.pdf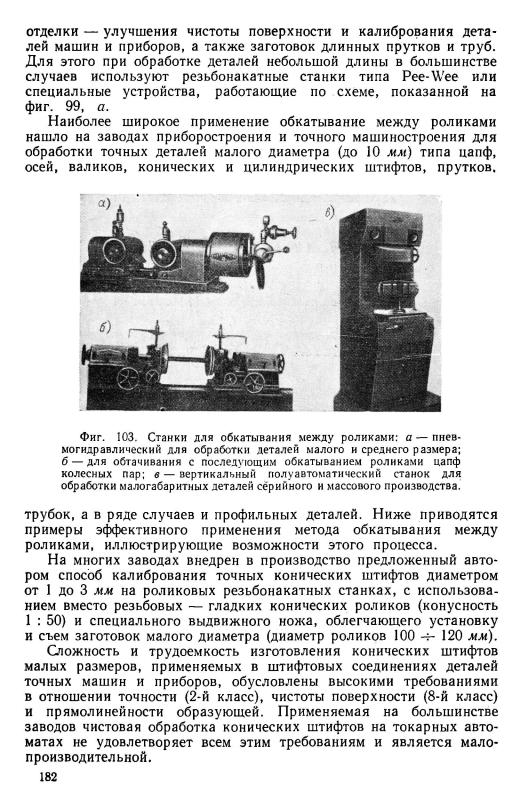
Обработка конических штифтов обкатыванием между роликами осуществляется по схеме, показанной на фиг. 104, на резьбонакат ных станках без какой-либо их переделки или модернизации. Исполь зуемое в этих случаях специальное приспособление — выдвижной нож — показано на фиг. 105 1 Опорный нож 4 и салазки 5 сделаны выдвижными. Они переме щаются от руки при помощи тяги 1 с рукояткой 2 вдоль образующей роликов по на правляющей основания 6, закрепляемого в суппорте
резьбонакатного станка. За
готовка 8 конического штиф та, обточенная предвари тельно на конус (с припу ском), укладывается на смен
ный нож 4 до упора 7, и |
|
|||
салазки 5, |
представляющие |
|
||
в сечении «ласточкин хвост», |
|
|||
вдвигаются |
между |
цилин |
|
|
дрическими |
или |
конусными |
|
|
роликами / |
и |
II, |
вращаю |
Фиг. 104. Схема калибрования конических |
щимися в одном направлении |
штифтов обкатыванием между роликами |
|||
с одинаковой окружной ско |
на резьбонакатном станке. |
|||
|
ростью.
При подходе поступательно перемещающегося ролика II вплот ную к заготовке последняя начинает обкатываться между роли ками, как при накатывании резьбы; при этом в результате пласти
Фиг. 105. Приспособление к резьбонакатному станку для калибрования конических и цилиндрических деталей малого диаметра.
ческой деформации происходит сглаживание шероховатостей, вырав нивание образующей и калибрование конуса с изменением диаме
тральных размеров в пределах 0,03 -г- 0,05 мм.
Лишь при неправильном выборе высоты (занижении) опорного ножа 4 заготовка, со значительным усилием прижимаясь к опорной поверхности ножа, может частично подвергаться истиранию. Нор мальным условиям обкатывания соответствует положение оси заго
1 Цифровые обозначения одноименных деталей на фиг. 104 и 105 одинаковы.
183
товки на 0,2 -г- 0,3 мм ниже оси роликов; исходя из этого и выби рают высоту ножа. Стабильность положения заготовок конических штифтов вдоль оси роликов, а следовательно, и постоянство их диа метральных размеров обеспечиваются установкой заготовок до упора 7 и салазок 5 с ножом — до упора 3. В некоторых случаях
положение заготовки на опорном ноже фиксируется двумя пло скими пружинами, закрепляемыми на торцах ножа.
Припуск на прокатывание конических штифтов диаметром до 3 мм
колеблется в пределах от 0,03 до 0,05 мм.
Диаметральные размеры заготовок штифтов приведены ниже.
Диаметр штифта в |
мм................................... |
1,0 |
1,5 |
2,0 |
3,0 |
Диаметр заготовок |
в мм............................... |
1,03 |
1,55 |
2,05 |
3,05 |
Заготовки под |
обкатывание протачиваются |
с |
точностью |
За класса (Сза).
Давление при обкатывании штифтов указанных в табл. 18 раз меров — 300 н-500 кг; окружная скорость роликов 8-4-10 м/мин.
Так же, как при накатывании резьбы, обработка производится
с обильной смазкой веретенным маслом.
