
книги из ГПНТБ / Шнейдер, Юрий Григорьевич. Холодная бесштамповая обработка точных деталей давлением
.pdfДля уменьшения трения между заготовкой и ограничительными дисками последние с внутренней стороны, обращенной к валкам, делаются с небольшим конусом.
Зубчатые валки с заборной частью состоят
из трех основных элементов по длине зуба (фиг. 79, б):
1)заборной части на длине /£;
2)калибрующей части на длине Z2;
3)обратного конуса на длине /3.
Наибольший диаметр валка на участке заборной части (в месте перехода заборной части в калибрующую) равен диаметру выступов зубчатого валка:
Da = т (z + 2,4),
а наименьший
Dal = т(?+ 1).
Назначение заборной части — облегчить осевое перемещение валков путем постепенного вдавливания зубьев в металл заготовки.
Калибрующий участок зубьев валков окончательно оформляет зуб обрабатываемого колеса, обеспечивая точность профиля и чистоту поверхности зубьев. Зубья валков на участке Z2 должны быть выпол
нены с особой тщательностью в отношении как формы и размеров,
так и микрогеометрии рабочих поверхностей.
Обратный конус на зубьях валков имеет меньший угол, чем забор ная часть, и предотвращает образование на поверхностях накатан ного зуба рисок — следов контакта с задней торцовой поверх ностью валков.
Технология и технико-экономические показатели процесса нака тывания зуба маломодульных зубчатых колес. Основным условием
обработки зубчатых колес накатыванием в холодном состоянии яв ляется достаточная пластичность металла заготовки.
Этому условию удовлетворяют алюминиевые и медные сплавы,
за исключением бронз некоторых марок. Достаточной пластичностью для образования зубьев маломодульных зубчатых колес в холодном состоянии обладают некоторые марки нержавеющей стали при условии
соответствующей предварительной термической обработки.
Впроцессе накатывания зуба поверхностные слои металла сильно
наклепываются, и наклеп распространяется на значительную глу бину.
Вцелях уменьшения износа зубчатых валков, а также предотвра щения возможного перенапряжения поверхностных слоев металла
заготовки целесообразно вводить промежуточную термическую обра
ботку — отжиг. Последний производится после накатывания чер
новыми валками, не имеющими заборной части, или после предвари тельного прохода валками с заборной частью.
По результатам экспериментальных исследований диаметр заго товок из медных и алюминиевых сплавов следует делать на 0,05 -z- -н 0,06 модуля меньше диаметра начальной окружности обрабаты ваемого зубчатого колеса,
151
Из составляющих режима накатывания зубьев наибольшее влия ние на протекание процесса пластического деформирования и произ водительность обработки оказывают окружная скорость и продоль ная подача зубчатых валков — при работе валками с заборной частью и радиальная подача — при накатывании зуба валками без заборной части.
С увеличением числа зубьев условия их образования накатыва
нием улучшаются, а оптимальные значения окружной скорости и соот
ветственно производительность обработки повышаются. Наивыгод нейшие величины окружной скорости при накатывании маломодуль ных зубчатых колес (диаметром 6 -н 80 мм) по результатам экспери ментального исследования составляют 3-4-30 м!мин.
Экспериментальные исследования [41 ], проведенные на зубона
катном станке с использованием двух зубчатых валков с заборной частью, выявили точностные возможности метода изготовления мало модульных зубчатых колес накатыванием.
Способ образования зуба выдавливанием зубчатыми валками,
профиль и размеры которых с большой точностью копируются на обрабатываемой заготовке, выгодно отличается от применяемых в настоящее время способов образования зуба.
Концентрическое расположение начальной окружности, окруж ностей выступов и впадин обеспечивает высокую точность накаты ваемых зубчатых колес по радиальному биению начальной окруж ности.
При накатывании зуба на длинных заготовках или коротких, но собранных на оправку в пакет (исследование проводилось на зуб чатых колесах, обрабатывавшихся в пакете) имеет место значитель ный разброс по точности, характеризуемый радиальным биением
начальной окружности. Так, из 25 обработанных зубчатых колес
по радиальному биению семь колес относились к |
1-му классу точно |
|
сти, четырнадцать — ко 2-му классу и |
четыре |
зубчатых колеса |
на 3 мк, вышли за пределы допуска 3-го |
класса точности. |
Такой разброс в значительной мере объясняется неодинаковыми условиями пластической деформации металла при образовании зуба у заготовок, по-разному расположенных в направлении продольной подачи валков.
