
книги из ГПНТБ / Шнейдер, Юрий Григорьевич. Холодная бесштамповая обработка точных деталей давлением
.pdf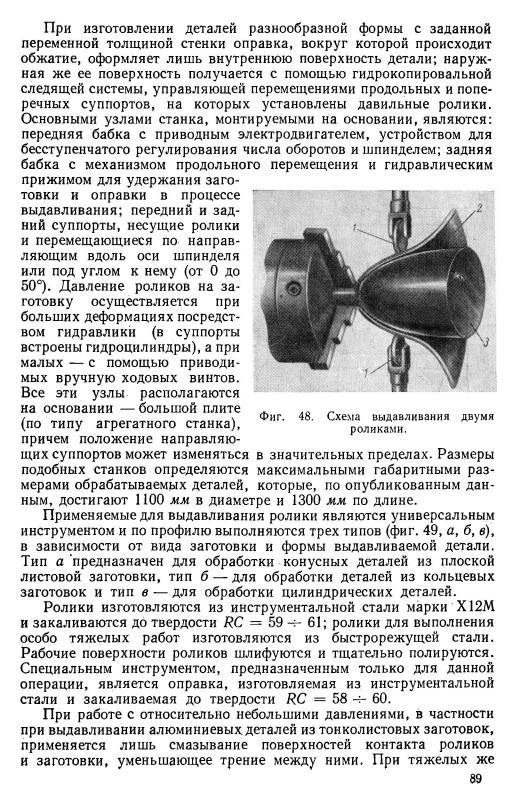
работах, связанных с большими утонениями стенок заготовки,
когда давление достигает огромных значений (до 28 000 кг/см2), нагрев заготовки и роликов столь значителен, что помимо смазки приходится применять и охлаждение.
Смазочная среда должна быть достаточно вязкой во избежание смывания ее охлаждающей жидкостью. Хорошие результаты дает смазка роликов и заготовки коллоидной цинковой суспензией или настоем дисульфата молибдена.
Заготовками при выдавливании могут служить вырезанные из листа круги или квадраты (фиг. 50, а), чашки, полученные вытяжкой (фиг. 50, б), кольца,
|
|
|
|
|
|
свальцованные |
из |
полосы |
|||||
|
|
|
|
|
|
и сваренные встык (фиг. 50, в), |
|||||||
|
|
|
|
|
|
поковки (фиг. 50, г), штампо |
|||||||
|
|
|
|
|
|
ванные детали (фиг. |
50, |
5). |
|||||
|
|
|
|
|
|
Максимальная |
толщина ли |
||||||
|
|
|
|
|
|
стовых |
заготовок из мягкой |
||||||
|
|
|
|
|
|
стали 25 мм, из нержавею |
|||||||
|
|
|
|
|
|
щей стали |
15 |
18 мм. |
|
||||
|
|
|
|
|
|
За один переход выдав |
|||||||
|
|
|
|
|
|
ливанием |
удается |
получать |
|||||
|
|
|
|
|
|
конусные |
детали |
из |
сталей |
||||
|
|
|
|
|
|
с углом не менее 30°, а из |
|||||||
|
|
|
|
|
|
алюминия—с углом не менее |
|||||||
|
|
|
|
|
|
20°. |
Уменьшение |
толщины |
|||||
|
|
|
|
|
|
стенки по сравнению с тол |
|||||||
|
|
|
|
|
|
щиной |
исходной |
заготовки |
|||||
|
|
|
|
|
|
в среднем составляет 70 -н |
|||||||
Фиг. 49. |
Давильные |
ролики, применяемые |
|
-- 75%. |
|
|
|
|
50, а) |
||||
на |
токарно-давильных станках. |
|
|
Деталь-чаша (фиг. |
|||||||||
|
|
|
|
|
|
выдавливается |
из |
заготовки |
|||||
(котельное железо) представляющей собой плоский |
круг |
тол |
|||||||||||
щиной |
6,35 |
мм. |
Обработка |
ведется |
в |
два |
перехода |
при |
ско |
||||
рости |
вращения |
шпинделя |
250 |
об/мин. |
и |
подаче |
роликов |
||||||
0,5 мм/об. |
|
турбины (фиг. 50, |
в) |
изготовляемся |
из |
кольца |
|||||||
Деталь газовой |
|||||||||||||
с внутренним |
диаметром 3 1 7,5+0-038 |
мм, |
толщиной |
стенки |
16 |
мм |
и шириной 51 мм. Выемка в кольце выполняется вторым переходом,
специальным роликом, движение которого управляется гидро-
копировальным устройством. При числе оборотов шпинделя 300 об/мин. время обработки этой детали составляет от 12 до 15 мин. Вал реактивной турбины (сплав А-286) изготовляется выдавливанием из стальной поковки, предварительно обработанной на токарном станке. Обработка давлением производится за два перехода и эконо мит 40 кг металла на каждой детали по сравнению с токарной обработ кой. Другая деталь — корпус подшипника (фиг. 50, д') — выдав ливается в два приема из заготовки в виде диска толщиной 8,7 мм,
диаметром 508 мм, средняя часть которой предварительно оформ ляется штампом.