Точность диаметральных размеров при обкатывании соответствует 3 -4- 2-му классам; отклонения по углу не превышают 3 -4- 5', а откло нения от прямолинейности образующей в несколько раз меньше, чем при обработке точением и бесцентровым шлифованием. Нагляд
ное представление о шероховатости поверхности конических штиф
тов, обработанных различными методами, дают профилограммы (фиг. 106), снятые при 1000-кратном вертикальном и 50-кратном горизонтальном увеличении.
Если при обтачивании на |
токарном автомате НСр = 6-4-8 мк |
|
(\7 6), а при бесцентровом |
шлифовании Нср |
= 4 4- 5 мк (\7 7), |
то при обкатывании Нср не |
превышает 0,5 -4- |
0,8 мк (V Ю •= П). |
В результате обкатывания микротвердость |
возрастает на 20 -4- |
30%, что позволяет в ряде случаев заменить инструментальную высокоуглеродистую сталь сталями марок 20 или 30.
Продолжительность обкатывания между роликами конических штифтов диаметром от 1 до 3 мм не превышает 3-4-5 сек. и прак тически не зависит от величины припуска (в указанных выше преде лах) и материала заготовок.
Не менее эффективно применение метода обкатывания и для калибрования, рихтования и отделки цилиндрических деталей типа
валов и осей, |
показанных на фиг. 107 [45]. |
||
|
Обкатывание между роликами предварительно проточенной заго |
||
товки оси из стали ЭИ474 (фиг. 107, а) |
при давлении 600 -4- 800 кг |
||
в |
течение 3-4-4 сек. обеспечивает достижение требуемой черте |
||
жом точности |
3-го класса, чистоты |
поверхности 10-го класса |
|
и |
повышения |
микротвердости на 20%. |
Припуск на обкатывание |
составлял 0,02 -4- 0,04 мм. Производительность обкатывания по сравнению с применявшимся до этого полированием повышается
в 15 раз.
184
Обкатывание между роликами оси высотной компенсации
(фиг. 107, б) из латуни ЛС59-1 позволило получить детали, у кото рых прямолинейность Образующих и соосность различных участков не выходили за пределы 0,015 мм при улучшении чистоты поверх ности на два-три класса. В данном случае обкатывание заменило ручную рихтовку осей, производительность которой была в 20 раз меньше.
Обтачивание НСр -7мк V6
Бесцентровое шлифование НСр = 4,2мк |
47 |
|
Холодное прокатывание |
НСр = 0,8мк |
V10 |
Холодное прокатывание |
HCD = 0,5 мк |
V11 |
Фиг. 106. Профилограммы поверхностей конических штифтов, обра ботанных точением, бесцентровым шлифованием и обкатыванием. Вер
тикальное увеличение 1000х, горизонтальное 50х.
Маложесткие оси редуктора (фиг. 107, в), изготовляемые из стали марки У8А, обкатывались между роликами с целью достижения прямолинейности (прогиб не должен превышать 0,03 мм) и полиро вались.
Обкатывание между роликами в течение 3-^-4 сек. устра няет прогиб заготовок и улучшает исходную чистоту поверхности до 9 -г- 10-го класса. Производительность обработки осей повыси лась в восемь-десять раз.
В обоих последних случаях припуск на прокатывание между
роликами не оставляется. Столь высокие технико-экономические
показатели процесса обкатывания достигаются при выполнении следующих условий:
1)радиальное биение роликов не должно выходить за пределы 0,01 мм, а торцовое — 0,02 мм;
2)непараллельность осей роликов не должна превышать 0,015 мм;
3)ролики, изготовляемые из сталей Х12Ф1 или У10А и за
каливаемые до твердости RC = 56 58, должны быть тщательно шлифованы и доведены до 10 -ь- 11-го классов.
185
Фиг. 107. Детали, калибруемые обкатыванием между роликами: а — ось,
б — ось высотной компенсации; в — оси редуктора.
186
Обработка обкатыванием точных деталей малого диаметра несколько специфична. При обработке крупногабаритных деталей этот метод применяется лишь как отделочный процесс с целью улуч шения микрогеометрии и упрочнения поверхностного слоя металла; при этом в подавляющем большинстве случаев припуск не преду сматривают, исходя из того, что в результате обкатывания изменение формы и размеров практически не выходит за пределы относительно
Число оборотов роликоб за Время обкатывания
Дабдение,кг
Фиг. 108. Зависимость уменьшения диаметра заготовки: а — от давления при обкатывании; б — от числа оборотов роликов (с момента начала касания их с заготовкой).
больших полей допусков крупногабаритных деталей. Лишь в отдель ных случаях поле допуска на предварительную обработку сужается
к верхнему пределу. При обработке же точных деталей малого диа метра искажение формы и размеров заготовки даже в пределах нескольких микрон полностью исключило бы возможность практи ческого использования прокатывания между роликами как отделоч ного процесса. Это в равной мере относится и к другим методам холодной обработки металлов давлением, точностные возможности которых так же, как и прокатывания между роликами, пока мало исследованы.