Естественно, что при накатывании зуба в конце длинной заго товки или на последних штучных заготовках, собранных в пакет, условия пластической деформации металла будут наиболее тяжелыми, так как по мере продвижения валков в направлении подачи коли чество вытесненного ими металла непрерывно растет. Соответственно этому увеличивается и степень наклепа, в результате чего глубина проникновения зубьев валков в заготовку получается различной.
Это положение подтверждается результатами измерения. Наи большие отклонения по диаметральным размерам получились у край
них зубчатых колес. Значительно повышается износоустойчивость зуба по сравнению с колесами, обработанными резанием, что объ ясняется характером деформации металла при холодной пластиче ской обработке давлением (фиг. 81, б).
152
Произведенные замеры микротвердости и чистоты рабочих поверх ностей зуба накатанных зубчатых колес из дуралюмина и латуни
показали, что в результате наклепа поверхностная твердость зуба латунных колес возрастает по сравнению с исходной на 20 -4- 25%,
а дуралюминовых — на 15 ч- 20%. Чистота поверхности соответ ствует 8 ч- 9-му классу.
Схема накатывания зуба тремя валками [42] принципиально не отличается от схемы обработки двумя валками с осевой подачей заготовки (фиг. 77). Главным рабочим движением здесь также яв
ляется синхронное вращение валков, вращение заготовки и относи тельное перемещение валков относительно друг друга. Деление
заготовки на заданное число зубьев производится в обоих случаях в начале процесса при помсщи направляющей шестерни, а в дальней шем автоматически зубьями самой заготовки.
Однако наличие третьего накатного валка позволяет вести про цесс более интенсивно и производительно, надежно центрировать
валки относительно заготовки, что исключает одну из серьезных причин снижения точности зубчатого венца. Замена осевой подачи заготовки подачей накатных валков вдоль оси заготовки несколько
упростили кинематику станка и позволили производить накатывание на токарных станках с помощью сравнительно несложных приспо соблений.
Приспособление, показанное на фиг. 80, устанавливается на осно вании суппорта токарного станка; заготовка (в виде прутка или пакета дисков) закрепляется в центрах, как показано на фиг. 81, а.
Основными условиями нормального протекания процесса нака тывания зуба являются: строгая параллельность осей вращения вал ков между собой, параллельность их оси вращения заготовки,
а также совмещение оси центрирующего отверстия приспособления
сосью центров станка. Допускаемое отклонение переднего торца одного из валков относительно торцов двух других не должно выхо
дить за пределы + 0,005 мм.
Точность станка, на котором производится накатывание, оказы вает существенное влияние на точность основных размеров получае
мых колес.
Станки, используемые для накатывания зубчатых колес, должны удовлетворять нормам точности, предусмотренным ГОСТ. При нака тывании колес 2-го и более высокого класса требования к точности станков повышаются. Прямолинейность и параллельность напра вляющих должны быть в пределах 0,02 мм на длине 1000 мм; допу стимая непараллельность оси шпинделя в направлении движения каретки в вертикальной плоскости не должна превышать 0,01 мм
на длине 300 мм, а в горизонтальной —0,08 мм на длине 500 мм. Настройка приспособления сводится к установке валков на межцен
тровое расстояние Ло, рассчитываемое по формуле 2.
л _ mz |
mzH |
яо — |
+ ~2~ ’ |
1 Временная производственная инструкция «Холодная накатка зубьев цилинд рических зубчатых колес малых модулей».
153
Фиг. 80. Трехвалковое приспособление к токарному станку для накатывания зуба маломодульных зубчатых колес (а); конструкция зубонакатного валка (б).
154
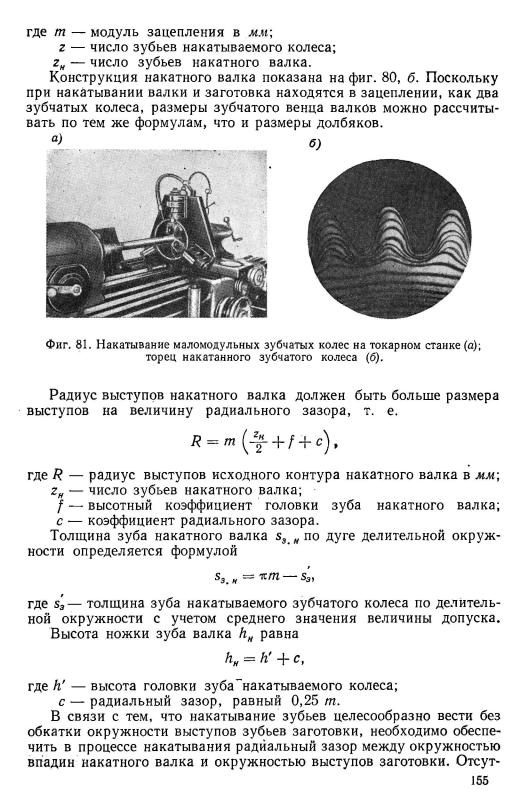
ствие необходимого зазора ведет к перегрузке зубьев валков, пере напряжению зубьев заготовки и потере точности зубчатого венца.