90
б)
а)
Фиг. 50. Детали, изготовляемые выдавливанием: а — из листовых заготовок; б — из чашек, получен ных вытяжкой; в — из кольца; г — из поковки; д — из штампован
ной заготовки.
0 4 8 2
Приведенные примеры свидетельствуют об универсальности, производительности и экономичности описанного способа обработки полых деталей.
По данным исследований, точность выдавливания сравнительно высока: рассеивание размеров лежит в пределах 0,1% от номиналь ного диаметрального размера обрабатываемых деталей, что соот ветствует точности порядка 4-го класса. Толщина стенки выдержи вается с точностью 0,05 -н 0,08 мм. Чистота обработки соответствует 7 -г- 8-му классу.
Производство токарно-давильных станков в СССР несколько отстало, несмотря на то, что на многих предприятиях страны давиль ные процессы применяются довольно широко; это объясняется прежде всего недооценкой технологами этого весьма производитель
ного и прогрессивного способа формообразования сложных и трудо емких в изготовлении полых деталей. Хотя отсутствие исчерпы вающих теоретических и достаточно проверенных эксперименталь ных данных, необходимых для построения технологических про
цессов, а следовательно, и для проектирования соответствующего
оборудования, затрудняют широкое внедрение давильных работ
в производство, однако опыт отечественных предприятий свидетель
ствует о том, что и в этих условиях возможно весьма эффективное
применение давильных работ в самых различных отраслях промыш
ленности. Так, на давильно-обкатном станке ЦНИИТМАШ произ водительно изготовляются котельные днища диаметром до 5,5 м. Сферическая часть днища получается из листа выдавливанием пуансоном, перемещающимся с помощью гидроцилиндра, а закатка краев днища — обкаткой роликами с механическим приводом. На Московском заводе малолитражных автомобилей успешно рабо тает машина для выдавливания обкаткой роликами заготовок авто мобильных деталей — валов и др. На станке ЛТ-5 Лубненского станкостроительного завода из алюминиевого листа производится
выдавливание цилиндрического стакана диаметром 100 мм и дли ной 180 мм, с последующим раскатыванием горловины до диаметра 26 мм. Средняя скорость выдавливания 800 м/мин.
В Ленинграде разработан новый совершенный токарно-давильный
станок 3P53 (фиг. 46, в) [19], предназначенный для изготовления пустотелых изделий типа обтекателей, сопел, колпаков, рефлекторов, сепараторных тарелок и других деталей, изготовляемых из алюми ниевых, медных и стальных листов и труб.
На станке могут быть обработаны изделия длиной от 20 до 600 мм, диаметром от 20 до 400 мм.