Однако опыт прокатывания точных деталей (точных конических штифтов, осей) и результаты проведенного автором исследования свидетельствуют о возможности применения этого метода обработки не только для неразмерной отделки и упрочнения поверхностей,
но одновременно и с целью получения требуемой точности. Умень шение размера прокатываемой заготовки зависит от следующих
факторов: физико-механических свойств обрабатываемого металла,
высоты, формы и шага шероховатостей исходной поверхности и тре буемой чистоты поверхности, давления на ролики, времени прока тывания и в меньшей степени—от скорости вращения роликов и подачи одного из них (при работе по схеме, показанной на фиг. 99,а).
187
Опыт отечественных и зарубежных заводов показывает, что наибо лее широкое применение получило прокатывание между роликами с целью улучшения до 8-^ 10-го классов микрогеометрии поверх ностей, предварительно обточенных с чистотой 5 -4- 6-го классов или шлифованных с чистотой 7-го класса; при этом происходит
уменьшение диаметрального размера в пределах |
0,02 ч- 0,05 мм. |
В данном случае уменьшение диаметрального |
размера обкаты |
ваемых заготовок будет определяться высотой шероховатостей исход ной поверхности и поверхности, получающейся после обкатывания.
В тех случаях, когда целью обкатывания является не только улуч
шение микрогеометрии заготовки, но и калибрование ее до требуемого
размера, |
это можно осуществить в первую очередь за счет |
регулиро |
|
вания давления. |
показана зависимость между давлением |
и умень |
|
На фиг. 108, а |
|||
шением |
диаметра |
обкатываемых заготовок из стали марки А12 |
|
и латуни |
марки ЛС62. |
|
При постоянном давлении уменьшение диаметра будет тем боль шим, чем пластичнее обрабатываемый металл, чем выше шерохо ватости исходной поверхности и чем меньше их шаг, чем меньше
окружная скорость роликов и подача одного из них и чем больше время обкатывания.
При постоянном давлении размер заготовки можно регулировать за счет времени обкатывания с момента начала касания роликов с заготовкой; для этого необходимо наличие на станке устройства, автоматически выключающего подачу ролика.
На фиг. 108, б показана зависимость уменьшения диаметра обка
тываемой заготовки (сталь 35) от числа оборотов роликов с момента начала соприкасания их с заготовкой.
Однако во всех случаях для данного материала и условий обра ботки существует предел длительности обкатывания; чрезмерно длительное прокатывание приводит к перенапряжению поверхност ных слоев металла, проявляющемуся первоначально в ухудшении чистоты поверхности, а затем — в образовании чешуйчатое™, раз мазывании металла заготовки и налипании его на ролики. Время обкатывания необходимо особо строго регламентировать в случае,
когда процесс ведется при больших окружных скоростях заготовок.
Это относится в первую очередь к обработке заготовок малого диа метра, так как в этих случаях соотношение диаметров роликов и заготовки и соответственно скоростей их вращения весьма велико.
Так, при калибровании штифтов или осей диаметром 2 мм роликами диаметром 120 мм, вращающимися с относительно малой окружной скоростью (30 об/мин.) заготовка делает 1800 об/мин. В этих усло виях превышение длительности обкатывания на 2 ч- 3 сек. над оптимальной уже может привести к разрушению поверхностных слоев металла.