Наличие заборных конусов (фиг. 80, б) и заточки под углом 3 = 90° способствует созданию хороших условий пластического течения металла в осевом и радиальном направлениях. Именно заборная часть накатного валка осуществляет перемещение основного объема
металла в процессе накатывания; калибрующая часть производит окончательное оформление эвольвентного профиля накатываемого
зуба и придает его поверхностям требуемую чистоту.
В качестве материала для накатных валков, рекомендуется при менять инструментальные стали Х12Ф1 и Х12ФН; твердость валков после закалки RC = 60 — 61.
Тщательная отделка рабочих поверхностей накатного валка способствует уменьшению трения между ними и металлом заготовки, созданию лучших условий пластического течения металла и, как следствие, уменьшению необходимого усилия накатывания. Такое же
влияние на процесс накатывания оказывает качественная и обиль ная смазка. Хорошие показатели обеспечивает смазывающая смесь,
состоящая из 95% веретенного масла 2 (ГОСТ 1707—51) и 5% петро латума (ГОСТ 4096—54). Смазка должна подаваться в объеме 10-:-15 л
в минуту. Остальные условия накатывания близки к описанным ранее условиям обработки зубчатых колес двумя валками.
Основными составляющими режима накатывания, определяющими динамические характеристики процесса и его производительность, являются скорость накатывания (окружная скорость вращения заго товки) и продольная подача накатных валков относительно оси заго товки.
Производительность накатывания, выражаемая через длину L,
находится в прямой зависимости от числа оборотов заготовки в ми нуту’/? и скорости подачи валков s мм/об.
L — s-n мм/мин.
Однако с увеличением значений s и п возрастают нагрузка на зубья накатных валков и потребляемая в процессе накатывания мощность, ограниченные прочностью валков и мощностью станка.
Зависимости между режимом накатывания, величиной осевых Рх и радиальных Ру составляющих усилий и потребляемой мощностью накатывания при обработке, латунных и дуралюминовых зубчатых колес [42] с модулем т = 1 мм показаны на графиках фиг. 82. При накатывании зубчатых колес из цветных металлов (дуралюмин, латунь, бронза) рекомендуется работать со скоростью накатывания, равной 100 м/мин, и подачей не свыше 0,5 мм/об.
При накатывании незакаленных сталей марок 1X13, 2X13, 3X13, 4X13, ЗОХГСА скорость накатывания не должна превышать 50 м/мин, а подача —0,020 мм/об.
Исследования и пока еще небольшой опыт промышленного при менения описанного способа накатывания маломодульных зубчатых колес показали, что достигаемая точность обработанного давлением зубчатого венца по всем параметрам соответствует 3-му классу;
156
получение зубчатых колес более высокой точности связано с необхо
димостью выполнения ряда дополнительных условий.
Одним из таких условий (помимо перечисленных ранее) является однородность исходной твердости металла заготовок. Так, при нака тывании зубчатых колес из дуралюмина марки Д1Т (т = 0,8 мм\ z = 104) 2-го класса точности выявлена необходимость выдерживать
Фиг. 82. Графики зависимостей: а —■ усилий Рх и Ру от подачи при накатывании зубчатого колеса из латуни Л62; б — усилий Рх и Ру от подачи при накатывании колес из дуралюмина Д16Т; в — потребляемой мощности от подачи при накатыва нии зубчатого колеса из латуни ЛС62; г — потребляемой мощности от подачи при накатывании колес из дуралюмина Д16Т.
Модуль т = 1; число накатываемых зубьев z = 50.
колебания твердости заготовок (а также отдельных участков каждой из них) в пределах не более 6-4-8 единиц НВ. Невыполнение этого условия (в одном случае твердость металла накатывавшихся заго товок из листового дуралюмина колебалась в пределах НВ = 38-4-90) приводит к значительному разбросу размеров зубьев накатываемых колес при постоянном значении диаметра заготовок под накатывание.
Разбивка же заготовок на группы по твердости, с соответственно различными диаметрами под накатывание, в производственных усло виях практически неосуществима.
Более широкое и эффективное внедрение в производство совершен
ного и высокопроизводительного метода обработки маломодульных
зубчатых колес накатыванием требует:
а) повышения износостойкости и прочности накатного инстру
мента;
157
Фиг. 83. Накатывание мел ких профильных канавок подпружиненным роликом.