Выдавливание может производиться как вручную на оправке, так и с гидроприжимом и по копиру. Станок может быть использован
и для |
осуществления обычных |
токарно-копировальных работ. |
Основные технические характеристики токарно-давильного станка |
||
3P53 |
следующие: |
|
Высота центров в мм................................... |
225 |
|
Расстояние между центрами в мм................ |
750 |
92
Наибольший диаметр |
листовой |
заготовки |
|
|||
в мм.......................................................... |
|
|
|
|
|
550 |
Наибольший диаметр изделия (типа ста |
|
|||||
кана), проходящего над нижней частью |
|
|||||
суппорта в мм........................................... |
|
|
|
|
|
220 |
Наибольший диаметр изделия, выдавливае |
|
|||||
мого ручным давильником |
в мм .... |
|
|
420 |
||
Наибольший диаметр |
заготовки |
из |
трубы |
|
||
в мм.......................................................... |
|
|
|
|
|
200 |
Наибольший диаметр |
изделия |
из |
трубы |
|
||
в мм...................................................................... |
|
|
|
|
|
30 |
Наибольшая длина изделия из трубы в |
мм |
600 |
||||
Диапазон чисел оборотов шпинделя |
в |
ми |
|
|||
нуту .................................................................. |
|
|
|
|
|
3504-2800 |
Мощность электродвигателя |
в |
кет .... |
|
2,74-5,54-6; трехскорост |
||
|
|
|
|
|
|
ной |
Гидравлический привод перемещения продольного и поперечного |
||||||
суппортов в сочетании с электрогидравлическим способом управле |
||||||
ния обеспечивает постоянство |
суммарной |
скорости копирования |
||||
и диапазон углов копирования от 0 до 90°, независимо от профиля |
||||||
изготовляемых изделий. Возможность наладки станка на полуавто |
||||||
матический цикл работы исключает физически тяжелый труд рабо |
||||||
чего-давильщика. |
|
|
|
|
|
|
С 1956 г. на Тбилисском станкостроительном заводе производятся |
||||||
токарно-давильные станки с высотой центров 500 мм. |
||||||
10. Накатывание резьбы роликами, плашками, резьбовым |
||||||
полукольцом и роликом, резьбонакатными головками |
||||||
Из всех формообразующих процессов холодной бесштамповой |
||||||
обработки металлов давлением способ накатывания резьбы получил |
||||||
наибольшее распространение, особенно в последние годы. На неко |
||||||
торых отечественных предприятиях в настоящее время до 70 4- 80% |
||||||
резьбовых деталей обрабатывается накатыванием. Низкая стоимость |
||||||
изготовления в сочетании с высокой механической и усталостной |
||||||
прочностью накатанной резьбы выгодно отличают процесс накаты |
||||||
вания от всех известных в настоящее время методов обработки |
||||||
резьбы. Производительность метода накатывания резьбы плоскими |
||||||
плашками выше производительности нарезания резьбовыми голов |
||||||
ками в 9 раз, нарезания лерками — в 16 раз и фрезерования резьбы — |
||||||
в 30 раз. Процесс формообразования резьбы при накатывании проис |
||||||
ходит без снятия стружки и сопровождается большими радиальными |
||||||
усилиями, под действием которых пластически деформированный |
||||||
поверхностный слой с волокнами, |
облегающими контур накаты |
|||||
ваемой резьбы, уплотняется |
и |
приобретает |
повышенную механиче |
скую прочность и твердость.
Исследования [21 ] в этой области показывают, что поверхностная микротвердость накатанной резьбы возрастает в два раза, значительно увеличивается предел прочности при растяжении и на срез и на 25% повышается усталостная прочность.
93
Фиг. 51. Схемы обработки резьбы накатыванием: а — плоскими плашками; б — двумя |
роликами с винтовой нарезкой; в — двумя роликами с кольцевой нарезкой; г — двумя |
|||
е — двумя роликами |
различного диаметра; ж ■— двумя роликами, вращающимися |
|||
роликами (поперечно-винтовое накатывание); д — роликом и резьбовым |
сегментом; |
|||
ми; к—раскатывание |
короткой резьбы; л—раскатывание резьбы на большой длине. |
|||
с различной скоростью; з—головкой с тремя роликами; и—головкой с двумя ролика- |
------------ >- свободное движение. |
|||
----------- > — принудительное |
движение, |
|||
|
|
'94 |
95 |
|
Одним из достоинств метода накатывания резьбы является также более высокая чистота боковых поверхностей витка резьбы, чем при фрезеровании, шлифовании и даже доводке.
Проведенные автором сравнительные исследования чистоты поверхности резьбы стальных деталей при различных способах
обработки дали следующие результаты:
при нарезании леркой .... |
Нср= 18 -г-8 мк (V5-^V6) |
|
при нарезании дисковым резцом |
tfcp = 7-?-4 мк (V6-^-V7) |
|
при |
шлифовании........................ |
Нср = 4 -4- 2 мк (V7-^-V8) |
при |
накатывании ....................... |
Нср = 1,0-т-„0,4 мк (V9-r-VH) |
Если учесть, что при накатывании резьбы достигается также точность 2 -г- l-ro классов, то этот метод можно отнести к наиболее совершенным из. современных технологических процессов, сочетаю щим функции черновой, чистовой и отделочной обработки. Именно
эти особенности и достоинства определили столь широкое применение во всех отраслях промышленности и продолжающееся в настоящее время развитие способа изготовления резьбы пластическим дефор мированием.