Сказанное |
иллюстрируется |
микрофотографиями, приведенными |
||||
на фиг. |
109. |
обкатывании |
в |
течение |
3 ч- 4 |
сек. достигается |
Если |
при |
|||||
чистота |
поверхности 10-го |
класса (сталь |
марки |
У10А, диаметр |
188
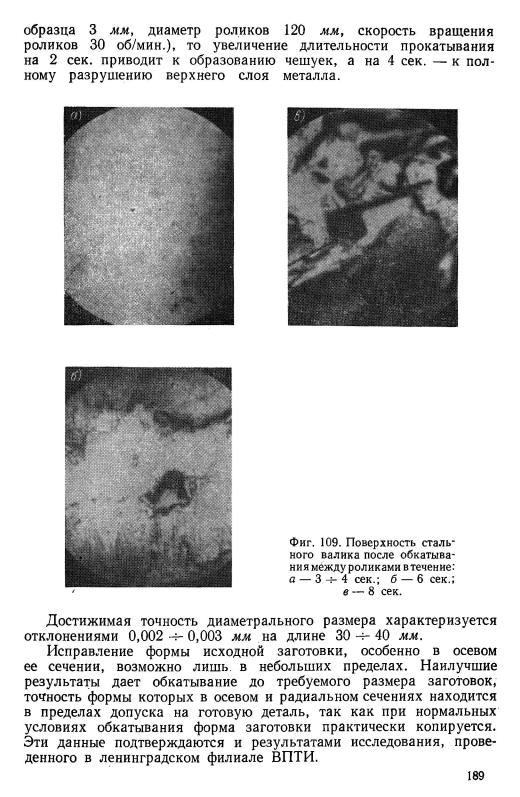
Так, прокатывание производственной детали — штока воздухо распределителя тормоза MT3-135 из жаропрочной стали марки
1Х18Н9Т (фиг. 110) производилось на резьбонакатном станке глад кими роликами диаметром 115 мм, шириной 65 мм (при такой ширине роликов рабочая часть штока диаметром 10 мм обрабатывалась
одновременно по всей длине, равной 54,5 мм). |
Исследованием было |
||
|
установлено, что погрешности фор |
||
|
мы заготовки (овальность и конус |
||
|
ность), полученные при предвари |
||
|
тельной обработке шлифованием, |
||
|
не изменялись, если |
они не пре |
|
*-38 —*4 |
вышали 3 мк. |
Подтвердился также |
|
ранее приведенный вывод о высо |
|||
-- -------------92,5 С3 |
кой стабильности метода прокаты- |
||
Фиг. ПО. Шток. |
вания между роликами даже при |
||
|
изменении |
условий |
обработки |
в значительных пределах. Так, с изменением давления от 1 до 5 т
при постоянных скорости (у = 9 м/мин.) и времени (Т = 10 сек.) обкатывания чистота поверхности во всех случаях соответствовала 11-му классу; тот же класс чистоты сохранялся и при изменении скорости обкатывания в пределах от 5 до
18 м/мин. Оптимальными условиями обка- |
' |
|
тывания |
штока оказались: давление — |
|
1,5 н-2 |
т, окружная скорость роли- |
|
а)
Фиг. 111. Тяжок сектора, шаровая поверхность которого калибруется обкатыванием между роликами (а); схема обкатывания шаровой поверхности (б).
ков — 12 м/мин., время прокатывания — 10 сек., припуск под обкатывание — 0,015 мм\ смазка — веретенное масло.
Все показатели процесса обкатывания между роликами сохра
няются и при обработке деталей более сложной формы, чем цилин дрические валы и оси. Так, на одном из заводов обкатыванием дости гается 10-й класс чистоты поверхности и 3-й класс точности шаровой поверхности стального (сталь марки У8А) тяжка сектора тахометра
(фиг. 111, а). В -данном случае по окружности роликов сделаны сфе рической формы канавки (фиг. 111, б). При обкатывании не только
190
Значительно |
повышается |
производительность |
(время |
обкатывания |
4 — 5 сек.) |
по сравнению |
с применявшейся |
до этого |
полировкой |
(3 мин.), но и сохраняется точность формы, что практически нельзя достичь при полировании.
Обкатывание между роликами по второй схеме (фиг. 99, б) осу
ществляется |
при обработке заготовок большего диаметра (свыше |
50 мм) на |
специальных станках |
или с помощью приспособлений
кметаллорежущим станкам. Примером применения такого
способа обкатывания может слу жить обработка одновременно тремя роликами цилиндрической поверхности и галтелей шейки коленчатого вала по схеме, пока занной на фиг. 112 [46].
Цилиндрическая поверхность
обрабатывается гладким цилиндри |
Фиг. 112. Схема одновременного обка |
|||
ческим |
роликом, а |
две галтели — |
тывания цилиндрической поверхности |
|
двумя |
сферическими роликами, |
и галтелей шейки коленчатого вала. |
||
расположенными с |
противополож- |
|
||
ной стороны. |
Сферические ролики производят давление на шейку под |
|||
некоторым углом к |
ее оси, что осуществляется путем их разжима |
|||
равномерно |
в обе |
стороны с помощью разжимного устройства. |
||
Такой способ |
обкатывания весьма |
производителен и совершенен. |
Фиг. 113. Схема обкатывания между роликами, вращающимися с различными окружными скоростями (а); триб с цапфами, калибруемыми обкатыванием (б).
Обработка по третьей схеме (фиг. 99, в) пока не получила широ
кого распространения и применяется лишь с целью калибрования
по размеру (в пределах 0,1 мм) и улучшения чистоты поверхности
(до 9-н10:го класса) цилиндрических прутков длиной от 100 до 3000 мм.
В некоторых случаях применяют схему обкатывания между двумя роликами, вращающимися с различной окружной скоростью
(фиг. ИЗ, а), устанавливая заготовку несколько выше линии цен тров роликов. Возникающая вследствие разности окружных
191