б) создания более жестких кон струкций накатных приспособлений
и специальных зубонакатных стан ков фирменного производства, рабо
тающих по принципу накатывания
не только цилиндрическими валками, но и плоскими плашками;
в) проведения исследований про цессов накатывания зубьев различ ными способами с целью выявления оптимальных условий обработки.
При обработке деталей с точными мелкими (глубиной до 0,5 мм) коль
цевыми винтовыми профильными
канавками может быть применен предложенный автором и внедрен ный в производство способ накаты вания роликами, упруго прижимае мыми к вращающейся заготовке, по схеме, показанной на фиг. 83. В этом
случае погрешности формы заготовки и ее установки не отражаются на точ
ности канавок, глубина которых полу чается строго равномерной во всех сечениях по окружности заготовки.
Заготовка 4 (фиг. 83) принуди тельно вращается с оправкой, уста новленной в центрах токарного стан ка. Накатной ролик 2 с кольцевыми канавками, свободно вращающийся на оси /, с определенным усилием
поджимается к заготовке пружиной
3. Ролик вращается от трения о за готовку.
13. Обработка профильных деталей
прокатыванием между роликами и плоскими плашками
Многие детали машин и приборов имеют сложную геометрическую фор му и ограничены профильными по верхностями. В большинстве случаев это малогабаритные, но весьма тру доемкие детали, особенно при обра ботке их профильных поверхностей фасонными режущими инструментами
на металлорежущих станках.
Более совершенной и произво дительной является обработка
158
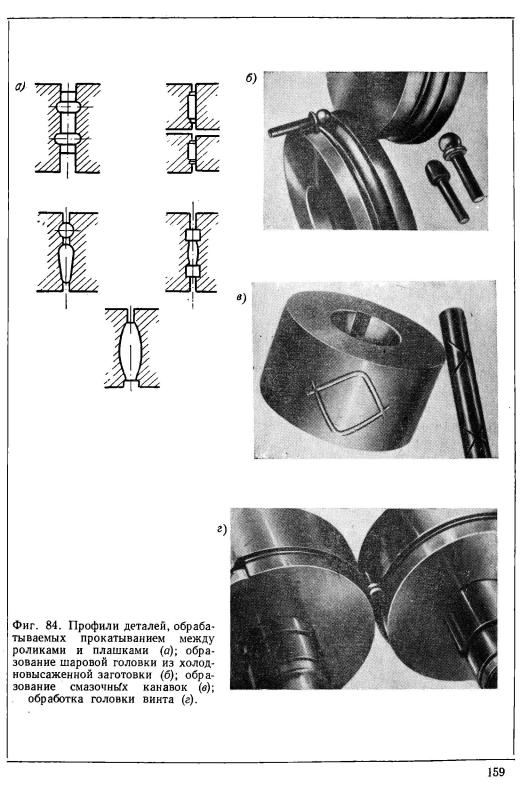
подобного рода деталей давлением путем прокатывания деталей — тел вращения между двумя вращающимися роликами и волочением деталей, ограниченных профильными линейчатыми поверхностями.
Прокатыванием между роликами и плашками можно качественно и производительно обрабатывать профильные детали типа показан ных на фиг. 84 [90, 91 ].
В настоящее время относительно широкое применение на заводах получило накатывание наружной резьбы, в меньшей степени —
Фиг. 85. Схема прокатывания между роликами: а — подача заготовки сверху (s^i>fa); б—подача заготовки снизу (vj= г’а); в — без подачи заготовки (иг = v?).
накатывание знаков, делений и рифлений. Еще меньше распро
странен процесс прокатывания при изготовлении разнообразных
профильных деталей.
Трудности, связанные с внедрением в производство прокатывания профильных деталей, обусловлены необходимостью изготовления сложных и трудоемких профильных роликов и установления опыт
ным путем оптимальных параметров режима прокатывания. При от
сутствии теории процесса и достаточно полных и надежных опытных данных выбор режима холодного прокатывания в каждом отдельном
случае связан с необходимостью проведения экспериментальных ис
следований.
Ниже приводятся некоторые данные о сущности и теории про цесса, а также рекомендации по его отладке в производственных условиях, основанные на результатах экспериментального иссле дования [43 ] и испытаний, проведенных автором.
Процесс холодного прокатывания между роликами может быть осуществлен по одной из трех схем (фиг. 85).
При работе по первой схеме (фиг. 85, а) прокатывание заго
товки производится между двумя профильными роликами 1 и 3,
160