Процесс накатывания резьбы сравнительно хорошо исследован и широко освещен в технической литературе, поэтому здесь кратко
рассматриваются лишь новые схемы накатывания, оборудование и инструмент, пока еще не получившие широкого применения в про мышленности, а также приводятся данные, характеризующие область рентабельного применения различных способов получения резьбы пластическим деформированием.
На фиг. 51 приведены основные принципиальные схемы обработки резьбы накатыванием.
Первый способ — накатывание резьбы плоскими плашками (фиг. 51, а) — получил наиболее широкое приме
нение при крупносерийном и массовом производстве резьбовых
деталей 3 и 2-го классов точности на деталях из конструкционных сталей и цветных металлов. До последнего времени нижний предел диаметров заготовок (2), накатываемых плашками (/, <5), ограничи
вался 3 мм, в силу чего большое число деталей (в первую очередь крепежных) с резьбой диаметром менее 3 мм обрабатывалось лер ками — малосовершенным дорогостоящим инструментом.
Кроме того, широкое применение способа накатывания резьбы плоскими плашками ограничивалось сложностью их изготовления, особенно для обработки резьб малого диаметра.
В настоящее время задачи использования этого метода в условиях серийного и мелкосерийного производства для накатывания резьб диаметром менее 3 мм и усовершенствования производства плашек
успешно решаются. На ленинградских заводах спроектирована и успешно эксплуатируется серия высокопроизводительных авто матов для накатывания резьб малого диаметра. Каждый из автоматов серии предназначен для обработки резьбы определенного диаметра,
что позволило упростить его конструкцию, повысить надежность
96
в эксплуатации и сделало экономически целесообразным исполь* зование его при обработке деталей малых партий (начиная от 50 -н 100 шт.) с размером резьбы М.2,7; М3; М4; М5.
Тщательное выполнение деталей станка, их сборка и регулировка
(особенно направляющих подвижной плашки), а также изготовление плашек повышенной точности обеспечили накатывание резьбы 2-го класса точности с чистотой поверхности 8 -н 9-го класса. Резьба плашек в этом случае обрабатывается фрезерованием многониточной
фрезой и доводится притиром после термической обработки. Как
Фиг. 52. Кинематическая схема автомата для накатывания резьб малого диаметра.
видно из кинематической схемы резьбонакатного автомата (фиг. 52),
основными его узлами являются: кулисный механизм, осуществляю
щий возвратно-поступательное перемещение ползуна с подвижной плашкой; питающее устройство с бункером; механизм, подающий заготовки к плашкам; устройство для сбрасывания деталей с накатан ной резьбой.
Привод главного движения осуществляется от электродвигателя через ременную передачу Г, 2\ 3 на шестерню 4, кулисную шестерню 5
скамнем 6 и кулису 7. К верхней части кулисы шарнирно прикреп лен шток 34, соединенный с ползуном 33, перемещающимся по направ
ляющим 12 станка.
Впередней части ползуна вертикально установлена подвижная плашка 22, закрепленная двумя прихватами 23\ вторая, неподвижная плашка 21 закреплена двумя винтами 20.
Питающий механизм работает от шкива 8, сидящего на одной оси
скулисной шестерней; с помощью ремня вращение передается со шкива 8 на шкив 9, на оси которого закреплен кулак 10, качающий
7 Го. Г. Шнейдер |
648 |
97 |
в вертикальной плоскости толкатель 11. Последний шарнирно соеди нен с питателем 35, перемещающимся вверх и вниз по направляю щему пазу бункера 38.
Питатель представляет собой две тонкие стальные склепанные пластины, расстояние между которыми определяется диаметром заготовок под накатывание. При опускании питателя заготовки 37
падают из бункера в пространство между пластинами, а при подъеме питателя — скатываются по наклонному лотку 36 к подаю щему механизму. Подающий механизм срабатывает от ползуна 33; на боковой стороне последнего сделан выступ 32 с криволинейной
поверхностью, к которой постоянно плоской пружиной 17 поджи мается ролик 16.
Подача заготовок в плашки осуществляется следующим образом: во время рабочего хода ползуна с подвижной плашкой вперед выступ 32, перемещаясь вместе с ползуном, надавливает на ролик 16
и отводит назад шток 13, в котором закреплен ролик. На другом конце штока закреплен второй ролик 14, поворачивающий при отходе штока назад кулачок 15. На одной оси с кулачком 15 сидит собачка 19, входящая в выем толкателя 18, поджимаемого плоской пружиной 17.
Таким образом, если в начале движения ползуна выступ 32,
надавив на шток 13, откинет собачку 19 назад и отведет толкатель 18 от плашек, то при дальнейшем движении ползуна вперед, когда подвижная плашка подойдет к неподвижной, ролик 16, сойдя с выступа 32, позволит толкателю под действием пружины 17 пе реместиться вперед и втолкнуть очередную заготовку между плаш ками.
Сбрасывающее устройство также срабатывает при движении ползуна, на котором закреплена колодка 24 со штоком 30; в последнем вертикально установлен штифт 28.
На столе станка закреплена стойка 26, в которой консольно закреплен поводок 29 с пальцем 25 и сбрасывателем 31.
При ходе ползуна вперед штифт 28 |
наталкивается на палец 25 |
и поворачивает его вместе с поводком |
и сбрасывателем вокруг оси |
(по часовой стрелке). При этом сбрасыватель, выполненный в виде тонкого стержня, следует за накатываемой заготовкой и в момент
окончания накатывания сбрасывает готовый винт с неподвижной плашки в ящик.
Висходное положение поводок со сбрасывателем возвращаются
спиральной пружиной 27 при отходе ползуна назад.
Точность резьбы, накатываемой на автомате, по всем параметрам соответствует 2-му классу; чистота поверхности —8-н9-му классам. Производительность автомата 3600 деталей в час.
Внастоящее время применяются резьбонакатные автоматы с пита
телем барабанно-лопастного типа, испытание которых в работе
дало хорошие результаты.
Подобные автоматы обеспечивают производительное и качествен ное изготовление деталей с резьбой диаметром от 2 мм и выше, 2-го класса точности.
98
Накатывание резьбы диаметром менее 2 мм осуществляется
плашками, резьба на которых также накатана резьбовым перевод ником 122].
Накатывание резьбы на переводниках по схеме, показанной на фиг. 53, а, осуществляется на специально приспособленном для
этого поперечно-строгальном станке, на котором обрабатываются |
|||
и резьбовые детали. В этом |
а) |
||
случае к станку предъявля |
|||
|
|||
ются повышенные требования |
|
||
в отношении плавности хода |
|
||
ползуна, отсутствия ударов |
|
||
и остановок |
при изменении |
|
|
направления |
движения пол |
|
|
зуна, отсутствия люфтов в на |
|
||
правляющих, |
жесткости за |
|
крепления стола и приспо
собления для накатывания.
Закаленный резьбовой пе реводник, прокатываемый несколько раз подряд между сырыми заготовками плашек, создает негативный отпечаток своей резьбы на рабочих
поверхностях обеих загото вок (твердость заготовок пла шек НВ= 120). Переводники
для накатывания на плаш |
|
||
ках резьб. Ml,4; |
Ml,7 и М2 |
|
|
выполняются |
четырехзаход- |
|
|
ными. Чертеж |
|
переводника |
|
приведен на фиг. 53, б, а его |
|
||
размеры—в табл. 11. Резьба |
|
||
на переводниках |
нарезается |
Фиг. 53. Схема накатывания резьбы перевод |
|
дисковыми гребенками по |
ником на заготовках резьбонакатных пла |
||
окончательным |
исполнитель |
шек (а); чертеж переводника для накатыва |
|
ным размерам. |
|
|
ния резьбы на плоских плашках (б). |
|
изготовляются |
из стали марки ШХ15, плашки — |
|
Переводники |
|||
из сталей марок Х12М, Х12Ф1, |
Х12ФН, 9ХС или ХВГ. Наилучшие |
результаты по стойкости показывают плашки из сталей марок Х12Ф1 и Х12ФН. Особо ответственной операцией в технологическом процессе изготовления плашек является их термическая обработка. Для предотвращения деформации заготовок во время термической
обработки и |
получения |
чистой |
поверхности резьбы |
закалка |
|
плашек производится |
в |
нейтральной среде в соляных ваннах |
|||
или в камерных печах. |
В |
первом |
случае технологический процесс |
||
термической |
обработки |
плашек из |
сталей марок Х12Ф1 |
и Х12ФН |
|
таков: |
|
|
|
|
|
1)нагрев в камерной печи до температуры 500° в течение 1 часа;
2)нагрев до температуры 1060 -ч- 1070° в соляной ванне;
7* |
99 |